表面处理处理种类.docx
《表面处理处理种类.docx》由会员分享,可在线阅读,更多相关《表面处理处理种类.docx(20页珍藏版)》请在冰点文库上搜索。
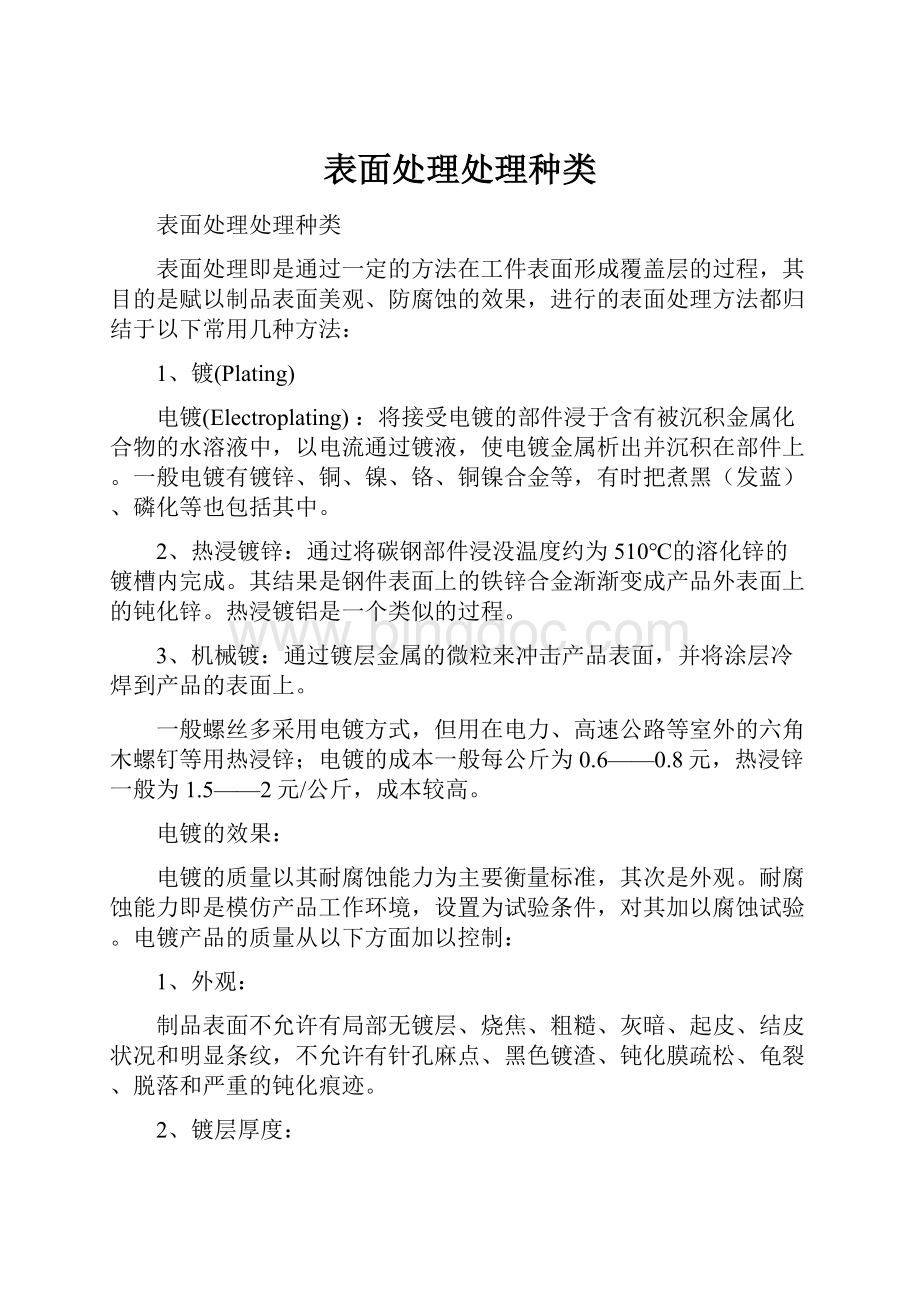
表面处理处理种类
表面处理处理种类
表面处理即是通过一定的方法在工件表面形成覆盖层的过程,其目的是赋以制品表面美观、防腐蚀的效果,进行的表面处理方法都归结于以下常用几种方法:
1、镀(Plating)
电镀(Electroplating):
将接受电镀的部件浸于含有被沉积金属化合物的水溶液中,以电流通过镀液,使电镀金属析出并沉积在部件上。
一般电镀有镀锌、铜、镍、铬、铜镍合金等,有时把煮黑(发蓝)、磷化等也包括其中。
2、热浸镀锌:
通过将碳钢部件浸没温度约为510℃的溶化锌的镀槽内完成。
其结果是钢件表面上的铁锌合金渐渐变成产品外表面上的钝化锌。
热浸镀铝是一个类似的过程。
3、机械镀:
通过镀层金属的微粒来冲击产品表面,并将涂层冷焊到产品的表面上。
一般螺丝多采用电镀方式,但用在电力、高速公路等室外的六角木螺钉等用热浸锌;电镀的成本一般每公斤为0.6——0.8元,热浸锌一般为1.5——2元/公斤,成本较高。
电镀的效果:
电镀的质量以其耐腐蚀能力为主要衡量标准,其次是外观。
耐腐蚀能力即是模仿产品工作环境,设置为试验条件,对其加以腐蚀试验。
电镀产品的质量从以下方面加以控制:
1、外观:
制品表面不允许有局部无镀层、烧焦、粗糙、灰暗、起皮、结皮状况和明显条纹,不允许有针孔麻点、黑色镀渣、钝化膜疏松、龟裂、脱落和严重的钝化痕迹。
2、镀层厚度:
紧固件在腐蚀性大气中的作业寿命与它的镀层厚度成正比。
一般建议的经济电镀镀层厚度为0.00015in~0.0005in(4~12um).
热浸镀锌:
标准的平均厚度为54um(称呼径≤3/8为43um),最小厚度为43um(称呼径≤3/8为37um)。
3、镀层分布:
采用不同的沉积方法,镀层在紧固件表面上的聚集方式也不同。
电镀时镀层金属不是均匀地沉积在外周边缘上,转角处获得较厚镀层。
在紧固件的螺纹部分,最厚的镀层位于螺纹牙顶,沿着螺纹侧面渐渐变薄,在牙底处沉积最薄,而热浸镀锌正好相反,较厚的镀层沉积在内转角和螺纹底部,机械镀的镀层金属沉积倾向与热浸镀相同,但是更为光滑而且在整个表面上厚度要均匀得多。
4、氢脆:
紧固件在加工和处理过程中,尤其在镀前的酸洗和碱洗以及随后的电镀过程中,表面吸收了氢原子,沉积的金属镀层然后俘获氢。
当紧固件拧紧时,氢朝着应力最集中的部分转够,引起压力增高到超过基体金属的强度并产生微小的表面破裂。
氢特别活动并很快渗入到新形成的裂隙中去。
这种压力-破裂-渗入的循环一直继续到紧固件断裂。
通常发生在第一次应力应用后的几个小时之内。
为了消除氢脆的威胁,紧固件要在镀后尽可能快地加热烘焙,以使氢从镀层中渗出,烘焙通常在375-4000F(176-190℃)进行3-24小时。
由于机械镀锌是非电解质的,这实际上消除了氢脆的威胁
5.自催化镀(Auto-catalyticPlating),一般称为"化学镀(ChemicalPlating)"、"无电镀(ElectrolessPlating)"等自催化镍磷镀及工业应用
无电解镀镍是目前国际上发展速度较快的表面处理工艺。
它以无公害、操作简单和可镀基底广泛以及镀层良好的耐磨耐腐性能受到工业界普遍瞩目和青睐。
自催化镍磷镀(以下称化学镀镍)技术,是目前国际上发展速度最快的低温表面强化高新技术。
它最初是作为电镀镍和电镀铬的代用镀层而工业化应用,以后发展到耐腐蚀性、耐磨性和电磁波屏蔽特性等多功能用途而获得广泛应用。
尤其在国际上它作为一个无公害排放的表面处理工艺,获得绿色环保技术的美称,受到了工业界的普遍瞩目和青睐。
其应用几乎涉及所有工业领域。
化学镀镍在石油天然气工业中的应用多年来石油天然气一直是化学镀镍的检验场,化学镀镍已在大量的应用中有出色表现.在北美所有的化学镀镍中大约15%是用于油气工业.已证明对石油天然气工业最有价值的性能是镀层的厚度均匀性,优异的耐蚀性能以及耐磨/耐冲刷性能.许多用于这一领域的传统基体材料的性能通过应用化学镀镍而大大改善,并且降低了制造成本,延长了使用寿命.延长寿命这一点具有特别重要的意义,因为石油天然气工业中停机更换部件费用很高.石油天然气工业的作用分为三个主要部分,地面作业,地下/井下作业和海上作业.设备通常暴露于氢化物,硫化氢,二氧化碳,盐水,海水和含高浓度硫化物的暗礁水等苛刻的环境条件下,并且还合并有吸入泥沙和泥浆引起的磨损问题以及在某些情况下温度高达250oC.通过化学镀镍而使性能提高的典型部件包括:
地面作业----防喷器,制动系统,节流器,压缩机,燃气轮机,泵体,泵,连接管路和阀等;地下/井下作业---联接器,测井仪,拄塞,分隔器,泵,安全阀装置和油管.海上作业---防喷器,燃气轮机/压缩机,热交换器,泵,隔水管连接器和阀化学镀镍层的厚度均匀性,耐腐蚀性和耐磨性性能促使其广泛用于阀和流量控制装置.显然,这些设备是油井作业的关键设备,油井作业的主要经济因素是设备有良好的性能和长的寿命.人们首先认识到化学镀镍的可应用的性能是其耐腐蚀性,光洁度和厚度均匀性.这些性能为球阀塞提供了所要求的表面条件,并改善了阀座部分的密封状况.人们最初只把化学镀镍看作是可能代替硬铬的一种选择,而现在化学镀镍在这一市场已占统治地位.在这一领域最具典型性的是低碳钢球阀常常采用75微米厚的化学镀镍层.可以看到化学镀镍在石油天然气工业所有领域中已获得了成功的应用.例如:
中东一家工厂的原油生产,相关的气体中含有55%的硫化氢,加工温度80oC,压力20MN/m2(3000psi).在这种条件下,由于腐蚀,表面开裂和冲蚀而发生的失效使低碳钢球阀的最长使用寿命仅3个月.而球阀采用75微米的化学镀镍层大大延长了设备的使用寿命,经过两年的连续运行未见设备表面损坏.使用海水注入系统的采油厂,其球阀也能获得同样的好处.操作过程包括在高压下泵送海水以迫使原油到达表面.在沙特阿拉伯的Ghawar油田,阀采用75微米厚的化学镀镍层,成功地经受了操作条件的考验,运行四年未发现镀层损坏.化学镀镍除了已成功地应用于石油天然气工业中的球阀,它在其他工程领域的阀部件的应用也同样成功.例如:
为埃及阿斯旺大坝项目制造的大型球阀的阀杆采用了化学镀镍.阀部件必须保证即使长期不动也能在需要时开闭自如并且运行可靠.采用75微米厚的化学镀镍层保护阀杆免遭腐蚀和磨损便提供了这种可靠性.106吨的巨型阀,其孔径260cm,仅上阀杆就超过了6吨重.在Khuff气井,经过化学镀镍处理的阀,节流器和其他部件的性能同样给人流下了深刻的印象.Khuff气井的气质较差,产生于大理石和石灰石岩层,岩层一般含有6%(mol)的二氧化碳和0.1%(mol)的硫化氢,它还含有大约28L/Mm3以己烷为主的冷凝物,7L/Mm3的水.井口气压一般为35MN/m2(5000psi),温度为90oC,气体流速通常大于6米/秒.在这些条件下,由于腐蚀/冲蚀造成的钢部件损坏是非常严重的.点蚀和冲蚀导致碳钢节流器上金属损失率为每年3—5毫米,而在所有湿润表面上采用了25微米厚的化学镀镍层则成功地解决了这个问题.通过应用化学镀镍也能克服球阀在上述环境下产生的问题,一般采用75微米厚的化学镀镍层可使球塞至少六年免遭腐蚀.化学镀镍的耐腐蚀性,硬度,表面光洁度,润滑性对防火流量阀的生产和性能十分有益.要求这些阀正常操作时能不漏气泡,而在不小心暴露于650oC温度后能充当节流阀,并且要求在着火时也能工作.化学镀镍也用于某些关键的安全阀中.例如:
防喷器是用于紧急情况下的关闭油气井的安全阀,由液压驱动活塞组成,能够切入油气管道,堵塞油气的流动.经测试以后,只要求一套装置在紧急情况下运行一次,但必须保证性能良好,为此,在活塞或密封表面不允许发生腐蚀和物理损伤.常用大约100微米厚的化学镀镍曾来达到所需的硬度和耐腐蚀性.
6.浸渍镀(ImmersionPlating)采用硫酸铜、硫酸亚锡为主盐的置换反应浸镀法在钢铁件表面制得金黄色铜锡合金层。
通过添加含氟系阴离子及羧基系阴离子的络合剂,控制铜、锡离子的置换反应速度,获得15%~39%铜含量的合金镀层,外观呈18~22K金色,膜层结合力好,耐蚀性优良 化学镀仿金的类型有两种,一种是使用还原剂的化学还原型,所形成的镀膜一般为赤褐色或色泽不好的金色,其镀膜的附着力差。
浸镀即置换镀或接触镀,是一种无需外界电流或还原剂,利用两种金属的电位差产生的电动势驱动的置换反应。
浸渍镀设备少、效率高、成本低
7.阳极氧化(Anodizing)接近表面镀层处理,金属或合金的电化学氧化。
将金属或合金的制件作为阳极,采用电解的方法使其表面形成氧化物薄膜。
金属氧化物薄膜改变了表面状态和性能,如表面着色,提高耐腐蚀性、增强耐磨性及硬度,保护金属表面等。
例如铝阳极氧化,将铝及其合金置于相应电解液(如硫酸、铬酸、草酸等)中作为阳极,在特定条件和外加电流作用下,进行电解。
阳极的铝或其合金氧化,表面上形成氧化铝薄层,其厚度为5~20微米,硬质阳极氧化膜可达60~200微米。
阳极氧化后的铝或其合金,提高了其硬度和耐磨性,可达250~500千克/平方毫米,良好的耐热性,硬质阳极氧化膜熔点高达2320K,优良的绝缘性,耐击穿电压高达2000V,增强了抗腐蚀性能,在ω=0.03NaCl盐雾中经几千小时不腐蚀。
氧化膜薄层中具有大量的微孔,可吸附各种润滑剂,适合制造发动机气缸或其他耐磨零件;膜微孔吸附能力强可着色成各种美观艳丽的色彩。
有色金属或其合金(如铝、镁及其合金等)都可进行阳极氧化处理,这种方法广泛用于机械零件,飞机汽车部件,精密仪器及无线电器材,日用品和建筑装饰等方面。
补充:
除金属外,其他物质在阳极所引起的氧化作用,也称为“阳极氧化”
补充:
在现实工艺中,针对铝合金的阳极氧化,比较多,可以应用在日常生活中,以为这种工艺的特性,使铝件表面产生坚硬的保护层,可用于生产厨具等日用品。
但铸造铝的阳极氧化效果不好,表面不光良,还只能是黑色。
铝合金型材就要好一点。
8.化学转化层(ChemicalConversionCoating);化学转化层(ChemicalConversionCoating)钢铁发蓝(Blackening),俗称”发黑“钢铁磷化(Phosphating)...复合电镀(弥散电镀)compositeplating用电化学法或化学法使用权金属离子与均匀悬浮在溶液中的不溶液性...钢铁发蓝(Blackening),俗称"煲黑"钢铁磷化(Phosphating)
9铬酸盐处理(Chromating)
10金属染色(MetalColouring)
11涂装(PaintFinishing),包括各种涂装如手工涂装、静电涂装、电泳涂装等
12热浸镀(Hotdip),。
热浸镀简称热镀,是将被镀金属材料浸于熔点较低的其他液态金属或合金中进行镀层的方法。
此法的基本特征是在基体金属与镀层金属之间有合金层形成
13热浸镀锌(Galvanizing),俗称"铅水"
14热浸镀锡(Tinning),热浸镀锡其主要是将待镀物利用一半自动工全自动方式经连续的水洗、酸洗藉以清除待镀物表面沾污的污物及锈点后,经浸渍助焊剂以利后续的镀锡加工之后再浸渍锡液,而后再经连串的撒甩、敲捶、回转等步骤后,藉以去除镀物本体上多余的锡液及使锡液均匀的布设于其上,再施以冷却干燥后,即可依上述步骤而得一对工作物产生热浸镀锡的作用
15阴极溅射,具有足够能量的带电粒子或中性粒子碰撞物体表面时,可把能量传递给表面的原子。
只要表面原子获得的能量大于本身的电离能,就能摆脱周围原子的束缚而离开物体表面,这种现象称为溅射。
16真空镀(VacuumPlating),真空镀主要包括真空蒸镀、溅射镀和离子镀几种类型,它们都是采用在真空条件下,通过蒸馏或溅射等方式在塑件表面沉积各种金属和非金属薄膜,通过这样的方式可以得到非常薄的表面镀层,同时具有速度快附着力好的突出优点,但是价格也较高,可以进行操作的金属类型较少,一般用来作较高档产品的功能性镀层,例如作为内部屏蔽层使用。
17离子镀(IonPlating),离子镀在真空条件下,利用气体放电使气体或被蒸发物质部分电离,并在气体离子或被蒸发离子镀原理图物质离子的轰击下,将蒸发物质或其反应物沉积在基片上的方法。
其中包括磁控溅射离子镀、反应离子镀、空心阴极放电离子镀(空心阴极蒸镀法)、多弧离子镀(阴极电弧离子镀)等。
18表面硬化:
所谓表面硬化法是指通过适当的方法使零件的表层硬化而零件的心部仍然具有强韧性的处理。
通过这种处理,可以改善零件的耐磨性以及耐疲劳性,而由于零件的心部仍然具有良好的韧性和强度,因此对冲击载荷有良好的抵抗作用。
常用的表面硬化处理方法主要有渗碳、氮化、硬质阳极氧化、镀铬、表面淬火以及渗金属等。
(1)渗碳
钢的渗碳就是含碳量较低的钢制零件在渗碳介质中加热或者保温,使碳原子渗入表面,获得一定的表面含碳量,在淬火之后,含碳量高的表层硬度很高,而含碳量低的心部硬度低仍具有良好的韧性。
目的是使零件获得高的表面硬度、耐磨性以及高的接触疲劳强度和弯曲疲劳强度。
主要用于承受磨损、交变接触应力或者弯曲应力和冲击载荷的零件,如轴、齿轮、凸轮轴等,这些零件要求表面有很高的硬度而心部要有足够的强度和韧性。
渗碳法分为固体渗碳法、液体渗碳法和气体渗碳法三种。
另外还有真空渗碳法。
固体渗碳法就是把零件放入固体渗碳剂(由木炭粉以及BaCO3和Na2CO3等促进剂组成)中然后放入渗碳容器里加热到900℃—930℃保温一定时间。
液体渗碳是把工件浸入以氰化钠(NaCN)为主(含NaCl、NaCO3和Na2CO3等添加剂)
的熔融盐浴里,氰化钠分解所生成的C和N渗入工件中。
气体渗碳是把零件放入通有CH4和CO的容器里加热使碳原子渗入工件表面。
渗碳层的深度可以达到几个毫米,其深度随渗碳时间的增加而增加,随渗碳温度的升高而加深,但是渗碳速度随时间的延长而减慢。
对不要渗碳的部位一般采用镀铜保护或者预留加工余量、渗碳后把该处切掉的方法进行防护。
渗碳后必须进行淬火和低温回火处理以得到零件所需要的硬度(可达HRC55—65),注重高硬度时在150℃左右回火,而为了保持零件的尺寸精度,防止时效变形时在180℃—200℃左右回火。
最后必须要提及一点是,我们经常提到的渗碳层深度是指淬火后的有效硬化层深度,国标GB9450—88上规定为从零件表面到维氏硬度值为550HV的距离,实际碳在零件中扩散达到的距离比这个要大得多。
附图:
Q235钢和20#钢渗碳淬火后显微组织(100倍、200倍)
(2).氮化
氮化是指把合金钢(一般含有Al、Cr、Mo)在无水氨气(NH3)流中在500℃—570℃左右长时间加热,使钢的表面形成一层硬度很高又耐腐蚀的氮化物(主要为Fe2N、Fe3N、Fe4N)。
一般有气体渗氮、液体渗氮和辉光离子渗氮。
氮化时合金钢的含碳量一般在0.2%—0.5%,主要由零件心部的机械性能来决定含碳量,含碳量高时阻碍N的扩散,从而减少氮化层的厚度,而含碳量少时,零件截面上的硬度梯度变化就会大,从而造成氮化层容易剥离。
Al的作用是增加渗氮后钢的表面硬度,Cr可以增加氮化层的厚度,Mo可以防止在500℃—570℃长时间加热造成的回火脆性,Cr、Mo对材质的改良也很重要。
历史最久国际上普遍采用的渗氮钢是38CrMoAl。
一般的氮化零件的工艺流程为锻造—退火—粗加工—调质—精加工—氮化。
不需要氮化的部位可以镀Ni或者镀Sn或者镀Pb20%+Sn80%。
氮化处理前先对零件进行调质处理,使其具有良好的塑性和韧性,氮化处理后不再实施淬火、回火,并且氮化处理本身的温度就比较低,所以工件的变形小。
氮化处理后工件表面的硬度可以达到HRC65—72,比渗碳处理后的硬度更高更耐磨,并且耐腐蚀性能要好。
辉光离子渗氮法是把零件置于真空反应炉内,用真空泵把炉内抽真空,然后通入N2和H2的混合气体,把炉内压力调整到100—1000Pa,以炉体接阳极,工件接阴极,在两极间通数百伏的直流电时产生辉光放电,这时所产生的氮离子就会高速向工件表面运动。
而处在阴极的工件被冲击出铁原子,与氮离子结合成FeN,随即被工件表面吸附,在离子轰击作用下,逐步分解为低价氮化物和氮原子,氮原子就向内部渗入及扩散。
辉光离子渗氮的时间与普通渗氮相比要短的多,普通渗氮要几十个小时,而辉光离子渗氮最快只要几个小时。
附图:
20#钢和40Cr钢氮化后显微组织(400倍)
(3).硬质阳极氧化
铝的阳极氧化是以铝或铝合金作阳极,以铅板作阴极在电解液中电解,使其表面生成氧化膜层。
经过阳极氧化,铝表面能生成厚度为几个至几百微米的氧化膜。
这层氧化膜的表面是多孔蜂窝状的,比起铝合金的天然氧化膜,其耐蚀性、耐磨性和装饰性都有明显的改善和提高。
采用不同的电解液和工艺条件,就能得到不同性质的阳极氧化膜。
阳极氧化的主要工艺流程:
脱脂除油—碱腐蚀—抛光—阳极氧化—染色—封孔处理。
碱腐蚀的目的是去除铝合金表面致密但不均匀的氧化膜,对高硅铝合金,采用HN03、HF混合溶液,其他铝合金采用以NaOH溶液为主的碱性槽液。
抛光的目的是得到光亮的基体表面,分为机械抛光、电解抛光和化学抛光。
机械抛光就是采用机械方法磨出光亮表面。
电解抛光是利用电流的作用,使铝合金发生电化学反应,在铝合金表面凸凹不平的部分发生不同程度的溶解,使铝件表面产生光滑的镜面效果。
化学抛光就是把零件浸在化学溶液里面发生反应从而得到光亮的表面,分为酸性抛光和碱性抛光。
染色就是利用阳极氧化膜的多孔结构和强吸附性能,将已阳极氧化处理的铝制件浸渍在有机染料或无机染料的溶液中,则氧化膜针孔吸附染料而着色。
另外还有电解着色、整体着色等。
由于铝及铝合金生成的氧化膜具有高的孔隙率和吸附性,很容易被污染,尤其在腐蚀性环境中,腐蚀介质容易进入膜层孔隙而引起腐蚀。
氧化膜染色后应进行封闭处理,以增加色泽的耐晒性和耐蚀性。
在工业生产中,经过阳极氧化的膜层,不管染色与否,一般都要进行封闭处理。
一般采用的是热水封闭和蒸汽封闭,其原理为氧化膜表面和孔壁的三氧化二铝在热水中发生水化反应,生成水合氧化铝,使原来氧化膜的体积增加33~100%,氧化膜体积的膨胀使膜孔显著缩小,从而达到封孔的目的。
反应式为:
Al2O3+nH2O=Al2O3?
nH2O
此外还可以采用各种化学溶液封闭,如重铬酸钾溶液封闭,封闭后的阳极氧化膜呈浅黄色,有特别高的耐蚀性。
阳极氧化采用的电解液主要有硫酸、草酸、铬酸,其中硫酸阳极氧化处理应用最为广泛。
如果没有特别指明,一般指的是硫酸阳极氧化。
硫酸阳极氧化具有槽液成本低、成分简单、操作维护简便、氧化膜透明度高、着色性高等特点,因而得到广泛应用。
硫酸阳极氧化操作条件为:
H2SO4(体积)10%~30%
温度℃18~22
Al/g.L-1≤20
电流密度/A.dm-20.6~3
时间/min10~60
草酸氧化膜的特点和硫酸氧化膜相近,孔隙率低于硫酸氧化膜,耐蚀性和硬度高于硫酸氧化膜。
草酸的槽液成本和操作电压高于硫酸,有些合金的草酸氧化膜颜色较深。
草酸和硫酸阳极氧化都需要良好的冷却系统配套。
铬酸阳极氧化膜特别耐腐蚀,主要应用干飞机制造工业,铬酸氧化膜和油漆的附着力强,也用于作油漆的底层,铬酸阳极氧化膜灰色不透明,一般不用于装饰。
为了提高阳极氧化膜的硬度和厚度,把硫酸氧化槽的温度降低至0℃,电流密度提高至2.7~4.0A/dm2,可以获得25~50μm的“硬质氧化膜”。
用草酸加少量硫酸可以在5~15℃得到硬质氧化膜。
有些专利用优化硫酸的浓度,加有机酸或其他添加剂,进行硬质阳极氧化。
阳极氧化膜厚度一般为5—20μm,硬质阳极氧化膜最厚可以达到60—250μm,硬度一般为HV240—500,熔点高达2050℃,短时间能耐1500—2000℃的高温,并且导热系数低,电阻率好,具有很高的绝缘性能但是阳极氧化膜都很脆,随着厚度的增加脆性增大,因此硬质阳极氧化膜不能承受冲击、弯曲和变形。
硬质阳极氧化膜的耐腐蚀性也比一般的阳极氧化膜要好。
附图:
阳极氧化膜(前者为电镜扫描照片,后者为结构示意图)
(4).镀铬
铬的硬度可以达到800~10OOHV,是最硬的金属。
它有很强的钝化性能,在大气中很快钝化,因而铬层在大气中很稳定,能长期保持其光泽,在碱、硝酸、硫化物、碳酸盐以及有机酸等腐蚀介质中非常稳定,但可溶于盐酸等氢卤酸和热的浓硫酸中。
铬镀层优点为硬度高、耐磨性好、光反射性强。
并且耐热性佳,在480"C以下不变色,50O℃以上才开始氧化,700"C则硬度下降。
铬镀层缺点为太硬易脆、易脱落。
铬镀层具多孔性,所以对钢铁腐蚀性不很理想,所以一般先镀铜,再镀镍最后再镀一层铬才能达到防腐蚀及装饰的目的。
传统的镀铬工艺,其电镀液以铬酸为基础,以硫酸作催化剂,两者的比例为100:
1。
经典的常规镀铬溶液配方为
CrO3 250g/L
H2SO4 2.5g/L
Cr3+ 3g/L
常规镀铬中,只有12-15%的电流用于沉积铬层,80-85%的电流用于析出氢气。
氢气会渗入铬层,也会渗入基体达几十微米。
氢气的渗入,使得钢的疲劳强度下降约30-40%。
因此镀后必须进行去氢处理。
而镀前也必须先做去应力处理:
因为镀铬对应力的敏感性很高,镀铬表面必须没有应力存在,一般镀件经机械加工、研磨,或硬化热处理都有残留应力,可加热150至230"C消除残留应力。
镀硬铬就是比一般的镀铬层厚一点,所以相应的时间也要延长,一般需要十几个小时。
(5).表面淬火
表面淬火是指将工件表面一定深度范围内迅速加热到淬火温度,然后迅速冷却,在一定深度范围内达到淬火目的的热处理工艺。
目的是在工件表面一定深度范围内获得马氏体组织,而心部仍保持淬火前的组织状态(调质或者正火状态),从而使表面硬而耐磨,而心部又有足够的塑性和韧性。
主要用于中碳调质钢和球墨铸铁制的机器零件。
主要的表面淬火方式有感应加热表面淬火、火焰淬火以及激光加热和电子束加热表面淬火。
感应加热表面淬火,是使工件表面产生一定的感应电流,迅速加热零件表面,然后迅速淬火的一种金属热处理方法。
感应加热原理:
工件放到感应器内,感应器一般是通入中频或高频交流电(500-300000Hz)的空心铜管。
产生交变磁场在工件中产生出同频率的感应电流,这种感应电流在工件的分布是不均匀的,在表面强,而在内部很弱,到心部接近于0,叫做集肤效应。
利用这个集肤效应,可使工件表面迅速加热,在几秒钟内表面温度上升到800-1000oC,而心部温度升高很小。
根据电流频率的不同,可将感应加热表面淬火分为三类:
第一类是高频感应加热淬火,常用电流频率范围为200~300千赫兹,一般淬硬层深度为0.5~2.0mm。
适用于中小模数的齿轮及中小尺寸的轴类零件等。
第二类是中频感应加热淬火,常用电流频率范围为2500~800赫兹,一般淬硬层深度为2~10mm。
适用于较大尺寸的轴和大中模数的齿轮等。
第三类是工频感应加热淬火,电流频率为50赫兹,不需要变频设备,淬硬层深度可达10~15mm。
适用于较大直径零件的穿透加热及大直径零件如轧辊、火车车轮等的表面淬火。
感应加热表面淬火具有表面质量好,脆性小,淬火表面不易氧化脱碳,变形小等优点,所以感应加热设备在金属表面热处理中得到了广泛应用。
火焰加热淬火是用乙炔—氧或煤气—氧等火焰直接加热工件表面,然后立即喷水冷却,以获得表面硬化效果的淬火方法。
火焰加热温度很高(约3000℃以上),能将工件迅速加热到淬火温度,通过调节烧嘴的位置和移动速度,可以获得不同厚度的淬硬层。
表面淬火淬硬层深度一般计至半马氏体区。
附图:
感应加热表面淬火和火焰加热表面淬火示意图
表1 几种常用材料和工艺的选择
序号工艺时间硬化层深度