从含钪氯化烟尘中提取钪+.docx
《从含钪氯化烟尘中提取钪+.docx》由会员分享,可在线阅读,更多相关《从含钪氯化烟尘中提取钪+.docx(53页珍藏版)》请在冰点文库上搜索。
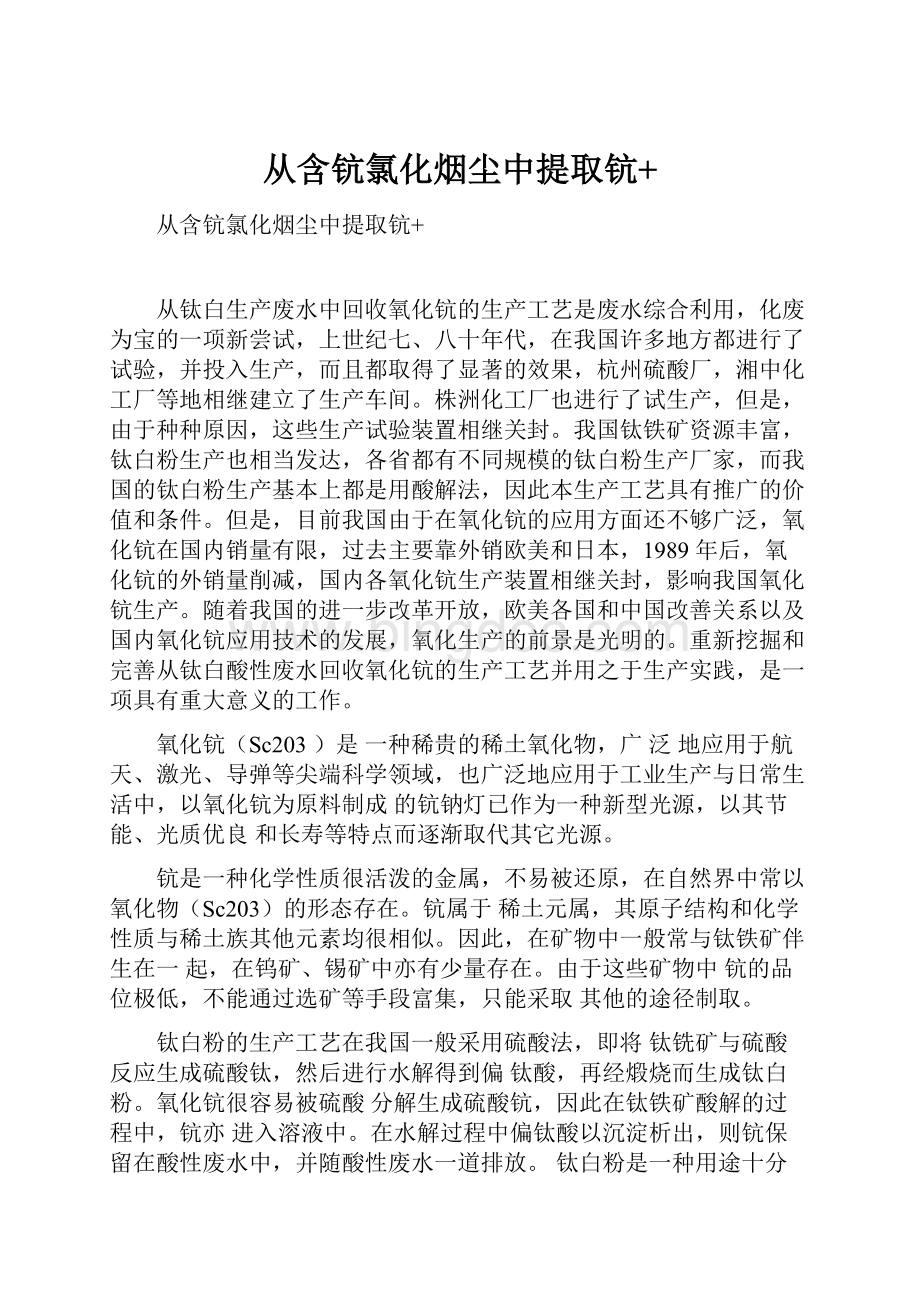
从含钪氯化烟尘中提取钪+
从含钪氯化烟尘中提取钪+
从钛白生产废水中回收氧化钪的生产工艺是废水综合利用,化废为宝的一项新尝试,上世纪七、八十年代,在我国许多地方都进行了试验,并投入生产,而且都取得了显著的效果,杭州硫酸厂,湘中化工厂等地相继建立了生产车间。
株洲化工厂也进行了试生产,但是,由于种种原因,这些生产试验装置相继关封。
我国钛铁矿资源丰富,钛白粉生产也相当发达,各省都有不同规模的钛白粉生产厂家,而我国的钛白粉生产基本上都是用酸解法,因此本生产工艺具有推广的价值和条件。
但是,目前我国由于在氧化钪的应用方面还不够广泛,氧化钪在国内销量有限,过去主要靠外销欧美和日本,1989年后,氧化钪的外销量削减,国内各氧化钪生产装置相继关封,影响我国氧化钪生产。
随着我国的进一步改革开放,欧美各国和中国改善关系以及国内氧化钪应用技术的发展,氧化生产的前景是光明的。
重新挖掘和完善从钛白酸性废水回收氧化钪的生产工艺并用之于生产实践,是一项具有重大意义的工作。
氧化钪(Sc203)是一种稀贵的稀土氧化物,广泛地应用于航天、激光、导弹等尖端科学领域,也广泛地应用于工业生产与日常生活中,以氧化钪为原料制成的钪钠灯已作为一种新型光源,以其节能、光质优良和长寿等特点而逐渐取代其它光源。
钪是一种化学性质很活泼的金属,不易被还原,在自然界中常以氧化物(Sc203)的形态存在。
钪属于稀土元属,其原子结构和化学性质与稀土族其他元素均很相似。
因此,在矿物中一般常与钛铁矿伴生在一起,在钨矿、锡矿中亦有少量存在。
由于这些矿物中钪的品位极低,不能通过选矿等手段富集,只能采取其他的途径制取。
钛白粉的生产工艺在我国一般采用硫酸法,即将钛铣矿与硫酸反应生成硫酸钛,然后进行水解得到偏钛酸,再经煅烧而生成钛白粉。
氧化钪很容易被硫酸分解生成硫酸钪,因此在钛铁矿酸解的过程中,钪亦进入溶液中。
在水解过程中偏钛酸以沉淀析出,则钪保留在酸性废水中,并随酸性废水一道排放。
钛白粉是一种用途十分广泛的添加剂,在油漆、涂料等生产领域都需消耗大量的钛白粉。
以我省为例,仅XX化工厂就年产钛白粉8000余吨,年耗钛铁矿2万余吨,矿石中Sc203按80g/t计算,每年可供回
收的Sc203就可达1600kg,回收率按50%计,每年XX可从钛白废水中回收Sc203800kg,价值约1600万元。
若在全国所有钛白粉生产厂家推广,其经济价值不可估量,而且妥善地解决了钛白粉生产中的酸性废水对环境的污染,其环境效应也十分可观。
XX化工厂曾于1986年投资30万元(不包括厂房),兴建了一个年产50kg的Sc203的生产试验车间,并于1988年初进行了为期二个月的试生产,生产出了合格的产品,取得了较为满意的效果。
1基本原理和生产工艺流程
1.1基本原理
从钛白酸性废水回收氧化钪,一般采用液-液萃取法。
在钛白粉的生产过程中,钛铁矿中的钪有70%~80%以Sc3+存在于水解废液中,其余部分在硫酸亚铁结晶和钛白水解的洗涤尾液中流失,由于原矿中Sc含量很低,一般为80~120g/t,因此在钛白废水中Sc3+的含量也很低,一般为10~20mg/L,而废水的其它杂质Fe、TiO2等都大大高于Sc2O3的含量,要使微量的钪富集,采取先除杂的办法是不经济的,因而只能采取先萃取后除杂的工艺路线。
萃取是利用溶剂中的溶质在两种不同的溶液中达到平衡后其分配比不一样,来使被提取的元素与杂质分离。
本项目采用的萃取剂是TBP+P204+煤油溶液组成的有机萃取剂,其萃取反应式为:
在萃取过程中,绝大部分Sc3+被萃取,同时大量Fe2+、Ti4+等杂质亦被萃取进入有机相中,因此萃取后必须进行酸洗除杂,以硫酸加双氧水进行洗涤,由于Fe2+、Ti4+等极易被酸化,生成硫酸盐而进入废酸中,而Sc3+则仍能紧密结合在有机络合物中而保留在有机相中,其主要反应为:
钪保留在经酸洗除杂后的有机相中,则采用加碱反萃使Sc3+从络合物中解脱出来,而有机相仍可返回使用,其主要反应式为:
经反萃后,Sc在沉淀物中含量增高,但杂质仍是主要的,为了得到纯度较高的氧化钪,必须进行精制。
精制的原理是利用优溶原理,Sc(OH)3能优溶于HCI溶液中,而Ti(OH)4等则较难溶解,控制一定的pH值,使Sc(OH)3溶解生成ScCI3溶液,其反应式为:
Sc(OH)3+3HCI=ScCI3+3H2O
然后用草酸将Sc3+沉淀下来,得到较为纯净草酸钪沉淀,其反应式为:
2ScCI3+3H2C2O4=Sc(C2O4)3!
+6HCI
最后为灼烧,将草酸钪沉淀在高温下灼烧氧化而生成Sc2O3的产品,其反应式为:
2Sc(C2O4)3+3O2=2Sc2O3+12CO2"
1.2生产工艺流程
2.3设备选型设计与设备连接
2.3.1设备选型设计
本装置的主体设备是非标设备,必须根据生产能力来进行设计。
(1)一段萃取槽
为带搅拌器的四段式逆流萃取槽,材质为PVC,外形尺寸为1900>1670>1170mm。
因目前生产量较小,只开二段即可,如果四段全开,产量可增加一倍。
(2)二段反萃除杂槽
为带搅拌器的十二级逆流反萃槽,材质为PVC,外形尺寸为2670>900>500mm。
(3)搪瓷反应罐
用于第三段碱反萃,为K-1000型,容量为1m3,带螺旋搅拌器与加热夹套。
2.3.2设备连接
氧化钪车间为长30m,宽5m,高8m的钢混结构二层楼房,三个母液池与一个废酸回收池布置于一楼地下,母液高位槽、硫酸高位槽、TP高位槽和液碱高位槽布置于东头二楼半平台上,以保证液体流动间的位差。
氧化钪的富集生产过程为连续生产,氧化钪的精制生产在实验室内进行,为间断生产。
2.4生产技术条件控制
2.4.1TP煤的配制
配料比:
P204100kg即10%
TBP30kg即3%
磺化煤油870kg即87%
配制工艺在搪瓷反应罐中进行,将P204、TBP和磺化煤油按上述比例加入,进行充分搅拌,然后放入TP回收槽中,再用泵送至TP高位槽备用。
2.4.2硫酸洗液和碱液的配制
硫酸洗液成分为8NH2SO4+1NH2O2,在配酸槽内进行,然后用泵送至高位酸槽备用。
碱液浓度为2.5NNaOH,在配碱槽内进行,配制好的碱液用泵送至高位碱槽备用。
2.4.3一段萃取工艺
日处理量为50m3钛白废水,则母液流量控制为38L/min,有机相比O/W取1120,则有机相流量控制为1.9L/min。
搅拌器转速控制为450r/min。
萃取时间为6min(二段),则萃取率可达90%。
2.4.4二段反萃洗杂工艺
有机相与硫酸洗液相比控制为O/W=111。
搅拌器转动速度控制为450r/min。
硫酸洗液流量控制为1.9L/min。
2.4.5三段碱反萃工艺
本过程为间断生产,有机相与碱液相比控制为O/W=111。
每次放入碱液400L,有机负载相400L,进行搅拌并加热,温度控制为70~75C,搅拌时间为30~50min,直到有机相内残留Sc2O3<5~10mg/L为止。
然后静置澄清30~40min,依次放出白色沉淀物与有机相,沉淀物放入沉淀槽进行过滤沉淀,有机相放TP回收槽,并泵入高位TP槽回用。
沉淀物经过滤后取出进行精制,滤液可送配碱槽重新配制碱液。
2.4.6精制工艺
优溶:
采用10%HCI为溶剂,加热溶解,温度控制在90~100C,控制终点酸度在pH=1~1.5。
加草酸沉淀:
按2.5g/L加酒石酸,2g/L加EDTA,50g/L加10%草酸进行静置沉淀,并用1%的热草酸溶液洗涤二次,固液比控制为1110。
灼烧:
一般在马弗炉内进行,温度控制为750C。
保温灼烧1h即可得到Sc2O3产品。
2.5原材料消耗
2.5.1主要原材料单耗
(1)硫酸:
21.6kg/m3废水
(2)双氧水:
4L/m3废水
(3)磺化煤油:
43.5L/m3废水(不包括回收)
(4)TBP:
1.5L/m3废水(不包括回收)
(5)P204:
5L/m3废水(不包括回收)
(6)液碱(35%NaOH):
5L/m3废水(不包括2.6试验生产结果与经济效益
2.6.1试验生产结果
经过几年来的摸索与两个月的生产试车,结果如下:
(1)打通了生产流程,生产出了合格的产品,经检验产品中Sc2O3
含量达到85%。
(2)证实了以TB煤从钛白酸性废水中回收氧化钪的“萃取、洗杂、反萃、精制”的生产流程是可行的。
(3)摸索出了萃取生产中较为理想的工艺参数,为提高萃取回收率,降低成本创造了有利的条件。
(4)同时探索出了一整套测定氧化钪在废水中、富集物中以及成品中的快速,可靠的分析方法,为生产和试验提供了可靠的保证。
2.6.2经济效益
生产1kg氧化钪,其生产成本为6169.78元,Sc2O4含量为85%~90%的产品价格为2万元/kg,按年产氧化钪50kg计,则年创利为:
692011元,半年内就可全部收回投资。
如果将成品价格为50000元/kg,则利润更可成倍增加,其经济效益更加惊人。
提取氧化钪后的废酸水,以及在洗杂中加入的硫酸全部可以返回钛白车间酸解工序用于配酸,亦可送磷肥车间使用,无废水排放,同时也间接创造了经济效益。
在该工艺中还可以回收进入酸性废水中的钛白,不但提高了钛白车间的总回收率,也具有一定的经济效益。
/min
Sc3+
Fe2+
Ti4+
4
30
0
2
6
40
0
4
8
60
0
6
10
80
0
8
12
90
0
10
14
90
10
20
16
92
15
30
18
95
20
40
1基本原理和生产工艺流程
1.1基本原理
从钛白酸性废水回收氧化钪,一般采用液-液萃取法。
钛的生产处理过程中,含钛矿物作为原料,在电弧炉中熔炼制得高钛渣,钪以Sc2O3的形式留在高钛渣中。
此高钛渣在进行高温氯化生产TiCl4时,钪被氯化成ScCl3。
以烟尘的形式被捕收于集尘器中。
于是钪在氯化烟尘中得到明显的富集,其含量可达0.03~0.12%。
此氯化烟尘是一种很好的提钪原料。
本文作者已进行了从氯化烟尘浸取钪的实验研究工作〔1〕,得到最佳浸出条件,其钪浸取率可达82%以上。
但由于在浸取钪的过程中,铁、锰等杂质也随钪一起被浸出,从而使得所得到的含钪溶液中含有大量的铁、锰杂质。
从盐酸浸出液中分离和富集钪的方法国内外已有文献报道,目前大多采用溶剂萃取法和离子交换法〔2~4〕。
这些方法一般操作复杂,价格昂贵,有待于寻找工艺简单可行,经济上更趋合理的方法。
本文采用一种沉淀剂,该沉淀剂对钪的选择性强,在一定的条件下可与钪作用生成沉淀,使钪进入沉淀物中,铁、锰等杂质则不进入沉淀物中,从而达到钪与铁、锰杂质分离的目的。
实验表明,这种分离工艺具有简单、经济的特点,钪的沉淀率可达100%,一次沉淀的铁、锰去除率大于98%,二次沉淀的铁、锰去除率大于99.8%。
1 原料
氯化烟尘取自某厂高钛渣高温沸腾氯化制取TiCl4时在集尘器中收集的废弃烟尘,其主要化学成分见表1。
用此氯化烟尘为原料,按本文作者在文献〔1〕中得到最佳浸出条件,即温度为室温,S∶L=1∶2,浸出介质为2%wt盐酸水溶液浸取钪,得到含钪的盐酸浸出液,浸出液经过滤,滤液中钪含量为237.25mg/L,此时钪的浸出率可达82%以上。
2.2 钪与铁、锰的分离
2.2.1 pH对铁、锰沉淀的影响
由Fe-H2O系及Mn-H2O系的E-pH图可知,pH>2时,Fe3+会水解生成Fe(OH)3沉淀;pH>7.5时,Mn2+会水解生成Mn(OH)2沉淀。
由于钪沉淀的最佳酸度为pH=5,为避免铁与钪共沉淀,首先用铁粉将溶液中的Fe3+还原成Fe2+(Fe2+水解生成Fe(OH)2的酸度为pH=7,pH=5的钪沉淀条件下,不会有Fe(OH)2沉淀生成),然后调整溶液酸度,在沉淀剂量与钪量之比为30∶1、室温条件下进行沉淀实验,分析滤液中的Fe2+、Mn2+含量,用差减法求得沉淀中的Fe2+、Mn2+含量,进而求得Fe2+、Mn2+的沉淀率,考察溶液酸度对Fe2+、n2+的沉淀的影响,结果见表5。
由表5可知,随着pH增大,Fe2+、Mn2+沉淀率减小,在pH=5时的钪最佳沉淀条件下,Fe2+、Mn2+沉淀率分别为1.8%和1.5%,对应的铁、锰去除率分别为98.2%和98.5%。
较好地实现了钪与铁、锰分离的目的。
pH=6时,无沉淀生成。
2.3 沉淀剂与钪的分离
沉淀剂在酸性溶液中沉淀,在碱性溶液中溶解,而Sc3+则相反,在酸性增加时会溶解,在pH>5时沉淀生成Sc(OH)3。
根据这一特性,用稀盐酸溶解含钪沉淀物,使Sc以ScCl3的形式转入溶液中,这时沉淀剂不溶解,仍为沉淀,于是可使钪从沉淀剂中分离出来。
为了使钪尽可能多地以ScCl3形式转入溶液,实验考察了盐酸浓度、用量对钪溶解的影响,结果见表9。
从氯化渣中浸出钪的研究
李亮
(攀枝花学院材料工程学院,四川攀枝花617000)
摘要:
以富集钪后的氯化渣为原料,研究了浸出酸种类、原料粒度、浸出酸浓度、浸出液固质量比、浸出温度和浸
出时间对钪浸出率的影响。
条件试验和正交试验表明,最佳试验条件为:
浸出酸种类为硫酸;浸出酸浓度为40%;
原料粒度为44μm(325目);浸出液固质量比为3.5;浸出温度70℃;浸出时间为8h。
浸出温度、浸出液固质量比
和浸出酸浓度对钪浸出率的影响大小依次为:
浸出温度>浸出液固质量比>浸出酸浓度。
稳定试验表明:
钪的浸
出率在95%以上,为下步进行钪的回收创造了有利条件。
关键词:
钪;提取;氯化渣;浸出;浸出率
中图分类号:
TF845.1文献标识码:
A文章编号:
1004-7638(2011)02-0015-05
ExtractingtheScandiumfromtheChlorineSlagging
LiLiang
(MaterialsEngineeringInstituteinPanzhihuaUniversity,Panzhihua617000,Sichuan,China)
Abstract:
Selectingthechlorineslaggingafterconcentrationasarawmaterial,theinfluenceoftheleaching
sourtype,rawmaterialgranularity,theleachingacidconcentration,theleachingliquidsolidmass
ratio,theleachingtemperatureandtheextractiontimeonthescandiumleachingratehavebeenstudied.
Theconditionexperimentandorthogonaltestindicatethatthesuperiorexperimentconditionis:
theleaching
souristhesulfuricacid;theleachingacidconcentrationis40%;thegranularityoftherawmaterial
is44μm(325items);theleachingliquidsolidmassratiois3.5;theleachingtemperatureis70℃;the
extractiontimeis8h.Theleachingtemperature,leachingliquidsolidmassratioandleachingacidconcentration
totheleachingrateinfluencesizeinturnare:
Theleachingtemperatureismorethantheleaching
liquidsolidmassratio,andthelaterismorethantheleachingacidconcentration.Thestabilitytest
indicated:
Thescandiumleachingratemayreachabove95%,anditcreatestheadvantagetocarryon
thescandiumrecycling.
Keywords:
scandium;extracting;chlorineslagging;leaching;leachingrate
0引言
在自然界中,作为稀土元素之一的金属钪,由于其以伴生矿物的形式稀散地分布于其他矿物中,分离和提取的难度较大,所以价值不菲,在一般工业中用量较少。
虽然如此,但是由于金属钪及其化合物具有较多的优异性能,诸如熔点高,比重小,强度大,热稳定性能好,化学活性较强等,因而被广泛地应用于宇航材料、电光源、电子工业、核技术、超导技术、医疗卫生行业及化工生产等重要领域中[1-4]。
我国是金属钪资源较为丰富的国家,其储量居世界第一,已探知的含钪矿物种类达800多种[5],这为今后我国大力开发利用金属钪资源奠定了物质基础。
因此,深入研究钪的回收及提取工艺意义重大。
我国钪资源的提取主要为通过从生产钛白粉的硫酸废液与钛生产过程中的氯化烟尘中回收利用。
另外,国内有些厂家也在积极研究从氧化铝赤泥、钨渣、稀土、选矿尾矿等中提取和回收钪。
本文拟对金属钪资源的分布状况进行总结,并重点阐述我国对金属钪的主要提取方法及其典型生产工艺和技术的研究现状与进展,以期为我国钪工业的发展提供一定的理论参考。
1钪资源状况
金属钪作为一种性能优越的稀有金属[6],最先是由瑞典化学家尼尔森(L.F.Nilson)于1879年从斯堪的纳维亚(Scandinavia)半岛的硅铍钇矿和钛硅酸稀金矿中发现的[7-9],因而被命名为Scandium,化学符号为Sc。
在地壳中,Sc的平均丰度达36×10-6,与金属Be,Sr,As,Se,W等的丰度大致相当。
Sc的平均丰度数据表明,其在地壳中的含量并不低。
但是,金属Sc的分布极为分散,绝大部分Sc结合其他稀土金属,以化合物的形式分布在800多种含钪矿物中[10-11];也有少数混杂稀土金属,形成自然界极稀少的独立矿
物[12],见表1。
目前,富集于钨锡矿、铀钍矿、稀土矿、钽铌矿、
铝土矿、白云母和钛铁矿等副产品中的Sc,是自然
界中具有工业意义的Sc资源,这些资源中Sc品位(按
Sc计)一般小于0.02%。
全世界金属钪的工业总储量
为200万t左右(以Sc计),其中,中国、美国和俄
罗斯等国家的储量较为丰富[9],国外金属钪资源的
主要分布情况如表2所示[13]。
2我国钪的主要提取方法
我国提取和回收金属钪的主要方法有溶剂萃取法、化学沉淀法和离子交换法3种[16-18]。
1)溶剂萃取法
溶剂萃取法中,首先将有机相和水相相互混合,待水相中要分离出来的物质进入有机相后,再通过两相质量密度的不同而将两相分开,从而实现液体混合物的分离或提纯。
该法是富积和提取钪最为重要的方法,具有选择性好、处理量大、操作简单、适用介质条件及应用范围广泛等优点[19]。
由于萃取液性质和机制的不同,萃取剂包含酸性含磷萃取剂、羧酸萃取剂、中性含磷萃取剂、螯合萃取剂等4类。
在金属钪的提取利用中,应用最广的萃取剂为有机磷酸类,常用的萃取剂如表4所示。
这种酸性磷类萃取剂可与钪离子形成十分稳定的萃合物,因而其萃取能力较强,有相当高的萃取率。
在金属钪的回收利用过程中,其关键技术体现在根据不同的原料和溶液成分,探寻有效的萃取体系,并建立与之适宜的工艺流程。
2)化学沉淀法
化学沉淀法是富集和提取钪的一种比较成熟而
常用的方法,且其工艺较为简单。
采用化学沉淀法
提取钪时,需要选择最佳的沉淀剂。
而根据不同矿
物体系的特点,可供选择的沉淀剂通常有氢氧化
物、氨水、草酸盐、碳酸盐、氟化物及二元酒石酸
盐等[12]。
例如孙本良等[20]从含钪氯化烟尘的盐酸浸
出液中采用沉淀法进行钪与铁、锰的分离时,先用
浓度为0.1mol·L-1的NaOH溶液调整溶液pH值,使
沉淀剂只与Sc3+反应生成沉淀,铁以Fe2+的形式存
在。
因为沉淀剂在酸性溶液中沉淀,但在碱性溶液
中溶解,而Sc3+正好相反。
根据这一原理,用稀盐
酸溶解沉淀物,就能将Sc3+以ScCl3的形式从沉淀剂
中分离出来,在提取钪的同时又能分离铁、净化钪,
整个处理过程钪的沉淀率达100%。
由于采用化学沉淀法提取的钪及其化合物的纯
度较低,难以满足工业需要。
故一般情况下,采用
该法提取Sc时必须结合其它的提取方法,以获得纯
度较高的钪化合物。
3)离子交换法
离子交换法是实现钪与某些结构复杂、性质相似的较难分离元素之间的有效分离方法之一,其分
离效果好,适用于生产高纯度的Sc2O3,现已得到了
广泛的应用[10]。
目前,钪离子交换工艺中使用的树
脂主要有Dowex-50,BioRadAG50W,X8,DiaiomSK1
等阳离子交换树脂,以及Dowexl,Ab-17等阴离子交
换树脂。
由于钪具有较强的化学活性,在低酸度介
质(HCl或H2SO4)中,可用强酸性阳离子交换分离
树脂上的Sc与Fe,Al,Ti,Ur等元素,然后用一定浓
度的硫酸作洗脱剂就可使钪和杂质元素得到有效分
离;同时,钪能形成硫酸盐络阴离子,利用这一性
质,可用碱性阴离子交换并分离树脂中不能形成硫
酸盐络阴离子的Al,Ca,Cd,Co,Cu,Zn,Mg,Ni等元素。
以上3种提取和回收钪的主要方法,其技术均较
为成熟,且各有优势。
相较而言,化学沉淀法的工艺较为简单,故最为成熟而常用,但提取的化合物
纯度不高;溶剂萃取法中萃取剂和萃取体系的选取
较为复杂,有待进一步发展;离子交换法生产的
Sc2O3的纯度最高,更具优势,但其操作较之溶剂萃
取法和沉淀法,工艺更为复杂,成本也更高些。
3我国钪生产的典型工艺和技术
由于金属钪主要掺杂在各种矿物中,而且含量
较低,考虑到资源利用的合理性和生产成本,独立
开采钪矿是不适宜的,故一般是在提炼其它矿物的
过程中综合回收钪,如从冶炼的废渣、废液和烟尘
中分离、提纯金属钪。
其典型的回收工艺包括对原
料进行预处理,采用HCl或H2SO4浸出、萃取或离子
交换、沉淀剂沉淀、灼烧,最终获得纯度较高的S