热轧板带钢车间设计Word文档格式.doc
《热轧板带钢车间设计Word文档格式.doc》由会员分享,可在线阅读,更多相关《热轧板带钢车间设计Word文档格式.doc(138页珍藏版)》请在冰点文库上搜索。
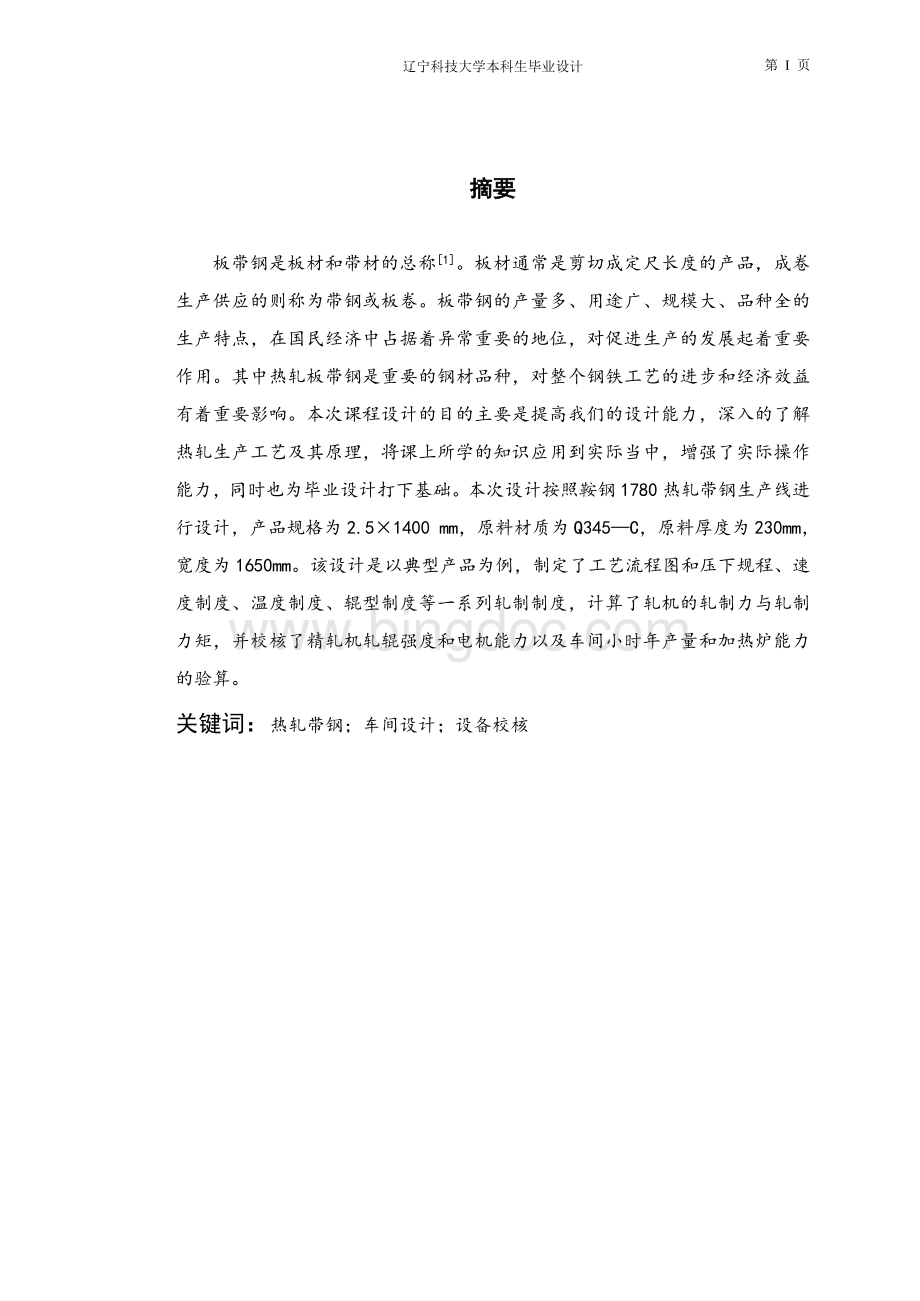
1.2.1热轧板带钢的种类、规格及用途 2
1.2.2板带产品的使用特点、生产特点及技术要求 3
1.3热轧带钢生产工艺概述 3
1.3.11700ASP工艺流程及其先进技术 3
1.3.21780工艺流程及其先进技术 4
1.4热轧工艺装备关键技术 5
1.4.1无头轧制 5
1.4.2ASR技术 6
1.4.3CVC技术[4] 7
1.4.4在线制造 9
1.4.5现代建模方法 9
1.5热轧宽带钢的发展趋势 9
2产品方案 10
2.1产品方案的编制[4] 10
2.1.1产品方案简介 10
2.1.2编制产品方案的原则及方法 10
2.1.3选择计算产品 10
2.2坯料 11
2.2.1钢种 11
2.2.2坯料规格 11
2.3产品特点 11
2.3.1产品质量标准[3] 11
2.3.2产品性能 13
2.3.3产品规格 13
2.3.4产品目标值 14
2.4产品方案和金属平衡 14
2.4.1产品方案 14
2.4.2金属平衡[4] 17
3生产工艺过程和设备的选择 19
3.11780生产工艺流程及其概述 19
3.2生产方案的选择[4] 19
第IV页
3.3工艺布置特点和设备的选择 20
3.3.1机组配置 20
3.3.2加热炉的选择 20
3.3.3侧压设备的选择 20
3.3.4粗轧机组的选择 21
3.3.5立辊轧机的选择 22
3.3.6保温装置的选择 24
3.3.7飞剪机的选择 25
3.3.8高压水除鳞设备的选择 26
3.3.7精轧机组的选择 27
3.3.10层流冷却 30
3.3.11卷取机的选择 30
4生产工艺流程图和典型产品的确定 33
4.1生产工艺流程图 33
4.2确定轧制方法 34
4.3根据产品选择原料 34
5压下规程设计 35
5.1粗轧机压下规程的制定 35
5.1.1粗轧机组各道次的压下量分配 36
5.1.2根据成品板宽确定精轧坯宽度 36
5.1.3计算粗轧机组轧制时的宽展量 37
5.1.4计算坯料轧前的膨胀宽度 38
5.1.5计算立辊各道次侧压量 38
5.2精轧机压下规程的制定 39
5.2.1精轧机组各道次的压下量分配 40
6校核咬入能力 41
7轧制时间制度 42
7.1粗轧轧制时间计算 42
7.2精轧轧制时间计算 44
7.3轧机工作图表[4] 49
7.3.1粗轧机工作图表 49
7.3.2精轧机工作图表 50
8温度制度 51
8.1粗轧时各道次的温降 51
8.2精轧温度制度 53
8.3卷取温度制度 54
9速度制度 55
9.1粗轧机速度制度 55
9.2精轧机速度制度 55
9.2.1前滑值计算 55
9.2.2精轧速度计算 57
第V页
10计算各道的平均变形速度 59
10.1粗轧各道次的平均变形速度 59
10.2精轧各道次的平均变形速度 60
11辊型制度 62
11.1辊形控制 62
12轧制力及轧制力矩的计算 65
12.1粗轧机轧制力和轧制力矩的计算 66
12.2精轧机轧制力和轧制力矩的计算 72
13轧机设备校核 78
13.1粗轧机轧辊强度校核 78
13.2精轧机轧辊强度校核 81
13.3电机能力校核[5] 86
14轧钢机产量计算 90
14.1轧钢机小时产量的计算 90
14.2轧钢机平均小时产量的计算 91
14.4加热炉生产能力的校核 94
15车间平面布置、仓库面积及起重运输 95
15.1车间平面布置原则[4] 95
15.2金属流线型式 95
15.3设备间距的确定 96
15.4仓库面积计算 99
15.4.1确定仓库面积的原则 99
15.4.2原料仓库面积的确定 100
15.4.3成品仓库面积的确定 100
16车间主要经济技术指标 102
17环境保护 104
17.1环境保护概述 104
17.2环境保护的内容与对策 104
17.2.1绿化 104
17.2.2水质处理 104
17.2.3噪音防治 105
17.2.4大气污染的防治 105
17.2.5有害废弃物的处理 106
17.2.6车间的综合利用 106
专题—热轧板带润滑技术 107
摘要 107
Abstract 108
1综述 109
1.1热轧板带润滑技术的发展及应用 109
2热轧工艺润滑的机理及作用 111
2.1热轧工艺润滑的机理 111
2.2热轧工艺润滑的作用[10] 112
第VI页
3热轧润滑的供油方法和热轧润滑油 116
3.1热轧润滑的供油方法 116
3.2热轧润滑油[11] 118
3.2.1热轧油的主要技术参数 118
3.2.2热轧工艺润滑对热轧油的性能要求 119
4热轧轧制润滑系统[12] 120
4.1润滑系统的组成 120
4.2热轧润滑的应用系统 121
4.2.1应用系统的组成 121
4.2.2应用系统的操作 122
4.3轧机上设备布置情况 123
4.4轧制润滑主要的技术参数 125
5热轧工艺润滑剂[13] 126
5.1板带钢润滑剂具备的基本功能 126
5.2对热轧润滑剂的要求 126
5.3润滑剂的分类及转移现象 127
6热轧工艺润滑的影响及存在的问题[14] 128
6.1工艺润滑对轧机控制系统的影响及措施 128
6.1.1工艺润滑对AGC功能的影响及措施 128
6.1.2工艺润滑对活套控制的影响及措施 128
6.2热轧工艺润滑存在的问题 128
结语 129
致谢 130
参考文献 131
第131页
1综述
1.1热轧板带钢发展史
板带钢是板材和带材的总称。
其中热轧板带钢轧机的发展已有80多年历史,从提高生产率和产品尺寸精度、节能技术、提高成材率和板形质量、节约建设投资、减少轧制线长度实现紧凑化轧机布置到热连轧机和连铸机的直接连接布置,热轧板带钢生产技术经历了不同的发展时期。
1.1.1国外热轧板带的发展
1960年以前建设的热带钢轧机称第一代热带钢轧机。
[2]这一时期热带钢轧机最重要的技术进步是将厚度自动控制(AGC)技术应用于精轧机,从根本上改善了供给冷轧机的原料板带钢的厚度差。
20世纪六、七十年代是热轧板带钢轧机发展的重要时期。
同时连铸技术发展成熟,促使热连轧机从最初使用钢锭到使用连铸坯。
60年代后新建的热带钢轧机很快采用了轧制过程计算机控制,这一时期新建的轧机称为第二代热带钢轧机。
1969年至1974年在日本和欧洲新建的轧机称为第三代热带钢轧机。
20世纪80年代,板带钢生产更加注重产品质量,同时对于低凸度带材需求量不断增长,这使板带钢板形控制技术成为热轧板带钢轧制技术重要课题之一。
90年代,热轧板带钢在工艺方面有重大突破,1996年日本川崎钢铁公司成功开发无头连续轧制板带钢技术,解决了在常规热连轧机上生产厚度0.8~1.2mm超薄带钢一系列技术难题。
1.1.2国内热轧板带钢的发展
我国第一套热轧宽带钢轧机始建于1957年,即鞍钢的半连续轧机,全套设备从当时苏联引进,为一套2800mm/1700mm半连续式板带轧机,既生产中厚钢板,又生产钢卷,该轧机的轧制中厚板部分于1958年7月先投产,1959年精轧机组投产,开辟了我国宽带钢卷生产历程。
就我国热带钢轧机半个世纪的发展历程来看,我国热轧宽带钢轧机主要经历了由设备简单、控制落后的半连续式轧机型;
代表当时先进水平,自动化水平较高的连续式布置;
再到具有紧凑型可逆式粗轧机,大能力定宽设备,全自动控制系统的半连续式布置轧机或代表世界先进水平的薄板坯连铸连轧带钢生产线等三个阶段。
1.2热轧板带钢产品概述
1.2.1热轧板带钢的种类、规格及用途
热轧带钢品种有:
低碳钢、中碳钢、高碳钢;
船用结构钢、管线钢、锅炉用钢、焊瓶钢、IF深冲钢、无取向硅钢、包晶钢、高强双相钢等。
[3]热轧带钢是用热轧方法生产出来的成卷交货的钢,产品尺寸及规格要求见表1.1。
表1.1 热轧带钢的尺寸规格
钢带公称厚度/mm
1.2,1.4,1.5,1.8,2.0,2.5,2.8,3.0,3.2,3.5,3.8,4.0,4.5,5.0,5.5,6.0,6.5,7.0,8.0,10.0,11.0,13.0,14.0,15.0,16.0,18.0,19.0,20.0,22.0,25.0
钢带公称宽度/mm
600,650,700,800,850,900,1000,1050,1100,1150,1200,1250,1300,1350,1400,1450,1500,1550,1600,1700,1800,1900
我国热轧钢卷的规格:
表1.2热轧钢卷规格
厚度
宽度
钢卷
内径:
外径
质量
单位宽度
1.2~25.4mm
600~
1900mm
762
mm
2150
mm
最大
43.6t
23kg/mm
热轧带钢用途:
主要用作冷轧带钢的原料,其次是作焊管坯、轻型型钢及剪切板材的原料。
或以厚规格钢卷为原料生产厚壁大直径螺旋焊管。
1.2.2板带产品的使用特点、生产特点及技术要求
板带产品的使用特点:
1)可任意剪裁、弯曲、冲压、焊接、制成各种制品构件,使用灵活方便;
2)可弯曲、焊接成各类复杂断面的型钢、钢管、大型工字钢、槽钢等结构件;
3)表面积大,故包容覆盖能力强。
4)表面质量要求高。
板带材的生产特点:
1)平辊轧出2)形状简单3)轧制压力大
技术要求:
1)尺寸要求精确2)板形要求良好3)表面要求光洁4)性能要求较高
1.3热轧带钢生产工艺概述
1.3.11700ASP工艺流程及其先进技术
(1)1700工艺流程[3]
连铸坯→步进式加热炉→高压水除鳞→R1(E1)粗轧机(带立辊)→R2(E2)粗轧机(带立辊)→热卷箱→飞剪→高压水除鳞→精轧机组→层流冷却→卷取机→检查→成品
(2)1700ASP采用的先进技术
1)国内第一套中薄板坯连铸机,采用当代最先进的奥钢联中薄板坯连铸工艺,板坯厚度范围100mm-135mm;
2)采用短流程直接热装工艺;
3)采用计算机控制的步进梁式加热炉;
4)采用先进的热卷箱技术,极大提高了带钢表面质量,均衡了带坯头尾温差,改善了带钢机械性能同卷差;
5)采用先进的滚筒飞剪,以实现带坯的头、尾自动剪切;
6)采用先进的液压AGC控制,辅之以电动AGC控制以实现对带钢的自动厚度控制;
并使用液压调辊缝偏差。
7)采用先进的正弯控制及窜辊控制,以实现对带钢的板形控制;
8)采用可实现卷取温度自动控制带钢层流式冷却装置;
9)采用全液压具有自动跳步控制技术的地下卷取机;
10)采用基础自动化(DDC)、过程控制级(SCC)、生产控制级(PCC)、生产管理级(ERP)四级计算机控制系统。
1.3.21780工艺流程及其先进技术
(1)1780工艺流程[3]
连铸坯→步进式加热炉→高压水除鳞→SP定宽压力机→()粗轧机(带立辊)→()粗轧机(带立辊)→保温罩→飞剪→高压水除鳞→E连轧前立辊→精轧机组→层流冷却→卷取机→检查→入库
(2)1780采用的先进技术
1)采用连铸坯热装工艺,可节约能源,缩短交货周期。
2)采用步进梁式加热炉,提高板坯加热质量。
3)采用板坯定宽侧压机,一次侧压量最大可达350mm,以适应板坯热装和直接热装工艺,有利于连铸与热轧轧制计划的协调,减少板坯规格和库存量。
4)粗轧机采用电动压下、液压微调及宽度自动控制(RAWC),提高带坯的厚度和宽度精调。
5)设置中间辊道保温罩,以减少温降,使带钢纵向、横向温度均匀。
6)设置E立辊轧机,进一步改善带钢边部质量,提高成材率。
7)精轧机全部采用长行程液压压下和液压AGC,并在-采用PC轧机,以保证成品带钢厚度精度和板形质量。
8)采用在线磨辊装置(ORG)和液压弯辊装置,可实现“自由轧制”,扩大单位轧制量,减少换辊次数,提高作业率。
9)精轧机采用快速换辊装置。
10)采用高效层流冷却装置。
11)采用带自动踏步控制(AJC)的全液压卷取机。
12)主传动电动机采用交流调速新技术;
主传动采用由大功率元件GTO组成的电源交换器。
13)采用基础自动化级(DDC)、过程控制级(SCC)、生产控制级(PCC)、生产管理级(ERP)四级计算机控制系统。
1.4热轧工艺装备关键技术
1.4.1无头轧制
无头轧制技术[2]是随着日益剧烈的市场竞争和高质量的产品要求而产生的,所谓无头轧制就是将加热到开轧温度的钢坯,在加热炉及粗轧机之间用移动式焊机将钢坯头尾焊接起来,实现钢坯在轧机中的连续轧制。
无头轧制的采用是为了满足生产各种热轧薄板的需要。
与常规的分批次轧制工艺相比,无头轧制是一种具有成本效益的工艺。
(1)无头轧制的特点
无头轧制是钢铁加工流程的第三次飞跃,无论对传统长、带材热连轧,还是薄板坯连铸连轧都是很有发展前途,代表了当今世界热轧带钢技术的最高水平,与传统轧制方法相比具有如下优点:
1)钢材全长以恒定速度进行轧制,减少了甩尾和迭轧,提高了带钢运行的稳定性,生产率有较大提高,可大量稳定地生产全长终轧温度和卷取温度、力学性能更均匀的产品,极大地降低了生产成本;
2)对钢材全长施加恒定张力,使钢材断面形状波动减少,钢材质量改善;
3)由于成品长度不受限制,根据交货状态要求剪切,成品率显著提高;
4)提高了润滑轧制的效果,通过润滑轧制和强制冷却轧制新品种;
5)钢品咬入次数减少,减少对轧辊冲击,解决穿带问题,有利于提高轧辊寿命。
(2)无头轧制的目的
无头轧制的目的在于解决间断轧制问题的同时超越间断轧制的限制。
其中主要有:
通过无头尾轧制解决穿带问题;
通过无非稳定轧制提高质量稳定性和成材率;
通过提高连接部位穿带速度并使间隙时间为零提高生产效率;
可生产超越过去极限轧制尺寸的超薄带钢或宽幅薄板,以及通过润滑轧制和强制冷却轧制新品种。
(3)无头轧制的原理和工艺
无头轧制工艺由薄带坯供给工序、焊接后处理工序、精轧工序和卷取工序组成。
由炼钢厂提供的板坯经粗轧后作为薄带坯。
为了将薄带坯无滞后地供给焊接装置,在粗轧机出口侧设置了三位置薄带坯卷取机。
三位置薄带坯卷取机可同时卷取和开卷,以缩短开卷的周期时间,同时可吸收粗轧和精轧时间的波动。
前一块钢轧制过程中后续薄带坯到来时,便进入焊接工序。
焊接工序在先行材和后行材同步运动的焊接装置内进行。
精轧工序设备与传统设备几乎无异,为了在轧制中变更板厚,各机架压下控制和张力控制、冷却液等的温度控制都需要更佳的响应性。
最后是卷取工序,在前带坯卷取几乎结束时剪切其尾端并高速卷入,然后急减速、停车,卸出带卷。
接着,在切断后一带坯的头部后高速进入另一台卷取机。
两台卷取机交替动作。
(4)无头轧制的效果
无头轧制的效果,可从板厚精度、温度精度和成材率等方面来考察。
在厚度命中率方面,无头轧制无论是1.2mm还是1.0mm都超过了99%。
这是因为常规轧制中由于穿带造成的板厚波动在无头轧制中大幅度降低;
在成材率方面,无头轧制提高约1%;
在精轧出口温度和卷取温度命中率方面,无头轧制两者的精度都上升了2%~3%以上。
这是因为板带的形状稳定、温度容易降低的原头部以1000m/min以上的高速穿带。
1.4.2ASR技术
无取向硅钢热轧板形控制的ASR技术可用来满足冷轧硅钢片日趋严苛的板形质量要求,ASR非对称自补偿工作辊偏摆控制功能开发与窜辊策略的实现是大型工业生产应用ASR技术的重要条件。
在分析提出ASR板形控制技术应用要求基础上,在1700热连轧机过程控制系统MAC机新增了一系列寄存器和编制、修改梯形图程序,开发了记忆功能,实现了ASR偏摆控制功能和特定窜辊策略,可适应多种宽度无取向硅钢连续编排的大工业生产方式。
ASR技术的基本原理是根据轧制过程中轧辊的磨损规律,设定特殊窜辊方式,使得工作的磨损由“U”形变为“4”形,即打开凹槽型磨损的槽箱的一个边,使轧件始终处于辊形较为平坦的区域内,打破“由宽至窄”的Coffin轧制规程约束,并结合工作辊强力弯辊保证承载辊缝形状的正常可控。
显然,ASR技术是利用辊形和窜辊的非对称性来改变工作辊的磨损,改善辊缝的非对称性。
因此,ASR技术在解决因凹槽型“U”磨损带来的凸度偏大的同时,对于有条件地实现SFR自由规程轧制、低凸度超平材轧制或扩大轧制单位具有重要意义。
1.4.3CVC技术[4]
在轧机机型确定的情况下,辊形是板形控制最直接、最活跃的因素。
自20世纪80年代开始,我国引进的多套热连轧、冷连轧机采用国外提供的轴向移位变凸度工作辊辊形,如三次连续变凸度进行板形控制。
事实证明,对辊形的特性进行分析研究并结合实际生产情况进行改进,对提高板形控制水平尤为重要。
(1)CVC轧机的类型
CVC轧机即连续可变凸度轧机,这种轧机的主要特征是工作辊设计成S形,上下工作辊外形是一样的,彼此呈1800反向配置,均可以横向移动。
当上下工作辊横移时,可得到中性凸度、正凸度和负凸度的轧辊凸度,而且使辊缝断面形状可在较大范围内无级连续调节。
CVC轧机只需一套辊型就可以满足轧制不同宽度带钢对板形调节的要求,如果它与工作辊弯辊装置相配合,更能扩大板形调节范围。
当CVC辊轴向移动距离为100^150mm时,再加上弯辊作用,辊缝调节量可达60μm左右,这是一般轧机达不到的。
CVC轧机的类型:
图1.1:
CVC轧机类型图
(a)