加压捏炼机操作规程.docx
《加压捏炼机操作规程.docx》由会员分享,可在线阅读,更多相关《加压捏炼机操作规程.docx(17页珍藏版)》请在冰点文库上搜索。
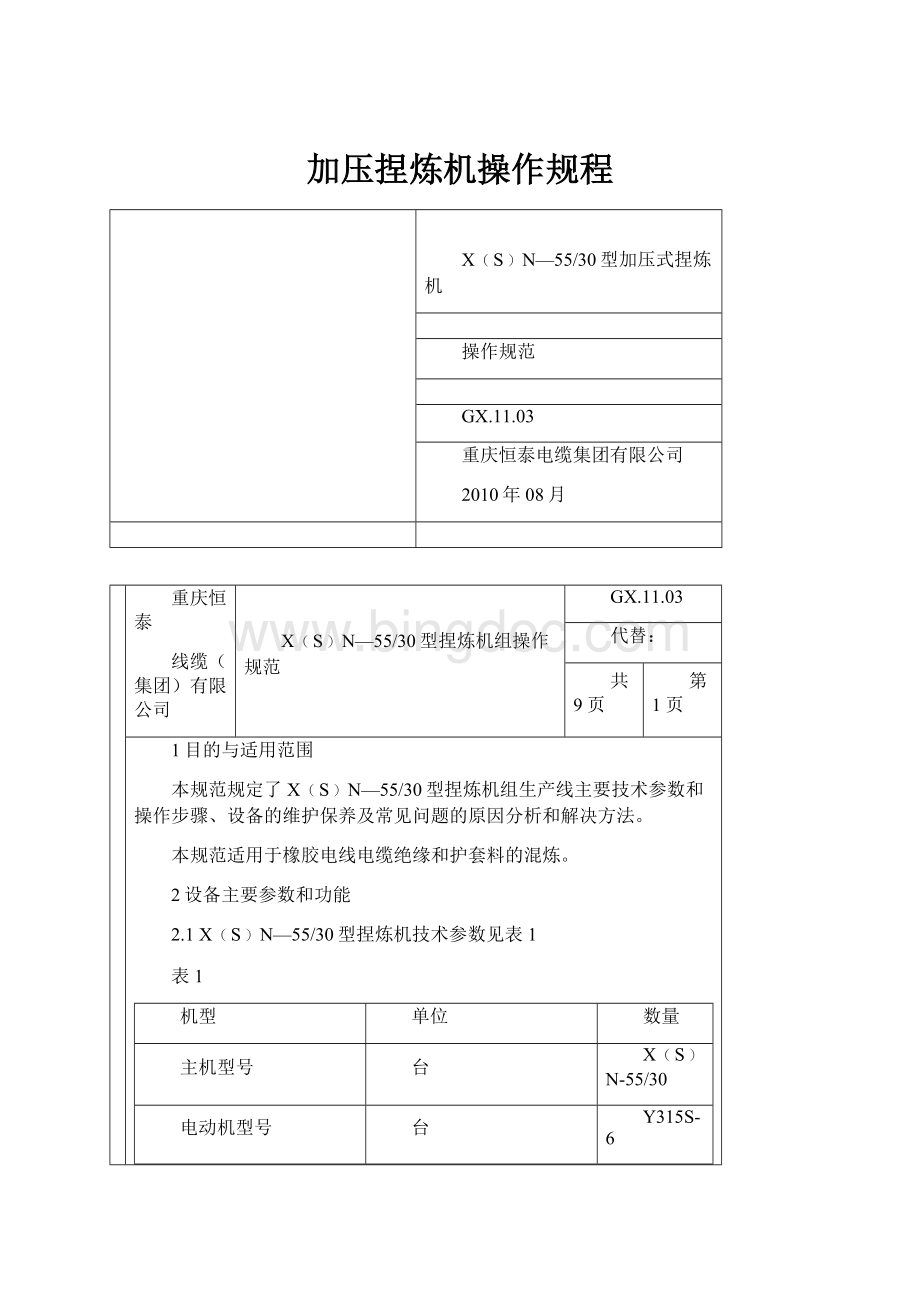
加压捏炼机操作规程
X﹙S﹚N—55/30型加压式捏炼机
操作规范
GX.11.03
重庆恒泰电缆集团有限公司
2010年08月
重庆恒泰
线缆(集团)有限公司
X﹙S﹚N—55/30型捏炼机组操作规范
GX.11.03
代替:
共9页
第1页
1目的与适用范围
本规范规定了X﹙S﹚N—55/30型捏炼机组生产线主要技术参数和操作步骤、设备的维护保养及常见问题的原因分析和解决方法。
本规范适用于橡胶电线电缆绝缘和护套料的混炼。
2设备主要参数和功能
2.1X﹙S﹚N—55/30型捏炼机技术参数见表1
表1
机型
单位
数量
主机型号
台
X﹙S﹚N-55/30
电动机型号
台
Y315S-6
主电机功率
KW
75
转速
r/min
980
电压
V
380
行星减速机型号
台
NGW112C-8
传动比
——
31.25
上顶拴对胶料的压力
MPa
0.15~0.2
压缩空气压力
MPa
0.6~0.8
压缩空气耗量
M3/min
0.3
冷却水压力﹙炼胶﹚
MPa
0.3~0.4
冷却水耗量
m3/h
10
加热用蒸汽压力﹙炼塑﹚
MPa
≤0.8
卸料方式
----
密炼室翻转140°
外形尺寸﹙长×宽×高﹚
mm
4760×1900×3250
总重
t
10
操作规范
会签
标准化
编制
审定
标记
处数
更改文件号
签字
日期
校对
批准
X﹙S﹚N—55/30型捏炼机组操作规范
GX.11.03
共9页
第2页
2.2捏炼机的工作原理;
2.2.1混炼就是在密炼机内将各种配合剂均匀的加入到橡胶中,制成混合胶的过程。
在混炼过程中,要考虑到各配合剂的性能、作用与用量。
安排加料顺序,用量少的,难分散的先加,用量多的易分散的后加。
混炼时加料的顺序对混合质量影响很大,加料顺序不当,轻则影响分散,重则导致烧焦,使胶料报废,对企业造成严重经济损失。
2.2.2混炼;可分为一段混炼与二段混炼;一般罐硫使用的是一段混炼,因为罐硫设备螺杆短需要使用热喂料所以有时是现混炼现加硫化剂、现出片,现用。
如果胶皮凉了,还必须重新混炼加热。
也有先混炼好压成大片停放,要使用时在开炼机上加硫出片。
我们目前使用的是分段混炼,就是先混炼-压片-滤橡-冷却-停放。
再重新温橡-混炼-加硫-出片-冷却-停放待用。
一般混炼好的胶料必须停放8小时以上才能二段混炼加硫效果比较好;
2.3加料顺序;
2.3.1护套;标胶+丁苯+小料—碳黑—大料+增塑剂—卸料。
2.3.2绝缘;标胶+丁苯+小料+白炭黑—大料+增塑剂—卸料。
2.3.3除了上述加料顺序之外,还有逆混法和引料法;
2.3.4逆混法又称为倒混炼法。
加料顺序与一般的加料顺序相反;
2.3.5即;:
填充—炭黑—橡胶—小料和软化剂—加压混炼—排胶;
2.3.6此法一开始就把硫化体系和促进剂以外的所有其它配合剂一起先投入密炼机内,然后再投入橡胶进行混合,可以充分利用装料容积,改善高填充炭黑的分散性。
由于所有的配合剂一次加入,上顶拴的升降次数减少了,混炼周期时间可以缩短;特别有利于填充剂含量较多、挺性较差的顺丁橡胶、乙丙橡胶的混炼。
操作时应注意装填系数和上顶拴压力尽量增加,以防胶料在密炼机内发生漂移而影响湿润分散效果。
密炼机的密封性能要好。
2.4引料法;又称为种子炼胶法,常用于塑炼胶与配合剂间湿润性较差,吃粉速度较慢的混炼。
此法就是先在密炼室内加入1.5~2.0kg预先混炼好的但没有加硫化剂的胶料,然后再加入塑炼胶和各种配合剂进行混炼。
这样可以加快吃粉能力和混炼速度。
目前橡套电缆行业都使用密闭式炼胶机作为橡胶的塑炼或混炼。
密炼机的主要组成部分有;混炼室、转子、上顶拴、下顶拴、冷却系统、密封装置、润滑系统和传动装置。
其主要工作部分为混炼室,混炼室内有不等速相对旋转的两个转子,转子断面呈椭圆形,表面有两条螺旋线状凸棱。
当旋转时,在混炼室表面和两个转子间对橡胶产生复杂的机械作用。
橡胶在混炼室内不仅受到转子的剪切力,而且转子凸棱的轴向力作用还使橡胶在轴向进行搅和与捏炼,所以混炼效果好,质量较均匀。
每种型号的密炼机制造厂家都有一定的容量规定。
2.5与开炼机相比,密炼机有下面六个特点;
2.5.1橡胶在混炼室内受到转子的强烈剪切。
2.5.2密炼机生热极大,温度高,属于高温混炼、塑炼类型。
2.5.3密炼机不能观察塑炼情况,只能凭借电流表和温度计来控制。
2.5.4操作安全,并可能使加工过程实现自动化和远距离操纵。
2.5.5混炼温度控制困难,容易引起胶料的局部焦烧。
5.5.6不适合多种颜色胶料以及胶料品种变换频繁的情况,排胶不规则,形状不规定,必须配备开炼机压片。
标记
处数
更改文件号
签字
日期
X﹙S﹚N—55/30型捏炼机组操作规范
GX.11.03
共9页
第3页
2.6装胶容量;
2.6.1装胶容量影响混炼或(塑炼)效果。
容量过小,橡胶在混炼室内打滚,不能获得很好的混炼或(塑炼)效果;容量过大,会使设备超负荷运转,容易损坏机器,故正确选择极为重要。
2.6.2密炼机的装胶容量由下例公式计算;
P=KrV(公斤)
式中;P—装胶容量(公斤);
K—填充系数,一般为0.5~0.67;
r—橡胶混炼时的比重;
V—密炼机混炼室的总容量,
3:
橡料混炼理论;
3.1橡料是由橡胶和各种配合剂组成的,过去认为这是一种粗糙的粉粒材料在橡胶中的悬浮体,现在认为橡料是由多种细粒子分散体与橡胶分散介质所组成的胶态分散体系。
但它不同于一般的分散体系,其特点如下;
3.1.1橡胶的粘度极高,在一般情况下分散体系比较稳定,配合剂粒子结聚倾向不明显。
3.1.2橡料中各组份能互相溶解,从而构成复合分散介质,如橡胶与增塑剂能互溶,硫磺常温下也可部分地溶解于橡胶。
3.1.3橡料中的细粒状配合剂在与橡胶的接触界面上产生一定的化学和物理结合,甚至硫化后仍然继续保持。
这对橡料和橡皮的性能起着重要影响。
为使细粒状配合剂能均匀地分散,并与橡胶形成稳定的胶态分散体系,要有两个条件;一是用机械作用使配合剂掺入橡胶,并在其中均匀分散;二是配合剂与橡胶接触的表面有较大的活性,以形成稳定的分散体系。
两者互相促进,表面的活性作用使机械掺合更容易进行;使机械力的分散作用发挥得更充分。
3.2橡料的混炼过程;
3.2.1粉碎;是将大块的聚集状配合剂如石蜡等,在密炼机内翻转挤压成小颗粒压向橡胶表面,以便于混入。
3.2.2吃粉;即在机械作用下使橡胶变形,将压在橡胶表面的粉状或液态配合剂混入橡胶中,使之成为致密的胶料。
这是混炼过程中的主要内容,在整个过程中占相当多的时间,甚至延续到混炼最后。
3.2.3分散;将混入的配合剂通过机械剪切作用被搓开逐渐变小,并进一步由表面层均匀分散。
分散主要取决于混炼时间的剪切应力,为此希望剪切应力要高些,也就是橡料塑性低时对分散比较有利。
3.2.4翻炼;目的是提高加工均匀性,主要取决于剪切变形,剪切变形大,橡料容易均匀。
3.2.5增加塑性;这是混炼中的必然过程,由于橡胶分子的断链而使塑性增大,对下道工序加工的影响较大。
但提高塑性主要是塑炼的任务,但我们是用的标胶无需塑炼,这就要求在混炼时必须要混炼到位,否则塑性肯定不够此处跟大家强调一下。
其实以上各个阶段是一个混炼周期,在混炼周期中实际上都是相互交叉进行的,在一个混炼周期中,橡料的门尼粘度、温度、配合剂在胶中的分散程度以及设备电机的输入功率等都起着关键的作用。
标记
处数
更改文件号
签字
日期
X﹙S﹚N—55/30型捏炼机组操作规范
GX.11.03
共9页
第4页
3.3混炼时橡胶和配合剂间的相互作用;
3.3.1配合剂的表面性质各不相同,对橡胶介质的活性也不一样。
根据其表面特性,配合剂可分为二类,一类是亲水性配合剂,如碳酸钙、陶土、氧化镁、氧化锌等,这类配合剂与橡胶的作用活性较小,不易为橡胶所湿润,因此不易均匀分散;另一类为疏水性配合剂,如各种炭黑。
这类配合剂与橡胶的作用活性较大,易为橡胶所湿润,工艺性能良好。
亲水性配合剂可应用表面活性剂改性,使其能为橡胶所湿润,易于分散和提高对橡胶的补强效果。
常用的表面活性剂有硬脂酸,某些树脂和木质素等。
3.3.2在混炼过程中,当聚集状的填料粒子一旦与橡胶分子结合,在剪切力作用下粒子聚集体被搓开,填料粒子产生了新的表面又可与另外的橡胶分子结合,从而使聚集体不但变小而终于达到良好的分散。
活性填充粒子表面结合了橡胶分子或为不溶于橡胶剂的结合橡胶,这种结合有利于填料的分散,并使分散体系稳定。
3.3.3混炼初期不可采用高温,否则易生成大的填料聚集体与多量橡胶结合的凝胶粒子(低结构炭黑较易生成凝胶),难以进一步分散。
比较理想的是,在混炼初期填料与橡胶只有有限的结合而具有高的剪切力,当填料分散后再升高温度以帮助形成结合橡胶。
混炼后的橡料在存放过程中,这种结合还会继续进行。
因此,如果没有适当的稳定剂或较大的表面结合力时,橡胶中细分散的粒子有互相结聚而变大的趋势。
由于橡胶粘度极高,这种结聚现象一般速度很慢而不显著。
但当橡料粘度降低到一定程度时(如橡料在琉化时),结聚作用会加剧,从而使橡皮性能显著下降。
可见提高橡料的稳定性十分重要。
3.4上顶拴压力的控制;
3.4.1上顶拴在混炼室上部,由压缩空气操纵上升下压,,同时可对混炼室内的橡料产生所需要的压力,提高混炼效果。
加料口也是由压缩空气操纵打开和关闭。
下顶拴在混炼室下部,也由压缩空气操纵打开和关闭卸料口,混炼室的两侧由密封装置封闭
3.4.2密炼机上顶拴的作用是将胶料控制在密炼室内,对胶料施加压力防止胶料在室壁和转子表面上打滚,限制和避免加料口处出现胶料停滞现象。
混炼时,上顶拴必须对胶料施加足够的压力,压力不足,上顶拴出现浮动,胶料不能压紧,混炼效果降低,混炼不均匀;同时,加料口处容易形成死角,死角处的胶料得不到混炼。
此外,压力增加,除了能够增加装胶量、减少密炼室内的非填充空间、提高填充程度之外,还能够提高胶料的剪切作用,对胶料的捏炼和配合剂的分散非常有利。
混炼速度加快,混炼时间缩短,混炼效率得到提高。
3.4.3压力不能过大,压力过大,,胶料既得不到良好的混炼,也不会使混炼时间缩短;因压力过大胶料生热快,密炼机内的温度不容易控制,混炼质量没有保障;功率消耗会增大。
上顶拴压力的确定是以胶料填满混炼室为标准,目前一般情况上顶拴的压力在0.3~0.6MPa为宜。
3.4.5在实际操作中,要特别注意哪些密度较小的粉料投入后,不能立即施加压力,而是将上顶拴慢慢放下,经过一定时间后,再施加压力。
假若开始加压,粉剂容易飞扬和挤压成块,影响混合分散质量;甚至还会由上顶拴将胶料挤出加料口,出现卡住现象,影响混炼操作。
3.5混炼温度;胶料在密炼室内,随着各组份料的投入,温度不断升高。
慢速密炼机的排胶温度可高达110度;快速密炼机的排胶温度更高,达到130度以上。
虽然混炼温度高有利于胶料的塑性流动与变形,有利于对粉状配合剂粒子表面的湿润,吃粉快。
但是混炼温度过高,胶料变软机械剪切作用降低,也不利于配合剂的分散;橡胶分子链的热氧化裂变加剧,降低了胶料的物理机械性能;橡胶和炭黑之间产生过多的化学结合而产生过多的凝胶,可塑性降低,胶料表面粗糙,给下面的加工工序带来困难。
因此需要对转子进行冷却,用冷却水将多余的热量排出。
但为了防止冷却温度过低,容易出现胶料被压散不成整体,对胶料的捏炼不利;不容易操作;会使密炼机超负荷运行等。
必须把混炼温度控制在适宜的范围内,才是保证胶料混炼质量的重要因素。
由于混炼时密炼机内温度不但变化,随着配合剂的加入和混炼时间的延长,温度不但上升,所以混炼时必须注意温度自动测量记录仪显示的温度、混炼时间、冷却水流量。
卸料时温度显示不能高于110度。
加硫时温度不能高于80度。
。
标记
处数
更改文件号
签字
日期
X﹙S﹚N—55/30型捏炼机组操作规范
GX.11.03
共9页
共5页
3.6混炼时间;混炼时间与设备条件、工艺规程、操作水平等都有关系;混炼时间短,则配合剂分散不好或未完全混合,塑性过低。
混炼时间过长,则生产量低,容易造成过炼而影响成品电缆的性能,所以每次加料混炼的时间要经过实际侧量来制定。
一般每车胶料混炼的时间约为12-15分钟左右。
加硫时间为5~8分钟左右。
当然胶种不同混炼时间也不一样,以实际操作为准。
4:
生产前的准备工作:
4.1捏炼机操作工要进行全面培训,了解设备工作原理,熟悉机器的性能和操作方法,并严格遵守安全操作规程。
4.2检查捏炼机机组及其附属设备和仪表等是否正常完好,水冷却系统、气源是否畅通。
4.3开机前应将工作场地清扫干净,拆除与之无关的工具及设备。
4.4检查机械运转情况,要求运转平稳,无异常声音,无异常震动。
密炼室内及转子是否干净,不得有异物存在。
4.5按表﹙2﹚给各个部位加注符合规定的润滑油﹙脂﹚。
4.6准备好各种必备的工具。
5:
生产中的检查事项:
5.1负荷时行星齿轮减速机应运转平稳,无异常震动和周期性噪音,翻转机构应转动平稳。
5.2转子密封装置是否完好,在工作中只容许有少量粉状物漏出,不得有团状或块状物料泄漏。
5.3转子轴承温度≤40℃,转子轴承最高温度≤70℃
5.4行星减速机轴承温度≤40℃,行星减速机轴承最高温度≤70℃。
6:
捏炼胶皮质量要求和自检项目:
6.1加料顺序严格按工艺进行,严禁乱加、多加、少加。
6.2混炼温度:
混炼时温度天然丁苯在110℃左右、氯化聚乙烯和三元乙丙在120℃~130℃,加硫时温度在80℃以下。
6.3混炼时间:
混炼约为12-15分钟,加硫时间约为5~8分钟。
冷机时间长一些,热机时间短一些。
6.4根据设备的新旧程度、胶料比重加减每车胶料的重量。
6.5混炼时密炼室口要多打扫几次。
6.6卸料前发现有粉状物因继续混炼。
6.7换胶种或换颜色时密炼室与顶栓要打扫干净。
6.8如果混炼时温度超过工艺温度因停机加大冷却水流量等温度达到要求再进行混炼。
6.9卸料时密炼室须翻转1400等料卸完后再复位。
标记
处数
更改文件号
签字
日期
X﹙S﹚N—55/30型捏炼机组操作规范
GX.11.03
共9页
第6页
7:
停车交接班:
7.1关掉应关的各个电气开关和冷却水开关,擦拭设备,地面打扫清洁。
7.2填写历史记录。
8:
设备的维护和保养:
8.1检查各连接螺栓是否有松动情况,顶栓上下是否灵。
8.2检查压料装置和翻转卸料机构其运行应灵活可靠,不得有卡阻现象。
8.3经常检查上顶栓气缸、加料口门气缸活塞杆密封性能,如发现泄漏应及时更换密封圈。
8.4经常检查通水软管,如有破裂应及时更换。
8.5经常检查转子密封装置的密封情况,在正常情况下,允许有少量的物料泄漏,若物料大量泄漏,应重新调紧密封装置的弹簧压力,使密封圈受力均匀一致,但不能将弹簧压死,若调整后仍然漏料严重,则应及时拆检和清洗密封圈,若发现损坏应进行更换。
8.6混炼室向前翻转1400时,将限位开关提前断电,以混炼室不接触前面的支撑座为宜﹙距离约为5~10mm﹚.
8.7按表﹙2﹚给各个部位加注符合规定的润滑油﹙脂﹚。
表2
序号
润滑部位
润滑点数
供油方式
润滑油牌号
加油周期
A
支承架
2
压力油嘴
钙基润滑脂ZGN-1
5天一次
﹙注1﹚
B
转子轴承
4
压力油嘴
钙基润滑脂ZGN-2
每月一次
C
导向杆
2
人工加油
钙基润滑脂ZGN-2
5天一次
D
速比齿轮箱
1
油浸润滑
齿轮油冬季N68、夏季N100
半年换一次
E
行星齿轮减速器
1
油浸润滑
齿轮油冬季N68、夏季N100
第一次250h换
以后2000h换一次
F
液压系统油箱
1
人工加油
机械油冬季N32、夏季N46
保持油标油位
G
油雾器
1
人工加油
机械油N32
保持油标油位
标记
处数
更改文件号
签字
日期
X﹙S﹚N—55/30型捏炼机组操作规范
GX.11.03
共9页
共7页
9安全生产操作注意事项
9.1捏炼机操作一定要注意安全,严禁疲劳工作。
9.2开机前仔细检查安全保险、电源、水源。
9.3开机前准备好口罩、手套等防护用品,袖口、衣扣扣好,机器运转时,操作工的头、手及持在手中的物件必须始终远离运转中的转子,不能置于密炼室加料口的上方。
9.4严格按工艺操作规程操作,所生产的胶料能满足工艺性能要求。
9.5根据胶料品种的要求对转子进行加减冷却水。
9.6合理控制混炼温度、时间,对操作不挡而产生胶皮的质量问题负责。
9.7对操作中产生胶料质量问题的原因进行分析,采取纠正或预防措施。
9.8原材料或半成品胶皮不能接触地面,以免影响胶皮质量。
9.9严禁吸烟、窜岗、遛岗、睡岗、喝酒上岗,对因上述原因造成的损失负责。
9.10负责在换胶皮品种或换颜色时保证其颜色纯度。
9.11对所使用的设备进行日保养、维护。
9.12操作人员积极参加公司各方面的培训,开动脑筋为公司节能降耗提出合理化建议。
9.13设备外表面应保持清洁,若有物料应及时用刷子清扫干净﹙不能直接用手清扫﹚搞好现场6S管理。
9.14机器维修时,必须停机并切断电源和气源,若手及持在手中的物件须伸入密炼室或置于上顶栓、加料门下面时必须用结实的钢绳将上定拴和加料门扎牢在立柱上﹙或采取其它措施﹚,以防止上顶栓、加料门下落。
9.15卸料时如果胶料粘转子,不能用手拉,让设备多转一下,还不行停机取出,检查粘转子的原因,调整配方或操作方法。
9.16下班前整理好自己的工具,关掉电源、水源、气源。
标记
处数
更改文件号
签字
日期
XK—550型开炼机组操作规范
GX.11.03
共9页
第8页
10质量问题的产生原因与解决方法见表3:
表3
序号
质量问题的类型
产生原因
解决方法
1
表面不光滑、粗糙
1混炼时间短。
2混炼温度低。
3增塑剂或含胶量低。
1调整混炼时间,使填充于橡胶间充分混合均匀。
2温度低使石蜡等固体增塑剂没有溶化,特别是每天的第一车。
3增塑剂比例过少或含胶量低也会出现表面不光滑、粗糙等现象,合理调整配方结构。
2
产品表面有杂质或表面有熟胶颗粒断面有粉孔
1所使用的填充料内有杂质,胶皮在滤橡时滤网破了不知道,混炼、出片时胶料搞到地下导致有沙子等杂物混入胶料中。
2胶料焦烧时间太短,胶皮早期硫化。
3出片时冷却不到位,造成整筐胶中间不能散热而熟胶。
4没有处理的有熟胶的机头胶混入好胶中。
5捏炼机混炼或加硫温度太高。
6混炼时间、温度、配方不能满足工艺要求。
7粉状配合剂受潮,导致胶皮水分含量大分散困难。
1对所使用的各种填充料进行检查,发现有杂质或手感有粗颗粒的不能用,退回。
滤橡时发现滤网破后滤过的胶皮,必须重新过滤。
在所有操作过程中原胶、半成品胶料不能搞到地上弄脏,粉状配合剂撒在地上不能使用报废。
2适当调低硫化剂与促进剂的用量。
3出片时注意胶皮温度,如果发现胶皮过热,把每筐胶少放一些摊开使其自然冷却以免使胶皮烧焦。
4对机头胶进行分类保管,能使用的胶料必须在开炼机上加少量防焦剂与硬脂酸处理后才能使用。
5捏炼机混炼或加硫温度要根据不同的胶种合理控制机身温度。
6合理控制混炼时间、温度,配方要按不同的季节调整。
7如果没有烘干设备,发现受潮的粉状配合剂一例不能使用。
标记
处数
更改文件号
签字
日期
X﹙S﹚N—55/30型捏炼机组操作规范
GX.11.03
共9页
第9页
表3
序号
质量问题的类型
产生原因
解决方法
3
胶皮塑性高或低或不均匀
1增塑剂量大或混炼时温度太高。
2增塑剂比例少混炼温度低或开炼机薄通三角包没到位。
3混炼时间太长或太短。
1不能平凡更换增塑剂用量,机温控制在工艺范围内。
2增塑剂比例合理,如果刚开始辊筒温度低时辊距打小一点多打几个三角包。
3提高操作工的质量意识,参照工艺对不同的胶料、不同的温度选择不同的混炼时间。
4
胶皮使用时欠硫、过硫或硫化不均
1硫化体系与硫化促进剂不足或开机时气压低、线速度太快。
2硫化体系与硫化促进剂过多或线速度太慢。
3混炼、压片不到位。
1发现欠硫现象提高气压,降低线速度,还不行胶皮退从新调整硫化体系与硫化促进剂。
2发现过硫现象降低气压,加快线速度。
3混炼、压片严格按工艺要求操作,每天的第一车要延长混炼、压片时间。
5
绝缘线芯或电焊机线导体发黑
1导体进汽、水。
2线速度太慢。
3导体本身氧化严重。
4所使用的硫化体系不对或使用了硬脂酸。
1生产时连接好生产与牵引线胶皮预防进汽、水。
2加快线速度一般在15m/分钟。
3保管好导体避免导体氧化。
4严禁使用硫磺或秋兰姆系列硫化体系,硬脂酸也会导致导体发黑。
6
绝缘线芯火花试验电压击穿点多
1绝缘胶皮硫化不足,造成绝缘线芯起泡、压扁、炸口。
2胶皮有杂质。
3绝缘线芯表面划破、刮伤。
4绝缘胶皮偏心或绝缘外径太小,绝缘胶皮太簿。
1改进硫化体系使绝缘胶皮充分硫化性能达到标准要求。
2加强滤橡管理,并且在加硫、出片过程中保持胶料的清洁,无杂质混入。
3把模套拆下清除模套内的杂质或熟胶。
4重新调整偏心使绝缘厚度能达到标准要求。
7
绝缘线芯或成品护套压扁
1硫化不足。
2收线过紧或交叉压线。
1减慢挤出速度或提高蒸汽压力,调整胶料的硫化体系,减少正硫化时间,加强硫化程度。
2适当减小收线张力,排线平整,不能交叉压线。
标