造渣制度.docx
《造渣制度.docx》由会员分享,可在线阅读,更多相关《造渣制度.docx(19页珍藏版)》请在冰点文库上搜索。
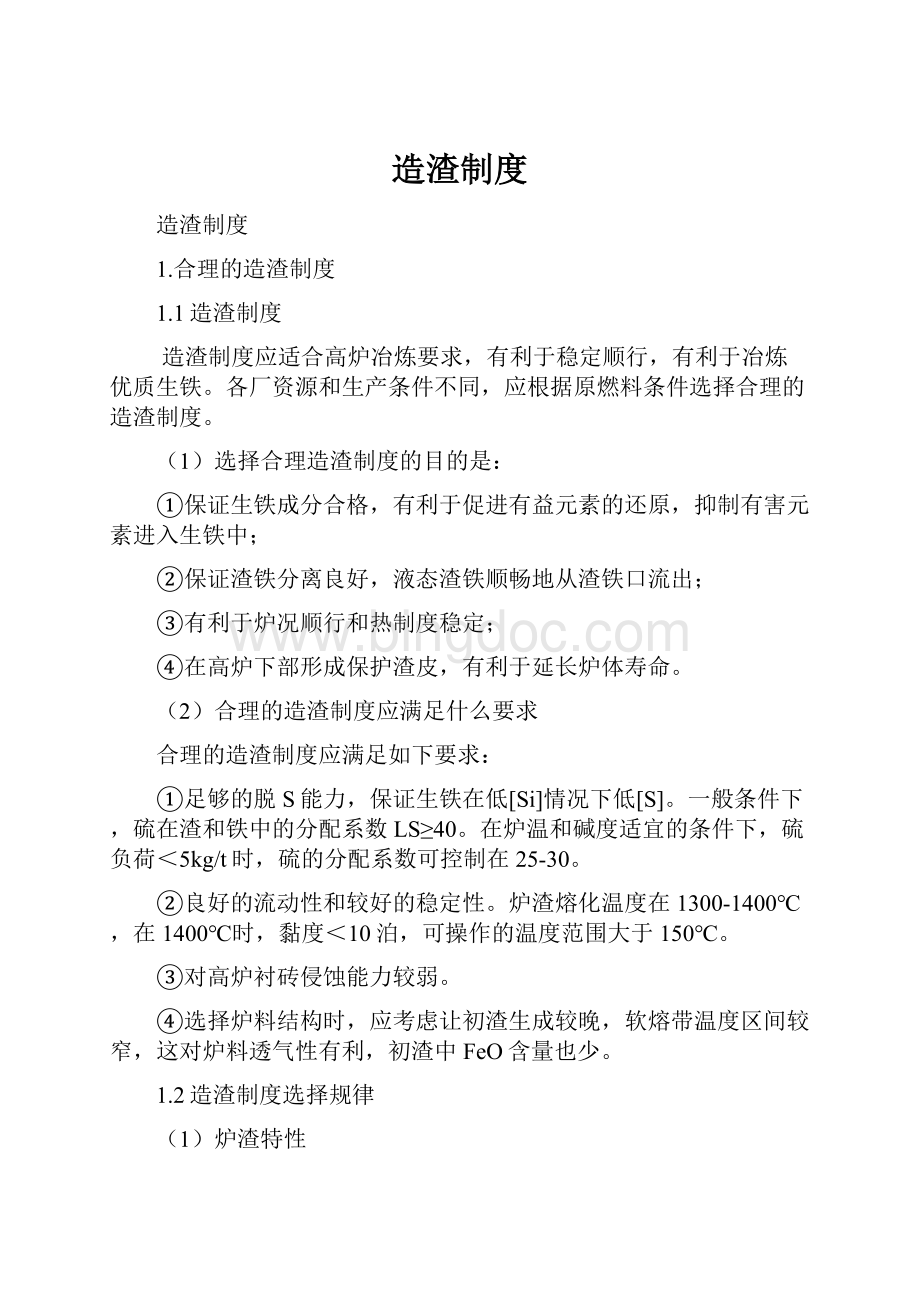
造渣制度
造渣制度
1.合理的造渣制度
1.1造渣制度
造渣制度应适合高炉冶炼要求,有利于稳定顺行,有利于冶炼优质生铁。
各厂资源和生产条件不同,应根据原燃料条件选择合理的造渣制度。
(1)选择合理造渣制度的目的是:
①保证生铁成分合格,有利于促进有益元素的还原,抑制有害元素进入生铁中;
②保证渣铁分离良好,液态渣铁顺畅地从渣铁口流出;
③有利于炉况顺行和热制度稳定;
④在高炉下部形成保护渣皮,有利于延长炉体寿命。
(2)合理的造渣制度应满足什么要求
合理的造渣制度应满足如下要求:
①足够的脱S能力,保证生铁在低[Si]情况下低[S]。
一般条件下,硫在渣和铁中的分配系数LS≥40。
在炉温和碱度适宜的条件下,硫负荷<5kg/t时,硫的分配系数可控制在25-30。
②良好的流动性和较好的稳定性。
炉渣熔化温度在1300-1400℃,在1400℃时,黏度<10泊,可操作的温度范围大于150℃。
③对高炉衬砖侵蚀能力较弱。
④选择炉料结构时,应考虑让初渣生成较晚,软熔带温度区间较窄,这对炉料透气性有利,初渣中FeO含量也少。
1.2造渣制度选择规律
(1)炉渣特性
在高温下有良好的流动性和稳定性及较强的脱硫能力,且侵蚀性较弱的炉渣,称为一般炉渣或普通炉渣。
我国宝钢、鞍钢、武钢、首钢、济钢等大中型钢铁厂的炉渣都属于一般炉渣。
这种炉渣在碱度小于1.2,大部分的熔化性温度较低,具有良好的流动性和稳定性,脱硫效果好。
据统计,冶炼制钢铁时,二元碱度CaO/SiO2在1.05-1.15范围,三元碱度CaO+Mgo/SiO2在1.2-1.32范围。
国外日本、德国渣量小,硫负荷5-6kg/t,二元碱度大于1.2,三元碱度1.45。
特殊炉渣一般都是由于特殊铁原料决定的。
如酒泉钢铁厂的含钡炉渣,矿石含BaSO4、BaSO3,以BaO形态进入炉渣。
包头钢铁厂的含氟渣,熔化温度比普通炉渣低100-200℃。
攀钢有高钛渣,重钢有低钛渣。
(2)根据炉渣特性,造渣制度应遵循如下规律:
①若渣量少,AL2O3偏高时,二元碱度应高些,一般为1.15-1.2。
相反,渣量大,AL2O3偏低时,二元碱度应低些,一般为1.05-1.10。
②若渣量少,原燃料硫负荷偏高时,炉渣碱度应高些,一般为1.20-1.25。
相反,渣量大,硫负荷低时,炉渣碱度应低些,一般为1.0-1.05。
③小高炉较大高炉在相同条件下炉缸温度偏低,所以小高炉炉渣碱度可相对高些。
④生铁含【Si】高时,碱度应适当降低,反之则适当提高。
⑤渣中MgO主要功能是改善炉渣流动性和稳定性,最佳含量7-10%。
渣中AL2O3偏高时,MgO最高含量不宜超过12%。
1.3利用不同炉渣性能满足生产需要
生产中会遇到原燃料条件变化、高炉操作障碍、铁种改变等实际情况,通常是利用改变炉渣成分来满足下列需要。
(1)脱除有害杂质
①当矿石含碱金属(K、Na)较高时,为了减少碱金属在炉内循环富集的危害,需要选择熔化温度较低的酸性炉渣。
②若炉料中硫负荷大,需要适当提高碱度,以利脱硫。
③单纯增加CaO提高碱度,会造成炉渣黏度增加,致使渣中硫的扩散速度降低,不但不能很好地脱硫,还会影响高炉顺行;特别是渣中MgO含量低时,增加CaO含量对黏度的炉渣性能影响更大。
因此应适当增加渣中MgO含量,提高三元碱度以增加脱硫能力。
虽然从热力学观点看,MgO脱硫能力不如CaO,但在一定范围内,MgO能够改善脱硫的动力学条件,因而脱硫效果很好。
首钢曾经将渣中MgO含量在4.32-16.76%范围进行试验测定,得到MgO与CaO脱硫能力的比值是0.89-1.15,结果表明:
MgO以7-12%为好。
(2)处理炉缸堆积
高炉冶炼中会遇到炉缸不同程度的堆积现象,因炉渣碱度过高而炉缸产生堆积时,可用比正常碱度低的酸性炉渣来清洗。
若高炉下部有黏结或炉缸堆积较严重时,可以采用萤石洗炉方法,降低炉渣黏度和熔化温度,清洗下部黏结物。
济钢350高炉使用集中数批酸性球团的方法处理炉缸堆积,效果较好。
(3)抑制或促进硅、锰还原
抑制或促进硅、锰还原,通常是根据冶炼不同铁种的需要,同样是利用炉渣成分的改变来实现。
当冶炼硅铁、铸造铁时,需要促进硅的还原,应该选择较低的炉渣碱度;
当冶炼制钢铁时,既要控制硅的还原,又要较高的铁水温度,应该选择较高的炉渣碱度;
若冶炼锰铁,因MnO还原困难,并需要消耗较大热量,则需提高炉渣碱度,利用CaO置换MnO,对锰还原有利并可以降低热量消耗。
各类铁种对碱度的控制范围
铁种
硅铁
铸造铁
炼钢铁
锰铁
CaO/SiO2
0.6-0.9
0.8-1.05
1.05-1.2
1.2-1.7
2.高炉内的造渣过程
2.1炉渣的区分
现代高炉多用熔剂性熟料冶炼,一般不直接向高炉加入熔剂。
由于在烧结(或球团)生产过程中熔剂已先矿化成渣,大大改善了高炉内的造渣过程。
高炉造渣过程是伴随着炉料的加热和还原而产生的重要过程——物态变化和物理化学过程。
高炉渣从开始形成到最后排出,经历了一段相复杂的过程。
开始形成的渣称为“初成渣”,最后排出炉外的渣称“末渣”,或称“终渣”。
从初成渣到末渣之间,其化学成分和物理性质处于不断变化过程的渣称“中间渣”。
2.2初成渣的生成
初渣生成包括固相反应、软化、熔融、滴落几个阶段。
固相反应在高炉上部的块状带发生游离水的蒸发、结晶水或菱铁矿的分解,矿石产生间接还原。
同时,在这个区域发生各物质的固相反应,形成部分低熔点化合物。
固相反应主要是在脉石与熔剂之间或脉石与铁氧化物之间进行。
当用生矿冶炼时其固相反应是在矿块内部,SiO2与FeO之间进行,形成低熔点化合物,还在矿块表面脉石(或铁的氧化物)与粘附的粉状CaO之间进行,形成CaO-Fe2O3等类型的低熔点化合物。
当高炉使用自熔性烧结矿(或自熔性球团矿)时,固相反应主要在矿块内部脉石之间进行。
矿石的软化(在软熔带)由于固相反应形成低熔点化合物,在进一步加热时开始软化。
同时由于液相的出现改善了矿石与熔剂间的接触条件,继续下降和升温,液相不断增加,最终软化熔融,进而成流动状态。
矿石的软化到熔融流动是造渣过程中对高炉行程影响较大的一个环节。
各种不同的矿石具有不同的软化性能。
矿石的软化性能表现在两个方面:
一是开始软化的温度,二是软化的温度区间。
很明显,矿石开始软化的温度愈低,则高炉内液相初渣出现得愈早;软化温度区间愈大,则增大阻力的塑性料层愈厚。
一般说矿石的开始软化温度波动在700-1200℃之间。
2.3终渣形成
中间渣经过风口区域后,其成分与性能再一次的变化(碱度与黏度降低)后趋于稳定。
此外在风口区被氧化的部分铁及其它元素将在炉缸中重新还原进入铁水,使渣中FeO含量有所降低。
当铁流或铁滴穿过渣层和渣铁界面进行脱硫反应后,渣中CaS将有增加。
最后从不同部位和不同时间集聚到炉缸的炉渣相互混匀,形成成分和性质稳定的终渣,定期排出炉外。
通常所指的高炉渣均系指终渣。
终渣对控制生铁的成分,保证生铁的质量有重要影响。
终渣的成分是根据冶炼条件经过配料计算确定的。
在生产中若发现不当,可通过配料调整,使其达到适宜成分。
2.4炉渣在高炉内的变化
(1)不同区域
铁矿石在下降过程中,受上升煤气的加热,温度不断升高,其物态也不断变化,使高炉内形成不同的区域。
①在块状带内,发生游离水蒸发、结晶水分解,矿石的间接还原度达30-40%,固相反应形成低熔点化合物是造渣过程的开始。
随着温度升高,低熔点化合物中呈现少量液相,开始软化黏结。
②在软熔带内形成的初渣,特点是FeO、MnO含量高,碱度偏低,相当于天然矿石和酸性球团矿的碱度,成分不均匀。
③在滴落带,从软熔带滴下的中间渣在穿越滴落带时成分变化很大,FeO、MnO因被还原而降低,熔剂或高碱度烧结矿中的CaO进入渣中使碱度升高,甚至超过终渣的碱度。
④在燃烧带,中间渣穿过焦柱进入炉缸积聚,当接近风口中心线时吸收煤气上升的焦炭灰分,这时候的碱度逐步降低。
⑤在炉缸渣铁贮存区内,炉渣完成渣铁反应,吸收脱硫产生的CaS和Si氧化的SiO2等元素,最后成为终渣。
(2)主要成分
再从几项化学成分变化来看:
①初渣在炉腹以上FeO、MnO含量达到5%左右,到炉腹下部其含量达到8%,说明这一带进行着大量直接还原。
②Al2O3在初渣中含量只有3-5%,下降过程中尤其到风口以后有所提高,说明燃料灰分中Al2O3参与造渣。
③MgO在初渣中只有5-6%,到炉缸之前达11%,接近终渣成分,说明MgO是逐渐参与造渣的。
④初渣中碱金属氧化物较多,到炉缸时则降低。
这是因为在风口高温区时有部分被挥发,但在炉子中上部则存在循环富集。
(3)炉缸反应
①炉腹中部以上,生铁含C不超过0.5%,大量渗碳反应是在高温区及炉缸附近进行的。
②风口部位的生铁含S超出产品铁8倍以上,即大量的脱硫反应是在炉缸进行的。
③生铁中Si、Mn含量在进入炉缸前均高于成品铁,说明风口带出现再氧化过程。
3.炉渣的性质及其影响因素
3.1炉渣的来源
炉渣的成份来自以下几个方面:
(1)矿石中的脉石;
(2)焦炭灰分和煤粉灰分;
(3)熔剂氧化物;
(4)被侵蚀的炉衬;
初渣中含有大量矿石中的氧化物,如FeO、MnO等。
对炉渣性质起决定性作用的是前三项。
脉石和灰分的主要成分是SiO2和AL2O3,称酸性氧化物;熔剂氧化物主要成分是CaO和MgO,称碱性氧化物。
这些氧化物单独存在时,熔点都很高。
SiO2熔点1713℃,AL2O3熔点2050℃,CaO熔点2570℃,MgO熔点2800℃。
炉渣的主要成分就是上述4种氧化物,这么高的熔点,在高炉条件下根本不能熔化。
只有它们之间互相作用形成低熔点化合物,才能熔化成具有良好流动性的熔渣。
3.2炉渣软熔特性对冶炼的影响
炉渣的软熔特性与矿石的软化特性有关,其对高炉冶炼的影响是,矿石软化温度越低,初渣出现的越早,软熔带位置越高;软化区间越大,软熔带熔着层越宽,对煤气流的阻力越大,对高炉顺行不利。
①炉渣熔化性对高炉冶炼的影响很大。
炉渣熔化之后能自由流动的温度叫熔化性温度。
在选择炉渣时究竟是难熔的炉渣有利还是易熔渣有利,这需要据不同情况具体分析,具体对待。
难熔炉渣开始软熔温度较高,从软熔到熔化的范围较小,则在高炉内软熔带的位置低,软熔层薄,有利高炉顺行。
②炉渣黏度直接关系到炉渣流动性,而炉渣流动性又直接影响高炉顺行和生铁的质量等指标。
它是高炉工作者最关心的炉渣性能指标。
炉渣要有良好的流动性,并能自由地与铁水分离。
炉渣黏度是流动性的倒数,炉渣自由流动的最大黏度为2~2.5Pas。
③炉渣稳定性是指炉渣的化学成分或外界温度波动时,对炉渣物理性能影响的程度。
若炉渣的化学成分波动后对炉渣物理性能影响不大,此渣具有良好的化学稳定性。
同理,如外界温度波动对其炉渣物理性能影响不大,称此渣具有良好的热稳定性。
生产过程中由于原料条件和操作制度常有波动,以及设备故障等都会使炉渣化学成分或炉内温度波动,炉渣应具有更好的稳定性。
④炉渣的表面张力对炼钢过程有较大实用意义,在高炉操作中,以往研究不够,因为一般高炉渣的表面张力尚未小到对高炉冶炼带来不利影响的程度。
最近研究认为,表面张力小的炉渣,流动性好,有利炉渣脱硫。
3.3影响炉渣黏度的因素及其改善方法
(1)影响炉渣黏度的因素
影响炉渣黏度的因素比较多,主要有:
①渣温不足;②渣碱度升高;③炉缸堆积;④有些成分影响炉渣黏度,MgO、MnO、FeO等能降低炉渣黏度,Al2O3、CaO等有时会升高炉渣黏度。
炉渣中MgO含量提高后,炉渣黏度受二元碱度的影响将明显减少。
碱性炉渣为短渣,炉渣过碱时流动性差,会使风口表现为出现挂渣。
酸性炉渣为长渣,它随着温度的下降最终会影响脱硫效率下降。
(2)改善炉渣流动性
根据生产的铁种和原料条件,确定合理的炉渣成分是十分关键的。
有条件的地方使用部分白云石做熔剂,提高渣中MgO含量以改善流动性;MnO虽然能改善炉渣流动性,但正常情况下外加锰矿,经济上损失太大,Mn进入炉渣里也是一种浪费。
其次保证充足的炉缸热量,渣水物理热充足,是提高渣水流动性,减少渣中带铁的重要条件。
4.炉渣脱硫反应
硫在铁水和炉渣中以元素S、FeS、MnS、MgS、CaS等形态存在,其稳定程度依次是后者大于前者。
其中MgS和CaS只能溶于渣中,MnS少量溶于铁中,大量溶于渣中,FeS即溶于铁中,也溶于渣中。
炉渣的脱硫作用就是渣中的CaO、MgO等碱性氧化物与生铁中的硫反应生成只溶于渣中的稳定化合物CaS、MgS等,从而减少生铁中的硫。
按分子论的观点,渣铁间的脱硫反应是以如下形式进行的:
[FeS]→←(FeS)
(FeS)+(CaO)=(CaS)+(FeO)
(FeO)+C=[Fe]+CO↑
即渣铁界面上生铁中的[FeS]向渣面扩散并溶入渣中,然后与渣中的(CaO)作用生成CaS和FeO,由于CaS只溶于渣而不溶于铁,FeO则被固体碳还原生成CO离开反应界面,生成Fe进入生铁中,从而脱硫反应可以不断进行。
总的脱硫反应是:
[FeS]+(CaO)+C=[Fe]+(CaS)+CO-149140kJ
现代炉渣离子结构理论认为,熔融炉渣不是由分子构成而是由离子构成的,因此,脱硫反应实际上是离子反应而不是分子反应。
渣铁之间的脱硫反应是通过渣铁界面上离子扩散的形式进行的,即渣中的O2-离子向铁水面扩散,把自己所带的两个电子传给S,使铁水中的S原子成为S2-离子进入渣中,而由于失去电子变成中性原子氧与碳作用形成CO进入煤气中,进入渣中的S2-离子则与渣中的Ca2+、Mg2+等正离子保持平衡。
因此,脱硫反应实际上是渣铁界面上氧和硫的离子交换,可用如下离子反应式表示:
[S]+2e+S2-
+)O2--2e=[O]
[S]+O2-=S2-+[O]
渣中的碱性氧化物不断供给氧离子和进入生铁中的氧原子与固体碳作用形成CO,不断离开反应面,使上述脱硫反应继续进行。
5.影响脱硫能力的因素
影响脱硫能力的因素有如下几项:
(1)炉渣化学成分
①炉渣碱度。
一般规律是炉渣碱度愈高,脱硫能力愈强。
但碱度过高使渣的流动性变坏,阻碍硫的扩散,同时由于过高的碱度下容易析出正硅酸钙的固体颗粒,不仅提高了黏度,而且降低了炉渣的实际碱度,从而使炉渣的脱硫能力降低。
②MgO。
MgO也具有一定的脱硫能力,但不及CaO,这是由于MgS不及CaS稳定。
但渣中一定范围内增加MgO含量能提高炉渣的温度性和流动性,还可以提高总碱度,这就相当于增加了氧负离子浓度,有利于脱硫反应。
③Al2O3。
Al2O3不利于脱硫,当碱度不变而增加Al2O3含量时,炉渣的脱硫能力会降低。
④FeO。
FeO对脱硫极为不利,(Fe2++O2-=[Fe]+[O])反应增加了生铁中氧的浓度,所以渣中FeO要尽量少。
(2)渣铁温度。
脱硫反应是吸热反应,提高温度对反应有利,同时还降低了炉渣黏度,促进了硫离子的扩散。
(3)提高硫分配系数LS。
硫在炉渣中的质量分数与铁水中的质量分数之比,叫做硫分配系数LS。
铁矿石中S允许含量≤0.3%,S负荷≯5kg/t。
S元素分配:
6.2%生铁,1.5%瓦斯灰,92.2%炉渣。
高炉脱硫是在铁滴穿过炉缸积聚的渣层、渣层与铁层的交界面和铁口通道三处进行的,动力学条件最好的是铁口通道,而渣铁层界面最差。
改善脱硫动力学条件,是提高脱硫效果的重要条件。
由此可看出,高炉不放上渣,使炉渣都从铁口与铁水一起放出,会更好地发挥其脱硫能力。
(4)高炉操作。
正确运用各种调剂因素,保证高炉顺行,是充分发挥炉渣脱硫能力,降低生铁含硫量的重要条件。
6.当前造渣制度存在的问题
6.1当前存在的问题:
(1)不少高炉一级品率低,生铁平均含硫大于0.03%,甚至大于0.04%。
[S]高,将使炼钢工序因造渣物料增加和吹炼时间延长,而造成产量降低、成本升高。
(2)由于进口矿配比增加,Al2O3含量增加,炉渣流动性降低而影响炉渣脱硫能力。
(3)炉渣碱度波动大。
以上问题,都影响生铁含[Si]的有效降低。
6.2对造渣制度的新认识
关于造渣制度最近以来有了新的认识。
从高炉造渣、脱硫角度看发生的变化,一是渣量大幅度减少,由500kg/t降低到250-350kg/t,对S的包容能力降低。
二是焦炭和煤粉含硫量降低,并普遍弃用高S矿石,硫负荷降低。
Al2O3在过去教科书上以15%为上限,而现在国内实践中远远超过这个界限,达到18——20%,还能保持高冶强和顺行。
但较高含量仍对顺行不利。
MgO可以降低高Al2O3渣熔点,改善其流动性和稳定性。
渣中MgO来源于烧结矿,烧结矿中MgO过高,影响强度,因此以控制(MgO)9.5-11.0%为宜。
Al2O3属于中性,但在高炉冶炼中被认为是酸性物质,其熔点是2050℃。
在高炉冶炼中与SiO2结合,产生熔点是2050℃的物质,使渣铁流动性差,分离困难。
CaO熔点是2070℃,MgO熔点是2800℃,但与SiO2和Al2O3结合后生成熔点低于1400℃的物质,在高炉内熔化,形成流动性良好的炉渣。
几个厂家的经验:
鄂钢配比进口球,渣量减少,Al2O3升高,在提高炉渣碱度的同时降低MgO含量,[Si]相应降低,最低单炉月平均[Si]达到0.33%。
莱钢是在中等Al2O3含量情况下,通过增加MgO而改善了炉渣流动性和脱硫能力。
泰钢Al2O3含量平均达18.2%,最高22%,炉渣流动性和稳定性变差,有炉墙粘结和炉缸堆积现象。
淮特、兴澄、鄂钢炉渣中的Al2O3含量分别为14.2%、13.62%、15.98%,对应炉温[Si]分别为0.4%、0.4%、0.5%。
也可以看出Al2O3含量与炉温应呈对应关系,Al2O3含量高时必须适当上提炉温。
6.3济钢应对高Al2O3炉渣实践
(1)表2008年1月至10月6#炉炉渣平均Al2O3含量
月份
1
2
3
4
5
6
7
8
9
10
Al2O3含量(%)
16.68
16.36
16.32
16.47
16.92
17.25
16.33
16.57
16.88
17.12
(2)特点
济钢条件下,高Al2O3炉渣有几个特点:
①黏度高,堵塞气流通道,易引起难行;
②直接造成炉缸渣性堆积;
③炉身下部、炉腹炉腰部位形成粘结,引起炉型变化,影响气流分布,造成难行及堆积。
从生产实际中,可以明显的感觉到这几个特点,最明显的是炉缸堆积和下部粘结,而这两个问题中最迫切而难解决的是下部粘结。
解决这一问题的关键应该是炉渣黏度问题:
黏度η=Boexp(En/RT)
其中R:
气体状态常数;T:
温度;En:
黏流活化能,与渣中复合阴离子团的结构有关。
式中看出,温度是影响黏度的最主要参数,黏度随温度的升高而下降,1500℃时粘度与1400℃时相比降低一半左右。
而MgO含量对黏度影响也很重要,在MgO<20%范围增加含量都使η下降。
为保证顺行,防止下部粘结,打开中心气流,是应坚持的方向,而防粘结的关键就在于[Si]参数的选择,从实践中得出如下结论:
①[Si]选择要同各项内外因素结合综合考虑,决不能盲目一味降[Si];
②目前风、氧(富氧率5-6%)、顶压情况下,不宜做低[Si];
③应对高Al2O3炉渣的关键是提高炉温,[Si]应在0.5~0.6范围,对应物理温度1460℃~1490℃,不能过低,尤其避免连续过低;
④控制[Si]要有清醒认识,坚决的手段,还要具体的办法;
⑤解决好粘结问题,才能考虑缩风口,加长风口,打开中心,进一步活跃炉缸,降焦比;另外还有一个问题,风机能力大并不一定天然开中心,参考兄弟厂经验,提高风量同时一定要注意加长风口,配合上部料制。
不然难以达到开中心降消耗目的。
6.4使用蛇纹石优化炉渣成份
2009年炉料结构大幅度变化条件下,2月份高炉开始大量使用蛇纹石,全月吨铁平均达到18kg/t。
(1)高炉使用蛇纹石的目的
由于原料资源中球团矿产量大量降低,以及烧结矿中Al2O3含量升高,炉渣Al2O3含量也随着升高,带来炉渣粘稠,最终影响炉况的稳定。
需要一种含MgO较高的酸性辅料,既可代替酸性球团矿平衡碱度,又能提高炉渣MgO含量。
在可选择的辅料中,蛇纹石是最佳选择,因为蛇纹石含MgO和SiO2高达38%左右,能够满足以上两个条件,目前的生产条件使用蛇纹石可以实现两个目标。
①作为酸性料,代替部分或全部球团矿,减少甚至取消球团矿,增加块矿使用量。
②作为MgO来源,增加炉渣中MgO含量,改善炉渣流动性。
主要指标对比
项目
利用系数t/m3.d
入炉焦比kg/t
煤比kg/t
毛焦比kg/t
燃料比kg/t
综合焦比kg/t
富氧率%
风温℃
综合品位%
[Si]%
三级品%
CO2%
计划
3.9
429
147
473
/
532
/
1100
/
0.53
2
/
1月
3.88
438
137
487
575
531
4.787
1087
56.69
0.549
0.49
19.3
2月
3.774
423
145
460
568
522
3.723
1094
56.88
0.524
0.53
19.7
与1月比
-0.106
-15
8
-27
-7
-9
-1.064
7
0.19
-0.025
0.04
0.4
与计划比
-0.126
-6
-2
-13
/
-10
/
-6
/
-0.006
-1.47
/
利用系数完成3.774t/m3.d,比计划低0.126t/m3.d,利用系数降低原因主要是配合公司限产,减少富氧率,造成利用系数降低。
焦比(含小焦)完成423kg/t,比计划低6kg/t,比上月降低15kg/t。
喷煤比完成145kg/t,比计划低2kg/t,比上月升高8kg/t。
在炉况稳定的前提下,喷煤比升高与否主要取决于煤粉的价格导向,随着内部结算价格的调整,提高喷煤比有明显的降低成本优势,因此高炉也随着逐步增加喷煤量。
生铁[Si]全月平均0.524%,比计划低0.006%。
炉料结构对比
球团矿%
烧结矿%
块矿%
吨铁蛇纹石kg
1月
24.4
72.9
2.7
4
2月
15
75.5
9.5
18
对比
-9.4
+2.6
+6.8
+14
各高炉炉渣成份对比
2#
3#
4#
5#
6#
1月
Al2O3
17.82
17.69
17.4
17.43
16.74
MgO
10.19
10.08
9.6
9.86
9.91
渣铁比
386
374
383
393
373
2月
Al2O3
18.94
18.97
18.84
18.62
18.69
MgO
10.32
10.5
10.23
10.56
10.76
渣铁比
366
369
367
377
370
2月份与1月比较,渣中Al2O3明显升高,在烧结矿中MgO含量未大幅度提高的条件下,在高炉中使用蛇纹石,达到了既降低球团矿比例,又增加渣中MgO含量目的,在渣中Al2O3含量继续升高的不利条件下,通过提高蛇纹石用量,增加渣中MgO含量,基本保持了良好的渣铁流动性。
7.部分试题(摘自全国冶金题库)
395、(中级工,选择题,较易,无,