基于PLC的四柱万能液压机液压系统设计资料.docx
《基于PLC的四柱万能液压机液压系统设计资料.docx》由会员分享,可在线阅读,更多相关《基于PLC的四柱万能液压机液压系统设计资料.docx(40页珍藏版)》请在冰点文库上搜索。
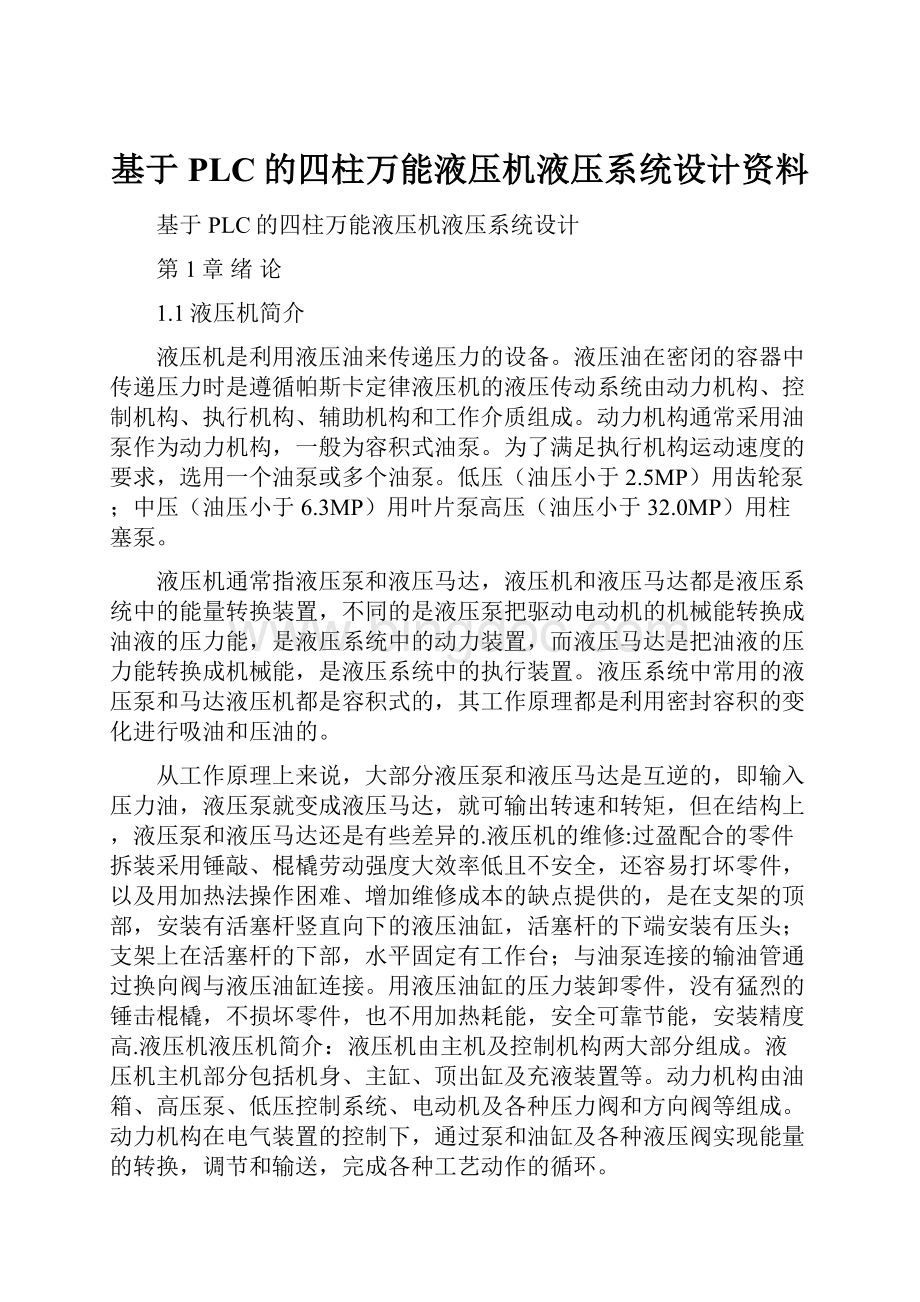
基于PLC的四柱万能液压机液压系统设计资料
基于PLC的四柱万能液压机液压系统设计
第1章绪论
1.1液压机简介
液压机是利用液压油来传递压力的设备。
液压油在密闭的容器中传递压力时是遵循帕斯卡定律液压机的液压传动系统由动力机构、控制机构、执行机构、辅助机构和工作介质组成。
动力机构通常采用油泵作为动力机构,一般为容积式油泵。
为了满足执行机构运动速度的要求,选用一个油泵或多个油泵。
低压(油压小于2.5MP)用齿轮泵;中压(油压小于6.3MP)用叶片泵高压(油压小于32.0MP)用柱塞泵。
液压机通常指液压泵和液压马达,液压机和液压马达都是液压系统中的能量转换装置,不同的是液压泵把驱动电动机的机械能转换成油液的压力能,是液压系统中的动力装置,而液压马达是把油液的压力能转换成机械能,是液压系统中的执行装置。
液压系统中常用的液压泵和马达液压机都是容积式的,其工作原理都是利用密封容积的变化进行吸油和压油的。
从工作原理上来说,大部分液压泵和液压马达是互逆的,即输入压力油,液压泵就变成液压马达,就可输出转速和转矩,但在结构上,液压泵和液压马达还是有些差异的.液压机的维修:
过盈配合的零件拆装采用锤敲、棍橇劳动强度大效率低且不安全,还容易打坏零件,以及用加热法操作困难、增加维修成本的缺点提供的,是在支架的顶部,安装有活塞杆竖直向下的液压油缸,活塞杆的下端安装有压头;支架上在活塞杆的下部,水平固定有工作台;与油泵连接的输油管通过换向阀与液压油缸连接。
用液压油缸的压力装卸零件,没有猛烈的锤击棍橇,不损坏零件,也不用加热耗能,安全可靠节能,安装精度高.液压机液压机简介:
液压机由主机及控制机构两大部分组成。
液压机主机部分包括机身、主缸、顶出缸及充液装置等。
动力机构由油箱、高压泵、低压控制系统、电动机及各种压力阀和方向阀等组成。
动力机构在电气装置的控制下,通过泵和油缸及各种液压阀实现能量的转换,调节和输送,完成各种工艺动作的循环。
液压机的分类:
利用帕斯卡定律制成的利用液体压强传动的机械,种类很多。
当然,用途也根据需要是多种多样的。
如按传递压强的液体种类来分,有油压机和水压机两大类。
水压机产生的总压力较大,常用于锻造和冲压。
锻造水压机又分为模锻水压机和自由锻水压机两种。
模锻水压机要用模具,而自由锻水压机不用模具。
我国制造的第一台万吨水压机就是自由锻造水压机。
液压机(油压机)按结构形式现主要分为:
四柱式、单柱式(C型)、卧式、立式框架等。
按用途主要分为金属成型液压机、折弯液压机、拉伸液压机、冲裁液压机、粉未(金属,非金属)成型液压机、压装液压机、挤压液压机
图1.1单柱液压机
图1.2四柱液压机结构和工艺过程
图1.3磁性材料制品液压机
等。
几种液压机的外观和工作原理如图1.1~图1.3所示。
液压机的工作原理:
液压机是依靠液态介质,就是液压油等利用水和油的静压力。
液压机主要适用于以结构件为主的粉末冶金、机械零件的生产,同时也适用于精密陶瓷、电子陶瓷及硬质合金制品的压制成型。
1.2液压机发展背景
液压机的发展历史已经有100年之多。
大约在16世纪的时候,世界上就出现了水力机器锤。
在18世纪,蒸汽锤的随之诞生。
此后,的一百多年的时间有出现了液压机,液压机对于锻造具有划时代的意义。
再后来大型自由锻锤逐渐被淘汰,目前只保留了5吨以下的中小型自由锻锤。
第二次世界大战后,为了迅速发展航空工业,美国在1955年左右,先后制造了两台315000KN和两台700000KN大型模锻液压机。
直到十九世纪末,逐渐发展成为资本主义发展成为帝国主义,资本输出,向外扩张,争夺殖民地并瓜分世界成了帝国主义的主要内容。
由于具备扩张的需要,锻造和模锻液压机有了迅速发展。
1934年德国制造了70000KN模锻水压机,1938----1944年相继建造了三台150000KN锻造水压机和一台300000KN模锻水压机。
解放前,我国属于半封建半殖民地国家,没有自己独立的工业体系,也根本没有液压机制造工业,只有一些修配用的小型液压机。
解放以后,在党的正确领导下,我国迅速建立了独立自主的完整的工业体系。
我国已能自己设计和制造汽车,机车,发电设备,轧钢设备,飞机,大炮,原子弹以及人造卫星等产品,这些都需要各种液压机有相应的发展。
1957---1962年,我国已经开始自行设计,自行制造各种锻压设备,其中有近30台10000KN到31500KN的中型锻造液压机及二台万吨级大型锻造液压机,同时,也初步建立了一支设计和制造液压机的技术队伍。
近二十年来,世界各国在锻造操作机与锻造液压机联动机组,大型模锻液压机,挤压液压机等各种液压机方面又有了很多新的发展,自动量测和自动控制的新技术在液压机上得到了广泛应用,机械化和自动化程度有了很大的提高。
六十年代,我国先后成套设计并制造了一些重型液压机,其中有300000KN有色金属模锻水压机,120000KN有色金属挤压水压机,80000KN黑色金属模锻水压机等。
近几十年来,又有了一些新的发展,如设计并自制了一批较为先进的60000KN以下的锻造水压机,并已经向国外出口。
相应地,我国也陆续制定了各种液压机的系列及零部件标准。
目前的液压机,除应当充分发挥现有各种液压机的生产潜力之外,还及时的提高设备利用率,同时还搞好锻造操作机,还有他辅助设备的配套工作,另外还要加强对设备的维修和设备本身的技术改造外,同时还要加强锻造液压机和锻造操作机的联动,这样就及时的锻件尺寸自动显示和自动控制,因此锻造液压机组的程序控制和自动控制的研究。
同时应加强对现代化的大型模锻液压机,这样就大型挤压液压机以及其他特种用途液压机的研究。
1.3国内外液压机发展现状
由于液压机的液压系统和整机结构方面,已经比较成熟,国内外液压机的发展主要体现在控制系统方面。
微电子技术的飞速发展,为改进液压机的性能、提高稳定性、加工效率等方面提供了可能。
相比来讲,国内机型虽种类齐全,但技术含量相对较低,缺乏技术含量高的高档机型,这与机电液一体化,中小批量柔性生产的发展趋势不相适应。
在国内外液压机产品中,按照控制系统,液压机可分为三种类型:
一种是以继电器为主控元件的传统型液压机;一种是采用可编程控制器控制的液压机;第三种是应用高级微处理器(或工业控制计算机)的高性能液压机。
三种类型功能各有差异,应用范围也不尽相同。
但总的发展趋势是高速化、智能化。
(1)继电器控制方式是延续了几十年的传统控制方式,其电路结构简单,技术要求不高,成本较低,相应控制功能简单,适应性不强。
其适用于单机工作、加工产品精度要求不高的大批量生产(如餐具、厨具产品等),其也可组成简单的生产线,但由于电路的限制,稳定性、柔性差。
现在,国内许多液压机厂家是以这种机型为主,使用对象多为小型加工厂,或加工精度要求不高的民用产品。
国外众多厂家只是保留了对这种机型的生产能力,而主要面向以下两种技术含量高的机型组织生产。
(2)可编程控制器是在继电器控制和计算机控制发展的基础上开发出来的,并逐渐发展成以微处理器为核心,把自动化技术,计算机技术,通讯技术溶为一体的新型工业自动控制装置。
目前已被广泛的应用于各种生产机械以及自动化生产过程中。
随着技术的不断发展,可编程序控制器的功能更加丰富。
早期的可编程序控制器在功能上只能进行简单的逻辑控制。
后来一些厂家开始采用微电子处理器作为可编程序控制器的中央处理单元(CPU),从而扩大了控制器的功能,使其不仅可以进行逻辑控制,而且还可以对模拟量进行控制。
因此,可编程控制器控制方式是介于继电器方式和工业控制机控制方式之间的一种控制方式。
可编程控制器有较高的稳定性和灵活性,但在功能方面与工业控制机相比有一定差异。
现在,国内有些厂家采用可编程控制器控制方式,如天津锻压机械厂有近60%的产品装有PLC。
通过采用PLC控制,使系统的控制性能和可靠性大大提高。
国外厂家如丹麦的STENHQJ公司采用了SIEMENS的可编程控制器,实现对压力和位移的控制。
(3)工业控制机控制方式是在计算机控制技术成熟发展的基础上采用的一种高技术含量的控制方式。
这种控制方式以工业控制机或单片/单板机作为主控单元,通过外围接口器件(如A/D,D/A板等)或直接应用数字阀实现对液压系统的控制,同时利用各种传感器组成闭环回路式的控制系统,达到精确控制的目的。
1.4液压机发展趋势
(1)高速化,高效化,低能耗。
提高液压机的工作效率,降低生产成本。
(2)机电液一体化。
充分合理利用机械和电子方面的先进技术促进整个液压系统的完善。
(3)自动化、智能化。
微电子技术的高速发展为液压机的自动化和智能化提供了充分的条件。
自动化不仅仅体现的在加工,应能够实现对系统的自动诊断和调整,具有故障预处理的功能。
(4)液压元件集成化,标准化。
集成的液压系统减少了管路连接,有效地防止泄漏和污染。
标准化的元件为机器的维修带来方便。
第2章液压系统设计
2.1明确液压系统设计要求
要求设计的液压系统需完成的工作循环是:
上缸快速下行→慢速加压→保压延时→快速回程并停止;下缸活塞项出→退回,或浮动压边→停止→项出。
已知:
液压系统最高工作压力为25MPa(泵出口),最大工作流量60L/min;公称力2000KN,主缸最大行程710mm;顶出缸最大顶出力400KN,顶出最大行程250mm。
调查研究机计算结果表明:
主缸最大下行的速度约为100mm/s,慢压的最大速度为10mm/s,主缸最大回程的速度约为50mm/s;运动部件的重力G约为3000N,静摩擦力
=为120N,动摩擦力
为90N;加速或减速时间
。
顶出缸向上顶出的速度约为35mm/s,向下退回的速度约为80mm/s;运动部件的重力G约为1200N,静摩擦力
为105N,动摩擦力
为72N,加速或减速时间
。
表2.1各工况的运动参数和动力参数表
工况
速度v(mm/s)
运动部件重力(N)
静摩擦力
(N)
动摩擦力
(N)
加速或减速时间△t(s)
主缸
快降
100
3000
120
90
0.05
慢压
10
回程
50
顶出缸
顶出
35
1200
105
72
退回
80
2.2分析液压系统工况
(1)负载分析
主缸在各工作阶段的负载
启动阶段
加速阶段
慢压阶段
快速回程阶段
顶出缸在各工作阶段的负载
启动阶段
加速阶段
向上顶出阶段
向下退回阶段
(2)速度图和负载图的绘制
负载图按上面的数值绘制,主缸、顶出缸负载图分别如图2.2(a)、图2.3(a)和所示;速度图按主缸快降行程为510mm、慢压行程为200mm
和表2.1数据等绘制速度图,滑块、顶出缸速度图分别如图2.2(b)、图2.3(b)所示。
(a)主缸负载图
(b)主缸速度图
图2.2主缸负载图和速度图
(a)顶出缸负载图
(b)顶出缸速度图
图2.3顶出缸负载图和速度图
2.3拟定液压系统原理图
该液压系统要求流量大、功率大,空行程和加压行程的速度差异大,因此要求功率合理利用,工作稳定性和可靠性要高。
(1)供油方式选择
由工况系统分析可知,加速阶段与慢压阶段的流量相差很大,如选择定量单泵供油,在慢压阶段时会由于能量损失太大而使油液发热,从节省能量、减少发热、合理利用功率角度考虑,本设计采用一个恒功率变量轴向柱塞泵供油,泵在工作过程中基本维持恒功率输出,故系统效率高,发热小。
另外,单独采用一齿轮泵来供给系统低压控制油。
(2)速度控制回路的选择
在液压机工作过程中,负载是逐渐增大的,且功率较大,运动速度较高,为提高效率此系统要求温升量小,故在此次选用容积调速回路,这种调速回路具有速度负载变化量小,刚性较好,效率较高,发热和泄漏小的特点。
(3)速度换接方式的选择
根据设计要求,换接要平稳可靠,可选择行程阀控制的速度换接回路。
该系统主油路压力高、流量大,不宜采用电磁换向阀。
由于有单独的控制油泵供油,为达设计要求本系统在主油路上采用M型三位四通电液换向阀,控制油路上采用二位二通电磁换向阀。
它的特点是结构简单,调节行程比较方便,阀的安装也比较容易。
(4)压力控制回路的选择
为方便工作过程中的压力变换与调节,保证安全,主由路采用先导式溢流阀进行二级调压和安全溢流。
控制油路采用直动式溢流阀进行调压。
对液压机来说,保压过程对产品尺寸和质量影响较大,保压过程是防止产品尺寸回弹。
最简单的保压回路是使用单向阀,因此拟采用一个单向阀与活塞密封圈、充液阀一起组成保压回路,保压时间通过PLC编程控制。
保压结束之后,不能立即换向回程,须用卸压回路先卸压,否则会因液压缸中储存的大量能量突然释放而产生很大的液压冲击。
拟采用充液阀(外泄式)内部的卸压阀在控制油压下先进行缓慢卸压,然后再换向回程。
这种回路能减轻液压缸换向引起的振动和噪音。
(6)顶出缸液压回路的选择
为保证上下两缸的动作协调和安全,采用两缸换向阀串联互锁的方法,使其中一缸必须在另一缸停止不动时才能动作。
由于顶出液压缸换向时阀芯所需推力较大,宜采用K型三位四通电液换向阀进行换向。
此换向回路的特点是:
操纵方便,换向平稳无冲击。
另外,在顶出工作阶段的进油路上安装溢流阀,进行安全溢流。
同时在利用顶出缸进行浮动压边时,为了获得一定的压边力,再串联一个节流阀和溢流阀。
将上述所选定的液压回路进行归并,并根据需要作必要的修改和调整,最后画出液压系统原理图如图2.5所示
1—齿轮泵2—柱塞泵3—溢流阀4—远程调压阀5—调压阀6—电液换向阀7—压力开关表8—电磁换向阀9—液控单向阀10—背压阀11—泄荷阀12—压力继电器13—单向阀14—充液阀15—充液箱16—主缸17—顶出缸18—安全阀19—节流阀20—调压阀21—电液换向阀22—滤油器
图2.5液压系统图
2.3.1液压系统工作原理
2.3.1.1主缸运动过程
(1)快速下行当按下下行启动按钮后,电磁铁1DT、5DT通电吸合。
低压控制油使电液换向阀6切换到右位,同时经电磁阀8使液控单向阀9打开。
主泵l经电液换向阀6的右位,单向阀13向主缸16上腔供油,主缸下腔液压油经液控单向阀9、电液换向阀6的右位、电液换向阀21的中位回油。
此时主阀滑块22在自重作用下快速下降。
(2)慢速接近工件加压当主缸滑块上的挡铁到达接近开关SQ2的位置时,电磁铁5DT断电,电磁阀8处于常态位,液控单向阀9关闭。
主缸液压油经背压阀10、电液换向阀6的右位、电液换向阀2l的中位回流到油箱。
由于回油路上有背压力,滑块单靠自重就不能下降,主泵1供给的液压油使它下行,速度减慢。
这时主缸上腔压力升高。
充液阀14关闭。
来自主泵l的液压油推动活塞使滑块慢速接近工件,当主缸活塞的滑块抵住工件后,阻力急剧增加,上腔液压油压力进一步提高,主泵1的排油量自动减小,主缸活塞以很慢的速度对工件加压。
(3)保压当主缸上腔的液压油压力达到设定值时,压力继电器12发出信号,使电磁铁1DT断电,电液换向阀6回复中位,将主阀上、下油腔关闭。
同时主泵1的流量经电液换向阀6、电液换向阀2l的中位进行卸载。
单向阀13保证了主阀上腔良好的密封性,主缸上腔维持高压。
保压时间可由时间继电器调整。
时间继电器受压力继电器12控制。
(4)卸压、快速回程保压时间结束时,时间继电器发出控制信号使电磁铁2DT通电,或当压制成型时由接近开关SQ3发出控制信号使电磁铁2DT通电。
主缸处于回程状态。
当电液换向阀6切换至左位后,主缸上腔还未卸压,压力很高,卸荷阀11处于开启状态,主泵1的液压油经电液换向阀6的左位、卸荷阀11流回至油箱。
这时主泵1在低压下运转,该压力不足以打开液控单向阀14的主阀芯,但能打开液控单向阀14中的卸载小阀芯,主阀上腔的液压油经此卸载小阀芯的开口而流回充液箱15,压力逐渐降低。
该过程一直持续到主缸上腔压力降到较低值时,卸荷阀11关闭,主泵1的供油压力升高,推开液控单向阀14的主阀芯。
此时主泵1的液压油经电液换向阀6的左位、液控单向阀9流入主缸下腔;而主缸上腔的液压油经
充液阀14回流到充液箱15,实现主缸快速回程。
(5)停止当主缸滑块上的挡铁到达接近开关SQl的位置时,电磁铁2DT断电,主缸活塞被中位为M机能的电液换向阀6锁紧而停止运动,回程结束。
此时主泵1的液压油经电液换向阀6、电液换向阀2l回流到油箱,泵处于卸载状态。
2.3.1.2顶出缸运动过程
顶出缸17只有在主缸16停止运动时才能动作。
由于液压油先经过电液换向阀6后才进入电液换向阀21,顶出缸17的运动受电液换向阀2l控制,当电液换向阀21处于中位时,才有油通向顶出缸,实现了主缸16和顶出缸17的运动互锁。
(1)顶出按下顶出按钮,电磁铁3DT通电吸合,液压油由主泵l经电液换向阀6的中位、电液换向阀2l的左位流人顶出缸下腔,上腔液压油则经电液换向阀21回油,活塞上升;
(2)退回当电磁铁3DT通断电,电磁4DT通电吸合时,油路换向,顶出缸的活塞下降。
2.4液压系统计算和选择液压元件
2.4.1确定液压缸主要尺寸
(1)工作压力p的确定。
由设计要求可知,液压系统最大工作压力(泵)为25MPa。
由液压设备类型查参考文献[2]中表2-1,选取液压缸工作压力为24MPa。
(2)计算上模液压缸内径D和活塞杆直径d。
由负载图可知,最大外负载F为1003000N,按参考文献[2]中表2-2可取背压
为零,机械效率
为0.95,按参考文献中表2-2查得d/D为0.7。
由下式
(2.1)
代入数据得:
解得:
D=0.237m。
根据参考文献[2]中的表2-4,将液压缸内径圆整为标准直径系列D=250mm。
活塞杆直径d按d/D=0.7及参考文献中[2]中的表2-5活塞杆直径系列,取d=180mm。
计算顶出缸内径D和活塞杆直径d。
根据参考文献[1]中的表11-2及液压缸额定压力系列,可取其工作压力为16MPa。
由负载图知最大外负载F为401419N,按参考文献[2]中的表2-2可取背压
为零,机械效率
为0.95,按参考文献中表2-2查得d/D为0.7。
由式(3.1)得:
(2.2)
=
=0.183m
根据参考文献[2]中的表2-4,将液压缸内径圆整为标准直径系列D=180mm,杆直径d按d/D=0.7及参考文献中[2]中的表2-5活塞杆直径系列,取d=125mm。
各缸的工作压力和主要尺寸如表2.2所示。
表2.2缸的工作压力和主要尺寸
工作压力(MPa)
缸体内径(mm)
活塞杆直径(mm)
主缸
24
250
180
顶出缸
16
180
125
2.4.2确定液压泵的压力和流量,选择泵的规格
(1)确定泵的工作压力
考虑到正常工作时进油管路中有一定的压力损失,所以泵的工作压力为
(2.3)
式中:
—液压泵的最大工作压力;
—执行元件最大工作压力;
—进油管路中的压力损失,初算是简单系统可取0.2~0.5MPa,复杂系统取0.5~1.5MPa,本设计取0.5MPa。
代入数据得:
上述计算所得的
是系统的静态压力,考虑到系统在各种工况的过渡阶段出现的动态压力往往超过静态压力。
另外,考虑到一定的压力储备量,并确保泵的寿命,因此所选泵的额定压力
应该满足
。
中低压系统取较小值,高压系统取较大值。
在本设计中
。
(2)确定泵的流量
由设计要求可知,液压系统(泵出口)最大工作流量为60L/min。
由于选用的是恒功率变量泵,故主缸快速下行时,系统有最大工作流量。
(3)选择液压泵的规格
根据以上算得的
和
查阅参考文献[5],现选用A7V401RPGH型恒功率变量轴向柱塞泵。
该泵的基本参数为:
最大排量40.1ml/r,最小排量为零;额定压力35MPa,最高压力40MPa;额定(实际)流量为56.4L/min(1450r/min);功率为34kw(35MPa);容积效率
,总效率
。
根据背压阀18的调压范围,改变柱塞泵伺服阀心弹簧的预压缩量,从而调节泵的输出功率值,使其工作在15KW(16MPa)。
(4)选择与液压泵匹配的电动机
由于选用的是恒功率变量柱塞泵,且该泵的参数可知其输出功率P为34kw,泵的效率
,故所需电动机功率
为
查阅参考文献[6]中的电动机产品样本,选用Y225M-4型电动机,其额定功率为45kw,额定转速为1450r/min。
2.4.3选择液压阀
根据所拟定的液压系统图,计算分析通过各阀油液的最高压力和最大流量,选择各阀的型号和规格,列于表3.3(表中阀类元件主要选自GE系列)。
表2.3液压元件明细表
序号
元件名称
估计通过流量(L/min)
额定流量(L/min)
额定压力(MPa)
额定压降(MPa)
型号、规格
1
齿轮泵
—
14.5
10
—
CB-10
2
轴向柱塞泵
—
56.2
35
—
A7V401RPGH
3
安全阀
2.5
63
31.5
—
DB10A1-50/315
4
远程调压阀
2.5
63.
31.5
—
KP—4B
5
调压阀
2.5
63
16
—
YF3-E10B
6
电液换向阀
56.2
80
16
<0.5
34DYF3M-E10B
7
压力开关表
—
—
—
—
4K-F10D-1
8
电磁换向阀
14.5
25
16
<0.5
22DF3Y-E10B
9
液控单向阀
50
80
16
0.1
YAF3-Eb10B
10
背压阀
56
63
16
—
YF3-E10L
11
泄荷阀
1.5
63
6.3
—
YF3-10B
12
压力继电器
—
—
—
—
HED1KA20/35
13
单向阀
56.2
80
16
0.2
AF3-Ea10B
14
充液阀
—
—
0~31.5
0.2
SL15GB230
15
电液换向阀
56.2
80
16
<0.5
34DYF2K-E10B
16
节流阀
20
25
16
—
ALF-E10B
17
行程开关
—
—
—
—
Y-Hb6F
18
滤油器
24
—
—
—
XU-B32
2.4.4确定管道尺寸和油箱容积
油管内径尺寸一般可参照选用的液压元件接口尺寸而定,也可按管路允许流速进行计算。
本系统主油路流量为上模快降时流量q=60L/min,压油管的允许流速取V=4m/s,按参考文献[1]中式(7-9)进行计算,内径d为
(2.4)
若主油路流量按快速回程时取q=50L/min,则可算的油管内径d=16.3mm。
综合诸因素油管按
选用内径为17mm的无缝钢管。
吸油管内径现参照A7V401RPGH变量泵吸油口连接尺寸选择,取吸油管内径d为50mm。
本设计为中高压液压系统,参照参考文献[2]中的表4-1,液压油箱的有效容积按泵的流量的6~12倍确定,现选用容量为1000L的油箱,其型号为BEX-1000。
2.5液压缸的设计
2.5.1确定液压缸主要尺寸
由前述计算可知,主缸的工作压力为24MPa,缸内径D=250mm,活塞杆直径d=180mm;顶出缸的工作压力为16MPa,缸内径D=180mm,活塞杆直径d=125mm。
(1)计算液压缸壁厚和外径
液压缸的壁厚由强度条件计算,缸的材料选用45号钢。
由于主缸的工作压力很大,属高压系统,故视其缸筒为厚壁圆筒。
按材料力学中的厚壁圆筒