一模一腔直浇口顶杆顶出水杯的塑料模具设计.docx
《一模一腔直浇口顶杆顶出水杯的塑料模具设计.docx》由会员分享,可在线阅读,更多相关《一模一腔直浇口顶杆顶出水杯的塑料模具设计.docx(25页珍藏版)》请在冰点文库上搜索。
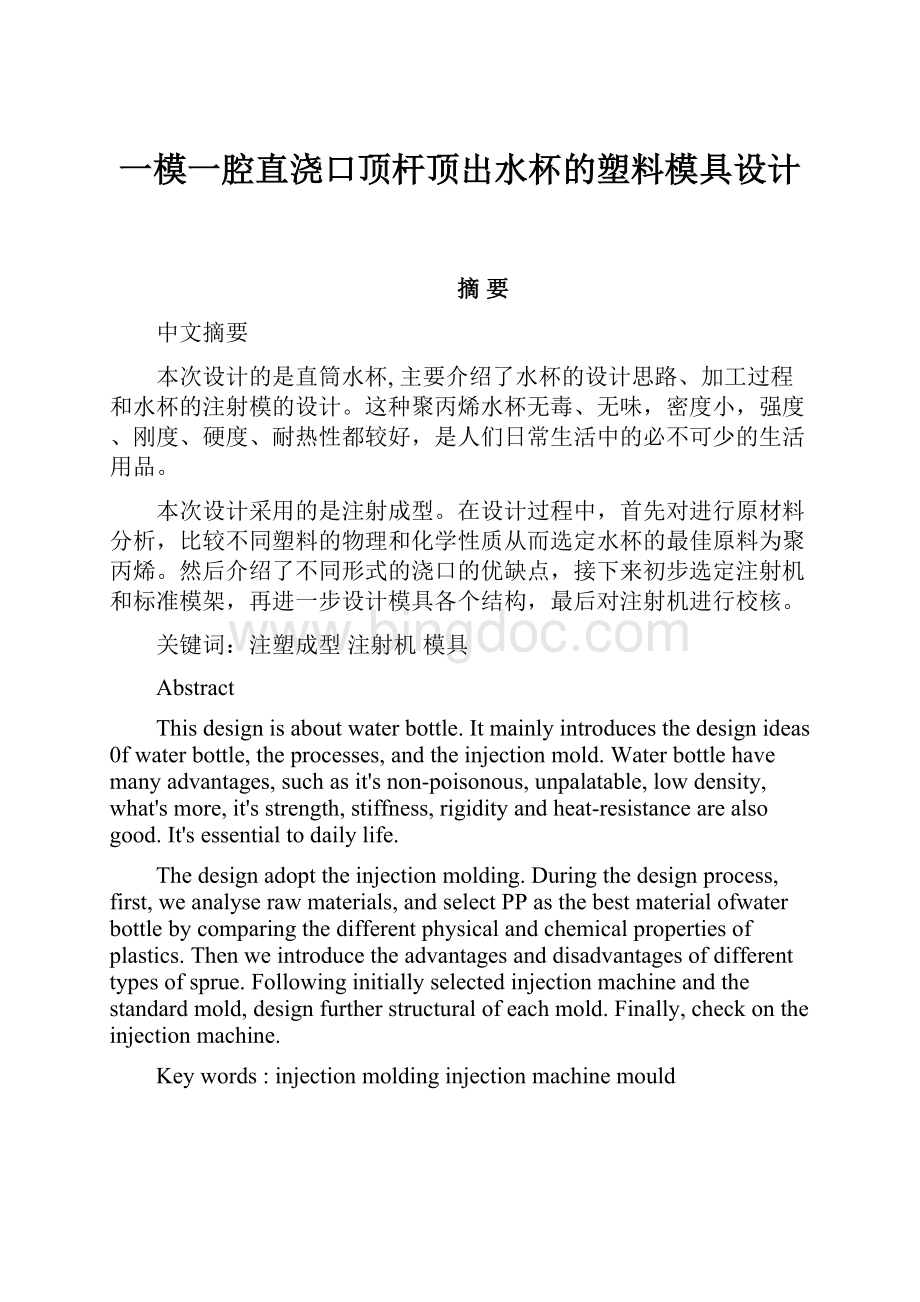
一模一腔直浇口顶杆顶出水杯的塑料模具设计
摘要
中文摘要
本次设计的是直筒水杯,主要介绍了水杯的设计思路、加工过程和水杯的注射模的设计。
这种聚丙烯水杯无毒、无味,密度小,强度、刚度、硬度、耐热性都较好,是人们日常生活中的必不可少的生活用品。
本次设计采用的是注射成型。
在设计过程中,首先对进行原材料分析,比较不同塑料的物理和化学性质从而选定水杯的最佳原料为聚丙烯。
然后介绍了不同形式的浇口的优缺点,接下来初步选定注射机和标准模架,再进一步设计模具各个结构,最后对注射机进行校核。
关键词:
注塑成型注射机模具
Abstract
Thisdesignisaboutwaterbottle.Itmainlyintroducesthedesignideas0fwaterbottle,theprocesses,andtheinjectionmold.Waterbottlehavemanyadvantages,suchasit'snon-poisonous,unpalatable,lowdensity,what'smore,it'sstrength,stiffness,rigidityandheat-resistancearealsogood.It'sessentialtodailylife.
Thedesignadopttheinjectionmolding.Duringthedesignprocess,first,weanalyserawmaterials,andselectPPasthebestmaterialofwaterbottlebycomparingthedifferentphysicalandchemicalpropertiesofplastics.Thenweintroducetheadvantagesanddisadvantagesofdifferenttypesofsprue.Followinginitiallyselectedinjectionmachineandthestandardmold,designfurtherstructuralofeachmold.Finally,checkontheinjectionmachine.
Keywords:
injectionmoldinginjectionmachinemould
第一部分综述
目前,塑料制品得到了越来越广泛的应用,塑料的成型方法也越来越多,如注射成型、挤压成型、真空成型、发泡成型、中空吹塑成型、薄膜吹塑成型,以及热固性塑料的各种成型等。
其中,塑料的注射成型是最主要的成型方法,塑料注射模则是注射成型的工具。
在现代塑料注射成型的生产实践中,高效的塑料注射机、先进的塑料注射模具和合理的注射成型工艺是不可缺少的三项主要因素,本说明书即介绍了一模一腔直浇口顶杆顶出水杯塑料模具设计的基本过程。
1.1制品原材料的选择
塑料行业是20世纪发展最快的行业,也是21世纪最有前途的行业之一。
塑料的发展直接导致了塑料模具的发展。
塑料模具是用来生产塑料制品的工具,在设计模具之前,必须对塑料的成型工艺性能有充分的了解和掌握,只有充分熟悉成型工艺条件之间的内在关系,才能精确控制模具尺寸与塑料制品的尺寸,才能设计出优良的模具。
以下为通用塑料的使用性能和用途。
1.1.1聚苯乙烯PS
性能:
电绝缘(尤其高频绝缘性)性优良,无色透明,透光率仅次于有机玻璃,着色性、耐水性、化学稳定性良好,力学强度一般,刚性好,但性脆,易产生应力碎裂,不耐笨、汽油等有机溶剂。
用途:
适于制作绝缘透件、透明件、装饰件日用品、泡沫包装材料及建筑隔热材料等。
1.1.2聚乙烯PE
性能:
耐腐蚀性、电绝缘(尤其高频绝缘性)性优良,可以氯化、辐照改性,可用玻璃纤维增强。
高密度聚乙烯(HDPE)熔点、刚性、硬度和强度较高、耐应力开裂性好,吸水性小,有突出的绝缘性能和良好的耐辐照性。
低密度聚乙烯(LDPE)柔软性、伸长率、冲击强度和透明性较好。
线性低密度聚乙烯(LLDPE)的性能介于LDPE和HDPE之间。
茂金属聚乙烯(mPE)主要用于薄膜,薄膜强度、柔软性、热封性和透明性极好。
超高分子量聚乙烯(UHMWPE)冲击强度高,耐疲劳,耐磨,用冷压烧结成型。
用途:
高密度聚乙烯适于制作管材、中空瓶、注射制品、重包装膜、编织袋、撕裂膜、大包带、周转箱及丝类等。
低密度聚乙烯用于制作地膜、大棚膜、保鲜膜、电缆及注射件等。
线性低密度聚乙烯主要用于薄膜、注射制品、编织袋、打包带等。
超高分子量聚乙烯适于制作减磨、耐磨及传动零件。
1.1.3聚氯乙烯PVC
(1)硬聚氯乙烯(HPVC)
性能:
力学强度高,硬度大,绝缘性优良,耐酸碱力极强,化学稳定性好,阻燃性好,印刷及焊接性好,但软化点低。
用途:
适于制造型材、管材、棒材、板材、片材、丝类、中空瓶、焊条及注射制品(管件和阀门等),代替木材和金属材料。
(2)软聚氯乙烯(SPVC)
性能:
制品柔软,断裂伸长率大,力学强度大、耐腐蚀性、电绝缘性均低于硬聚氯乙烯,且易老化。
用途:
适于制作大棚薄膜、盐膜、日用膜、电线电缆绝缘层、革类、鞋类、软管、软片及密封材料等。
1.1.4聚丙烯PP
性能:
性对密度小,强度、刚性、耐热性均优于低压聚乙烯,可在100℃左右使用。
具有优良的耐腐蚀性,耐疲劳性好,良好的高频绝缘性,不受湿度影响,但低温变脆,不耐磨,易光老化。
用玻璃纤维增强后,强度接近工程塑料。
聚丙烯的共聚物(PP-C)可改善其冲击性能,其中无轨共聚物(PP-R)主要用于管材,嵌段共聚物(PP-B)主要用于大型容器、周转箱等。
用途:
PP适于制作注射制品、汽车配件、壳体、日用品、打包带、编织袋、双向拉伸膜(烟膜、黏胶带基膜等)、电容器膜、上水管材、地热管、片材(吸塑成保证盒、一次性水杯等)及中空瓶等。
[1]
根据以上制品性能,综合参考,特别是聚丙烯具有很好的耐热性,正是水杯需要的性能,所以选择PP作为水杯的原材料。
经查阅[2],由张维合主编《注塑模具设计使用教程》书中表1-1以及表1-4可知PP的计算收缩率及其他性能如表1-1。
表1-1PP的计算收缩率及其他性能
性能名称
数值
性能名称
数值
收缩率
1%~2.5%
熔点/℃
164
相对密度/g/cm3
0.90~0.91
流程比
250:
1
模温/℃
160~230
型腔压力/MPa
20
注射压力MPa
70~140
玻璃化温度/℃
-20
第二部分设计过程
在选定原材料后,根据课程设计要求,我们需要设计的是直浇口一模一腔顶杆顶出水杯的塑料模具设计,所以浇口方式、型腔数目、顶出方式都已经确定。
据此,先设计塑料制品的尺寸。
2.1塑料水杯尺寸的确定
用途:
盛水。
使用要求:
耐高温、表面光滑、无毒、韧性好。
选定其制品尺寸:
水杯总高度:
70mm;
水杯外直径:
60mm;
水杯壁厚:
1.5mm;
杯底壁厚:
3.5mm。
如图2-1-1所示。
(a)
(b)(c)
图2-1-1水杯三视图(a)俯视图(b)主视图(c)侧视图
按塑件尺寸计算体积:
Vs=[(60/2)2×70×3.14-(57/2)2×66.5×3.14]mm2=28.21cm2
查表1-1,取PP密度为0.90g/cm3
则塑件重量:
Ms=Vsρ=28.21×0.90=25.389g
2.2成型零部件的设计
型腔是直接成型塑料制件的部分,它通常由凸模,凹模,型芯和成型杆、镶块等构成。
2.2.1型腔、型芯工作部位尺寸的确定
查表1-1PP塑料的收缩率为1%~2.5%
平均收缩率S=(1%+2.5%)/2=1.75%
型腔工作部位尺寸:
型腔内形尺寸:
LM=D(1+S)=60×(1+1.75%)=61.05mm
型腔深度尺寸:
HM=H(1+S)=70×(1+1.75%)=71.225mm
型芯外形尺寸:
lM=d(1+S)=57×(1+1.75%)=58mm
型芯高度尺寸:
hM=h(1+S)=66.5×(1+1.75%)=67.66mm
式中,Ls——塑件外型径向基本尺寸的最大尺寸(mm);
ls——塑件内型径向基本尺寸的最小尺寸(mm);
Hs——塑件外型高度基本尺寸的最大尺寸(mm);
hs——塑件内型径向基本尺寸的最小尺寸(mm);
Δ——塑件公差(mm);
δ——模具制造公差,取(1/3~1/4)。
则型芯、型腔的尺寸如表2-2-1所示:
表2-2-1型芯、型腔尺寸
尺寸类型
尺寸(mm)
型腔直径
61.05
壁厚
1.5
型芯直径
58.00
型腔高度
71.22
底厚
3.5
型芯高度
67.66
2.3选用标准模架
由设计要求,为一模一腔直浇口顶杆顶出,选择直浇口A型模架。
根据塑料制品尺寸,有:
模架宽度W>塑件最大宽度+型腔侧壁厚×2
模架长度L>塑件最大长度+型腔侧壁厚×2
垫块高度C>H5+H6+塑件高度
根据经验取型腔侧壁厚为10mm,代入数据得到:
W>60+10×2=80mm
L>70+10×2=80mm
C>H5+H6+70
根据以上数据查得[3]基本型模架组合尺寸选用4040系列模架。
选定模板厚度:
A=80mm
动模板厚度:
B=40mm
垫块厚度:
C=130mm
模具厚度H模=H1+H2+H4+A+B+C=30+50+50+80+40+130=380mm
即模具外形尺寸:
450×400×380mm
即所选模架为A4040-80×40×130GB/T12555—2006,
模架的基本尺寸如表2-3。
表2-3-14040系列模架标准参数表
W
L
W1
W2
W3
C
H1
H2
400
400
450
68
260
130
30
50
H3
H4
H5
H6
W4
W5
W6
W7
35
50
25
30
198
234
324
330
模架尺寸示意图如图2-3-1。
图2-3-1直浇口模架组合尺寸图示
2.4注射机的选定
注射模是安装在注射机上的,因此在设计注射模具时应该对注射机有关技术规范进行必要的了解,以便设计出符合要求的模具,同时选定合适的注射机型号。
从模具设计角度考虑,需要了解注射机的主要技术规范。
在设计模具时,最好查阅注射机生产厂家提供的有关“注射机使用说明书”上标明的技术规范。
因为即使同一规格的注射机,生产厂家不同,其技术规格也略有差异。
2.4.1初步选定注射机
选用注射机时,通常是以某塑件(或模具)实际需要的注射量初选某一公称注射量的注射机型号,然后依次对该机型的公称注射压力、公称锁模力、模板行程以及模具安装部分的尺寸一一进行校核。
(1)注射量
要求
式中,V机—额定注射量,cm3
V塑件—塑件与浇注系统凝料体积和,cm3
=
=28.21+1.126=29.336cm3
则
=29.336/0.8=36.67cm3
(2)注射压力
要求
式中,
—注射机的注射压力
—PP的成型压力,为70~140MPa
所以,
140MPa
(3)锁模力
式中,P—PP成型时的型腔压力,为20MPa
F—塑件及浇注系统在分型面上的投影面积和,mm2
各型腔及浇注系统及各型腔在分型面上的投影面积
F=
×(61.05/2)2=2925.78mm2
=20×2925.78=58.5kN
根据以上分析计算,查得[3]常用注射技术规范及特性,初选注射机型号为:
XS-ZY-500。
注射机参数详见表2-4-1。
项目
参数
项目
参数
额定注射量/㎝3
500
喷嘴圆弧半径/mm
18
螺杆(柱塞)直径/mm
65
喷嘴孔直径/mm
3
注射压力/MPa
145
顶出形式
中心液压顶出,中心距100mm
注射行程/mm
200
动、定模固定板尺寸/mm×mm
700×850
注射方式
螺杆式
拉杆空间/mm
540×440
锁模力/KN
3500
合模方式
液压-机械
最大成型面积/㎝3
1000
液压泵流量(L/min)
200
模板最大行程/mm
500
液压泵压力/Mpa
6.5
模具最大厚度/mm
450
电动机功率/Km
22
模具最小厚度/mm
300
机器外形尺寸/mm×mm×mm
6500×1300×2000
表2-4-1XS-ZY-500注射机参数
2.5浇注系统的设计
浇注系统由主流道、分流道、浇口、冷料井所组成。
由课程设计任务,我们选择直浇口浇注。
取分型面在水杯口处,浇口在水杯底部。
为了水杯美观,这里不设计冷料井。
一般而言,主流道即可作为直浇口使用,主流道是一端与注射机喷嘴相接触,可看作是喷嘴的通道在模具中的延续,另一端与分流道相连的一段带有锥度的流动通道。
2.5.1直浇口(主流道)设计要点
1)主流道设计成圆锥形,其锥角可取2°~6°,流道壁表面粗糙度取Ra=0.63μm,且加工时应沿道轴向抛光。
2)主流道如端凹坑球面半径R2比注射机的、喷嘴球半径R1大1~2mm;球面凹坑深度3~5mm;主流道始端入口直径d比注射机的喷嘴孔直径大0.5~1mm;一般d=2.5~5mm。
3)主流道末端呈圆无须过渡,圆角半径r=1~3mm。
4)主流道长度L以小于60mm为佳,最长不宜超过95mm。
5)主流道常开设在可拆卸的主流道衬套上;其材料常用T8A,热处理淬火后硬度53~57HRC。
综合以上要点,设计的直浇口如图2-5-1。
图2-5-1直浇口示意图
2.5.2直浇口尺寸计算
根据经验:
d=d0+(0.5~1)
D
2t
其中D—直浇口近型腔直径,mm
t—塑料制品底厚,mm
d0—喷嘴直径,mm
d—直浇口近喷嘴处直径,mm
据表2-4-1,有d0=3mm,则d=d0+(0.5~1)=3.5mm,D=2×3.5=7mm。
此时,计算直流道熔体体积
Vj=
Vj—浇注系统体积,cm3;
L—沿主流道弧面向上延长形成的圆椎体高度。
因2d=D,故L=50.2mm
所以Vj=1.126cm2
浇注系统重量:
m=1.126×0.90=1.01g
2.5.3浇口套的设计
由于主流道要与高温塑料及喷嘴接触和碰撞,所以模具的主流道部分通常设计成可拆卸更换的衬套,简称浇注套或浇口套。
浇口套的形式有多种,可视不同模具结构来选择。
按浇注系统不同,浇口套通常被分为二板模浇口套和三板模浇口套两大类。
这里我们选择二板模浇口套。
浇口套尺寸规格如图2-5-2。
图2-5-2浇口套规格示意图
根据设计的直浇口尺寸,查阅GB/T4169.19-2006塑料注射模模零件第19部分,取D=20mm,D1=35mm,D2=40mm,D3=3.2mm,L=80mm。
浇口套20×80GB/T4169.19—2006
2.6推出系统的设计
在开模过程中,将塑件从模具中顶出的装置。
根据课程设计要求,选择顶杆顶出方式。
2.6.1脱模力的计算
推件力Ft=Ap(μcos
—sin
)+qA1
式中,A—塑料包络型芯的面积,mm2
P—塑件对型芯单位面积的包紧力,p取0.8×107~1.2×107Pa
—脱模斜度,取10~20
q—大气压力,0.09MPa
μ—塑件对钢的摩擦系数,约为0.1~0.3
A1—制件垂直脱模方向的投影面积,mm2
制件垂直脱模方向的投影面积:
A1=
mm2
Ft=Ap(μcos
—sin
)+qA1
=12322.24×0.8×107×(0.1cos2°-sin1°)/106+0.09×2925.78
=7019.84N
2.6.2圆推杆推出的设计
(1)圆推杆位置设计
推杆应布置在制品包紧力大的地方,推杆不能太靠边,要保持1~2mm的钢厚。
由于水杯壁厚为1.5mm,且制件所需脱模力极大,不适合顶水杯边缘,综合考虑,采用一根顶杆顶杯底的方式。
(2)圆推杆大小及规格
因制品的几何形状及型腔结构等的不同,所用推杆的截面形状也不尽相同,常用推杆的截面形状为圆形。
推杆又可分为普通推杆与成型推杆两种,我们这里选用普通推杆。
其结构形式见图2-6-1。
图2-6-1推杆规格示意图
=130-30+50+40+70=260mm
为了使塑件在推杆推出过程中不被推杆穿破,查阅PP弯曲强度为67.5MPa,
67.5×(π/4)D2≥Ft
Ft=7019.84N
求得D≥11.11mm。
考虑到包紧力、摩擦力等其他脱模阻力,可以选择更大直径的推杆,故本设计中选取D=16mm。
根据国家标准:
推杆12×300GB/T4169.1—2006
D=16mmD1=22mmh=7mmR=0.8mmL=300mm
材料与硬度:
材料由制造者选定,推荐采用4Cr5MoSiV1、3Cr2W8V
硬度50HRC~55HRC,其中固定端90mm长度范围内硬度35HRC~45HRC。
淬火后表面可进行渗氮处理,渗氮层深度为0.08mm~0.15mm,心部硬度40HRC~44HRC,表示硬度
900HV。
2.7导向系统的设计
导向系统主要包括动、定模的导柱导套和侧向抽芯机构的导向槽等。
其作用是保证动模与定模闭合时能准确定位,脱模时运动可靠,以及模具工作时承受侧向力。
2.7.1导柱导向机构设计要点
(1)小型模具一般只设置两根导柱,当其元合模方位要求,采用等径且对称布置的方法,若有合模方位要求时,则应采取等径不对称布置,或不等径对称布置的形式。
大中型模具常设置三个或四个导柱,采取等径不对称布置,或不等径对称布置的形式
(2)直导套常应用于简单模具或模板较薄的模具;Ⅰ型带头导套主要应用于复杂模具或大、中型模具的动定模导向中;Ⅱ型带头导套主要应用于推出机构的导向中
(3)导向零件应合理分布在模具的周围或靠近边缘部位;导柱中心到模板边缘的距离δ一般取导柱固定端的直径的1~1.5倍;其设置位置可参见标准模架系列
(4)导柱常固定在方便脱模取件的模具部分;但针对某些特殊的要求,如塑件在动模侧依靠推件板脱模,为了对推件板起到导向与支承作用,而在动模侧设置导柱
(5)为了确保合模的分型面良好贴合,导柱与导套在分型面处应设置承屑槽;一般都是削去一个面,或在导套的孔口倒角
(6)导柱工作部分的长度应比型芯端面的高度高出6~8mm,以确保其导向作用
(7)应确保各导柱、导套及导向孔的轴线平行,以及同轴度要求,否则将影响合模的准确性,甚至损坏导向零件
(8)导柱工作部分的配合精度采用H7/f7(低精度时可采用H8/f8或H9/f9);导柱固定部分的配合精度采用H7/k6(或H7/m6)。
导套与安装之间一般用H7/m6的过渡配合,再用侧向螺钉防止其被拔出
(9)对于生产批量小、精度要求不高的模具,导柱可直接与模板上加工的导向孔配合。
通常导向孔应做志通孔;如果型腔板特厚,导向孔做成盲孔时,则应在盲孔侧壁增设通气孔,或在导柱柱身、导向孔开口端磨出排气槽;导向孔导滑面的长度与表面粗糙度可根据同等规格的导套尺寸来取,长度超出部分应扩径以缩短滑配面。
2.7.2带头导柱
导向机构能在注塑过程中和模具中起到定位作用,导向作用,承受冲模过程中一定的侧向压力,承受模具本身重量的作用。
一般而言,导柱前端应倒圆角、半球形或做成锥台形,以使导柱能顺利地进入导套。
导柱表面有多个环形油槽,用于储存润滑油,减小导柱和导套表面的摩擦力。
根据GB/T4169.4-2006塑料注射模零件第4部分:
带头导柱示意图如下:
图2-7-1带头导柱规格示意图
由标准模架知L=250mm,D1=30mm,D=25mm,h=8mm,L1=50mm
材料:
T10A
带头导柱25
250
50GB/T4169.4-20064根
2.7.3带头导套
导套与导柱一起构成了导向系统,使导向系统具有在模具中不可缺少的作用。
为使导柱顺利进入导套,导套的前端应倒圆角。
导向孔最好做成通孔,以利于排除孔内的空气。
如果模板较厚,倒空必须做成盲孔时,可在盲孔的侧面打一个小孔排气或在导柱的侧壁磨出排气槽。
根据GB/T4169.3-2006塑料注射模具零件第3部分:
带头导套示意图如下:
图2-7-2带头导套规格示意图
D=35mm;D1=48mm;D2=54mm;D3=36mm;L=140mm;h=10mm;R=5mm
材料:
T10A
带头导套35
140GB/T4169.3-20064根
2.8其他结构件设计
2.8.1复位杆
常用的复位机构多采用复位杆复位。
由于它制造简单,易于安装和调节,复位动作稳定可靠,得到了广泛的应用。
它与顶出元件同时安装在顶杆固定板上,合模时定模分型面推动复位杆并带出顶出系统同时复位。
GB/T4169.13-2006塑料注射模具零件第13部分:
复位杆示意图如下:
图2-8-1复位杆规格尺寸
D=25mm;D1=30mm;h=8mm;L=200mm
材料:
T10A
复位杆25
200GBT4169.13-2006
2.8.2定位圈
因为采用的有托唧咀,所以用定位圈配合固定在模具的面板上。
定位圈也是标准件,外径为Φ100mm,内径Φ70mm。
具体固定形式如图2-8-1所示:
图2-8-2定位圈规格示意图
D=100mmD1=35mmh=15mm
材料:
45钢
定位圈100GB/T4169.18-2006
2.8.3垫块
由于推出系统为顶杆顶出,而非手动脱模,即在模具中需要一空间收纳推杆,为了在模具中设计这一空间,则使用垫块,提供高度空间,使推杆在不工作时能存在于模具中而不影响其他部件工作。
垫块尺寸规格见下图:
图2-8-3垫块规格示意图
在标准模架中,L=400,H=130,由GB/T4169.6-2006中关于垫块尺寸的规定,取W=68,垫块材料选用45钢。
2.9注塑模温度控制系统设计
根据塑件的具体情况和实践经验,模具冷却系统的设计要点如下。
①冷却水道与成型面处应取相同的距离,使水道的排列与成型面形状相符。
②冷却水道应使成型零件表面冷却均匀,模具的温差不大。
一般情况下,冷却水道设置的数量越多,其冷却效果越好,越均匀。
③冷却水道的直径一般在φ8到φ12之间选取。
直径太小不容易加工,而直径过大,对冷却效果也有不利影响。
④冷却水道的距离应适当。
一般采用的距离为5d,当同意成型面上塑件厚度加厚时,可使水道的距离组建缩短,并靠近型腔,以取得局部冷却的效果。
⑤浇注部位由于经常接触的注射机喷嘴,而熔料首先从浇口注入,所以浇口部位是模具上温度最高的部位。
为了达到模温平衡,冷却水道应首先通过浇口部位,而熔融料流的方向