冲压模具课程设计指导说明书.docx
《冲压模具课程设计指导说明书.docx》由会员分享,可在线阅读,更多相关《冲压模具课程设计指导说明书.docx(35页珍藏版)》请在冰点文库上搜索。
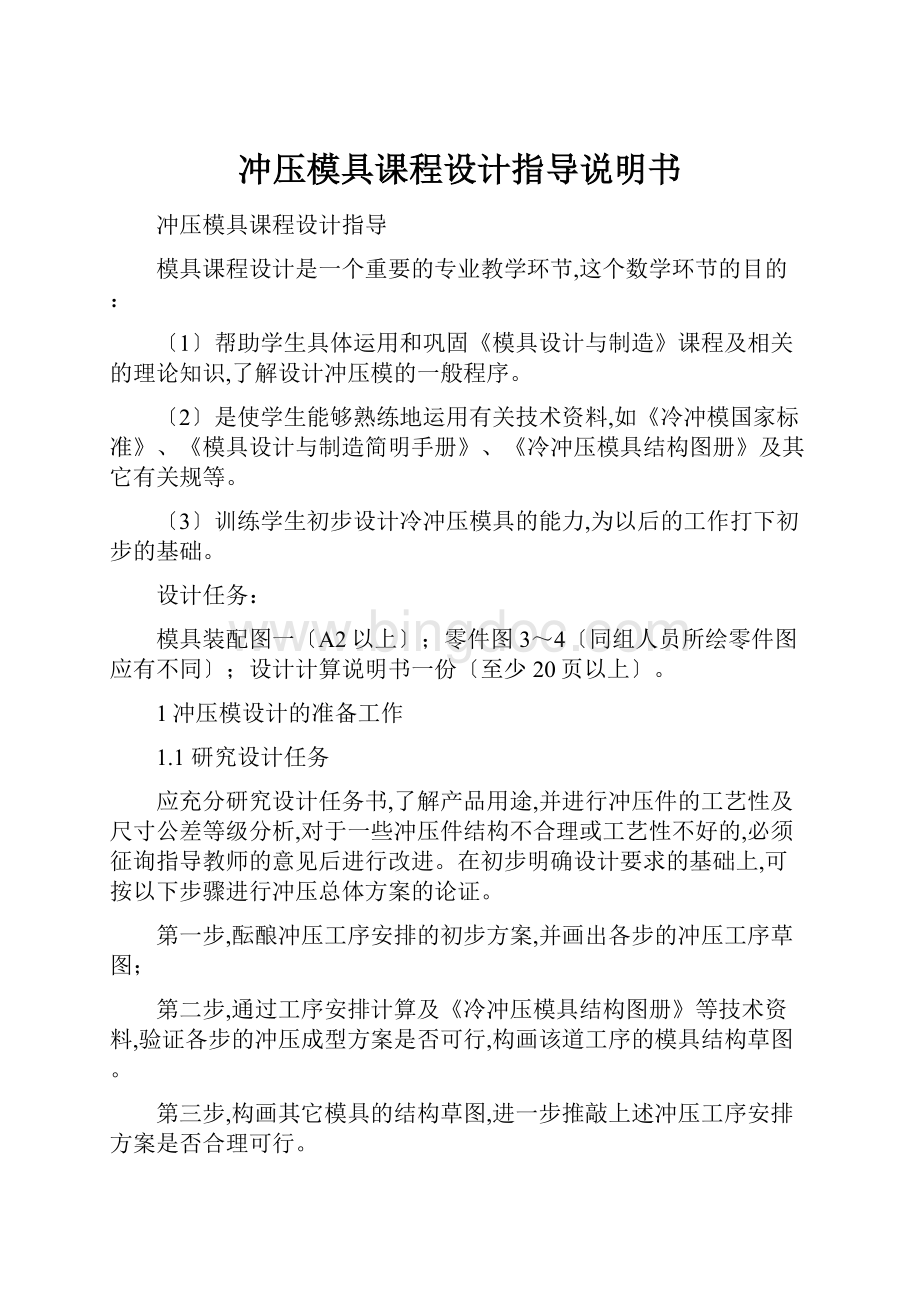
冲压模具课程设计指导说明书
冲压模具课程设计指导
模具课程设计是一个重要的专业教学环节,这个数学环节的目的:
〔1〕帮助学生具体运用和巩固《模具设计与制造》课程及相关的理论知识,了解设计冲压模的一般程序。
〔2〕是使学生能够熟练地运用有关技术资料,如《冷冲模国家标准》、《模具设计与制造简明手册》、《冷冲压模具结构图册》及其它有关规等。
〔3〕训练学生初步设计冷冲压模具的能力,为以后的工作打下初步的基础。
设计任务:
模具装配图一〔A2以上〕;零件图3~4〔同组人员所绘零件图应有不同〕;设计计算说明书一份〔至少20页以上〕。
1冲压模设计的准备工作
1.1研究设计任务
应充分研究设计任务书,了解产品用途,并进行冲压件的工艺性及尺寸公差等级分析,对于一些冲压件结构不合理或工艺性不好的,必须征询指导教师的意见后进行改进。
在初步明确设计要求的基础上,可按以下步骤进行冲压总体方案的论证。
第一步,酝酿冲压工序安排的初步方案,并画出各步的冲压工序草图;
第二步,通过工序安排计算及《冷冲压模具结构图册》等技术资料,验证各步的冲压成型方案是否可行,构画该道工序的模具结构草图。
第三步,构画其它模具的结构草图,进一步推敲上述冲压工序安排方案是否合理可行。
第四步,冲压工序安排方案经指导教师过目后,即可正式绘制各步的冲压工序图,并着手按照"设计任务书"上的要求进行课程设计。
1.2资料及工具准备
课程设计开始前必须预先准备好《冷冲模国家标准》、《模具设计与制造简明手册》、《冷冲压模具结构图册》等技术资料,及图板、图纸、绘图仪器等工具。
也可将课程设计全部或部分工作安排在计算机上用AutoCAD等软件来完成,相应地需事前调试设备及软件、准备好打印用纸及墨盒等材料。
1.3设计步骤
冲压模课程设计按以下几个步骤进行。
〔1〕分析冲压件的工艺性〔结构、尺寸、精度、材料等方面〕〔5%〕;
〔2〕拟定冲压工序安排方案、画出冲压工序图、画出待设计模具的排样图〔阶段考核比例为15%〕
〔3〕计算冲压力〔包括冲裁力、卸料力、推件力等〕、确定模具压力中心、确定凸凹模间隙,计算刃口尺寸、确定待设计模具的有关结构要素〔各个模板的外形尺寸、卸料弹簧或橡胶的自由高度等〕、选用模具典型组合等,初选压力机〔主要考虑公称压力、装模高度、滑块行程、工作台面尺寸等因素〕〔25%〕;
〔4〕设计及绘制模具装配图〔25%〕;
〔5〕设计及绘制模具零件图〔25%〕;
〔6〕按规定格式编制设计说明书〔5%〕;
〔7〕课程设计面批后或答辩〔建议对总成绩在10%的围适度调整〕。
1.4明确考核要求
根据以上6个阶段应该形成的阶段设计成果实施各阶段的质量及考核,从而形成各阶段的考核成绩,结合考勤记录及面批或答辩记录对总成绩在10%左右的围适度调整。
冲裁模的设计程序
冲裁模具结构类型选择程序
2冲裁模结构设计示
2.1排样论证的基本思路
排样论证的目的是为了画出正确的模具排样图。
一个较佳的排样方案必须兼顾冲压件的公差等级、冲压件的生产批量、模具结构和材料利用率等方面的因素。
1.保证冲压件的尺寸精度
图1所示冲压件,材料为10钢板,料厚1mm,其未注公差尺寸精度等级为IT12,属一般冲裁模能达到的公差等级,不需采用精冲或整修等特殊冲裁方式。
从该冲压件的形状来看,完全可以实现少、无废料排样法。
但该冲压件的尺度精度等级决定了应采用有废料排样法。
图1冲压件及排样图
2.考虑冲压件的生产批量
高产量,最高产量:
采用高效率高寿命模具,多为连续模
中等产量:
尽量采用典型模具结构,减少设计和制造工时
低产量:
采用简单模具,如组合冲模、钢片模、聚氨脂橡胶冲模等
该冲压件的月生产批量为3000件,属于中等批量的生产类型,因此不考虑多排、或一模多件的方案〔该方案较适宜大批量生产,约几十万件以上〕;也不考虑采用简易冲裁模常用的单、直排方案,根据成批生产的特点,再结合该冲压的形状特点,以单斜排、一模一件、级进排样方案为宜。
3.提高原材料利用率
在绘制排样图的过程中,应注意提高冲压原材料的利用率。
但提高原材料的利用率,不能以大幅提高冲裁模结构的复杂程度为代价。
图2所示是垫圈冲压件及其冲裁排样图。
如果单纯为了提高原材料的利用率而采用三排或三排以上、一模多件的冲载方案,虽然确实有助于提高原材料的利用率,但模具制造成本却随之大幅提高,其结果往往得不偿失。
排样图上搭边值设计是否合理,直接影响到原材料的利用率和模具制造的难易程度。
总是采用最小许用搭边值[amin]、[a1min]往往人为地提高了模具的制造难度,而在通常情况下却并不能提高原材料的利用率。
以一条长1000mm的料条为例,若对图2所示的垫圈冲压件以[amin]=0.8mm进行排样,可排〔1000-0.8〕/<34+0.8>=28.7个,实际为28个;若以a=1.5mm进行排样,则可排〔1000-1.5〕/<34+1.5>=28.1个。
可见每个步距上省下0.7mm长的料,最终整条料上并不能多排一个工件,两者的利用率是完全相同的。
除使用卷料进行冲压外,一般搭边值均应在[amin]的基础上圆整〔料宽尺寸也须圆整〕,以降低模具制造难度。
图2垫圈冲压件及冲裁排样图
4.模具结构论证
在保证产品尺寸公差等级的前提下,应尽量简化模具结构复杂程度,降低模具制造费用,这是设计模具的铁则。
图2所示的垫圈冲压件,因外形比较简单,且壁厚较大,所以采用复合模冲裁排样方案就比采用级进模冲裁的方案好。
倒装复合模的结构比顺装复合模简单,所以应优先考虑采用倒装复合模。
最终能否采用复合模冲裁方案以及采用何种复合模结构的关键是验算冲压件的最小壁厚。
经验算垫圈冲压件的最小壁厚,可用倒装复合模冲裁方案。
2.2选择压力机及确定压力中心示
根据图2复合模冲裁排样图,经计算模具工艺总力P∑=10.32〔tf〕,可初步选择J23-16F压力机。
记录有关技术参数供今后校核用。
最大封闭高度:
205mm;封闭高度调节量:
45mm;工作台尺寸前后:
300mm、左右:
450mm;垫板尺寸厚度:
40mm;孔径:
Φ210mm;模柄孔尺寸直径:
Φ40mm;模柄孔深度:
60mm。
计算压力中心的方法教材上已有详尽的介绍。
要计算出压力中心的精确位置既繁锁又无必要。
除了少数几种情况,例如:
精密冲裁模具、多工位自动级进模和一些造价昂贵的模具为保险起见需要精确计算外,一般情况下,可以根据对称原理把压力中心大致定在条料宽向的中心线和送料方向上最远的两个凸模〔有侧刃时,侧刃也算作凸模〕距离的中线的交合点"O"上,只要这个0点与实际压力中心之间的偏距小于模柄半径〔已知模柄直径为Φ40mm〕,就能达到模具平稳工作要求;而一旦0点与实际压力中心之间的偏距超出模柄半径的围,就要调整各凹模洞口在凹模板上的位置,使实际压力中心进入模柄半径围。
2.3冷冲模国家标准的使用
根据图2复合模冲裁排样图,结合模具制造工艺,圆形模板比矩形模板加工简便,因此本模具就采用圆形模板。
首先要计算圆形凹模板的轮廓尺寸:
厚度H=K·b1=0.4×38=15.2mm;直径D=L1+2l1=34+2×22=78mm。
查阅GB2858.4-81,根据"就近就高"的原则初定凹模周界:
H×D=16×Φ80。
1.确定模具的主要结构要素
根据垫圈产品图排样方案论证结果,已确定本模具采用倒装式复合模结构。
在此基础上,尚须确定如下结构要素。
<1>确定送料方式
模具相对于模架是采用从前往后的纵向送料方式,还是采用从右往左的横向送料方式,这主要取决于凹模的周界尺寸。
如L〔送料方向的凹模长度〕<B〔垂直于送料方向的凹模宽度〕时,采用纵向送料方式;L>B时,则采用横向送料方式;L=B时,纵向或横向均可。
就本例的圆形凹模板而言,其送料方式应采用纵向送料。
另外采用何种送料方式,还得考虑压力机本身是开式还是闭式而定。
<2>确定卸料形式
模具是采用弹压卸料板,还是采用固定卸料板,取决于卸料力的大小,其中材料料厚是主要考虑因素。
由于弹压卸料模具操作时比固定卸料模具方便,操作者可以看见条料在模具中的送进动作,且弹压卸料板卸料时对条料施加的是柔性力,不会损伤工件表面,因此实际设计中尽量采弹压卸料板,而只有在弹压卸料板卸料力不足时,才改用固定卸料板。
随着模具用弹性元件弹力的增强〔如采用矩形弹簧〕,弹压卸料板的卸料力大大增强。
根据目前情况,当材料料厚约在2mm以下时采用弹压卸料板,大于2mm时采用固定卸料板较为贴近实际。
本模具所冲材料的料厚为1mm,因此可采用弹压卸料板。
<3>模架形式
如采用纵向送料方式,适宜采用中间导柱导套模架〔对角导柱导套模架也可〕;横向送料适宜采用对角导柱导套模架:
而后侧导柱导套模架有利于送料〔纵横向均可且送料较顺畅〕,但工作时受力均衡性和对称性比中间导柱导套模架及对角导柱导套模架差一些;四角导柱导套模架则常用于大型模具;而精密模具还须采用滚珠导柱导套。
本模具采用中间导柱导套模架,一是对纵向送料方式较适宜,二是中间导柱导套模架工作时受力比较均衡、对称。
2.典型组合选择示
计算凹模周界及确定模具的主要结构是为了选用合适的模具结构典型组合。
根据本模具采用纵向送料方式、弹压卸料板、倒装复合模、中间导柱导套模架及凹模周界为H×D=16×Ф80,可从《冷冲模国家标准》查到复合模圆形厚凹模典型组合〔GB2873.3-81〕。
各模具零件的标准外形尺寸H×D如下:
〔1〕上垫板〔GB2858.6-81〕4×Ф801块;
〔2〕固定板〔GB2858.5-81〕12×Ф801块;
〔3〕凹模〔GB2858.4-81〕<22×Ф80>调整至18×Ф801块;
〔4〕卸料板〔GB2858.5-81〕10×Ф801块;
〔5〕固定板〔GB2858.5-81〕14×Ф801块;
〔6〕下垫板〔GB2858.6-81〕4×Ф801块;
本典型组合推荐使用3只M8的紧固螺钉、2只Ф8的圆柱销、3只杆部直径为Ф8的台肩式卸料螺钉、凸凹模的推荐长度为42mm、配用模架闭合高度在140~165mm之间。
有了模具结构的典型图,模具设计就大为简化。
只要根据排样图中凸模或凸凹模的位置,分别把各个凸模或凸凹模画入典型组合可,并相应地在凹模板或凸凹模上开制相应的凹模洞口及在其它零件上画出漏料孔、打料系统等,就可得到一完整又正确的装配图。
3.非标准模具的对照设计
有些矩形凹模板根据计算结果会很难选到一个合适的标准凹模板。
例如某狭长冲压件,其凹模周界的计算值:
H×L×B=20×60×125,与之最为接近的标准凹模板尺寸为:
H×L×B=20×125×125,仍相差悬殊。
解决的办法是根据H×L×B=20×125×125的标准凹模板找到模具的典型组合,同样根据该典型组合构画装配图,只是把模具的所有模板的L尺寸全部换成非标准尺寸60mm,而尺寸H及B保持不变,进行必要的有限非标准设计。
2.4绘制模具装配图示
有了模具结构典型组合图,就可以着手绘制模具装配图。
我们一般应根据模具结构典型组合图绘制模具结构草图,这样无论在布置图面、还是考虑结构细节等问题上都将带来许多便利之处。
1.图面布置规
为了绘制一美观、正确的模具装配图,必须掌握模具装配图面的布置规。
图3所示是模具装配图的图面布置示意图,可参考使用。
1-档案编号。
如果这份图纸将来要归档,就在该处编上档案号〔且档案号是倒写的〕,以便存档。
不能随意在此处填写其它容。
图3图面布置示意图
1-档案编号处2-布置主视图3-布置俯视图4-布置产品图5-布置排样图
6-技术要求说明处7-明细表8—标题栏
2-通常布置模具结构主视图。
在画主视图前,应先估算整个主视图大致的长与宽,然后选用合适的比例作图。
主视图画好后其四周一般与其它图或外框线之间应保持有约50~60mm的空白,不要画得"顶天立地",也不要画得"缩成一团",这就需要选择一合适的比例。
推荐尽量采用1:
1的比例,如不合适,再考虑选用其它《机械制图国家标准》上推荐的比例。
3-布置模具结构俯视图。
应画拿走上模部分后的结构形状,其重点是为了反映下模部分所安装的工作零件的情况。
俯视图与边框、主视图、标题栏或明细表之间也应保持约50~60mm的空白。
4-布置冲压产品图。
并在冲压产品图的右方或下方标注冲压件的名称、材料及料厚等参数。
对于不能在一道工序完成的产品,装配图上应将该道工序图画出,并且还要标注本道工序有关的尺寸。
冲压产品图的方向应与冲压方向〔即工件在模具中的位置〕一致。
特殊情况下不一致时必须用箭头注明冲压方向。
5-布置排样图。
排样图上的送料方向与模具结构图上的送料方向必须一致,排样图中应标明料宽〔带公差〕、搭边值和步距、斜排时工件的旋转角度。
通常从排样图的剖面线上可以看出是单工序模具还是连续模或复合模。
〔对于弯曲、卷边的工序要考虑材料的纤维方向〕
6-写技术要求。
简要注明对该模具的要求和注意事项,技术条件。
技术条件主要包括:
模具的闭合高度、冲裁模具的间隙、标准模架及代号及装配要求和所用的冲压设备型号等。
〔可参考国家标准的相关要求〕
7-布置明细表及标题栏。
结合图4标题栏及明细表填写示例〔其格式可参照国家标准GB/T10609.1-89,GB/T10609.2-89〕,应注意的要点如下。
〔1〕明细表至少应有序号、图号、零件名称、数量、材料、标准代号和备注等栏目;
〔2〕在填写零件名称一栏时,应使名称的首尾两字对齐,中间的字则均匀插入;
〔3〕在填写图号一栏时,应给出所有零件图的图号。
数字序号一般应与序号一样以主视图画面为中心依顺时针旋转的方向为序依次编定。
由于模具装配图一般算作图号00,因此明细表中的零件图号应从01开始计数。
没有零件图的零件则没有图号。
〔4〕备注一栏主要标标准件规格、热处理、外购或外加工等说明。
一般不另注其它容。
图4标题栏及明细表填写示例
8处布置标题栏。
作为课程设计,标题栏主要填写的容有模具名称、作图比例及签名等容。
其余容可不填。
图5倒装复合模
1-下模座 2、3-导柱 4-卸料螺钉 5-下垫板 6-凹模固定板 7-凸凹模
8-弹压橡皮 9-卸料板 10-挡料顶 11-推块 12、27-冲孔凸模 13-冲孔凸模固定板
14-开制三叉通孔的垫板 15、25、33-圆柱销 16-上模座 17、18-导套 19-模柄
20-防转销 21-打杆 22-三叉打板 23-上垫板 24-顶杆 26-凹模 28-六角螺钉
29-活动挡料销 30-半圆头螺钉 31-扭簧 32-六角螺钉
2.装配图的绘制要求
图5所示是垫圈冲孔落料复合模的装配图,在绘制模具装配图时,初学者的主要问题是图面紊乱无条理、结构表达不清、剖面选择不合理等,还有作图质量差如引出线"重叠交叉"、螺销钉作图比例失真,漏线条等错误屡见不鲜。
上述问题除平时练习过少外,更主要的是缺乏作图技巧所致。
一旦掌握了必要的技巧,这些错误是可以避免的。
结合例,下面简要地叙述绘制模具装配图的具体要求。
要说清这个问题,先要了解为什么要绘制模具装配图。
绘制模具装配图最主要的是要反映模具的基本构造,表达零件之间的相互装配关系。
从这个目的出发,一模具装配图所必须达到的最起码要求一是模具装配图中各个零件〔或部件〕不能遗漏。
不论哪个模具零件,装配图中均应有所表达;二是模具装配图中各个零件位置及与其它零件间的装配关系应明确。
下面简要叙述装配图的作图技巧。
〔1〕装配图的作图状态
冲裁模装配图主视图一般应按模具闭合状态画出〔也可一半处于闭合状态一半处于非工作状态〕,比例最好为1:
1,直观性好,有助于校核各模具零件之间的相对关系。
绘图顺序为:
先里后外,先上后下。
即先画产品,然后绘制凸模、凹模……。
可采用全剖或阶梯剖视,剖切到凸模和顶件块等旋转体时其剖面不画剖面线,有时候为了图面清晰,非旋转体的凸模也不画剖面线。
〔2〕剖面的选择
图5所示模具的上模部分剖面的选择应重点所映凸模的固定,凹模洞口的形状、各模板之间的装配关系〔即螺钉、销钉的安装情况〕,模柄与上模座间的安装关系及由打杆、打板、顶杆和推块等组成的打料系统的装配关系等。
上述需重点突出的地方应尽可能地采用全剖或半剖,而除此之外的一些装配关系则可不剖而用虚线画出或省去不画,在其它图上〔如俯视图〕另作表达即可。
模具下模部分剖面的选择应重点反映凸凹模的安装关系、凸凹模的洞口形状、各模板间的安装关系〔即螺钉、销钉如何安装〕、漏料孔的形状等,这些地方应尽可能考虑全剖,其它一些非重点之处则尽量简化。
图5中上模部分全剖了凸模的固定,凹模洞口形状及螺销钉的安装情况〔并在左面布置销钉、右面布置紧固螺钉及另一销钉显得错落有致〕,对于模柄与上模座的联接情况进行了局部剖〔并顺便画出防转销钉显得构图极为巧妙〕,而对打料系统的装配关系也尽量全剖,使其他读图者一目了然。
下模部分对凸凹模的固定,凸凹模洞口及漏料孔的形状,卸料板与卸料螺钉的联接情况,紧固螺钉与圆柱销的结构情况都进行了全剖。
而对活动挡料钉的安装情况则采取了用虚线表达的方式。
这样的布置需要设计者经过一番精心的运筹后才能获得。
〔3〕序号引出线的画法
在画序号引出线前应先数出模具中零件的个数,然后再作统筹安排。
在图5的模具装配图中,在画序号引出线前,数出整副模具中有33个零件,因此设计者考虑左方布置18个序号,右方再布置15个序号。
根据上述布置,然后用相等间距画出33个短横线,最后从模具引画零件到短横线之间的序号引出线。
按照"数出零件数目→布置序号位置→画短横线→引画序号引出线"的作图步骤,可使所有序号引出线布置整齐、间距相等,避免了初学者画序号引出线常出现的"重叠交叉"现象。
〔4〕尺寸标注
注明轮廓尺寸、安装尺寸、配合尺寸
注明闭合高度尺寸
带斜楔的模具应标出滑块行程尺寸
模具装配图绘制完成后,要审核模具的闭合高度、漏料孔直径、模柄直径及高度、打杆高度、下模座外形尺寸等与压力机有关技术参数间的关系是否正确。
本例经审核后确认满足J23-16F压力机参数要求。
3冲裁模零件设计示
3.1图形的绘制方法
按照模具的总装配图拆画模具零件图。
模具零件图既要反映出设计意图,又要考虑到制造的可能性及合理性。
零件图设计的质量直接影响模具的设计周期和造价。
零件图是零件加工的唯一依据,图中应标注全部的尺寸、公差、表面粗糙度、材料及热处理。
技术要求等。
图6凸模〔材料:
T10A〕
图形的不绘条件
画零件图的目的是为了反映零件的构造,为加工该零件提供图示说明。
那么哪些零件需要画零件图呢?
这可用一句话概括:
一切非标准件、或虽是标准件但仍需进一步加工的零件均需绘制零件图。
以图5倒装复合模为例,下模座1虽是标准件,但仍需要上面加工漏料孔、螺钉过孔及销钉孔,因此要画零件图;导柱、导套及螺销钉等零件是标准件也不需进一步加工,因此可以不画零件图。
两个互相对称的模具零件,一般应分别绘制图样;如绘在一图样上,必须标明两个图样代号!
零件图的视图布置
为保证绘制零件图正确,建议按装配位置画零件图,不要任意旋转和颠倒!
〔但轴类零件按加工位置,即一般轴心线为水平布置〕。
以图5所示的凸模26为例,装配图上该零件的主视图反映了厚度方向的结构,俯视图则为原平面的结构情况,在绘该凸模26的零件图时,建议就按装配图上的状态来布置零件图的视图,实践证明:
这样能有效地避免投影关系绘制的错误。
零件图的绘制步骤
绘制模具装配图后,应对照装配图来拆画零件图。
推荐如下步骤。
绘制所有零件图的图形,尺寸线可先引出,相关尺寸后标注,以图5为例。
模具可分为上下两大部分。
在画上半部分的零件图时,绘制的顺序一般采用"自下往上,相关零件优先"的步骤进行。
凹模26是工作零件可以首先画出;绘完凹模26的图形后,对照装配图,推块11与凹模26相关,其外形与凹模洞口完全一致,厚度应比凹模大出0.5mm,根据这一关系马上画出推块11的图形;接下来再画冲孔凸模固定板13的图形画好凸模固定板13以后,再对照模具装配图画出装在冲孔凸模板13的冲孔凸模12、冲孔凸模27等与之相关零件的图形……。
在画上模部分的零件图时,应注意经过上模座16、上垫板14、冲孔凸模固定板13及凹模26等模板上的螺销钉孔的位置一致。
在画下模部分的零件图时,一般采用"自上往下,相关零件优先"的步骤进行。
先画卸料板9的图形,然后对照装配图上的装配关系,画活动挡料钉28、挡料钉10的图形。
再画凸凹7的图形……。
在画下模的零件图时,也应注意经过卸料板9、凸凹模固定板6、下垫板5、下模座1上的螺丝钉孔的位置及凸凹模7、下垫板5、下模座1上漏料孔位置的一致。
按照上述步骤,根据装配关系对零件形状的要求,绘制各零件图的图形,能很容易地正确绘制出模具零件的图形,并使之与装配关系完全吻合。
3.2尺寸标注方法
从事模具设计的人都有这样的体会:
画图容易标注尺寸难。
将一零件图的图形绘制正确和将一零件图上的所有尺寸标注正确相比要容易得多。
然而初学者中普遍存在一种"重图形、轻尺寸标注"的倾向,一旦进行课程设计,所标注的尺寸或错误百出或紊乱不堪,令人难以读图;甚至出现螺销钉孔错位致使模具无法装配的严重错误,漏尺寸漏公差值等现象更是比比皆是。
究其原因除了平时练习少外,更为重要的是缺乏必要的方法。
进行尺寸标注时,建议根据装配图上的装配关系,用"联系对照"的方法标注尺寸,可有效地提高尺寸标注的正确率,具有较好的合理性。
基本要求:
·所有的配合尺寸和精度要求较高的尺寸都应该标注公差〔包括形位公差〕。
未注公差按照IT14级制造。
模具刃口尺寸按照计算值标注。
·模具零件在装配过程中的加工尺寸应注明"配作"、"装配后加工"等字样或者在技术要求中说明。
·所有的加工表面都应该注明表面粗糙度等级。
可根据各个表面的工作要求和精度等级来决定,具体可参考相关设计资料。
1.尺寸的布置方法
对于初学者出现尺寸标注紊乱、无条件等现象,主要是尺寸"布置"方法不当。
要使用所有标注的尺寸在图面上布置合理、条理清晰,必须很好地运筹。
图7所示的冲孔凸模固定板13的零件图中共有近20个尺寸,其中俯视图左侧布置螺销钉及顶杆过孔尺寸;下方布置顶杆过孔孔距尺寸、冲孔凸模12固定孔孔距尺寸、螺销钉孔的孔距尺寸及模板的外形直径尺寸;上方则布置孔距的角度尺寸。
主视图上布置了冲孔凸模27和12的固定孔形状尺寸、及模板的厚度等尺寸。
这种布置方法合理地利用了零件图形周围的空白,既条理分明、又方便了别人读图。
尺寸布置还要求其它相关零件图相关尺寸的"布置地"尽量一致。
如图8所示的上垫板14中的尺寸就参照了图7中布置方法,尽量地作到"同一尺寸在图纸的同一地点出现"。
如Ф9、Ф7、Ф30、Ф56、Ф80、30°、厚度14等尺寸的"布置地"基本上同图7冲孔凸模固定板零件图中的"布置地"相同。
这样的尺寸标注方式极便利了读图者。
学生要确立"图纸主要是"画给别人看的!
"的观念,学习与借鉴本例中的尺寸布置方法。
图7冲孔凸模固定板〔材料:
Q235〕图8开制三叉型孔的上垫板〔材料:
45〕
2.尺寸标注的思路
要使尺寸标注正确,就要把握尺寸标注的"思路"。
前面要求绘制所要零件图的图形而先不标注任何尺寸,就是为了在标注尺寸时能够统筹兼顾,用一种正确的"思路"来正确地标注尺寸。
下面以图5倒装复合模为例阐述尺寸标注的"思路"。
<1>标注工作零件的刃口尺寸
根据模具设计法则,先标注基准件上刃口尺寸〔即冲孔凸模和落料上的刃口尺寸〕,再标注对应件上的刃口尺寸〔即凸凹模上的刃口尺寸〕;但符合模中也可将凸凹模作为基准件,凸模、凹模作为对应件进行尺寸标注。
所有零件图的图形绘好后,先找出本模具的工作零件即凸凹模7、冲孔凸模12和27、落料凹模26,把着三图纸对照起来,按照尺寸布置后安排好的"地点"标注刃口尺寸。
这样可保