基于PLC的加热炉温控制系统设计.docx
《基于PLC的加热炉温控制系统设计.docx》由会员分享,可在线阅读,更多相关《基于PLC的加热炉温控制系统设计.docx(36页珍藏版)》请在冰点文库上搜索。
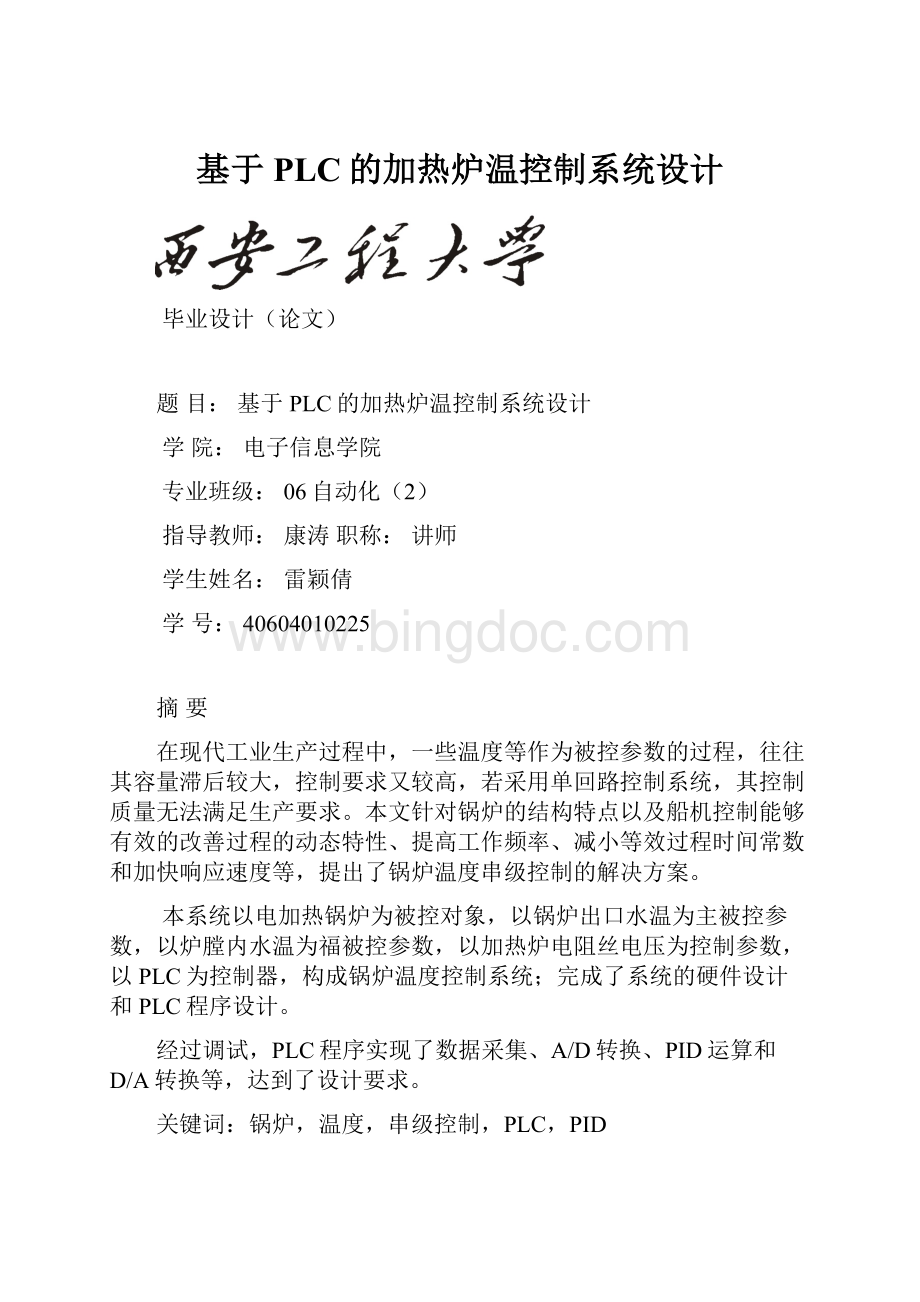
基于PLC的加热炉温控制系统设计
毕业设计(论文)
题目:
基于PLC的加热炉温控制系统设计
学院:
电子信息学院
专业班级:
06自动化
(2)
指导教师:
康涛职称:
讲师
学生姓名:
雷颖倩
学号:
40604010225
摘要
在现代工业生产过程中,一些温度等作为被控参数的过程,往往其容量滞后较大,控制要求又较高,若采用单回路控制系统,其控制质量无法满足生产要求。
本文针对锅炉的结构特点以及船机控制能够有效的改善过程的动态特性、提高工作频率、减小等效过程时间常数和加快响应速度等,提出了锅炉温度串级控制的解决方案。
本系统以电加热锅炉为被控对象,以锅炉出口水温为主被控参数,以炉膛内水温为福被控参数,以加热炉电阻丝电压为控制参数,以PLC为控制器,构成锅炉温度控制系统;完成了系统的硬件设计和PLC程序设计。
经过调试,PLC程序实现了数据采集、A/D转换、PID运算和D/A转换等,达到了设计要求。
关键词:
锅炉,温度,串级控制,PLC,PID
ABSTRACT
Inmodernindustrialproduction,somecourse'scapacityoftenlagsbehindrelativelylargely,controlalsoexpectrelativelymuchregardingtemperature,etc,ifadoptthecontrol
systemofsinglecircuit,itsqualityofcontrolisunabletomeettheproductionrequirement.Becausethebunchesofcontrolcanimprovethedynamiccharacteristicofthecourseeffectively,improveoperatingfrequency,reducingthetimeconstantoftheequivalentcourseandacceleratingtheresponsespeed,etc.Thistexthaveproposedonebunchofsolutionsofcontrolofboilertemperature.
Thissystemleavestargetofaccusingofonboilerwithelectricity,exportwatertemperature.Withboilerforaccuseofparametermainly,regardtheburnerhearthwatertemperatureasonepairofparametersofaccusingof,regardvoltageofresistancewireoftheheatingfurnaceasthecontrolparameter,regardPLCasthecontroller,formonebunchofcontrolsystemsofboilertemperature;FinishthedesigningofsystematichardwareandtheprogramwithPLC.
Throughdebugging,PLCprocedurehasrealizedthedatagathering,A/Dchanging,PIDoperationandD/Achanging,etc,hasreachedthedesigningrequirement.
KEYWORDS:
boiler,temperature,bunchesofcontrol,plc,pid
前言
随着我国国民经济的快速发展,锅炉的使用范围越来越广泛。
而锅炉温度控制是工业生产过程中经常遇到的过程控制,有些工艺过程对其温度的控制效果直接影响着产品的质量,因而设计一种较为理想的温度控制系统是非常必要的。
而锅炉系统是一个具有时变和时滞的比较复杂的系统,因此,对锅炉温度进行控制是工业过程控制中一个重要而且困难的问题。
由于PLC具有高可靠性、易于实现等优点,在工业控制领域中得到了广泛的应用。
进入21世纪以来,PLC已经由原来的逻辑控制器发展成具有较强的数据处理能力、通讯能力的标准工控设备,用其进行各种算法的实现是工控领域的发展趋势。
本设计以锅炉为被控对象,以锅炉水温为主被控参数,以加热炉电阻丝电压为控制参数,以PLC为控制器,;采用PID算法,运用PLC梯形图编程语言进行编程,实现锅炉温度的自动控制。
本文对锅炉温度控制系统的硬件和软件都进行了介绍,全文主要有5个部分。
第1部分是对锅炉温度控制系统的总体方案的介绍。
控制总体方案的设计是系统设计的核心。
若设计方案设计不正确,则无论选用何种先进的过程控制仪表或计算机系统,其安装如何细心,都不可能使系统在工业生产过程中发挥良好的作用,甚至系统不能运行。
第2部分是对锅炉温度控制系统控制算法的选择和参数的设置进行了介绍。
采用合适的控制算法能更好地对整个系统进行控制。
第3部分是锅炉液位控制系统硬件的设计,对选择的仪表、设备等的性能、使用方法和接口要求等进行了介绍。
第4部分是对锅炉液位控制系统软件程序的编制,主要是采用PLC梯形图编程语言进行编程,并写出相应的流程图和地址分配。
第5部分是对锅炉温度控制系统的调试与实验。
其中包括单元电路调试、程序调试、系统调试、系统试验和结果分析。
由于本人水平有限,错误和疏漏之处在所难免,敬请各位老师和同学批评指正。
第1章控制系统总体方案
1.1概述
随着我国国民经济的快速发展,锅炉的使用范围越来越广泛。
而锅炉温度控制是工业生产过程中经常遇到的过程控制,有些工艺过程对其温度的控制效果直接影响着产品的质量和产量。
现代锅炉的生产过程可以实现高度的机械化,这就为锅炉的自动化提供了有利条件。
锅炉自动化是提高锅炉安全性和经济性的重要措施。
目前,锅炉的自动化主要包括自动检测、自动调节、程序控制、自动保护和控制计算五个方面。
实现锅炉自动化能够提高锅炉运行的安全性、经济性和劳动生产率,改善劳动条件,减少运行人员。
锅炉是工业企业重要的动力设备,其任务是供给合格稳定的蒸汽或热水,以满足负荷的需要。
锅炉设备是一个复杂的控制对象,燃气燃油锅炉主要输入变量包括负荷、给水、燃料量、送风和引风量等,主要调节变量包括水位、温度及压力、烟气氧量和炉膛负压等;电加热锅炉主要输入变量包括负荷、锅炉给水和电阻丝电压等,主要调节变量包括水位和温度等。
锅炉生产过程的各个主要参数都必须严格控制。
锅炉系统是一个具有时变和时滞的比较复杂的系统,因此,对锅炉温度进行控制是工业过程控制中一个重要而且困难的问题。
在锅炉自动控制系统中,除了应用基于反馈控制原理而设计的各种调节器系统以外,计算机技术的应用也越来越普及。
由于PLC具有高可靠性、易于实现等优点,在工业控制领域中得到了广泛的应用。
进入21世纪以来,PLC已经由原来的逻辑控制器发展成具有较强的数据处理能力、通讯能力的标准工控设备,用其进行各种算法的实现是工控领域的发展趋势。
本设计以电加热锅炉为被控对象,以锅炉水温为被控参数控参数,以加热炉电压为控制参数,以PLC为控制器,构成锅炉温度控制系统,实现锅炉水温的定值控制。
1.2控制方式的确定
自动控制方式一般有两种:
即开环控制和闭环控制。
开环控制是指控制装置与被控对象之间只有按顺序工作,没有反向联系的控制过程,按这种方式组成的系统称为开环控制系统,其特点是系统的输出量不会对系统的控制作用发生影响,没有自动修正或补偿的能力。
开环控制没有反馈环节,系统的稳定性不高,响应时间相对来说很长,精确度不高,使用于对系统稳定性精确度要求不高的简单的系统.。
人工控制一般是开环控制。
比如人工转换电扇档位实现转速的控制。
闭环控制有反馈环节,从输出量变化取出控制信号作为比较量反馈给输入端控制输入量,一般这个取出量和输入量相位相反,所以叫负反馈控制。
通过反馈系统使系统的精确度提高,响应时间缩短,适合于对系统的响应时间,稳定性要求高的系统。
自动控制通常是闭环控制。
比如家用空调温度的控制。
PID就是应用最广泛的闭环控制器。
如图1-1所示,系统是用于电加热炉温度控制系统的闭环控制系统的PID闭环控制系统,系统目标设定值为期望的加热炉温度,闭环控制器的反馈值通过温度传感器测得,并经A/D变换转换为数字量;目标设定值与温度传感器的反馈信号相减,其差送入PID控制器,经比例、积分、微分运算,得到叠加的一个数字量;该数字量经过上限、下限限位处理后进行D/A变换,输出一个电压信号去控制固态继电器,以控制加热炉的温度。
该系统的PID控制器一般采用PLC提供的专用模块(本系统采用FB58模块),也可以采用编程的方法(如PLC编程、高级语言编程或组态软件编程等)生成一个数字PID控制器。
同时,其它功能如A/D、D/A都由PLC实现,加热炉的反馈信号直接送PLC采集,控制固态继电器的电压信号也由PLC送出,从而控制加热炉的温度。
图1.1电加热炉温度控制系统的闭环控制系统应用实例
综上所述,根据系统工艺要求,决定在系统设计中采用闭环控制方式。
1.3温度传感器的选择
温度是一个基本的物理量,自然界中的一切过程无不与温度密切相关。
温度传感器是最早开发,应用最广的一类传感器。
根据美国仪器学会的调查,1990年,温度传感器的市场份额大大超过了其他的传感器。
从17世纪初伽利略发明温度计开始,人们开始利用温度进行测量。
真正把温度变成电信号的传感器是1821年由德国物理学家赛贝发明的,这就是后来的热电偶传感器。
50年以后,另一位德国人西门子发明了铂电阻温度计。
在半导体技术的支持下,本世纪相继开发了半导体热电偶传感器、PN结温度传感器和集成温度传感器。
与之相应,根据波与物质的相互作用规律,相继开发了声学温度传感器、红外传感器和微波传感器。
这里我们主要介绍热电阻和热电偶。
1.热电偶
工业热电偶作为测量温度的传感器,通常和显示仪表、记录仪表和电子调节器配套使用,它可以直接测量各种生产过程中不同范围的温度。
若配接输出4-20mA、0-10V等标准电流、电压信号的温度变送器,使用更加方便、可靠。
对于实验室等短距离的应用场合,可以直接把热电偶信号引入PLC进行测量。
热电偶的工作原理是,两种不同成份的导体,两端经焊接,形成回路,直接测量端叫工作端(热端),接线端子端叫冷端,当热端和冷端存在温差时,就会在回路里产生热电流,这种现象称为热电效应;接上显示仪表,仪表上就会指示所产生的热电动势的对应温度值,电动势随温度升高而增长。
热电动势的大小只和热电偶的材质以及两端的温度有关,而和热电偶的长短粗细无关。
根据使用场合的不同,热电偶有铠装式热电偶、装配式热电偶、隔爆式热电偶等种类。
装配式热电偶由感温元件(热电偶芯)、不锈钢保护管、接线盒以及各种用途的固定装置组成。
铠装式热电偶比装配式热电偶具有外径小、可任意弯曲、抗震性强等特点,适宜安装在装配式热电偶无法安装的场合,它的外保护管采用不同材料的不锈钢管,可适合不同使用温度的需要,内部充满高密度氧化绝缘体物质,非常适合于环境恶劣的场合。
隔爆式热电偶通常应用于生产现场伴有各种易燃、易爆等化学气体的场合,如果使用普通热电偶极易引起气体爆炸,则在这种场合必须使用隔爆热电偶。
热电偶传感器有自己的优点和缺陷,它灵敏度比较低,容易受到环境干扰信号的影响,也容易受到前置放大器温度漂移的影响,因此不适合测量微小的温度变化。
由于热电偶温度传感器的灵敏度与材料的粗细无关,用非常细的材料也能够做成温度传感器。
也由于制作热电偶的金属材料具有很好的延展性,这种细微的测温元件有极高的响应速度,可以测量快速变化的过程,如燃烧和爆炸过程等。
对一般的工业应用来说,为了保护感温元件避免受到腐蚀和磨损,总是装在厚厚的护套里面,外观就显得笨大,对于温度场的反应也就迟缓得多。
使用热电偶的时候,必须消除环境温度的波动对测量带来的影响。
有的把它的自由端放在不变的温度场中,有的使用冷端补偿器抵消这种影响。
当测量点远离仪表时,还需要使用热电势率和热电偶相近的导线来传输信号,这种导线称为补偿导线。
2.热电阻
热电阻是中低温区最常用的一种温度测量元件。
热电阻是基于金属导体的电阻值随温度的增加而增加这一特性来进行温度测量的。
当电阻值变化时,二次仪表便显示出电阻值所对应的温度值。
它的主要特点是测量精度高,性能稳定。
其中铂热电阻的测量精度是最高的。
铂热电阻根据使用场合的不同与使用温度的不同,有云母、陶瓷、簿膜等元件。
作为测温元件,它具有良好的传感输出特性,通常和显示仪、记录仪、调节仪以及其它智能模块或仪表配套使用,为它们提供精确的输入值。
若做成一体化温度变送器,可输出4-20mA标准电流信号或0-10V标准电压信号,使用起来更为方便。
热电阻大都由纯金属材料制成,目前应用最多的是铂和铜。
此外,现在已开始采用铬、镍、锰和铑等材料制造热电阻。
根据使用场合的不同,热电阻也有铠装式热电阻、装配式热电阻、隔爆式热电阻等种类,与热电偶类似。
铂电阻的工作原理是,在温度作用下,铂热电阻丝的电阻值随温度变化而变化,且电阻与温度的关系即分度特性符合IEC标准。
分度号Pt100的含义为在0℃时的名义电阻值为100Ω,目前使用的一般都是这种铂热电阻。
此外还有Pt10、Pt200、Pt500和Pt1000等铂热电阻,Cu50、Cu100的铜热电阻等。
本设计选用镍铬-镍硅N型热电偶。
1.4微型计算机的选择
工业中常用的控制器有工业控制计算机、单片机和可编程控制器等。
与其它几种控制器相比较,可编程控制器是综合了计算机技术、自动化技术与继电器逻辑控制概念而开发的一代新型工业控制器,是专为工业环境应用而设计的。
它可以取代传统的继电器完成开关量的控制,比如,将行程开关、按钮开关、无触点开关或敏感元器件作为输入信号,输出信号可控制电动阀门、开关、电磁阀和步进电机等执行机构。
它采用可编程的存储器,在其内部存储,执行逻辑运算,顺序控制、定时计数和算术运算等操作的指令,通过数字式、模拟式的输入和输出控制各种类型的机械和生产过程实现自动化。
工业控制采用PLC,显示了突出的优越性,因它可对用户提出的生产控制要求和意见,能方便地在现场进行程序修改和调试,使系统的灵活性大大增强。
内部的软继电器使系统在控制中能严格地起到互锁作用,增加了系统的可靠性,简化设备,维修方便。
而且,随着PLC的发展,在硬件、软件方面都会有更先进的计数出现。
针对系统的特点,分析各控制器的优缺点,采用PLC作为本次设计的控制器。
具体比较如下:
首先,PLC和PC控制相比,具有以下优点:
(1)对低端应用,PLC具有极大的性能价格比优势.工控机的价格较高,将它用于小型开关量控制系统以取代继电器控制,无论是在体积和价格上都很难接受,可靠性也远不如PLC。
(2)PLC的可靠性无可比拟,故障停机时间最少.基本WindowsNT/2000/XP操作系统的IPC
控制系统,在实时任务处理,长期稳定运行,抗病毒和恶意攻击等方面还存在较大的问题.IPC控制系统在可靠性和安全性等方面还未获得广泛的认同。
(3)PLC是专为工厂现场应用环境设计的,结构上采取整体密封或插件组合型,对印制板,电源,机架,插座的制造和安装,均采取了严密的措施。
(4)PLC是使用专门为工业设计的编程语言,这些语言简单易学.工控机如果用VB,VC等语言来编程,需要花更多时间来学习,编程的效率也没有PLC高.如果使用Windows操作系统,其稳定性远远不如PLC,时间控制精度也较差。
(5)与PC机发展太快相比,PLC产品可以长期供货,并提供长期的技术支持。
(6)PLC有庞大的有经验的设计人员,维护人员和技术支持系统。
其次,与单片机相比,具有以下优点:
1.由专业大公司精心设计的硬件和软件系统,功能强大、可靠性好。
2.编程方法简单易学,即使是不熟悉电脑的工程师也可以用它开发复杂的控制系统。
3.抗干扰能力强,适用于环境恶劣的工业控制场合。
4.有丰富的扩展模块和联网能力,可以做成大型复杂的工业控制系统。
再次,目前在张力、速度、液位特别是温度等过程控制中,经常使用温控器等专用控制器或用户自制设备。
这些控制器虽然使用和设置比较简单且控制针对性强,但是用途比较单一,控制范围有限,同时用户自身的经验技巧不易应用到其中。
近年来,随着技术的发展,
PLC的处理速度越来越快,功能也越来越丰富。
因此,采用PLC进行PID控制可以逐渐取代一些传统的控制手段。
就以温度为例,可以比较出采用PLC的优点。
通常所使用的温度控制器适用于单纯的单回路温度控制,而PLC可以实现多回路的整体控制,相比主要有以下的特点:
在多点加热时,可以错开加热导通时序,避免同时导通引起的大电流;在控制过程中可以自由简便地修改设定值及其它参数;可以定时自动执行所需的控制曲线;可以使用相位控制,降低冲击电流、峰值电流,减少加热器频繁冷热变化引起的热压力;可以同时控制系统或机械中的其它动作;可以实现多种报警功能等等。
最初的PLC主要是用于取代继电器进行顺序控制,其后又逐步扩充了数值运算、模拟量、电机控制、网络通信。
从发展趋势看,PID控制特别是温度控制将是今后PLC应有的功能。
综上,针对系统的工艺机构及要求,最后选择了S7-200的小型机CPU221和模拟量EM231等模块。
1.5系统的原理框图
加热炉温度控制系统基本构成如图1.2所示,它由PLC主控系统、固态继电器、加热炉、温度传感器等4个部分组成。
图1.2加热炉温度控制系统基本组成
加热炉温度控制实现过程是:
首先温度传感器将加热炉的温度转化为电压信号,PLC主控系统内部的A/D将送进来的电压信号转化为西门子S7-200PLC可识别的数字量,然后PLC将系统给定的温度值与反馈回来的温度值进行比较并经过PID运算处理后,给固态继电器输入端一个控制信号控制固态继电器的输出端导通与否从而使加热炉开始加热或停止加热。
既加热炉温度控制得到实现。
其中PLC主控系统为加热炉温度控制系统的核心部分起着重要作用。
第2章控制算法的选择和参数计算
2.1控制算法的选择
在温度自动控制中,比较常见的几种算法有PID控制、模糊控制、纯滞后补偿、智能控制等。
PID控制是比例、积分和微分三种动作的合成作用,其作用是使被控制对象达到并保持于设定值(SV),当SV发生变化时,能使受控对象快速达到新的目标值。
通常,在控制系统中有一定容量的储能元件,因此系统中常会有一定的惯性和时间上的滞后,负载的变化以及电源系统的干扰都会给控制带来影响,造成系统参数的变化,从而使控制性能改变。
采用PID调节,可对系统偏差进行比例调节,引入积分环节,对偏差进行积分,提高了系统控制精度和抗外界干扰能力。
引入微分环节,用于克服系统的惯性滞后,从而提高系统的稳定性。
这就大大提高了控制系统的性能和品质。
PID调节是经典控制理论中最典型的控制规律,在以往的模拟控制系统中得到了广泛的应用,对相应的控制对象进行控制时获得了比较满意的结果。
作为一种非常简便、有效的控制方法,PID控制长期以来一直被广泛用于温度、液位、张力、压力、速度等过程控制系统中。
虽然在多年的实际应用中,也出现了多种改进型的PID算法,例如模糊PID控制、智能PID控制等,但是常规的PID控制算法对大多数控制系统已经能够满足误差精度要求,因此许多用于过程控制的设备都采用常规的PID控制算法。
此次方案的设计也不例外。
2.2参数的计算
在工业生产中,一般用闭环控制方法来控制温度、压力、流量、速度这一类连续变化的模拟量,无论是使用模拟调节器的模拟控制系统还是使用计算机(包括PLC)的控制系统,PID(ProportionalIntegralDifferential,即比例-积分-微分调节)都因其良好的控制效果,得到了广泛的应用。
利用可编程序控制器(PLC)实现对模拟量的PID闭环控制,具有性能价格比高、用户使用方便、可靠性高、抗干扰能力强等特点。
用PLC对模拟量进行数字PID控制时,可采用3种方法:
使用PID过程控制模块、使用PLC内部的PID功能指令、或者用户自己编制PID控制程序。
前两种方法要么价格昂贵,在大型控制系统才使用;要么算法固定,不够灵活。
因此,如果有的PLC没有PID功能指令,或者虽然可以使用PID指令,但是希望采用其他的PID控制算法,此时只能采用第三种方法,即自编PID控制程序。
在此研究的正是这种方法。
采用PID控制时,Kp、Ts、Td的设置直接影响最终的控制技术。
分别或组合改变这三个参数,可以使受控对象的响应时间、超调、稳态误差等指标达到用户要求,因此Kp、Ts、Td这三个参数的确定是PID控制的一个重要环节
2.2.1PID算法
在过程控制系统中,PID调节器的输入输出关系式为:
mv(t)=Kp[ev(t)+
∫ev(t)dt+TDdev(t)/dt]+M
式中:
误差信号ev(t)=sv(t)-pv(t),mv(t)是调节器的输出信号,KP是调节器的比例系数,TI和TD分别是积分时间常数和微分时间常数,M是偏移量。
式(3-1)中等号右边的前3项分别是比例、积分、微分部分,它们分别与误差、误差的积分和微分成正比。
如果取其中的一项或两项,就可以组成P、PI或PD调节器。
基于PLC的闭环控制系统如图3-1所示,虚线部分在PLC内。
图中的sv(n),pv(n),ev(n),mv(n)均为第n次采样时的数字量,pv(t),mv(t),c(t)为模拟量。
假设采样周期为TS,系统开始运行的时刻为t=0,用矩形积分近似精确积分,用差分近似精确微分,将式(3-1)离散化,第n次采样时控制器的输出为
mv(n)=Kpev(n)+KI
+KD[ev(n)-ev(n-1)]+M (3-2)
式中的KI=KpTS/TI,KD=KpTD/TS,分别是积分系数和微分系数。
2.2.2PID参数的整定
(1)确定整定方法
假设采样周期为T,系统开始运行的时刻为t=0,则第k次采样时控制器的输出为:
u(k)=kp[e(k)+
+T
]+M(3-3)
这即是PID规律的离散化形式,应指出的是,按式(3-3)计算u(k)时,为PID位置控制算式,其输出值与过去所有状态有关,计算时要占用大量的内存和花费大量的时间。
△u(k)=u(k)-u(k-1)=kp{e(k)-e(k-1)+
e(k)+
[e(k)-2e(k-1)+e(k-2)]}+M(3-4)
按式(3-4)计算在时刻k时的输出量u(k),只需用到采样时刻k的偏差值e(k),以及向前递推一次及两次的偏差值e(k-1)、e(k-2)和向前推一次的偏差u(k-1),此式即为增量形式的PID采样调节的控制方程。
这大大节约了内存和计算时间。
为此,可选控制式:
u(k)=u(k-1)+kp{e(k)-e(k-1)+
e(k)+
[e(k)-2e(k-1)+e(k-2)]}+M
(3-5)
参数整定的实质是通过改变调节器的参数,使