机械专业切管机设计毕业论文.docx
《机械专业切管机设计毕业论文.docx》由会员分享,可在线阅读,更多相关《机械专业切管机设计毕业论文.docx(70页珍藏版)》请在冰点文库上搜索。
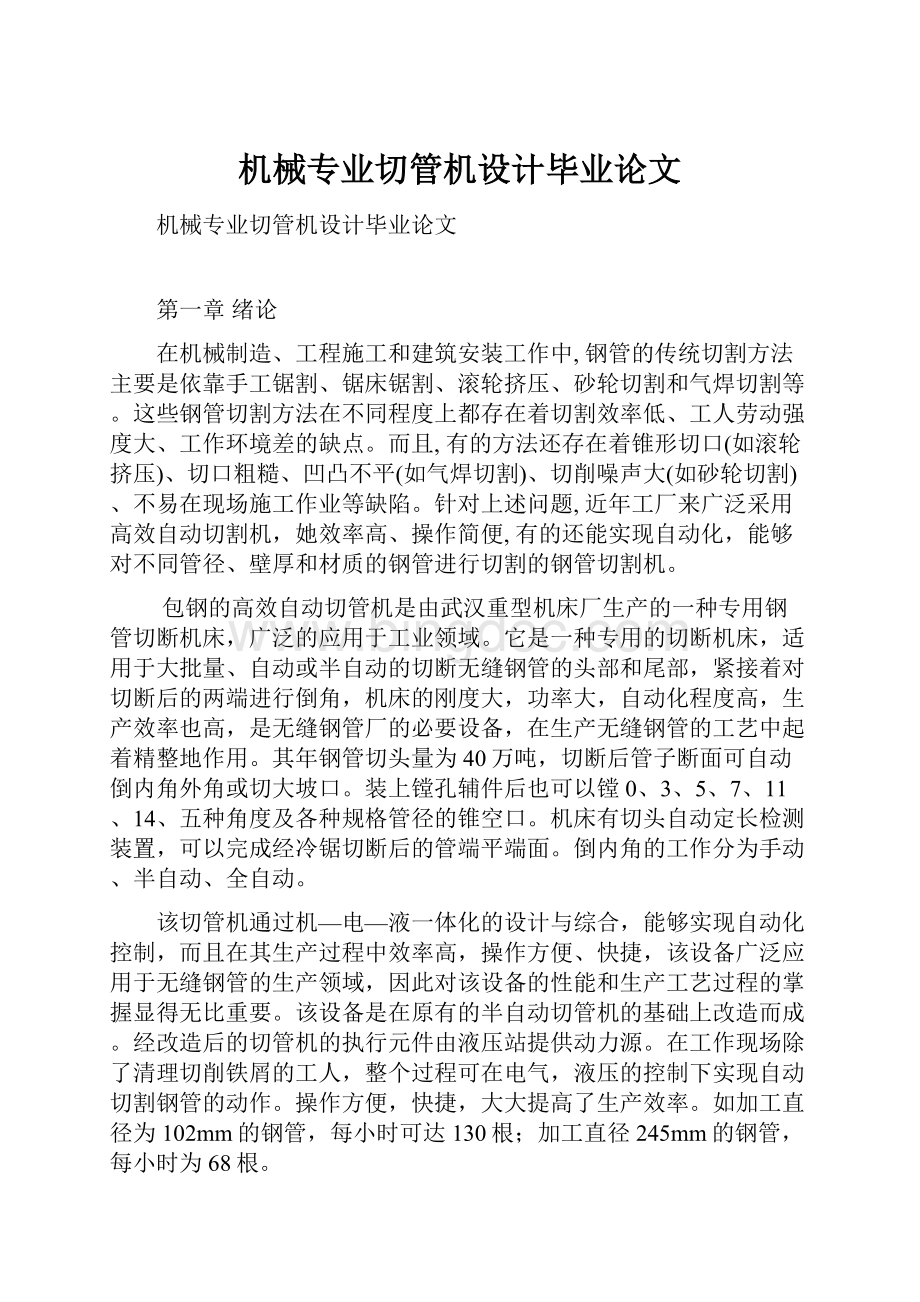
机械专业切管机设计毕业论文
机械专业切管机设计毕业论文
第一章绪论
在机械制造、工程施工和建筑安装工作中,钢管的传统切割方法主要是依靠手工锯割、锯床锯割、滚轮挤压、砂轮切割和气焊切割等。
这些钢管切割方法在不同程度上都存在着切割效率低、工人劳动强度大、工作环境差的缺点。
而且,有的方法还存在着锥形切口(如滚轮挤压)、切口粗糙、凹凸不平(如气焊切割)、切削噪声大(如砂轮切割)、不易在现场施工作业等缺陷。
针对上述问题,近年工厂来广泛采用高效自动切割机,她效率高、操作简便,有的还能实现自动化,能够对不同管径、壁厚和材质的钢管进行切割的钢管切割机。
包钢的高效自动切管机是由武汉重型机床厂生产的一种专用钢管切断机床,广泛的应用于工业领域。
它是一种专用的切断机床,适用于大批量、自动或半自动的切断无缝钢管的头部和尾部,紧接着对切断后的两端进行倒角,机床的刚度大,功率大,自动化程度高,生产效率也高,是无缝钢管厂的必要设备,在生产无缝钢管的工艺中起着精整地作用。
其年钢管切头量为40万吨,切断后管子断面可自动倒内角外角或切大坡口。
装上镗孔辅件后也可以镗0、3、5、7、11、14、五种角度及各种规格管径的锥空口。
机床有切头自动定长检测装置,可以完成经冷锯切断后的管端平端面。
倒内角的工作分为手动、半自动、全自动。
该切管机通过机—电—液一体化的设计与综合,能够实现自动化控制,而且在其生产过程中效率高,操作方便、快捷,该设备广泛应用于无缝钢管的生产领域,因此对该设备的性能和生产工艺过程的掌握显得无比重要。
该设备是在原有的半自动切管机的基础上改造而成。
经改造后的切管机的执行元件由液压站提供动力源。
在工作现场除了清理切削铁屑的工人,整个过程可在电气,液压的控制下实现自动切割钢管的动作。
操作方便,快捷,大大提高了生产效率。
如加工直径为102mm的钢管,每小时可达130根;加工直径245mm的钢管,每小时为68根。
该切割机的特点是:
该机床的执行元件全部采用液压传动。
由油缸顺序动作来完成切割过程。
分别为翻板油缸、托辊油缸、夹紧油缸、水平刀架油缸和倒角油缸。
各个油缸依次动作,完成相应的控制动作。
两台液压泵循环工作为切管机提供压力,液压泵的压力油分两路分别进入两组控制油缸(每组控制油缸由以上介绍的五个油缸组成)。
这两组控制油缸分别控制两个切管机进行钢管的切头和切尾动作。
每台切管机的一个工作循环如下:
1.钢管通过输送轨道输送到停料台;
2.通过翻板将停料台上的钢管翻倒另一输送轨道上去;
3.钢管经轨道输送到切割机内的调配位置,伸出的多余费钢将被切掉;
4.用滚子托架把钢管支起,使钢管能在托架上转动,并避免钢管和轨道的摩擦;
5.夹紧装置把钢管夹紧;
6.主轴旋转;
7.刀台快进—工进,使刀头接触到钢管处,然后进行切断动作;
8.切断后刀台快速退回,同时另一自动刀架对钢管进行倒角(倒内角);
9.主轴减速并停止转动;
10.夹紧装置放松;
11.托架放下;
12.钢管由输送轨道退出切割机;
13.翻板把头部切制好的钢管对齐,然后再进行切尾工作(同切头);
14.切尾动作循环同切头相同;
15.此时,即可放下另一根钢管,从而实现一个工作循环。
切割机的各个动作都是由液压控制的,本次设计的就是切割机系统的液压控制部分。
第二章总体方案的设计
2.1毕业设计任务及设计参数
2.1.1设计参数:
翻板拉杆:
速度 V升=V降=13m/min
行程 450mm
水平刀架:
管径φ180
管长25m
壁厚 8~18mm
主轴转速150r/min
主电机转速825r/min
进给量 0.4mm/r
快进速度 V进=90mm/s
快退速度 V退=90mm/s
工进行程 50mm
快进行程 160mm
快退行程 210mm
刀具材料 YT15
刀具主偏角 90°
刀具副偏角 10°
刀具耐磨时间 90min
钢种 45#
托 架:
速度 V升=V降=3.6m/min
行程 35mm
夹紧拉杆:
速度 V夹=V松=3.6m/min
行程 170mm
2.1.2设计任务:
1、完成毕业实习并上交实习报告,实习报告要求全部计算机打印;
2、完成专题外文资料翻译5000以上印刷符号,要求计算机打印;
3、完成与设计题目相关的专题小论文的撰写工作,题目自定,不小于3000汉字,要求全部计算机打印;
4、完成设计计算说明书,在2万字左右。
要求文字通顺、书写工整、条理清晰,说明透彻,计算准确、资料齐全、按统一规定格式、封面、装订成册,要求全部计算机打印。
5、制图:
要求装配图和零部件图符合工程制图规范,要求至少1张1#图纸手工绘制,其它图纸CAD或CAXA绘制,本设计要求完成如下图纸设计。
①切管机总图,0#;
②液压泵站,0#;
③液压原理图,0#;
④集成块,5+1#;
2.1.3专题部分要求
1、总体方案的设计
总体方案的确定及有关说明。
包括停料台的位置,翻板的位置,托架的位置,夹紧装置的位置,各种油缸的数量、位置,水平刀架的位置,液压装置的位置以及有关附属设备的用途、安装位置等。
2、液压系统的设计;
3、液压集成块的设计;
4、液压泵站的设计;
5、操作和设备维护;
6、结束语。
2.1.4本题目的重点和难点以及与同组其它学生所做题目的关系
本题目的重点:
液压系统的设计;
本题目的难点:
液压集成块的设计。
自己设计一个题目,与同组其他学生无关。
2.1.5可行方案的筛选方法提要
各种设计方案比较、选择、计算绘图,要求学生自己确定可行方案并筛选。
2.1.6与本设计题目相关的理论知识提要
与本设计题目相关的理论知识包括流体力学;金属材料及热处理;公差与配合;
机械设计;液压传动;电液比例技术;液压控制系统;机电控制等
2.2总体方案的确定及有关说明
2.2.1组成部分
1.钢管输送轨道
2.翻板机构
3.停料台
4.托架
5.刀台
6.夹紧装置
7.机械传动部分
8.液压控制回路
9.液压泵
10.油箱
11.液压缸
12.机架
13.其他辅助设备
2.2.2设备的安装位置及有关说明
整个系统的执行元件由液压站提供动力,液压站的压力油分两路分别到两台切管机,两台切管机分别完成切头、切尾和倒角的动作。
两台切管机之间布置的是停料台和翻板装置,以及将管道送入切管机内预定位置的输送轨道。
钢管在完成了切头的工序后被输送到另一切管机完成切尾的动作。
整个工作的过程是由控制部分发出控制信号来驱动执行元件动作实现自动化的生产。
本设备的布置如图2.1所示
图2.1设备的安装位置
2.2.3各种油缸数量的初步确定
水平刀架(倒角)油缸1个托架油缸4个
翻板油缸1个夹紧油缸1个
2.3确定液压系统方案
根据以上切割机的工作要求,设计相应的液压系统,来控制切割机的动作循环,现有以下两个方案。
2.3.1方案一:
此方案是在液压回路中的液压阀全部采用插装阀。
插装阀在高压大流量的液压系统中应用很广,由于插装元件以标准化、模块化,将几个插装式元件组合一下便可以组成复合阀。
和普通液压阀相比,它有如下优点:
1.采用锥阀结构,内阻小,响应快,密封好,泄露少。
2.机能多,集成度高,配置不同的先导控制级就能实现方向、压力、流量的多种控制。
3.通流能力大,特别适用于大流量的场合,它的最大通径可达200~250mm,通过的流量可达1000L/min。
4.结构简单,易于实现标准化,系列化。
当然插装阀也有一些缺点:
1.现在插装阀大多采用盖板式的,盖板内有油路,容易堵塞,出现故障。
2.插装阀多用二通插装阀,多个二通插装阀和各种先导阀组合,才能构成方向控制阀、压力控制阀和流量控制阀。
这就会使油路复杂,元件增多,也易出现故障。
3.插装阀的路路通问题:
由于插装阀回路都是有一个个独立的控制液阻组合起来的,因此它们动作的一致性不可能像传统滑阀系统那样可靠,如果先导油路设计不当,有可能产生所谓的瞬间路路通现象,这不但对于一些要求保压的系统或蓄能器系统是不允许的,有时甚至使整个系统瘫痪。
以翻板油缸的液压原理图为例
图2.2插装阀控制的翻板油缸液压原理图
2.3.2方案二:
此方案是在液压回路中的液压阀全部采用普通的液压阀,此方案的优点是:
1.普通液压阀容易买到,不用组合使用,连接简单。
2.系统油路简单、明了,出现故障时容易排查。
3.系统便于实现自动控制。
此方案的缺点:
1.通流能力受到一些影响。
2.密封性不太好,有泄露。
3.集成度不高。
以翻板油缸的液压原理图为例
图2.3普通阀控制的翻板油缸液压原理图
2.3.3液压系统方案的确定
参照以上两个液压系统方案的优缺点,本次设计的液压系统应简单、明了,不易出现故障,稳定性好。
系统的流量要求不太大,系统元件也不多不必高度集成,用方案二就能很好的完成设计要求,普通液压阀便于购买,维护、更换方便,组成的液压回路简单,不易出现故障。
所以选用方案二。
2.3.3.1执行元件的确定
翻板油缸:
执行的动作通过绕一轴的旋转完成将钢管从停料台翻到输送轨道上,此动作可由摆动油缸来完成。
托辊油缸:
托辊油缸完成的是直线运动,因而可选用单杆活塞双作用液压缸。
它的特点是:
有效的工作面积大,双向不对称。
夹紧油缸:
完成的是直线运动,选用单杆活塞双作用液压缸。
水平刀架(倒角)油缸:
完成的是直线运动,选用的是单杆活塞双作用液压缸。
2.3.3.2方向控制回路的确定
液压执行元件确定之后,其运动方向和运动速度的控制是拟订液压回路的核心问题。
方向控制用换向阀或逻辑控制单元来实现的。
本设计采用换向阀来实现。
翻板油缸在360度内旋转,完成180度的旋转后必须停住,等待下一动作的命令,因此选用三位四通换向法来完成动作。
托辊油缸只有上升和下降两个动作,因此可选用二位四通换向阀来完成换向动作。
夹紧油缸只有快进,夹紧,放松三个动作,可采用二位四通换向阀来完成控制动作。
水平刀架(倒角)油缸由快进、工进、快退和停止四个动作采用三位四通换向阀。
2.3.3.3制定调速方案
速度控制通过改变液压执行元件的输入或输出的流量或者利用密封空间的溶剂变化来实现。
相应的调速方式有节流调速、容积调速以及二者的结合—容积节流调速。
节流调速一般采用定量泵供油,用流量控制阀来改变输入或输出液压执行元件的流量来调节速度。
这种调速方式结构简单,由于这种系统必须用节流阀,故效率低,发热量大,多用于功率不大的场合。
此设计中考虑的效率和节能等方面的因素不选用节流调速方案。
容积调速是靠改变液压泵或液压马达的排量来达到调速的目的,其特点是没有溢流损失和节流损失,效率高。
但为了散热和补充泄漏,需要有辅助泵,此种调速方案适用于功率大、运动速度也高的液压系统。
但是对有活塞的运动速度不易控制,初步采用容积调速。
容积节流调速一般用变两泵供油,用流量控制阀调节输入或输出液压执行元件的流量并使供油量和需油量相适应。
故此系统采用容积节流调速。
2.3.3.4制定顺序动作方案
主机执行机构的顺序动作,根据设备的类型的不同,有的按固定的程序运行,有的则是随机或人为的。
工程机械的操纵机构多为手动,一般用手动多路换向阀来实现,加工机械的各执行元件的顺序动作多采用行程开关当工作部件移动到一定位置时,通过电气行程开关发出电信号给电磁铁推动电磁阀或直接压下行程阀来控制接续的动作。
本系统的执行元件采用执行元件来控制。
另外还采用压力控制,液压泵无载启动,经过一段时间,当泵正常运转后,延时继电器发出电信号使卸荷阀关闭,建立起正常的工作压力。
2.3.3.5系统的安全措施
为了使系统不因压力过大而破坏,在液压泵的压油管路上安装溢流阀,当系统的压力超过调定值的时候,溢流阀打开,液压油通过溢流阀回油箱。
2.3.3.6系统的卸荷
当系统短时间内停止工作,为了不频繁地开关电机和液压泵,在回路中设置卸荷回路,使系统的油液直接流回油箱。
2.3.3.7系统的过滤冷却回路
为了防止油液中的杂质对液压系统产生危害,在液压系统中设置过滤系统;液压系统的泵及油液在流过控制阀、弯管时有功率损失,损失的功率转化为油液的热能,使油液的温度升高,当油温过高时,就会使油液变质,从而使液压系统发生故障,所以液压系统要设置冷却系统。
2.3.3.8系统能源装置的选择
系统在整个工作过程中的流量变化很大,为了降低功率损耗,因此该系统采用变量泵向系统供油。
同时系统中加蓄能器,作为系统动力源的补充。
在蓄能器的出口处接一控制装置,当系统需要较大的流量时,控制装置打开,蓄能器和泵同时向系统供油,满足系统所需的流量。
2.4液压工作原理草图
液压工作原理草图初步拟定如图2.2所示:
图2.4液压原理草图
第三章液压部分的设计计算
3.1油缸的设计计算
油缸的材料:
选用45号钢
3.1.1翻板油缸
3.1.1.1翻板油缸的负载的确定
翻板油缸选用摆动式液压缸,可将液压能转换为机械能,实现往复摆动,回转角度为360°,它是带齿轮齿条机构的液压缸,齿条带动齿轮正反向回转并输出转矩。
本系统采用轴输出转矩,液压缸的轴与翻板油缸相连,翻板油缸可在360°内转动,每旋转180°完成一个钢管的举升动作,在360°内可以完成两个举升动作。
然后空载的情况下反转360°后继续以上的循环动作。
取钢管的长度为25m,取最大壁厚18mm,可计算钢管的重量
查得钢的密度为7.85t/m3
式(3.6)
考虑到一定的安全储备取
=2,取翻板的自重为1t
M=M管+M托=2+1=3t
图3.1翻板
如图所示的翻板取L1=L2=0.45m
在如图3.1所示的实线位置油缸的受力最大,则按实线位置进行计算:
设翻板油缸的扭矩为M缸
M1=G管×(0.45-0.09)+M翻式(3.1)
M2=M翻+M缸式(3.2)
由力矩平衡即M1=M2得
G管×0.36+M翻=M翻+M缸式(3.3)
M缸=M管×g×0.36×103=2×9.8×0.36×103=7056N·m
3.1.1.2翻板油缸的确定
由转矩计算公式经计算选用法兰UBFZS140摆动式液压缸,轴输出、双齿条结构、摆动角度360°。
(根据[4]表17-6-109)
当在额定工作压力P=6.3Mpa下工作时,转矩验算如下:
M转=2770(P-1.2),(根据[4]表17-6-109)将额定工作压力P=6.3Mpa代入上式得
M转=2770(P-1.2)=2770(6.3-1.2)=14127>7056,符合实际要求
由V升=V降=13m/min
式(3.4)
得:
∴该油缸的流量为:
Q翻=0.04836×360×9.2=160L/min式(3.5)
0.04836为每度转角用油量
(根据[4]表17-6-109)
3.1.2托架油缸
3.1.2.1托架油缸负载的确定
=2t,托辊的自重取为2t
则M=
+M辊=4t
∴G=Mg=4×9.8×103=39200N
∴每个油缸的负载为:
3.1.2.2托架油缸缸筒内径的确定
对于无杆腔的内径
式(3.7)
(根据[5]P166)
F1——液压缸的理论推力N
P——供油压力Mpa此处取为工程压力6.3Mpa(根据[12]表12.3-13)
——液压缸的机械效率,一般取为0.95
式(3.8)
(根据[5]P166)
考虑到液压缸阻力和机械部分的摩擦力取公称直径D=50mm,由机械零件设计手册第二版下册表31-5查得钢筒的外径为60mm。
对于有杆腔
F2——为液压缸的理论拉力
∵F2≦F1∴D’≦D
∴水平刀架油缸的内径取为D1=50mm。
内径为D1=50mm,由[4]表17-6-37,初步选择UYWF50×35-10型的液压缸,活塞杆直径为36mm。
3.1.2.3缸筒壁厚的验算
由上述选择的液压缸知壁厚为10mm
由D/δ=50/10=5〈10属于厚壁,按下式进行校核
式(3.9)
D为钢筒内径;
Py为钢筒试验压力,当钢筒的额定压力Pn≤16M时取Py=1.5Pn,Pn=6.3Mpa;
[σ]为钢筒材料的许用应力[σ]=σb/n=600/5=120Mpa(n为安全系数,通常取n=5);(根据[7]P81)
(验算通过)
3.1.2.4活塞杆的校核
活塞杆的材料选45号钢。
3.1.2.4.1活塞杆直径d的校核
由上述选择的液压缸知活塞杆的直径为36mm,
式(3.10)
(根据[7]P81)
(验算通过)
3.1.2.4.2活塞杆弯曲的稳定性的验算
图3.2活塞杆弯曲示意图
LB>(10~15)d,因受力完全在轴线上,主要按下式验算
F1≤Fk/nk
N式(3.11)
(根据[5]P169)
Mpa式(3.12)
式(3.13)
K——液压缸安装及导向系数K=1(后端法兰)
nk——安全系数,通常取nk=3.5~6,此处取为6
式(3.14)
Fk/nk=58211074/6=9701846N式(3.15)
∴F1(验算通过)
3.1.2.5托架油缸的确定
由以上的校核可知UYWF50×35-10型液压缸符合设计要求,此液压缸为冶金设备用的,尾部法兰连接,行程为35mm,工作压力在10Mpa时的推力为19.63KN,壁厚10mm,活塞杆直径为36mm,活塞面积为19.63cm2,活塞选用组合式活塞,车氏C形滑环密封。
该型液压缸为冶金及重型机械专门设计,属于重负载液压缸,它工作可靠,耐冲击,耐污染,适用于高温高压、环境恶劣的场合。
3.1.2.6流量的计算
托架油缸速度V升=V降=3.6m/min
Q=uA=3.6×3.14×0.052×103/4=7.065L/min式(3.16)
四个油缸的总的流量为Q总=4×Q=4×7.065=28.26L/min
3.1.3水平刀架(倒角)油缸的设计计算
3.1.3.1切削力的计算
切削及切槽过程中
主切削力:
Fz=CFzapxFzfyFzKFz式(3.17)
背吃刀力:
Fy=CFuapxFufyFuKFu式(3.18)
(根据[13]P16)
其中KFz,KFu为分力计算试中当时及加工条件和求经验公式的条件不符时各种因素对修正系数的积。
CFz,CFu决定于被加工材料和切削条件的系数
xFz,xFu,yFz,yFu,nFz,nFu分别为分力公式中切削深度ap,进给量f和切削速度Uc的指数
式(3.19)
查手册《机械加工工艺手册》p885表27-24确定以下参数
切槽及切段时:
CFz=3600,xFz=0.72,yFz=0.8
CFu=1390,xFu=0.73,yFu=0.67
KF=KMFKγoFKKγFKλsFKγξFKTF式(3.20)
刀具的主偏角
=90o,
=0.89,
=0.50
取刃倾角
,
,
前角
,
,
刀具耐用度T=90min
切断刀
由手册
ap在切断和车槽时为切削刃的长度
B=3.5-16.5mm,取B=4mm。
(根据[1][2])
∴主切削力:
Fz=CFzapxFzfyFzKFz
背吃刀力:
Fy=CFuapxFufyFuKFu
∴水平刀架油缸的负载为:
F缸=2×Fy=2×1091=2181(N)
3.1.3.2水平刀架油缸内径的确定
考虑到系统的阻力及惯性力等因素的影响,取标准直径为40mm。
由机械零件设计手册第二版下册表31-5查得钢筒的外径为50mm。
内径为D1=40mm,由机械设计手册第四版第四卷表17-6-37,初步选择UYWF40×210-10型的液压缸,活塞杆直径为28mm。
3.1.3.3钢筒壁厚的验算
由上述选择的液压缸知壁厚为10mm
由D/δ=40/10=4〈10属于厚壁,按下式进行校核
(验算通过)
3.1.3.4活塞杆的校核
活塞杆的材料选45号钢。
3.1.3.4.1活塞杆直径d的校核
由上述选择的液压缸知活塞杆的直径为28mm,
(验算通过)
3.1.3.4.2活塞杆弯曲的稳定性的验算
LB>(10~15)d,因受力完全在轴线上,主要按下式验算
F1≤Fk/nk
N
Mpa
K——液压缸安装及导向系数K=1(后端法兰)
nk——安全系数,通常取nk=3.5~6,此处取为6
Fk/nk=2129670/6=354950N
∴F1(验算通过)
3.1.3.5水平刀架油缸的确定
由以上的校核可知UYWF40×210-10型液压缸符合设计要求,此液压缸为冶金设备用的,尾部法兰连接,行程为210mm,工作压力在10Mpa时的推力为12.57KN,壁厚10mm,活塞杆直径为28mm,活塞面积为12.57cm2,活塞选用组合式活塞,车氏C形滑环密封。
3.1.3.6流量的计算
水平刀架油缸快进(退)时的流量最大
快进(退)速度V=0.54m/min
Q=uA=0.54×3.14×0.042×103/4=6.78L/min
3.1.4夹紧油缸
3.1.4.1夹紧油缸负载的确定:
工件受主切削力Fz=6082N的力的作用,要保证被夹紧不动,夹紧力所产生的摩擦力必须大于等于6082N,考虑到安全性取Fz=6090N
工件和夹紧力之间的摩擦系数为:
光滑表面
=0.15(根据[14]表6-2)
所需的最小夹紧力
F=
∴N1=N2=N3=13533N(根据[14]P275)
图3.3夹紧装置工作示意图
按照夹紧力的计算公式
FK=F×K
FK——实际所需夹紧力,F按静力平衡原理计算出的理论夹紧力
K——安全系数,通常取1.5—2.5,精加工和连续切削时取小值,粗工和断续切削时取大值,此处取K=2.5(根据[14]P276)
∴FK1=FK2=FK3=KN=2.5×13533=20299.5N
∴F夹=20299.5×3=60898.5N
3.1.4.2夹紧油缸的内径
(根据[5]P166)
考虑到液压缸阻力和机械部分的摩擦力取公称直径D=125mm,由机械零件设计手册第二版下册表31-5查得钢筒的外径为146mm。
内径为D1=125mm,由机械设计手册第四版第四卷表17-6-37,初步选择UYWF125×170-10型的液压缸,活塞杆直径为90mm。
3.1.4.3钢筒壁厚的验算
由上述选择的液压缸知壁厚为21mm
由D/δ=125/21=5.95〈10属于厚壁,按下式进行校核
(验算通过)
3.1.4.4活塞杆的校核
活塞杆的