压力管道施工教案文档格式.docx
《压力管道施工教案文档格式.docx》由会员分享,可在线阅读,更多相关《压力管道施工教案文档格式.docx(20页珍藏版)》请在冰点文库上搜索。
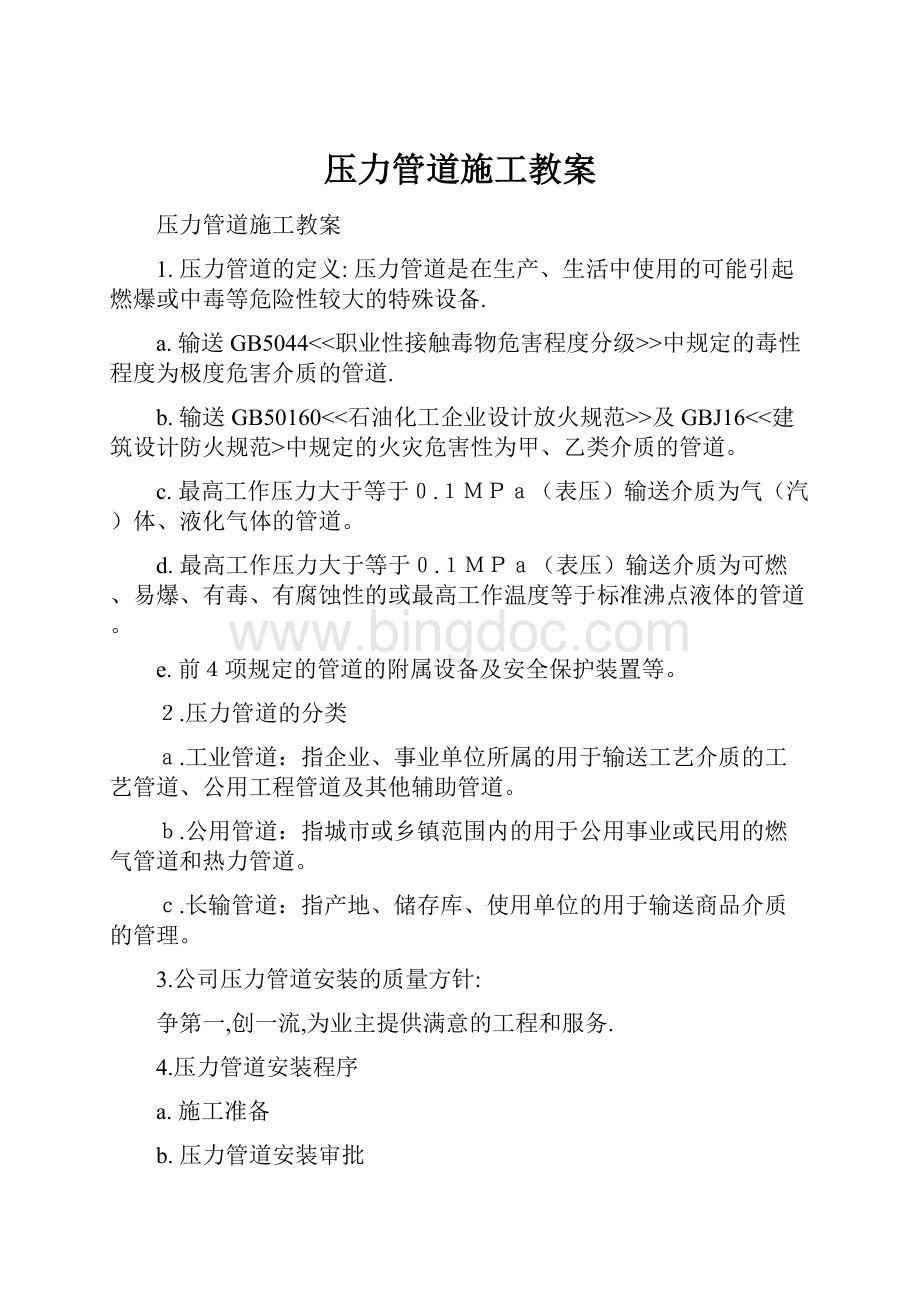
c.单线图与管道装配图的配合:
单线图与平面图;
单线图与流程图;
单线图与管口方位图;
单线图与管架位置图的配合。
4.1.3单线图的分段
单线图的分段要预先确定,安装技术员确定分段后要通报焊接技术员,并下达到施工作业队。
4.1.4焊口编号
根据单线图分段,焊接技术员预先在单线图上编制焊口编号,并在实施时及时进行调整。
4.1.5施工方案及技术交底
工艺管线安装方案
管道试压吹扫方案
焊接工艺规程(WPS)
管道施工技术交底
技术交底必须以书面的形式交到每个作业组并取得接受交底的签证.
施工技术方案的编审执行<
施工技术方案管理规定>
的规定.
4.1.6材料的发放
材料的发放应以单线图中的材料量为依据汇总下拨,现场发料必须以单线图为准,一次或分部分下发进行领料责任签证.
4.2压力管道安装审批
压力管道安装前,项目部应填写<
<
压力管道安装申请书>
和<
申请安装的压力管道概况一览表>
报综合管理员,并准备下列资料到各级质量技术监督行政部门进行审批:
a.压力管道施工方案
b.焊工合格证
c.焊接工艺评定
d.技术人员资格证书
e.焊材合格证
f.无损检测人员资格证书
4.3管线的预制
4.3.1管子的切割
钢管应用机械方法切断,大直径钢管应采用磁爬切割器自动气割;
切口表面应平整、无裂纹、重皮等缺陷,端面倾斜偏差应符合规定;
切割后的管段必须保留色标,否则应在切割前移植。
4.3.2管子的制孔
a.焊接凸台需要在管子上制孔的必须进行机械钻孔,成孔直径为凸台的内径,允差为2mm。
b.需要在管子上割孔的,开孔直径应保证凸台组对后,与主管的间隙保持在2.4—4mm范围内。
割孔后应用砂轮打磨,直至坡口表面呈现金属光泽。
c.制孔后应清除残留在主管内的切屑、熔渣和氧化皮等污物。
d.管道安装后的制孔应采取特殊措施,以保证管道内的清洁,同时进行责任人员的签字
4.3.3管道预制
a.管道预制应以单线图为依据
b.管道预制应遵守下列规定;
为保证工程质量和便于安装,应进行管线分段设计,合理选定自由管段和封闭管段;
现场连接的管子要预留50mm余量作为调整长度;
在预制件上要标记管线编号和焊口号;
管线预制时要与现场安装方向一致,防止安装时和单线图标记不一致;
管道预制时需要加临时垫片调整长度时应用石棉垫片,不允许用压铁线的方法代替。
c.管道坡口加工应采用机械加工的方法并保证坡口面平整,坡口内外表面10mm以内清理干净,不允许有影响焊接质量的缺陷。
d.管道组成件焊口的组对应作到内壁齐平,内壁错边量、对口间隙执行施工技术交底的规定。
e.预制管段加工尺寸允许偏差除另有规定外,应执行GB50235工业金属管道工程及验收规范的要求。
4.3.4清洁与封闭
a.贮存的管材必须保持管口封堵,保证管内清洁。
b.管道预制过程中,未施工的管段在每天下班前都应进行封口。
施工过程中,管内不允许混进杂质,禁止施工人员将焊材、零部件、工具等存放在管道内。
c.预制完成的管道必须进行空气吹扫,大直径的管道应进行人工清扫。
经清扫或吹扫完的管道要封口,封口率要达到100%。
封口前QC工程师应检查确认并签证。
d.预制管段应有足够的刚度,必要时可以进行加固,以保证存放、运输时不变形。
法兰口密封面应加护盖,防止碰撞划伤。
4.4管道的焊接
4.5管道的安装
4.5.1管道安装前应具备的条件:
a.管架施工经检验合格并办理交接手续
b.与管道连接的的机械找正合格并固定完毕
c.管道组成件及管道支承件已检验合格
d.管道预制件检验合格
e.按规定阀门已经试压完毕,可以安装
4.5.2安装前的清理
管道安装前应清除封堵用的管堵、塑料封口等,吊装时先45度斜立,人工敲打,进一步清除管内杂物,清洁后由QC工程师确认。
在安装过程中,绝对禁止将任何物品放入管内。
4.5.3安装顺序
预制管线运输到施工现场,应按单线图标识的方向卸车和摆放,按单线图号和焊口号核查管线的方向,按管线编号的顺序进行安装。
4.5.4管支架安装
a.配管施工前应进行管支架的安装,正确调整各管支架的水平位置、垂直位置和管道坡度,以利于管线和部件的对正。
b.尽量避免使用临时支吊架。
如不得以采用时,不得与正式支吊架位置冲突并应有明显的标记,在管道安装完毕后予以拆除。
c.导向支架、滑动支架和有热位移管道的吊点,安装时应注意方向,应在位移相反方向,按位移值的1/2偏位安装。
d.管道安装完毕后,应按设计规定逐个核对支吊架的形式和位置,作好《固定管架安装及弹簧支吊架调整记录》。
4.5.5管道组装
a.管道对口平直度应符合标准的规定:
当直径小于100mm时,允许偏差为1mm;
当直径大于100mm时,允许偏差为2mm,且全程允许偏差不大于3mm.
b.法兰连接时应保证法兰间的平行,其偏差应符合规定要求。
法兰应与管道同心,保证螺栓的自由穿入。
法兰密封面和密封垫片应符合标准的规定的要求。
c.螺栓紧固后螺母应满扣,螺栓
d.合金钢管道不应焊接临时支撑物,合金钢管道的调直其加热温度应控制在临界温度以下;
合金钢组对卡具应与管道材质相同,否则应用焊接该钢管的焊条在卡具上堆焊过渡层.
e.阀门安装前应按照要求进行试压,并应核对型号,按介质流向确定其安装方向并注意阀柄的安装是否便于操作。
用法兰和螺纹连接的阀门应在关闭状态下安装,以焊接方式连接的阀门应用氩弧焊焊接,焊接时阀门不得关闭。
管道安装中予留调节阀位置时,应制作与阀等长的短节替代。
安全阀应垂直安装,安全阀调校应由指定的专业调校单位试验合格并铅封。
f.管道的预拉伸(压缩)
管道的预拉伸(压缩)应遵循设计的规定。
管道的预拉伸(压缩)前应具备以下条件:
区域内固定支架间预拉口以外的所有焊缝均已清理完,需热处理的焊缝已经热处理且检验合格。
区域内支吊架已经安装完成,管子与固定支架已经固定,预拉口附近的支吊架已经予留足够的调整余量,支吊架弹簧已经按设计压缩并临时固定。
区域内所有连接螺栓已经拧紧,当预拉伸(压缩)的焊缝需热处理时,热处理后方可拆除临时卡具。
g.管道焊缝的布置要求
直管段两环焊缝间距不应小于100mm,且不小于管外径;
焊缝距弯管起弯点不得小于100mm,且不小于管外径;
管子的纵焊缝不宜设在底部;
环焊缝距支吊架净距不应小于50mm,热处理的焊缝距支吊架净距不应小于焊缝宽度的5倍,且不小于100mm;
不宜在焊缝及其边缘开孔;
加固环对接焊缝与管子的纵焊缝间距不应小于100mm,加固环距管子环焊缝的距离不应小于50mm.
h.管道安装允许偏差
项目
允许偏差(mm)
坐标
架空及地沟
室内
25
室外
15
埋地
60
标高
±
20
水平管道平直度
≦100
2L‰,最大50
100
3L‰,最大80
立管铅垂度
2L‰,最大30
成排管道间距
交叉管道的外壁或绝热层间距
4.5.6管子与机器的连接
a.管子与机器的连接应在机器固定后进行,安装前应检查,确认管道内部已处理干净.
b.在管子与机器的连接前,应在自由状态下检验法兰的平行度和同轴度,允许偏差应符合标准规定.
机械转速(r/min)
平行度(mm)
同轴度(mm)
3000-6000
不大于0.15
不大于0.5
6000
不大于0.1
不大于0.2
c.管道经试压、吹扫合格后不得承受设计以外的附加载荷,并且应进行复位检查,其结果仍然应符合标准规定。
4.5.7静电接地的安装
a.每对法兰或螺纹接头间电阻值超过规定值时,应设导线跨接。
b.管道系统的对地电阻值超过100欧姆时,应设两处接地引线,接地引线宜采用焊接形式。
c.用作静电接地的材料或零件,安装前不得涂漆。
导电接触面必须除绣并紧密连接。
d.钛管道及不锈钢管道导线跨接或接地引线应采用钛板及不锈钢板过渡。
e.静电接地安装完毕后,必须进行测试、调整,作好《管道静电接地测试记录》。
4.6管道试压
4.6.1管道系统试压包
位置相近、试验压力相近的管道与设备可以作为一个系统进行压力试验。
以平面工艺流程图为基础,将这些管道及设备组合起来,可以形成一个管道系统试压包。
管道系统试压包由项目部组织策划,报建设单位和其他相关单位审查批准。
4.6.2压力试验方案
a.压力试验的具体实施方案应以管道系统试压包为单元,以平面工艺流程图为基础。
图中应包括:
区号(系统号)、试验介质、设计压力、临时盲板安装编号、安装位置标记、盲板拆除栏、责任签字栏、工艺流程图号等
b.用气压试验来代替液压试验时,试压前必须进行预试验,试验压力为0.2Mpa。
c.试验管道系统中,隔断管道所用的插入临时盲板在安装现场处应有明显标识,以便利于日后管线复位。
盲板厚度应符合标准的规定。
d.试压用的仪表已经检测合格
4.6.3试压前的管线核查
4.6.4管道试压
试压过程中应建立试压施工组,负责管道试压和吹扫工作。
要落实指挥者和操作人员,明确责任。
试压前填写《管道系统压力试验记录》,试压过程必须有联合检查的各方代表参加,合格后在记录上签字确认。
4.7管道的吹扫与清洗
4.7.1管道的吹扫与清洗的一般要求
a.吹扫方案以平面流程图为基础,明确不应安装的部件、应安装的假件、吹扫留口、应流经的旁路、隔离部位等,表明气源来路。
b.管道的吹洗方法应根据 管道的使用要求、工件介质及管道内表面的脏污程度确定;
非热力管道不得用蒸汽吹扫
c.不允许吹洗的设备及管道与吹洗系统隔离
d.管道吹洗前,不应安装孔板、法兰连接的调节阀、重要阀门、节流阀、安全阀、仪表等;
对于焊接连接的上述阀门和仪表,应采取流经旁路或卸掉密封件等的保护措施。
e.吹洗的顺序 应按主管、支管、疏排管的顺序依次进行;
吹洗出的不得进入已吹洗的管道。
f.吹洗排放的脏液不得污染环境,严禁随地排放。
吹洗时应设置禁区。
蒸汽吹扫时,吹扫管道及附近不得放置易燃物。
管道吹洗合格后不得再进行影响管内清洗的其他作业
管道复位前,应由施工单位会同建设单位共同检查,并填写“管道吹扫及清洗记录”及“隐蔽工程记录”。
4.7.2水冲洗
冲洗管道应使用洁净水;
冲洗奥氏体不锈钢管道时,水中氯离子含量不得超过25ppm
冲洗时宜采用最大流量,流速不得低于1.5m/s
排放水应引入指定地点,排水时不得形成负压
水冲洗应连续都显得,以排出的水色和透明度与入口目测一致为合格;
当管道经水冲洗合格后暂不运行时,应将水排尽,并应及时吹干。
4.7.3空气吹扫
空气吹扫应利用生产装置的大型压缩机,也可利用装置中的大型容器蓄气,进行间断性吹扫;
吹扫压力不得超过容器和管道的设计压力,流速不宜小于20m/s
吹扫忌油管道时,气体中不得含油。
空气吹扫过程中,当目测排气无烟尘时,应在排气口设靶板检验,5min内靶板上无铁锈、尘土水分入其他杂物为合格。
4.7.4蒸汽吹扫
蒸汽吹扫以大流量蒸汽进行吹扫,流速不应低于30m/s.
蒸汽吹扫前应先进行暖管,及时排水,并检查管道热位移。
蒸汽吹扫应按加热-冷却-再加热的顺序循环进行。
蒸汽吹扫应设靶检验,符合设计要求为合格。
4.7.5化学清洗
管道进行化学清洗时,必须与无关的管道隔离;
化学清洗配方必须经过鉴定,并经实践证明是有效可靠的;
化学清洗时,操作人员必须经根据不同的清洗液,身着专用防护用品;
化学清洗合格的管道,当不能及时投运时,应进行封闭或者充氮保护。
4.7.6油清洗
润滑、密封及控制油管道,应在机械扫及管道酸洗后,系统试运转前进行清洗,不锈钢和管道宜用蒸汽吹净后进行油清洗;
油清洗应以油循环的方式进行,并及时清洗或更换滤芯;
油清洗按有关标准进行检验;
油清洗应采用适合于被清洗机械的合格油,清洗合格的管道,应采取有效的保护措施;
试运转前应采用具有合格证的工作用油。
4.8管线复位
管线试压、吹扫工作结束后应及时进行管线复位。
操作者按照责任分工,对照试压包、吹扫包上面的设定,按数点件,逐一拆除盲板、假件,安装阀件及其它安装的零部件,加上正式垫片,按最终板图纸恢复管道系统。
压力管道安装质量主要控制环节、控制点
系
统
控制环节
控
制
点
控制点级别
工作见证
停检点
(H)
审阅点
(R)
检查点
(E)
一材料系统
材料采购
1
QC工程师
材料工程师
材料采购计划
材料代用
2
现场代表
设计代表
安装工程师
《材料代用单》表023
材料验收
3
质量证明确认
《合格证汇总表》表030《说明书、合格证粘贴表》表031
4
材料检查与复验
《阀门试验记录》表701《管件检查验收记录》表702《高压钢管检查(校验)记录》表703
材料保管及发放
5
材料摆放、标识、领料发放
材料保管员
现场标识、台帐
焊材管理
6
焊材验收、保管
监检部门
二工艺系统
安装审批
7
《安装申请书》审批
综合管理员
《安装申请书》
技术准备
8
图纸审查
设计变更
建设单位
现场地表
《施工图会审记录》表018、019《设计变更通知单》表021《工程联络单》表022
9
工艺文件方案编制
焊接管理员
施工方案、工艺文件
10
工艺文件方案审批
工程公司
总工程师
管道预制
11
管子的切割,切口或螺纹的加工
现场标识
12
管道支、吊架的制作
现场实物
13
管道加工表面质量及几何尺寸偏差
《高压管弯管加工记录》表704
14
管道加工热处理和无损检测
单线图
管道安装
16
与安装管道有关的土建工程,设备工程验收
《工序交接卡》
17
清洗、脱脂、防腐
《管道系统吹扫及清洗记录》表712《管道防腐施工记录》表713
18
管道法兰、焊缝及其它连接件的安装
《地上管道安装工序质量控制表》表H-301
19
阀门安装与安全附件
《安全阀调试记录》表708《安全附件安装记录》表707
21
补偿器安装
《管道补偿装置安装记录》表705
22
管道支架安装,弹簧支、吊架安装调试
《固定管架及弹簧支、吊架调整记录》表706
23
静电接地安装
《管道静电接地测试记录》表710
24
管线核查
现场实物、质量记录
强度试验
监检代表
《管道系统压力试验记录》表711
26
严密性试验
27
系统吹扫、清洗
《管道系统吹扫及清洗记录》表712
28
管线复位
现场签证
29
管道涂漆
《管道防腐施工记录》表713
30
管道绝热
《管道隔热工程施工记录》表714
31
质量评定
质量检验评定表
工程验收
32
资料收集、整理
各种记录、试验报告等
33
竣工验收
交工文件、监检证书
三焊接系统
焊接材料
34
焊材的保管、烘干、回收发放
《焊条烘干记录》《焊条(焊丝)发放记录》
焊接设备
35
焊接设备型号、规格、性能
《设备使用计划》
焊接工艺
36
焊接工艺试验委托
《焊接工艺试验委托单》
37
焊接工艺试验
《焊接工艺评定报告》及记录、报告
38
焊接工艺评定的审核与批准
管理者代表
监检单位
39
编制焊接方案和焊接工艺规程WPS
焊接方案、焊接工艺指导书或焊接过程卡
焊工资格
40
《焊工登记表》表025焊工合格证
焊接施工管理
41
焊接接头
42
《管道焊接工作记录》表709
43
焊接返修
焊接环境
44
焊接环境管理
《气象记录》
四热处理系统
焊后热处理
45
热处理方案编制审批
热处理方案
46
热处理曲线《热处理报告》表133
47
热处理效果检查
五理化系统
理化试验
48
接受理化委托、试件
试验委托单
49
试验报告
《焊接接头机械性能试验报告》表119、120
六无损检测系统
无损检测
50
无损检测人员
《无损检测人员登记表》表024
51
接受委托
委托单
52
无损检测报告
《无损检测报告》表126、127、129-132
53
射线检测底片
1.检查点:
管道安装过程中进行各种检测\验证的点,提供检查数据,判断合格与否,规定表格见证或印检标记.
2.审阅点:
可以通过抽查、检查或审阅认可方式进行管理的工序点。
3.停点:
压力管道安装过程中必须暂时停止下来进行见证和检验的,未经制定责任人、指定部门和授权代表签字,此点就不能继续,以此来验证认定上一道全部工序的正确,否则,要造成返工或不可弥补的质量损失或事故的工序点。
压力管道安装流程图