基于PLC的四级传送带控制系统的设计.docx
《基于PLC的四级传送带控制系统的设计.docx》由会员分享,可在线阅读,更多相关《基于PLC的四级传送带控制系统的设计.docx(77页珍藏版)》请在冰点文库上搜索。
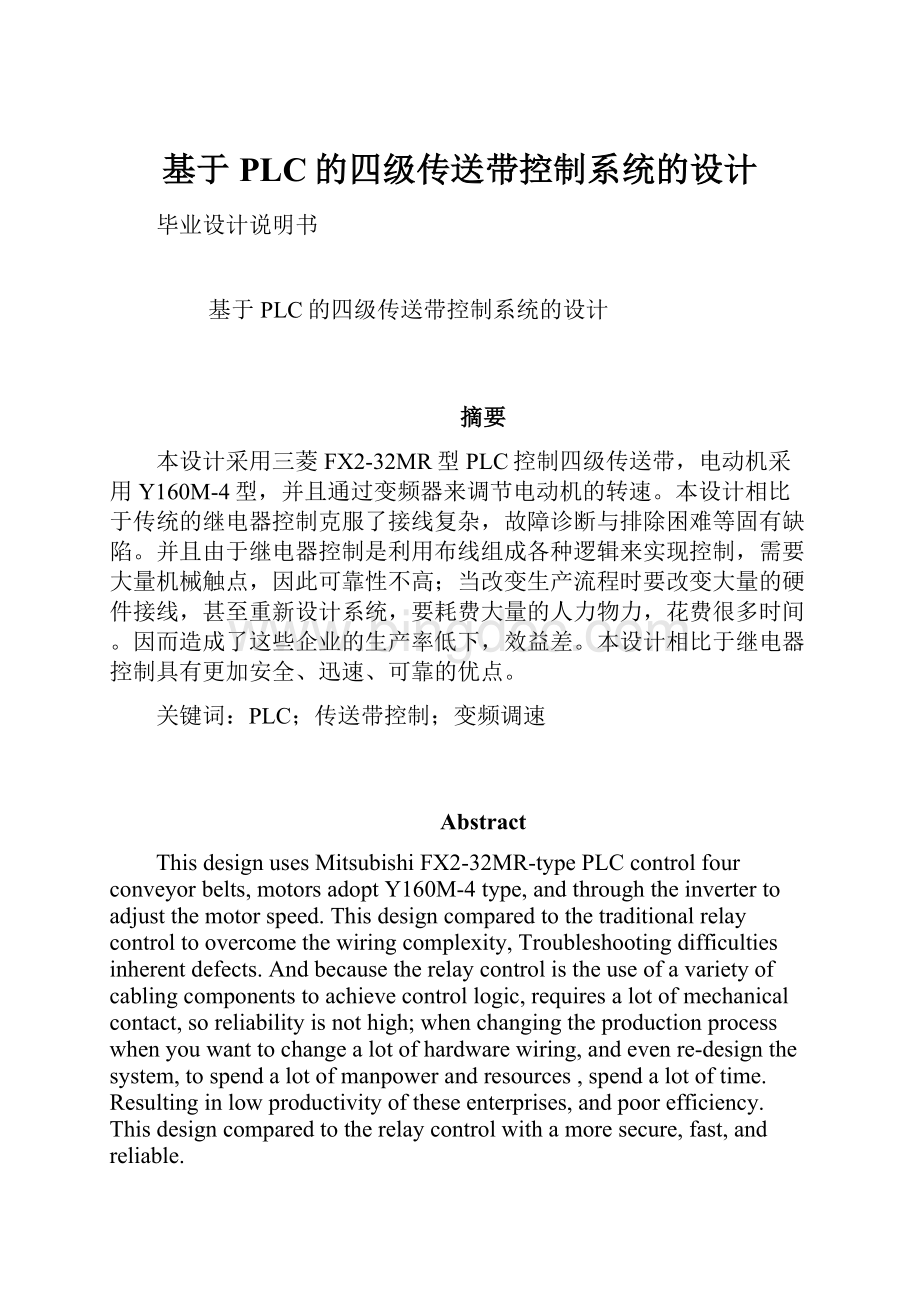
基于PLC的四级传送带控制系统的设计
毕业设计说明书
基于PLC的四级传送带控制系统的设计
摘要
本设计采用三菱FX2-32MR型PLC控制四级传送带,电动机采用Y160M-4型,并且通过变频器来调节电动机的转速。
本设计相比于传统的继电器控制克服了接线复杂,故障诊断与排除困难等固有缺陷。
并且由于继电器控制是利用布线组成各种逻辑来实现控制,需要大量机械触点,因此可靠性不高;当改变生产流程时要改变大量的硬件接线,甚至重新设计系统,要耗费大量的人力物力,花费很多时间。
因而造成了这些企业的生产率低下,效益差。
本设计相比于继电器控制具有更加安全、迅速、可靠的优点。
关键词:
PLC;传送带控制;变频调速
Abstract
ThisdesignusesMitsubishiFX2-32MR-typePLCcontrolfourconveyorbelts,motorsadoptY160M-4type,andthroughtheinvertertoadjustthemotorspeed.Thisdesigncomparedtothetraditionalrelaycontroltoovercomethewiringcomplexity,Troubleshootingdifficultiesinherentdefects.Andbecausetherelaycontrolistheuseofavarietyofcablingcomponentstoachievecontrollogic,requiresalotofmechanicalcontact,soreliabilityisnothigh;whenchangingtheproductionprocesswhenyouwanttochangealotofhardwarewiring,andevenre-designthesystem,tospendalotofmanpowerandresources,spendalotoftime.Resultinginlowproductivityoftheseenterprises,andpoorefficiency.Thisdesigncomparedtotherelaycontrolwithamoresecure,fast,andreliable.
Keywords:
PLC,conveyorcontrol,VVVF
第一章绪论
作为通用工业控制计算机,30年来,可编程控制器从无到有,实现了工业控制领域接线逻辑到存储逻辑的飞跃;其功能从弱到强,实现了从逻辑控制到数字控制的进步;其应用领域从小到大,实现了单体设备简单控制到胜任运动控制、过程控制及集散控制等各种任务的跨越。
今天的可编程控制器正在成为工业控制领域的主流控制设备,在世界各地发挥着越来越大的作用,因此,PLC的应用也就成为了一个热点问题。
在PLC诞生之前,工业控制设备的主流品种是以继电器、接触器为主体的控制装置。
继电器、接触器是一些电磁开关,后来随着工业自动化程度的不断提高,使用继电器电路构成工业控制系统的缺陷不断地暴露出来,在20世纪60~70年代,社会的进步要求制造出小批量、多品种、多规格、低成本、高质量的产品以满足市场需要,不断的提出改善生产机械功能的要求。
加上当时电子技术已经有了一定的发展,于是人们开始寻求一种以存储逻辑代替接线逻辑的新型工业控制设备,这就是我们现在所说的PLC。
PLC由于采用现代大规模集成电路技术,采用严格的生产工艺制造,内部电路采用了严格的抗干扰技术,具有很高的可靠性,从PLC的机外电路来说,使用PLC构成控制系统,和同等规模的继电接触器系统相比,电气接线及开关接点以减少到数百甚至数千分之一,故障也就大大降低,此外,PLC带有故障电路的自我检测功能,出现故障时可及时发出报警信息,这样,整个系统具有极高的可靠性也就不足为怪了。
此次毕业设计的课题内容即为PLC在四级传送带控制系统中的应用。
其研究的主要内容是:
四级传送带的顺序启动和逆向顺序停止,以及出现故障时PLC和系统对其的处理。
整个系统可显示各皮带输送带的运行状况,并对整个过程会出现的所有情况做出了合理的自动控制,是极具实用价值的一项自动化应用实例。
第二章方案论证
第一节传送带的控制方式
一、继电接触器控制方式
继电接触器控制系统:
是使用按钮、开关、行程开关、继电器、接触器等组成的控制系统。
它通过电气触点的闭合和分断来控制电路的接通与断开,实现对电动机拖动系统的起动、停止、调速、自动循环与保护等自动控制。
优点:
具备控制器件结构简单、价格低廉、控制方式直观、容易掌握、工作可靠易维护等优点。
缺点:
这些电器的机械动作寿命是有限的,必须按时更换损坏的电器,否则会影响系统的可靠性。
另外,根据加工工艺的要求,需要改变控制逻辑关系时,必须修改线路,重新安装配线,这对现代机床的控制要求是很不适应的。
普通车床是应用非常广泛的金属切削工具,目前采用传统的继电器控制的普通车床在中小型企业中仍大量使用。
由于继电器系统接线复杂,故障诊断与排除困难,并存在着固有缺陷。
由于它是利用布线组成各种逻辑来实现控制,需要大量机械触点,因此可靠性不高;当改变生产流程时要改变大量的硬件接线,甚至重新设计系统,要耗费大量的人力物力,花费很多时间。
因而造成了这些企业的生产率低下,效益差,反过来这些企业又没有足够的资金购买新的数控车床。
二、单片机控制方式
依据单片机目前的发展状况,单片机控制的优点是:
A、成本较低。
由于现在单片机的价格相对都比较低,而且外围电路的元器件价格也不高,所以整体设计起来,成本比较低。
B、可以对外部存储容量根据需要进行扩展,设计可以相对比较灵活。
C、由于现存有许多已经设计很完善的子程序,在系统软件设计中可以直接调用,减少较大工作量。
单片机虽然有一个五脏俱全的微计算机,但由于本身无自开发能力,必须借助开发工具来开发应用软件,以及对硬件系统进行诊断。
另外,单片机内的ROM比较小,所以在设计中系统必须在外面配置EPROM电路和扩展电路。
其缺点为:
A、系统硬件设计相对比较复杂,硬件设计包含扩展电路部分和系统配置电路部分,系统电路设计工作量相对较大,影响系统开发的时间。
B、系统的抗干扰能力相对较差,很难保证系统的可靠性和稳定性。
C、系统需要自己设计电源,而且不能保证系统的可靠运行。
D、维护维修相对比较麻烦,维修需要的时间也相对较长。
三、PLC控制方式
可编程逻辑控制器具有以下鲜明的特点。
A、使用方便,编程简单。
采用简明的梯形图、逻辑图或语句表等编程语言,而无需计算机知识,因此系统开发周期短,现场调试容易。
另外,可在线修改程序,改变控制方案而不拆动硬件。
B、功能强,性能价格比高。
一台小型PLC内有成百上千个可供用户使用的编程元件,有很强的功能,可以实现非常复杂的控制功能。
它与相同功能的继电器系统相比,具有很高的性能价格比。
PLC可以通过通信联网,实现分散控制,集中管理。
C、硬件配套齐全,用户使用方便,适应性强。
PLC产品已经标准化、系列化、模块化,配备有品种齐全的各种硬件装置供用户选用,用户能灵活方便地进行系统配置,组成不同功能、不同规模的系统。
PLC的安装接线也很方便,一般用接线端子连接外部接线。
PLC有较强的带负载能力,可以直接驱动一般的电磁阀和小型交流接触器。
硬件配置确定后,可以通过修改用户程序,方便快速地适应工艺条件的变化。
D、可靠性高,抗干扰能力强。
传统的继电器控制系统使用了大量的中间继电器、时间继电器,由于触点接触不良,容易出现故障。
PLC用软件代替大量的中间继电器和时间继电器,仅剩下与输入和输出有关的少量硬件元件,接线可减少到继电器控制系统的1/10-1/100,因触点接触不良造成的故障大为减少。
PLC采取了一系列硬件和软件抗干扰措施,具有很强的抗干扰能力,平均无故障时间达到数万小时以上,可以直接用于有强烈干扰的工业生产现场,PLC已被广大用户公认为最可靠的工业控制设备之一。
E、系统的设计、安装、调试工作量少。
PLC用软件功能取代了继电器控制系统中大量的中间继电器、时间继电器、计数器等器件,使控制柜的设计、安装、接线工作量大大减少。
PLC的梯形图程序一般采用顺序控制设计法来设计。
这种编程方法很有规律,很容易掌握。
对于复杂的控制系统,设计梯形图的时间比设计相同功能的继电器系统电路图的时间要少得多。
PLC的用户程序可以在实验室模拟调试,输入信号用小开关来模拟,通过PLC上的发光二极管可观察输出信号的状态。
完成了系统的安装和接线后,在现场的统调过程中发现的问题一般通过修改程序就可以解决,系统的调试时间比继电器系统少得多。
F、维修工作量小,维修方便。
PLC的故障率很低,且有完善的自诊断和显示功能。
PLC或外部的输入装置和执行机构发生故障时,可以根据PLC上的发光二极管或编程器提供的信息迅速地查明故障的原因,用更换模块的方法可以迅速地排除故。
第二节传送带控制方式的确定
可编程序控制器PLC是微机技术与传统的继电接触控制技术相结合的产物,它克服了继电接触控制系统中的机械触点的接线复杂、可靠性低、功耗高、通用性和灵活性差的缺点,充分利用了微处理器的优点,又照顾到现场电气操作维修人员的技能与习惯,特别是PLC的程序编制,不需要专门的计算机编程语言知识,而是采用了一套以继电器梯形图为基础的简单指令形式,使用户程序编制形象、直观、方便易学;调试与查错也都很方便。
用户在购到所需的PLC后,只需按说明书的提示,做少量的接线和简易的用户程序编制工作,就可灵活方便地将PLC应用于生产实践。
选PLC的优点A、采用PLC控制则PLC采用了计算机技术,其控制逻辑是以程序的方式存放在存储器中,要改变控制逻辑只需改变程序,因而很容易改变或增加系统功能。
系统连线少、体积小、功耗小,而且PLC所谓“软继电器”实质上是存储器单元的状态,所以“软继电器”的触点数量是无限的,PLC系统的灵活性和可扩展性好LC的用户程序是按一定顺序循环执行,所以各软继电器都处于周期性循环扫描接通中,受同一条件制约的各个继电器的动作次序决定于程序扫描顺序,这种工作方式称为串行工作。
B、PLC的用户程序是按一定顺序循环执行,所以各软继电器都处于周期性循环扫描接通中,受同一条件制约的各个继电器的动作次序决定于程序扫描顺序。
PLC通过程序指令控制半导体电路来实现控制的,速度快,程序指令执行时间在微秒级,且不会出现触点抖动问题。
C、PLC采用半导体集成电路作定时器,时钟脉冲由晶体振荡器产生,精度高,定时范围宽,用户可根据需要在程序中设定定时值,修改方便,不受环境的影响,且PLC具有计数功能,而电器控制系统一般不具备计数功能。
PLC大量的开关动作由无触点的半导体电路来完成,其寿命长、可靠性高,PLC还具有自诊断功能,能查出自身的故障,随时显示给操作人员,并能动态地监视控制程序的执行情况,为现场调试和维护提供了方便。
因为PLC控制有上述优点,所以本设计采用PLC来控制传送带。
第三章传送带介绍
第一节传送带的发展历史
17世纪中,美国开始应用架空索道传送散状物料;19世纪中叶,各种现代结构的传送带输送机相继出现。
1868年,在英国出现了皮带式传送带输送机;1887年,在美国出现了螺旋输送机;1905年,在瑞士出现了钢带式输送机;1906年,在英国和德国出现了惯性输送机。
此后,传送带输送机受到机械制造、电机、化工和冶金工业技术进步的影响,不断完善,逐步由完成车间内部的传送,发展到完成在企业内部、企业之间甚至城市之间的物料搬运,成为物料搬运系统机械化和自动化不可缺少的组成部分。
第二节传送带的现状
目前发达国家的胶带生产工艺装备和试验测试设备已达到相当先进和完善的地步,整个生产工艺连续化,普遍采用计算机控制,使成型、硫化、磨削、切割等工艺设备和功率试验机等测试设备实现了高度机电一体化,操作人员少,生产效率高,产品质量相当高。
如德国的Scholz公司、Berstorff公司、日本的神户公司等专业生产此类专用设备;某些大的橡胶公司如Pirell公司和Gates公司等也可自行设计制造此类设备。
但引进这些厂家的设备价格相当昂贵,一为国产设备价格的3~10倍,从而使其在国内的推广应用受到约束。
从20世纪80年代末开始,国内少数有实力的厂家,如上海胶带股份有限公司、无锡橡胶厂、贵州大众橡胶有限公司、洛阳橡胶制品厂、宁波伏龙同步带有限公司(原宁波同步带总厂)、宁波凯驰胶带有限公司、苏州盖茨霓塔传动带有限公司等相继从德国或美国引进了部分新型传动带生产设备,开始生产切边V带、同步带和多楔带,产品很受用户青睐,市场销路相当不错。
这些先进生产设备的引进,对提高我国胶带行业的工装水平,改善落后状况起到了积极的推动作用。
但我们应该清醒地认识到,拥有先进设备的毕竟只是少数厂家,而其他大多数厂家的生产设备仍十分落后,成型工艺无恒张力装置,只实现了自由张力下的成组成型,不少企业还采用手工操作;硫化工艺大多数企业仍采用颚式平板硫化机分段硫化;而拥有动态疲劳试验机的只有5、6家,行业整体测试手段落后,也是我国传动带质量不高的一个重要原因。
为了提高我国胶带行业的装备水平,目前,国内已有数家高校或企业在开发研制新型传动带生产设备,较突出的有青岛化工学院、哈尔滨工业大学、西北工业大学、福建三明橡机设备公司等,他们均是在消化、吸收引进设备的基础上,根据国情和自身的条件,进行国产化研制的。
就设备的技术含量、自动化程度和生产线配备来说,以青岛化工学院研制的设备最为先进和齐全。
该院于1996年承担了“九五”国家重点科技攻关项目“橡胶V带及同步带成套设备开发”,并于2000年4月初通过了国家科委的项目验收。
与会专家一致认为,该项目包括主机、辅机和工装模具在内的全套生产线设备均达到甚至超过国际同类设备的先进水平,完全可以替代进口。
目前,该院在国内已占据技术领先位置,并在不断地进行创新设计,设备价格仅为进口设备价格的1/3~1/5。
第三节传送带常见问题及处理方法
传送带运行时输送带跑偏是最常见的故障之一。
跑偏的原因有多种,其主要原因是安装精度低和日常的维护保养差。
安装过程中,头尾滚筒、中间托辊之间尽量在同一中心线上,并且相互平行,以确保输送带不偏或少偏。
另外,带子接头要正确,两侧周长应相同。
在使用过程中,如果出现跑偏,则要作以下检查以确定原因,进行进行调整。
输送带跑偏时常检查的部位和处理方法有:
(1)检查托辊横向中心线与带式输送机纵向中心线的不重合度。
如果不重合度值超过3mm,则应利用托辊组两侧的长形安装孔对其进行调整。
具体方法是输送带偏向哪一侧,托辊组的哪一侧向输送带前进的方向前移,或另外一侧后移。
(2)检查头、尾机架安装轴承座的两个平面的偏差值。
若两平面的偏差大于1mm,则应对两平面调整在同一平面内。
头部滚筒的调整方法是:
若输送带向滚筒的右侧跑偏,则滚筒右侧的轴承座应当向前移动或左侧轴承座后移;若输送带向滚筒的左侧跑偏,则滚筒左侧的轴承座应当向前移动或右侧轴承座后移。
尾部滚筒的调整方法与头部滚筒刚好相反。
(3)检查物料在输送带上的位置。
物料在输送带横断面上不居中,将导致输送带跑偏。
如果物料偏到右侧,则皮带向左侧跑偏,反之亦然。
在使用时应尽可能的让物料居中。
为减少或避免此类输送带跑偏可增加挡料板,改变物料的方向和位置。
传送带除了上述跑偏问题,还经常出现磨损、划伤、破损、搭接部位开裂等问题,这些设备问题的出现不仅加快了传送带的损坏,而且造成物料的漏撒和浪费,通常出现传送带设备问题以后,企业都是通过缝补、加热硫化或者报废更新,这些方式都不能很好的解决设备问题,报废更新更是造成了设备采购成本的上升。
现在欧美国家通过对高分子复合材料的研究,发现高分子橡胶材料针对传送带磨损、划伤、破损、搭接部位开裂等问题可进行有效解决,在线现场快速修复。
第四节传送带的发展方向
未来传送带设备将向着大型化发展、扩大使用范围、物料自动分拣、降低能量消耗、减少污染等方面发展。
大型化包括大输送能力、大单机长度和大输送倾角等几个方面。
水力输送装置的长度已达440公里以上带式输送机的单机长度已近15公里,并已出现由若干台组成联系甲乙两地的“带式输送道”。
不少国家正在探索长距离、大运量连续输送物料的更完善的输送机结构。
扩大输送机的使用范围,是指发展能在高温、低温条件下有腐蚀性、放射性、易燃性物质的环境中工作的,以及能输送炽热、易爆、易结团、粘性物料的传送带设备。
第四章可编程控制器的概述
第一节PLC的基本概念
早期的可编程控制器称作可编程逻辑控制器(ProgrammableLogicController,PLC),它主要用来代替继电器实现逻辑控制。
随着技术的发展,这种采用微型计算机技术的工业控制装置的功能已经大大超过了逻辑控制的范围,因此,今天这种装置称作可编程控制器,简称PC。
但是为了避免与个人计算机(PersonalComputer)的简称混淆,所以将可编程序控制器简称PLC。
PLC自1969年美国数据设备公司(DEC)研制出现,现行美国、日本、德国的可编程序控制器质量优良,功能强大。
第二节PLC的基本结构
PLC实质是一种专用于工业控制的计算机,其硬件结构基本上与微型计算机相同,基本构成为:
A、电源
PLC的电源在整个系统中起着十分重要的作用。
如果没有一个良好的、可靠的电源系统是无法正常工作的,因此PLC的制造商对电源的设计和制造也十分重视。
一般交流电压波动在+10%(+15%)范围内,可以不采取其它措施而将PLC直接连接到交流电网上去
B、中央处理单元(CPU)
中央处理单元(CPU)是PLC的控制中枢。
它按照PLC系统程序赋予的功能接收并存储从编程器键入的用户程序和数据;检查电源、存储器、I/O以及警戒定时器的状态,并能诊断用户程序中的语法错误。
当PLC投入运行时,首先它以扫描的方式接收现场各输入装置的状态和数据,并分别存入I/O映象区,然后从用户程序存储器中逐条读取用户程序,经过命令解释后按指令的规定执行逻辑或算数运算的结果送入I/O映象区或数据寄存器内。
等所有的用户程序执行完毕之后,最后将I/O映象区的各输出状态或输出寄存器内的数据传送到相应的输出装置,如此循环运行,直到停止运行。
C、存储器
存放系统软件的存储器称为系统程序存储器。
存放应用软件的存储器称为用户程序存储器。
D、输入输出接口电路
现场输入接口电路由光耦合电路和微机的输入接口电路,作用是PLC与现场控制的接口界面的输入通道。
现场输出接口电路由输出数据寄存器、选通电路和中断请求电路集成,作用PLC通过现场输出接口电路向现场的执行部件输出相应的控制信号。
E、功能模块
如计数、定位等功能模块。
F、通信模块
如以太网、RS485、Profibus-DP通讯模块等。
第三节PLC的工作原理
当PLC投入运行后,其工作过程一般分为三个阶段,即输入采样、用户程序执行和输出刷新三个阶段。
完成上述三个阶段称作一个扫描周期。
在整个运行期间,PLC的CPU以一定的扫描速度重复执行上述三个阶段。
A、输入采样阶段
在输入采样阶段,PLC以扫描方式依次地读入所有输入状态和数据,并将它们存入I/O映象区中的相应的单元内。
输入采样结束后,转入用户程序执行和输出刷新阶段。
在这两个阶段中,即使输入状态和数据发生变化,I/O映象区中的相应单元的状态和数据也不会改变。
因此,如果输入是脉冲信号,则该脉冲信号的宽度必须大于一个扫描周期,才能保证在任何情况下,该输入均能被读入。
B、用户程序执行阶段
在用户程序执行阶段,PLC总是按由上而下的顺序依次地扫描用户程序(梯形图)。
在扫描每一条梯形图时,又总是先扫描梯形图左边的由各触点构成的控制线路,并按先左后右、先上后下的顺序对由触点构成的控制线路进行逻辑运算,然后根据逻辑运算的结果,刷新该逻辑线圈在系统RAM存储区中对应位的状态;或者刷新该输出线圈在I/O映象区中对应位的状态;或者确定是否要执行该梯形图所规定的特殊功能指令。
即,在用户程序执行过程中,只有输入点在I/O映象区内的状态和数据不会发生变化,而其他输出点和软设备在I/O映象区或系统RAM存储区内的状态和数据都有可能发生变化,而且排在上面的梯形图,其程序执行结果会对排在下面的凡是用到这些线圈或数据的梯形图起作用;相反,排在下面的梯形图,其被刷新的逻辑线圈的状态或数据只能到下一个扫描周期才能对排在其上面的程序起作用。
在程序执行的过程中如果使用立即I/O指令则可以直接存取I/O点。
即使用I/O指令的话,输入过程影像寄存器的值不会被更新,程序直接从I/O模块取值,输出过程影像寄存器会被立即更新,这跟立即输入有些区别。
C、输出刷新阶段
当扫描用户程序结束后,PLC出刷新阶段。
在此期间,CPU按照I/O映象区内对应的状态和数据刷新所有的输出锁存电就进入输路,再经输出电路驱动相应的外设。
这时,才是PLC的真正输出。
第五章主要器件的选型
第一节PLC型号的选择
一、PLC的选型原则
在PLC系统设计时,首先应确定控制方案,下一步工作就是PLC工程设计选型。
工艺流程的特点和应用要求是设计选型的主要依据。
PLC及有关设备应是集成的、标准的,按照易于与工业控制系统形成一个整体,易于扩充其功能的原则选型所选用PLC应是在相关工业领域有投运业绩、成熟可靠的系统,PLC的系统硬件、软件配置及功能应与装置规模和控制要求相适应。
熟悉可编程序控制器、功能表图及有关的编程语言有利于缩短编程时间,因此,工程设计选型和估算时,应详细分析工艺过程的特点、控制要求,明确控制任务和范围确定所需的操作和动作,然后根据控制要求,估算输入输出点数、所需存储器容量、确定PLC的功能、外部设备特性等,最后选择有较高性能价格比的PLC和设计相应的控制系统。
(一)输入输出(I/O)点数的估算
I/O点数是可编程序控制器的一个简单明了的性能参数,也是应用计算机赛最直接的参数。
在机型选择时必须注意一下问题:
产品手册上给出的最大I/O点数的确却含义,由于各公司的习惯不同,所给出的最大I/O点数含义并不完全一样,有的给出的时I/O总点数,即包括输入也包括输出,也就是手册上给出的点数是输入点数和输出点数之和,有的则分别给出最大输入点数和最大输出点数。
要分清模拟量I/O点数和数字量I/O点的关系。
有的产品模拟量I/O点数要占数字量I/O点数,有的产品则分别独立给出且互相并无影响。
远程I/O的考虑,对于较大的控制系统,控制对象较为分散,一般都要采用远程I/O,在选择机型时,要注意可编程序控制器是否具有远程I/O的能力和能驱动远程I/O点数。
智能I/O的考虑,在机型选择考虑I/O点数的同时,还要考虑智能I/O的能力,具有智能I/O模板可方便的解决高速计数,闭环控制等特殊的控制功能。
I/O点数的余量,无论如何,在系统硬件设计中要留有充分的I/O点数作为备用,这主要时基于二方面的考虑,一是系统设计的更改,如果不留有充分的余量,一旦系统设备调整,控制功能增加,就要全部推翻原有设计好的系统,造成不必要的损失;二是手册上给出的最大I/O点数都是在理想情况下获得的参数,一旦满负荷运行,就要影响整个系统的响应速度和可靠性,给系统带来不良的影响,为了保证所设计的控制系统的正常运行,在系统硬件设计时,建议根据实际I/O点数留有20%~30%的余量。
(二)存储器容量的估算
在初步估算时,对于仅需开关量控制的系统,将I/O点数乘以8,就是所需的存储器的字数,这一要求一般都能满足,在只有模拟量输入,没有模拟量输出的系统中,一般要对模拟量信号作数据传送,数据滤波和比较运算等操作。
估算时可为