张伟毕业设计说明书.docx
《张伟毕业设计说明书.docx》由会员分享,可在线阅读,更多相关《张伟毕业设计说明书.docx(27页珍藏版)》请在冰点文库上搜索。
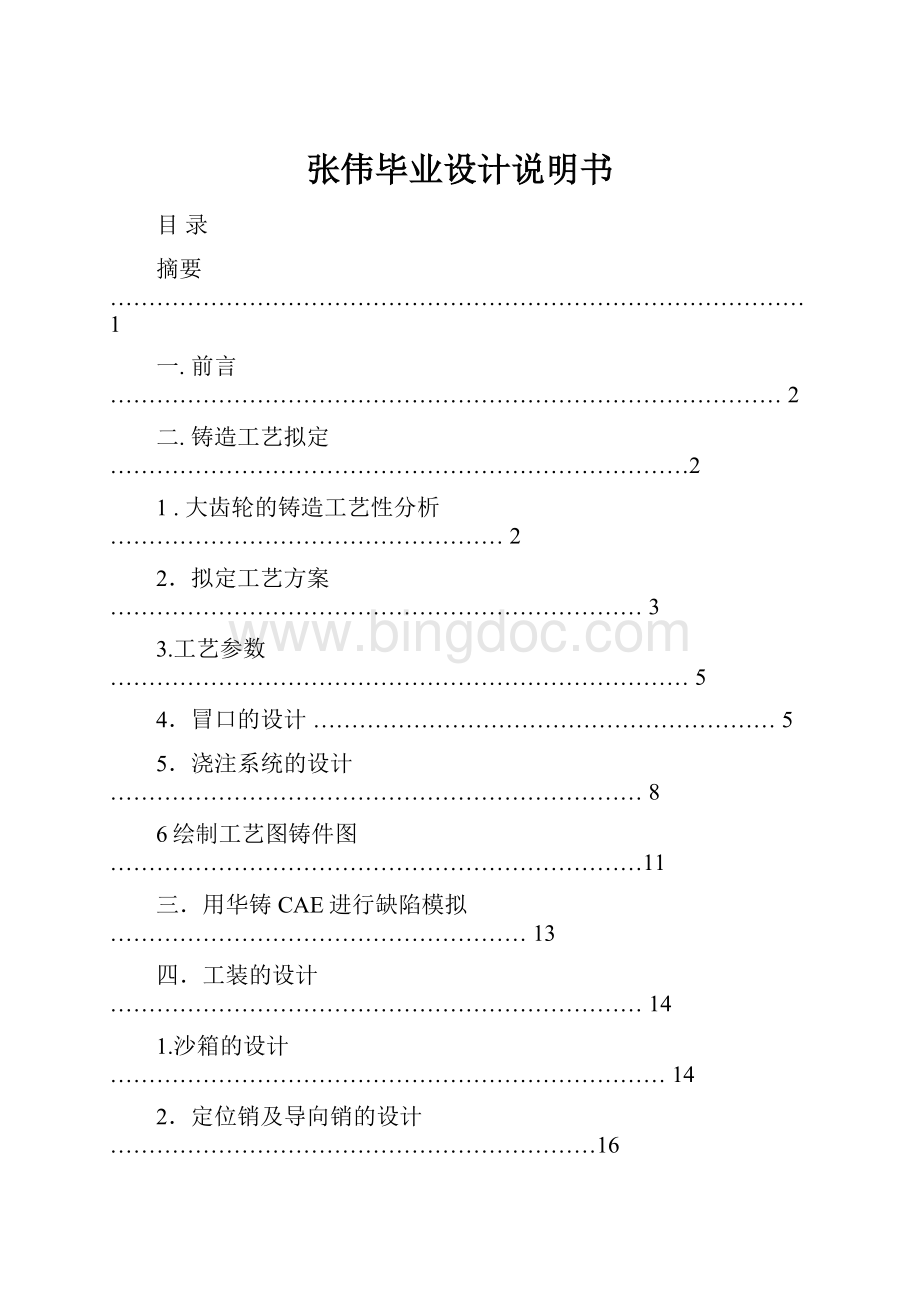
张伟毕业设计说明书
目录
摘要………………………………………………………………………………1
一.前言……………………………………………………………………………2
二.铸造工艺拟定…………………………………………………………………2
1.大齿轮的铸造工艺性分析……………………………………………2
2.拟定工艺方案……………………………………………………………3
3.工艺参数…………………………………………………………………5
4.冒口的设计……………………………………………………5
5.浇注系统的设计……………………………………………………………8
6绘制工艺图铸件图……………………………………………………………11
三.用华铸CAE进行缺陷模拟………………………………………………13
四.工装的设计……………………………………………………………14
1.沙箱的设计………………………………………………………………14
2.定位销及导向销的设计………………………………………………………16
3.模样设计……………………………………………………………………17
4.模板设计………………………………………………………………………20
5.模板装配图………………………………………………………………22
五.铸造工艺卡…………………………………………………………24
六.总结与体会……………………………………………………………………25
七.致谢词………………………………………………………………………25
参考文献……………………………………………………………………………25
摘要
本设计是轴承座铸造工艺与工装设计。
分析了轴承座铸件结构特点、技术条件,在以上的基础上介绍了轴承座的铸造工艺设计,包括分型面的选取和浇注系统、冒口及砂芯的设计。
在铸造工艺的基础上,设计了模样、模板、芯盒及砂箱。
利用华铸CAE对轴承座铸钢件进行凝固过程的数值模拟,揭示了产生缩松、缩孔的部位和形成原因,从而对铸造工艺进行优化。
模拟结果表明,合理设置冒口、冷铁,可以保证铸件的顺序凝固和金属液的有效补缩,获得结构完整、没有缺陷的铸件。
【关键词】轴承座;活塞;铸造工艺;模拟
Abstract
Thisdesignisbearingcastingprocessandfixturedesign.Analysisofthestructurecharacteristics,operatingcastingtechnology,onthebasisofaboveofthebearingisintroduced,includingthecastingprocessdesignoftheselectionandgatingsystem,riserandsandcoredesign.Onthebasisofcastingdesignandappearance,templateandcoreboxesandsandbox.UseofcaststeelcastingsIowabearingonCAEsolidificationprocessofnumericalsimulation,andrevealstheshrinkage,shrinkageofproduceandformation,thusofcastingprocessoptimization.Simulationresultsshowthatthereasonablesettingriser,coldironcastings,canguaranteethemoltenmetalsolidificationandeffectiveshrinkage,completestructureandnodefectscasting.
[key]housings,Thepistons,Castingprocess,simulation1.
一.前言
随着科技的发展,中国人世的进一步深入,对铸件的要求也越来越高。
铸件不但要求要有较好的表面光洁度及尺寸精度,而且对其内在质量的控制方面提出了更高的要求。
对铸件质量的考核指标不仅仅局限于表面、宏观的缺陷控制,而且已深入到微观领域,如超探等级、耐压试验等一系列涉及其内部组织方面的指标。
本设计所涉及大齿轮正属于此类铸件,本次设计的目的就是要为生产出符合高考核标准的大齿轮所制订的铸造工艺。
[2]
二.铸造工艺拟定
1大齿轮的铸造工艺性分析
①设计条件
图2-1ZG35SiMn大齿轮
如图2-1,铸件零件是大齿轮,材料为ZG35SiMn,大批量生产。
零件质量要求非常高,须进行超声波探伤,并应符合GB/T7233的规定。
热处理后齿面的硬度为HB197-248.因此铸件不允许有气孔、缩松、裂纹、夹杂等影响强度的缺陷存在。
2.拟定工艺方案
①造型、制芯方法
铸件毛重12.15kg,大批量生产,故选择机器造型。
采用呋喃树脂砂造型。
②浇注位置、分型面及砂箱中铸件的数目
(1)方案一
图2-2方案一
采用分模造型,水平浇注,轮毂的中心孔做死,到时进行机械加工。
铸件轴线为垂直位置,过中心线的纵剖面为分型面,使分型面于分模面一致有利于、起模、排气和检验等。
各端的加工面水平位置和竖直位置均有。
铸造圆角为R5,中心孔采用砂芯,铸出一半,采用机加工完成。
横浇道开在下型分型面上,内浇道开在下型分型面上,熔融金属从铸件边缘冒口下方引入。
该方案中边缘处采用机加工完成,铸件质量较易获得保证。
此方案浇注时熔融金属充型平稳,整个铸件都处于下箱,使铸件的质量的到保证,不因有砂箱错位而影响铸件的质量。
图2-2示。
(2)方案二
图2-3方案二
如图2-3此种方案将分型面取在大齿轮的中间,容易产生飞边毛刺。
发生错箱时不能保证铸件的精度,不易保证铸件的尺寸精度。
经过比较决定采用方案一作为最终方案。
③砂箱中铸件的数量
铸件单件毛重12.15kg,不宜采用一箱多件,故拟定为一箱一件。
3工艺参数
①加工余量及拔模斜度
根据相关资料规定,采用砂型铸造的铸钢件成批和大量生产的尺寸尺寸公差等级为CT8-10,选择CT9,铸件机械加工余量等级为D级,由此查表可确定加工余量为3mm,拔模斜度根据相关资料按金属模样选取a=0°50′a(mm)=1.6
②铸出孔与槽
铸件上的孔和槽尺寸都较大,而且铸件的孔与槽不需要进行加工,故四个毛坯孔和槽都铸出。
③铸造收缩率
铸造收缩率是铸件从线收缩开始温度(从液相中析出枝晶搭成骨架开始具有固态性质时的温度)冷却至室温时的相对线收缩量,以模样与铸件的长度差除以模样长度的百分比表示:
ε=
×100%
式中L1—模样长度;L2—铸件长度。
[4]
铸造收缩率是考虑了各种影响因素之后的铸件实际线收缩率,它不仅与铸造金属的收缩率和线收缩起始温度有关,而且还与铸件结构、铸型种类、浇冒口系统结构、砂型和砂芯的退让性等因素有关。
对此铸件,根据相关资料经验选取线收缩率ε=2.%
④工艺补正量
对于成批,大量生产的铸件或永久性产品,不应使用工艺补正量。
所以不考虑工艺补正量。
⑤反变形量
一般中小铸件壁厚差别不大且结构上刚度较大时,不必留反变形量。
⑥砂芯负数
流忘砂芯,自硬砂芯,壳芯,热芯盒砂芯及小的粘土砂芯均不采用砂芯负数。
4.冒口设计
根据铸件尺寸,在PRO/ENGINEER中造出其三维模型,可知其重量为12.15kg。
①轮毂处模数计算
铸件模数由模数法计算得,在PRO/ENGINEER中可获知该部分的体积V=419661mm
,散热面积S=31368.6mm
,由Mc=V÷S=419661÷31368.6=13.37mm;
冒口模数确定冒口为圆柱形暗冒口,则MR=(1.1-1.2)Mc=(1.1-1.2)×13.37=(14.7-16)mm。
选取MR=14.9mm。
根据相关资料查得冒口的尺寸如图2-4所示:
图2-4
②确定轮缘冒口及补贴尺寸
采用比例法确定冒口及补贴尺寸。
比例法是在分析,统计大量工艺资料的基础上,总结出冒口尺寸经验确定法。
我国各地工厂根据长期实践经验,总结归纳出冒口各种尺寸相对于热节圆直径的比例关系,汇编成各种冒口尺寸计算的图表,详见有关手册。
比例法简单易行,已被广为采用。
现已常见的轮型铸钢件(如齿轮.车轮.皮带轮.摩擦轮和飞轮等)为例。
介绍用比例法确定冒口尺寸的方法步骤(见图2-5)。
图2-5
(1)热节圆直径dy的确定
根据零件图尺寸,加上加工余量和铸造收缩率作图,量出或算出热节圆直径dy(应考虑尖角效应)。
测量得dy=30
(2)按比例确定轮缘冒口尺寸
a.冒口补贴按下列经验比例关系确定:
d1=1.05dy
d2=1.05d1
b.冒口尺寸用下述比例关系计算:
暗冒口宽B=(1.5-1.8)dy=50
冒口长A=(1.5-2.0)B=100
c.冒口补缩距离L=4dy,当两冒口之间的距离超过此值时,应放冷铁或设水平不补贴。
(3)确定冒口个数
初步确定冒口个数为4个
(4)校验冒口补缩量
冒口补缩距离L=4dy=120mm
铸件需补缩的距离D=πd铸件=835.24mm
冒口的长度4×100=400
所需冒口数(835.24-400)/120=3.627取4
(5)冒口位置的确定
冒口位于铸件的具体位置见工艺图。
5.浇注系统设计
①浇注位置的确定
由于铸件对缩孔、缩松缺陷要求非常高,为了避免缩孔缩松缺陷采用顶注式,使其形成有利于重力补缩的合理温度梯度;铸件的重量比较小,浇入铸型的金属液不多,避免过多的金属液让铸型局部过热,采用两个内浇口,内浇口位于冒口下方,这样有利于避免在内浇道位置及附近产生缩孔、缩松。
②浇注时间的确定
浇注时间按照公式t=c
计算
其中c为浇注系数根据相关资料取c=1.1
G为浇注金属液的质量(包括冒口和浇注系统的质量)
铸件的质量为12.15kg,根据一般铸钢件的工艺出品率为50%左右,所以G=12.15÷50%=24.15取G=25kg
t=c
=1.1×
=5.5取t=6s
③浇注系统结构及尺寸确定
由于铸件尺寸较小,属于小型铸件,所以不适宜用漏包浇注,所以采用转包浇注。
用转包浇注时尺寸计算:
大批量生产小型铸钢件时,常用转包浇注。
多采用封闭式或半封闭式浇注系统,以加强撇渣能力。
常采用的浇注系统截面比为:
∑F内:
∑F横:
∑F直=1:
(0.8-0.9):
(1.1-1.2)
内浇道截面尺寸按式∑F阻=G/tks’
式中G-流经∑F阻截面的金属液重量
k-浇注比速【kg/(cm²s)】
s’-金属液流动系数
浇注壁速k主要取决于铸件的相对密度d,而
d=G/V(kg/dm³)
式中V-铸件轮廓体积。
显然d值越大,说明铸件愈简单,壁越厚;d值越小,则铸件结构越复杂,壁越薄。
浇注比速k与G.d的关系见相关图表。
式中有关数据的取值如下:
金属液流动系数s’,碳钢取1.0,高锰钢取0.8;
浇注时间t=c
根据浇注钢液重量G和铸件相对密度d,就可以从表中查得F内。
根据单个浇道截面积,可从表中选择内浇道,横浇道的截面积尺寸。
一般地,内浇道厚度应小于铸件壁厚的0.7倍以下,才不致一起在内浇道处产生缩孔。
查表得:
∑F内=6.cm
∑F内:
∑F横:
∑F直=1:
(0.8-0.9):
(1).1-1.2=
6:
(4.8-5.4):
(6.6-7.2)
采用两个内浇道和两个横浇道,所以:
取F内=3cm,F横=2.6cm,F直=7.1cm
图2-6内浇道截面尺寸
(2)
图2-7横浇道截面尺寸(单向)
直浇道直径为φ30mm,各组元的截面积比例为:
∑F直:
∑F横:
∑F内=1:
0.87:
1.18
④浇口杯及直浇道的设计:
直浇道使用内径为30mm,外径为50mm的陶瓷管,在上模板上做出一个直径为26mm,高度为10mm的凸台用做定位。
根据相关资料查得浇口杯的尺寸如图2-8所示:
图2-8浇口杯尺寸
。
6.绘制工艺图、铸件图
图2-9铸造工艺示意图
图2-10铸件图
三.用华铸CAE进行铸件缺陷模拟
用Proe画出铸件图形,冒口浇道等,华铸CAE对铸件模拟时,观察铸件
有无缩孔,缩松。
华铸CAE”铸造工艺分析软件是分析和优化铸造工艺的重要工具。
它以铸件充型、凝固过程数值模拟技术为核心对铸件的成型过程进行工艺分析和质量预测,从而协助工艺人员完成铸件的工艺优化工作。
多年来在提高产品质量,降低废品,减少消耗,缩短试制周期,赢得外商订单等方面为众多的厂家创造了显著的经济效益,在行业内享有广泛的声誉和信誉。
模拟结果如图3-1,3-2
图3-1
图3-2
铸件内部无任何缺陷缩孔,缩松均在冒口和浇注系统中,铸件内部均已凝透
,所以对铸件质量比较好,工艺设计较为合理。
四.工装设计
1.沙箱的设计
根据铸件的外形轮廓尺寸及铸件采用一箱一件选择沙箱的内腔尺寸如下:
上沙箱:
550×450×150mm
下沙箱:
550×450×150mm
沙箱的壁厚设计为15mm,所以沙箱的外形轮廓尺寸为:
上沙箱:
580×480×150mm
下沙箱:
580×480×150mm
沙箱的具体尺寸如图4-1所示:
图4-1
2.定位销及导向销的设计
定位销及销套均采用过盈配合式,根据沙箱的外形轮廓尺寸设计定位销的尺寸如图4-2所示:
图4-2定位销尺寸
根据沙箱的外形轮廓尺寸,导向销的具体尺寸如图4-3所示:
图4-3
3.模样设计
铸造生产中,模样是用来形成铸件外表面的必要工艺装备。
模样的结构和质量的好坏,直接关系着铸件的几何形状、尺寸精度和表面质量,也影响着模样制造的工艺性、经济性,以及使用和操作性能。
正确的选择和设计模样是保证铸件质量,提高生产效率,降低成本,减轻劳动强度的重要环节。
模样的设计是铸造工艺设计的主要内容。
模样的设计和选择是铸造生产中的关键。
模样设计的主要内容一般包括:
模样材料的选择;结构尺寸的设计;尺寸的确定以及对模样技术要求的制定等。
模样材料的选择关系到铸件的尺寸精度、生产成本、制模周期和使用寿命等。
模样使用的材料应根据铸件的造型方法、生产批量,结合各种材料的使用特点来选用。
模样结构形式的设计,主要根据模样选用的材料,制造方法,模样的使用场合等。
好的模样结构设计应是经济合理,使用方便,同时能满足工艺要求,保证产品质量。
模样的尺寸精度影响铸件的尺寸精度。
在所有的模样尺寸中最重要的是模样的工作尺寸,即直接形成铸件的尺寸[11]。
模样的工作尺寸按下式进行计算:
模样的工作尺寸=(零件尺寸±工艺尺寸)×(1+铸造收缩率)[11]
对于铸钢件,由厂方经验得铸钢出铸造收缩率取2%
①下模样尺寸具体计算尺寸计算如下:
Am=(Ac+At)(1+εl)式中
Am—模样的工作尺寸;Ac—产品的零件尺寸;At—零件的铸造工艺附加尺寸;εl—铸造的线收缩率(2.0%)。
[7]
Ac(mm)
At(mm)
εl(%)
Am(mm取整)
60
6
2
68
266
6
2
277
90
0
2
92
14
0
2
14
表3-1模样尺寸计算
②模样材料的选择
由于铸件属批量生产,而且采用机器造型,所以选择金属材料的模样,具体为ZL102,整铸式,由于模样不大金属模样做成实心的。
下模样图的具体尺寸如图4-4所示:
图4-4
③模样在模板上的定位与紧固
为了使模样与模板安装顺利,采用定位销和导向销定位,用9个M8开槽沉头螺钉紧固,如图4-5所示:
图4-5模样的定位写紧固形式
4.模板设计
模板也称型板,一般是由模底板、铸件模样、浇冒口模样和定位销等经加工后装配而成。
其中模底板的工作表面形成铸型分型面,铸件模样和浇冒口模样形成铸型外轮廓、浇冒口系统型腔。
采用模板造型可以提高铸件质量和生产率,所以一般应用于大批量生产中,有时也应用于单件小批量生产中。
①模底板的材料
模底板尺寸大,在造型过程中受到强烈的冲击载荷,因此其受力强度大,要求高,故选用铸钢材质,具体为HT200。
②.确定模底板的尺寸
a.平面尺寸
根据铸件的尺寸大小及最小吃砂量的影响,确定砂箱的外框尺寸为
A×B=580×480,A,B分别为砂箱内框的长,宽。
模底板的平面尺寸:
长度为A0;宽度为B0。
A0=A+2bB0=B+2b式中b—砂箱分型面上凸缘的宽度,查表取15mm。
[7]
所以模板的外形轮廓尺寸为610×510mm
b.模底板的高度
根据使用要求,选取模底板高度H=100mm。
C.模底板的厚度和加强肋
加强肋的布置
加强肋的布置采用矩形正交式,如图4-6所示:
图4-6
图3-9加强肋布置
③模底板和砂箱的定位装置
根据模底板轮廓尺寸选用M16的定位销及导向销,长度均为125mm。
④模底板吊轴
吊轴和模底板一起铸出,如图4-7所示:
图4-7吊轴结构与尺寸
5.模板装配图
图4-8模板装配图(下模板)
五.铸造工艺卡
零件号
1#
零件名称
大齿轮
每台件数
1
材料
铸件重量(㎏)
铸件材质
炉料
每箱毛坯铸件数
净重
毛重
浇注系统重
12.15
15.8
1.5
ZG35SiMn
废钢
1
造型
砂型名称
砂型类别
(干型或湿型)
造型方法
砂箱编号
砂箱内部尺寸(㎜)
长
宽
高
上箱
表干型
机器
1
580
480
150
下箱
表干型
机器
2
580
480
150
中箱
砂型
面砂
背砂
涂料
干燥前
干燥后
芯撑
编号
重量
编号
重量
编号
次数
编号
次数
1
2
浇注系统
内浇口
横浇口
直浇口
浇口杯编号
过滤网编号
一箱冒口数目
一箱出气孔数目
数量
每个截面积(cm2)
数量
每个截面积(cm2)
数量
截面积(cm2)
2
3
2
2.6
1
7.1
0#
5
0
浇注
钢水出炉温度℃
浇注温度℃
每箱钢水消耗㎏
浇注时间s
冷却时间(min)
>1580
1490—1540
27
6
60~120
铸件落砂与清理
名称
落砂
落芯
铸件清理
热处理
方法
机械
抛丸
退火
使用设备
捅箱机
震动
抛丸机
热处理炉
备注
六.总结与体会
我在本次大齿轮铸造工艺与工装设计过程中,系统的了解了铸造工艺与工装设计的基本步骤与思想,掌握了铸造工艺参数的选取、浇注系统的设计原则以及冒口的计算与设计;利用华铸CAE系统对铸造工艺的模拟,了解了其基本操作,掌握了对分析数据的后置处理。
通过数值模拟,加强了对铸钢件顺序凝固的重要性理解以及通过设置冷铁来控制凝固顺序的基本方法。
设计过程中,进一步熟悉了AUTOCAD、PROENGINEER等计算机辅助设计软件的操作运用。
通过这次全面的设计过程,使我明白作为一个工程技术人员,应当具备耐心、细心、专心的基本素质;另外,铸造方法是一个复杂的过程,影响最后铸件质量的因素很多,对于铸造工作者的工作经验显得尤为重要,在拟定铸造工艺的过程中并不是所有的工艺参数及方法都有参照的标准,因此,对于一个铸造工作者在拟定工艺的过程中应当大胆地摸索、创新。
七.致谢词
在杨世洲老师的悉心指导下使我顺利完成了大学四年中最为重要的毕业设计。
导师渊博的专业知识,严谨的治学态度,精益求精的工作作风,诲人不倦的高尚师德,严以律己、宽以待人的崇高风范,朴实无华、平易近人的人格魅力对我影响深远。
不仅使我树立了远大的学术目标、掌握了基本的绘制铸造工艺图的方法,还使我明白了许多待人接物与为人处世的道理。
本论文从选题到完成,每一步都是在导师的指导下完成的,倾注了导师大量的心血。
在此,谨向导师表示崇高的敬意和衷心的感谢!
【参考文献】
[1]朱景梓.英汉机械工程技术词汇.科学出版社,1983.9
[2]梁燕春.重工科技-2002年2期
[3]中国机械工程学会铸造专业学会编.铸造手册第5卷铸造工艺.1994.10.北京:
机械工业出版社
[4]李弘英赵成志编著.铸造工艺设计.机械工业出版社.2006.1
[5]中国机械工程学会铸造分会编.铸造手册铸钢第2版.2004.8.北京:
机械工业出版社
[6]李魁盛主编.铸造工艺设计基础.北京:
机械工业出版社1981.1
[7]《铸造工艺工装备设计手册》编写组编.铸造工艺装备设计手册.机械工业出版社.1989.5