ABS塑件的注射成型工艺分析及模具设计.docx
《ABS塑件的注射成型工艺分析及模具设计.docx》由会员分享,可在线阅读,更多相关《ABS塑件的注射成型工艺分析及模具设计.docx(31页珍藏版)》请在冰点文库上搜索。
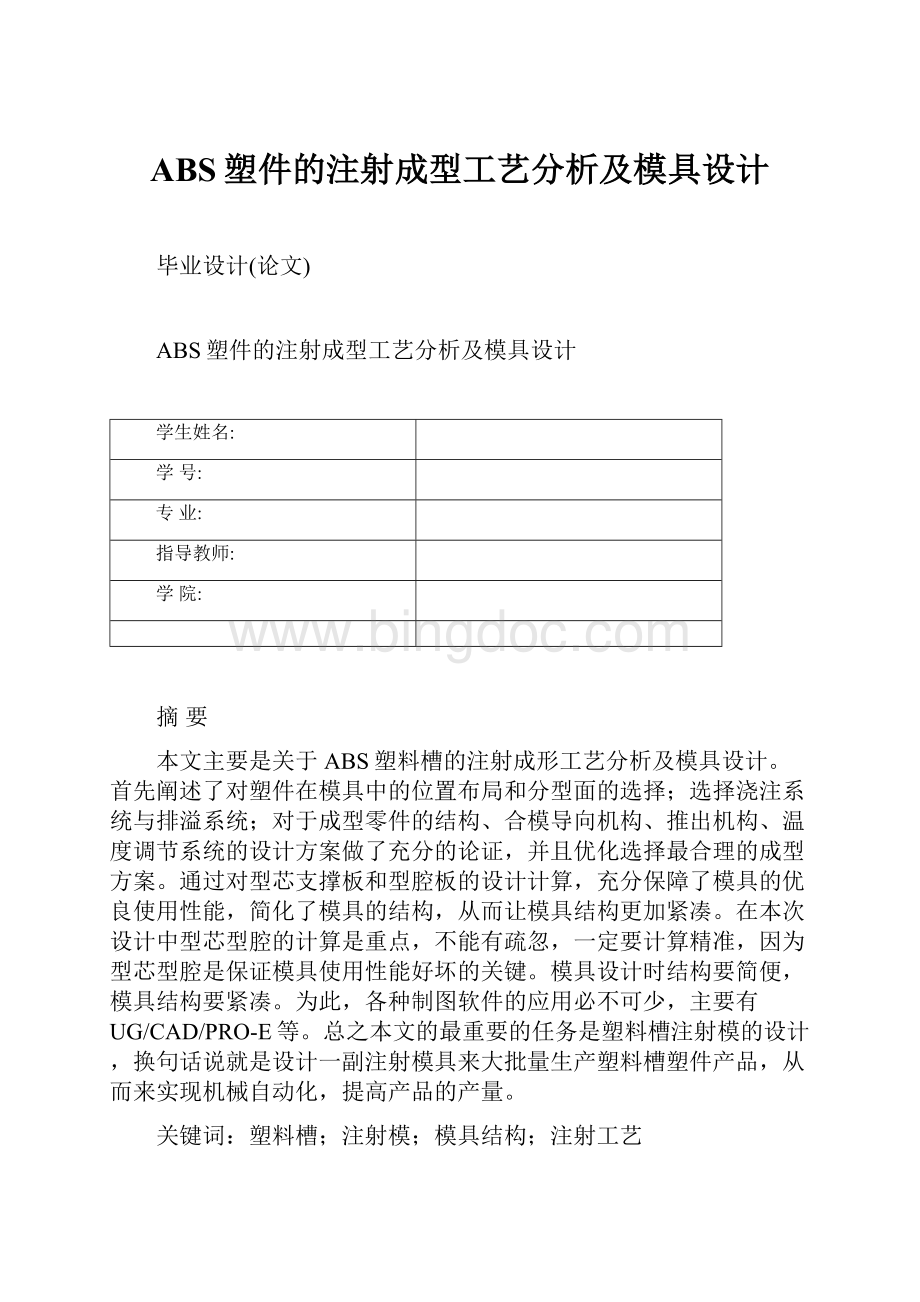
ABS塑件的注射成型工艺分析及模具设计
毕业设计(论文)
ABS塑件的注射成型工艺分析及模具设计
学生姓名:
学号:
专业:
指导教师:
学院:
摘要
本文主要是关于ABS塑料槽的注射成形工艺分析及模具设计。
首先阐述了对塑件在模具中的位置布局和分型面的选择;选择浇注系统与排溢系统;对于成型零件的结构、合模导向机构、推出机构、温度调节系统的设计方案做了充分的论证,并且优化选择最合理的成型方案。
通过对型芯支撑板和型腔板的设计计算,充分保障了模具的优良使用性能,简化了模具的结构,从而让模具结构更加紧凑。
在本次设计中型芯型腔的计算是重点,不能有疏忽,一定要计算精准,因为型芯型腔是保证模具使用性能好坏的关键。
模具设计时结构要简便,模具结构要紧凑。
为此,各种制图软件的应用必不可少,主要有UG/CAD/PRO-E等。
总之本文的最重要的任务是塑料槽注射模的设计,换句话说就是设计一副注射模具来大批量生产塑料槽塑件产品,从而来实现机械自动化,提高产品的产量。
关键词:
塑料槽;注射模;模具结构;注射工艺
ABSTRACT
ThisarticleisabouttheABSplasticinjectionmoldinggroovesTechnologyAnalysisandDieDesign.Firstexpoundedbyplasticinthemoldpartinglinepositionandlocation,selectthegatingsystemandoverflowdischargesystem.Formoldingpartsofthestructure,moldguidemechanism,pushingmechanism,temperaturecontrolsystemdesigntodoafulldemonstration,choosethemostreasonableandoptimizedesign.Bythecalculationofthecoresupportplateandcavityplate,adequateprotectionoftheexcellentperformanceofthemold,simplifyingthedesignofthemold,sothatmoldmorecompact.Inthisdesign,thecorecavitycomputingisthekeypoint,thecalculationmustbeaccurate,becausethecorecavitymolddesignisanimportantfactortoensuretheperformanceisgoodorbad.Inaddition,takingintoaccountarticleinjectionmoldingprocessrequirements,avarietyofgraphicssoftwareapplicationsisessential,mainlyinUG/CAD/Pro-Eandsoon.
Keywords:
plastictank;injectionmolding;moldstructure;injectionprocess
6.3模具装配总图......................................................................................................28
7.1结论......................................................................................................................29
7.2展望......................................................................................................................29
致谢.............................................................................................................................33
附录............................................................................................................................35
1绪论
在未来的模具行业里,塑料模具的发展前景将会优于其它的模具,塑料模具在模具市场中所占的比重将会逐步提升。
当今塑料工业发展不断壮大,因此对塑料模具相对应的要求也是非常的高,照这个形式发展下去,一些精密的、大型的、复杂的、耐用的塑料模具在模具市场中也是有非常的好的前景,有着很大的竞争力。
与此同时,因为近几年来进口的模具中,一些精确度高的、大型地、复杂的、耐用的模具占有量很大,因此从减少进口,促进内销的角度出发,研究、开发一些实用性强、精度高的模具是具有现实意义和远大前景。
1.1塑料简介
ABS塑件是一种没有颜色,没有味道,没有毒害的有机聚合物。
外表非常像聚乙烯,但是又比聚乙烯还更加透明,重量更加轻。
它的密度为0.90~0.91g/cm3。
它不溶于水,色泽鲜亮。
抵抗微量塑性变形的应力、表征材料最大均匀塑性变形的抗力、外力是压力时的强度极限和固体材料抗拒永久形变的特性及弹性性能都比(C2H4)n要更好。
ABS固定方向拉伸之后可以加工成铰链,它有与众不同的抵抗弯曲疲劳强度。
例如用ABS可以把铰链制造成一个整体,ABS熔化的温度是164~170摄氏度,能够在一百摄氏度以上的温度下采取消毒处理。
其在低的温度使用温度可达零下十五摄氏度,但是当温度低于零下30摄氏度时会发生断裂。
ABS的绝缘性能非常好。
因为它不吸水,所以湿度不能干涉到它的绝缘性能。
但是在空气中的氧、阳光,高温催化下非常容易降解、物理性能、化学性能都会发生改变,因此一定要加入防老化剂,以此来阻止或延缓致它的老化。
在这里我选用ABS材料的一个重要因素正是因为它有非常良好的冲击力,硬度很高,而且不容易磨损,流动性能很好,不容易发生变形等优点。
总结归纳:
ABS在升温时它的流动性能加强,成型的压力优点高,因此塑件上的
相对来说比较大,在模具的设计时应该留意尽量缩小浇注系统对料流的冲击,模具的环境温度应该保持在五十到六十度,并且在酮、醛、酯、氯代烃中进行成型,之后应该进行调湿技术处理。
1.2注塑成型及注塑模
注射成型也可以叫做注塑或者注射模塑,它的基本工艺程序是将融化了的塑料在注射机注射活塞或螺杆的双重推动下,快速的将物料射入封闭的模具型腔内部,通过慢慢的降温使之凝固或者固化成形,得到所需塑件。
无论是柱塞式注射机还是移动螺杆式注射机,一个完整的注射成型工艺过程通常包括成型前准备、注射过程和制品后处理。
总的模具注塑过程可以概括为:
注射成型的工艺条件:
压力、时间、温度。
在精密制品的成型,确立成型条件决非易事,由于影响它的成型条件的因素很多,有模具结构、装备、原材料、电压波动及温度等。
在国内外市场,运用较为广泛的模拟分析软件有德国的FOBLSDELOW、美国的CFLOW、华中科大的H-FLOW。
其中MOLDFLOW软件包括三个部分:
MOLDFLOWPLASTICSADVISERS(产品优化顾问,简称MPA),MOLDFLOWPLASTICSINSIGHT(注射成型模拟分析,简称MPI),MOLDFLOWPLASTICSXPERT(注射成型过程控制专家,简称MPX)。
可以完全代替试模的是CAE,它提供了从塑件材料整体设计至投入车间生产的工艺路线,可以说CAD技术的应用成功不单单是对大幕分传统模具制件的重大影响,更是对企业工厂车间生产提高制品质量,防止模具返修和降低成本等的重大的技术成果。
1.3本次设计的意义与目的
本次设计属于各项综合性指标的毕业课题设计,同时也是一项非常具有意义的相关专业实训任务,因为它的各项综合性要求比较强,而且它的需要了解的应用技术层面高。
伴随着我国市场经济调整的,我国所需要的各种机械零件需求量剧增,以及机械类工艺产品更新过快,导致我国的机械类产品销售竞争相当火。
因此ABS塑料模具已非常广泛地应用在机械模具生产制造之中。
模具生产设计制造工艺现在已经发展成是现代化生产实践中必不可少的重要环节。
那么这就影响着模具制造行业在我国的机械制造销售市场民的每个产业链中也愈加离不开进行最佳模具制造设计工艺来提高生产加工质量。
如此看来模具的工艺设计完善与否已是当下机械工业生产的重要手段和工艺发展方向之一。
现如今的机械类工业模具产品的品种和车间生产效率的高低,取决于模具设计工艺的发展和技术经济水平的提高。
在即将毕业投入岗位的时候,学校根据各个专业要求安排了本次的毕业设计。
本次毕业计的同学根据自己的兴趣选取一个课题进行全方面的设计也是材料成型及控制工程专业的学生在学完技术基础课和专业课的基础上,所需要进行的设一个尤为关键的实践性教学目的。
本次设计的技术要求:
1.要求完成模具整体装配图一张
2.主要零件(型芯、型腔、浇注系统、推荐装置等)图3-5张
3.详细的设计计算过程
4.有关零件的选用依据及过程
5.主要零件(型芯、型腔等)的制造工艺规程1-2份
2塑料材料分析
2.1塑料材料的基本特性
ABS塑料是丙烯腈、丁二烯和苯乙烯的三元共聚物。
这三种组分的各自特性,使得ABS塑料具有“硬、韧、刚”的综合力学性能。
ABS的性能指标:
密度1.02——1.05(
),收缩率
,熔点
,弯曲强度80Mpa,拉伸强度35
49Mpa,拉伸弹性模量1.8Gpa,弯曲弹性模量1.4Gpa,压缩强度18
39Mpa,缺口冲击强度11
20
,硬度62
86HRR,体积电阻系数
。
ABS的热变形温度为93
118℃,制品经退火处理后还可提高10℃左右。
ABS在-40℃时仍能表现出一定的韧性,可在-40
100℃的温度范围内使用。
2.2塑件材料成型性能
是一种没有颜色,没有味道,没有毒害的有机聚合物。
外表非常像聚乙烯,但是又比聚乙烯还更加透明,重量更加轻。
它的密度为0.90~0.91g/cm3。
它不溶于水,色泽鲜亮。
抵抗微量塑性变形的应力、表征材料最大均匀塑性变形的抗力、外力是压力时的强度极限和固体材料抗拒永久形变的特性及弹性性能都比(C2H4)n要更好。
要求塑件精度高时,模具温度可控制在50
60℃,要求塑件光泽和耐热时,模具温度应控制在60
80℃。
ABS比热容低,塑化效率高,凝固也快,故成型周期短。
2.3塑件材料主要用途
根据ABS塑件中的存在三种组成成分的比例差异,那么导致其各项性能也略有差异,从而为了适应各种不同的使用用途。
因此根据其应用的不同,ABS塑件可以大致分为超高抗冲击型、高抗冲击型、中抗冲击型、低抗冲击型和耐热性。
BS的性能指标:
密度1.02——1.05(
),收缩率
,熔点
,弯曲强度80Mpa,拉伸强度35
49Mpa,拉伸弹性模量1.8Gpa,弯曲弹性模量1.4Gpa,压缩强度18
39Mpa,缺口冲击强度11
20
,硬度62
86HRR,体积电阻系数
。
ABS的热变形温度为93
118℃,制品经退火处理后还可提高10℃左右。
ABS在-40℃时仍能表现出一定的韧性,可在-40
100℃的温度范围内使用。
3塑件的工艺分析
对ABS塑件的工艺性分析是模具设计中必不可少的一个环节,其中包括塑件的形状大小、尺寸、结构、精度以及它的表面质量的分析。
以便对塑件的工艺性进行完整的分析和控制。
ABS塑件2D视图如图3-1所示,是本次要成型的塑件;
图3-1ABS塑件图
3.1塑件的结构设计
(1)、脱模斜度
塑料制件在冷却时收缩,它在脱模前通常包住模具的型芯或型箱中。
因此要想防止因脱模力过大的影响,与脱模方向平行的制件的表面应有一定的脱模斜度。
通常塑件的脱模斜度约取0.5~1.5
,根据文献[1],塑件材料ABS的型腔脱模斜度为0.35
~1
30/
,型芯脱模斜度为30/~1
(2)、塑件的壁厚
塑件的壁厚是设计时需要考虑的关键因素。
表3-1塑件壁厚厚薄的缺点
壁厚太厚的缺点:
材料消耗增大,生产成本提高,更重要的是会延缓塑件在模内的冷却速度,使成型周期延长,另外还容易产生气泡、缩孔、凹陷等缺陷。
壁厚太薄的缺点:
刚度差,在脱模、装配、使用中会发生变形,影响到塑件的使用和装配的准确性。
因此塑件的壁厚一般在1~4
,最常用的数值为1.5~3
。
该产品壁厚均匀,周边和底部壁厚均为1-1.5
。
(3)、塑件的圆角
本塑件都有圆角过渡,符合注塑成型要求。
(4)、孔
由于型芯对熔体有分流作用,在孔成形时非常容易产生熔裂痕,故设计孔间距和孔到边缘的距离通常都要大于孔径,此外周边需要增加壁厚,来保证它的强度和刚度。
塑件中间有一个方孔,侧面是一圈台阶,台阶上有一小孔,两孔的方向一致,所以可以顺利脱模,所以需要无需采用滑块抽芯机构。
3.2塑件尺寸及精度
塑件尺寸的差异关键在于流动性和注射机的规格,因此在设备及设计工艺条件相同的情况下流动新好的塑件可以成型尺寸较大的制品。
从环境保护和绿色健康角度出发只要能够满足要求,一般都应将制品的结构设计的尽量紧凑。
该塑件的材料为ABS,流动性较好,适用于成型不同尺寸的制品。
根据任务书和图纸要求,本次产品尺寸均采用MT5级精度,可用普通注塑成型达到其精度要求。
3.3塑件表面粗糙度
塑料制品的表面粗糙度一般为Ra0.02~1.25
之间,模腔表壁的表面粗糙度应为塑件的1/2,即Ra0.01~0.63
。
模具在成型时因为型腔的各种损耗导致制品的粗糙度增加,那么需要抛光来实现复原。
该塑件外部需要的表面粗糙度比内部要高,为Ra0.8
,内部为Ra1.2
,因此在外侧不应留有成型痕迹。
3.4塑件的体积和质量
本次设计中,塑件的质量和体积采用粗略计算法,
塑件体积V=侧面的体积+底面体积,整个产品可以分为1个圆柱形和2个圆环形,
V1=32×44×38
=53504mm3
V2=42×30×36.5
=45990mm3
V3=10×20×4÷2
=400mm3
V4=3.14×2.15×2.15×4
=58.06mm3
所以整个产品的体积为
V=53504-45990+400-58.06=7855.94mm3=7.86cm3
所以粗略计算该塑件制品的体积为7.86
,ABS的密度为1.05
,所以其质量为8.253克。
4塑件的成形工艺设计与模具结构设计
4.1注射成型工艺过程分析
第一步:
首先使用的设备和塑件保证注射成型顺利进行及产品质量需要以下的步骤:
(1)、成型前对原材料的预处理
由于本次设计是ABS材料,而它的吸水性强,故需要干燥处理。
温度为100到200摄氏度,干燥2-3小时。
(2)、料筒的清洗
在使用注射机进行注射成型前,对于注射机-特别是料筒,需要进行清洗。
由于柱塞式注射机料筒的存量大导致料筒转动困难,因此清洗时进行拆卸后再洗;对螺杆式通常是直接换料清洗,也可采用对空注射法清洗。
(3)、脱模剂的选用
脱模剂是让成型零件容易从脱出而敷在注射模表面上的一种助剂。
本设计中为了便于注射时顺利脱模,将用到的脱模剂为硬脂酸锌
第二步:
注射成型过程
本次设计ABS塑件的注射成型过程中主要包括塑化成型和成型冷却
第三步:
制件的后处理
本次设计的ABS塑件脱模后,制件由于成型时内外温度不均就还存在一定的内应力,那么就需要制定消除这种内应力的措施来保证制件的工艺性和力学性能。
常采用退火及调湿度措施,本次成型采用退火2-3h的后处理。
4.2浇口种类的确定
浇注系统的定义:
注射机的喷嘴至型腔的流动管道。
设计浇注系统的目的是为了使塑件的熔体充满整个型腔并传递到各个部分。
它的组成包括主流道、分流道、浇口以及冷料穴四部分。
而浇口的设计对于塑件能否完整的成型其关键作用。
本次设计采用的是侧入式浇口,原因是因为本次设计对线圈塑件的外表面质量要求高,其结构如图4-1所示;为防止溢料,便于更换,同时节省优质材料,在注射机与模具接触处设计一个浇口套,具体如图4-2所示。
图4-1浇口结构示意图
图4-2浇口套尺寸图
4.3型腔数目的确定
本次设计采用的是一模两腔的布置形式,具体见图4-3所示。
因为:
1.该注塑模尺寸较小,而采用的浇口形式又是侧入式浇口;
2.一模两腔更经济,更加节省成本还能提高成型效率。
4.4注射机的选择和校核
选取注射机为海天SYS-20。
注射方式为螺杆式注射成型,其有关性能参数见表4-1所示。
表4-1SYS注塑机参数
型号
单位
SYS-20
参数
螺杆直径
mm
22
理论注射容量
g
20
注射压力
Mpa
1200
注射行程
mm
250
螺杆转速
r/min
0~160
料筒加热功率
KW
9.75
锁模力
KN
200
拉杆内间距(水平×垂直)
mm
450×560
允许最大模具厚度
mm
300
允许最小模具厚度
mm
200
模板最大距离
mm
600
顶出方式
机械顶出
4.4.1注射量的校核
本次ABS塑件模具设计成型的注射量应该满足注射机内的熔体质量为额定注射量的80%左右,其检验公式如下所示:
式中:
--型腔数量
--单个塑件的重量(g)
--浇注系统所需塑料的重量(g)
本设计中:
n=2
8.253g
=1.76g
M=2x8.253+1.76=18.266g
注塑机额定注塑量为20g
注射量符合要求
4.4.2塑件在分型面上的投影面积与锁模力的校核
在注射成型时影响锁模力的重要因素主要有模具分型面上的投射面积的大小,如果投影面积大于注射成型所能承受的最大投影面积就会出现模具膨胀和溢出塑料的现象。
核算公式如下:
式中n--型腔数目
--单个塑件在模具分型面上的投影面积
--浇注系统在模具分型面上的投影面积
n=2
=44×32-42×30=148
=272+3.14×4×4=322.24
=2x148+322.24=618.24
本次设计中应设计让注射成型压力与分型面的投射面积的乘积不大于注射机的额定锁模力。
计算公式如下:
(
)P式中:
P—塑料熔体对型腔的成型压力(MPa)
F—注射机额定锁模力(N)
其它意义同上
根据教科书表5-1,型腔内通常为20-40MPa,一般制品为24-34MPa,精密制品为39-44MP
(
)P=618.24x30x1.1x0.001=20.402KN<200KN
锁模力符合要求
4.4.3注射机的尺寸检验
(1)、模具厚度(闭合高度)
模具闭合高度必须满足以下公式
式中
--注射机允许的最大模厚
--注射机允许的最小模厚
本设计中模具厚度为235mm200(2)、开模行程(S)的校核
开模行程的定义是:
注射模具打开闭合过程中动模固定板移动的横向距离。
本次设计所用到的是卧式注射机,而影响它的开模行程的主要因素为模具的厚度,其计算公式如下所示:
Smax>S=H1+H2+H3+C
式中H1--模具厚度
H2--顶出行程
H3--包括浇注系统凝料在内的塑件高度
C–安全距离
本设计中
=600
=235mm
=40mmH3=85mmC取30mm
(3)、顶出装置的校核
在本次设计的顶出装置时,推出机构需要检验它的顶出形式,即模具的推板面积能够完全盖住本注射机的双顶杆以及顶出距离能够是模具能够顺利的脱出。
本设计的注射机的机械顶出结构能够满足制件脱出的顺利进行。
5注射模具结构设计
5.1分型面的设计
分型面的定义:
把模具分成若干个部分,各部分的接触表面分开时脱出塑件和浇注塑料,闭合时又需要解除封闭的接触表面。
分型面的选择是模具能否完整成型的重要因素,因此合理的选择分型面至关重要。
选择分型面时,应从以下几个方面考虑:
1)分型面尽量选择在塑件外形的最大轮廓处;
2)使塑件在开模后留在动模上;
3)分型面的痕迹不影响塑件的外观;
4)浇注系统,特别是浇口能合理的安排;
5)尽量让推杆的痕迹不显露在塑件外形的表面上;
6)使塑件易于脱模。
本次设计的分型面选择为平面分型面,并且选择在该塑件的最大平面处,然后开模的塑件留在动模的一侧处。
5.2型腔的布局
本次设计的型腔结构将直接影响到浇注系统的结构设计,因此型腔的布局务必使每个型腔通过浇注系统时所承受的压力相同,来保证各型腔内的塑件的质量较为稳定。
因此本次设计采用平衡式流道,其型腔的布局见附件II所示。
5.3浇注系统的设计
浇注系统的定义:
指模具中塑料熔体由注射机喷嘴至型腔之间的进料通道。
其作用是使塑料熔体充满整个的型腔。
本次毕业设计采用的是侧入式浇口浇注系统。
5.3.1浇注系统组成
普通流道浇注系统的组成一般包括以下几个部分。
1-主浇道2-第一分浇道3-第二分浇道4-第三分浇道
5-浇口6-型腔7-冷料穴
5.3.2确定浇注系统的原则
在设计浇注系统时应考虑下列有关因素:
1)、成型塑料的工艺性能特性,例如塑件熔体的流动性、收缩性等性能的影响。
2)、浇口的设计它的数量和结构时要考虑到是否利于塑料熔体的流动,并且还能有利于通道排气;还要预先考虑熔接痕的位置以及对塑件质量的影响。
3)、设计时要尽量缩小塑件熔体到型腔之间的距离,以便能够较小压力损失。
4)、为了预防型芯的变形和塑件的位移,要考虑高压时塑料熔体对型芯的冲击。
5)、设计时考虑浇注系统冷凝料的产生来减小原材料的损失。
6)、浇口的设计需要考虑是否能够有效的去除冷凝料,以防它的堆积影响塑件的外观。
5.3.3主流道设计
主流道的设计一般垂直于分型面,而本次设计中主流道设计成圆锥形,它的圆锥角为2-4度,这样有利于冷凝料顺利的从主流道脱出。
(1)主流道尺寸
通常主流道和喷嘴的接触处设计成球面凹坑这样能够保证两者紧紧接触并且能够防止漏料。
根据所选注塑机,则主流道小端尺寸为:
d=注塑机喷嘴尺寸+(0.5~1)=4+(0.5~1)=5mm
主流道球面半径SR=喷嘴球半径+(1~2)=12+(1~2)=14mm
(2)主流道衬套形式
本次设计为衬套和定位环为分体式;
材料采用T10钢,热处理淬火后表面硬度为45HRC~48HRC。
主流道衬套的固定,采用4个M6X20的螺丝直接锁附固定。
5.3.4分流道设计
(1)分流道断面形状的选择
选择分流道截面形状时有各种形状供我们选择,例如:
圆形、矩形、