圆盖塑料模具设计.docx
《圆盖塑料模具设计.docx》由会员分享,可在线阅读,更多相关《圆盖塑料模具设计.docx(10页珍藏版)》请在冰点文库上搜索。
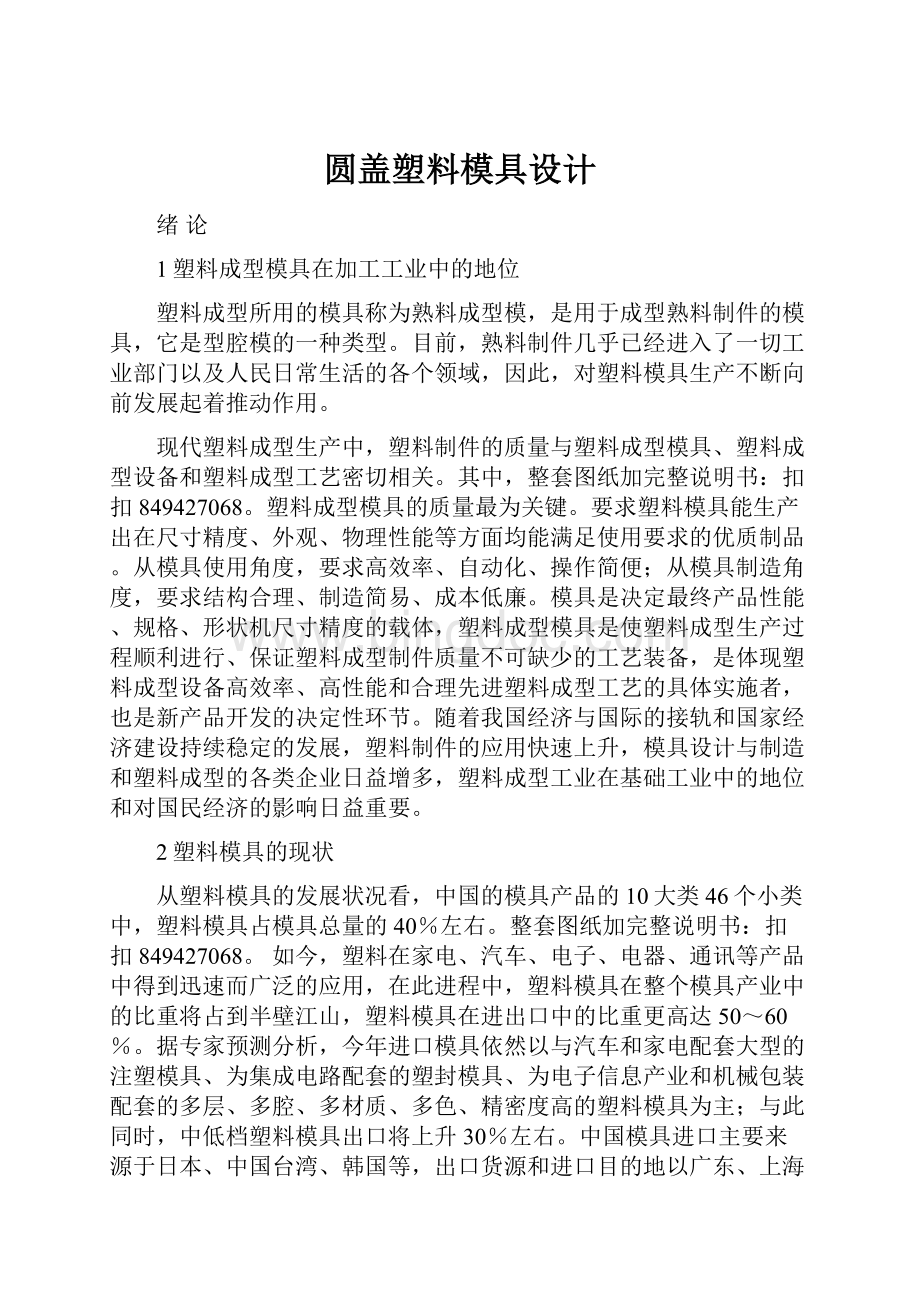
圆盖塑料模具设计
绪论
1塑料成型模具在加工工业中的地位
塑料成型所用的模具称为熟料成型模,是用于成型熟料制件的模具,它是型腔模的一种类型。
目前,熟料制件几乎已经进入了一切工业部门以及人民日常生活的各个领域,因此,对塑料模具生产不断向前发展起着推动作用。
现代塑料成型生产中,塑料制件的质量与塑料成型模具、塑料成型设备和塑料成型工艺密切相关。
其中,整套图纸加完整说明书:
扣扣849427068。
塑料成型模具的质量最为关键。
要求塑料模具能生产出在尺寸精度、外观、物理性能等方面均能满足使用要求的优质制品。
从模具使用角度,要求高效率、自动化、操作简便;从模具制造角度,要求结构合理、制造简易、成本低廉。
模具是决定最终产品性能、规格、形状机尺寸精度的载体,塑料成型模具是使塑料成型生产过程顺利进行、保证塑料成型制件质量不可缺少的工艺装备,是体现塑料成型设备高效率、高性能和合理先进塑料成型工艺的具体实施者,也是新产品开发的决定性环节。
随着我国经济与国际的接轨和国家经济建设持续稳定的发展,塑料制件的应用快速上升,模具设计与制造和塑料成型的各类企业日益增多,塑料成型工业在基础工业中的地位和对国民经济的影响日益重要。
2塑料模具的现状
从塑料模具的发展状况看,中国的模具产品的10大类46个小类中,塑料模具占模具总量的40%左右。
整套图纸加完整说明书:
扣扣849427068。
如今,塑料在家电、汽车、电子、电器、通讯等产品中得到迅速而广泛的应用,在此进程中,塑料模具在整个模具产业中的比重将占到半壁江山,塑料模具在进出口中的比重更高达50~60%。
据专家预测分析,今年进口模具依然以与汽车和家电配套大型的注塑模具、为集成电路配套的塑封模具、为电子信息产业和机械包装配套的多层、多腔、多材质、多色、精密度高的塑料模具为主;与此同时,中低档塑料模具出口将上升30%左右。
中国模具进口主要来源于日本、中国台湾、韩国等,出口货源和进口目的地以广东、上海、北京、江苏居多,而中国塑料模具出口目的地比较分散,主要是输往中国香港地区,其中不少为转口贸易。
3塑料成型模具的发展趋势
目前为止,我国在塑料模的制造精度、模具标准化程度、制造周期、模具寿命以及塑
料成型设备的自动化程度和精度等方面已经有了长足的进步。
从塑料成型模具的设计理论、设计实践和制造技术出发,实践与制造大致有以下几个方面的发展趋势。
(1)注重开发大型,精密,复杂模具;随着我国轿车,家电等工业的快速发展,成型零件的大型化和精密化要求越来越高,模具也将日趋大型化和精密化。
(2)加强模具标准件的应用;使用模具标准件不但能缩短模具制造周期,降低模具制造成本而且能提高模具的制造质量。
因此,模具标准件的应用必将日渐广泛。
(3)推广CAD/CAM/CAE技术;模具CAD/CAM/CAE技术是模具技术发展的一个重要里程碑。
实践证明,模具CAD/CAM/CAE技术是模具设计制造的发展方向,可显著地提高模具设计制造水平。
(4)重视快速模具制造技术,缩短模具制造周期;随着先进制造技术的不断出现,模具的制造水平也在不断地提高,基于快速成形的快速制模技术,高速铣削加工技术,以及自动研磨抛光技术将在模具制造中获得更为广泛的应用。
第一章塑件工艺性分析
零件名称:
圆盖(如图1-1所示)
生产批量:
大批量
材料:
ABS
关键词:
整套图纸加完整说明书:
扣扣849427068。
未注公差取MT5级精度
要求设计圆盖模具
图1-1圆盖塑件图
塑件的工艺性分析包括塑件的原材料分析、塑件的尺寸精度分析、塑件表面质量和塑件的结构工艺分析,其具体分析如下。
1.1塑件原材料分析
见表1-1。
表1-1塑件的原材料分析
材料品种
ABS,属于热塑性塑料。
结构特点
无定形高聚物,透明。
使用温度
只能在较低温度下使用,热变形温度一般在70~98℃。
化学稳定性
有一定的化学稳定性,能耐碱、硫酸、磷酸。
10%~30%的盐酸、稀硝酸及其他有机酸,但不耐硝酸及氧化剂的作用等。
性能特点
电绝缘性(尤其是高频绝缘性)优良,无色透明,透光率仅次于有机玻璃,着色性、耐水性良好,机械强度一般。
成型特点
无定性料,吸湿性小,不易分解;
流动性较好(溢边值为0.03mm左右),可用螺杆或柱塞注射机成型;喷嘴用直通式或自锁式,但应防止飞边;
易采用高料温、高模温、低注射压力、延长注射时间,有利于降低内应力,防止缩孔、变形。
结论
1.流动性好采用螺杆或柱塞式注射机成型,喷嘴用直通式或自锁式;可采用各种形式的浇口,浇口和塑件应圆弧连接,防止去除浇口时损坏塑件;脱模斜度应大,顶出均匀,以防脱模不良而发生开裂变形。
2.温度敏性高,对料温应严格控制,否则会出现“银丝”、透明性差现象。
3.塑件壁厚均匀,最好不带嵌件(如有嵌件应预热),各面应圆弧连接,不宜有缺口、尖角。
1.2塑件的尺寸精度、表面质量分析
1.2.1塑件的尺寸精度分析
该塑件需标注的公差尺寸,属于一般精度要求,其他尺寸均为未标注公差的自由尺寸,可按MT5查取公差,塑件的主要尺寸的公差(单位均为mm)。
1.2.2塑件表面质量分析
该塑件要求外形美观,外表面没有斑点及熔接痕,粗糙度可取Ra1.6µm,而塑件内部没有较高的表面粗糙度要求。
1.3塑件的结构工艺分析
具体分析如下:
(1)从图纸上分析,该塑件基本上为对称体,该塑件大端接触处设计脱模容易,且飞边去除容易,设计合理。
(2)该塑件另一端端部有圆弧过渡,便于人手触摸,设计合理。
综上所述,该塑件可采用注射成型加工。
1.4确定成型设备选择与模具工艺规程编制
(1)计算塑件的体积V=448,0316mm3(过程略)。
(2)计算塑件的质量计算塑件的质量为了选择注射机及确定模具型腔数。
根据有关手册查得ρ=1.05g/cm3。
所以,塑件的质量为:
(1)
根据塑件形状及尺寸采用一模两件的模具结构;考虑外形尺寸,对塑件及材料的分析
及注塑时所需的压力情况,参考模具设计手册出初选柱塞式注射机:
XS-Z-60。
该注塑机的参数如表1-3所示:
表1-3注塑机的参数
额定注射量/cm³
60
螺杆直径/mm
38
注射压力/Mpa
122
注射行程/mm
170
注射方式
柱塞式
锁模力/KN
500
最大成型面积/cm³
130
最大开合模行程/mm
180
模具最大厚度/mm
200
模具最小厚度/mm
70
喷嘴圆弧半径/mm
12
喷嘴孔直径/mm
4
动定模固定板尺寸/mm
330x440
拉杆空间/mm
190x300
合模方式
液压-机械
顶出方式
中心顶出
1.5塑件的注射工艺参数的确定
1.5.1ABS注射成型工艺参数
ABS注射成型工艺参数见表1-4,试模时,可根据实际情况做适当调整。
表1-4ABS
工艺参数
规格
工艺参数
规格
预热和干燥
温度t:
60~75
成型时间/s
注射时间
15~45
时间s:
2h
保压时间
0~3
料筒温度t/℃
前段
140~160
冷却时间
15~60
中段
160~170
总周期
40~120
后段
170~190
螺杆转速n/(r/min)
48
喷嘴温度t/℃
160~170
后处理
方法
红外线灯,烤箱
模具温度t/℃
32~65
温度t/℃
70
注射压力p/Mpa
60~110
时间s/h
2~4
1.5.2塑件的结构工艺性分析
圆盖模塑工艺卡见表1-5。
表1-5圆盖模塑工艺卡
(厂名)
塑料注射成型工艺卡片
资料编号
车间
共页
第页
零件名称
圆盖
材料牌号
ABS
设备型号
XS-Z-60
装配图号
AN00-00
材料定额
大批量
每模件数
4件
零件图号
单件质量
0.470g
工装号
材料干燥
设备
温度t/℃
60~75
时间/h
2
料筒温度
喷嘴/℃
160~170
前段/℃
140~160
中段/℃
160~170
后段/℃
170~190
模具温度/℃
32~65
时间
注射/s
15~45
保压/s
0~3
冷却/s
15~60
压力
注射压力Mpa
60~110
背压Mpa
后处理
温度/℃
鼓风烤箱70
时间定额
辅助
时间/h
24
单件
检验
编制
校对
审核
组长
车间主任
检验组长
主管工程师
第二章注射模的结构设计
注射模结构设计主要包括:
分型面的选择,模具型腔数目的确定及型腔的排列,浇注系统设计,型芯型腔结构的确定,推件方式,模具结构零件设计等内容。
2.1分型面的选择
根据塑件制品分型面的设计与选择原则,分型面应该设计在零件截面最大的部位,且不影响零件的外观。
塑件就包紧在动模型芯一点,因而留在动模点,这使模具的结构变得简单,因而选择该方法为模具设计的分型方案。
2.2型腔数目的确定及型腔布局
(1)若采用一模一腔,由于此零件的外型尺寸很大,模架相对于这个模具显得特别大,且适合大批量生产。
(2)若采用一模多件,生产效率高,资源的利用率也高,这里选用的是一模两腔圆形分布,模具尺寸适中,不适合大批量生产,这样也有利于浇注系统的排列和模具的平衡。
2.3浇注系统的设计
2.3.1主流道的设计
根据手册查得XS-Z-60型注射机喷的有关尺寸如下:
喷嘴半径:
R1=12mm;
喷嘴孔直径:
d1=Ø4mm;
根据模具主流道与喷嘴的关系:
R=R1+(1~2)mm;d=d1+(0.5~1)mm
取主流道球面半径:
R=14mm;
取主流道的小端直径:
d=Ø4.5mm;
2.3.2分流道的设计
分流道的形状及尺寸与塑件的体积、壁厚、形状的复杂程度,注射速率的因素有关。