物料自动分拣控制系统设计.docx
《物料自动分拣控制系统设计.docx》由会员分享,可在线阅读,更多相关《物料自动分拣控制系统设计.docx(30页珍藏版)》请在冰点文库上搜索。
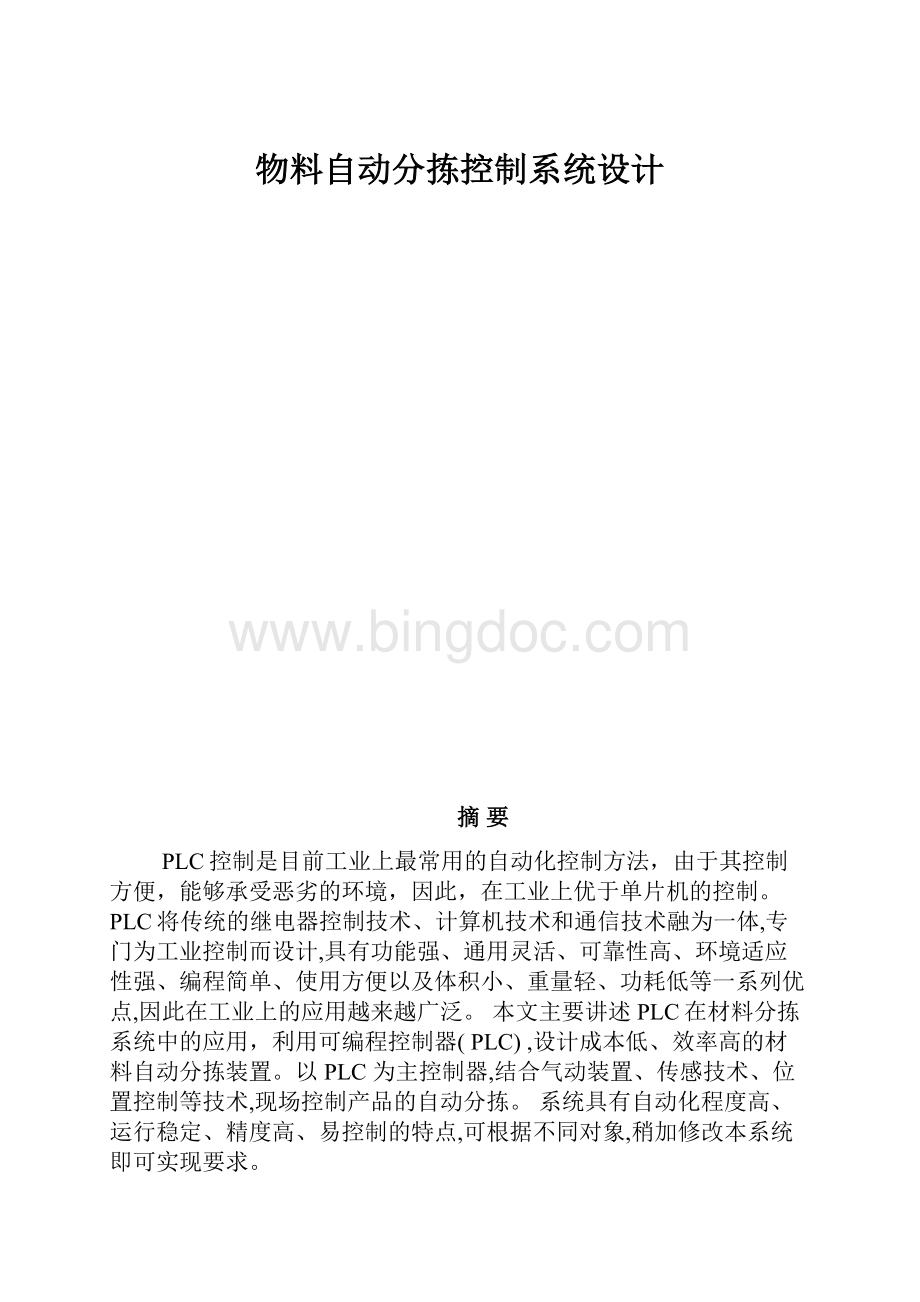
物料自动分拣控制系统设计
摘要
PLC控制是目前工业上最常用的自动化控制方法,由于其控制方便,能够承受恶劣的环境,因此,在工业上优于单片机的控制。
PLC将传统的继电器控制技术、计算机技术和通信技术融为一体,专门为工业控制而设计,具有功能强、通用灵活、可靠性高、环境适应性强、编程简单、使用方便以及体积小、重量轻、功耗低等一系列优点,因此在工业上的应用越来越广泛。
本文主要讲述PLC在材料分拣系统中的应用,利用可编程控制器(PLC),设计成本低、效率高的材料自动分拣装置。
以PLC为主控制器,结合气动装置、传感技术、位置控制等技术,现场控制产品的自动分拣。
系统具有自动化程度高、运行稳定、精度高、易控制的特点,可根据不同对象,稍加修改本系统即可实现要求。
关键词:
可编程控制器;分拣装置;控制系统;传感器
ABSTRACT
PLCcontrolisthemostcommonlyusedindustrialautomationcontrolmethod,becauseofitsconvenientcontroltowithstandanadverseenvironment,itisbetterthanMCUcontrolintheindustrial.PLCtraditionalrelaycontroltechnology,computerandcommunicationtechnologiesareintegratedspecificallyforindustrialcontrolanddesign,havestrongfunction,commonflexible,highreliabilityandenvironmentaladaptability,andprogrammingsimple,easytouseandsmallsize,lightweight,aseriesoflow-poweradvantagesinindustrialapplicationsbecomemoreextensive.
ThispaperfocusesonthePLCinthecannedbeverageproduction,Thedesignofanautomaticsortingdevicewithlowcostandhighefficiencyispresentedinthepaper,whichregardsprogrammablelogiccontroller(PLC)asthemastercontrollerandcombinespneumaticdevice,sensingtechnology,positioncontrolandothertechnologytoimplementautomaticselectingoftheproductslive.Thedeviceischaracteristicofhighautomation,steadyrunning,highprecisionandeasycontrol,whichcanfulfilltherequirementaccordingtodifferentsituationswithlittlemodifications.
Keywords:
programmablelogiccontroller;sortingdevice;controlsystem;sensors
绪论
1.1物料分拣系统概述
自动化的程度是工作发展程度的标志,自动分拣正是自动化中的一个必不可的部分,而PLC控制分拣装置以其成本低,效率高的优点,已经成为主流,他可以根据设定的程序无人的,高效的工作,维护费用极少。
由于全部采用机械自动化作业,因此,分拣处理能力较大,分拣分类数量也较多。
节省了大量的人力劳动,减少了企业的额外支出,是企业节省成本最好的方法。
尤其在需要进行材料分拣的企业,以往一直采用人工分拣的方法,由于人工作的个人限制性,因人而致使有的生产效率很低,误差多,生产成本高,企业的竞争能力差,阻碍了企业的正常发展。
所以分拣装置人PLC控制系统必然会取代人工的分拣工作。
这也正是其能够迅猛发展的根本原因,好是社会和企业发展的必然。
随着工业的越来越发展,业水平的越来越高,自动分拣装置完全取代人工作业是必须的也是必然的。
材料分拣采用可编程控制器PLC进行控制,能连续、大批量地分拣货物,分拣误差率低且劳动强度大大降低,可显著提高劳动生产率。
而且,分拣系统能灵活地与其他物流设备无缝连接,实现对物料实物流、物料信息流的分配和管理。
其设计采用标准化、模块化的组装,具有系统布局灵活,维护、检修方便等特点,受场地原因影响不大。
同时,只要根据不同的分拣对象,对本系统稍加修改即可实现要求,非常方面。
现在的大部分的企业都有自己的生产流水线,而自动分拣装置是流水线上不可少的部分,有的流水线甚至要用到多个分拣装置,这也说明它有着很大的市场空间。
PLC控制是目前工业上最常用的自动化控制方法,由于其控制方便,能够承受恶劣的环境,因此,在工业上优于单片机的控制。
材料分拣装置的PLC控制系统利用了PLC技术、位置控制技术、气动技术、传感器技术、电动技术传动技术等,这些技术都是自动化技术中必要的,可以说是现代工作生产现场生产设备的一个微小的模型。
本论文主要介绍了材料分拣装置的PLC控制系统的结构、硬件组成、软件控制、程序流程以及软硬件的组装和调试方法。
让大家对材料分拣装置的PLC控制系统有一个较为深入的了解。
1.2物料分拣系统的发展现状与趋势
纵观国内外物料分拣系统的应用情况可以发现,国外的物流配送中心或工业中倾向于采用自动化程度很高的分拣系统,而且应用也较为广泛。
而在我国,由于物流业起步晚,物料分拣系统中人工作业的比例也较高。
尽管自动分拣系统有非常多的优点,但因其要求使用者必须具备一定的技术经济条件,在发达国家某些行业不用自动分拣系统的情况也很普遍。
其主要原因有两点:
一是一次性投资巨大,先期投入回收慢。
系统的设备复杂,投资和运营成本相当高,需要可靠的货源作保证,也许只有大型生产企业或专业物流公司才有能力投资。
小企业则无能为力。
二是系统对商品外包装要求高。
为使大部分商品都能用机械进行自动分拣,需要采取诸如推行标准化包装、根据分拣商品统一的包装特性定制分拣机等二次措施。
但要让所有商品的供应商都执行国家的包装标准是很困难的,定制分拣机又会使硬件成本上升,且越是特别的通用性就越差。
虽然物料分拣系统有它的局限性,但随着社会的高速发展,一切都讲究效率,我相信高效率的物料分拣系统设计将会被人们越来越重视。
而本设计就针对物料分拣设计出了一个由PLC控制的分拣系统,解决了组成系统的设备能在安全工作的同时又能提高物料分拣效率的问题。
1.3研究的目的及意义
分拣系统中物料传感器以及气缸应自动化设备更新时的需要,可以大量代替单调往复或高精度需求的工作,在先进制造领域中扮演着极其重要的角色。
它可以搬运货物、分拣物品、代替人的繁重劳动。
可以实现生产的机械化和自动化,能在高温、腐蚀及有毒气体等环境下操作以保护人身安全,可以广泛应用于机械制造、冶金、电子、轻工业和原子能等部门。
分料盘在物料分拣中起着关键作用,安装在其内部的步进电机的驱动将使分料盘发生相应的动作来达到物料的最终分拣。
由于同样实现了自动化分拣,因此在现代工业中也较广泛地使用。
可编程控制器(PLC)是以中央处理器为核心,综合了计算机和自动控制等先进技术,具有可靠性高、功能完善、组合灵活、编程简单、功耗低等优点,已成为目前在物料分拣控制系统中使用最多的控制方式。
使用PLC的自动控制系统具有体积小,可靠高,故障率低,动作精度高等优点。
使其适应了工业等的需要。
本课题试图开发PLC对物料与分拣物料的控制,并借助必要的精密传感器,使其能够对不同颜色以及种类的物料按预先设定的程序进行分拣,适用于可变换生产品种的中小批量自动化生产,广泛应用于柔性生产线。
采用PLC控制,是一种预先设定的程序进行物料分拣的自动化装置,可部分代替人工在高温和危险的作业区进行单调持久的作业,并且在产品变化或临时需要对物料传感器,气缸进行新的分配任务时,可以允许方便的改动或重新设计其新部件,而对于位置改变时,只要重新编程,并能很快地投产,降低了安装和转换工作的费用。
第1章材料分拣装置结构及总体设计
PLC控制分拣装置涵盖了PLC技术、气动技术、传感器技术、位置控制技术等内容,是实际工业现场生产设备的微缩模型。
本章主要介绍分拣装置的工艺过程及控制要求。
要想进行PLC控制系统的设计,首先必须对控制对象进行调查,搞清楚控制对象的工艺过程、工作特点,明确控制要求以及各阶段的特点和各阶段之间的转换条件。
1.1材料分拣装置工作过程概述
如图1-1所示为本分拣装置的结构示意图。
图1-1材料分拣装置结构示意图
它采用台式结构,内置电源,有三相异步电机、汽缸、电磁阀、旋转编码器、气动减压器、滤清器、气压指示等部件,可与各类气源相连接。
选用颜色识别传感器及对不同材料敏感的电感式传感器,分别固定在网板上,且允许重新安装传感器排列位置或选择网板不同区域安装。
系统上电后,要等到手动启动后系统才进入运行状态,当有物料从料口到传送带上时,光电传感器输出信号给PLC,同时电感传感器和光纤传感器进行检测,将物料信息反馈给PLC,PLC根据物料的材质和颜色,选择不同的速度传送道不同的位置,并控制对应的电磁阀动作,将物料推入对应的仓中。
1.2系统的技术指标
输入电压:
AC200~240V(带保护地三芯插座)
消耗功率:
250W
环境温度范围:
-5~40℃
气源:
大于0.2MPa切小于0.85Mpa
1.3系统的设计要求
系统的设计要求主要包括功能要求和控制要求,进行设计之前,首先应分析控制对象的要求。
1.3.1功能要求
材料分拣装置应实现基本功能如下
(1)分拣出金属和非金属
(2)分拣黑色和白色
(3)金属料、白色非金属和黑色非金属料分别用不同的速度传送
1.3.2系统的控制要求
系统利用各种传感器对待测材料进行检测并分类。
当待测物体经机械手或其他传送机构送入传送带后,依次接受各种传感器检测。
如果被某种传感器测中,通过相应的气动装置将其推入料仓中。
其控制要求有如下几个方面:
(1)系统送电后,各部分在初始位置时,需要手动启动后方可运行
(2)电机运行,带动传输带传送物体向前运行
(3)有物料时,电动机带动传送带动作,将物料送走
(4)当电感传感器检测到金属物料时,汽缸1动作
(5)当光纤传感器检测到白色非金属物料时,汽缸2动作
(6)当电感传感器和光纤传感器均没有检测到,而光电传感器检测到有物料时,汽缸3动作
(7)汽缸运行应有伸出限位保护
(8)按下停止按钮,要等到该物料分拣完成后方可停止
(9)启动后,有物料就自动分拣,而分拣完成就自动停止
第2章控制系统的执行机构设计
检测元件与执行装置的选择主要是对旋转编码器和各个传感器的选择,并对其作简要介绍。
2.1光电式旋转编码器
旋转编码器是与步进电机连接在一起,在本系统中可用来作为控制系统的计数器,并提供脉冲输入。
它转化为位移量,可对传输带上的物料进行位置控制。
传送至相应的传感器时,发出信号到PLC,以进行分拣,也可用来控制步进电机的转速。
本系统选用鑫亚H38S6-500-3-2-24增量式旋转编码器,其组成和原理如图2-3所示。
图2-1旋转编码器的组成及原理示意图
旋转编码器介绍:
旋转编码器是用来测量转速的装置。
技术参数主要有每转脉冲数(几十个到几千个都有),和供电电压等。
它分为单路输出和双路输出两种。
单路输出是指旋转编码器的输出是一组脉冲,而双路输出的旋转编码器输出两组相位差90度的脉冲,通过这两组脉冲不仅可以测量转速,还可以判断旋转的方向。
编码器如以信号原理来分,可分为增量脉冲编码器(SPC)和绝对脉冲编码器(APC)两者一般都应用于速度控制或位置控制系统的检测元件。
编码器码盘的材料有玻璃、金属、塑料,玻璃码盘是在玻璃上沉积很薄的刻线,其热稳定性好,精度高,金属码盘直接以通和不通刻线,不易碎,但由于金属有一定的厚度,精度就有限制,其热稳定性就要比玻璃的差一个数量级,塑料码盘是经济型的,其成本低,但精度、热稳定性、寿命均要差一些。
工作原理如下:
由一个中心有轴的光电码盘,其上有环形通、暗的刻线,有光电发射和接收器件读取,获得四组正弦波信号组合成A、B、C、D,每个正弦波相差90度相位差(相对于一个周波为360度),将C、D信号反向,叠加在A、B两相上,可增强稳定信号;另每转输出一个Z相脉冲以代表零位参考位。
由于A、B两相相差90度,可通过比较A相在前还是B相在前,以判别编码器的正转与反转,通过零位脉冲,可获得编码器的零位参考位。
分辨率:
编码器以每旋转360度提供多少的通或暗刻线称为分辨率,也称解析分度、或直接称多少线,一般在每转分度5~10000线。
信号输出:
信号输出有正弦波(电流或电压),方波(TTL、HTL),集电极开路(PNP、NPN),推拉式多种形式,其中TTL为长线差分驱动(对称A,A-;B,B-;Z,Z-),HTL也称推拉式、推挽式输出,编码器的信号接收设备接口应与编码器对应。
信号连接:
编码器的脉冲信号一般连接计数器、PLC、计算机,PLC和计算机连接的模块有低速模块与高速模块之分,开关频率有低有高。
如单相联接,用于单方向计数,单方向测速。
A、B两相联接,用于正反向计数、判断正反向和测速。
A、B、Z三相联接,用于带参考位修正的位置测量。
A、A-,B、B-,Z、Z-连接,由于带有对称负信号的连接,电流对于电缆贡献的电磁场为0,衰减最小,抗干扰最佳,可传输较远的距离。
对于TTL的带有对称负信号输出的编码器,信号传输距离可达150米。
对于HTL的带有对称负信号输出的编码器,信号传输距离可达300米。
H38S6-500-3-2-24增量式旋转编码器的分辨率为500线,而本系统带动传送带的带轮半径为30mm,所以脉冲当量为
U=2πr/500=0.0377mm
从料口到1、2、3号仓的距离分别为200mm、300mm、400mm,所以脉冲数分别为
n1=L1/u=530
n2=L2/u=796
n3=L3/u=1061
2.2电感式接近开关
电感式接近开关属于有开关量输出的位置传感器,用来检测金属物体。
它由LC高频振荡器和放大处理电路组成,利用金属物体在接近这个能产生电磁场的振荡感应头时,使物体内部产生涡流。
这个涡流反作用于接近开关,使接近开关振荡能力衰减,内部电路的参数发生变化。
由此,可识别出有无金属物体接近,进而控制开关的通或断。
本系统选用LJG2A-4/ZONA2电感传感器。
接线图如图2-4,原理图如图2-5。
图2-2LJG2A-4/ZONA2型电感传感器接线图
图2-3电感传感器工作原理图
电感传感器介绍:
由铁心和线圈构成的将直线或角位移的变化转换为线圈电感量变化的传感器,又称电感式位移传感器。
这种传感器的线圈匝数和材料导磁系数都是一定的,其电感量的变化是由于位移输入量导致线圈磁路的几何尺寸变化而引起的。
当把线圈接入测量电路并接通激励电源时,就可获得正比于位移输入量的电压或电流输出。
电感式传感器的特点是:
①无活动触点、可靠度高、寿命长;②分辨率高;③灵敏度高;④线性度高、重复性好;⑤测量范围宽(测量范围大时分辨率低);⑥无输入时有零位输出电压,引起测量误差;⑦对激励电源的频率和幅值稳定性要求较高;⑧不适用于高频动态测量。
电感式传感器主要用于位移测量和可以转换成位移变化的机械量(如力、张力、压力、压差、加速度、振动、应变、流量、厚度、液位、比重、转矩等)的测量。
常用电感式传感器有变间隙型、变面积型和螺管插铁型。
在实际应用中,这三种传感器多制成差动式,以便提高线性度和减小电磁吸力所造成的附加误差。
2.3光纤传感器
选用欧姆龙(OMRON)公司生产的,型号为E3X-NA11光纤传感器。
此传感器为黑白颜色传感器,可检测目标物体对黑白色的反射比率,从而鉴别物体颜色。
E3X-NA11传感器引脚如图2-7所示
图2-4光纤传感器电路图
光纤传感器介绍:
光纤是光电接近开关(简称光纤式光电开关)由光纤检测头、光纤放大器两部分组成,放大器和光纤检测头是分离的两部分,光纤检测头的尾部部分分成分别插入两个光纤孔。
光纤是光电传感器的输出连接至PLC。
光纤式光电开关的传感器部分没有丝毫电路连接,不产生热量,只利用很少的光能,这些特点使光纤传感器成为危险环境下的理想选择。
还可以用于关键生产设备的长期高温可靠稳定的监视。
相对于传统传感器,光纤传感器的优点有:
抗电磁干扰,可工作于恶劣黄警,传输距离长,使用寿命长,此外,由于光纤头具有较小的体积,所以可以安装在很小的空间里。
光纤传感器调试:
安装完成后,用螺丝刀进行灵敏度的调节,调节时会看到“入光量指示灯”发生的变化。
在检测距离固定后当白色共检出现在光纤头下方时,“动作显示灯”亮,提示检测到工件,当黑色共检出现在光纤头下方时,“动作显示灯”不亮,这个光线是光电开关调试完成。
2.4电动机
步进电机是将电脉冲信号转变为角位移或线位移的开环控制元件。
在非超载的情况下,电机的转速、停止的位置只取决于脉冲信号的频率和脉冲数,而不受负载变化的影响,即给电机加一个脉冲信号,电机则转过一个步距角。
这一线性关系的存在,加上步进电机只有周期性的误差而无累积误差等特点。
使得在速度、位置等控制领域用步进电机来控制变的非常的简单。
步进电机作为执行机构用于带动传输带输送物料前行,与旋转编码器连接在一起。
可以通过控制脉冲个数,来控制角位移量,从而达到准确定位的目的。
同时,可以通过控制脉冲频率来控制材料分拣装置的可编程控制系统控制电机转动的速度,达到调速的目的。
步进电机选用的型号为42BYGH101。
2.5磁控接近开关
磁控接近开关(简称磁控开关)主要用于检测位置变化磁控开关是一种非接触式位置检测开关,不会磨损和损伤被测对象速度比较快。
磁控接近开关工作原理:
当有磁性物质接近磁控开关时,磁控开关被磁化而使得接点吸合在一起,从而使回路接通。
在本系统中,采用上海双旭电子有限公司的D-C73磁性开关,在气缸的活塞杆上安装磁性物质,在汽缸缸筒外面各安装一个磁控开关,这样就能识别各是否到极限位置。
应用时,采用共阴接法,棕色线接PLC输入端,蓝色线接公共端。
图2-8磁性开关的外观及工作原理
图2-9磁性开关的内部电路
调试:
先将磁控开关安装在气缸外面,先不拧紧,把气缸杆拉出,然后调节磁控开关的位置,调到指示灯亮的时候,说明位置刚好,拧紧螺丝即可。
2.6光电开关
光电开关是利用光的各种性质,检测物体的有无和表面状态的变化等的传感器。
用在环境比较好、无灰尘、无粉尘污染的场合,为非接触式测量,对被测物体无任何影响,在工业生产过程中得到广泛的应用。
此处采用漫反射式光电开关,它是一种集发射器和接收器于一体的传感器,当有被检测物体经过时,物体将光电开关发射器发射的足够量的光线反射到接收器,于是光电开关就产生了开关信号。
当被检测物体的表面光亮或其反光率极高时漫反射式的光电开关是首选的检测模式。
该系统采用SICK(德国施克)公司的MHT15-N2317光电开关,其外形和工作原理如下图所示:
2-10MHT15-N2317光电开关工作的原理
根据上图所示,在接线时,光电开关的褐色线接电源的“+”端,蓝色线接电源的“-”端,黑色线接PLC的输入点。
安装与调试:
光电开关具有检测距离长,对检测物体限制小,响应速度快,分辨率高,便于调整等优点。
但在安装过程中,必须保证传感器到被检测物体的距离在“检出距离”的范围内,因此,需要认真调试。
当检测到物料时,磁性开关上的指示灯就会离开亮,此时有输出,否则就没检测到。
2.7电磁阀及气缸
气源处理装置:
气源处理组件及其回路原理图分别如图1-14所示。
气源处理组件是气动控制系统中的基本组成器件,它的作用是除去压缩空气中所含的杂质及凝结水,调节并保持恒定的工作压力。
在使用时,应注意经常检查过滤器中凝结水的水位,在超过最高标线以前,必须排放,以免被重新吸入。
气源处理组件的气路入口处安装一个快速气路开关,用于启/闭气源,当把气路开关向左拔出时,气路接通气源,反之把气路开关向右推入时气路关闭。
气源处理组件输入气源来自空气压缩机,所提供的压力为0.6~1.0MPa,输出压力为0~0.8MPa可调。
输出的压缩空气通过快速三通接头和气管输送到工作单元。
双作用直线气缸:
标准气缸是指气缸的功能和规格是普遍使用的、结构容易制造的、制造厂通常作为通用产品供应市场的气缸。
双作用气缸具有结构简单,输出力稳定,行程可根据需要选择的优点,但由于是利用压缩空气交替作用于活塞上实现伸缩运动的,回缩时压缩空气的有效作用面积较小,所以产生的力要小于伸出时产生的推力。
这里采用CDJ2B16*60气缸,其工作原理和示意图如下:
图2-11单电控电磁换向阀的工作原理
单电控电磁换向阀组:
电磁换向阀是利用其电磁线圈通电时,静铁芯对动铁芯产生电磁吸力使阀芯切换,达到改变气流方向的目的。
电磁阀带有手动换向和加锁钮,有锁定(LOCK)和开启(PUSH)2个位置。
用小螺丝刀把加锁钮旋到在LOCK位置时,手控开关向下凹进去,不能进行手控操作。
只有在PUSH位置,可用工具向下按,信号为“1”,等同于该侧的电磁信号为“1”;常态时,手控开关的信号为“0”。
在进行设备调试时,可以使用手控开关对阀进行控制,从而实现对相应气路的控制,以改变推料缸等执行机构的控制,达到调试的目的。
这里采用MVSE-300-4E1单控电磁阀,工作原理如下:
图2-12单电控电磁换向阀的工作原理
第3章控制系统的硬件设计
PLC控制系统的硬件设计,主要是根据被控制对象对PLC控制系统的功能要求,确定系统所需的用户输入、输出设备,选择合适的PLC类型,并分配I/O点。
3.1系统的硬件结构
设计系统的硬件结构框图,如图2-1所示。
图3-1系统的硬件结构框图
3.2系统关键技术
系统关键技术即分析控制系统的要求,确定I/O点数,选择PLC的型号,然后进行I/O分配。
3.2.1确定I/O点数
根据控制要求,输入应该有2个开关信号,3个传感器信号,包括电感传感器、光纤感器。
相应地,有3个汽缸运动位置信号,每个汽缸的动作到位信号,共计11个信号。
输出包括控制电动机以不同速度运行的3个发向变频器的信号,以及3个控制汽缸动作的电磁阀。
共需I/O点18个,其中11个输入,8个输出。
3.2.2PLC的选择
根据上面所确定的I/O点数,且该材料分拣装置的控制为开关量控制。
因此,选择一般的小型机即可满足控制要求。
本系统选用西门子公司的S7-200系列CPU224CN型PLC。
它有14个输入点,10个输出点,满足本系统的要求。
3.2.3PLC的I/O分配
根据所选择的PLC型号,对本系统中PLC的输入输出端子进行分配,如表1所示
表1材料分拣装置PLC输入和输出端子分配表
西门子PLC(I/O)
分拣系统接口(I/O)
备注
输
入
部