风机盖注塑模毕业设计说明书.docx
《风机盖注塑模毕业设计说明书.docx》由会员分享,可在线阅读,更多相关《风机盖注塑模毕业设计说明书.docx(54页珍藏版)》请在冰点文库上搜索。
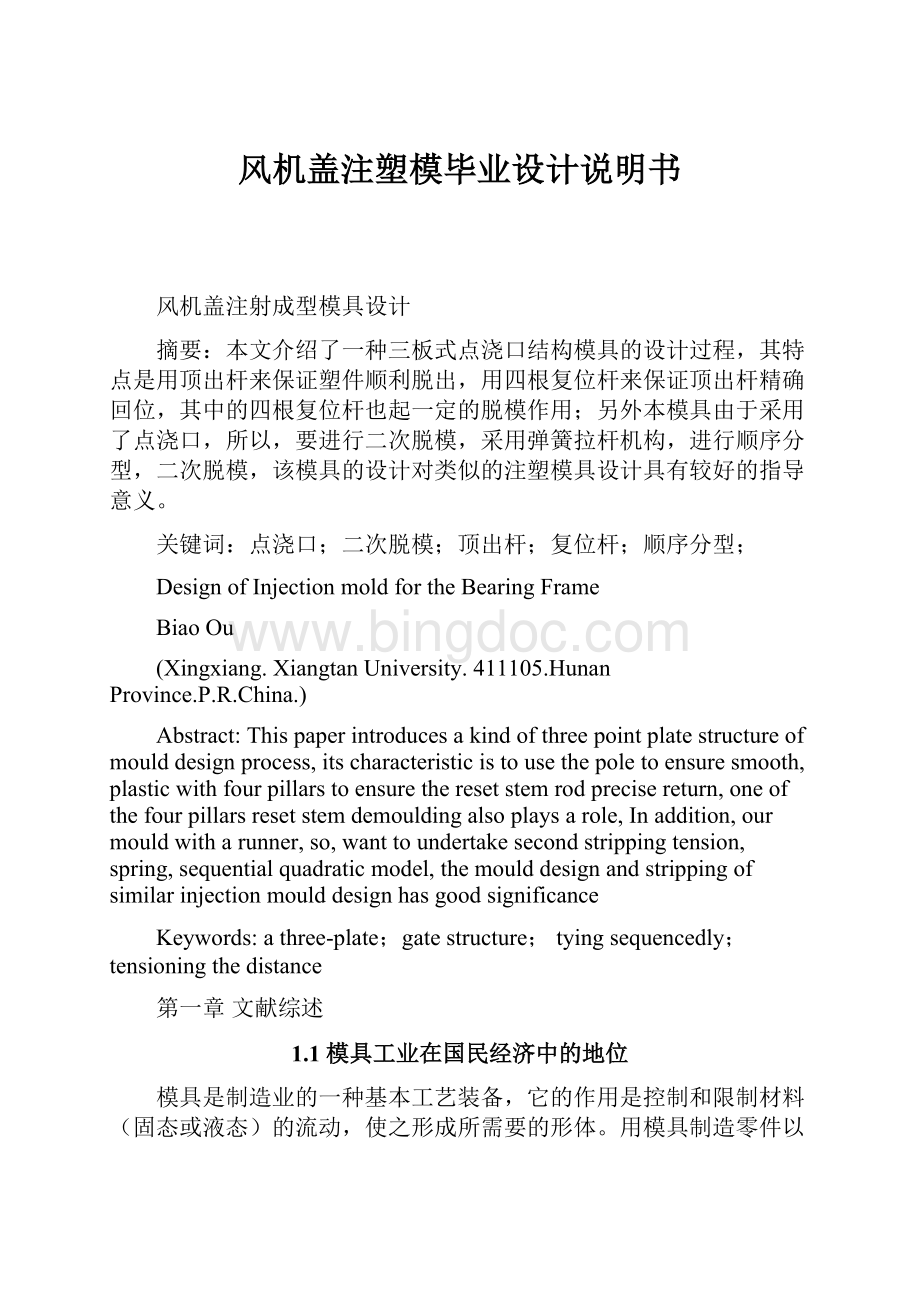
风机盖注塑模毕业设计说明书
风机盖注射成型模具设计
摘要:
本文介绍了一种三板式点浇口结构模具的设计过程,其特点是用顶出杆来保证塑件顺利脱出,用四根复位杆来保证顶出杆精确回位,其中的四根复位杆也起一定的脱模作用;另外本模具由于采用了点浇口,所以,要进行二次脱模,采用弹簧拉杆机构,进行顺序分型,二次脱模,该模具的设计对类似的注塑模具设计具有较好的指导意义。
关键词:
点浇口;二次脱模;顶出杆;复位杆;顺序分型;
DesignofInjectionmoldfortheBearingFrame
BiaoOu
(Xingxiang.XiangtanUniversity.411105.HunanProvince.P.R.China.)
Abstract:
Thispaperintroducesakindofthreepointplatestructureofmoulddesignprocess,itscharacteristicistousethepoletoensuresmooth,plasticwithfourpillarstoensuretheresetstemrodprecisereturn,oneofthefourpillarsresetstemdemouldingalsoplaysarole,Inaddition,ourmouldwitharunner,so,wanttoundertakesecondstrippingtension,spring,sequentialquadraticmodel,themoulddesignandstrippingofsimilarinjectionmoulddesignhasgoodsignificance
Keywords:
athree-plate;gatestructure;tyingsequencedly;tensioningthedistance
第一章文献综述
1.1模具工业在国民经济中的地位
模具是制造业的一种基本工艺装备,它的作用是控制和限制材料(固态或液态)的流动,使之形成所需要的形体。
用模具制造零件以其效率高,产品质量好,材料消耗低,生产成本低而广泛应用于制造业中。
模具工业是国民经济的基础工业,是国际上公认的关键工业。
模具生产技术水平的高低是衡量一个国家产品制造水平高低的重要标志,它在很大程度上决定着产品的质量,效益和新产品的开发能力。
振兴和发展我国的模具工业,正日益受到人们的关注。
早在1989年3月中国政府颁布的《关于当前产业政策要点的决定》中,将模具列为机械工业技术改造序列的第一位。
具工业既是高新技术产业的一个组成部分,又是高新技术产业化的重要领域。
模具在机械,电子,轻工,汽车,纺织,航空,航天等工业领域里,日益成为使用最广泛的主要工艺装备,它承担了这些工业领域中60%~90%的产品的零件,组件和部件的生产加工。
模具制造的重要性主要体现在市场的需求上,仅以汽车,摩托车行业的模具市场为例。
汽车,摩托车行业是模具最大的市场,在工业发达的国家,这一市场占整个模具市场一半左右。
汽车工业是我国国民经济五大支柱产业之一,汽车工业重点是发展零部件,经济型轿车和重型汽车,汽车模具作为发展重点,已在汽车工业产业政策中得到了明确。
汽车基本车型不断增加,2005年将达到170种。
一个型号的汽车所需模具达几千副,价值上亿元。
为了适应市场的需求,汽车将不断换型,汽车换型时约有80%的模具需要更换。
中国摩托车产量位居世界第一,据统计,中国摩托车共有14种排量80多个车型,1000多个型号。
单辆摩托车约有零件2000种,共计5000多个,其中一半以上需要模具生产。
一个型号的摩托车生产需1000副模具,总价值为1000多万元。
其他行业,如电子及通讯,家电,建筑等,也存在巨大的模具市场。
目前世界模具市场供不应求,模具的主要出口国是美国,日本,法国,瑞士等国家。
中国模具出口数量极少,但中国模具钳工技术水平高,劳动成本低,只要配备一些先进的数控制模设备,提高模具加工质量,缩短生产周期,沟通外贸渠道,模具出口将会有很大发展。
研究和发展模具技术,提高模具技术水平,对于促进国民经济的发展有着特别重要的意义。
1.2各种模具的分类和占有量
模具主要类型有:
冲模,锻摸,塑料模,压铸模,粉末冶金模,玻璃模,橡胶模,陶瓷模等。
除部分冲模以外的的上述各种模具都属于腔型模,因为他们一般都是依靠三维的模具形腔是材料成型。
(1)冲模:
冲模是对金属板材进行冲压加工获得合格产品的工具。
冲模占模具总数的50%以上。
按工艺性质的不同,冲模可分为落料模,冲孔模,切口模,切边模,弯曲模,卷边模,拉深模,校平模,翻孔模,翻边模,缩口模,压印模,胀形模。
按组合工序不同,冲模分为单工序模,复合模,连续模。
(2)锻模:
锻模是金属在热态或冷态下进行体积成型是所用模具的总称。
按锻压设备不同,锻模分为锤用锻模,螺旋压力机锻模,热模锻压力锻模,平锻机用锻模,水压机用锻模,高速锤用锻模,摆动碾压机用锻模,辊锻机用锻模,楔横轧机用锻模等。
按工艺用途不同,锻模可分为预锻模具,挤压模具,精锻模具,等温模具,超塑性模具等。
(3)塑料模:
塑料模是塑料成型的工艺装备。
塑料模约占模具总数的35%,而且有继续上升的趋势。
塑料模主要包括压塑模,挤塑模,注射模,此外还有挤出成型模,泡沫塑料的发泡成型模,低发泡注射成型模,吹塑模等。
(4)压铸模:
压铸模是压力铸造工艺装备,压力铸造是使液态金属在高温和高速下充填铸型,在高压下成型和结晶的一种特殊制造方法。
压铸模约占模具总数的6%。
(5)粉末冶金模:
粉末冶金模用于粉末成型,按成型工艺分类粉末冶金模有:
压模,精整模,复压模,热压模,粉浆浇注模,松装烧结模等。
模具所涉及的工艺繁多,包括机械设计制造,塑料,橡胶加工,金属材料,铸造(凝固理论),塑性加工,玻璃等诸多学科和行业,是一个多学科的综合,其复杂程度显而易见。
1.3我国模具工业的现状
自20世纪80年代以来,我国的经济逐渐起飞,也为模具产业的发展提供了巨大的动力。
20世纪90年代以后,大陆的工业发展十分迅速,模具工业的总产值在1990年仅60亿元人民币,1994年增长到130亿元人民币,1999年已达到245亿元人民币,2000年增至260~270亿元人民币。
今后预计每年仍会以10℅~15℅的速度快速增长。
目前,我国17000多个模具生产厂点,从业人数五十多万。
除了国有的专业模具厂外,其他所有制形式的模具厂家,包括集体企业,合资企业,独资企业和私营企业等,都得到了快速发展。
其中,集体和私营的模具企业在广东和浙江等省发展得最为迅速。
例如,浙江宁波和黄岩地区,从事模具制造的集体企业和私营企业多达数千家,成为我国国内知名的“模具之乡”和最具发展活力的地区之一。
在广东,一些大集团公司和迅速崛起的乡镇企业,为了提高其产品的市场竞争能力,纷纷加入了对模具制造的投入。
例如,科龙,美的,康佳和威力等知名集团都建立了自己的模具制造中心。
中外合资和外商独资的模具企业则多集中于沿海工业发达地区,现已有几千家。
在模具工业的总产值中,企业自产自用的约占三分之二,作为商品销售的约占三分之一。
其中,冲压模具约占50℅(中国台湾:
40℅),塑料模具约占33℅(中国台湾:
48℅),压铸模具约占6℅(中国台湾:
5℅),其他各类模具约占11(中国台湾:
7℅)。
中国台湾模具产业的成长,分为萌芽期(1961——1981),成长期(1981——1991),成熟期(1991——2001)三个阶段。
萌芽期,工业产品生产设备与技术的不断改进。
由于纺织,电子,电气,电机和机械业等产品外销表现畅旺,连带使得模具制造,维修业者和周边厂商(如热处理产业等)逐年增加。
在此阶段的模具包括:
一般民生用品模具,铸造用模具,锻造用模具,木模,玻璃,陶瓷用模具,以及橡胶模具等。
1981年——1991年是台湾模具产业发展最为迅速且高度成长的时期。
有鉴于模具产业对工业发展的重要性日益彰显,自1982年起,台湾地区就将模具产业纳入“策略性工业适用范围”,大力推动模具工业的发展,以配合相关工业产品的外销策略,全力发展整体经济。
随着民生工业,机械五金业,汽机车及家电业发展,冲压模具与塑料模具,逐渐形成台湾模具工业两大主流。
从1985年起,模具产业已在推行计算机辅助模具设计和制造等CAD/CAM技术,所以台湾模具业接触CAD/CAM/CAE/CAT技术的时间相当早。
成熟期,在国际化,自由化和国际分工的潮流下,1994年,1998年,由台湾地区政府委托金属中心执行“工业用模具技术研究与发展五年计划”与“工业用模具技术应用与发展计划”,以协助业界突破发展瓶颈,并支持产业升级,朝向开发高附加值与进口依赖高的模具。
1997年11月间台湾凭借模具产业的实力,获得世界模具协会(ISTMA)认同获准入会,正式成为世界模具协会会员,。
整体而言,台湾模具产业在这一阶段的发展,随着机械性能,加工技术,检测能力的提升,以及计算机辅助设计,台湾模具厂商供应对象已由传统的民用家电,五金业和汽机车运输工具业,提升到计算机与电子,通信与光电等精密模具,并发展出汽机车用大型钣金冲压,大型塑料射出及精密锻造等模具。
第二章塑件工艺分析
2.1塑件材质工艺性
此风机盖是采用PP(聚丙烯)注塑成的。
查相关手册可知如下:
2.1.1基本特性
聚丙烯,英文名称:
Polypropylene,简称:
PP由丙烯聚合而制得的一种热塑性树脂。
按甲基排列位置分为等规聚丙烯(isotaeticPolyProlene)、无规聚丙烯(atacticPolyPropylene)和间规聚丙烯(syndiotaticPolyPropylene)三种。
甲基排列在分子主链的同一侧称等规聚丙烯;若甲基无秩序的排列在分子主链的两侧称无规聚丙烯;当甲基交替排列在分子主链的两侧称间规聚丙烯。
一般生产的聚丙烯树脂中,等规结构的含量为95%,其余为无规或间规聚丙烯。
工业产品以等规物为主要成分。
聚丙烯也包括丙烯与少量乙烯的共聚物在内。
通常为半透明无色固体,无臭无毒。
由于结构规整而高度结晶化,故熔点高达167℃,耐热,制品可用蒸汽消毒是其突出优点。
密度0.90g/cm3,是最轻的通用塑料。
耐腐蚀,抗张强度30MPa,强度、刚性和透明性都比聚乙烯好。
缺点是耐低温冲击性差,较易老化,但可分别通过改性和添加抗氧剂予以克服。
PP是一种半结晶性材料。
它比PE要更坚硬并且有更高的熔点。
由于均聚物型的PP温度高于0C以上时非常脆因此许多商业的PP材料是加入1~4%乙烯的无规则共聚物或更高比率乙烯含量的钳段式共聚物。
聚物型的PP材料有较低的热扭曲温度(100C)、低透明度、低光泽度、低刚性,但是有有更强的抗冲击强度。
PP的强度随着乙烯含量的增加而增大。
PP的维卡软化温度为150C。
由于结晶度较高,这种材料的表面刚度和抗划痕特性很好。
PP不存在环境应力开裂问题。
通常,采用加入玻璃纤维、金属添加剂或热塑橡胶的方法对PP进行改性。
PP的流动率MFR范围在1~40。
低MFR的PP材料抗冲击特性较好但延展强度较低。
对于相同MFR的材料,共聚物型的强度比均聚物型的要高。
由于结晶,PP的收缩率相当高,一般为1.8~2.5%。
并且收缩率的方向均匀性比PE-HD等材料要好得多。
加入30%的玻璃添加剂可以使收缩率降到0.7%。
均聚物型和共聚物型的PP材料都具有优良的抗吸湿性、抗酸碱腐蚀性、抗溶解性。
然而,它对芳香烃(如苯)溶剂、氯化烃(四氯化碳)溶剂等没有抵抗力。
PP也不象PE那样在高温下仍具有抗氧化性。
2.2工艺方案分析比较及选择
塑料加工的基本方法大致可以分为七大类:
压塑成形、传递成形、注塑成形、挤出成形、吹塑成形、热成形、铸塑成形。
根据成形加工方法的不同,可以采用多种方法生产制品。
下面对三种主要的加工方案做个分析比较。
2.2.1方案一:
采用压塑成形
压塑成形是塑料在一定型腔中,通过加压且通常需要加热的成形方法。
热固性塑料和热塑性塑料都可以用压塑成形,但主要用于热固性塑料。
压塑成形的主要优点是:
1用的设备和模具比较简单;
2适用于流动性较差的塑料;
3可模压较大和较厚的制品;
4制件收缩率小;
5各向性能比较均匀。
压塑成形的主要缺点是:
6生产周期长、效率低;
7劳动强度大,尤其是移动式模具;
8制品常有较厚的溢边,不能模压要求尺寸精度准确性较高的制品。
2.2.2方案二:
采用传递成形
传递成形是将一定量的塑料压塑粉或料坯放到料室中加热熔融,然后用柱塞(或称压柱)对加料室内塑料熔体加压将料块快速压入已闭合的热型腔内,当熔体充满型腔后,再经适当保压和固化,即可取出制品。
热固性塑料和热塑性塑料都可以采用传递成形方法成形制品。
2.2.3方案三:
采用注射成形
注射成形是将粉状塑料从注射机料斗送入已加热的料筒,经加热熔融后,受柱塞或螺杆的推动,熔融塑料通过料筒前端的喷嘴快速注入闭合塑模中,经冷却(热塑性塑料)定型或加热(热固性塑料)定型后,开启模具取出制品。
几乎所有的热塑性塑料和部分热固性塑料都可以用注射成形。
制品原料为PS塑料,属于热塑性塑料。
采用方案一成形制品时,由于热塑性塑料模压时模具需要交替加热与冷却,生产周期长,效率低,不适合于大批量生产制品。
采用方案二成形制品时由于热塑性塑料的固化时间长,生产周期长,也不适应生产该制品。
与前面两种成形方法相比,注射成形具有成形周期短,能一次成形外形复杂、尺寸精确的制品,生产效率高,易于自动化;注塑机为单机操作,更换原料及模具均很方便,是一种经济高效的成形方法。
由此可见,方案三是成形制品的最好方案。
2.3成型工艺参数的确定
2.3.1成型原理
如图1所示:
图1
2.3.2成型过程
(1)、成型前的准备
对原料外观的检测和工艺性能的测定;物料的预热和干燥;嵌件的预热;料筒的清洗;脱模剂的选用。
(2)、注射成型过程
包括加料、加压、注射、保压、冷却定型、脱模等工序。
(3)、塑料的后处理
退火处理。
2.3.3主要用途
聚丙烯:
无毒、无味,密度小,强度、刚度、硬度耐热性均优于低压聚乙烯,可在100度左右使用.具有良好的电性能和高频绝缘性不受湿度影响,但低温时变脆、不耐磨、易老化.适于制作一般机械零件,耐腐蚀零件和绝缘零件。
常见的酸、碱有机溶剂对它几乎不起作用,可用于食具。
2.3.4成型特点
1.结晶料,湿性小,易发生融体破裂,长期与热金属接触易分解。
2.流动性好,但收缩范围及收缩值大,易发生缩孔.凹痕,变形。
3.冷却速度快,浇注系统及冷却系统应缓慢散热,并注意控制成型温度,料温低温高压时容易取向,模具温度低于50度时,塑件不光滑,易产生熔接不良,流痕,90度以上易发生翘曲变形。
4.塑料壁厚须均匀,避免缺胶,尖角,以防应力集中。
2.3.5聚氯乙烯的注塑模工艺条件
注塑模工艺条件:
注塑机选用:
对注塑机的选用没有特殊要求。
由于PP具有高结晶性。
需采用注射压力较高及可多段控制的电脑注塑机。
锁模力一般按3800t/m2来确定,注射量20%-85%即可。
干燥处理:
如果储存适当则不需要干燥处理。
熔化温度:
PP的熔点为160-175℃,分解温度为350℃,但在注射加工时温度设定不能超过275℃。
熔融段温度最好在240℃。
模具温度:
模具温度50-90℃,对于尺寸要求较高的用高模温。
型芯温度比型腔温度低5℃以上。
注射压力:
采用较高注射压力(1500-1800bar)和保压压力(约为注射压力的80%)。
大概在全行程的95%时转保压,用较长的保压时间。
注射速度:
为减少内应力及变形,应选择高速注射,但有些等级的PP和模具不适用(出现气泡、气纹)。
如刻有花纹的表面出现由浇口扩散的明暗相间条纹,则要用低速注射和较高模温。
流道和浇口:
流道直径4-7mm,针形浇口长度1-1.5mm,直径可小至0.7mm。
边形浇口长度越短越好,约为0.7mm,深度为壁厚的一半,宽度为壁厚的两倍,并随模腔内的熔流长度逐肯增加。
模具必须有良好的排气性,排气孔深0.025mm-0.038mm,厚1.5mm,要避免收缩痕,就要用大而圆的注口及圆形流道,加强筋的厚度要小(例如是壁厚的50-60%)。
均聚PP制造的产品,厚度不能超过3mm,否则会有气泡(厚壁制品只能用共聚PP)。
熔胶背压:
可用5bar熔胶背压,色粉料的背压可适当调高。
制品的后处理:
为防止后结晶产生的收缩变形,制品一般需经热水浸泡处理。
2.4塑件结构工艺性
塑料密封头见图2,整体尺寸70×53×36mm,表面精度要求不高,尺寸精度要求不高。
根据塑件的用途,工作环境,对塑件图上制品形状,尺寸精度,表面粗糙度等要求进行综合性分析,可知该塑件的工艺性较好,比较容易注射成型。
技术要求
1.未注圆角半径R1。
2.塑料未注公差按MT6级。
3.按大批量生产设计模具。
4.塑件材料PP。
图2.塑件图
2.5塑件工艺性分析
1、该塑件尺寸不大且要求塑件表面精度等级较高,无凹痕。
采用点浇口单分型面型腔注射模可以保证其表面精度。
2、注塑成型制品的生产纲领属大批量生产,对于大批量生产,由于模具价格在整个生产费中所占的比较小,生产率和模具寿命比较突出,因此可考虑使用自动化程度较高的复杂模具结构,以及对成型零部件采用较好的模具材料。
3、大批量,选择一模一件。
第三章设备的初步选择
3.1初选设备
通常影响射出机选择的重要因素包括模具、产品、塑料、成型要求等,因此,在进行选择前必须先收集或具备下列资讯:
模具尺寸(宽度、高度、厚度)、重量、特殊设计等;
使用塑料的种类及数量(单一原料或多种塑料);
注塑成品的外观尺寸(长、宽、高、厚度)、重量等;
成型要求,如品质条件、生产速度等。
在获得以上资讯后,即可按照下列步骤来选择合适的射出机:
3.1.1由产品及塑料决定机种及系列
由于射出机有非常多的种类,因此一开始要先正确判断此产品应由哪一种注塑机,或是哪一个系列来生产,例如是一般热塑性塑胶或电木原料或PET原料等,是单色、双色、多色、夹层或混色等。
此外,某些产品需要高稳定(闭回路)、高精密、超高射速、高射压或快速生产(多回路)等条件,也必须选择合适的系列来生产。
3.1.2由模具尺寸判定模具大小是否合适
模具的宽度及高度需小于或至少有一边小于大柱内距;
模具的宽度及高度最好在模盘尺寸范围内;
模具的厚度需介于注塑机的模厚之间;
模具的宽度及高度需符合该注塑机建议的最小模具尺寸,太小也不行。
3.1.3由模具及成品判定“开模行程”及“托模行程”是否利于取件
开模行程至少需大于成品在开关模方向的高度的两倍以上,且需含竖浇道的长度;托模行程需足够将成品顶出。
3.1.4由产品及塑料决定“锁模力”吨数
当原料以高压注入模穴内时会产生一个撑模的力量,因此注塑机的锁模单元必须提供足够的“锁模力”使模具不至于被撑开。
锁模力需求的计算如下:
由成品外观尺寸求出成品在开关模方向的投影面积;
撑模力量=成品在开模方向投影面积(cm²)×模穴数×模内压力(kg/cm²);
模内压力随原料而不同,一般原料取350~400kg/cm²;
机器锁模力需大于撑模力量,且为了保险起见,机器锁模力通常需大于撑模力量的1.17倍以上。
本塑料件注射量:
本模具使用一模一件,故塑件总体积为
(50×40-2×3.14×4×4)×3+(16+50)/2×60×3+(40+30)/2×52×3+3.14×(8×8-5×5)×30=20772mm³。
考虑浇流道的废料,所需的注射量为20772/70%=29674mm³=29.674cm³。
初步计算撑模力:
P*A/1000
p:
模具内压力(kgf)A:
产品投影面积(cm²)
成品在开关模方向的投影面积(cm²)×模穴数×模内压力(kg/cm²);
19.8cm²×2×380kg/cm²=15048kg
撑模力为:
150480×10=150.48KN
根据计算及原材料的注塑成型工艺参数,初选注射机型号,选择的注塑机的注塑压力必须大于成型制品所需的注射压力,注射机额定注射量必须大于塑件注射量,锁模力必须大于撑模力,综上初选型号为XS—Z—60,其各项参数如图表3所示:
表2.XS—Z—60型注射机参数
型号
SZ60/450
最大注射容量
78cm³
注射压力
122Mpa
锁模力
500kN
最大注射面积
130cm²
最大模具厚度
300cm³
最小模具厚度
100mm
喷嘴圆弧半径
SR20mm
喷嘴孔半径
R2mm
中心顶出孔半径
R25mm
模板开模行程
220mm
拉杆空间(长
宽)
300
190
螺杆直径
38mm
模板尺寸
330
440
机器外形尺寸
3160
850
1460
图3
第四章确定模具结构
4.1分型面及型腔的确定
4.1.1分型面的确定
如何确定分型面,需要考虑的因素比较复杂。
由于分型面受到塑件在模具中的成型位置、浇注系统设计、塑件的结构工艺性及精度、嵌件位置形状以及推出方法、模具的制造、排气、操作工艺等多种因素的影响,因此在选择分型面时应综合分析比较,从几种方案中优选出较为合理的方案。
选择分型面时一般应遵循以下几项原则:
(1)保证塑料制品能够脱模
这是一个首要原则,因为我们设置分型面的目的,就是为了能够顺利从型腔中脱出制品。
根据这个原则,分型面应首选在塑料制品最大的轮廓线上,最好在一个平面上,而且此平面与开模方向垂直。
分型的整个廓形应呈缩小趋势,不应有影响脱模的凹凸形状,以免影响脱模。
(2)使型腔深度最浅
模具型腔深度的大小对模具结构与制造有如下三方面的影响:
1)目前模具型腔的加工多采用电火花成型加工,型腔越深加工时间越长,影响模具生产周期,同时增加生产成本。
2)模具型腔深度影响着模具的厚度。
型腔越深,动、定模越厚。
一方面加工比较困难;另一方面各种注射机对模具的最大厚度都有一定的限制,故型腔深度不宜过大。
3)型腔深度越深,在相同起模斜度时,同一尺寸上下两端实际尺寸差值越大。
若要控制规定的尺寸公差,就要减小脱模斜度,而导致塑件脱模困难。
因此在选择分型面时应尽可能使型腔深度最浅。
(3)使塑件外形美观,容易清理
尽管塑料模具配合非常精密,但塑件脱模后,在分型面的位置都会留有一圈毛边,我们称之为飞边。
即使这些毛边脱模后立即割除,但仍会在塑件上留下痕迹,影响塑件外观,故分型面应避免设在塑件光滑表面上。
(4)尽量避免侧向抽芯
塑料注射模具,应尽可能避免采用侧向抽芯,因为侧向抽芯模具结构复杂,并且直接影响塑件尺寸、配合的精度,且耗时耗财,制造成本显著增加,故在万不得己的情况下才能使用.
(5)使分型面容易加工
分型面精度是整个模具精度的重要部分,力求平面度和动、定模配合面的平行度在公差范围内。
因此,分型面应是平面且与脱模方向垂直,从而使加工精度得到保证。
如选择分型面是斜面或曲面,加工的难度增大,并且精度得不到保证,易造成溢料飞边现象。
(6)使侧向抽芯尽量短
抽芯越短,斜抽移动的距离越短,一方面能减少动、定模的厚度,减少塑件尺寸误差;另一方面有利于脱模,保证塑件制品精度。
(7)有利于排气
对中、小型塑件因型腔较小,空气量不多,可借助分型面的缝隙排气。
因此,选择分型面