复合模课程设计冲压课程设计说明书.docx
《复合模课程设计冲压课程设计说明书.docx》由会员分享,可在线阅读,更多相关《复合模课程设计冲压课程设计说明书.docx(25页珍藏版)》请在冰点文库上搜索。
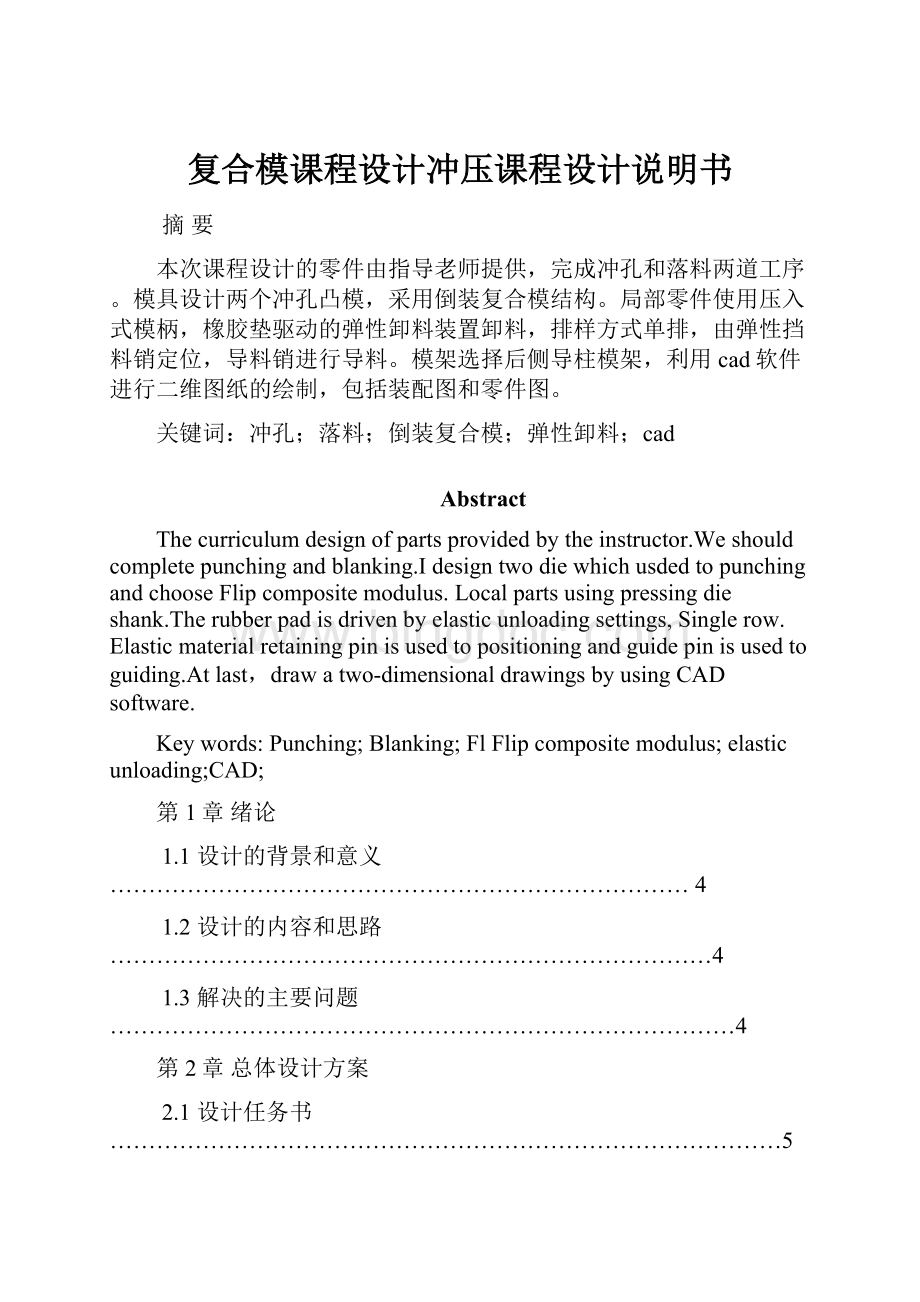
复合模课程设计冲压课程设计说明书
摘要
本次课程设计的零件由指导老师提供,完成冲孔和落料两道工序。
模具设计两个冲孔凸模,采用倒装复合模结构。
局部零件使用压入式模柄,橡胶垫驱动的弹性卸料装置卸料,排样方式单排,由弹性挡料销定位,导料销进行导料。
模架选择后侧导柱模架,利用cad软件进行二维图纸的绘制,包括装配图和零件图。
关键词:
冲孔;落料;倒装复合模;弹性卸料;cad
Abstract
Thecurriculumdesignofpartsprovidedbytheinstructor.Weshouldcompletepunchingandblanking.IdesigntwodiewhichusdedtopunchingandchooseFlipcompositemodulus.Localpartsusingpressingdieshank.Therubberpadisdrivenbyelasticunloadingsettings,Singlerow.Elasticmaterialretainingpinisusedtopositioningandguidepinisusedtoguiding.Atlast,drawatwo-dimensionaldrawingsbyusingCADsoftware.
Keywords:
Punching;Blanking;FlFlipcompositemodulus;elasticunloading;CAD;
第1章绪论
1.1设计的背景和意义…………………………………………………………………4
1.2设计的内容和思路……………………………………………………………………4
1.3解决的主要问题………………………………………………………………………4
第2章总体设计方案
2.1设计任务书……………………………………………………………………………5
2.2冲压工艺分析…………………………………………………………………………5
2.3冲裁方案确定…………………………………………………………………………6
2.4排样……………………………………………………………………………………7
2.5计算冲压力……………………………………………………………………………8
2.6确定模具压力中心……………………………………………………………………9
2.7计算凸凹模刃口尺寸…………………………………………………………………9
第3章工作零件设计
3.1凹模结构设计…………………………………………………………………………12
3.2凸凹结构设计…………………………………………………………………………12
3.3凸模结构设计…………………………………………………………………………13
第4章其他零件设计………………………………………………………………………13
第5章总装配图草图
5.1装配草图………………………………………………………………………………16
5.2装配技术要求…………………………………………………………………………16
总结………………………………………………………………………………………………18
参考文献…………………………………………………………………………………………19
致谢………………………………………………………………………………………………20
第1章绪论
在室温下,利用安装在压力机上的模具对被冲材料施加一定的压力,使之产生分离和塑性变形,从而获得所需要形状和尺寸的零件(也称制件)的一种加工方法。
因为通常使用的材料为板料,故也常称为板料冲压。
在冲压加工中,将材料加工成零件(或半成品)的一种特殊工艺装备,称为冲压模具(俗称冲模),加工对象主要是金属板材,加工利用了板材冲压成形性能(主要是塑性),加工设备主要是压力机,加工工艺装备冲压模具。
冲压生产的三要素:
合理的冲压工艺、先进的模具、高效的冲压设备
1.1设计的背景和意义
21世纪的今天,中国凭借丰富且廉价的人力资源、庞大的市场及其它许多有利条件,已成为承接工业发达国家模具业转移的良好目的地。
随着国际交往的日益增多和外资在中国模具行业的投入日渐增加,中国模具已经与世界模具密不可分,中国模具在世界模具中的地位和影响越来越重要。
在这个大背景下,机械专业大学生应该在大学生活中就了解学习到各类模具的计算分析绘制。
1.2设计的内容和思路
本课题要求对给定零件进行落料、冲孔复合冲压模设计,通过对零件进行详细的工艺分析确定零件的冲压工艺方案并制定部分零件的制造工艺,如:
凸模、凹模、凸凹模、凸模固定板、垫板、凹模固定板、卸料板、导尺、挡料销、导正销等。
通过该课题能够让学生掌握中等复杂程度零件冲压模具设计与制造的一般方法,对零件冲压工艺方案的制定、工艺计算及模具设计有了更深层次的认识,并学会对模具设计资料的检索与整合以及对已有资料的充分合理的使用,该实践性课题是对学生理论学习水平的实践和检验,可对以后从事类似的工作有一定的指导性与实践性意义。
1.3需要解决的主要问题
分为以下几点:
1)熟悉整个模具设计过程,包括排样,压力中心计算,刃口尺寸计算等等。
2)各个零部件的具体尺寸选用。
3)CAD绘制二维零件图纸。
4)CAD绘制二维装配图纸。
5)对绘制的图形各部分进行校核。
第2章总体设计方案
2.1设计任务书
零件:
图2-1设计零件图
冲孔直径9mm,半圆半径30mm
材料:
Q235
料厚:
1mm
精度:
IT8
2.2冲压工艺分析
1)、材料零件的材料为Q235普通碳素钢,具有良好的冲压性能,适合冲裁。
2)、结构该工件形状简单,对称,由圆和直线组成,查手册得孔边距,孔心距,孔径均满足复合冲裁要求。
3)、精度零件外形:
IT11,孔心距:
IT11,零件内形:
IT10均满足冲裁加工工艺精度要求。
(查取表2-1公差等级表获得零件形状公差)
4)、结论可以冲裁。
参考文献【1】
表2-1基准件标准公差数值
基本尺寸
/mm
公差等级
IT1
IT2
IT3
IT4
IT5
IT6
IT7
IT8
IT9
IT10
IT11
IT12
IT13
IT14
IT15
IT16
≤3
>3~6
>6~10
>10~18
>18~30
>30~50
>50~80
>80~120
>120~180
>180~250
>250~315
>315~400
>400~500
0.8
1
1
1.2
1.5
1.5
2
2.5
35
4.5
6
7
8
1.2
1.5
1.5
2
2.5
2.5
3
4
5
7
8
9
10
2
2.5
2.5
3
4
4
5
6
8
10
12
13
15
3
4
4
5
6
7
8
10
12
14
16
18
20
4
5
6
8
9
11
13
15
18
20
23
25
127
6
8
9
11
13
16
19
22
25
29
32
36
40
10
12
15
18
21
25
30
35
40
46
52
57
63
14
18
22
27
33
39
46
54
63
72
81
89
97
25
30
36
43
52
62
74
87
100
115
130
140
155
40
48
58
70
84
100
120
140
160
185
210
230
250
60
75
90
110
130
160
190
220
250
290
320
360
400
100
120
150
180
210
250
300
350
400
460
520
570
630
140
180
220
270
330
390
460
540
630
720
810
890
970
250
300
360
430
520
620
740
870
1000
1150
1300
1400
1550
400
480
580
700
940
1000
1200
1400
1600
1850
2100
2300
2500
600
750
900
1100
1300
1600
1900
2200
2500
2900
3200
3600
4000
2.3冲裁工艺方案确定
该零件包括落料、冲孔两个基本工序,可以采用以下三种工艺方案:
方案①:
先落料、再冲孔。
采用单工序模生产。
方案②:
落料—冲孔复合冲压。
采用复合模生产。
方案③:
冲孔—落料级进冲压。
采用级进模生产。
方案①模具结构简单,但需要两道工序、两套模具才能完成零件的加工,生产效率较低,难以满足零件大批量生产的需求。
方案②只需要一套模具,冲压件的形位精度和尺寸易于保证,且生产效率也高。
尽管模具结构较方案一复杂,但由于零件的几何形状简单对称,模具制造并不困难。
方案③也只需要一套模具,生产效率高,但零件的冲压精度不易保证。
通过以上三种方案的分析比较,对该冲压件生产以采用放案②为佳。
综合考虑零件厚度等条件最后确定选用倒装复合模。
2.4排样
表2-2板料冲裁时的合理搭边值
板料
厚度
手送料
自动送料
圆形
非圆形
往复送料
a
a1
a
a1
a
a1
a
a1
≤1
1.5
1.5
2
1.5
3
2
2.5
2
1-2
2
1.5
2.5
2
3.5
2.5
3
2
2-3
2.5
2
3
2.5
4
3.5
3.5
3
3-4
3
2.5
3.5
3
5
4
4
3
4-5
4
3
5
4
6
5
5
4
5-6
5
4
6
5
7
6
6
5
6-8
6
5
7
6
8
7
7
6
>8
7
6
8
7
9
8
8
7
表2-3条料宽度偏差
剪切方式
条料宽度
材料厚度
≤0.5
0.5-1
1-2
2-3
3-4
4-5
龙门剪
板机剪切
≤50
-0.4
-0.6
-1.0
-1.2
-1.4
-1.6
50-120
-0.7
-0.7
-1.2
-1.6
-1.8
-2.0
120-180
-1.0
-1.5
-1.7
-2.0
-2.2
-2.5
滚剪切割
≤20
-0.05
-0.08
-0.10
-
-
-
20-30
-0.08
-0.10
-0.15
-
-
-
30-50
-0.10
-0.15
-0.20
-
-
-
方案A
图2-2排样方案A图
1)搭边:
查表2-2得搭边值,a=2mm,a1=1.5mm
2)步距:
h=30mm+1.5mm=31.5mm
3)条料宽度:
B=98+2×2=102mm
4)条料利用率:
一个步距内放一个制件,故A1=2607.678mm2
方案B
图2-3排样方案B图
1)搭边:
查表2-2得搭边值,a=2,a1=1.5
2)步距:
h=98+1.5=99.5mm
3)条料宽度:
由表2-3查得条料宽度公差取0.7,则
B=30+2×2=34mm
4)条料利用率:
一个步距内放一个制件,故A1=2607.678mm2
综合考虑本人选择方案A排样
2.5计算冲压力
表2-4卸料力推件力顶件力系数
材料
厚度mm
K卸
K推
K顶
钢
《0.01
0.065-0.075
0.1
0.14
0.1-0.5
0.045-0.055
0.063
0.08
0.5-2.5
0,04-0,05
0,.055
0.06
2.5-6.5
0.03-0.04
0.045
0,05
6.5
0.02-0.03
0.025
0.03
铝合金铝
0.025-0.08
0.03-0.07
0.03-0.07
紫铜黄铜
0.02-0.06
0.03-0.09
0.03-0.09
表2-4卸料力推件力顶件力系数
1)落料力
该模具采用弹性卸料和下出料方式。
落料力:
零件外轮廓线长度为L=262.2mm,则:
F1=Ltσb=262.2×1×450N=117.99kN
冲孔力:
内孔轮廓线长度L=56.55mm则:
F2=Ltσb=56.55×1×450N=25.44kN
落料时的卸料力:
由资料查的K卸=0.04,则:
F卸=K卸F1=0.05×117.99kN≈4.72kN
推件力取凹模刃口直壁高度h=6,n=h/t=6/1=6。
由资料查的推件力系数:
K推=0.055,则:
F推=nK推F2=6×0.055×25.44kN≈8.40kN
选择冲床时的总冲压力为:
F总=F冲+F推=117.99kN+25.44kN+4.72kN+8.40kN=156.55kN
2.6确定模具压力中心
如图2-4所示:
因为该零件左右对称,所以x0=0,利用CAD查询命令可以查出该零件的重心位置为:
y0=16.37mm
图2-4工件压力中心坐标图
2.7计算凸模凹模刃口尺寸
表2-5冲裁模初始双面间隙值z
表2-6磨损系数x
板料厚度mm
制件公差mm
≤1
≤0.16
0.17-0.35
≥0.36
<0.16
≥0.16
1-2
≤0.20
0.21-0.41
≥0.42
<0.20
≥0.20
2-4
≤0.24
0.25-0.49
≥0.50
<0.24
≥0.24
≥4
≤0.30
0.31-0.59
≥0.60
<0.30
≥0.30
磨损系数
非圆形x值
圆形x值
1.0
0.75
0.5
0.75
0.5
表2-7规则形状冲裁模凸凹模制造偏差
基本尺寸
δp
δd
基本尺寸
δp
δd
≤18
-0.020
+0.020
180-260
-0.030
+0.045
18-30
-0.020
+0.025
260-360
-0.035
+0.050
30-80
-0.020
+0.030
360-500
-0.040
+0.060
80-120
-0.025
+0.035
>500
-0.045
+0.070
120-180
-0.030
+0.040
由表2-5查得间隙值Zmin=0.1mm,Zmax=0.14mm
1)冲孔
采用配合法加工方法,以凸模为基准件,凸模磨损后尺寸减小,刃口尺寸减小故外轮廓尺寸属于B类尺寸。
B9=
mm=
mm,
2)落料
由于外形轮廓较复杂,采用配合法加工方法,以凹模为基准件时,凹模磨损后刃口尺寸都增大,因此外轮廓除内凹圆弧部分属于B类尺寸,其他尺寸均为A类尺寸,孔中心距及孔边距为C类尺寸。
由表2-6得当△≥0.42时,x=0.5,0.21≤△≤0.41时,x=0.75,当x≤0.20时,x=1
零件外形基本尺寸如图2-5所示
图2-5零件外形基本尺寸图
则:
A98=
mm=
A30=
=
mm
A26.2=
mm
B30=
mm
C48=48±0.039/8mm=48±0.004875mm
C15=15±0.027/8mm=15±0.003375mm
第3章工作零件设计
3.1凹模结构设计
表3-1凹模壁厚系数K
b/mm
材料厚度t/mm
≤1
1-3
3-6
≤50
0.30-0.40
0.35-0.50
0.45-0.60
50-100
0.20-0.30
0.22-0.35
0.30-0.45
100-200
0.15-0.20
0.18-0.22
0.22-0.30
>200
0.10-0.15
0.12-0.18
0.15-0.22
落料凹模形状尺寸如图3-1所示
图3-1凹模形状尺寸图
1)厚度
查表3-1得凹模厚度系数K=0.3,则凹模厚度H=Kb=0.3x98≈30mm
2)凹模壁厚c=(1.5~2)H=45mm
3)凹模宽度B=120mm
4)凹模长度B=188mm
3.2凸凹模结构设计
凸凹模形状尺寸如图3-2
图3-2凸凹模形状尺寸
1)凸凹模高度L=h1+h2+h
h1为凸凹模固定板厚度,取0.6-0.8个凹模厚度即取16mm
h2为卸料版厚度取14mm
h为橡胶垫高度取22mm
2)凸凹模下漏料孔直径选Φ12,冲孔废料由冲孔凸模冲入凹模洞口中,积累到一定数量,由下模漏料孔排出,不必清除废料,操作方便,应用很广,但工件表面平直度较差,凸凹模承受的张力较大,因此凸凹模的壁厚应严格控制,以免强度不足
3.3凸模结构设计
冲孔凸模形状尺寸如图3-3
图3-3冲孔凸模形状尺寸
1)凸模长度
凸模长度L=h1+h2+t
h1为凸模固定板厚度选取16mm
h2为落料凹模厚度选取30mm
t料厚1mm
所以冲孔凸模长度选取47mm
第4章其他零件设计
参考文献【2】选择各部分零件
4.1送料定位机构设计
采用活动挡料销定位,安装在橡胶垫和活动卸料板之间。
工作时可随凹模下行而压入孔内,工作很方便.
4.2卸料机构设计
1)采用弹性卸料板。
因为是倒装式复合模,所以卸料板安装在下模。
2)采用打料装置将工件从落料凹模中推下,罗在模具工作表面上。
3)下模座上采用漏料孔排出。
冲孔废料在下模的凸凹模内积聚到一定数量,便从下模座的漏料孔中排出。
4.3出件机构设计
因为采用倒装复合膜,所以用上出件方式。
4.4橡胶垫
为保证橡胶垫不过早失去弹性而破坏,其允许的最大压缩两不得超过摘要高度的45%,一般取自由高度的35%~45%。
橡胶垫的预压缩量一般取自由高度的10%~15%。
橡胶垫产生的力
式中
—压力;
—橡胶垫横截面积;
—与橡胶垫压缩量有关的单位压力,如表4-1所示。
表4-1橡胶压缩量和单位压力
橡胶压缩量(%)
单位压力(MPa)
橡胶压缩量(%)
单位压力(MPa)
10
15
20
0.26
0.50
0.70
25
30
35
1.03
1.52
2.10
取A=160x160-60x90-3.14x25x25/2=19218.75,则
P=p卸/A=5500/19218.75=0.28MPa
取压缩量为25%,预压缩量为15%,工作行程
mm。
所以橡胶垫的自由高度为
h自由=s/(0.20-0.10),取20mm
预压缩量取为
2m。
则H=22mm
4.5凸凹模固定板
凸凹模固定板形状与凹模板一致,厚度为16mm
4.6凸模固定板
凸模固定板将凸模固定在模座上,其平面轮廓尺寸与凹模板外形尺寸相同,但还应考虑紧固螺钉及销钉的位置。
固定板的凸模安装孔与凸模采用过渡配合H7/m6、H7/n6,压装后将凸模端面与固定板一起磨平。
凸模固定板为圆形,厚度一般取凹模厚度的0.6~0.8倍,材料为Q235,厚度选16mm
4.7垫板
压入式模柄与凸模固定板中间需加一块垫板厚度选取8mm
4.8模架
参考文献[3]选用后侧导柱式模架
4.9模座
参考文献[3]选用如下图模座,
图4-1上模座图4-2下模座
上模座:
L×B×H=200×125×40
下模座:
L×B×H=200×125×50
4.10压力机选用
选择压力机JC23-25
公称压力250KN
模具闭合高度270mm
压力机工作台尺寸370x560,一般工作台面尺寸每边应大于模具下模座尺寸50~70mm,所以该压力机可以选用。
4.11模柄
参考文献[3]选用直径d=40mm,D=79mm、材料为Q235的A型凸缘式模柄,模柄B40×79JB/T7646.3—1994
4.12导柱导套
选用A型滑动导柱导套
导柱:
25x100
导套25x100x38
第5章总装配图草图
1.装配草图
1.凹模2.凸模3.推杆4.凸模固定板导料销5.垫板6.上模座7.导套销钉8.导柱9.螺钉10.模柄销钉11.推件块12.板料13.导料销14.凸凹模15.橡胶16.凸凹模固定板17.卸料螺钉卸料版18.下模座19.挡料销20.紧定螺钉
2.装配技术条件要求
1.装配时应保证凸,凹模之间的间隙均匀一致,配合间隙符合设计要求,不允许采用使凸,凹模变形的方法来修正间隙。
2.推料,卸料机构必须灵活,卸料板或推件器在冲模开启状态时,一般应突出凸凹模表面0.5~1.0mm。
3.当采用机械方法联接硬质合金零件时,连接表面的表面粗糙度参数值为0.8um。
4.各接合面保证密合。
5.落料,冲孔的凹模刃口高度,按设计要求制造,其漏料孔应保证畅通,一般应比刃口大0.2~2mm。
6.冲模所有活动部分的移动应平稳灵活,无滞止现象,滑块,楔块在固定滑动面上移动时,其最小接触面积不少于其面积的四分之三。
7.各紧固用的螺钉,销钉不得松动,并保证螺钉和销钉的端面不突出上下模座平面。
8.各卸料螺钉沉孔深度应保持一致。
9.各卸料螺钉,顶杆的长度应保持一致。
10.凸模的垂直度必须在凸凹模间隙值的允许范围内。
11.冲模的装配必须复合模具装配图,明细表及技术条件的规定。
12.凸模,凸凹模等与凸模固定板的配合一般按H7/m6,H7/N6保证工作稳定可靠。
13.在保证可靠的使用前提下,凸模,凹模,导柱,导套等零件的固定可采用性能良好并稳定的粘结材料浇注固定。
总结
本课题设计是对制件采用倒装复合方式冲裁。
对本课题设计进行了深入的研究和分析、总结。
本设计的工作原理是上模部分依靠模柄固定在冲床上,下模部分用压力板安装在冲床的工作台上;工作时,条料沿导料板送至挡料销处定位,开动压力机,上模随滑块向下运动,具有锋利刃口的冲孔凸模与凹模一起穿过条料使冲件和废料与条料分离而完成冲裁工作。
通过分析模具的结构组成及工作原理知道本课题设计的要点:
①工作零件是进行冲裁工作的零件,它是冲裁模的主要零件,比如凸模与凹模就是工作零件,此零件要求的刚度和强度要求很高,设计时要考虑其材料的问题,以及零件与固定零件的间隙要适当而且要分布均匀,这是保证冲裁件质量的关键。
②基础零件是固定凸模