年产1万吨异丙苯反应及烃化液的工艺设计资料.docx
《年产1万吨异丙苯反应及烃化液的工艺设计资料.docx》由会员分享,可在线阅读,更多相关《年产1万吨异丙苯反应及烃化液的工艺设计资料.docx(49页珍藏版)》请在冰点文库上搜索。
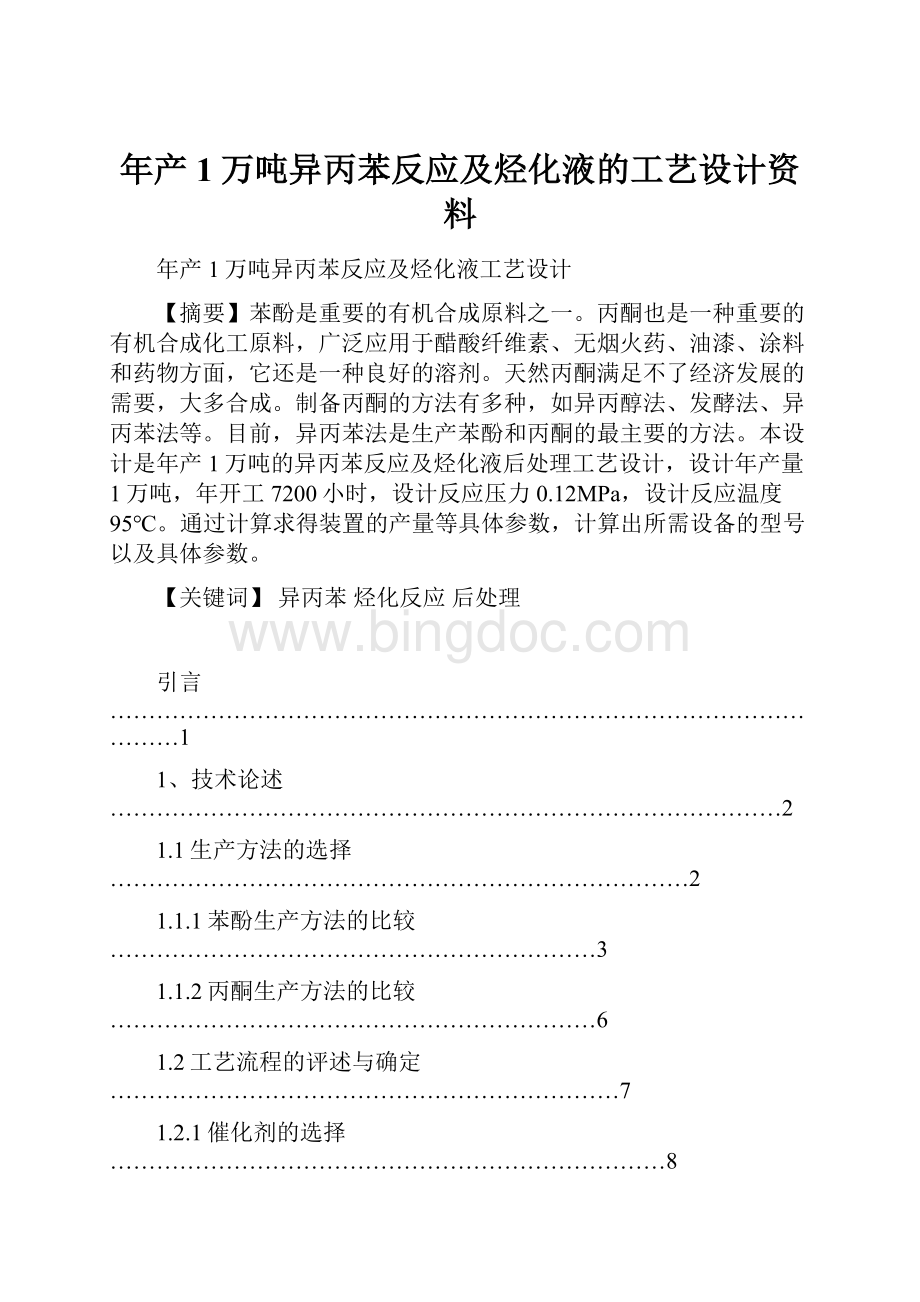
年产1万吨异丙苯反应及烃化液的工艺设计资料
年产1万吨异丙苯反应及烃化液工艺设计
【摘要】苯酚是重要的有机合成原料之一。
丙酮也是一种重要的有机合成化工原料,广泛应用于醋酸纤维素、无烟火药、油漆、涂料和药物方面,它还是一种良好的溶剂。
天然丙酮满足不了经济发展的需要,大多合成。
制备丙酮的方法有多种,如异丙醇法、发酵法、异丙苯法等。
目前,异丙苯法是生产苯酚和丙酮的最主要的方法。
本设计是年产1万吨的异丙苯反应及烃化液后处理工艺设计,设计年产量1万吨,年开工7200小时,设计反应压力0.12MPa,设计反应温度95℃。
通过计算求得装置的产量等具体参数,计算出所需设备的型号以及具体参数。
【关键词】异丙苯烃化反应后处理
引言………………………………………………………………………………………1
1、技术论述……………………………………………………………………………2
1.1生产方法的选择…………………………………………………………………2
1.1.1苯酚生产方法的比较………………………………………………………3
1.1.2丙酮生产方法的比较………………………………………………………6
1.2工艺流程的评述与确定…………………………………………………………7
1.2.1催化剂的选择………………………………………………………………8
1.2.2烃化反应器的选择…………………………………………………………8
1.2.3烃化反应产物的后处理……………………………………………………9
1.2.4三废处理……………………………………………………………………10
1.3工艺条件的论述与确定…………………………………………………………11
1.3.1配料比………………………………………………………………………11
1.3.2反应压力……………………………………………………………………11
1.3.3反应温度……………………………………………………………………11
1.4工艺流程叙述……………………………………………………………………12
1.4.1烃化反应…………………………………………………………………12
1.4.2尾气处理……………………………………………………………………12
1.4.3烃化液的处理………………………………………………………………12
1.5安全环保措………………………………………………………………………13
1.5.1安全措施…………………………………………………………………13
1.5.2三废处理……………………………………………………………………13
2、工艺设计计算………………………………………………………………………14
2.1物料衡算…………………………………………………………………………15
2.1.1烃化塔物料衡算……………………………………………………………15
2.1.2烃化塔气液分离计算………………………………………………………19
2.1.3第一尾气冷凝器的物料衡算………………………………………………22
2.2热量衡算…………………………………………………………………………25
2.2.1烃化塔的热量衡算…………………………………………………………26
2.2.2第一尾气冷凝器热量衡算…………………………………………………28
2.2.3烃化液冷却器热量衡算……………………………………………………29
2.3设备工艺设计计算…………………………………………………………………30
2.3.1烃化反应器工艺计算…………………………………………………………30
2.3.1.1塔径D……………………………………………………………………30
2.3.1.2塔高H…………………………………………………………………30
2.3.2反应器换热器计算……………………………………………………………31
2.3.3烃化液冷却器计算……………………………………………………………31
2.3.4烃化塔第一尾气冷凝器计……………………………………………………32
2.3.5沉降罐估算……………………………………………………………………32
2.3.6事故放料罐选…………………………………………………………………33
2.3.7烃化反应器接管计算…………………………………………………………33
2.3.8泵的选择………………………………………………………………………34
主要参考文献…………………………………………………………………………36
致谢……………………………………………………………………………………37
工艺流程图……………………………………………………………………………38
引言
苯酚是重要的有机合成原料之一,广泛应用于合成塑料(如酚醛树脂)、纤维(如锦纶、聚酰胺纤维)医药、农药和燃料中间体等工业生产中。
随着有机合成工业,特别是塑料和合成纤维工业的迅速发展,苯酚的需求量逐年增加。
苯酚的生产最早起源于从煤焦油中提取天然苯酚,所以苯酚又叫石碳酸。
这是由朗格在1834年发现的。
在第一次世界大战前,生产苯酚主要采用这种方法。
后来由于酚醛树脂用途日益发展,苯酚的需求量猛增,天然苯酚远远不能满足需求,合成苯酚应运而生。
丙酮也是一种重要的有机合成化工原料,广泛应用于醋酸纤维素、无烟火药、油漆、涂料和药物方面,它还是一种良好的溶剂。
天然丙酮满足不了经济发展的需要,大多合成。
制备丙酮的方法有多种,如异丙醇法、发酵法、异丙苯法等。
在异丙苯法问世之前,主要用发酵和异丙醇法生产。
目前,异丙苯法是生产苯酚和丙酮的最主要的方法。
异丙苯法生产苯酚和丙酮的工艺路线最早由前苏联实现工业化,于1949年建成了第一座异丙苯法合成苯酚丙酮的工厂。
1954年开始,美国市场出现了异丙苯法合成的苯酚。
发展到20世纪60年代中期,异丙苯法合成苯酚量已经占世界苯酚总产量的50%,目前已占90%以上。
我国对异丙苯法合成苯酚丙酮的研究是从1958年开始的,并在1970年实现了万吨规模的工业生产。
经过十几年来我国广大科技人员的努力,已基本掌握了异丙苯法生产苯酚丙酮的技术,形成了具有自己特色的工艺流程。
通过研究计算年产1万吨苯酚丙酮装置,采用催化剂主要是金属卤化物〔AlCl3〕,同时采用一个反应器的流程。
烃化反应中的AlCl3用量选用3%。
烃化液的组成大约为:
异丙苯30%、苯60%、其他10%。
本设计采用压力:
0.12MPa。
本设计确定反应温度控制在95℃。
气体空塔速度:
0.15m∕s,设备生产强度:
200Kg·h-1·m-3,丙烯转化率:
96%(mol),苯转化率:
35%(mol)。
主、副反应分配率:
异丙苯(主反应)95%(mol),二异丙苯(副反应)3.5%(mol),三异丙苯(副反应)1.5%(mol)。
通过计算本设计完全满足了生产要求,并符合安全环保标准。
1、技术论述
1.1生产方法的选择
1.1.1苯酚生产方法的比较
(1)磺化法
磺化法是最早合成苯酚的方法,1923年美国孟山都公司研制投产。
具体方法是将苯与浓硫酸发生磺化反应生成苯磺酸,再与亚硫酸钠反应生成苯磺酸钠,然后用氢氧化钠碱熔生成苯酚钠,最后经酸化生成苯酚、反应方程式如下;
磺化
+H2SO4+H2O
2+Na2SO32+SO2+H2O
320~350℃
+2NaOH(S)+Na2SO3+H2O
碱熔
酸化
2+SO2+H2O2+Na2SO3
此种方法设备简单,产率较高,适合于中小规模的生产。
但需要消耗大量的浓硫酸和烧碱,而且对设备的腐蚀相当严重,且副产大量的亚硫酸钠,利用价值很小,且造成很大的污染。
因此,这种方法在国际上已经淘汰,不再发展。
(2)氯化法
1924年,美国道化学公司研制成功了用氯苯水解法合成苯酚。
方法是苯被氯气氯化生成氯苯,氯苯再在高温高压和催化剂的作用下被稀碱液水解得苯酚钠,苯酚钠再经酸化既得苯酚。
反应方程式如下:
+Cl2+HCl
水解
+2NaOH+NaCl+H2O
酸化
+HCl+NaCl
此种方法需要大量的氯,这些氯主要来源于电解食盐水,因此耗能较大:
反应中有HCl存在,腐蚀相当严重:
水解条件相当苛刻,温度要达到400℃,压强高达30Mpa,能耗大。
虽然在污染问题上得到了一定的改善,取代了磺化法,但仍旧没有被广泛采用。
(3)拉西法(氧氯化法)
这种方法首先由德国的拉西研究的,故称拉西法。
它是对氯化法的改良。
具体方法是将盐酸、空气和苯的混合物通过固体氯化铜催化剂进行氧氯化反应,生成氯苯,再用过热水蒸气将氯苯水解成苯酚和盐酸。
在第二个反应中生成的盐酸,可供第一个反应使用。
反应方程式如下:
CuCl2(S)
+HCl+1/2O2+H2O
水解
+H2O(g)+HCl
此种方法操作条件温和,但HCl有水存在时腐蚀性特别严重,温度大于150℃时,用搪瓷材料防腐已经不够了,维修费用较高,所以应用不广泛。
(4)环己烷法
美国科学设计公司采用苯和氢生成环己烷,环己烷在催化剂的作用下被空气氧化成环己醇,环己醇再脱氢生成苯酚。
反应方程式如下:
Ni
+3H2
催化剂
+1/2O2
Ni
+3H2
此法所需的氢由脱氢反应生成,并循环使用,原料只需要苯和空气,来源丰富。
这种方法如果工业化成功,将是很好的方法。
澳大利亚的孟山都公司小试成功,建成了2万吨/年的工厂,但后来又改成了异丙苯法,此法没有实现工业化。
(5)苯直接氧化法
苯在催化剂作用下直接被氧化生成苯酚。
反应方程式如下
催化剂
+1/2O2
此法一步完成,反应简单,但催化剂选择性低,中间产品复杂,且产品收率较低。
研究多年,未实现工业化。
如果能找到合适的催化剂和反应条件,将是种理想的的方法。
(6)甲苯氧化法
这是唯一不以苯为原料的方法,1955年美国道化学公司开发的。
方法是以甲苯为原料,钴盐做催化剂,用空气氧化生成苯甲酸,再以铜盐为催化剂,将苯甲酸用空气进行液相氧化得到苯酚。
反应方程式如下:
O2,钴盐催化剂
140℃,2atm
O2,Cu盐催化剂
240℃+CO2
1978年美国鲁姆斯公司提出了以甲苯为原料的气相苯甲酸脱羧基法制苯酚的新工艺,它克服了液相法副产焦油和残渣多的缺点。
国际上此法与异丙苯法是目前竞争最激烈的。
但在理论上,脱羧降解要尽量少用,因为能源利用不合理。
在国外,甲苯较便宜,比苯便宜20%~30%,它的成本较低,具有很强的竞争力。
而在我国。
甲苯和苯价格相当,此法使用较少。
(7)异丙苯法
异丙苯法发展比较晚,但是发展最快,近几十年来得到了迅速的发展。
具体方法是苯和丙烯以AlCl3或固体磷酸为催化剂,进行烷基化反应(工业上又称烃化反应)生成异丙苯,异丙苯在液相加热,通入空气,进行催化氧化而生成过氧化氢异丙苯,再用酸分解成苯酚和丙酮。
具体反应方程式如下:
1烃化反应
CH3
AlCl3或H3PO4
+CH3CH=CH2
CH3
2氧化反应
CH3CH3
+O2催化剂
CH3CH3
3酸分解
CH3O
-COOHH++H3C-C-CH3
CH3
此种方法腐蚀明显减轻,污染也减轻,技术也相当成熟。
最大的优点就是可以联产丙酮,它也是重要的有机原料之一,并且原料苯和丙烯来源丰富可以利用石油炼制的副产物,经济合理。
1.1.2丙酮生产方法的比较
生产丙酮的方法基本上分为两大类:
一类是以植物为原料的发酵法;一类是以石油为原料的合成法。
直到20世纪30年代,淀粉仍然是生产丙酮的原料。
一般情况下,每生产1吨丙酮大约需要11~12吨的淀粉或60~66吨的糖蜜。
由于发酵法生产丙酮需要大量的含淀粉植物,但是原料来源有限,所以逐渐被以石油为原料的合成法替代。
目前使用的合成法主要有异丙醇法、液化石油气氧化法、丙烯醇法、异丙苯法等。
(1)异丙醇法
将异丙醇催化脱氢或催化氧化脱氢生成丙酮。
反应方程式如下:
异丙醇催化脱氢:
OHZnOO
H3C-CH-CH3CH3CCH3+H2
350~400℃
异丙醇催化氧化脱氢:
OH催化剂O
CH3-CH-CH3+
O2CH3CCH3+H2O
丙酮收率为85%~90%,收率低是此法的一个缺点。
(2)液化石油气氧化法
采用液化石油气(丙烷-丁烷)为原料,将它与空气按一定的比例混合,在加热加压下反应,产物除了丙酮外,还得到醇、醛、酸等有机化合物。
缺点是收率低,耗能大。
(3)丙烯醛——异丙醇法
丙烯在铜催化剂下气相氧化生成丙烯醛,丙烯醛与异丙醇在MgO-ZnO混合催化剂作用下反应得到丙烯醇和丙酮,异丙醇用空气氧化生成丙酮和过氧化氢,最后用钨酸作催化剂由过氧化氢与丙烯醇制取甘油。
具体反应方程式如下:
Cu
CH2=CHCH3+O2CH2=CH-CHO+H2O
OHMg-ZnOO
CH2=CH-CHO+CH3-CH-CH3CH2=CHCH2OH+CH3CCH
OHO
CH3-CH-CH3+O2CH3CCH+H2O2
CH2=CHCH2OH+H2O2钨酸
理论上每生产1mol甘油就可以得到2mol丙酮
(4)异丙苯法
反应过程在苯酚的生产方法中介绍过了。
以上介绍的几种生产丙酮的方法各有特点,发酵法较落后,但在有副产的蜜糖的情况下仍可以采用。
在合成法中以异丙醇和异丙苯法为常见,异丙苯法可以在一个装置中同时生产苯酚和丙酮,也成为生产丙酮的主要方法。
通过以上几种方法的对比,可以确定采用异丙苯法来合成苯酚和丙酮
1.2工艺流程的评述与确定
异丙苯法生产苯酚丙酮的过程可分为四个工序:
①烃化丙烯、苯合成异丙苯的过程②氧化异丙苯氧化生成过氧化异丙苯的过程③酸分解在酸的作用下,过氧化氢异丙苯分解生成苯酚和丙酮的过程④精制分离精制苯酚和丙酮的过程
本设计重点在烃化工序。
烃化的工艺过程大致由五个部分组成:
催化剂的制备;原料预处理;烃化反应器;烃化反应产物的后处理;三废处理。
烃化工序工艺流程的确定主要是催化剂和反应器的选择。
1.2.1催化剂的选择
所用的催化剂主要是金属卤化物(如AlCl3)和强无机酸(如固体磷酸),在工业上采用的催化剂就是这两种。
这两种方法在工艺条件和工艺流程等方面都有很大的差别,各有优缺点。
(1)磷酸气相法
它是20世纪40年代开发的,采用固体磷酸催化剂生产异丙苯的工艺流程主要是美国环球油品公司开发的技术。
此法的优点是无强腐蚀,无污水对环境保护有利;设备材质防腐要求不高,易解决;流程简单,设备台数少;单位产品耗能低;易于大型化。
它的不足之处在于选择性低,收率低,因为磷酸法没有反烃化方应,使生成的副产物多;在高温高压下反应,要求设备、泵等密封严密,并且要耐高温,加工难度大,投资高;催化剂易失活,要求反复再生。
磷酸法对于装置规模较大时(年产10万吨以上),它的优越性才突出,而且此法对设备材质要求也高。
对于本设计规模较小,优越性不太突出,并且国内的设备材质等也难以满足要求,所以不采用此法。
(2)液相三氯化铝法
这种方法也是40年代开发的。
催化剂是AlCl3的一种络合物,由烷基苯、AlCl3和盐酸组成。
此法技术成熟,工艺条件温和。
它的优点弥补了磷酸法的不足,收率较高些,有反烃化的效果。
但一直存在着设备腐蚀和污水处理的问题。
本设计就是采用此法。
1.2.2烃化反应器的选择
在采用烃化反应器的型式时必须考虑以下几点:
本反应是气液非均相反应,要保证气液充分接触,使反应顺利进行;反应很易达到平衡,混反影响不大;反应液有强烈的腐蚀性;AlCl3络合物在高温下长期使用,易生成树脂,堵塞管道。
如果采用填料塔,气液相接触较好,有利于传质,接触面更新较快,有利于反应的继续进行。
但反应温度不可避免局部过高,AlCl3络合物就会结成树脂,堵塞填料,所以不用填料塔。
如果采用有搅拌器的反应槽,搅拌对传质和表面更新都有利,但是有反应
AlCl3+3H2O→Al(OH)3+HCl,有HCl存在,腐蚀严重,而且对搅拌器不好防腐,所以也不采用这种方法。
根据以上几个特点,采用结构简单的鼓泡空塔,其结构简单,不易堵塞,易于作防腐处理。
由于烃化液和AlCl3络合物得比重差不大,采用气态丙烯鼓泡进料的办法就可以使络合物在整个反应区域内分布得比较均匀,也可使苯和丙烯充分接触。
采用气态丙烯还有一个主要因素是保证苯过量,丙烯不足,从而减少多烷基苯的生成。
对于反应的换热装置也不装在内部,而是在塔外(如夹套等),否则要作防腐处理,很复杂。
目前主要有采用一个反应器和采用两个反应器的流程。
国内烃化流程都是采用一个反应器。
烃化反应和反烃化反应在同一个反应器中进行。
缺点是生成的多烷基苯多,不能实现反应的最佳化。
为了避免生成过多的多烷基苯,必须使反应在过量苯存在下进行,这样造成了反应器生产能力下降,也增加了烃化液精馏分离塔的负荷。
为了克服这一缺点,让烃化反应和反烃化反应分别在不同的反应器中进行,即采用两个反应器。
采用两个反应器在国外已经工业化了。
一个进行烃化反应,一个进行反烃化反应。
此法优点①可进一步降低AlCl3的消耗定额②异丙苯收率提高,反应器成产能力提高。
两个反应分别在两个反应器中进行,都可以实现反应的最佳化,多异丙苯含量降低,异丙苯收率提高,同时反应器的生产能力也提高了③降低了精馏塔的负荷,减少了苯干燥塔和脱苯塔的一次投资和操作费用。
采用两个反应器,即使丙烯与苯环的分子比增大,多异丙苯增加也不多,而异丙苯产量可有明显的提高。
这样苯过量不大,减少了精馏塔负荷;同时因进料苯和剩余苯减少,处理它的苯干燥塔和脱苯塔也可以减小,一次投资降低;苯流量小,动力操作费用也减少。
这些都说明采用两个反应器比采用一个反应器优越的多,但在我国两个反应器的工艺还不成熟,技术条件不具备。
所以本设计采用一个反应器的流程,即鼓泡塔反应器,物料并流。
1.2.3烃化反应产物的后处理
烃化反应器出来的烃化液和三氯化铝络合物必须分离开,并将烃化液精制,以得到异丙苯。
一般都采用沉降、水洗和中和进行处理。
(1)反应混合物的沉降
络合物具有较大的比重(烃化液比重是0.86,络合物比重是1.2~1.3),所以采用一般的沉降器就可以将它们分离。
原来采用两个沉降器串联,反应液出料进入第一沉降器,沉降下来的络合物返回烃化器。
研究发现采用两个沉降器有很多的缺点:
①设备庞大,生产能力低。
沉降槽内络合物靠自重回流,流速很慢,约为0.2m/s,所以沉降回流的管子造的都很粗。
为了保证沉降时间足够,络合物能较多的沉降下来,沉降槽的体积都很大,用两个大槽设备庞大,造价高,空间占用也大。
要保证充分的沉降时间,就使生产周期延长,势必造成生产能力下降。
②精制更困难。
因为第一沉降槽内温度和络合物浓度都较高,易生成副产物,而且停留时间长,给杂质的生成提供了机会,给精制带来了更大的困难。
可见采用沉降、冷却、再沉降的流程不合理。
现改为烃化液冷却到60~65℃,再沉降。
先冷却避免烃化液和络合物在高温下长时间的接触生成更多的副产物。
沉降时间1小时左右,时间缩短,生产能力提高。
沉降1小时,能保证充分的沉降,若延长沉降时间对沉降效果的影响并不明显,反而降低了生产能力。
(2)烃化液的水洗和中和
烃化液在沉降后还含有少量的三氯化铝,因为三氯化铝在烃化液中有一定的溶解度。
为了去除这部分络合物,可以采用水洗和碱中和的办法。
①水洗(在空塔中水洗)
AlCl3+3H2OAl(OH)3+3HCl
②中和(碱洗):
水洗后的烃化液中基本没有三氯化铝了,但是溶液呈酸性,还需要用氢氧化钠中和,即碱洗,也采用空塔。
1.2.5三废处理
用三氯化铝催化剂生产异丙苯的这一工艺流程最大的缺点是,过程中排出大量的污水,要经过处理才能排放,使得流程复杂,动力消耗增加。
污水中主要的有害物质是芳烃和Al(OH)3。
Al(OH)3的分离很困难,可采用简单蒸馏的方法回收芳烃,并把含有Al(OH)3的污水作为浮选剂,这种方法要保证Al(OH)3溶解。
废气是烃化尾气,里面没反应的丙烷送去做燃料。
废渣有焦油,规模小时可以烧掉,规模大时要分离出来回收利用。
1.3.工艺条件的论述与确定
烃化反应是一个汽液相反应,主要工艺条件是反应温度、反应压力和催化剂的用量、原料的配比等。
1.3.1配料比
即丙烯与苯核的分子比,实际上是反应器进料中烃基(这里指异丙基,它不只包括丙烯,还包括进料中带入的二异丙苯中的异丙基,因为在反烃化反应中异丙基也起到丙烯的作用)和苯核(苯和异丙苯、多异丙苯中的苯核)分子数目之比,习惯称做分子比。
烃化生成二异丙苯和三异丙苯的速度比异丙苯的快。
随着分子比的上升,异丙苯增加,但是多异丙苯的含量增加更快,所以不仅造成了多异丙苯的循环量大,而且也会增大烃焦油量;若分子比很小,芳烃过量很多,异丙苯的产量很低,生产能力小,而且有大量的苯没有反应,苯的转化率太低会增加精馏系统的负荷,增大了操作费用和一次性投资。
为了得到异丙苯和抑制多元异丙苯的生成,采用控制丙烯的含量,让芳烃过量,但不能过量太大。
综合考虑苯的一次转化率、收率、设备生产能力等因素,工业生产中所选用的较佳的丙烯/苯=0.4~0.6。
本设计采用的分子比是0.5左右,经研究得到这时烃化液的组成大约为:
异丙苯30%、苯60%、其他10%。
1.3.2反应压力
烃化反应式:
C6H6(l)+CH2=CHCH3(g)C6H5(C3H7)(l)
此反应是气相分子数减少的反应,压力上升有利于丙烯的溶解,也使苯的转化率上升。
但因为常压下烃化反应的转化率已接近100%(以丙烯的转化率计,因为丙烯不足),反应压力的影响不显著。
压力上升时反应液的泡点也上升,使反应温度上升导致催化剂失活,对烃化反应不利,甚至使反应不能进行,从这方面看加压不利。
为保证温度不大于120℃(避免催化剂失活)要求压力不大于6Kgf/cm2。
综合考虑,稍加一点压,只是为了克服阻力损失。
所以本设计采用压力:
0.12MPa。
1.3.3反应温度
烃化反应是放热反应。
根据热力学和动力学分析,温度上升,反应平衡常数下降,但反应速率上升,副反应速率也上升;温度下降,反应平衡常数上升,但反应速率下降。
反应温度对烃化反应的平衡影响不大,提高温度对平衡常数影响不大。
温度低,反应速率慢;温度高,反应速率提高,但是副反应速率提高更快。
当温度大于120℃时,催化剂三氯化铝络合物不耐高温,会发生结焦现象形成树脂,使催化剂失活,反而使反应速率急剧下降。
温度高,也可引起丙烯聚合,副反应增加。
目前烃化反应器换热的方法是用未反应的苯汽化带出反应放出的热。
所以反应温度就是在反应压力下一定组成混合物的泡点。
混合物的组成大约为:
异丙苯30%、苯60%、副产品10%,反应压力为0.12MPa时混合液的泡点是97.5℃,一般控制在95~100℃,本设计确定反应温度控制在95℃。
1.4工艺流程叙述
1.4.1烃化反应
烃化反应是在95℃、0.12MPa下进行的,是放热反应,反应热主要靠苯蒸发带出,其余热利用反应器的夹套换热器与水换热。
1.4.2尾气处理
从烃化塔T116顶部出来的