单晶炉操作规范34页word.docx
《单晶炉操作规范34页word.docx》由会员分享,可在线阅读,更多相关《单晶炉操作规范34页word.docx(30页珍藏版)》请在冰点文库上搜索。
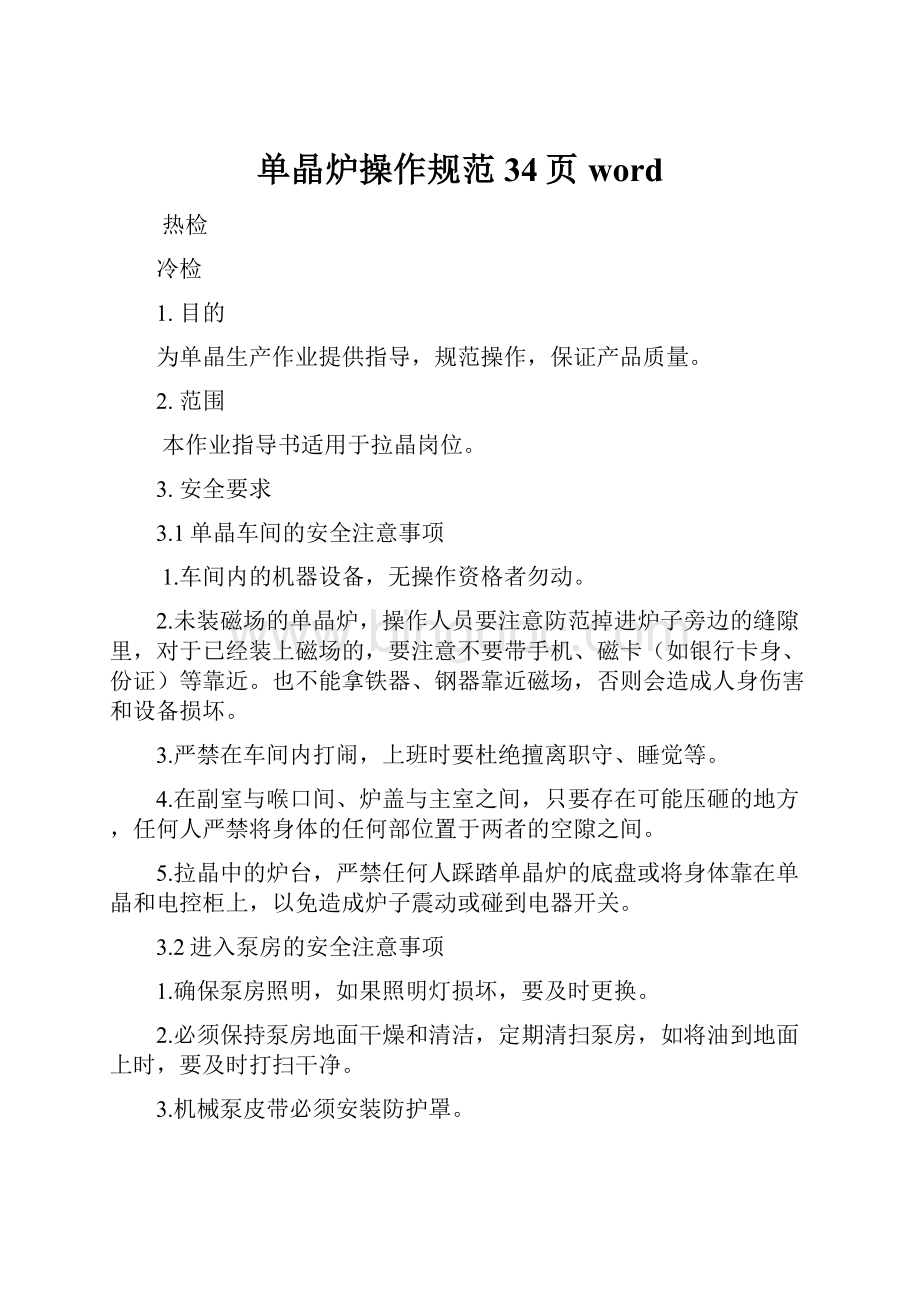
单晶炉操作规范34页word
热检
冷检
1.目的
为单晶生产作业提供指导,规范操作,保证产品质量。
2.范围
本作业指导书适用于拉晶岗位。
3.安全要求
3.1单晶车间的安全注意事项
1.车间内的机器设备,无操作资格者勿动。
2.未装磁场的单晶炉,操作人员要注意防范掉进炉子旁边的缝隙里,对于已经装上磁场的,要注意不要带手机、磁卡(如银行卡身、份证)等靠近。
也不能拿铁器、钢器靠近磁场,否则会造成人身伤害和设备损坏。
3.严禁在车间内打闹,上班时要杜绝擅离职守、睡觉等。
4.在副室与喉口间、炉盖与主室之间,只要存在可能压砸的地方,任何人严禁将身体的任何部位置于两者的空隙之间。
5.拉晶中的炉台,严禁任何人踩踏单晶炉的底盘或将身体靠在单晶和电控柜上,以免造成炉子震动或碰到电器开关。
3.2进入泵房的安全注意事项
1.确保泵房照明,如果照明灯损坏,要及时更换。
2.必须保持泵房地面干燥和清洁,定期清扫泵房,如将油到地面上时,要及时打扫干净。
3.机械泵皮带必须安装防护罩。
4.清洁机械泵和换油时,必须在泵的电源开关上悬挂警示牌,工作完毕后取走警示牌。
5洗泵时严禁将杂物掉入机械泵腔内。
3.3拆装炉
1.上班必须穿戴好劳保用品。
装炉时,还需戴口罩、手套等防护用品。
2.拆炉取晶时、注意不要被烫伤、划伤、碰伤。
3.晶体出炉后按指定地点摆放,并将晶体上多余的籽晶部份剪掉。
4.拆拿及安装石墨件时要戴上线手套。
3.4乙醇、丙酮的使用
1.工业乙醇及有丙酮害、使用时,要注意防止其溅入眼内。
2.严禁用内酮擦拭密封圈!
注意:
乙醇和丙酮都是易燃物,应安全使用和妥善保管。
4.工艺流程
5.4.1工艺流程图
压力化/溶料
抽空/检漏
装炉
拆炉
转肩
放肩
引晶
稳定化
停炉
收尾
等径
4.2过程控制
4.2.1.1取晶体
1、停炉5小时后须先进行手动热检漏并记录,(真空度<15mTorr)泄漏率应<15mTorr(0.55Pa/5min)。
泄漏率超出范围应报修。
手动热检漏操作步骤:
在触摸屏上将电控系统退到手动状态,关闭供气管道上的手动球阀,将三个电磁阀全部打开,然后抽空到极限真空。
停泵并保持炉子各阀门状态不变,等待约1分钟,然后开始观察5分钟内真空的变动情况,计算出泄漏率。
最后,将炉子状态复原。
2.检漏完毕后,分阶段缓慢降低晶转到零)持续时间约3-5分钟)。
禁止将晶转快速或直接降到零!
用蘸酒精的普通擦护纸将炉体外壁从上到下擦拭一遍。
包括提拉头、检修平台、副炉筒、护盖、主炉筒。
擦拭过程中要小心保护好线路及精密部件,也要防止造成环境的交叉污染。
3.停炉6小时后,才能充气拆炉。
穿戴好劳保护用品,准备好拆炉工具。
充氩气到大气压后,必须查看晶体完全提升到副室后方可提升副室。
4.将晶体提升到副室圆筒内,用托晶盘防护后,将副室转出。
转出时注意推动的速度要缓慢均匀,以防止晶体撞到炉筒上。
注意:
副室升起后,由于左右可旋转,要注意防止碰坏聂尔根。
(测直径CCD)
5.在晶体下方摆放好取晶框后,撤掉托晶盘,然后降下晶体,在晶体离取晶框底部还有3-5mm距离时,停止下降,严禁使晶体接触到取晶框(会导致上轴钢丝绳因跳槽而损坏)。
剪断细颈前,一人扶住取晶框,另一人用手抓住重锤或连杆(禁止触碰籽晶),然后剪断细颈后,要有控制地逐步释放重锤,防止重锤快速旋转和自由晃动,否则会导致钢丝绳跳槽或籽晶磕碰损伤。
6.检查钢丝绳是否完好可用。
若有变硬,毛刺或其它损坏情况,则应请维修人员去除老化、损坏部分,或换新的,注意钢丝绳在更换、维修后要及时校准限位!
7.在晶体上标识晶体编号,如实完整填写《单晶生产随工单》后,将晶体放置到规定的地方。
提渣盖了要标识好并妥善保存,待专门人员回收。
4.2.1.2拆热场、冷却和打扫炉内卫生。
SC籽晶控制板CC坩埚控制板引晶目的:
排除位错
SR晶转控制板CR埚转控制板收尾目的:
减小位错提高成精率
SL晶升控制板CL埚升控制板晶向:
110两线
111三线FB掺硼料
100四线SG掺钾料
1.戴上高温隔热手套,将热屏、保温盖取出,放置到石墨件专用小车上。
将主炉筒升起旋出(垂直方向上要离开热系统)。
将废石英、埚底料取出标记后放置到规定地点。
然后升高埚位将三瓣石墨埚、石墨埚托、隔热体、托杆依次取出,拉到冷却室冷却。
2.注意:
(1)取出的热屏应倒扣在小车上、防止高温下重金属进入石墨中从而造成原料的污染,
(2)在升炉筒时要保护好热电锥、防止碰到炉盖。
(3)在以上的操作过程中,要注意人身安全和设备安全!
8”22”
2.待热场温度降下后,按附录一《热场及炉腔清扫规范》进行石墨和炉内卫生的清理。
严禁在高纯车间打扫石墨件!
计算锅跟比=晶体直径2e固(2.33g/cm3)200C(固态)
钳锅内径2e液(2.5g/cm3)14200C(液态)
验算锅跟比=B2-B1(锅跟位)
A2-A1(晶体位)
4.2.3装炉
4.2.3.1安装热场
1.确认热场打扫干净,所用石墨件及保温毡上无挥发物及浮灰,下底盘清理干净。
上保温大盖的密封毡完好可用。
2.加热器石墨螺钉先拧紧(拧紧的尺度:
尽量珠紧),拧松防止高温烧结,再拧紧防止松动打火。
尤其磁场炉,若未拧紧,会加重加热器在通电时的振动。
3.托杆与下轴安装稳固、对中、托杆与下轴的固定螺钉拧紧即可(拧紧的尺度:
适可而止)。
4.确认隔热体、:
石墨埚托及三瓣埚是否完好可用
5.托杆与隔热体:
隔热体与石墨埚:
石墨埚托与三瓣埚托之间的止口在安装时要保证其连接必须吻合良好:
做到旋转滑动自如。
6.将主炉筒的下沿及下炉筒的上沿用酒精擦试干净后全上主炉筒,查看、对中热电锥的取光孔。
7.除上下保温盖及热屏以外的所有石墨件确认安装完毕并互相对中后,才能准备装料。
1热场无挥发物
2取光孔排气孔对齐
3冷却水及泵油是否正常
4.2.3.2装料
1.装料前的准备
(1)确认已完成设备点检项目,设备方面已不存在影响开炉的问题,周围环境良好。
(2)检查所备多晶料及母合金与报告单是否相符。
(3)准备好剪刀、装料车等用品。
穿戴好装料服、口罩、手套。
(4)将装料车擦拭干净。
2检查和安装石英坩埚
打开石英坩埚包装、戴好薄膜手套把埚举起对准光源检查石英坩埚,有下列特征之一者,为不合格,不能使用。
(1)磕碰损伤(位于坩埚上沿的微小碰损除外)。
(2)裂纹。
(3)严重划痕。
(4)气泡处于内壁,并且已经开裂。
(5)直径≥3mm气泡,数量≥1个。
(6)直径﹤3mm气泡,数量≥5个。
(7)线度尺寸≥3mm的杂质点,数量≥1个。
(8)线度尺寸﹤3mm的杂质点,数量≥5个。
(9)线度尺寸﹤3mm的气泡、杂质点,合计数量≥5个。
注:
杂质点:
处于坩埚内壁,液面淹没线以下的有色斑点。
气泡:
处于坩埚内壁,液面淹没线以下,夹在坩埚壁内的空洞。
检查没有问题后(若发现石英异常时及时与班长联系,经判断不能使用后,进行更换),将坩埚放入三瓣石墨埚内,过程中不能有任何磕碰发生,尽量装水平。
20时石英埚比较重,可两人配合装入。
装坩埚时要防止将坩埚外壁的石英渣子带入埚内,
3.装料
(1)更换装石英坩埚用一次性手套后,才能继续装料。
(2)两人配合,一人用剪刀把多晶料外包装袋沿塑封线剪开,另一人必须戴一次性手套将料取出放到高纯小车上。
注意在整个过程中外层包装不能直接或间接接触到料。
(3)按以下要求装料:
①首先选择小碎块的料铺满坩埚底部。
②选择较小块的料继续装入埚的中下部,中下部的料可以装得紧凑些并且贴近埚壁,但应该是自然堆砌,而不是硬挤。
与坩埚内壁接触的料块,应尽量选择具有表面光滑的球型面的料,避免尖锐对着埚壁。
③中度及较大块料码放在坩埚中部及中上部并靠近石英埚边,并注意使之对称放置,料块的线度尺寸应﹤100mm,太大时,需要选择两块同样大小的料块,双手握实后互相拍碎后方可装进,注意拍料时要小心避免迸出的料打到眼睛或掉到地上。
④选择小块料装在坩埚的上部,码放成圆锥型,每块料必须垒实,保证不能滑落。
埚中料块不宜装得太高,衡量标准是:
最上面靠近石英埚壁的料块,其重心外于石英坩埚上沿之下。
除最末一层外,仍可轻轻靠在埚壁上,但应注意几点:
I减少料块与埚边的接触面积,以防止挂边:
Ii在料块互相之间的相对位置方面,要预估料块在跨料后、是否会架桥,然后进行相应的调整:
iii装最上面一层时,料块不要靠在埚壁上。
禁止为了多装料而在坩埚上沿处“搭围墙“:
硬挤硬塞更属于严厉禁止之列。
宁愿少装料,也不要冒溅料、挂边的风险:
Iv在装料时,要预留足够的坩埚旋转空间,确保坩埚旋转时料不会碰到热屏。
V禁止将大块料装在最上层,防止塌料时砸伤石英坩埚。
(4)装料过程中应注意的几个问题:
1装料过程中必须保证料块是轻轻的与石英埚接触的,避免任何的磕碰和撞击。
2装料过程中严禁多品原料与包装外表面直接的接触。
3拍料时一定要戴好线手套,必要时戴上护目境。
4不论是上、中、下哪个部位,料块尖锐部位不能直接对着坩埚壁。
5要注意装料过程中防止把料洒进护底盘,如果有料块掉进炉膛,要设法取出,
6在装有大量沫子料(线度尺寸﹤1mm)时,要注意不能装满,料和石英埚上沿留有约20mm的余量,防止料受热膨胀后益出。
7如有预掺杂,应将掺装在石英坩埚的中部,避免提渣时将掺杂提出。
4.装完料降坩埚时,注意不要超过下限(不是设备下限位,而是热场装配时确定的安全下限。
18”热场坩埚的下限位为-115,20”热场坩埚的下限位为-103)防止造成短路。
5.装热屏时要脱掉装料服,换戴上新的薄膜手套,以防手沾污多晶料及热屏,并且要避免热屏撞上多晶料块。
装好后要检查料块与热屏之间的距离,要保证熔料时坩埚有安全的旋转空间。
6.检查无误后,用酒精擦净主炉室、炉盖、副室及隔离阀等处的密封面,合上炉盖。
关闭隔离阀后,检查籽晶、重锤等是否安装妥当,然后合上副室,停稳籽晶,打开隔离阀。
7.籽晶为重要部件,需要仔细保护,主要注意以下几点:
(1)防止机械损伤:
整个拆炉、装料过程早,籽晶不能有任何磕碰、损伤。
当无法确认是否有损伤时,应更换新籽晶。
有磕碰嫌疑的籽晶被换下后,应防止其再被作为籽晶使用(应回收改作原料用)。
(2)防止沾污:
装籽晶时要戴干净的薄膜手套,并且在手拿籽晶时要避免接触将要引晶的那一端:
籽晶装好后到被换下之前,禁止对籽晶任何形式的接触(包括用酒精擦拭),特别是下端用于熔接的部分:
籽晶脏了后,只能更换,不能用酒精擦拭。
(3)确保安装妥当:
每次装料后,都应检查籽晶,要能够在钼夹头内略微有上下松动的余地。
8.更改计算机中参数。
(1)更改初始装料量的参数为本次的实际装料数量。
操作步骤:
在操作界面按工艺参数按钮,出现初始化界面,把初始装料量(kg)改为本次实际装料量。
(2)更改坩埚跟踪/投料重量为实际投料数量。
操作步骤:
在操作界面按坩埚跟踪按钮,出现坩埚跟踪按钮控制环界面,修改投料重量当前坩埚内的实际料重。
如果在初始界面修改了初始装料量,然后采用自动抽真空步骤,此处的投料重量会自动修改初始装料量一致。
(3)查看计算机内每一步骤的工艺参数是否设置正确。
在以后拉晶操作步骤中,也要养成每次选择自动步骤之前,先查看工艺参数是否设置正确的习惯!
其中以下两类参数要特别小心。
(a)涉及晶体长度及坩埚位置的参数。
(b)步骤型的参数,要注意最末一个参数的设置。
比如,放肩表
、收尾表、最末一行的晶体长度,要确保足够长。
4.2.3抽空
1.确定主真空泵和副室真空泵一切正常后启动泵。
2.启动主真空泵时,需点动两三次后,再开泵。
稍等片刻后依次打开球阀和节流阀。
不经点动直接开泵和过快地打开球阀和地流阀都是错误的操作方法。
3.进行抽真空/检漏步骤
操作步骤:
在操作界面按工艺选择按钮,出现自动工艺(返回)界面,在此界面下按抽真空按钮即可。
当抽真空步骤完成之后系统将自动转入检漏步骤。
两分半后将显示出泄漏率数值。
若泄漏过大(﹤50mTorr/hr)可将系统切换至手动状态下手动通几次氩气后抽到极限真空。
再次进入自动工艺(返回)真空度﹤40mTorr/hr界面选择检漏进行自动检漏。
4.2.5压力化/熔料
1.检漏合格后,在操作界面按工艺选择按钮,出现自动工艺(返回)界面,在此界面下按压力化按钮,此时系统的压力控制将自动进入闭环,电脑将把炉内压力控制在我们设定的压力数值上。
压力化完成之后如果在工艺自动步骤里选择了自动进入熔料工艺,电脑将自动转入熔料步骤。
这时就可以打开加热器进行加热。
2.化料后期,我们要根据塌料情况而适当的升高埚位。
如果不及时将坩埚升上来,料块的主体部分处于低温区,增加化料的时间,也就增加了坩埚与硅液的高温反应时间,不利于坩埚的保护。
而且,埚底长期处于低温区,增加了漏料的风险。
因此操作人员要及时注意化料情况,随着料的垮塌手动升起埚位,但应让坩埚和热屏之间保持安全距离,预防原料在跨踏时碰上热屏,也不能一次性将坩埚升降太多,会使熔料温度变化太大导致跳料。
3.整个化料的过程中,都要有安全意识。
尤其在化料后期,操作人员不能离开炉台,要随时观察情况,及时处理挂边、搭桥、漏料及其他意外事故。
为了防范漏料,在平时就应该积累以下经验:
高温多少时间会第一次垮料,这时的液面高度应该在什么位置。
首次见到熔液后记住液面高度记号(以后液面只可能上升,不可能下降)。
判断漏料除了这些经验以外,还可以查看加热电源是否稳定(通过曲线数据里面的功率曲线是否平稳进行判断),因为漏料会造成短路打火。
4.在料块要化完时,就要及时将功率降下来,用高温的余热将剩下的料化完。
发现液面上渣子较多时,可以考虑降籽晶进行提渣。
注意:
为防止温度太高将重锤烤变形或加速钢丝绳的老化。
提渣时要提前将功率降到引晶功率附近,将埚位升高,并将氩气流量减半(以免渣子被吹到埚边),再沾渣子。
渣子粘好后,可以将埚位适当降低,以防范渣子在提升中掉进熔硅里,导致熔硅溅到热屏上。
4.2.5稳定化
下述第2步到第7部,是指在完成了温度校准情况下的正常操作步骤。
如果是新炉子首次开炉,或者热场有较大改动,或者自动调节温度已经不能很好地使用。
则需要在第2步和第3步之间进行一次温度校准工作。
温度校准做好后,只要能够正常地进行下述2-7步的操作,不需要再次进行校准。
温度校准的具体操作见附录四。
2.料熔化完后,将加热功率调节至引晶熔接功率。
手动将坩埚位置升到引晶埚位。
引晶埚位的确定方法,参见附录二。
3.待温度初步稳定后(判断标准:
液面温度到达1440~1470范围内),将热场温度和液面温控投入闭环。
然后将炉压设定点调节到2托。
进行低压挥发。
4.当低压挥发时间达到60分钟后,将炉压设定点恢复到正常值(即:
SOP参数中等径步骤的设定值)。
然后,等待电脑自动调节好引晶温度。
5.判断电脑已经调节好引晶温度的标准如下:
(1)热场温度及液面温度均已保持10分钟不变,不变的判断标准是温度波动范围在±10C范围内。
(2)液面温度的稳定点在1450±10C范围内,热场温度的稳定点在2300±100C范围内
当上述两项条件同时成立时,即认为引晶温度已经调节好,可以开始熔接、引晶。
6.如果生产安排有要求,则按附录三《提样测电阻率要求》中的要求提小头测电阻率并进行掺杂操作。
如果不需要提小头测电阻率,则可直接进入引晶步骤。
7.提小头测电阻率并掺杂完成后,重复上述第2到第4部,但是其中的低压挥发时间减少到20分钟。
让电脑自动调节好引晶温度。
然后开始引晶。
4.2.6引晶
1.把籽晶逐渐降到液面以上约10mm左右进行预热约5-10分钟,将籽晶熔接好。
2.在晶体提升里依次激活上升和慢速按钮,将外部引晶器控制晶体运动前的√去掉,才能使用点动引晶。
注意:
选择点动引晶时需要在系统维护里的工艺设置下的手动引晶栏里的点动引晶前打√。
3.在工艺选择里选手动引晶。
4.把晶升慢速给定一数值(如0.6mm/min),不能设定为0.0mm/min。
否则会使晶升电机寿命缩短。
(1)引晶要求熔接、缩颈均匀良好、直径在3-5mm之间,长度为所要拉制晶体的直径(如6吋为160mm,8吋为200mm)。
(2)引晶高速段的平均速度应控制在5-6mm/min之间,并且以此拉速生长的细颈长度要大于50mm。
过慢不能排除位错,过快则入肩时易放“飞”(放肩时长得太快,以至于呈方形),容易导致单晶半途鼓掉。
4.2.7放肩
在工艺选择里选放肩即可自动放肩。
4.2.8当肩部放大到接近要求直径时,在工艺选择里选择转肩即可。
转肩后的晶体直径必须在要求的范围内。
直径不在范围内的要进行调整。
直径太小,埚跟比相对偏慢,会导致液面下降过多,单晶容易断棱。
4.2.7等径
1.观察当光圈从出现到变亮变圆说明已经转过肩了,在工艺选择里选等径。
测量晶体直径长到预定值时就可以压好聂耳根光圈,在操作界面按等径控制,然后在此界面上按ON即可打上闭环。
注意在压聂耳根时让等径信号在500左右。
压好后,在系统维护界面里选择模拟量,查看红外直径信号的显示应在2.500左右。
偏差太大要进行调整。
注意:
进入等径后,晶体生长到等径SOP下的生长控制I打开长度的设定长度时生长控制会自动打上闭环。
2等径时鼓掉(断线)的处理
(1)处理原则
(2)当鼓棱长度大于所拉制晶体直径的两部左右时,应当按单晶进行冷却,冷却步骤见下面
(2),然后取出。
不足所拉制晶体的两部时,分以下几种情况处理:
①如果原料较差,或者化完料后看见液面有较多渣滓,应该提渣(俗称“提饼子”、“提盖子”)。
②如果原料较好,且化完料后液面较干净,应该回熔,回熔步骤见(3)。
③如果近期成晶比较正常,出现放肩过程中断线的情况,应该考虑提渣。
提渣时,不必进行冷却。
(2)冷却单晶的步骤如下:
①先将计算机等径控制、热场控制、坩埚跟踪界面切换为OFF,即退出闭环,埚转降至1转、晶转降到原来的二分之一,并将加热功率适当升高(以防结晶)。
②将坩埚下降20-30mm,使晶体脱离液面。
③冷却流程见下表。
晶体尺寸
冷却流程
拉速设定
保持时间
6吋
1.拉速3.0mm/min
30min
2.拉速4.5mm/min
60min
3.拉速8.0mm/min
30min
4.提至副室并隔离.炉压350毛
30min
8吋
1.拉速3.0mm/min
30min
2.拉速4.5mm/min
60min
3.拉速6.0mm/min
60min
4.提至副室并隔离.炉压350毛
60min
注意:
要严格按照冷却流程进行冷却,防止因冷却不到位导致晶裂。
④冷却结束后充气到常压按取晶要求取出晶体,检查好籽晶、钢丝绳。
将炉盖上的密封圈、隔离阀等擦拭干净,合好副室。
⑤先打开副室泵,然后在工艺选择里选择副室净化。
计算机将按程序对副室进行赶气抽空,当提示净化完成时,打开隔离阀。
最后记住关闭副泵阀门及副泵。
(3)回熔步骤如下:
①先将计算机等径控制、热场控制、坩埚跟踪界面切换为OFF退出闭环,将晶转减半,埚转降至1-2rpm。
并将加热功率适当升高(熔料功率的90%左右)。
②将埚位降到原引晶埚位以下10-20mm,这一点非常重要,不然在回熔过程中液面逐渐升高会淹没热屏。
③逐渐将单晶棒降到液面下回熔,一次不可下降太多(10mm以内),等液体里的固体棒子熔完脱离液面后方可再下降一次。
如果降得太多太快,会使固体棒子戳到石英坩埚,酿成事故。
注意:
在进行完上述操作后,要注意检查坩埚跟踪里的投料量和实际情况是否相符。
3.等径过程中需要检查的项目
(1)按照附录五《拉晶中埚跟比的验算方法》验算埚跟运行是否正常,并将验算结果记录。
(2)查看炉子的压力控制情况,看氩气流量、炉压和节流阀开度的数值是否正常。
尤其是节流阀开度正常应该保持在20-40%之间,如开度太大。
超过50%,就要对真空系统进行排查,停炉后还需进行检修。
(3)每隔1小时测量晶体的直径,出现直径偏差过大,尤其是直径不够时要及时进行调整。
并且要注意到:
直径偏差过大时,原来设定的埚跟比也不适用了,会导致液面偏离恒定位置,晶体容易鼓掉。
4.拉晶时间的控制要求:
(1)普通拉晶,提倡不要超过60个小时,严禁超过72小时,即在50小时后还没拉出单晶就应考虑提多晶。
这里的拉晶时间从熔完料开始计算,下同。
(2)对于磁场拉晶,提倡不要超过70小时,严禁超过90小时,即在60小时后还没拉出单晶时就应考虑提多晶。
在执行上述规定时,也要防止走向另一个极端:
轻易放弃拉单晶的努力。
即普通拉晶和磁场拉晶的运行时间还分别在50和60小时之内,就不能够放弃试拉单晶的努力。
4.2.8收尾
1.当剩料重量达到要求重量时,在工艺选择里选收尾即可。
热场
晶体直径
收尾重量(㎏)
18吋
6吋
4~5
18吋
8吋
7~8
20吋
6吋
5~6
20吋
8吋
8~9
2.收尾长度为所拉制单晶的断面直径。
4.2.9停炉
1.收尾完成后,在工艺选择里选停炉,待功率降为0后,关掉加热电源,进行冷却。
2.停炉冷却5个小时后,停气抽空,抽空到极限后,关阀、关泵、进行手动检漏(此为热检漏)。
将真空度及检漏数据记录下来。
检漏完成后,将炉膛充气到一半(即:
炉压300-400乇),保持到拆炉。
3.停炉满6小时后,可以拆炉。
5煅烧要求
5.1新炉台、新热场的煅烧
5.1.1新炉台煅烧前工作
1.新炉台进行空炉真空验收:
极限真空﹤15mTorr,泄漏﹤30mTorr/h,通过后方可安装热场煅烧。
2.新炉需将炉膛擦拭干净。
安装新的热场时,必须将石墨件表面打扫干净,热场装配要对中。
3.确认上轴、下轴的限位、行程和零位都已经进行校正。
5.1.2全套新热场的煅烧步骤
1.第一步,真空煅烧,目的是去除水份及易挥发物质。
(1)由于新热场含有大量水分,极限真空的标准降低到100mTorr。
即:
抽空到100mTorr以内后,即可加热。
第一次功率30kw,一直烧到真空数值小于100mTorr后,加第二次功率到60kw,当煅烧到真空数值再次小于100mTorr后,加第三次功率到90kw,保持90kw,直到真空数值小于50mTorr,停止煅烧。
(2)在上述第二、第三次加功率后,要保证真空数值不大于200mTorr,否则炉内容易出现电离打火。
如果出现真空数值大于200mTorr,则需要将功率降低到上一步骤的数值。
保持煅烧2小时后,再次尝试增加功率,如此循环往复,直到将真空数值烧到小于100mTorr。
2第二步,真空煅烧,目的是彻底清洁石墨毡。
(1)经第一次煅烧后,将热场全部拆出彻底清扫热场及炉腔。
然后装炉抽空。
达到要求的极限真空(50mTorr)后,开始加热。
(2)在2小时内,逐步均匀地将功率加到最高功率90kw。
保持12小时后停炉。
(3)在拆炉前应检查极限真空及泄漏率,如果达到工艺标准的要求:
极限真空﹤20mTorr泄漏率﹤40mTorr/h,则可转入第三步煅烧。
否则应上报班长,查找原因解决问题后方可转入第三步煅烧。
3.第三步,通氩气煅烧,目的是为拉晶作准备。
(1)将热场全部拆出并清扫干净。
用砂纸打炉膛,要将炉内壁的彩色挥发物彻底打扫干净。
对副室也要仔细清扫。
(2)装炉,抽空到要求的极限真空(﹤20mTorr)后,通氩气煅烧。
在1小时内逐步升高