液压系统的设计.docx
《液压系统的设计.docx》由会员分享,可在线阅读,更多相关《液压系统的设计.docx(22页珍藏版)》请在冰点文库上搜索。
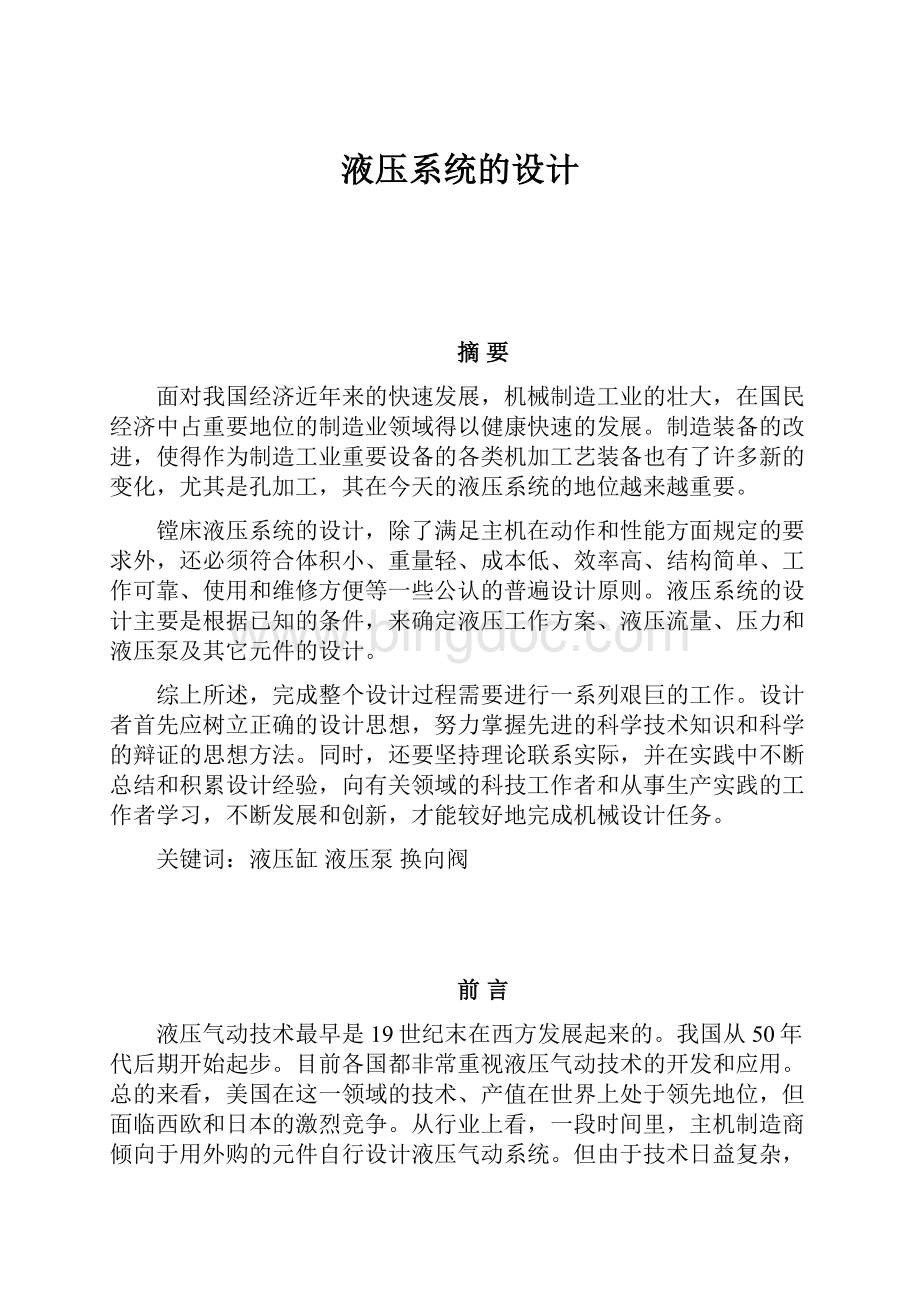
液压系统的设计
摘要
面对我国经济近年来的快速发展,机械制造工业的壮大,在国民经济中占重要地位的制造业领域得以健康快速的发展。
制造装备的改进,使得作为制造工业重要设备的各类机加工艺装备也有了许多新的变化,尤其是孔加工,其在今天的液压系统的地位越来越重要。
镗床液压系统的设计,除了满足主机在动作和性能方面规定的要求外,还必须符合体积小、重量轻、成本低、效率高、结构简单、工作可靠、使用和维修方便等一些公认的普遍设计原则。
液压系统的设计主要是根据已知的条件,来确定液压工作方案、液压流量、压力和液压泵及其它元件的设计。
综上所述,完成整个设计过程需要进行一系列艰巨的工作。
设计者首先应树立正确的设计思想,努力掌握先进的科学技术知识和科学的辩证的思想方法。
同时,还要坚持理论联系实际,并在实践中不断总结和积累设计经验,向有关领域的科技工作者和从事生产实践的工作者学习,不断发展和创新,才能较好地完成机械设计任务。
关键词:
液压缸液压泵换向阀
前言
液压气动技术最早是19世纪末在西方发展起来的。
我国从50年代后期开始起步。
目前各国都非常重视液压气动技术的开发和应用。
总的来看,美国在这一领域的技术、产值在世界上处于领先地位,但面临西欧和日本的激烈竞争。
从行业上看,一段时间里,主机制造商倾向于用外购的元件自行设计液压气动系统。
但由于技术日益复杂,使得用从各制造商购得的元件建立具有稳定市场效益的液压气动系统越来越困难。
设计的任务正向元件制造商转移,由专业液压气动厂商供应成套系统,但只有大公司才能承担这项任务。
基于此,全球性的跨国公司展开了竞争、合并。
大量的资金用于研究开发和技术革新,较小的公司负担不了这样的开支,其中很大一部分被挤出市场。
我国经过40多年的发展,液压气动行业已具有一定的独立开发能力,能生产出一批技术先进、质量较好的元件、系统和整机,随着我国加入WTO,向国际先进技术学习、与世界着名的大公司合作的机会越来越多,这将是这一行业的发展趋势。
近年来,液压传动由于应用了计算机技术、信息技术、自动控制技术、新材料等后取得了新的发展,使液压系统和元件正向高压、高速、高精度、高效率的方向发展,在完善比例控制、伺服控制、数字控制等技术上取得新的成就。
液压系统的发展方向是:
创制新型节能、微型元件﹑高度的组合化、集成化和模块化和微电子结合,走向智能化。
综上所述,液压工业在国民经济中的作用是很大的,它常常用来衡量一个国家工业水平的重要标志之一。
与世界上主要的工业国家相比,我国的液压工业还有相当差距,标准化、优质化的工作有待于继续做好,智能化的工作刚刚起步,为此必须急起直追,才能迎头赶上。
第1章液压传动概述
液压气动技术是机械设备中发展最快的技术之一。
特别是近年来与微电子、计算机技术相结合,使液压气动技术进入了一个新的发展阶段。
目前,已广泛应用在工业各领域。
由于近年来微电子、计算机技术的发展,液压、气动元器件制造技术的进一步提高,使液压气动技术不仅作为一种基本的传动形式上占有重要地位,而且以优良的静态、动态性能成为一种重要的控制手段。
液压传动的工作原理及组成
工业各部门使用液压传动的出发点是不尽相同的:
如工程机械、压力机械是利用它们在传递动力上的长处;航空工业是利用其结构简单、体积小、重量轻、输出功率大的特点;机床是利用它们在操纵控制上的优点,利用其能在工作过程中实现无级变速,易于实现频繁的换向,易于实现自动化等。
液压传动的工作原理:
液压传动是利用液体的压力能来传递动力的一种传动式,
液压传动的过程是将机械能转换和传递的过程。
液压系统的组成
动力装置——液压泵;
执行装置——液压缸和液压马达;
控制调节装置——控制阀;
辅助装置——除上面以外的其他装置。
液压传动的特点
液压传动的优点
1.液压传动装置运动平稳,反应快,惯性小,能高速启动,制动和换向。
2.在同等功率情况下,液压传动装置体积小,重量轻,结构紧凑。
例如同功率液压马达的重量只有电动机的10%-20%。
3.液压传动装置能在运行中方便的实现无及调速,且调速范围最大可达1:
2000(一般为1:
1000)。
5.操作简单方便,易于实现自动化。
当它电气联合控制时。
能实现复杂的自动工作循环和远距离控制。
6.易于实现过载保护。
液压元件能自行润滑,使用寿命较长。
7.液压元件实现了标准化、系列化、通用化,便于设计、制造和使用。
液压传动的缺点
1.液压传动不能保证严格的传动比,这是由于液压油的可压缩性和泄露造成的。
2.液压传动对油温变化较敏感,这会影响它的工作稳定性。
因此液压传动不宜在很高或很低的温度下工作,一般工作温度在-15℃~60℃范围内较合适。
3.为了减少泄露,液压元件在制造精度上要求较高,因此它的造价高,且对油液的污染比较敏感。
4.液压传动装置出现故障时不易查找原因。
5.液压传动在能量转换(机械能—压力能—机械能)的过程中,特别是在节流调速系统中,其压力、流量损失大,故系统效率低。
6.液压传动在能量转换的过程中,其压力、流量损失大,故系统效率低。
液压工作的介质
物理性质
1.密度单位体积的液体质量称密度。
矿物油型液压油在15℃时的密度为900㎏/m3左右,在实际使用中可以认为不受温度和压力的影响。
2.可压缩性和膨胀性
液体受压力的作用而使体积发生变化的性质称为液体的可压缩性。
液体受温度的影响而使体积发生变化的性质成为液体的膨胀性。
体积为V的液体,当压力变化量为△p时,体积的绝对变化量为△V,液体在单位压力变化下的体积相对变化量为
k=-
式中,k称为液体的体积压缩系数。
因为压力增大时液体的体积减少所以上式右边加一负号,以使k为正值。
液体体积压缩系数的倒数称为液体的体积弹性模量,用K表示。
即
体积弹性模量K表示液体产生单位体积相对变化量时所需要的压力增量。
在使用中,可用K值来说明液体抵抗压缩能力的大小。
液压油的可压缩性对液压传动系统的动态性能影响较大,但当液压传动系统在静态下工作时,一般可以不予考虑。
对液压工作介质的要求
⑴.有适当的黏度和良好的黏温特性
⑵.氧化安定性和剪切安定性好
⑶.抗乳化性、抗泡沫性好
正确合理地选用工作介质,对于保证液压系统正常工作、延长使用寿命、提高工作可靠性、防止事故发生等都有非常重要的影响。
液压油液的选用,首先根据液压传动系统的工作环境和工作条件来选择合适的液压油类型,然后再选用液压油的黏度。
第2章总评方案
工况分析
分析系统工况。
首先,根据已知条件,绘制运动部件速度循环图。
如下图所示,然后计算各阶段的外负载并绘制负载图。
负载循环图
液压缸所受外负载F包括三种类型:
即:
F=Fw+Ff+Fa
式中:
Fw----------工作负载对于金属切削机床来说,即为沿活塞运动方向的切削力。
本系统中Fw为15000N。
Fa--------运动部件速度变化时的惯性负载。
Ff--------导轨摩擦阻力负载。
启动时为静摩擦力,启动后为动摸擦力。
对于平导轨Ff可由下式求:
Ff=f(G+FRn)
G-------运动部件重力
FRn-----垂值与导轨工作负载
f-------导轨摩擦系数。
本系统中静摩擦系数为,动摩擦系数为。
则求的:
Ffs=×20000=4000N。
Ffa=×20000=2000N。
上式中Ffs为静摩擦阻力,Ffa为动摩擦阻力。
Fa=
式中g----重力加速度
t-------加速度或减速度时间﹑本系统中t取
v------t时间内的速度变化量
根据上述计算结果,列出各工作阶段所受的外负载如下表,并画出上图所示的负载循环图。
工作循环各阶段的外负载
工作循环
负载组成
负载值F/N
推力F*n/N
启动
F=Ffs
4000
4450
快速
F=Ffs
4000
4450
工进
F=Ft+Ffa
17000
18900
快退
F=Ffa
2000
2220
确定液压系统方案
确定供油方式
考虑到该机床在工作进给时负载较大,速度较低。
而在快速,快进是负载较小,速度较高。
从节省能量,减少发热考虑。
液压泵源系统宜选用双泵供油方式或变量泵供油。
现采用带压力反馈的限压式变量叶片泵。
调速方式的选择
在中小型专用机床的液压系统中,进给速度的控制一般采用截流阀或调速阀。
根据铣削类专用机床工作时对低速性能和速度负载特性都有一定要求的特点,决定采用限压式变量泵和调速阀组成的容积截流调速。
这种调速回路具有效率高,发热小和速度刚性好的特点,并且调速阀装在回油路上,具有承受负切削力的能力。
速度换接方式的选择
本系统采用电磁阀的快慢速换接回路,它的特点是结构简单,调节行程比较方便,阀的安装也比较容易,但速度换接的平稳性较差。
若要提高系统的换接平稳性,则可改用行程阀切换的速度换接回路。
最后把所选择的液压回路组合起来,即可组合成如下图所示.
液压系统原理图
电磁阀动作顺序如下表:
元件动作
1YA
2YA
3YA
启动
+
_
+
快进
+
_
+
工进
_
+
-
快退
+
_
+
执行元件的工况图:
(a)压力循环图
(b)流量循环图
(C)功率循环图
机床进给液压缸工况图
t1---快进时间t2----工进时间t3----快退时间
A:
启动:
按下启动键,电磁铁1YA通电,先导电磁铁阀4的左端接入系统。
由泵输出的油经先导电磁阀5流入液压缸,再经过先导电磁阀7的左端,进入液流阀回油路。
油路的工作情况为:
进油路:
过滤器2→变量泵3→先导电磁阀5→单向节流阀6→先导电磁阀7→液压缸8
回油路:
液压缸8→先导电磁阀5→油箱。
B:
快进:
按下启动键后,由电磁铁1YA,3YA通电。
先导电磁阀4的左端接入系统,同时先导电磁阀5的右端接入系统。
油路工作情况为:
过滤器2→单向液压泵3→先导电磁阀5→液压缸8。
回油路:
液压缸8→先导电磁阀5→油箱。
C:
工进:
按下按钮后,2YA通电,先导电磁阀5的右端和先导电磁阀7的右端接入系统。
进油路:
过滤器2→单向液压泵3→先导电磁阀5右端→液压缸8。
回油路:
液压缸8→先导电磁阀7右端→油箱。
D:
快退
按下按钮后,1YA,3YA,通电。
先导电磁阀5的左端和先导电磁阀7的右端接入系统。
进油路:
过滤器2→单向液压泵3→先导电磁阀5→先导电磁阀7→液压缸8。
回油路:
液压缸8→先导电磁阀5→油箱。
第3章确定主要参数
计算液压缸的尺寸流量
液压缸的结构简单,与杠杆、连杆、齿轮齿条、凸轮等机构配合使用能实现多种机械运动以满足各种要求。
按结构特点的不同,缸可以分为活塞式、柱塞式和摆动式三大类;按作用方式分为单作用和双作用两种。
根据系统要求,选择活塞式单作用的液压缸。
通常活塞缸由后端盖、缸筒、活塞、活塞杆和前端盖等主要部分组成。
为了防止工作介质向缸外或由高压腔向低压腔泄露,在缸筒与端盖、活塞与活塞杆、活塞与缸筒、活塞杆与前端盖之间均设有密封装置。
在前端盖外侧还装有防尘装置。
为防止活塞快速运动到行程终端时撞击缸盖,有些缸的端部设置缓冲装置。
液压缸工作的压力确定
液压缸工作压力主要根据液压设备的类型来确定,对于不同用途的液压设备,由于工作条件不同,通常采用的压力范围也不同。
液压设备的常用的工作压力
设备类型
机床
磨床
组合机床
龙门刨床
拉床
农业机械或中型工程机械
液压或起重机械
工作压力P/MPa
~
3~5
2~8
8~10
10~16
20~30
现参阅上表取液压缸的工作压力为Pa=
计算液压缸内直径D和活塞杆直径d
由负载图知最大负载F为18900N。
按下表取P2为,
=.
执行元件背压的估计直
系统类型
背压P2(Mpa)
中低压系统
0~8MPa
简单的系统
一般轻载的截流调速系统
~
回油路带调速阀的系统
~
回油路带背压阀的系统
~
采用带补液压泵的闭和回路
~
中高压系统
>8~16
同上
比中低压系统高
50%~100%
高压系统
如锻压机械等
初算时背压可忽略不记
液压缸内直径D与活塞杆d的关系
按机床类型选取d/D
按液压缸工作压力选取d/D
机床类别
d/D
工作压力P/(Mpa)
d/D
磨床,研磨床
~
<=2
~
插床,拉床,刨床
>2~5
~
钻床,镗床,铣床
>5~7
~
——
---------
>7
考虑到快进,快退速度相等。
取d/D为,代入公式:
F--------工作循环中最大的外负载
P1--------液压缸工作压力。
初算时可取系统工作压力P0
P2--------液压缸回油腔背压力
d/D-------活塞杆直径与液压缸内直径之比
-------液压缸的机械效率。
一般ncm=在本系统中
F=18900N,P1=,P2=,ncm=,d/D=.
则代入公式中可得:
D=82mm
液压缸内直径尺寸系列(GB2348-80)(mm)
8
10
12
16
20
25
32
40
50
63
80
(90)
100
(110)
125
(140)
160
(180)
200
(220)
250
320
400
500
630
注:
括号内数值为非优先选用值
活塞杆直径系列(GB-80)(mm)
4
5
6
8
10
12
14
16
18
20
22
25
28
32
36
40
45
50
56
63
70
80
90
100
110
125
140
160
180
200
220
250
280
320
360
400
根据上表可知,将液压缸内直径调整为标准系列直径D=90mm。
活塞杆直径d,按d/D=及查表可得d=63mm。
由此求得液压缸的腔的实际有效面积为:
根据上述D与d的直,可估算液压缸在各个工作阶段的压力,流量和功率。
按最低工进速度验算液压缸的最小稳定速度,由公式:
式中:
Qmin----------流量阀的最小稳定流量。
Vmin----------液压缸的最低速度。
由设计要求给定。
公式中Qmin是由产品样本查的GE系列调速阀,AQF3---E10B的最小稳定流量为min.本系统中调速阀是安装在回油路上,故液压缸有杆腔的实际面积:
可见上述不等式能满足液压缸的要求,能够达到所需的低速。
计算在工作阶段液压缸所需的流量
计算液压泵的电机功率
液压泵是靠密封工作容积变化来工作的,也称为容积泵。
容积泵具有两个特征:
1.有周期性的密封工作容积变化,密封工作容积由小变大吸油,由大变小压油。
2.有配流装置,它保证密封工作容积由小变大时只与吸油管接通;密封工作容积由大变小时只与压油管相通。
泵的工作压力的确定
液压泵的压力参数主要是工作压力和额定压力
工作压力是指液压泵在实际工作时输出油液的压力直,即泵出油口处压力直,也称系统压力。
此压力取决于系统中阻止液体流动的阻力。
阻力增大,工作压力升高;反之则工作压力降低。
如果将泵的压油口直接和油箱相通,则泵的工作压力接近为零;如果将泵的出口堵死,泵输出的油液无法排出,压力迅速增高,直至电机憋住或泵及其它元件被损坏。
额定压力是指泵在正常工作的条件下,按实验标准规定,在额定转速下连续运转的最高压力。
由于液压传动的用途不同,液压系统所需要的压力也不同,为了便于液压元件的设计、生产和使用,将压力分为几个等级,如下表:
压力分级
低压
中压
中高压
高压
超高压
压力/Mpa
≤
>~8)
>(8~16)
>(16~32)
>32
考虑的正常工作中进油路有一定的压力损失,所以泵的工作压力为:
公式中:
Pp-液压泵最大工作压力。
P1-执行元件最大工作压力。
-进油路中压力损失。
初算时简单系统取~,复杂系统取~.本系统取.
上述计算所得的Pp是系统的静态压力,考虑到系统在各种工况的过度阶段出现的动态压力往往超过静态压力。
另外考虑到一定的压力储备量,并确保泵的寿命。
因此,选泵的额定压力Pa应满足Pn≧(~)Pp.中低压系统取小直,高压系统取大直。
在本系统中Pn=.
泵流量和排量
排量V它是由泵密封容腔几何尺寸变化计算而得到的泵每转排出油液的体积。
也可以说在无泄露的情况下,用泵每转所排出的油液体积来表示,常用的单位为mL/r.
液压泵的最大流量应为:
式中Qp-液压泵的最大流量。
-同时动作的各执行元件所需流量之和的最大直。
Kl-系统泄漏系数。
一般取Kl=~,现取Kl=.
=×=min
选择液压泵的规格
根据以上计算的Pp和Qp再查阅有关手册,现采用YBX—16线压叶片泵,该泵的基本参数为:
每转排量
=16mm/r,泵的额定压力
=,电动机转速
=1450r/min,容积效率
=,总效率
=.
与液压泵匹配的电动机的选定
首先分别计算出快进与快退以及工进等不同共况时的功率。
取它们中的最大直作为选择电动机规格的依据。
由于在工进时泵的出的流量较小,泵的效率急剧降低,一般当流量在~1L/min范围内时,可取n=~.同时还应该注意的为了失所选择的电动机在经过泵的流量特性曲线,最大功率点时不致停转,需进行验算。
即:
公式中:
Pn------所选择电动机的额定功率。
PB------先压式变量泵的限定压力。
qp--------压力为PB时,泵的输出流量。
首先计算快进时功率。
快进时的外负载为4000N,进油路压力损失为。
由公式:
快进时所需电动机功率为:
工进时:
查阅电动机产品样本选用Y90S—4型电动机,其额定功率为,额定转速为1400r/min。
根据产品样本查得YBX---16的流量压力特性曲线,再由已知快进时流量为min,工进时流量为min,压力为4Mpa,作出泵的实际工作时的流量压力特性曲线。
YBX-16液压泵特性曲线
1-额定流量压力下的特性曲线。
2-实际工作时的特性曲线。
由上表查得曲线拐点的流量为24L/min,压力为,该点工作时对应的功率为:
所选电动机能够满足工作需要,拐点处能正常工作。
液压泵的气穴、噪声
气穴
液压泵在吸油过程中,吸油腔中的绝对压力会低于大气压。
如果液压泵离油面很高,吸油口处过滤器和管道的阻力过大,油液的黏度过大,则液压泵吸油腔中的压力很容易低于油液的空气分离压,这时,溶解在油液中的气体会从油液中分离出来,产生大量气泡,随着泵的运转,这些气泡被带入高压区,因受压缩,体积突然变小,气泡被击破,产生幅直很大的高频冲击压力,其直高达150Mpa,同时还产生局部高温。
这种高频液压冲击作用,不但会产生高频噪声,还会造成金属表面的气蚀现象,使泵的零件腐蚀损坏。
这就是液压泵的气穴现象。
为了避免在泵内产生气穴现象,应尽量降低吸入高度,采用通径较大的吸油管并尽量少用弯头,吸油管端采用容量较大的过滤器以减小吸油阻力。
液压泵的噪声
在液压系统的噪声中占很大的比例,减小液压泵的噪声是液压系统降噪处理中的重要组成部分。
产生噪声的原因:
1.泵的流量脉动引起压力脉冲,这是造成泵振动的动力源。
2.液压泵在其工作过程中,当吸油容积突然和压油腔接通,或压油容积突然和吸油腔接通时,均会产生流量和压力的突变而产生噪声。
3.气穴现象
4.泵内流道具有突然扩大和收缩,急拐变、通道面积过小等而导致油液旋涡而产生振动。
降低振动的措施:
1.吸油泵的压力和流量脉动,在泵的出口处安装蓄能器或消声器。
2.消除泵内液压急剧变化,如在配油盘吸、压油窗口开三角型阻尼槽。
3.压油管的某一段采用橡胶软管,对泵和管路进行隔振。
4.防止气穴现象和油中参混空气。
第4章选择液压元件
选择阀的类型
按作用分为:
1.方向控制阀(如单向阀、换向阀)
2.压力控制阀(如溢流阀、减压阀、顺序阀等)
3.流量控制阀(如节流阀、调速阀)
按控制方式分为:
1.开关控制阀借助于手轮、手柄、凸轮、电磁铁、液压、气压等定直地控制流体的流动方向、压力和流量,多用于普通液压传动系统。
2.比例控制阀与输入电信号使输出按一定的规律成比例地控制流体的流动方向、压力和流量,多用于开环程序控制控制系统。
3.伺服控制阀将微小的电气信号转换成大的功率输出,用以控制系统中液体的流动方向、压力和流量,它用于闭环控制系统。
4.电液数字式控制阀用数字信息直接控制,用以控制液体的流动方向、压力和流量。
阀口的规格大小用公称通径Dg(单位mm)表示,它小于阀的连接口径。
阀的流通能力常用阀的有效截面积即通流截面来表示。
由液流的动量定律可知,作用在阀芯上的液动力有稳态液动力和瞬态液动力两种。
1.稳态液动力对滑阀性能的影响是加大了操纵滑阀所需的力。
稳态液动力要使阀口关闭,相对于一个复位力,故它可使滑阀的工作趋于稳定。
2.顺态液动力是阀芯在移动过程中(即开口大小发生变化时)阀腔中液流因加速或减速作用在阀芯上的力。
这个力只于阀芯移动速度有关(即与阀口开度的变化率有关),与阀口开度本身无关。
本液压系统可采用力式系列或GE系列的阀。
方案一:
控制液压缸部分采用力式系列的阀。
方案二:
均选用GE系列的阀。
根据一定的液压系统图,按通过各元件的最大流量来选择液压元件的规格。
选用的液压元件如下:
液压元件明细表
序号
元件名称
方案一
方案二
通过流量
(L/min)
1
滤油器
XU—B32100
XU—B32100
24
2
液压泵
YBX---16
YBX---16
24
3
压力表开关
K—H6
KF3---EA10B
---
4
三位四通换向阀
4WE6E50/OAG24
34EF30---E108
20
5
二位三通换向阀
3WE6A50/0AG24
23EF3B---E10B
20
6
单向调速阀
2FRM5—20/6
AQF3-----E10B
20
选择液压元件确定辅助装置
确定管道尺寸
油管内直径尺寸一般可参照选用的液压元件,接口尺寸确定也可按管路允许流速进行计算。
本系统油路流量为差动时流量q=40L/min,压油管允许流速取V=4m/s。
则内直径d为:
若系统油路流量按快退时取q=min,可算得油管内直径d=.
综合诸多因数,现取油管的内直径d为12mm,吸油管同样可按上式计算(q=24L/min,V=s)现参照YBX~16变量泵吸油口连接尺寸。
取吸油管内直径d为25mm。
液压油箱容积的确定:
本系统为中压液压系统。
液压油箱容积按泵的流量的5~7倍来确定,现选用容量为160L的油箱。
液压系统的验算:
已知该系统液压系统中,选用油管内直径均为12mm。
各段管道的长度分别为:
选用L—HL32液压油,考虑到油的最低温度为15
。
查得15
液压油的运动粘度v为150cst=s。
油的密度
=920Kg/m3。
压力损失的验算
1.工作进给时,进油路压力损失,运动部件工作进给时的最大速度为18
进给时的最大流量为min。
则液压油在管内流速V1为:
管道流动雷偌数Re1为:
Re1<2300,可见油液在管道内流态为层流。
其沿程阻力系数为:
进油管道BC的沿程压力损失
P1-1为
查得换向阀4WE6E50/AG24