A级曲面工程简述.docx
《A级曲面工程简述.docx》由会员分享,可在线阅读,更多相关《A级曲面工程简述.docx(15页珍藏版)》请在冰点文库上搜索。
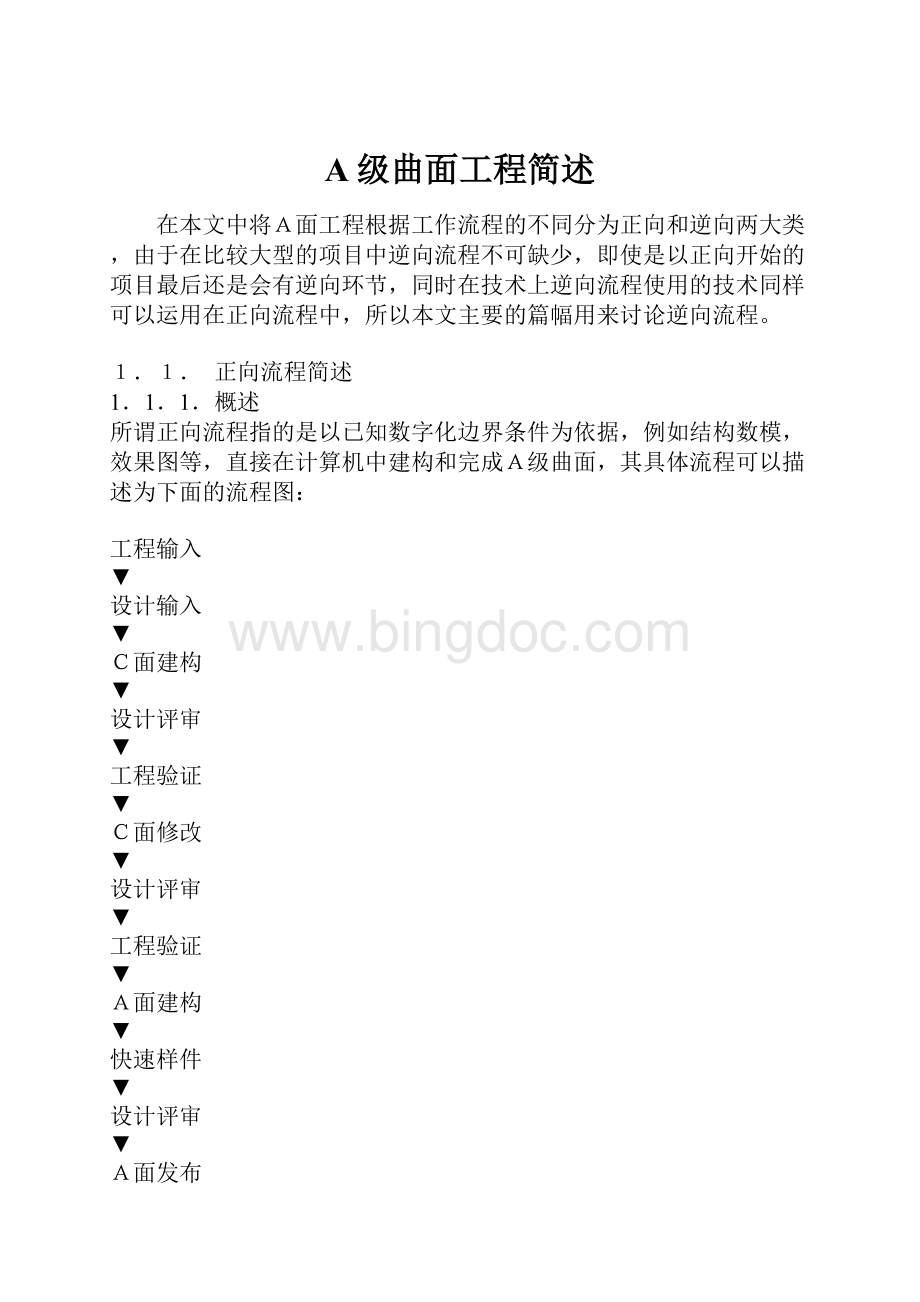
A级曲面工程简述
在本文中将A面工程根据工作流程的不同分为正向和逆向两大类,由于在比较大型的项目中逆向流程不可缺少,即使是以正向开始的项目最后还是会有逆向环节,同时在技术上逆向流程使用的技术同样可以运用在正向流程中,所以本文主要的篇幅用来讨论逆向流程。
1.1. 正向流程简述
1.1.1.概述
所谓正向流程指的是以已知数字化边界条件为依据,例如结构数模,效果图等,直接在计算机中建构和完成A级曲面,其具体流程可以描述为下面的流程图:
工程输入
▼
设计输入
▼
C面建构
▼
设计评审
▼
工程验证
▼
C面修改
▼
设计评审
▼
工程验证
▼
A面建构
▼
快速样件
▼
设计评审
▼
A面发布
▼
设计冻结
1.1.2.正向流程的优势与缺点
正向流程的优点是开发周期短,方案修改方便,开发成本低;缺点是风险具有不可预期性。
1.1.3.什么项目适合采用正向流程
一种情况是当我们对最后的产品的效果比较有把握时,我们总是愿意选择正向流程。
一种情况是我们需要做很多方向的尝试,并且最终的表现形态是样机,以此来试探市场的反应,比如概念车的开发,此时我们通常采用正向流程。
还有一种情况是由于开发周期或者预算的限制使我们无法采用逆向流程时,那么我们就选择正向流程。
1.2. 逆向流程简述
1.2.1.概述
以逆向流程进行的A面工程是整篇文章想要讨论的核心内容,在本文中我们把以某一个实际存在的模型作为建模依据和目的的工程称为逆向工程,这个模型可以是某个实际的产品也可以是油泥模型和样件。
在本文中主要讨论外表面的逆向工程,对于机械零件的逆向工程不作讨论。
逆向工程主要的目的有两个,第一是尽可能的靠近模型,第二是完成的模型有尽可能高的曲面质量。
其具体流程可以描述为下面的流程图:
点云的输入与处理
▼
切断面线
▼
构建基础面
▼
构建主要过渡曲面
▼
构建过渡曲面
▼
分件
▼
曲面质量初步检查
▼
设计评审
▼
工程验证
▼
修改
▼
断差,分缝,圆角
▼
曲面质量检查
▼
数据评审
▼
A面发布
▼
快速样件验证
▼
评审
▼
外表面数据冻结
1.2.2.逆向流程的优势与缺点
逆向流程的优势在于决策者能够最真实直观的看到产品最后的效果,从而将风险降到最低。
逆向流程的缺点是开发周期相对较长,投入相对较大,在后期不容易作大的修改。
1.1.什么项目适合采用逆向流程
一种情况是当我们希望生产的产品与某个既有产品几乎完全一样时,逆向流程是最佳的解决方案。
例如某家汽车配件制造公司希望投产某一名车的前保险杠。
另一种情况是某些较复杂或者投入较大的产品,二唯的图纸和计算机上虚拟的效果可能与真实的情况存在偏差,采用先制作油泥模型或者样品以供决策,在决策确认开发继续进行时,再将模型通过逆向工程转化为数据模型作为开发继续的基础。
例如在汽车开发中经常采用这一开发流程。
在实际的工作中,并不一定是绝对的逆向和正向的工作流程,通常会根据自身的开发条件,采取相互结合的开发流程。
第三章 逆向流程简述
1.1.工作开始的必要条件
逆向流程A面工程开始的必要条件有以下三个主要方面:
第一是设计已经经过评审确认;
第二是工程已经完成基本检查;
第三是模型扫描数据已经完成生成三角面,精简和对位的工作。
A面工程部门需要对以上工作进行检查和确认,在这些条件不具备的情况下如果开始进行A面的设计,那就需要有将来不断反复修改的准备,工作进度也将变的不可预期。
1.2.A面工程常用软件
下面我来简单的介绍一下我所知道的情况,由于各个大的厂家根据自己的产品特点采用了不同的A面标准和上下游环境的不同,于是采用不同的软件来完成A面工程。
例如大众采用ALIAS做设计,用ICEMSURF做A面,这几乎可以代表欧洲各大著名汽车公司的模式,例如奔驰、宝马等等;而通用则直接用ALIAS做设计和A面,意大利的一些设计公司也采用了这种模式;也有设计部门用UG公司的IMAGEWARE做A面;CATIA的A面模块也被用来完成A面工程,在日本和韩国有些设计公司采用这一模式。
以上只是我了解的比较常用的一些软件,当然我相信还有许多是我不了解的,但是应该采用的流程和方法是大致相同的。
本文探讨的内容更加集中在A面工程的本身,并不局限于某种软件,在平时的工作中大家肯定会有自己最熟悉的软件,那么不要因为他有一两个弱点就放弃,最熟悉的软件往往能带来最高的效率和最好的结果,要做的只是找到一个通用的数据转换平台,简单的学几招其他软件的特长,取长补短就行了,在后面章节的介绍中我会和大家讨论这些软件的优势和不足。
2、点云的输入与处理
2.1.点云的输入与检查
比较通用的点云格式是.stl格式,输入后首先要对点云数据进行检查:
首先检查生成的可视化三角面与模型的误差,细节特征的损失程度是否在可接受范围内
。
然后检查数据是否已经经过合适的精简,由于点云数据将占据比较大的资源,所以我们总是希望在保留必要的细节特征的前提下将点云精简到最小。
最后确认数据是否已经对完位,根据特征检查数据的对称情况。
2.2.点云的处理
如果点云数据太大,那么我们可以根据需要将点云分成几个部分单独存放在不同的层中,然后根据需要调用这些层,这样可以减少机器的负担。
3.切断面线
通常我们都会对点云切出断面线,最常用的切法是以X,Y,Z平面根据产品的大小和特征复杂情况按照一定的间距来切出一组断面线,根据软件的不同有些软件是对点来切断面线,有些软件是对三角面切断面线,效果有细微的不同,个人经验对三角面切出的断面线有更好的效果。
有些软件提供了更加自由的断面线的切法,例如可以以一条曲线作为路径来切断面线。
切断面线的作用是为了产生一组反映模型特征的曲线,将我们建构的曲面按同样的方式切出的断面线与点云上提取的断面线比对就可以反映曲面与点云的逼近程度。
4.构建基础面
所有物体都可以看成是六面体的变形与加减,基础面是指构成基本形体的大面,其他特征将堆积在这些基础面上。
基础面不太可能一次性准确到位,通常需要在后续的构建过程中进行调整,所以对构建基础面的要求是快速和尽量完整,这与素描有点相似,我们总是完成大形才去深入细节,整体的工作进度要求均衡,如果在某个细节上扣的太细,那么很可能在发现整体关系要调整时全部推翻以前的工作。
同时基础面的质量又会影响到后续的面的质量,所以对于面的质量来说,基础面有最高的质量要求,例如基础面的连续性精度会影响构建其上的面的精度,并且这种误差会被放大反映出来。
所以无论在开始构建与后续的调整中,基础面的质量都必须时刻得到保证,否则后续的工作都将只是尝试性的,无法作为最后的数据发布。
5、构建主要过渡曲面
主要过渡曲面通常是指基础面之间的过渡曲面,根据调整主要过渡曲面将可以基本上确定基础面是否合适,同时主要过渡曲面又是后续过渡曲面的基础。
在主要过渡曲面的构建过程中我们需要完成大量的调整基础面关系的工作,较高的连续性的要求也主要是在这个过程中,通常这个过程将占据整个工作量的一半以上。
6、构建过渡曲面
较大的倒角和许多的细节特征都可以归为这类曲面,通过调节过渡曲面与点云的逼近程度,进一步的来确定主要曲面与主要过渡曲面的关系。
这个过程需要我们反复的检查与调整。
完成了这个阶段,模型的基本特征已经明确了,曲面质量也基本确定了。
7、分件
根据设计输入进行分件,切出分缝的大小,这个阶段的分缝只是用来看效果的,完成了这一步的工作以后,我们需要对模型的曲面质量作一次全面的检查,通过分件,我们可能会对后续阶段的分面重新作出规划,确定没有不可接受的问题以后,我们将这版数据作为一个重要节点数据发布。
记住保存好这版数据,这将作为后续修改的基础,很多情况是我们往后进展了一大段以后又退回到这版数据,因为这版数据具有最大的修改灵活性。
8、数据评审
总设计将会组织造型与工程部门对数据进行分析,并且进行一次评审会议以确定后续方案,通常会进行一些修改,如果是大的修改,可能会重新进行造型设计,点云也将更新,如果是小的修改,那么我们可以直接在数据上修改。
A级曲面全面介绍!
在整個汽車開發的流程中,有一工程段稱為ClassAEngineering,重點是在確定曲面的品質可以符合A級曲面的要求。
所謂A級曲面的定義,是必須滿足相鄰曲面間之間隙在0.005mm以下(有些汽車廠甚至要求到0.001mm),切率改變(tangencyChange)在0.16度以下,曲率改變(curvaturechange)在0.005度以下,符合這樣的標準才能確保鈑件的環境反射不會有問題。
a-class包括多方面评测标准,比如说反射是不是好看、顺眼等等。
当然,G2可以说是一个基本要求,因为g2以上才有光顺的反射效果。
但是,即使G3了,也未必是a-class,也就是说有时虽然连续,但是面之间出现褶皱,此时就不是a-class
通俗一点说,class-A就必须是G2以上连接。
G3连续的面不一定是CLASS-A曲面。
汽车业界对于aclass要求也有不同的标准,GM要求比TOYOTA,BMW等等要低一些,也就是说gap和angle要求要松一些。
关于A-classsurfaces,涉及曲面的类型的二个基本观点是位置和质量。
位置——所有消费者可见的表面按A-Surface考虑。
汽车的console(副仪表台)属于A-surf,内部结构件则是B-surf。
质量——涉及曲面拓扑关系、位置、切线、曲面边界处的曲率和曲面内部的patch结构。
有一些意见认为“点连续”是C类,切线连续是B类,曲率连续是A类。
而我想更加适当地定义为C0、C1和C2,对应于B样条曲线方程和它的1阶导数(相切=C1)和它2阶导数(曲率=C2)。
因此一个A-surf有可能是曲率不连续的,如果那是设计的意图,甚至有可能切线不连续,如果设计意图是一处折痕或锐边,(而通常注塑或冲压不能有锐边,因此A-suuf一定是切线连续(C1)的)。
第二种思想以汽车公司和白车身制造方面的经验为基础,做出对A-surf更深刻的理解。
他们按独立分类做出了同样的定义。
物理定义:
A-surf是那些在各自的边界上保持曲率连续的曲面。
曲率连续意味着在任何曲面上的任一"点"中沿着边界有同样的曲率半径。
曲面是挺难做到这一点的
切向连续仅是方向的连续而没有半径连续,比如说倒角。
点连续仅仅保证没有缝隙,完全接触。
事实上,切连续的点连续能满足大部分基础工业(航空和航天、造船业、BIW等)。
基于这些应用,通常并无曲率连续的需要。
A-surf首先用于汽车,并在消费类产品中渐增(牙刷,Palm,手机,洗机机、卫生设备等)。
它也是美学的需要。
*点连续(也称为G0连续)在每个表面上生产一次反射,反射线成间断分布。
*切线连续(也称为G1连续)将生产一次完整的表面反射,反射线连续但呈扭曲状。
*曲率连续(也称为G2连续的,Alias可以做到G3!
)将生产横过所有边界的完整的和光滑的反射线。
在老的汽车业有这样一种分类法:
A面,车身外表面,白车身;B面,不重要表面,比如内饰表面;C面,不可见表面。
这其实就是A级曲面的基础。
但是现在随着美学和舒适性的要求日益提高,对汽车内饰件也提到了A-Class的要求。
因而分类随之简化,A面,可见(甚至是可触摸)表面;B面,不可见表面。
这是历史,是由来。
这5中连续性的名称分别叫做:
G0-位置连续,G1-切线连续,G2-曲率连续,G3-曲率变化率连续,G4-曲率变化率的变化率连续
这些术语用来描述曲面的连续性。
曲面连续性可以理解为相互连接的曲面之间过渡的光滑程度。
提高连续性级别可以使表面看起来更加光滑、流畅。
G0-位置连续
图中所示的两组线都是位置连续,他们只是端点重合,而连接处的切线方向和曲率均不一致。
这种连续性的表面看起来会有一个很尖锐的接缝,属于连续性中级别最低的一种。
G1-切线连续
图中所示的两组曲线属于切线连续,他们不仅在连接处端点重合,而且切线方向一致(可以看到相连的两条线段梳子图的刺在接触点位置是在一条直线上的)。
用过其他PC插图软件的用户,比如CorelDraw,实际上通常得到的都是这种连续性的曲线。
这种连续性的表面不会有尖锐的连接接缝,但是由于两种表面在连接处曲率突变,所以在视觉效果上仍然会有很明显的差异。
会有一种表面中断的感觉。
通常用倒角工具生成的过渡面都属于这种连续级别。
因为这些工具通常使用圆周与两个表面切点间的一部分作为倒角面的轮廓线,圆的曲率是固定的,所以结果会产生一个G1连续的表面。
如果想生成更高质量的过渡面,还是要自己动手。
G2-曲率连续
图中的两组曲线属于曲率线续。
顾名思义,他们不但符和上述两种连续性的特征,而且在接点处的曲率也是相同的。
如图中所示,两条曲线相交处的梳子图的刺常度和方向都是一致的(可以为0)。
这种连续性的曲面没有尖锐接缝,也没有曲率的突变,视觉效果光滑流畅,没有突然中断的感觉(可以用斑马线测试)。
这通常是制作光滑表面的最低要求。
也是制作A级面的最低标准。
G3-曲率变化率连续
图中的两组曲线的连续性属于曲率变化率连续。
这种连续级别不仅具有上述连续级别的特征之外,在接点处曲率的变化率也是连续的,这使得曲率的变化更加平滑。
曲率的变化率可以用一个一次方程表示为一条直线。
这种连续级别的表面有比G2更流畅的视觉效果。
但是由于需要用到高阶曲线或需要更多的曲线片断所以通常只用于汽车设计。
G4-曲率变化率的变化率连续
图中的两组曲线的连续级别属于曲率变化率的变化率连续。
“变化率的变化率”似乎听起来比较深奥,实际上可以这样理解,它使曲率的变化率开始缓慢,然后加快,然后再慢慢的结束。
这使得G4连续级别能够提供更加平滑的连续效果。
但是这种连续级别将比G3计算起来更复杂,所以几乎不会在小家电一类的产品设计中出现。
实际上,就算出现了,我们也未必看得出来。
总结一下这几种连续级别。
G0由于使模型产生了锐利的边缘,所以平时都极力避免,甚至想尽办法摆脱这种效果。
不常用
G1由于制作简单,成功率高,而且在某些地方及其实用,比如手机的两个面的相交处就用这种连续级别。
比较常用
G2由于视觉效果非常好,是大家追求的目标,但是这种连续级别的表面并不容易制作(VFX的这些高手们出的题目基本上就是和这种连续级别表面的制作方法拼命的),所以需要大家多多用心练习,这也是Nurbs建模中的一个难点。
这种连续性的表面主要用于制作模型的主面和主要的过渡面。
G3,G4这两种连续级别通常不使用,因为他们的视觉效果和G2几乎相差无几,而且消耗更多的计算资源。
这两种连续级别的优点只有在制作像汽车车体这种大面积、为了得到完美的反光效果而要求表面曲率变化非常平滑的时候才会体现出来。
检测工具---斑马线介绍(也叫做高光测试):
斑马线实际上是模拟一组平行的光源照射到索要检测的表面上所观察到的反光效果。
G0的斑马线在连接处毫不相关,各走各的,线和线之间不连续,通常是错开的。
G1的斑马线虽然在相接处是相连的,但是从一个表面到另一个表面就会发生很大的变形,通常会在相接的地方产生尖锐的拐角。
G2的斑马线则是相连,且在连接处也有一个过渡,通常不会产生尖锐的拐角,也不会错位。
G3,G4的斑马线很难和G2的区分开。
但是要注意,有时候显示的误差也会产生错位或者尖锐的拐角。
注意鉴别哦。
可以调整一下显示精度之后再看。
A级面介绍:
我们对A级曲面是这样理解的
1.轮廓曲面--通常都是A级曲面,这样的曲面通常都要求曲率连续,沿着曲面和相邻的曲面有几乎相同的曲率半径(相差0.05或更小,位置偏差0.001mm或角度相差0.016度。
)
2、A级曲面用高光等高线检测时显亮的曲线--这些曲线应该有一个共同的曲率特征,等高线连续且过度均匀、逐渐的发散或收缩,而不是一下子汇集消失到一点
3、A级曲面上的控制点也应该按一定的规律分布,一行控制点与另一行相邻的控制点的角度变化应该有一定的规律可循,这是画高质量的曲线所必需的
4、A级曲面模型的曲面的边界线又该可以被编辑、移动以生成另外一个曲线,同时这个新生成的曲线可以重新加入曲面来控制区面。
6、贝塞尔曲面的阶次和控制点数目一般应该是六,有时候可能会更高
7、是说关于拔模角度、对称性、间歇以及同相关曲面德关系等都要考虑。
这个要求我们在造型是对相关的工程问题也要予以足够的重视。
8、这是专门就曲率的变化来说的,光是曲率连续是不足以做出classa的曲面的。
还要求曲率的变化本身也是光顺的,实际上就是引出了G3的概念。
当然并不是说classa要求G3,但是比较接近G3的品质对曲面的品质肯定是有好处的。
关于A-classsurfaces,涉及曲面的类型的二个基本观点是位置和质量。
位置——所有消费者可见的表面按A-Surface考虑。
汽车的console(副仪表台)属于A-surf,内部结构件则是B-surf。
质量——涉及曲面拓扑关系、位置、切线、曲面边界处的曲率和曲面内部的patch结构。
有一些意见认为“位置续”是C类,切线连续是B类,曲率连续是A类。
而我想更加适当地定义为G0、G1和G2,对应于B样条曲线方程和它的1阶导数(相切=G1)和它2阶导数(曲率=G2)。
因此一个A-surf有可能是曲率不连续的,如果那是设计的意图,甚至有可能切线不连续,如果设计意图是一处折痕或锐边,(而通常注塑或冲压不能有锐边,因此A-suuf一定是切线连续(G1)的)。
第二种思想以汽车公司和白车身制造方面的经验为基础,做出对A-surf更深刻的理解。
他们按独立分类做出了同样的定义。
物理定义:
A-surf是那些在各自的边界上保持曲率连续的曲面。
曲率连续意味着在任何曲面上的任一"点"中沿着边界有同样的曲率半径。
曲面是挺难做到这一点的
切向连续仅是方向的连续而没有半径连续,比如说倒角。
点连续仅仅保证没有缝隙,完全接触。
事实上,切连续的点连续能满足大部分基础工业(航空和航天、造船业、BIW等)。
基于这些应用,通常并无曲率连续的需要。
A-surf首先用于汽车,并在消费类产品中渐增(牙刷,Palm,手机,洗机机、卫生设备等)。
它也是美学的需要。
*点连续(也称为G0连续)在每个表面上生产一次反射,反射线成间断分布。
*切线连续(也称为G1连续)将生产一次完整的表面反射,反射线连续但呈扭曲状。
*曲率连续(也称为G2连续的,Alias可以做到G3!
)将生产横过所有边界的完整的和光滑的反射线。
在老的汽车业有这样一种分类法:
A面,车身外表面,白车身;B面,不重要表面,比如内饰表面;C面,不可见表面。
这其实就是A级曲面的基础。
但是现在随着美学和舒适性的要求日益提高,对汽车内饰件也提到了A-Class的要求。
因而分类随之简化,A面,可见(甚至是可触摸)表面;B面,不可见表面。
这是历史,是由来。
CLASSA曲面没有十分严格的数学描述也没有十分严格的概念定义
有个等于没有解释的解释:
VERYSIMPLEANDVERYBUEATIFULSURFACE。
1、一般CLASSA的阶次与控制点数目都不多,UV方向大概在6~8个控制点
2、单独一个CLASSA曲面在UV方向都保证曲率的连续性及变化趋势的一致
3、CLASSA曲面之间的连接至少满足切向连续
4、使用多种数学检验方法来检验CLASSA曲面,不应该出现视觉上的瑕疵。
(如使用高光等高线来检验时,等高线连续且过度均匀间隙均匀。
一般不太可能在一个视觉方向上出现多个高光点等)
曲面設計領域[转帖]
曲面設計領域做A级面要很深的功力,也许到家还不知道什么是A级面謂A級曲面的定義,是必須滿足相鄰曲面間之間隙在0.005mm以下(有些汽車廠甚至要求到0.001mm),切率改變(tangencyChange)在0.16度以下,曲率改變(curvaturechange)在0.005度以下,符合這樣的標準才能確保鈑件的環境反射不會有問題。
我是做汽车行业的,做A级面的软件有CATIA,ICEM,SURFACE,PRO/E好象不行,因为曲面的要求比较高,做法当然需要很多步骤。
我相信大家对CATIA都很了解,法国的达梭公司,IBM负责销售与技术支持,CATIA是英文ComputerAidedTri-DimensionalInterfaceApplication的缩写。
是世界上一种主流的CAD/CAE/CAM一体化软件。
在70年代DassaultAviation成为了第一个用户,CATIA也应运而生。
从1982年到1988年,CATIA相继发布了1版本、2版本、3版本,并于1993年发布了功能强大的4版本,现在的CATIA软件分为V4版本和V5版本两个系列。
V4版本应用于UNIX平台,V5版本应用于UNIX和Windows两种平台。
V5版本的开发开始于1994年。
为了使软件能够易学易用,DassaultSystem于94年开始重新开发全新的CATIAV5版本,新的V5版本界面更加友好,功能也日趋强大,并且开创了CAD/CAE/CAM软件的一种全新风格。
法国DassaultAviation是世界著名的航空航天企业。
其产品以幻影2000和阵风战斗机最为著名。
CATIA的产品开发商DassaultSystem成立于1981年。
ATIA是汽车工业的事实标准,是欧洲、北美和亚洲顶尖汽车制造商所用的核心系统。
CATIA在造型风格、车身及引擎设计等方面具有独特的长处,为各种车辆的设计和制造提供了端对端(endtoend)的解决方案。
CATIA涉及产品、加工和人三个关键领域。
CATIA的可伸缩性和并行工程能力可显著缩短产品上市时间。
一级方程式赛车、跑车、轿车、卡车、商用车、有轨电车、地铁列车、高速列车,各种车辆在CATIA上都可以作为数字化产品,在数字化工厂内,通过数字化流程,进行数字化工程实施。
CATIA的技术在汽车工业领域内是无人可及的,并且被各国的汽车零部件供应商所认可。
从近来一些著名汽车制造商所做的采购决定,如Renault、Toyota、Karman、Volvo、Chrysler等,足以证明数字化车辆的发展动态。
Scania是居于世界领先地位的卡车制造商,总部位于瑞典。
其卡车年产量超过50,000辆。
当其他竞争对手的卡车零部件还在25,000个左右时,Scania公司借助于CATIA系统,已经将卡车零部件减少了一半。
现在,Scania公司在整个卡车研制开发过程中,使用更多的分析仿真,以缩短开发周期,提高卡车的性能和维护性。
CATI