数控机床主传动系统设计毕业论文正稿.docx
《数控机床主传动系统设计毕业论文正稿.docx》由会员分享,可在线阅读,更多相关《数控机床主传动系统设计毕业论文正稿.docx(60页珍藏版)》请在冰点文库上搜索。
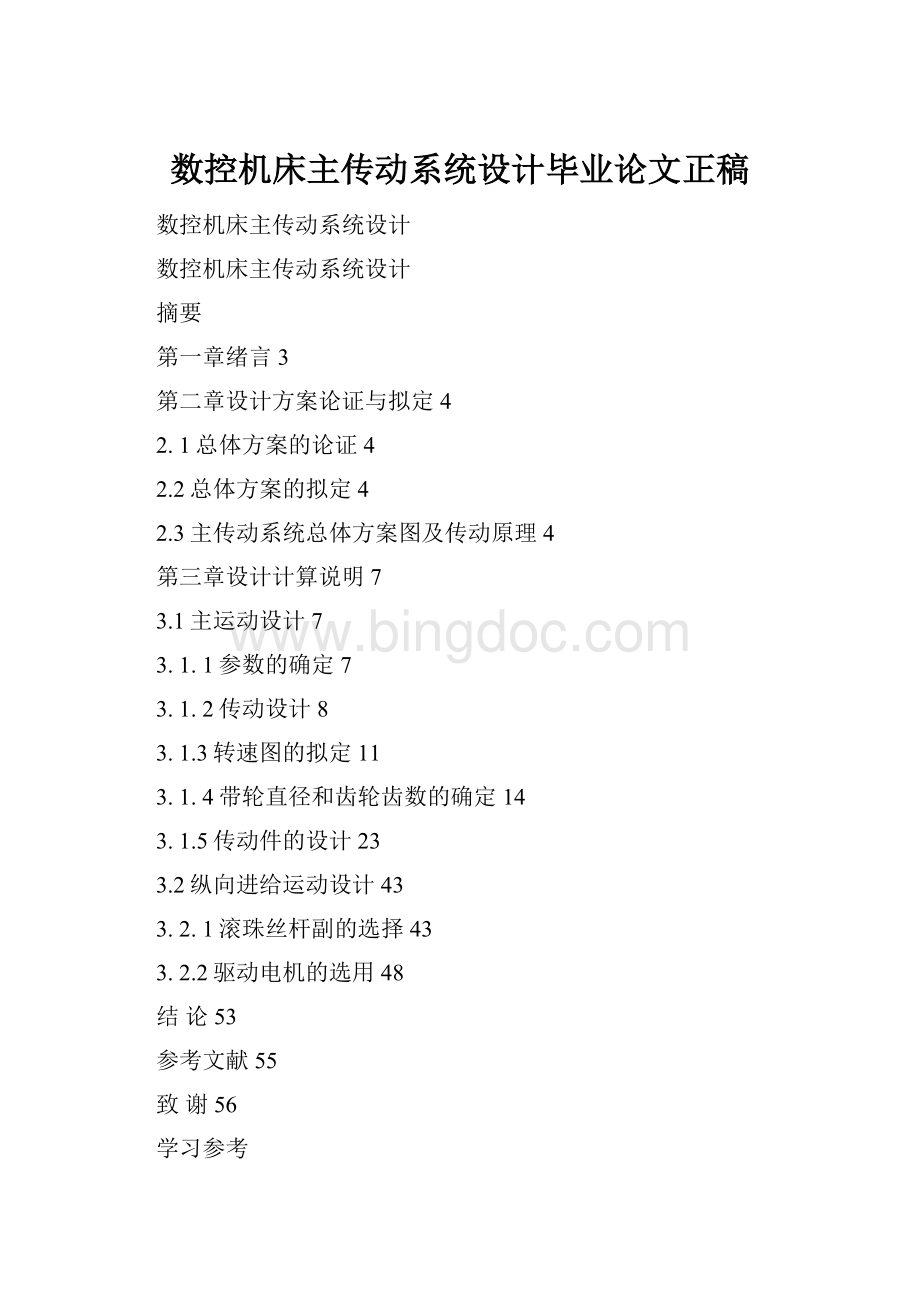
数控机床主传动系统设计毕业论文正稿
数控机床主传动系统设计
数控机床主传动系统设计
摘要
第一章绪言3
第二章设计方案论证与拟定4
2.1总体方案的论证4
2.2总体方案的拟定4
2.3主传动系统总体方案图及传动原理4
第三章设计计算说明7
3.1主运动设计7
3.1.1参数的确定7
3.1.2传动设计8
3.1.3转速图的拟定11
3.1.4带轮直径和齿轮齿数的确定14
3.1.5传动件的设计23
3.2纵向进给运动设计43
3.2.1滚珠丝杆副的选择43
3.2.2驱动电机的选用48
结论53
参考文献55
致谢56
学习参考
第一章绪言
当前的世界已进入信息时代,科技进步口新月异。
生产领域和高科技领域中的竞争II益加剧,产品技术进步、更新换代的步伐不断加快。
现在单件小批最生产的零件已占到机械加工总星的80%以上,而且要求零件的质量更高、精度更高,形状也口趋复杂化,这是摆在机床工业而前的一个突出问题。
为了解决复杂、精密、单件小批量以及形状多变的零件加工问题,一种新型的机床一一数字控制(Numericalcontrol)机床的产生也就是必然的了。
此次设计是数控机床主传动系统的设计,其中包括机床的主运动设计,纵向进给运动设计,还包括齿轮模数计算及校核,主轴刚度的校核等。
第二章总体方案论证与拟定
2.1总体方案的论证
数控乍床是基于数字控制的,它与普通车床不同,因此数控乍床机械结构上应具有以下特点:
1.由于大多数数控车床采用了高性能的主轴,因此,数控机床的机械传动结构得到了简化。
2.为了适应数控车床连续地自动化加工,数控车床机械结构,具有较高的动态刚度,阻尼精度及耐磨性,热变形较小。
3.更多地采用高效传动部件,如滚动丝杆副等。
CNC装置是数控车床的核心,用于实现输入数字化的零件程序,并完成输入信息的存储,数据的变换,插补运算以及实现各种控制功能。
2.2总体方案的拟定
1•根据设计所给出的条件,主运动部分z=18级,即传动方案的选择采用有级变速最岛转速是2000r/min,最低转速是40r/min,0=1.26。
2.纵向进给是一套独立的传动链,它们由步进电机.齿轮副,丝杆螺母副组成,它的传动比应满足机床所要求的。
3.为了保证进给传动精度和半稳性,选用燃擦小、传动效率高的滚珠丝杆螺母副,并应有预紧机构,以提高传动刚度和消除间隙。
齿轮副也应有消除齿侧间隙的机构。
4.采用滚珠丝杆螺母副可以减少导轨间的摩擦阻力,便于匸作台实现精确和微量移动,且润滑方法简单。
2.3主传动系统总体方案图及传动原理
1.数控车床主传动系统图
数控午床的主传动系统见图2.Io整个主传动系统主要由主运动传动链和纵
向进给传动链组成。
2.1总的传动系统图
2.传动原理
主轴部件是机床实现旋转运动的执行件,结构如图2.2所示,其工作原理如下:
交流主轴电动机通过带轮15把运动传给主轴7。
主轴有前后2个支承。
前支承由一个圆锥孔双列圆柱滚子轴承11和一对角接触球轴承10组成,轴承11用来承受径向载荷,两个角接触球轴承一个大口向外(朝向主轴前端),另一个大口向里(朝向主轴后端),用來承受双向的轴向载荷和径向载荷。
前支承轴的间隙用螺母8來支撐。
螺钉12用來防止螺母8回松。
主轴的后支承为圆锥孔双列圆柱滚子轴承14,轴承间隙由螺母1和6来调整。
螺钉17和13是防止螺母1和6回松的。
主轴的支承形式为前端定位,主轴受热膨胀向后伸长。
前后支承所用圆锥孔双列圆柱滚子轴承的支承刚性好,允许的极限转速高。
前支承中的角接触球轴承能承受较大的轴向载荷,且允许的极限转速高。
主轴所采用的支承结构适宜低速大载荷的需要。
主轴的运动经过同步带轮16和3以及同步带2带动脉冲编码器4,使其与主轴同速运转。
脉冲编码器用螺钉5固定在主轴箱体9上。
图2.2主轴部件
第三章设计计算说明
3.1主运动设计
3.1.1参数的确定
1.了解车床的基本情况和特点-一车床的规格系列和类型
1.通用机床的规格和类型有系列型谱作为设计时应该遵照的基础。
因此,对这些呈本知识和资料作些简要介绍。
本次设计中的车床是普通型车床,其品种,用途,性能和结构都是普通型车床所共有的,在此就不作出详细的解释和说明了。
2.车床的主参数(规格尺寸)和基本参数(GB1582-79,JB/Z143-79):
最大的工件回转直径D(mm)是400:
刀架上最大工件回转直径D1大于或等于200;主轴通孔直径d要大于或等于36;主轴头号(JB2521-79)是6;最大工件长度L是750〜2000;主轴转速范围是:
32〜1600:
级数范围是:
1&纵向进给量mm/rO.03〜2.5:
主电机功率(kw)是5.5〜10。
2.参数确定的步骤和方法
1.极限切削速度umax、umin
根据典型的和可能的工艺选取极限切削速度耍考虑:
工序种类、工艺要求刀具和匸件材料等因素。
允许的切速极限参考值如《机床主轴变速箱设计指导书》。
然而,根据本次设计的需要选取的值如下:
取umax=300m/min;
umin=30in/niino
2.主轴的极限转速
计算车床主轴的极限转速时的加工直径,按经验分别取(0.1〜0.2)D和(0.45-0.5)Do由于D二400mm,则主轴极限转速应为:
1000Umax/•o
nmax=r/min3.1
(0.1〜0.2)兀D
=2000r/min;
・lOOOUmm/.门c
nmin=r/min3.2
(0.45〜O・5)/rD
由于转速范围R=—=2000rZmin
11mm40r/min
3.3
=50:
因为级数Z己知:
Z=18级o
现以e=i.26和e=i.4i代入r二
得R=50和355,因此取0=1.26更为合适。
各级转速数列可直接从标准数列表中査出。
标准数列表给出了以e=1.06的从1〜10000的数值,因e二1.26二1.06',从表中找到nmax=2000r/min,就可以每隔3个数值取一个数,得:
2000,1600,1250,1000,800,630,500,400,315,250,200,160,125,100,80,63,50,40。
3.主轴转速级数z和公比0
己知:
匹二心
11inm
Rn=4)且:
z=2ax3b
18二3]X32x29
4.主电机功率一动力参数的确定
合理地确定电机功率N,使用的功率实际情况既能充分的发挥其使用性能,满足生产需要,乂不致使电机经常轻载而降低功率因素。
目前,确定机床电机功率的常用方法很多,而本次设计中采用的是:
估算法,它是一种按典型加工条件(工艺种类、加工材料、刀具、切削用量)进行估算。
根据此方法,中型车床典型重切削条件下的用量:
根据设计书表中推荐的数值:
取P二5.5kw
3.1.2传动设计
1.传动结构式、结构网的选择
结构式、结构网对于分析和选择简单的串联式的传动不失为有用的方法,但对于分析复杂的传动并想由此导出实际的方案,就并非十分有效,可考虑到本次设计的需要可以参考一下这个方案。
确定传动组及各传动组中传动副的数目:
级数为Z的传动系统有若干个顺序的传动组组成,各传动组分别有Zl、Z2、Z3…个传动副。
即
Z=Z1Z2Z33.4
传动副数由于结构的限制以2或3为合适,即变速级数Z应为2和3的因子:
3.5
Z=2ax3b
可以有几种方案,由于篇幅的原因就不一一列出了,在此只把已经选定了的和本次设计所须的正确的方案列出,具体的内容如下:
传动齿轮数目
轴向尺寸
2x(3+3+2)+2x2+1=21个
19b
传动轴数目
6根
操纵机构
简单,两个三联滑移齿轮,一个双联滑移齿轮
2.组传动顺序的安排
18级转速传动系统的传动组,可以安排成:
3x3x2,2x3x3,或3x2x3
选择传动组安排方式时,要考虑到机床主轴变速箱的具体结构、装置和性能。
在I轴上摩擦离合器时,应减小轴向尺寸,第一传动组的传动副不能多,以2为宜,本次设计中就是采用的2,—对是传向正传运动的,另一个是传向反向运动
的。
主轴对加工精度、表面粗糙度的影响大,因此主轴上齿轮少些为好,最后一个传动组的传动副选用2,或者用一个定比传动副。
3.传动系统的扩大顺好的安排
对于18级的传动可以有三种方案,准确的说应该不只有这三个方案,可为了使结构和其他方面不复杂,同时为了满足设计的需要,选择的设计方案是:
18=3[1]3[3]2[9]传动方案的扩大顺序与传动顺序可以一致也可以不一致,在此设计中,扩大顺序和传动顺序就是一致的。
这种扩大顺序和传动顺序一致,称为顺序扩大传动。
4.传动组的变速范围的极限植
齿轮传动副最小传动比uminN丄,最大传动比umax^2,决定了一个传动组
4
的最大变速范围rmax=umax/nminW8。
因此,要按照参考书中所给出的表,淘汰传动组变速范围超过极限值的所有传动方案。
极限传动比及指数X,X值为:
极限传动比指数
1.26
•11
x:
umin=—=—
4
6
X值:
umax=Cx=2
3
*
(x+X)值:
umin=Cx+x=8
9
5.最后扩大传动组的选择
正常连续的顺序扩大的传动(串联式)的传动结构式为:
Z=Z1[1]Z2[Zl]Z3[Z1Z2]
即是:
Z=18=3[1]3[3]2[9]
3.1.3转速图的拟定
运动参数确定以后,主轴各级转速就己知,切削耗能确定了电机功率。
在此基础上,选择电机型号,确定各中间传动轴的转速,这样就拟定主运动的转图,使主运动逐步具体化。
一.主电机的选定
中型机床上,一般都采用三相交流异步电机为动力源,可以在系列中选用。
在选择电机型号时,应按以下步骤进行:
1.电机功率M
根据机床切削能力的要求确定电机功率。
但电机产品的功率已经标准化,因此,按要求应选取相近的标准值。
N=5.5kw
2.电机转速m
异步电机的转速有:
3000、1500、1000、750r/min
在此处选择的是:
na=1500r/min
这个选择是根据电机的转速与主轴最高转速nmax和I轴的转速相近或相宜,以免采用过大的升速或过小的降速传动。
3.双速和多速电机的应用
根据本次设计机床的需要,所选用的是:
双速电机
4.电机的安装和外形
根据电机不同的安装和使用的盂要,有四种不同的外形结构,用的最多的有底座式和发兰式两种。
本次设计的机床所需选用的是外行安装尺寸之一。
具体的安装图可由手册查到。
5.常用电机的资料
根据常用电机所提供的资料,选用:
图3.1Y132S-4电动机
I轴从电机得到运动,经传动系统化成主轴各级转速。
电机转速和主轴最奇转速应相接近。
显然,从传动件在高速运转下恒功率工作时所受扭矩最小來考虑,I轴转速不宜将电机转速下降得太低。
但如果I轴上装有摩擦离合器一类部件时,高速下摩擦损耗、发热都将成为突出矛盾,因此,I轴转速不宜太高。
I轴装有离合器的一些机床的电机、主轴、I轴转速数据:
参考这些数据,可见,车床1轴转速一般取700〜1000r/min。
另外,也要注意到电机与I轴间的传动方式,如用带传动时,降速比不宜太大,否则I轴上带轮太大,和主轴尾端可能干涉。
因此,本次设计选用:
nl=960r/min
二.中间传动轴的转速
对于中间传动轴的转速的考虑原则是:
妥善解决结构尺寸大小与噪音、震动等性能要求之间的矛盾。
中间传动轴的转速较高时(如采用先升后降的传动),中间转动轴和齿轮承受扭矩小,可以使用轴径和齿轮模数小写:
d*VKT、VM,从而可以使用结构紧凑。
但是,这将引起空载功率N空和噪音Lp(—般机床容许噪音应小于85dB)加大:
N空二(3.5da+Cd:
d)KW3.6
式中:
C-一系数,两支承滚动或滑动轴承08.5,三支承滚动轴承C=10:
da-一所有中间轴轴颈的平均直径(mm);
d主一主轴前后轴颈的平均直径(mm);
En—主轴转速(r/min)o
Lp=201og|C](mz)a工n+4.5侖(1一tanB)(inz):
n订一K3.7
(mz)a—所有中间传动齿轮的分度圆直径的半均值mm:
(mz)主一主轴上齿轮的分度圆的平均值mm;
q一一传到主轴所经过的齿轮对数;
P-—-主轴齿轮螺旋角:
C1、K-一系数,根据机床类型及制造水平选取。
我国中型车床、铳床Cl=3.5o车床K=54,铳床K=50.5o
从上诉经验公式可知:
主轴转速n主和中间传动轴的转速和En对机床噪音和发热的关系。
确定中间传动轴的转速时,应结合实际情况作相应修正:
1.功率教大的重切削机床,一般主轴转速较低,中间轴的转速适当取高一些,对减小结构尺寸的效果较明显。
2.速轻载或精密午床,中间轴转速宜取低一些。
3.控制齿轮圆周速度uV8m/s(可用7级精度齿轮)。
在此条件下,可适当选用较高的中间轴转速。
3.齿轮传动比的限制
机床主传动系统中,齿轮副的极限传动比:
1.升速传动中,最大传动比umax^2o过大,容易引起震动和噪音。
2.降速传动中,最小传动比umin^l/4o过小,则使主动齿轮与被动齿轮的直径相差太大,将导致结构庞大。
3.1.4带轮直径和齿轮齿数的确定
根据拟定的转速图上的各传动比,就可以确定带轮直径和齿轮的齿数。
一.带轮直径确定的方法、步骤
1.选择三角型号
一般机床上的都采用三角带。
根据电机转速和功率査图即可确定型号(详情见(〈机床主轴变速箱设计指导〉〉4-1节)。
但图中的解并非只有一种,应使传动带数为3〜5根为宜。
本次设计中所选的带轮型号和带轮的根数如下:
B型带轮
选取3根
2.确定带轮的最小直径Dmin(D小)
各种型号胶带推荐了最小带轮直径,直接査表即可确定。
根据皮带的型号,从教科书〈〈机械设计基础教程〉〉
查表可取:
Dmin=140mm
3.计算大带轮直径D大
根据要求的传动比u和滑功率£确定D大°当带轮为降速时:
三角胶带的滑动率£=2%o
三角传动中,在保证最小包角大于120度的条件下,传动比可取1/7
WuW3。
对中型通用机床,一般取1〜2.5为宜。
因此,
137.2mmWD大343mm
经查表取:
D大=212mm
二.确定齿轮齿数
用计算法或查表法确定齿轮齿数,后者更为简单。
根据要求的传动比u和初步定出的传动齿轮副齿数和Sz,查表即可求出小齿轮齿数。
在本次设计中采用的就是常用传动比的适用齿数(小齿轮)表就见教科书
〈〈机床简明设计手册〉〉。
不过在表中选取的时候应注意以下儿个问题:
学习参考
1.不产生根切。
一般去Zmn^18〜20。
2.保证强度和防止热处理变形过大,齿轮齿根圆到键槽的壁厚6M2mm,—般取6>5mm则zBin^6.5+—,具体的尺寸可参考图。
m
3.同一传动组的各对齿轮副的中心距应该相等。
若莫数相同时,则齿数和亦应相等。
但由于传动比的要求,尤其是在传动中使用了公用齿轮后,常常满足比了上述要求。
机床上可用修正齿轮,在一定范围内调整中心距使其相等。
但修正最不能太大,一般齿数差不能超过3〜4个齿。
4.防止各种碰撞和干涉:
三联滑移齿轮的相邻的齿数差应大于4o应避免齿轮和轴之间相撞,出现以上的情况可以采用相应的措施来补救。
5.在同时满足以上的条件下齿轮齿数的确定已经可以初步定出,具体的各个齿轮齿数可以见传动图上所标写的。
6.确定轴间距:
轴间距是由齿轮齿数和后而计算并且经验算而确定的模数m而确定的,具体的计算值如下(模数和齿轮的齿数而确定的轴间距必须满足以上的儿个条件):
I轴与II轴之间的距离:
取m二2.5mm,由转速图而确定—=0.85
d]=niz
=2.5mmx51
3.8
=127.5nmi
d,=mz
■
=2・5mmx60
=150nmi
齿轮1与2之间的中心距:
=13&75imn
I【轴与【II轴之间的距离:
取m二2.5mm,由转速图而确定的传动比见图,
兰=0.8
48
29
—=0.5
57—.62
53
d3=mz3
=2.5nmix38
=95inm
d4=mz4
=2.5nmix48
=120nmi
3.10
齿轮3与4之间的中心距:
3.11
=107.5mm
I【I轴与IV轴之间的距离:
取m=3.5mm>由转速图而确定的传动比
63
d9=niZj
=3.5nmix54
=139mm
dio=呗
=3.5nmix34
=119nmi
3.12
齿轮9与10Z间的中心距:
189+119
=154nini
3.13
IV轴V轴之间的中心距离:
取m=3.5mm,由转速图而确定的传动比
耳=%
=3.5imnx20
=70nun山6=皿16
=3.5ininx78
=273inm
3.14
_d15+d16
4
_70+273
2-
=171.5111111
3.15
d】9=niz19
=3.511111x33
=115.5nmid20=叫。
=3.5minx33
=115.5nun
主轴到脉冲轴的中心甌取m二3.5mm,传动比i=l
I轴到反转轴VI轴的中心距:
取m=2.5mm>传动比i=1.47
一%+d20
m_
2
115.5+115.52
=115.5imn
3.17
d21=呼】
=2.5nmix50
=125mmd?
?
=HIZ22
=2.5nniix34
=85111111
3.18
3.19
125+85_-2__=10511ml
由齿顶高
hf=(h/+c*)m而取h/=lc"=0.25,可知:
3.20
齿顶高和齿跟高只与所取的模数m有关。
可知取m=2.5mm时,
=l\'m=lx2.5nmi=2.5mm
hf=(h/+c*)m=(1+O.25)x2.5mm=3.125mm
取m=3.5mm时:
B=h/in=1x3.5ium=3.5nmi
hf=(h/+c")m=(1+0.25)x3.5mm=4・375mm
三.主轴转速系列的验算
主轴转速在使用上并不要十分准确,转速稍髙或稍低并无太大影响。
但标牌上标准数列的数值一般也不允许与实际转速相差太大。
由确定的齿轮齿数所得的实际转速与传动设计理论值难以完全相符合,需要
验算主轴各级转速,最大误差不得超过正负10(屮-1)%0即
按公式:
2.21
△n二-2%〜+6%
如果超差,要根据误差的正负以及引起误差的主要环节,垂新调整齿数,使转速数列得到改善。
主运动传动链的传动路线表达式如下:
①140f
->->1—>
①212
(38、
51
―>——>
48
60
33
T1丨T
—
53
VI34
—>vlT——T
29
28
—
(57丿
正转
—>I
反转—Y
54]
34
了65〕
25
TIV—>
33
63
20
39
178丿
149>
—>V住轴)
图3.3主传动路线
所有主轴的详细的校核如下:
输入到II轴的转速n=1440r/minx-^^x—=803.3r/min3.22
21260
1.
2.
3.
4.
5.
6.
7.
8.
9.
10.
11.
nx—x—x—=8O3.3r/minx2.478=1990.58r/min
483433
An=
1990.58-2000
2000
x100%=-0.47%
nx—x—x—=803.3r/minx0.322=258.64r/min
483478
3.24
3.25
An=
25&64—250
250
x100%=3.46%
3.26
3865
nx一x—x—=803・3r/minx0.619=497.58r/min
486333
An=
497.58-500
x100%=-0.48%
500
387520
nx——x—x—=803.3r/minx0.08=64.66r/mill
486378
An=6466~63x100%=2.6%
63
383920
nx——x——x——=803.3r/minx1.24=997.66r/mill
484978
3.27
3.28
3.29
3.30
3.31
An=997.66-1000xl0Q%=_0-23%
1000
383920
nx——x—x——=803・3r/minx0.16=129.65r/mill
484978
A129.65-125—
An=x100%=3.7%
3.32
3.33
125
nx—x—x—=803.3r/minx1.949=1565.6r/mill533433
3.34
3.35
An=1565・6-1600x期%=^Q%
3.36
3.37
3.40
3.41
3.42
3.43
3.44
1600
335470
nx一x—x—=803・3r/minx0.253=203.45r/min
533478
20345-200
△n=x100%=1.7%3.38
200
337565
nx——x—x—=803.3r/minx0.487=391.4r/min3.39
536333
391.4-400
An=x100%=-2.0%
400
332520
nx一x—x—=803.3r/minx0.063=50.86r/min536378
An=5086~50x100%=1.7%
50
333965.
nx一x一x一=803.3r/minx0.977=784.781*/mill
534933
An=x100%=—1.9%
333920
nx——x—X—=803