轧钢厂设备维护保养检修规程Word文档格式.docx
《轧钢厂设备维护保养检修规程Word文档格式.docx》由会员分享,可在线阅读,更多相关《轧钢厂设备维护保养检修规程Word文档格式.docx(68页珍藏版)》请在冰点文库上搜索。
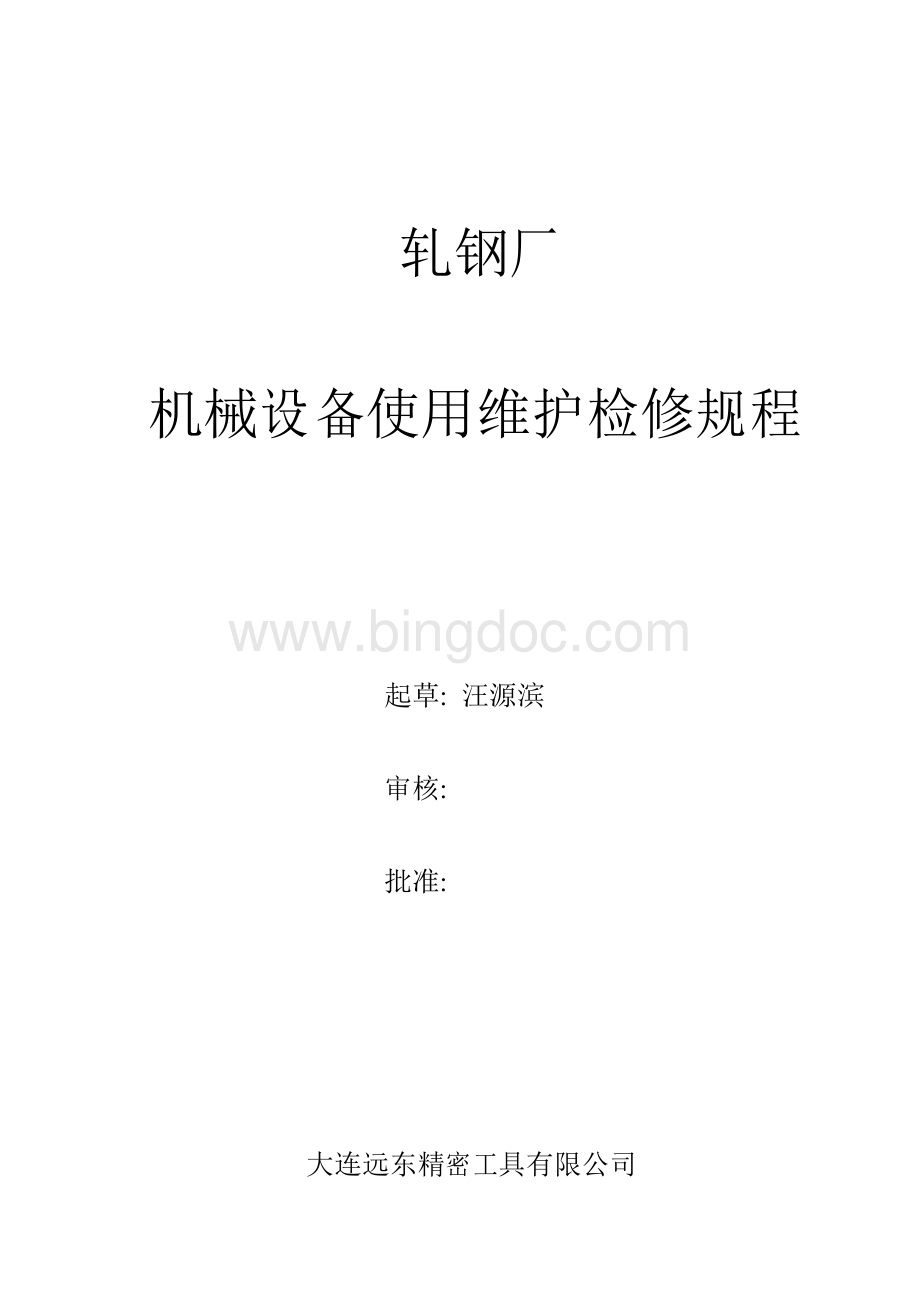
发现设备有异常现象,必须及时将这一情况反馈设备处,设备处负责安排机械或电气维修工处理;
1.2.2维修钳工按要求进行所有设备点检,对本班操作工询问,并做好点检记录。
发现问题及时反馈到设备处;
1.2.3每天对关键工序设备及重点设备进行必要抽查点检,发现问题及时安排处理,同时对各级人员点检状况进行检查,对关键设备隐患及时处理;
1.2.4每周设备处要对全厂设备的运行状况做分析总结,上报厂领导。
1.2.5严格执行设备隐患“闭环管理模式”。
具体如下:
(1)、岗位点检发现设备隐患及时处理和填写交接班记录。
对当班不能处理的隐患,填写班组“设备隐患记录”,并在其“处理安排”栏内填写“已上报”,并填写“设备隐患反馈表”交设
-3-
备处及厂领导,厂领导在班组“设备隐患记录”的结果栏内签收。
(2)、设备处点检发现设备隐患当天及时处理和填写相关记录。
当班不能处理的设备隐患填写设备处“设备隐患记录”,并在其“处理安排”栏内填写清楚安排意见,待到设备隐患处理完后在相应的结果栏内认真填写。
把上报的设备隐患填写到设备处“设备隐患记录”,并在“处理安排”栏内填写清楚安排意见,待到设备隐患处理完后在相应的结果栏内认真填写。
设备处不能安排处理的设备隐患,在其“处理安排”栏内填写“已记录”,并填写“设备隐患反馈表”交主管厂长,进行下步安排。
二、粗轧机组设备使用维护检修规程
1、设备主要性能
序
号
名称
工艺性能
设备参数
1
横列式轧
机
450横列式轧机机组
450轧机三架;
一架三辊,辊身长度1300;
二架三辊,辊身1000;
三架二辊,辊身1000;
机架间采
用万向联轴器联接;
压上压下由齿轮连杆机构组成,丝杠每转一圈,压上压下量为5mm;
轧辊轴向调整
量为左右各20mm。
2
1#2#升降
台
将轧件移送至三辊
轧机上辊缝进行轧制
辊道升降采用偏心轮机构,通过电机减速机驱动;
1#升降台辊子长度1300,2#升降台辊子长度
1000;
3
1#2#移钢
将轧件移送至下一列轧机进行轧制
采用绳轮、拨爪结构,由电机、减速机驱动一根主轴,由主轴带动绳轮及拨爪往复移动。
4
机前机后
辊道
往复传递轧件,完成轧制
由辊道架、辊子、轴承座及盖板组成,电机减速机
驱动辊子正反转。
2、设备使用规程
2.1主轧机启动前的准备工作:
2.1.1主润滑油压力不小于0.35MPa,检查主传动各进油口处油杯进油情况。
2.1.2轧辊冷却水供给正常。
2.1.3检查各辊道减速机润滑油量,及时加注润滑油;
辊道试运转,正反转运转稳定、无故障方可开动主轧机。
2.1.4主轧机开车前,鳄鱼剪、龙门剪必须完成试切动作,无故障方可开动主轧机。
2.1.5所有的选择开关均处于"
允许运行"
或"
接通"
位置;
可控电源已经通电,处于准备完毕,而且电源准备好,指示灯亮;
带联锁的辅助传动系统已运转,且处在允许的条件下;
操作人员发出轧机启动信号。
2.2启动和运转:
按下相应的轧机的"
启动"
按钮。
主轧机启动前必须确认粗轧润滑站开启,各润滑点供油正常;
冷却水开启,水量正常,方可启动主轧机。
2.3轧机的停车
正常的停车:
按下相应轧机的"
停止"
紧急事故停车:
按下"
急停"
故障自动停车:
联锁检测系统工作状态超出极限条件,引起轧机停车。
2.4辊道、升降台、移钢机
-4-
所有的选择开关均处于"
位置。
根据轧制需要控制辊道的启停、正反转;
升降台的上升、下降;
移钢机的移钢。
2.5设备运行过程中注意事项
2.5.1传动部分
电机、减速机与联接机运转过程中出现振动、噪音较大,润滑油供给不足,应立即停车;
检查各部分零部件,找出故障原因;
随时查看轴瓦处温度,温度过高即润滑冷却不到位,应立即停车处理。
2.5.2轧机部分
轧机运转过程中,随时查看轧辊转动情况,是否平稳、无噪音,如发现轧辊轴承出现问题,应立即停车,更换轧辊轴承。
3、设备维护与检修规程
3.1设备维护规程
3.1.1每班必须清扫设备,擦拭机器外表。
3.1.2检查各操作手柄,阀门是否灵活可靠,设备各部位是否良好。
3.1.3检查各润滑部位情况是否处于良好状况。
3.1.4操作者必须按操作规程进行操作,不得违反。
3.1.5检查地脚是否紧固,各部位连接螺栓是否紧固,有无松动。
3.1.6检查减速机以及机列设备的其它各供润滑点的给油润滑情况。
3.1.7检查易损件的磨损情况,及时修复更换。
3.1.8经常检查设备的润滑系统,,水冷系统是否有压力不正常,线路有跑、冒、滴、漏现象,发现问题及时处理。
3.1.9每班交接班时要严格按设备的巡点检制度,对所点检、巡检内容应详细填写点检卡。
3.2设备日常维护保养与定期检修
3.2.1设备日常维护项目与周期
维护项目
班
日
周
月
三个
六个
氧化铁皮和灰尘清理
★
轧辊轴承干油润滑(加注润滑脂)
检查管路有无泄漏
所有螺栓紧固件的紧固
5
辊道减速机润滑油检查与更换
6
主传动减速机、联接机齿轮啮合情况(磨损、接触斑点)
7
轧辊轴承的检查与更换
视轴承具体工作情况而定
3.2.2设备定期检修
-5-
1、
序号
类别
周期
检修内容
大修
两年至四年
1、解体整个减速机、联接机,全部零部件清洗、检查,更换损坏部件。
2、联轴器全部清洗检查,换油。
更换密封圈及磨损严重的零件。
3、连接轴视情况而定,磨损严重需更换。
4、齿轮清洗,检查,磨损严重更换。
中修
一年
1、减速箱开盖检查齿轮侧隙,齿面磨损,轴承间隙与磨损,更换损坏的零部件箱体密封。
2、主电机联轴器,齿表面磨损情况以及密封件磨损情况,有问题换新或修理、清洗更换润滑
脂。
3、万向接轴清洗检查更换损坏的零件。
小修
每周
1、检查各紧固连接件的紧固情况,不准有松动脱落现象。
2、及时检查各部轴承的温度及润滑情况,及时
清洗。
3、检查接手的润滑和磨损情况。
4、检查托架托瓦的磨损情况。
-6-
三、中轧机组设备使用维护检修规程1、设备主要性能
名称
机械设备参数
350轧机/4架320轧机/8架
短应力线式轧机,平立交替布置,中间设有立活套,实现无张力轧制
轧辊规格:
Φ350×
600mmΦ320×
600mm
最大轧制力:
1500KN
最大轧制力矩:
60/50KN·
m移动轨座行程:
670mm
万向接轴:
回转直径:
300mm
最大转矩:
100KN·
m伸缩量:
665mm
夹紧缸:
数量:
4套/台弹簧夹紧力:
85KN/台
活塞直径/杆径:
Φ130/Φ85mm
行程:
9mm
辊缝调整装置装置:
辊缝丝杆螺距:
6mm
压下液压马达转速:
60~150rpm压下减速机速比:
1:
49.016压下速度:
0.24mm/r
中轧机组由12架短应力线轧机组成,平立交替布置,与传统有牌坊轧机相比,它具有轧制能力大、轧机刚度大、轧机的重量和尺寸小,以及结构紧凑、换辊时间短和轧辊轴承使用寿命长等优点。
2.1轧机使用注意事项:
-7-
2.1.1操作者必须了解设备性能。
2.1.2开车前要检查轧机是否处于锁紧状态、平衡状态,确认液压系统无泄漏。
2.1.3开动轧机前要先通知液压站、稀油润滑站,开动相关设备,打开冷却水,风机,检查油温、油压,水量待一切情况正常后,经有关领导同意后,由主操室下达指令后,方可通知开车。
2.1.4开车前,将主轧灯开关合上,当绿灯显示时,主控制人员做好开车准备。
2.1.5开车后必须检查设备运行是否正常,如发现异常时,应立即停车,排除故障后方可重新启车运转。
2.1.6停车过程中应继续空转五分钟,并要减速停车,停车后必须将冷却水关闭好。
2.1.7在移动机架前,必须清扫导轨滑动面的障碍和灰尘,并在轨道上涂抹干油。
2.1.8在设备需要维护检修时,应严格遵守操作牌、停牌制度,保证安全作业。
2.1.9岗位操作人员要对设备经常定点检查。
2.1.10在轧钢人员进行换辊换槽操作时,应先打开锁紧装置,不能过大振动和冲击。
立式轧机在换辊时应注意当轧机移出轧制线后,应通过倾翻装置使轧机由立式转为水平位置后,才可进行下一步操作。
2.4设备运行过程中注意事项
电机、减速机运转过程中出现振动、噪音较大,润滑油供给不足,应立即停车;
检查各部分零部件,找出故障原因;
2.5轧机换孔与换机架操作规程
2.5.1.将轧机上的冷却水管、进出口导卫和导卫梁卸下。
2.5.2启动轧区泵站,夹紧缸松开,确认连接销为插入状态;
立轧机机架未落到移出小车上时,禁止将连接销打开。
2.5.3控制机架横移缸动作完成换孔操作,换孔之后切记将锁紧缸夹紧。
2.5.4换机架时,接上一步动作,平轧机直接将机架推出至底座机械限位处,打开联接销,横移缸退回,使连接轴与轧辊扁头脱离,使用天车将机架吊至维修车间;
立轧机换机架时,将机架
落到移出小车上,横移缸退回,推出移出小车,将机架吊走。
2.6轧机换辊操作规程
2.6.1.正确将轧机吊装到机修间机械手上,紧固锁紧螺栓。
2.6.2.拆下上下轧辊左右两侧的锁紧螺栓。
2.6.3.操作机械手使轧辊左右轴承座分开到最大行程。
2.6.4.检查左右两侧上下轴承座里面的轴承是否完好,完好的要加入适当的润滑脂,损坏的要更换。
2.6.5.吊装一组待装轧辊并放入机械手中。
2.6.6.操纵机械手使新轧辊移动至装辊位置。
2.6.7.操纵机械手使左右两个轴承座合拢到位。
-8-
2.6.8.依次装入轧辊两侧的紧固件。
2.6.9.检查装配好的轧辊是否运转灵活,否则分析原因并处理。
2.6.10.松开轴承座的锁紧螺栓,用天车吊至轧机底座上并锁紧固定。
2.6.11.安装导卫等部件。
2.6.12.在机架上挂上标牌,写清楚轧机的架次、轧制规格及轧辊外径。
2.6.13.将装配好的轧机吊到生产线上备用。
2.6.14.装配好的轧机作立辊轧机使用时,需翻转90度。
将带底座的轧机机架放置在翻转机构的翻转装置上,旋转90度后,将轧机机架吊走。
3、设备维护规程
3.1.8经常检查设备的润滑系统,水冷系统是否有压力不正常,线路有跑、冒、滴、漏现象,发现问题及时处理。
巡点检路线:
联轴器-减速机-万向接轴-接轴托架-液压缸-轧机工作机座
轧机轨座滑道干油润滑
轴承座与压下减速箱干油润滑
联接轴花键干油润滑
鼓形齿联轴器与接轴托架干油
润滑
轧辊轴承干油润滑
传动机构运转情况、轧辊轴承
转动情况
联轴器清洗维护
9
滚动导卫滚子转动情况、导管
磨损情况
10
-9-
11
12
压下螺母、丝杆螺纹的清洗维
护
3.2.2.1检修注意事项:
(1)轧辊轴承压盖不松动,密封不漏油。
(2)轴承无杂音,温度不超过60度。
(3)油路畅通,无跑、冒、滴、漏现象,每班至少检查两次。
(4)压下装置:
1)蜗轮减速机轴承声音正常,转动灵活。
减速机齿轮齿合间隙正常,无异音,振动小。
干油如何很好,不漏油。
各部螺栓紧固,齐全不松动。
2)丝杠、丝母润滑充足,磨损正常,压下螺丝与安全臼无间隙,压下端底部保持清洁。
3)轴向调整螺丝紧固。
4)平衡弹簧调整适量,各横梁无明显变形。
(5)主减速机:
1)设备运转时要求无异音,振动小。
2)轴承及齿轮齿合部位,要求润滑良好。
3)各传动处密封部位要求无泄漏油现象,密封可靠。
4)地脚,箱体连接螺栓无松动。
1)轴承声音正常,传动平稳。
2)无杂音,轴承温度不超过75℃.
3)润滑管路畅通,不漏油,并保持其油量充足,压力正常。
1)如减速箱整体起吊,只允许使用下箱体的吊耳。
(6)联接轴
1)各部螺丝齐全紧固。
2)传动声音正常,轴无明显变形,不得有振动、冲击。
3)滑动灵活,润滑良好,磨损正常。
4)密封罩无变形,无干涉。
(7)联轴器
1)连接螺栓齐全,紧固。
2)传动声音正常,润滑脂充足。
3.2.2.2设备定期检修
1、解体整个减速机,全部零部件清洗、检查,齿轮轴
更换,轴承更换。
更换密封圈及磨损严重的零件。
3、连接轴整体更换。
4、人字齿轮清洗,检查,磨损严重更换。
5、压下装置解体、清洗,更换压下螺母及各垫片。
6、机架锁紧装置拆检液压缸,更换密封件。
1、减速箱开盖检查齿轮侧隙,齿面磨损,轴承间隙与
磨损,更换损坏的零部件箱体密封。
2、检查平立轧机内衬板,磨损严重更换。
3、主电机联轴器,齿表面磨损情况以及密封件磨损情
2、0-
况,有问题换新或修理、清洗更换润滑脂。
4、伸缩接轴及万向接轴清洗检查更换损坏的零件。
5、横移机构清洗检查,更换压下丝母及部分零部件。
6、压下装置解体清洗,更换零件。
1、检查各紧固连接件的紧固情况,不得有松动、脱落
现象。
2、及时检查各部轴承的温度及润滑情况,及时清洗。
3、检查接手的润滑和磨损情况。
四、精轧机组设备使用维护检修规程
1.1预精轧机组
作用:
通过2机架无扭无张力连续轧制,将坯料轧制成满足精轧机组的要求的尺寸及精度。
结构:
机组由2架Φ285轧机组成,平立交替布置,机架间设有立活套;
轧机为悬臂辊环式结构,特点如下:
1.1.1轧辊箱为插入式结构,机架由轧辊箱和齿轮箱组成,轧辊箱插入齿轮箱即为轧机机架。
1.1.2轧辊箱箱体带有一法兰面板用来与齿轮箱连接,箱体内装有偏心套机构用来调整辊缝。
偏心套内装有油膜轴承与轧辊轴,在悬臂的轧辊轴端用锥套固定辊环。
水平机架与立式机架共用一种轧辊箱,可以互换。
1.1.3水平机架的齿轮箱内由输入轴和同步轴工两根带有齿轮的传动轴组成,机架可由一标准减速器调整速比。
1.1.4立式轧机的齿轮箱内比平式轧机多了一对螺旋伞式齿轮,用来改变传动方向和调整速比,其余部分与水平轧机相同;
平立轧机均采用SKF滚动轴承。
1.1.5辊缝的调节是旋转一根带有左、右丝扣和螺母的丝杆,使两组偏心套相对旋转,两轧辊轴的间距随偏心套的偏心相对轧线对称移动而改变辊缝,并保持原有轧线及导位的位置不变。
(1)辊环通过锥套连接在悬臂辊上,用专用的轧辊工具更换辊环。
(2)立式轧机采用地面传动形式。
1.1.6主要技术参数
辊环尺寸:
Φ285/255X95mm
辊环材质:
碳化钨
轧制钢种:
高速合金钢、合金工具钢、不锈钢及其他高合金钢
1.1.7轧辊拆卸专用工具
液压装辊工具:
工作压力40MPa
液压拆辊工具:
工作压力70MPa
1.2精轧机组
采用超重型顶交45度高速线材精轧机组,集中传动。
通过6机架连续微张力轧制,轧制出Φ5.5-10的成品线材,机组保证出口速度为25m/s。
结构:
轧辊箱为插入式结构,悬臂辊环,箱体内装有偏心套机构用来调节辊缝。
轧辊箱与锥箱采用螺栓直接连接,装配时轧辊箱箱体部分伸进锥箱内,使其轧辊轴齿轮分别与锥箱内两个同步齿轮啮合,轧辊箱与锥箱靠定位销定位。
通过轧辊轴末端的止推轴承,有效解决了轧辊轴轴向窜动的问题,保证轧件的尺寸精度。
辊缝的调节是旋转一根带左、右丝扣和螺母的丝杆,使两组偏心套相对旋转,两轧辊轴的
-11-
间距随偏心套相对轧线对称移动而改变辊缝,并保持原有轧线及导位的位置不变。
增速箱传动系统由3个圆柱齿轮及3根传动轴组成,结构简单,安装调整方便。
1.2.1主要性能:
轧机形式;
悬臂辊环式轧机
Φ228.3/Φ205X72mm
机组组成:
Φ230轧机六架、增速箱、大底座、挡水板与防水槽、缓冲箱、保护罩、联轴器等。
1.2.2轧辊拆卸专用工具
工作压力49.5MPa
液压卸辊工具:
工作压力70MPa
2.1使用注意事项:
2.1.1开车前要确认油、水、电、风等系统信号显示正常,各安全保护装置齐全可靠。
2.1.2开车前检查各导卫、水管及辊环安装是否牢固可靠。
2.1.3确认各辊环冷却水管无堵塞现象。
2.1.4开车前检查机组前碎断剪是否工作正常。
2.1.5保证各辊箱无严重漏油。
2.1.6开车前如检查出设备故障应立即处理,检修正常后方可开机。
2.2.正常的操作程序
轧机的启动准备,运转和停车。
2.2.1主轧机启动前的准备工作:
可