结构设计规范.docx
《结构设计规范.docx》由会员分享,可在线阅读,更多相关《结构设计规范.docx(18页珍藏版)》请在冰点文库上搜索。
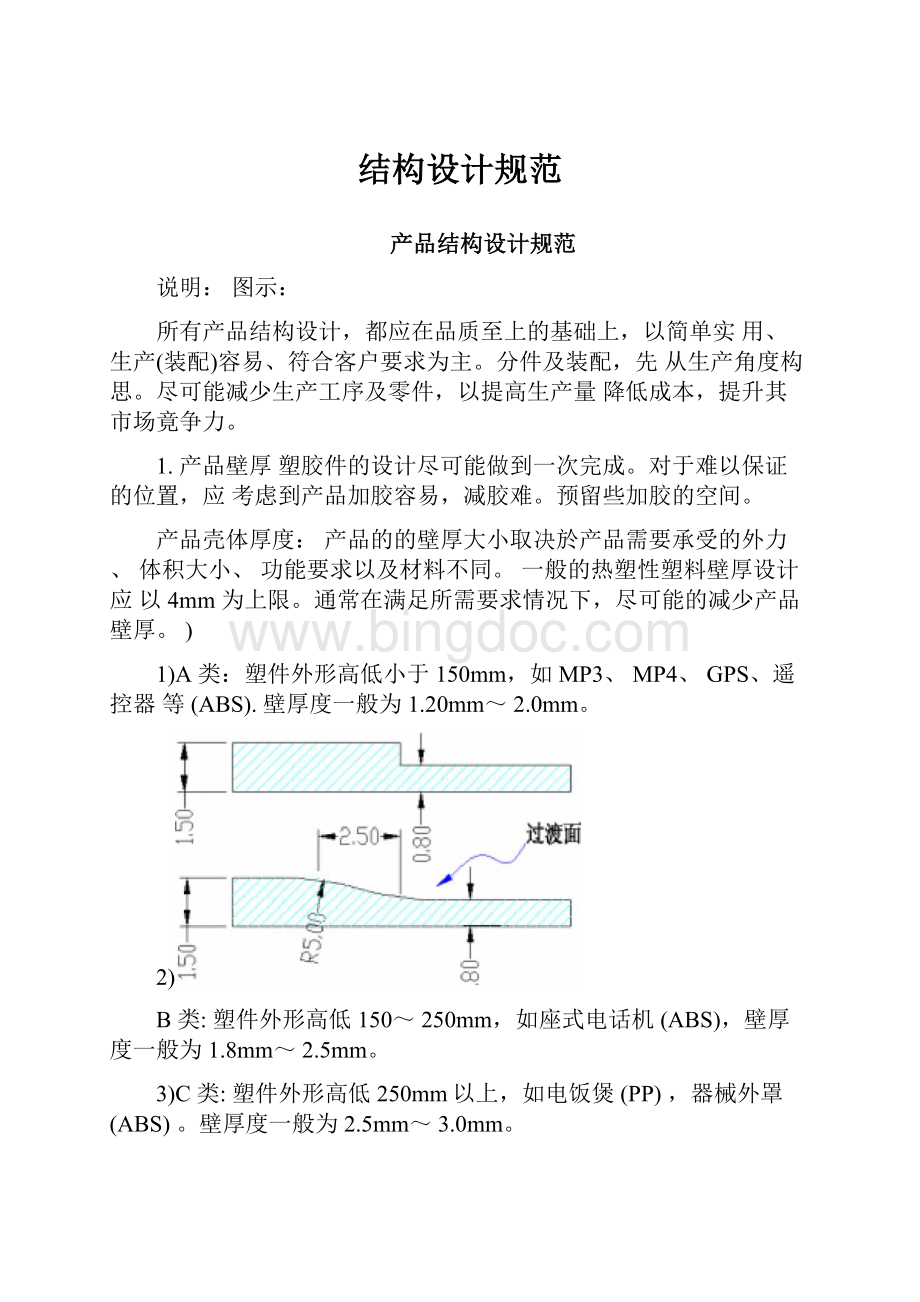
结构设计规范
产品结构设计规范
说明:
图示:
所有产品结构设计,都应在品质至上的基础上,以简单实用、生产(装配)容易、符合客户要求为主。
分件及装配,先从生产角度构思。
尽可能减少生产工序及零件,以提高生产量降低成本,提升其市场竟争力。
1.产品壁厚塑胶件的设计尽可能做到一次完成。
对于难以保证的位置,应考虑到产品加胶容易,减胶难。
预留些加胶的空间。
产品壳体厚度:
产品的的壁厚大小取决於产品需要承受的外力、体积大小、功能要求以及材料不同。
一般的热塑性塑料壁厚设计应以4mm为上限。
通常在满足所需要求情况下,尽可能的减少产品壁厚。
)
1)A类:
塑件外形高低小于150mm,如MP3、MP4、GPS、遥控器等(ABS).壁厚度一般为1.20mm~2.0mm。
2)
B类:
塑件外形高低150~250mm,如座式电话机(ABS),壁厚度一般为1.8mm~2.5mm。
3)C类:
塑件外形高低250mm以上,如电饭煲(PP),器械外罩(ABS)。
壁厚度一般为2.5mm~3.0mm。
4)D类:
对于对壳体有特别要求的产品,如音箱(壁厚对音响效果影象较大),壁厚由3.0mm~4.0mm不等。
5)
图1-1
产品的壁厚直接影响到其寿命及成本,过薄可能会造成制品强度和刚度不足,受力后容易翘曲变形。
成型时流动阻力大,大型复杂的零件难以成形,使用过程容易变形破裂。
过厚则增加材料的成本,成型周期加长,降低生产率,产品表面产生缩水、气泡等不良现象。
6)在产品壁厚设计时应充分考虑其体积大小、材质、使用场合。
参考客户意见等资料。
如果在使用过程中表面受外加力或气压水压等,更须作出适当计算。
7)A类产品通常会有小装饰件,装饰件壁厚为0.8~1.2。
8)不建议使用大件的塑胶装饰件,大装饰件可改用厚为0.6~1.0的不锈钢件。
9)
图1-2
IML件壁厚要求1.2以上,局部壁厚不小于0.8,凹陷的深度不大于0.3。
10)尽可能的保持塑件有均一的壁厚,若是无可避免地产生厚薄胶的渐变,塑件的局部壁厚不小于平均壁厚的一半,而且要求做平缓的过度面加大的导圆角(过度面与局部壁厚3:
1)。
(图1-1)
11)塑件转角位置用圆角过渡(图1-2)。
尖锐的圆角位通常会导致部件有缺陷及应力集中,尖角的位置亦常在电镀过程後引起不希望的物料聚积。
集中应力的地方会在受负载或撞击的时候破裂。
较大的圆角提供了这种缺点的解决方法,不但减低应力集中的因素,且令流动的塑料流得更畅顺和成品脱模时更容易。
圆角是壁厚的0.2~0.6,理想数值是壁厚的0.5。
2.止口:
止口在产品的组合中起到相互之间的定位、加固装配和调整接合线(夹口)的平整的作用。
常用的有单止口和双止口(见图2-1)。
1)大部分产品使用的都是单止口,凸止口宽一般来为壁厚的0.45倍。
高为宽度的1~1.5倍。
(常用高度有0.8mm,1.0mm,1.2mm,1.5mm,2.0mm。
体积大的产品还有3.0mm,4.0mm)。
2)双止口的使用相对会少。
一般用于防水或比较密封和须要用打胶方式固定的产品。
还有胶位厚的产品也常用。
3)凹凸止口的间隙通常单边为0.05mm~0.2mm(常用
有0.05mm,0.08mm,0.10mm,0.15mm)。
4)止口的宽度设计要求不小于0.70mm。
要注意凹止
口底面到产品外表面距离过于单薄而产不良痕迹。
(如图2-2)
5)A类产品侧壁厚要求1.8mm以上,凸止口为0.8x1.0(宽x长)或1.0x1.0。
凹凸止口的间隙为0.05,加3·的拔摸角。
B类产品侧壁厚要求2.3mm以上,凸止口为1.0x1.0
或1.2x1.5。
凹凸止口的间隙为0.08,加3·的拔摸角。
图2-1
图2-2
C类产品侧壁厚要求3.0以上,止口为1.5x1.5或
1.5x2.0。
凹凸止口的间隙为0.15,加3·的拔摸角。
3.装饰线(美观线):
产品的配合装饰线间隙(高)尺寸因其体积的大小而不一。
设计时应考虑装饰线与产品整体的协调。
通常有(0.30mm,0.50mm,0.8mm,1.0mm。
)宽度通常有(0.30mm,0.50mm,1.0mm)。
A类产品装饰线为0.3x0.3。
B类产品装饰线为0.5x0.5。
C类产品装饰线为0.8x0.8。
装饰线与凹凸止口的间隙关系设计如(图3-1)。
图3-1
4.拔模:
1)产品在其出模方向所有与模穴有磨擦的面积都应有拔模角,在结构设计前要详细检查表面有没有无法出模现象。
拔模角在产外观与结构允许的情况下尽可能加大,以方便产品加工生产。
2)对于外部有蚀纹工艺要求产品,跟据蚀纹的粗细和深度拔模角也相应不同(准确数据可参考相应的纹板)。
通常用的为0.5~5度。
特别对于较粗蚀纹,如果角度不够表面可能产生拖花现像。
常用为5~8度,最大的要达10多度。
3)对于表面透明或要求光洁度很好的产品,为防拖花角度通常加大到2~5度。
4)产品某些较单独或较细、容易变形位置,如喇叭网罩、装饰边框、较密集的喇叭孔等。
由于单薄或区域磨擦力集中,脱模时容易粘连前模,使产品拉断或变形。
拔模角通常要加大到5~7度。
(图4-1)
5)如果产品垂直高度比较大表面(表面无蚀纹)或比较高的筋、螺丝柱,为避免拔模后胶过厚表面产生缩水。
其拔模规则为拔模后壁厚比拔模前单边落差不小于0.20mm。
(图4-2)
6)塑件精度要求高,应采用较小的拔摸角。
塑件较高较大,应采用较小的拔摸角,即按落差计算。
塑件形状复杂,不易脱模,应采用较大的拔摸角。
塑件收缩率较大,应采用较大的拔摸角。
塑件壁较厚,收缩也增大,应采用较大的拔摸角。
7)产品表面如果有侧面行位开摸,则行位位置拔摸角可忽略。
5.倒圆角:
1)产品的所有外形棱线必须要导圆角。
特别注意电铸件或电铸按键的棱线
2)倒圆角应不小于R0,30mm,小于R0.30mm会被视为工艺角。
3)壳体的螺丝头沉孔边要加0.3以上的圆角。
4)特别注意电铸件或电铸按键的棱线防后期产生掉漆要加0.2以上的导圆角。
5)零件的所有转角尽可能的设计成圆角或用圆弧过渡。
(如图1-2)以减少应力的集中、提高强度和利于模具填充、脱模。
6)矩形通孔,要在四个拐角处留0.3-0.5的小圆角,避免出模时,由于应力集中,会有拉白拉裂等现象。
6.按钮设计:
1)按钮壁厚通常为1.0mm~1.5.0mm,裙边1.0mmX1.0mm(高)、1.5mmX1.2mm。
(图6-1)
2)按键的设计应考虑其加工和安装的方便性,高度不宜太高,通常体积不大的不高于15.0mm。
3)按键按其色彩、材料、工艺等尽可能的用弹簧筋等方式设计成组合体。
如:
电镀按键为一组,喷漆的为一组,透明的为一组等。
(图6-2)
4)
图6-1
按键弹簧筋尺寸:
宽度:
1.2~2.5
高度:
0.8~1.0
5)
按钮上下行程由所采用的
PCB板元件决定。
通常有:
0.30mm、0.5mm、1.0mm。
导电硅胶行程为
1.0~1.50mm
6)按键与壳体装配通常以壳体上的围筋压住按键裙边的方式来固定,外形若为圆形或椭圆形,要加定位筋。
定位筋高度为按钮行程2倍。
图6-2
7.按键间隙:
按键间隙会跟据按钮大小、表面和配合壳体的
工艺来决定。
1)通常小按键与壳体间隙为单边0.10mm加按键表面
工艺产生的单边厚度加上壳体工艺产生的单边厚
度。
如产品壳体为表喷油,按键为表面喷漆加UV
油。
则按键间隙为:
0.10mm+0.04(壳体喷漆)+0.04(按
键喷漆)+0.03(UV油)。
2)对于体积较大或行程较长按钮,因运动过程中容易
出现卡钮现像(如座式电话机)。
设计时应加大按钮
的拔模角,间隙通常为0.20mm(不包括工艺间隙)(如
图5)。
3)常用工艺间隙:
喷漆,0.03mm~0.05mm
UV油,0.03mm~0.05mm
电镀,0.03mm~0.05mm(水镀,
0.10mm)
4)
8.固定零件装配间隙
1)小零件如LED导光拄、小镜片、装饰件装配间隙单
边为0.05mm或0.07mm。
稍大的因收缩和变形不同
单边为0.10mm或0.15mm。
2)尺寸比较大的零件收缩和变形也大,装配间隙单边
可加大为0.30mm~0.50mm。
3)尺寸不大的硅胶或橡胶零件可设计为零配合,如
USB座橡胶盖。
(图10-1)
9.螺丝柱:
1)产品装配和模具加工中要求精度较高,其座标位置
尽可能的设计为整数,有难度也应精确到0.50(如
51.50或49.50)。
方便易记减少失误。
2)螺丝柱的大小在整套产品中尽量避免太多不同尺
寸,以求生产、装配、螺丝采购的方便和系统性。
3)螺丝柱不宜太高,太高会降低强度。
旁边可以加加
强筋(火箭脚)来加大强度,也可以通过加高螺丝
头沉台来降低螺丝柱高度。
4)
螺丝柱加强筋(火箭脚)高度不应与螺丝柱面相平,
通常是为螺丝柱的0.9。
5)
离壳边较近的螺丝柱加筋与壁相连起来,目的是加
强支柱的强度及使胶料流动更顺畅。
(图9-1)
6)
孔加倒斜角,螺丝头沉台加围筋。
(如图5)
7)
通常螺丝柱的外径是内径的两倍。
但如果这种方式螺
丝柱壁厚等於或超过胶料厚度而在表面产生缩水纹
及高成型应力。
则螺丝柱的厚度应为胶料厚度的
50-70%。
如因此螺丝柱不能提供足够强度,可以加加
强筋,若柱位置接近边壁,则可用一条肋骨将边壁
和柱相互连接来达到加强的效果。
常用的螺丝柱、螺丝头沉台孔、螺丝头孔
螺丝螺丝柱外径
螺丝柱内径
沉台孔
螺丝
头孔
3.506.50
3.00
3.70
6.70
3.005.20
2.40
3.20
6.0
2.604.50
2.20
2.80
5.20
2.304.20
1.90
2.50
4.60
2.004.00
1.70
2.20
4.20
1.703.20
1.30
2.00
3.50
1.403.00
1.00
1.60
2.60
1.002.60
0.70
1.20
2.50
8)
丝头孔如果较深螺丝头孔应尽可能的加大以方便螺
丝刀的操作。
9)
A类产品常用螺丝为
1.0~2.0。
B
类产品常用螺丝为
1.7~3.0。
C类产品常用螺丝为
2.6~4.0。
10)螺丝柱尽可能的避免靠边,靠边柱容易造成表面缩水。
(图9-2)
图9-1
图9-2
10.螺丝盖
1)螺丝盖要求做段差来定位高度如图10-1。
2)避免用大面配合如图10-1上面段有0.05的间隙。
尽量用筋骨做局部零配合,如图10-1的零配合面。
装入口要加C角作安装导入。
3)如果外表面是弧面必须有防呆设计。
4)表面必须有拆卸槽。
(图10-2)
5)螺丝盖的总高度不宜过高,通常是其直径的1.5倍。
11.卡扣
1)
卡扣的设计主要是用在零件间的连接或组合,扣位的组合部份在生产成品的时候同时成型,装配时无须配合其他如螺丝、介子等紧锁配件,只要需组合的两边扣位互相配合扣上即可,提供了一种不但方便快捷而且经济的产品装配方法。
2)按功能来区分,扣位的设计可分为成永久型和可拆卸型两种。
永久型扣位的设计方便装上但不容易拆下,可拆卸型扣位的设计则装上、拆下均十分方便。
可拆卸型扣位的勾形伸出部份附有适当的导入角及导出角方便扣上及分离的动作,如滑动式的电池门扣。
永久型的扣位则只有导入角而没有导出角的设计,所以一经扣上,相接部份即形成自我锁上的状态,不容易拆下。
这是最常用的一些如组合卡扣。
卡扣效果完全取决于塑胶的弹性,设计中特别注意其强度和变形量。
3)卡扣的根部要加圆角以减少应力的集中,防止断裂。
4)卡扣常用的扣合量
A类产品扣合量为0.5~0.8,预留加胶0.2以上。
B类产品装饰线为0.8~1.2。
预留加胶0.5以上。
5)扣位的设计时考虑斜顶的宽度和行程是否足够。
(宽度5.0以上,行程6.0以上。
)
6)卡扣的常用设计数据(A类产品):
①:
公扣厚度,0.8以上,注意弹力和缩水。
②:
公扣直身边,0.5以上。
3:
公扣挂钩高度,1.5以上,如有空间尽量做强。
4:
母扣挂钩高度,1.2以上。
如果公扣较高或强度不够可加加强筋。
公母扣必须要加导入C角。
(如图11-1)
5:
公母扣间隙,0.15以上。
⑥:
公母扣扣合间隙,0.05~0.10。
⑦:
母扣预留加胶空间,0.2以上,如有空间尽量加大。
⑧:
母扣扣合量,0.6以上。
⑨:
公母扣避空空间,如有空间尽量加大。
12.加强筋
1)加强筋在塑胶部件上是不可或缺的功能部份,加强筋有效地增加产品的刚性和强度而无需大幅增加产品切面面积。
对一些经常受到压力、扭力、弯曲的塑胶产品尤其适用。
此外,加强筋更可充当内部流道,有助模腔充填,对帮助塑料流入部件的支节部份很大的作用
2)留意加强筋设计过厚产品表面容易产生缩水纹、变形挠曲等问题。
加强筋厚度通常是相交的胶料壁厚的60%以下。
在一些非决定性的表面肋骨厚度可最多到70%。
3)如果加强筋没连着外壁则高度不应高於胶料厚的三倍,如果太高应加辅助加强筋(图12-1)。
当超过两条加强筋的时侯,加强筋之间的距离尽可能大于於胶料厚度的两倍。
4)在设计时应考虑到塑件的整体强度,在壁厚较弱或受外力的区域应加强筋来增加其强度。
5)塑件上尽可能不要做太多的穿孔,如因结构的需要的穿孔,可以在孔的周边加加强筋以加强塑件的强度。
(图12-2)
12-1
13.PCB的设计
1)为方便装配,每一块PCB都需要在成品的壳身上加上两支定位柱。
而且必须在上下壳身加上一些定位骨夹着PCB,以防止PCB受力而变形。
而定位柱的距离则越远越好,因为这样才可以保持PCB的位置而不会移位
2)PCB与壳身之间至少必须要有0.6mm以上的距离,如果有空间距离尽量留大。
3)常用的PCB厚度:
0.8mm,1.0mm,1.5mm,2.0mm,视乎产品的大小和PCB的尺寸而定,但一般最常用的厚度是1.0mm,1.5mm。
4)LCD屏必须严格按照规格书建立3D文档,包括FPC的位置及长度。
要认识到FPC后期几乎无法修改。
5)PCB的元器件与壳体的最间距:
高度0.2以上,宽0.5以上。
14.电池箱
1)电池与电池之间一定要有塑胶壁定位分隔。
2)电池箱必须使用最大的电池尺寸。
3)因为只有平均料厚的电池门是非常单薄。
所以尽可能的加上加强筋作强化作用。
4)电池门在外观许可时,应加上美工槽。
5)如电池门的位置是在产品的中央,而且在电池门的四周没有凹坑的时候。
必须加上手指位,作方便开启电池门之用。
6)当完成电池门与电池箱的设计后,必须进行电池门的模拟装配过程,检查安装过程是否干涉。
常用塑料制品的最小壁厚及常用壁厚推荐值:
(mm)
塑件材料
最小壁厚
小型件推荐值
中型件推荐值
大型件推荐值
PS
1
1.5
2~2.5
3~4
ABS
1
1.5
2~2.5
3~4
PP
1
1.5
2~2.5
2.5~3.5
PE
0.8
1.2
1.6
2.5~3.5
PC
1
1.8
2.5
3~4.5
POM
1
1.5
1.6
3.~5
PMMA
1
1.5
2.5
4~6.5