多层印制板层压工艺技术及品质控制三.doc
《多层印制板层压工艺技术及品质控制三.doc》由会员分享,可在线阅读,更多相关《多层印制板层压工艺技术及品质控制三.doc(14页珍藏版)》请在冰点文库上搜索。
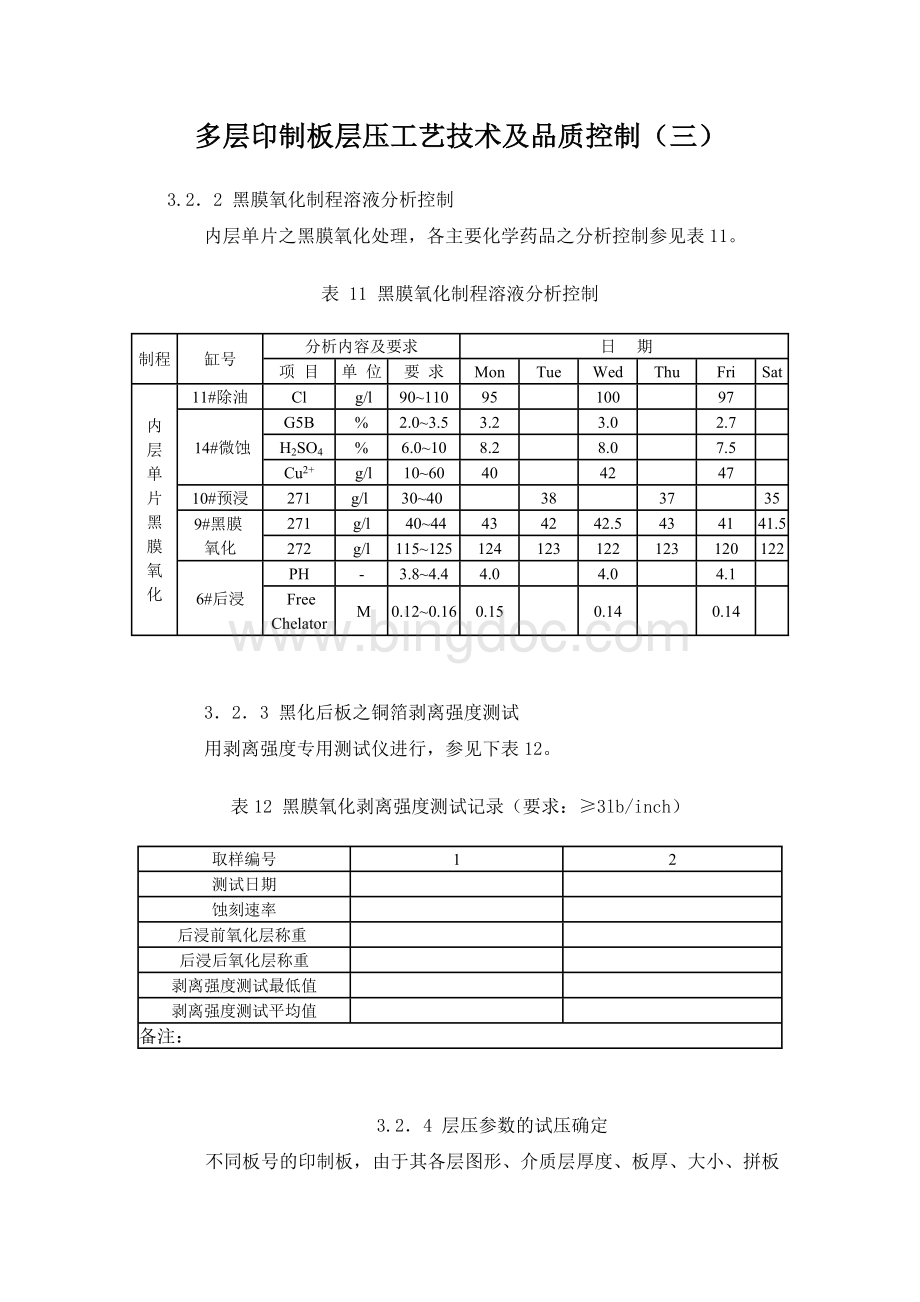
多层印制板层压工艺技术及品质控制(三)
3.2.2黑膜氧化制程溶液分析控制
内层单片之黑膜氧化处理,各主要化学药品之分析控制参见表11。
表11黑膜氧化制程溶液分析控制
制程
缸号
分析内容及要求
日 期
项目
单位
要求
Mon
Tue
Wed
Thu
Fri
Sat
内
层
单
片
黑
膜
氧
化
11#除油
Cl
g/l
90~110
95
100
97
14#微蚀
G5B
%
2.0~3.5
3.2
3.0
2.7
H2SO4
%
6.0~10
8.2
8.0
7.5
Cu2+
g/l
10~60
40
42
47
10#预浸
271
g/l
30~40
38
37
35
9#黑膜
氧化
271
g/l
40~44
43
42
42.5
43
41
41.5
272
g/l
115~125
124
123
122
123
120
122
6#后浸
PH
-
3.8~4.4
4.0
4.0
4.1
FreeChelator
M
0.12~0.16
0.15
0.14
0.14
3.2.3黑化后板之铜箔剥离强度测试
用剥离强度专用测试仪进行,参见下表12。
表12黑膜氧化剥离强度测试记录(要求:
≥3lb/inch)
取样编号
1
2
测试日期
蚀刻速率
后浸前氧化层称重
后浸后氧化层称重
剥离强度测试最低值
剥离强度测试平均值
备注:
3.2.4层压参数的试压确定
不同板号的印制板,由于其各层图形、介质层厚度、板厚、大小、拼板方式、每BOOK压板数及所用压机等诸多因素的差异,在正式生产前,需进行试压板操作,以确定其最佳层压参数。
具体操作步骤如下:
(1)排板时用两根带有K插头的温度感应线,分别接至一载盘的最上层和中间层之板边内,与半固化片相接触。
感应线之另一头,需引出压机外,并与多功能温度测试仪相连,便于随时度量温度;
(2)根据每BOOK压制层数、待压板之面积及厚度等要求,按规定分别预设每段压盘温度、压力和时间;
(3)进行试压操作,按一定间隔时间记录温度。
以下几点必须注意:
①试压过程中,中间层温度在80~130℃时,载盘最上层和中间层的温差不能超过25℃、温升速率不能超过1.3~5℃/min(可通过调整牛皮纸数量、压盘温度等);
②温度达85±5℃时,定低压转中压的时间、温度达110±5℃时,定中压转高压的时间;
③在试板压制过程中,中间层的温度须于170℃或以上更高温度保持20分钟以上;
④填写试压板记录,参见下表13。
表13试压板操作记录
板 号:
排版方式:
牛皮纸数量:
试压日期:
时间min
温度(℃)
压力psi
时间min
温度(℃)
压力psi
时间min
温度(℃)
压力psi
上
中
上
中
上
中
0
36
33
36
34
120
112
270
68
175
173
360
2
54
40
36
36
121
115
360
70
179
175
360
4
60
46
36
38
123
118
360
72
181
177
360
6
69
50
36
40
126
122
360
74
183
179
360
8
70
54
36
42
129
125
360
76
185
181
360
10
75
58
36
44
132
127
360
78
187
182
360
12
80
62
36
46
135
132
360
80
189
183
360
14
83
67
36
48
138
136
360
82
191
185
360
16
87
70
36
50
143
140
360
84
192
187
360
18
90
76
36
52
146
143
360
86
193
188
360
20
93
80
36
54
148
148
360
88
194
189
360
22
97
83
36
56
153
152
360
90
195
190
360
24
102
88
270
58
157
155
360
92
196
191
36
26
106
94
270
60
162
159
360
94
结束
28
110
99
270
62
165
163
360
96
30
114
104
270
64
168
167
360
98
32
118
109
270
66
171
170
360
100
(4)将经以上参数压制的多层印制板,按质量要求进行检测,结果参见下表14。
表14试板压制后检测记录
编号
检测项目
合格要求
检测结果(mil)
最 小
最 大
平 均
1
成品板总厚度
52.10~64.80mil
56.10
58.90
57.60
2
半固化片厚度
6.70~8.20min
7.36
7.53
7.45
3
中心介质层厚度
36.00~44.00min
38.90
40.40
39.70
4
外层铜箔厚度
0.7±0.07mil
-
-
0.72
5
内层铜箔厚度
1.40±0.14mil
-
-
1.37
6
热应力试验
无白点、分层、烧焦
板面正常、无左述缺陷
7
蚀刻铜后板面
无白点、分层
板面正常、无左述缺陷
8
收缩系数
±3mil
2.6mil
结论:
合格
备注:
(5)通过上述试板压制操作,得出该板号之压制参数。
参见下表15。
表15排板及层压工作指示
印制板号码:
排板方式:
板厚要求:
牛皮纸数量:
压制步骤
1
2
3
4
5
6
7
压盘温度(℃)
130
150
170
190
200
200
130
压制压力(PSI)
36
270
270
360
360
360
36
层压时间(MIN)
23
7
6
20
14
20
2
备注:
3.2.5层压板之铜箔剥离强度测试
选取层压后之4层板和6层板分别进行表面铜箔与半固化片之结合强度测试,参见表16。
表16铜箔剥离强度测试记录(要求:
≥6lb/inch)
试 样
四层板
六层板
测试日期
产品代码
工作单号
批次号
结果(lb/inch)
备注:
3.2.6层压板玻璃化转变温度(Tg)测试
通过DSC(扫描差热分析法)进行层压板玻璃化转变温度的测定,参见图三。
测试结果记录格式见下表17。
图三Tg测试曲线示意
表17多层印制板Tg测试记录(要求:
≥130℃;固化度≥95%)
产品代码
工作单号
批次号
Tg1
Tg2
Tg1/Tg2
备注:
3.2.7层压前后尺寸改变测定(参见下表18)
表18层压和前后尺寸稳定性测试记录(要求:
±0.05%)
产品代码
尺 寸
内层蚀刻后
层压操作后
结 果
A
材料描述
B
C
D
备注:
3.2.8内层单片黑化后表面离子沾污测试质量控制
内层单片黑化后,层压操作前表面离子沾污测试,对多层印制板压制后之印制板的绝缘等电气性能很重要,要求6.45μgNaCl/in2。
其方法如下:
(1)按要求于内层单片黑化线之出口处取板;
(2)用Omegameter600SMD专用测试仪进行表面离子污染清洁度测试。
参见表19。
表19内层单片黑化后表面离子沾污测试(工作周:
)
日期
Mon
Tue
Wed
Thu
Fri
Sat
P/N
W/O
Value(μg/in2)
3.2.9常用半固化片的温湿度控制
半固化片的贮存条件,将直接影响到其使用寿命。
其要求参见下表20。
表20各类半固化片贮存条件
半固化片种类
1080
2116
7628
贮存温度
4.5~21℃
4.5~21℃
4.5~21℃
贮存湿度
RH30~50%
RH30~50%
RH30~50%
有效保质期
3个月
3个月
3个月
备注:
若收货时距生产时间已超过3个月,则贮存期为6个月扣除由生产至收货这段时间。
3.2.10排板制作场所净化程度的控制
排板制作场所的净化对多层印制板的制作质量有很大影响。
需进行净化程度读数测定控制的主要有预排板间和排板间。
要求10000级净化程度,也即每立方英尺范围内,直径大于或等于5μm的灰尘颗粒数≤65。
可通过专用仪器“LASERPARTICLECOUNTER(ModelNo.227A”进行度量,要求每周读取一次。
参见表21。
表21排板制作场所灰尘颗粒读数控制(工作周:
)
测试位置
日 期
测试时间
灰尘颗粒数N
预排板间
排板间
此外,在条件允许的前提下,半固化片裁切间也需进行净化处理。
3.2.11多层板排板、层压操作过程控制记录(参见下表22)
表22多层印制板排板、层压过程控制表
压制
板号
生产
数量
黑化
时间
排板
方式
面积
Prepreg类型
牛皮纸数量
压板
时间
压制
温度
压力
大小
真空
情况
压机
号码
操作者签名:
备注 :
3.2.12多层印制板制作的统计式工序过程控制(SPC)
统计式工序过程控制是质量管理的重要途径。
它是由工艺技术部门确定工艺参数的最高和最低控制极限,有关人员收集操作过程收据,绘制成SPC图,反馈至技术部门。
技术部门根据SPC图,分析工序的工艺控制状态和能力,对工艺参数失控的工序进行分析,提出相应之改正措施。
多层印制板层压制作工序需进行SPC控制的项目主要有:
1.黑膜氧化工序:
(1)黑化后板之铜箔剥离强度控制(X/MR图),每周进行一次;
(2)黑膜氧化速率控制(X/RM图),每日进行一次;
(3)后浸槽液之pH控制(X/RM图),每日进行一次;
(4)黑膜氧化制作缺陷分析,每周进行一次。
2.排板及层压工序:
(1)四及六层板之铜箔剥离强度控制(X/MR图),每周进行一次;
(2)麻点和压痕分析控制(P—chart),每日进行一次;
(3)排板及层压制作缺陷分析,每周进行一次。
3.层压后工序:
(1)半自动法定位孔制作位置精度控制(X/RM图),每日进行一次;
(2)全自动法定位孔制作位置精度控制(X/RM图),每日进行一次;
(3)缺陷分析,每周进行一次。
统计上一周各工序制作缺陷种类及数量,与总板数进行比较;同时,比较各缺陷所占比例。
然后制作成相应图表,于各工序制作场所进行张贴,便于相关工序生产员工了解上周发生之制作缺陷,及时采取措施加以跟进,减少或避免同类缺陷的再次产生。
3.2.13多层印制板定位孔制作及层间重合度的测定/判定
1.多层印制板定位孔制作
多层印制板之定位孔制作分为依靠熟练操作员工和依赖先进仪器两种方式。
前者,需先铣去定位孔位置表面之铜箔,然后进行钻定位孔操作。
该法劳动强度高,生产效率较低,且质量难以得到保证。
目前,各多层印制板生产厂家普遍采用较先进的仪器设备,以下对这两种方法将作简单介绍:
(1)由熟练工人进行,采用上下光束对准内层定位孔标靶图形,进行定位孔之冲孔操作:
(2)C.C.D自动钻靶机。
定位孔钻制位置精度≤3mil,每钻3000次,需更换新的φ3.175mm之钻嘴:
(3)OPTIMIZER自动钻定位孔机。
对于较薄或较厚之板,当采用人工下光束对准冲定位孔法无法操作或质量难以保证时使用;
(4)日本MOTORO'S公司提供的X-rayDX-2A钻孔机。
该机加工之板面尺寸达到610×700mm,加工板厚度为0.1—5.0mm,钻孔孔径为由φ0.35~φ6.1mm。
2.多层印制板层间重合度测定/判定
多层印制板之层间重合度将直接影响多层印制板的制作质量,它是衡量层压制作水平高低的一项重要指标。
一般可通过以下几种方法来测定或判定:
(1)通过选取附联板图形,制作金相切片,利用金相显微镜读取有关数据,计算出层间重合度的大小。
该法需时较长,且为间接判定,对板面较大之多层印制板,尚需考虑附联板的选取位置等因素。
(2)GlenbrookTechnologiesInc.推出的“RTX-113”实时X射线检测系统(Real—TimeX-raylnspectionSystems)。
使用该设备,不但能进行多层印制板层间重合度的测定,而且能满足自动化生产所需的如钻孔位置精度判定。
(3)日本MURAKI有限公司生产的供多层板所用之X—射线双主轴自动量度及钻孔机(型号:
MMX-880)。
它可用来显示钻孔的精确度、层间重合度的测定成判定,而且对亏缺的图案也可成功进行钻孔。
其具有以下特点:
①同时显示两个目标,使固定更容易;
②将印制板钳在桌面后,更易得到高精度之量度及钻孔;
②第三孔也可于两个钻孔之上的90度位置得到,或于目标的中心点钻孔得到;
④自动补偿功能使两主轴保持高度位置准确性;
⑤若预设了可接受的距离和误差,钻孔便只对范围内的印制板进行操作。
3.2.14多层印制板生产中,提高层压生产效率之途径
根据各类型板的生产数量,进行一定的工艺试验,在保证多层印制板层压质量的前提下,适当改变排板方式、调整层压参数,可提高层压生产效率。
1.为满足层压工艺条件之非生产板的使用:
此处以800T真空压合机为例。
该机为6个BOOK,层压用钢板尺寸为36”×48”,按工艺要求每BOOK之压板张数:
8张≤每BOOK≤9张。
(1)DUMMY板的使用:
尽管受多层印制板生产设备的制约,但为提高生产效率,一般均采用拼板生产,最大尺寸为18”×24”。
当排板过程中,遇到生产板数量不够时,为保证层压后多层板之质量,往往采用DUMMY板作为替代板进行层压操作。
DUMMY板的具体制作及要求如下:
①所用板厚度与正式生产板厚度之差≤3mil;
②外形尺寸大小与生产板相同;
②DUMMY板需切角进行标识,以便层压后进行拆板时,能与生产板加以区分。
(2)添加59mil辅助板:
59mil辅助板之尺寸为36”×48”。
按工艺要求,每BOOK中待压板的数量为8张和9张可一同进行压制。
由于受生产板数量的制约,当每BOOK中待压板的数量不足8张时,需用59mil辅助板进行替代层压。
具体添加数量为:
7十1,6+2,5+3(加号后为59mil辅助板之添加数量)。
2.改变排板方式,提高层压效率:
(1)排板方式的改变:
如某型号板,其拼板后尺寸为15”×21”,原采取四拼方式进行层压操作,相应之半固化片下料尺寸为31”×49.50”。
现改为五块拼板方式,相应之半固化片下料尺寸为37”×49.50”。
参见下图四。
原排板方式
现排板方式
图四排板方式改变示意
(2)层压参数的改变:
由于排板方式由原来4块板/层改变为5块板/层,造成压板面积增大,故层压之初段压力和末段压力也需相应进行调整,具体为:
由原来之13/65kg/cm2增加至16/81kg/cm2。
3.多层板层数相同、板号不同之共同压制:
经工艺试验,在保证层压后板质量的前提下,该情形下板得以一同压制的条件为:
①两种板号多层板层压所用程式一样;
②所用末段压力与原各自之末段压力之差≤5kg/cm2。
如某种A板号之4层板,其层压所用末段压力为79kg/cm2;而某种B板号之4层板,其层压所用末段压力为80kg/cm2。
经计算:
(79+89)/2=84kg/cm2,而89-84=84-79=5kg/cm2,符合≤5kg/cm2要求。
结论:
采用末段压力84/cm2可使A、B板一同层压。
4.多层板层数不同、板号不同、层压所用程式相同之共同压制:
在该种情形下,往往采用改变某种板之排板方式,从而达到改变层压压力来实现共同压制的目的。
如某种C板号之8层板,其层压所用压力为18/89kg/cm2;某种D板号之6层板,其层压所用压力为18/90kg/cm2;而某种E板号之8层板,其层压所用压力为15/77kg/cm2。
由上述三种型号板之层压所用压力可看出:
C型号板和D型号板可一同压制,而E型号板与前两种板不可一同压制。
解决办法为:
通过改变E型号板之排板方式,来达到三者共同压制的目的。
(经改变E型号板的排板方式后,其层压所用压力由15/77kg/cm2变为18/89kg/cm2。
)三种型号板之排板方式参见下图五。
C型号板排板方式
D型号板排板方式
E型号板排板方式
图五 C、D、E型号板排板方式示意
5.多层板层数不同、板号不同、层压所用程式不同之共同压制:
该情形下,经工艺试验,在保证层压后板之质量的前提下,也可一同压制。
例如:
某型号四层板F共257块,另有某型号六层板G共5块。
F板为每层六拼,G板为每层5拼。
从工艺层压指示上看,F板采用程式3(转压时间36min),G板采用程式6(转压时间38min);但两种板之Cycletime均为140min。
按工艺要求:
4层和6层板,8或9Shee/BOOK可一同压制。
在工艺试验的基础上,决定采用F板之层压程式(程式3)进行压制,相应之排板方式如下:
BOOK1~BOOK3,每BOOK9层;BOOK4,每BOOK8层(可加一层59mil辅助板);BOOK5,每BOOK9层(其中F板8层十切角DUMMY板一块,G板一层5块)。
3.2.15多层印制板层压制作后板之缺陷成因分析及对策
多层印制板进行层压操作后,所得印制板会出现各种各样的问题,只有认真分析其产生之原因,才能及时采取纠正措施,防止类似问题的再次出现,最终达到提高多层印制板层压制作质量的目的。
表23层压缺陷成因分析及相应对策
层压缺陷
产生原因
表现形式
相应对策
1、层压后板发生气泡或起泡现象
①粘结表面不干净;
②挥发物含量偏高;
③半固化片流动性差;
④预压压力偏低;
⑤板温偏低;
⑥树脂动态粘度高,施全压时间较迟;
⑦温度偏高、预压时间偏长。
①微小气泡群集;
②严重时,可见局部层间分离。
①加强粘结表面清洁处理;
②降低预压压力和温升速率;
③更换半固化片或提高预压压力;
④适当提高预压压力;
⑤检查、调整热模温度;
⑥协调压力、温度和流动性三者间关系;
⑦适当降温、提高预压压力或缩短预压周期。
2、板面凹坑、树脂粘附现象
①排板造成铜箔表面有半固化片碎屑;
②脱模材料上粘有半固化片碎屑或树脂残留;
③由于净化不够所造成排板时杂物颗粒或灰尘于铜箔表面的沉积;
④操作人员着工作服不当造成头发及其他异物落在铜箔表面。
①表面有凹坑、指甲痕印但未穿透铜箔;
②表面局部被树脂覆盖。
①改变排板方式,减少铜箔表面沾有半固化片碎屑的机会;
②加强脱模材料之表面清洁,尤其是树脂残留;
③提高排板间的净化层度;
④加强操作人员的净化着装管理。
3、树脂含量不足或局部缺胶现象
①半固化片树脂含量低;
②半固化片树脂凝胶化时间长;
③树脂流动度过高;
④预压压力偏高;
⑤施全压时机不对。
①外观呈白色;
②局部显露玻璃布织纹。
①调整预压压力和温度;
②调整预压压力和温度,调整预压时间;
③适当降低层压温度或压力;
④降低预压压力;
⑤压制过程中,注意观察压力变化和温升情况,并仔细观察树脂的流动状态,调整施全压起始时间。
4、板厚不均现象
①同一BOOK内的层压板总厚度不同;
②同一层中各待压板厚度差大;
③热压模板之平行度差;
④待压板摆放位置偏离中心位置;
⑤内层单片四周边之阻流块设置不合理。
①层压后板之板厚不一致
①调整使其总厚度一致;
②选用厚度差小的覆铜板;
③调整热压模板平行度,并限制其多余的自由度;
④注意放置叠层于热压模板的中心区域;
⑤内层板成品加工框线外应设计成交叉或“梅花状”阻流块。
5、层压后板出现超厚或厚度不够现象
①所填半固化片数量不对;②凝胶化时间太短或太长;③预压所用压力不足或太大。
①经测量,板厚超过要求上限或低于要求之下限。
①检查排板记录;
②测定半固化片的特性指标,调整层压参数或更换半固化片;
③提高预压压力或减小预压压力。
6、层压后板出现翘曲现象
①内层图形设计为非对称性结构;
②半固化片与内层单片的下料方式不一致;
③排板时,半固化片的非对称或非镜向放置;
④内层单片加工前未进行预烘老化处理;
⑤半固化片于层压