预分解窑结皮机理研究.docx
《预分解窑结皮机理研究.docx》由会员分享,可在线阅读,更多相关《预分解窑结皮机理研究.docx(12页珍藏版)》请在冰点文库上搜索。
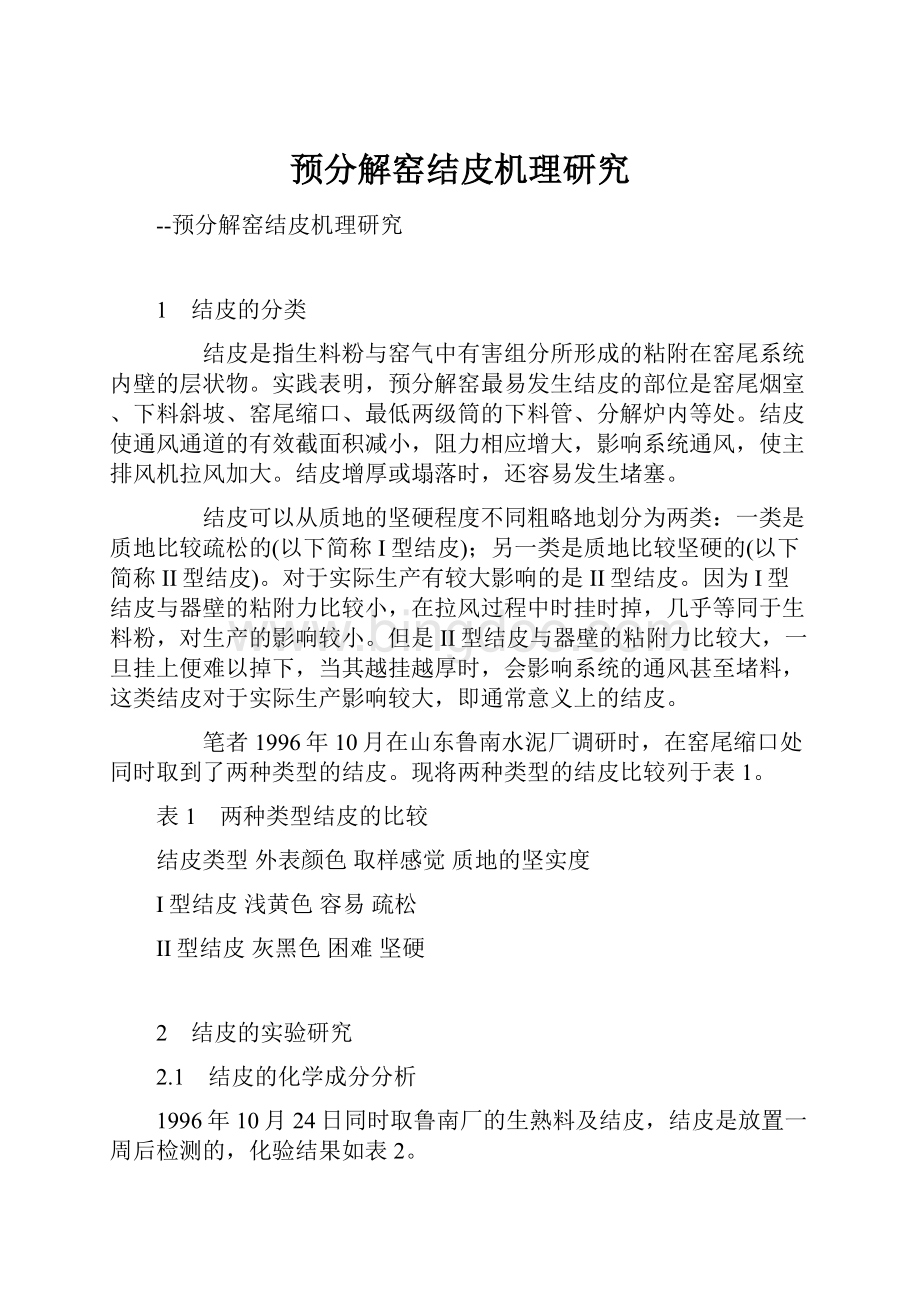
预分解窑结皮机理研究
--预分解窑结皮机理研究
1 结皮的分类
结皮是指生料粉与窑气中有害组分所形成的粘附在窑尾系统内壁的层状物。
实践表明,预分解窑最易发生结皮的部位是窑尾烟室、下料斜坡、窑尾缩口、最低两级筒的下料管、分解炉内等处。
结皮使通风通道的有效截面积减小,阻力相应增大,影响系统通风,使主排风机拉风加大。
结皮增厚或塌落时,还容易发生堵塞。
结皮可以从质地的坚硬程度不同粗略地划分为两类:
一类是质地比较疏松的(以下简称I型结皮);另一类是质地比较坚硬的(以下简称II型结皮)。
对于实际生产有较大影响的是II型结皮。
因为I型结皮与器壁的粘附力比较小,在拉风过程中时挂时掉,几乎等同于生料粉,对生产的影响较小。
但是II型结皮与器壁的粘附力比较大,一旦挂上便难以掉下,当其越挂越厚时,会影响系统的通风甚至堵料,这类结皮对于实际生产影响较大,即通常意义上的结皮。
笔者1996年10月在山东鲁南水泥厂调研时,在窑尾缩口处同时取到了两种类型的结皮。
现将两种类型的结皮比较列于表1。
表1 两种类型结皮的比较
结皮类型外表颜色取样感觉质地的坚实度
I型结皮浅黄色容易疏松
II型结皮灰黑色困难坚硬
2 结皮的实验研究
2.1 结皮的化学成分分析
1996年10月24日同时取鲁南厂的生熟料及结皮,结皮是放置一周后检测的,化验结果如表2。
表2 鲁南厂生熟料及结皮化学成分%
料样LossSiO2Al2O3fCaOFe2O3CaOMgOSO3K2ONa2OCl-
1号窑结皮22.810.93.99.551.8353.62.51.13.080.370.82
2号窑结皮15.39.43.8418.441.7255.02.238.173.400.411.62
1号窑入C1生料36.1612.72.81.8642.82.320.230.600.110.007
2号窑入C1生料36.1512.682.722.0242.432.530.350.650.130.02
1号窑熟料0.921.65.03.2563.983.640.280.720.240.002
2号窑熟料1.021.85.343.1363.353.700.230.800.220.009
由表2可以看出:
1)结皮中挥发性有害组分的含量高于生熟料。
由于生料中所含的碱、氯、硫等组分进入回转窑后,在窑的高温带挥发,以气态形式存在于窑气中,窑气在向窑尾运动的过程中温度逐渐降低,大约在7000C左右〔2〕,窑气中的碱、氯、硫又可能化合为液态的盐类,并很快吸附于物料的表面。
由于微细粉尘比表面积大,故吸附量更多。
冷凝后的有害组分又随生料一起入窑,再次进行挥发、冷凝循环,所以结皮中挥发性有害组分的含量高于生、熟料。
2)II型结皮的形成时间(或形成温度)比I型结皮长(或高)。
在鲁南厂取样时,2号窑的窑尾缩口结皮比1号窑难取;1号窑结皮质地比较疏松,2号窑结皮质地则比较坚硬;1号窑结皮外观呈浅黄色,2号窑结皮则呈灰黑色。
从直观上来看,2号窑结皮的形成时间(或形成温度)比1号窑长(或高),据了解1号窑结皮形成时间短,1个月左右,2号窑结皮形成时间长,半年左右。
从烧失量来看,1号窑结皮的烧失量(22.8%)大于2号窑(15.3%),也说明了2号窑结皮的形成时间(或形成温度)比1号窑长(或高)。
再从fCaO的含量来看,2号窑的结皮中fCaO的含量(18.44%)高于1号窑(9.55%),这也表明2号窑的结皮,由于形成时间(或形成温度)比1号窑长(或高),使其中的碳酸钙分解率大于1号窑,从而使得fCaO的含量大于1号窑,从而使得fCaO的含量大于1号窑。
以上分析表明,1号窑的结皮属于I型结皮,2号窑的结皮属于II型结皮。
3)II型结皮所含的挥发性有害组分比I型结皮高。
既然II型结皮的形成时间(或形成温度)比I型结皮长(或高),则从窑里高温带挥发出来的有害组分在II型结皮中的冷凝量大于I型结皮。
从表2看出,2号窑结皮中SO3、K2O、Na2O及Cl-的含量高于1号窑。
2.2 结皮的X射线衍射分析及扫描电镜分析
1)结皮是有害组分粘结生料粉而形成的。
1号窑结皮的X射线衍射分析结果如图1。
由图可以看出,结皮中的矿物以方解石为主,说明结皮含有大量的生料粉。
另外结皮中含有少量的KCl及2C2S·CaCO3(硅方解石)等矿物,而KCl及2C2S·CaCO3正是结皮的特征矿物,结皮就是KCl等特征矿物把生料粉粘结在窑尾系统的内壁而形成的。
从图1还知道,结皮中也含有一定量的fCaO,这是石灰石分解后生成的未参与形成水泥熟料主要矿物的氧化钙(CaCO3=CaO+CO2)。
图1 1号窑结皮的X射线衍射分析图
2号窑结皮的X射线衍射分析结果如图2。
由图可见,2号窑结皮也以方解石作为主导矿物,仍然含有KCl及2C2S·CaCO3等特征矿物。
如前所述,1号窑的结皮属于I型结皮,2号窑的结皮属于II型,它们都含有方解石、KCl及2C2S·CaCO3等特征矿物,具有一定的共性,从图3可以清楚地看到结皮中含有的大量的方解石颗粒(见图3中72—P)。
图2 2号窑结皮的X射线衍射分析
图3 2号窑结皮的SEM照片
2)含硫矿物在结皮的硬化中起着十分重要的作用。
由表2知道,2号窑结皮中的SO3、K2O、Na2O及Cl-含量比1号窑高,它们的比值分别为:
8.17/1.1=7.4;3.4/3.08=1.1;0.41/0.37=1.1;1.62/0.82=2,可见II型结皮与I型结皮相比,其中SO3的富集程度比K2O、Na2O及Cl-大。
由图1和图2知道,1号窑结皮中未发现,但是在2号窑结皮中却发现了CaSO4及K3Na(SO4)2,也说明II型结皮中SO3含量高于I型结皮。
这与化学分析的结果一致。
从结皮的扫描电镜照片也可以看到,结皮是由KCl、CaSO4等相粘结生料粉而形成的,图3中的69-P表示方解石、硫酸钙和氯化钾组成的微区。
含硫矿物在结皮的硬化中起着十分重要的作用。
由于硫主要来自煤,结皮中含硫量的增大除了与硫的循环富集有关外,还可能是由于窑、炉中煤粉燃烧不完全,在窑尾系统中进行二次燃烧,这一方面使得煤灰在生料中的掺量增加,另一方面产生的局部高温使挥发性有害成分的循环富集更加严重,这些都使结皮中的硫含量提高。
3)硅酸盐矿物的形成也导致结皮硬化。
经过X射线衍射分析知道,2号窑的结皮中含有大量的C2S,而1号窑的结皮中未发现C2S。
这一方面说明硅酸盐矿物的形成对于结皮的硬化具有很大作用,另一方面也说明窑尾温度过高是导致结皮的重要因素。
对于预分解窑来说,进入回转窑的粉料温度约为820~8600C。
结皮中含有大量的C2S,说明窑尾温度过高。
鲁南水泥厂的操作实践也表明,窑尾温度有时达到10000C。
过高的尾温使生料粘性增加;有害组分可能融化而起到粘结剂的作用;煤粉在高温下也表现出焦渣特性,特别是在系统中还原气氛严重时易分解出煤焦油;局部高温使挥发性有害成分的循环富集更加严重,这些都使结皮更加容易形成与硬化。
而尾温过高反映了窑、炉中存在煤粉不完全燃烧现象。
3 预分解窑结皮机理
3.1 挥发性组分的来源
在窑系统的废气中含有大量的挥发性组分,主要是碱、氯、硫,它们在整个系统中参与两种循环〔1〕内循环和外循环。
若丢弃窑灰,外循环则基本消除。
但是,由于在预热器系统中氧化钾的冷凝率高达81%~97%,因而预热器废气中带出的碱、氯、硫等有害组分相当低,因而窑灰重新回窑产生的外循环,对于生成结皮的影响不大。
由于预分解窑的结皮与有害组分有关,了解其来源很有必要。
1)碱的来源。
碱主要来源于原料,尤其是粘土。
对鲁南水泥厂使用的两种主要原料石灰石、粘土而言,化验结果显示,石灰石中碱为0.3%~0.8%,而粘土中的碱含量则为3.21%左右,证明碱主要来源于粘土。
粘土的X射线衍射分析如图4。
由图可知,粘土中含有相当数量的长石,它是碱存在的矿物形式之一。
在使用煤作燃料时,则少量的碱来自煤灰。
碱在原燃料中存在的矿物形态还有:
苛性碱(ROH)、氯化碱(RCl)、硫酸碱(R2SO4)及碳酸碱(R2CO3)和云母、伊利石等。
图4 鲁南厂粘土的X-射线衍射分析
2)硫的来源。
粘土中含有少量的硫,燃料中带入的硫通常较原料中多。
目前使用较多的燃料是煤。
煤中通常含有C、H、O、N、S等元素。
煤中的硫通常有三种存在形式:
有机硫、硫化物中的硫、硫酸盐中的硫。
有机硫和硫化物中的硫均能燃烧生成二氧化硫,所以又叫做可燃硫。
存在于硫酸盐中的硫不具有可燃性,在高温下,一部分会分解生成含硫化合物,而大部分留在灰分中。
鲁南水泥厂煤粉的X射线衍射分析如图5。
由图可知,该厂煤粉中含有大量的不具有可燃性的含硫矿物硫酸钙,以及多水高岭土、珍珠陶土等,说明鲁南水泥厂煤粉的可燃性比较差,容易产生不完全燃烧从而导致结皮的形成。
图5 鲁南水泥厂煤粉的X射线衍射分析
3)氯的来源。
S.N.Gosh认为〔7〕,氯主要来自水溶性碱的氯化物,即通常以KCl、NaCl的形式存在于原料内。
在生料中氯的含量通常比较低,但由于其蒸汽压高而容易挥发,使得氯的循环富集很严重。
以鲁南水泥厂为例计算如下:
由表2知,2号窑结皮与入一级筒的生料中的SO3、K2O、Na2O、Cl-的含量之比值分别为:
8.17/0.35=23;3.4/0.65=5;0.41/0.13=3;1.62/0.02=81。
1号窑结皮与入一级筒的生料中的SO3、K2O、Na2O、Cl-的含量之比值分别为:
1.1/0.23=5;3.08/0.6=5;0.37/0.11=3;0.82/0.0072=114。
两台窑的计算结果都说明,Cl-在生料中的富集比其它组分严重得多。
也正因为如此,KCl常常成为结皮的特征矿物。
3.2 结皮特征矿物的研究
近年来,关于结皮中是否含有中间相的争论比较激烈。
一般认为〔1〕,结皮的主要矿物成分是硅方解石(2C2S·CaCO3)。
中国建筑材料科学研究院曾对8个结皮试样进行了X射线衍射分析,结果发现大部分试样中都含有硅方解石(2C2S·CaCO3)。
美国波特兰水泥协会(PCA)也认为硅方解石是结皮的主要成分。
然而,国内有的学者指出〔10〕,在结皮料中,硅方解石等过渡矿物的形成需要较长的时间,它们直接导致结皮的可能性不大。
笔者基于实验事实,首先检测了鲁南水泥厂1号窑和2号窑的结皮,发现两类结皮中都含有硅方解石(2C2S·CaCO3),但是比较坚硬的2号窑结皮中还含有CaSO4及K3Na(SO4)2,说明中间相在结皮的形成中具有加速硬化的作用。
由于结皮中大都含有CaCO3、SiO2、fCaO、CaSO4、C2S、KCl、K3Na(SO4)2及2C2S·CaCO3等矿物,下面结合实验结果对结皮矿物进行综述。
1)CaCO3与SiO2
由于结皮是有害组分粘结生料粉形成的,并且生料入窑之前尚未完全分解(预分解窑入窑生料的碳酸钙分解率为85%~95%),入窑生料中就可能含有方解石、石英等未反应的水泥原料组分,已分解出来的CaO也可能与CO2反应生成CaCO3,它们可参与形成结皮的中间相。
如前所述,鲁南水泥厂两台窑的窑尾缩口结皮中均含有大量的方解石就是一例。
------
2)fCaO和C2S
预分解窑生料入窑时,其中的CaCO3有85%~95%已经分解,并且由于生料温度比较低,水泥熟料矿物尚未完全形成,fCaO的吸收也不可能完全,因此入窑生料中就可能含有fCaO。
由于粘土在6000C左右即已分解,预分解窑的入窑生料温度可达820~8600C,所以,生料入窑之前,粘土就已经分解出SiO2。
又因为硅酸二钙在8000C左右开始形成。
因此入窑生料中就含有C2S。
硅酸二钙的形成,使结皮更加坚实化。
鲁南厂2号窑的结皮中就含有fCaO和C2S,其中C2S不仅使2号窑的结皮比1号窑更坚实,而且使结皮外观呈灰黑色。
3)CaSO4和KCl
结皮中的硬石膏可能来源于两个方面:
其一是煤中含有不具备可燃性的硫酸钙时,CaSO4在煤粉燃烧后存在于灰分之中,当煤灰和其它有害组分与生料粉混合并粘附在衬料内壁形成结皮时,则煤灰中的CaSO4就成了结皮的一个组分;其二是由于煤粉燃烧时生成二氧化硫气体〔RSH(R表示烃基)+O2→CO2+H2O+SO2;4FeS2+11O2=2Fe2O3+8SO2〕,煤中的不可燃硫在到达窑的高温带时也可能分解出SO2,若粉料中同时存在着fCaO,有人认为〔11~13〕,CaSO4可以下列方式生成2SO2+O2+2CaO=2CaSO4,硬石膏在许多结皮(II型结皮)中都被检测到,它的形成将导致结皮易挂难掉。
鲁南厂2号窑的结皮中就含有CaSO4。
由于Cl-主要来源于原料,结皮中的KCl主要来自生料中Cl-的循环富集。
鲁南厂1号、2号窑的结皮中都含有KCl。
氯化钾是结皮的特征矿物。
4)2C2S·CaCO3与K3Na(SO4)2
硅方解石是一种被研究得比较普遍的过渡矿物。
H.M.Sylla〔14〕对2C2S·CaCO3的形成条件和性质进行了研究。
结果表明,在实验室电炉内,2C2S·CaCO3于CO2的气氛中在约700~9000C的温度范围内形成。
硅方解石的形成,主要由氯化物促进,也由碱所促进。
即有害组分的循环富集有利于硅方解石的形成。
粉状物料中一旦形成硅方解石,粉料便坚实化起来。
所以在预分解窑中,当有害组分的循环富集达到一定程度足以将粉料结实地粘附在衬料上时,便形成了对生产可能造成影响的结皮。
在温度进一步升高后,硅方解石就不再稳定。
由于鲁南水泥厂的实际情况是石灰石中MgO较高,煤的灰分也比较大,笔者参考鲁南厂结皮的化学成分(见表2)及有关参考资料〔7,14〕,配制了一系列的物料,重点考察MgO和煤灰对结皮矿物的影响。
实验配料如表3(取1号窑入一级筒的生料来配料)。
表3 实验配料表
料样编号配比各组分质量
198%生料+2%煤灰50g生料+1.2g煤灰
291%生料+9%煤灰50g生料+5.0g煤灰
387%生料+9%煤灰+4%MgO50g生料+5.0g煤灰+2.8gMgO
实验过程:
将料1、料2和料3按照上述配比配好后,混合均匀、磨细,然后进行对比实验。
实验条件及结果如下:
料1分别在9000C下保温10min和10h,再进行X-射线衍射分析,结果如图6及图7。
由图6及图7知道,保温时间短的物料中还有大量的方解石,而保温时间长的无方解石,这是因为方解石的分解率随着时间的延长而增大;但是两者都形成少量的硅方解石,它促使粉料坚实化,有利于结皮的形成。
在这两种情况下,都未发现K3Na(SO4)2的形成。
料2分别在9000C下保温10min和10h,再进行X射线衍射分析,结果如图8及图9。
由图可知,料2分别在9000C下保温10min和10h后都有硅方解石生成,这与料1的情形相似。
但是保温10h的物料中出现了一种新的矿物──K3Na(SO4)2,而料1及料2在9000C下保温10min都没有出现此矿物。
图6 料1的X射线衍射分析(9000C保温10h)
图7 料1的X射线衍射分析(9000C保温10min)
图8 料2的X射线衍射分析(9000C保温10min)
图9 料2的X射线衍射分析(9000C保温10h)
这就可以得出至少4个结论:
1)煤灰含量的增大有助于K3Na(SO4)2的形成。
料1在保温10min及10h后都没有出现此矿物,而料2保温10h后却形成了K3Na(SO4)2,由于料2的煤灰掺量大于1,说明煤灰含量的增大有助于K3Na(SO4)2的形成。
2)保温时间的延长有助于K3Na(SO4)2的形成。
料2保温10min未形成K3Na(SO4)2,保温10h后却形成了此矿物,这充分证明保温时间的延长有助于K3Na(SO4)2的形成。
3)K3Na(SO4)2的形成促使物料坚实化。
制样表明,料2保温10h后比保温10min后的物料坚硬;料2保温10h后比料1保温10h后的物料坚硬。
说明K3Na(SO4)2的形成促使物料坚实化。
4)K3Na(SO4)2可能通过化学反应而形成。
由于生料粉中不含K3Na(SO4)2,在实验室的高温炉中也不存在SO2气氛(因为配料采用的是煤灰而不是煤粉),K3Na(SO4)2不可能是有害组分只经过冷凝而不通过化学反应就形成。
K3Na(SO4)2可能通过化学反应而形成:
3K2SO4+Na2SO4=2K3Na(SO4)2(反应物K2SO4及Na2SO4主要来自煤灰)。
I.Jawed和J.Skalny认为〔15〕,K3Na(SO4)2是在还原气氛中形成的,于9000C以上分解。
由此可以推论,当分解炉或窑头煤粉燃烧不完全时,可能造成部分煤粉在窑尾系统中进行二次燃烧,从而造成还原气氛,在9000C以下可能产生K3Na(SO4)2,尤其在煤的灰分高时(硫含量相应较高),更容易形成K3Na(SO4)2,从而促使物料坚实化,有利于结皮的形成。
料3分别在9000C下保温10min和10h,再进行X射线衍射分析,结果如图10及图11。
图10 料3的X射线衍射分析(保温10min)
图11 料3的X射线衍射分析(保温10h)
结果表明,掺MgO后的生料保温10min后没有发现K3Na(SO4)2生成,而保温10h后却形成了K3Na(SO4)2,这一方面说明K3Na(SO4)2的形成需要较长时间,另一方面也说明MgO能促进K3Na(SO4)2的形成,从而有助于结皮的坚实化。
袁润章等研究认为〔10〕,在850~1100℃的温度范围之内,分解炉预热器的物料中会形成硫酸盐的熔体。
K3Na(SO4)2可能是在硫酸盐熔体介质中形成的。
从相图分析知道,在多组分体系中,系统的最低共熔温度一般随着组分数的增多而降低,如C2S-C3S-C3A体系,最低共熔温度为1455℃;而C2S-C3S-C3A-MgO体系,最低共熔温度为1375℃;C2S-C3S-C3A-MgO-Na2O-Fe2O3体系,最低共熔温度为1280℃。
MgO的存在可能使液相开始出现的温度降低而促进K3Na(SO4)2的形成,从而有助于结皮的坚实化。
国内有学者对预分解窑中控室的操作参数进行了回归分析〔16〕,通过回归分析知道,MgO含量高时,会引起窑尾结皮,影响系统通风,从而引起煤粉的不完全燃烧。
当MgO含量>1.65%时,操作上要适当降低最低一级筒的料温,防止结皮产生。
3.3 结皮机理
如前所述,结皮是指有害组分与生料粉所形成的粘附在衬料内壁上的层状物。
关于结皮的原因,H.Rumpf〔1〕认为是湿液薄膜表面张力作用下的熔融粘结,作用在表面上的吸力造成的表面粘结及纤维状或网状物质的交织作用造成的粘结。
由于窑气中的碱、氯、硫等有害组分在窑尾及预热器和分解炉中冷凝时,会使最低共熔温度降低,因此窑气中的碱、氯、硫等凝聚时,会以熔态的形式沉降下来,并与入窑物料和窑内粉尘一起构成粘聚性物质,而这种在生料颗粒上形成的液相物质薄膜,会阻碍生料颗粒的流动,从而造成结皮甚至堵塞。
引起预分解窑结皮的因素,至少有如下几种:
1)系统中有害组分(碱、氯、硫等)的循环富集。
这是形成结皮的重要条件。
从原燃料中引入系统的碱、氯、硫等有害组分,在生料通过窑的高温带时会挥发出现,并随着窑气向窑尾运动。
挥发出来的有害组分到达窑尾温度较低的区域时,便会以熔态的形式冷凝下来,这一方面使生料在煅烧过程中液相开始出现的温度降低而有利于结皮的形成,如一般情况下,生料的最低共熔温度为1250℃左右,H.Ritzmann〔17〕指出,CaSO4、K2SO4和Na2SO4共同存在时,最低共熔温度可能低于800℃;有氯化物存在时,最低共熔温度可接近700℃;另一方面有害组分形成的熔体会在生料或衬料表面铺展开来,起到“粘结剂”的作用,在系统温度降低时,就在衬料表面上形成结皮。
窑内的这种有害组分是导致结皮中间相形成的重要因素,如:
二氧化硫参与形成硫酸钙(2SO2+O2+2CaO=2CaSO4);氯化物促进硅方解石的形成;K3Na(SO4)2是在还原气氛中形成等等。
而结皮中间相的形成,常常导致结皮坚实化,使结皮越结越厚。
2)局部温度过高,这是形成结皮的关键因素。
系统中如果产生局部高温,一方面促进生料和燃料中有害组分的挥发及冷凝循环,并使内循环发生的区域进一步扩大;另一方面也可能使液相出现,把生料粘附在衬料的内壁而形成结皮。
从热力学的理论知道,液体的表面张力随着温度的升高而下降,表面张力与触角之间满足关系式:
cosθ=〔γ(s-g)-γ(1-s)〕/γ(1-g),若θ角减小,则液相易于在固体表面铺展开来。
现将此理论应用于结皮的研究之中:
如果预分解窑局部温度偏高,则使出现的熔体的表面张力下降,即γ(1-g)降低,由cosθ=〔γ(s-g)-γ(1-s)〕/γ(1-g)知道,熔体的表面张力下降必然导致cosθ增大,即接触角减小,这就表示在窑尾或分解炉中出现的熔体更容易在生料粉或衬料表面铺展开来,就更容易形成结皮。
所以,局部温度过高,这是形成结皮的关键因素。
产生局部高温的原因,至少有如下几个:
①煤粉的不完全燃烧。
窑头或分解炉中的煤粉由于多种原因燃烧不完全时,就可能到窑尾或低级旋风筒中去燃烧,从而产生局部高温,这是出现局部高温的主要原因。
引起煤粉的不完全燃烧又可能具有下列几个因素:
燃煤的灰分大。
煤灰含量高,说明煤质差,热值低,可燃性差,容易引起窑煤、炉煤的不完全燃烧;设备超负荷运转。
由于回转窑和分解炉的容量是有一定限度的,喂料量及喂煤量的过分加大将不利于生料及煤粉的悬浮分散,同时使得煤粉的燃烧空间变小而不利于煤粉的完全燃烧;分解炉结构不合理。
②喂料量的波动。
喂料量忽大忽小时,很容易打乱预热器、分解炉和窑的正常工作。
由于操作具有滞后的特点,有时跟不上喂料的变化,加减煤不及时,甚至出现短期断料也不能及时减煤,因此很容易因料小出现系统温度偏高,而造成结皮。
③回灰对结皮的影响。
回灰也叫做窑灰,是电收尘、增湿塔收集下来的物料。
由于回灰量小,在生料均化库中不容易被混合均匀,从而造成入窑生料成分的波动,影响窑的热工制度的稳定性;再则由于回灰中含有一定量的有害组分,它的重新入窑必然加剧挥发性组分的循环富集,这些都容易引起结皮。
④预热器漏进冷风对结皮的影响。
当预热器漏进冷风时,则物料温度和分解率都降低,为维持生产,系统排风必须加大,因而废气量增大,飞扬粉尘增加,循环负荷加大,导致入窑生料温度下降,能耗上升。
当预热器漏进冷风与热物料接触,很容易使热物料冷凝而粘附在系统的内壁而产生结皮。
此外,被带到窑尾或预热器中的煤粉遇到新鲜冷风,燃烧速度加快,产生局部高温而形成结皮。
此外,石灰石中氧化镁含量高也是结皮的一个因素,如前所述〔16〕,随着MgO含量的上升,经过回归分析知道,预热器出口气体温度上升;出口气体中氧气含量下降,说明气、料热交换效率下降,分解炉内存在煤粉的不完全燃烧,同时窑尾的负压随着MgO含量的上升而下降,说明窑内通风不良,窑尾易于结皮。
4 防止结皮的措施
由于结皮影响系统的通风,使阻力增大,这不仅使能耗上升,而且结皮严重造成堵塞时,有时被迫停窑处理,不利于水泥产质量的提高。
预防结皮具有重要意义。
现将防止结皮的措施简介如下:
1)减少或避免使用高硫和高氯的原料,这是减少结皮的前提。
国外部分公司对生料中有害成分含量的规定见表4。
表4 国外部分