综合实验报告上.docx
《综合实验报告上.docx》由会员分享,可在线阅读,更多相关《综合实验报告上.docx(20页珍藏版)》请在冰点文库上搜索。
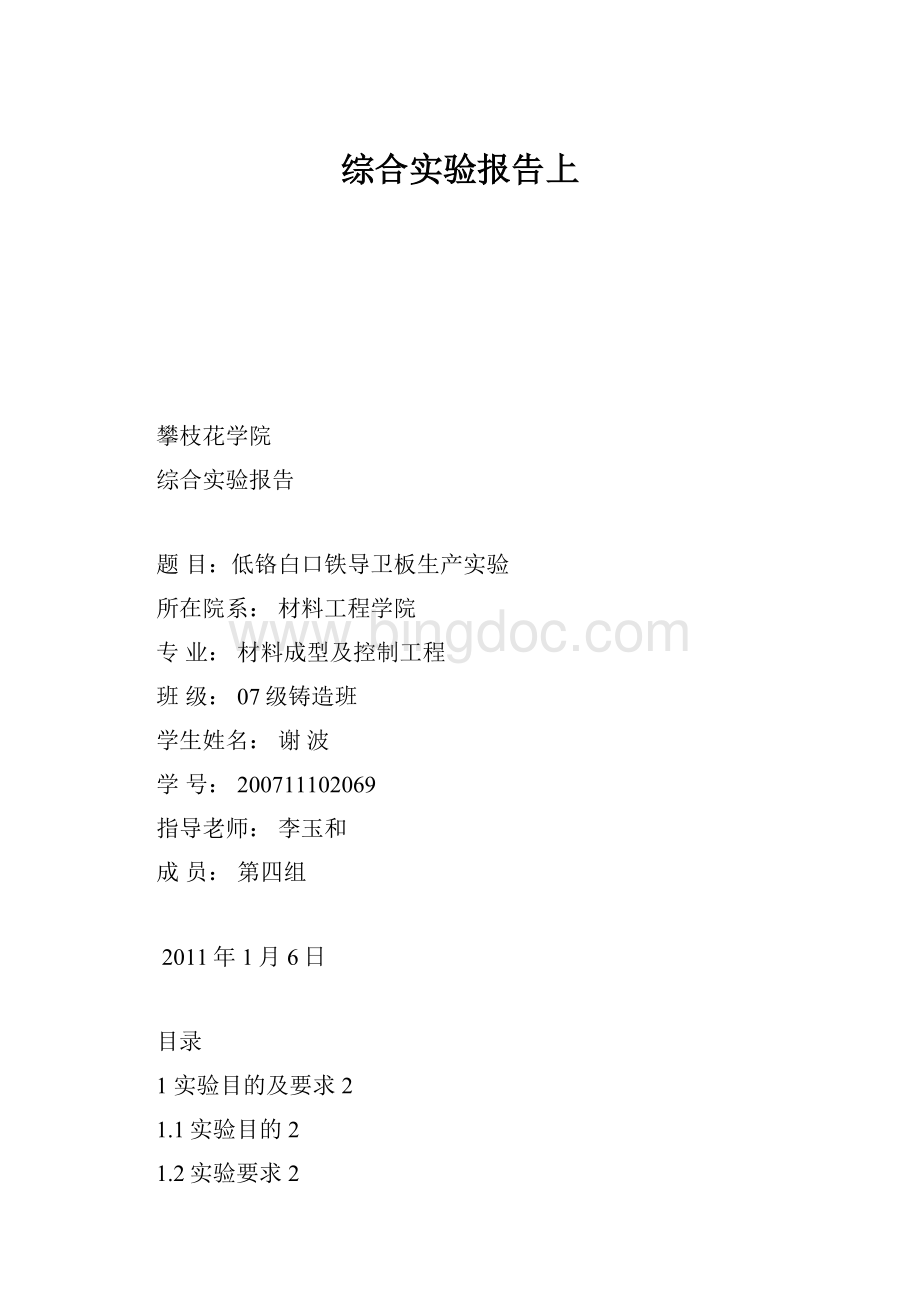
综合实验报告上
攀枝花学院
综合实验报告
题目:
低铬白口铁导卫板生产实验
所在院系:
材料工程学院
专业:
材料成型及控制工程
班级:
07级铸造班
学生姓名:
谢波
学号:
200711102069
指导老师:
李玉和
成员:
第四组
2011年1月6日
目录
1实验目的及要求2
1.1实验目的2
1.2实验要求2
2实验原理2
3实验设备及原料3
3.1实验设备3
3.2实验原料及药品3
4实验步骤3
4.1导卫板概述3
4.2材料选择4
4.3铸造工艺方案确定5
4.3.1零件结构的铸造工艺性分析5
4.3.1.1零件结构分析及零件结构的铸造工艺性分析原则5
4.3.1.2本次实验零件的铸造工艺性分析5
4.3.2分型面及浇注位置的确定6
4.3.2.1分型面的选择6
4.3.2.2浇注位置的确定6
4.5浇注系统计算8
4.6混砂及造型制芯10
4.6.1混砂10
4.6.2造型10
4.7合金熔炼11
4.7.1配料11
4.7.2熔炼12
4.8表面合金化13
4.9浇注及清砂13
4.10热处理15
4.11晶相观察及硬度测定15
5实验结果及分析改进17
5.1实验结果17
5.2分析改进18
5.3结论18
6实验心得19
参考文献20
1实验目的及要求
1.1实验目的
(1)了解导卫板的应用范围和发展概况,加深对导卫板生产工艺过程的了解。
(2)通过导卫板的实际生产巩固铸造工艺设计、造型材料选取、合金熔炼、金属热处理、晶相分析。
(3)验证用经稀土变质处理的低铬白口铸铁加950℃×2h加热空淬生产轧钢导卫板的可能性。
1.2实验要求
(1)铸造工艺的设计应正确并且符合学校的实际实验条件。
(2)实验过程中要服从老师的安排,遵守安全规程,保证人生安全及实验设备安全。
2实验原理
利用学校提供的原材料(废钢、生铁、铬铁、硅铁、锰铁、稀土等),进行电磁感应炉熔炼,得到目的钢种的合金液;并混制型砂,造型制芯进行浇注获得铸造产品;取样并定制合理的热处理工艺,通过实验(观察晶相、测定硬度)比较铸态式样和热处理后的式样的各项特征及性能。
本次实验我们这组选择的轧钢导卫板的生产。
由于用现成的木模造型,所以无零件图。
经测量绘制的木模图形为图1。
3实验设备及原料
3.1实验设备
本次实验所用的设备有电磁感应炉(25Kg)、台称、铁铲、砂箱、锤头、烤箱、切割机、砂轮机、箱式加热炉、大功率电吹风、钢钳子、石棉手套、抛光机、制样机、光学显微镜、HR150A硬度剂。
3.2实验原料及药品
本次实验用的主要材料,废钢、生铁、锰铁、硅铁、铬铁、铝豆,合金主要成份如表1。
造型材料,稀土、硅砂、消失模用涂料、铸造用粘土、水玻璃、水、晶相用的药品,无水酒精、4%硝酸酒精。
表1原材料成分
C
Si
Mn
Gr
Al
P
S
废钢(%)
0.2
0.2
0.2
—
—
0.03
0.03
生铁(%)
4.0
0.1
0.5
—
—
0.02
0.1
锰铁(%)
0.01
0.02
60
—
—
—
—
硅铁(%)
0.05
75
0.01
—
—
—
—
铬铁(%)
0.05
0.01
0.01
65
—
—
—
铝(%)
0.01
7
—
—
90
—
—
4实验步骤
4.1导卫板概述
导卫板是轧钢厂消耗量很大的易损件之一,是轧件进入和导出轧槽的关键控制件之一。
它主要用于诱导、夹持轧件(钢丝)顺利通过。
导卫板工作时与高温(1100℃)、高速(6m/s)轧件直接滑动接触,虽然有冷却水强制降温,但经测算,导卫板工作面的温度可达300℃。
在这种工况下,高温氧化磨损和疲劳剥落是主要的失效形式。
据统计,一副新导卫板平均只能用20h[1]。
目前常用的修复方式是堆焊,但堆焊后的耐磨性有限,且修复一两次后即彻底报废。
因此,要求制作导卫板的材料不仅具有良好的抗高温氧化性能和抗高温磨损性能,而且还要有良好的韧性,以满足抗冲击的要求。
普通导卫板使用寿命低,更换频繁,直接影响线材轧机生产作业率和人身安全。
4.2材料选择
由导卫板的工作条件可知生产导卫板的材质要有较高的强度、韧性、耐热疲劳性、耐磨性以及抗氧化性[1]。
目前我国使用的抗磨材料主要是高锰钢低合金钢和白口铸铁,其中白口铸铁的抗磨性居于首位,但因韧性较低。
使其应用受到限制。
所以,提高白口铸铁的韧性是发展白口铸铁抗磨材料的关键[2]。
提高自口铸铁韧性有四条主要途径。
一是提高Cr/C比,使含铬量>12%,碳化物由M3型变为M7C3型,共晶碳化物由连续的网状变为断开的板条状,从而据高其韧性,同时由于提高了碳化物的显微硬度(M7C3型碳化物的显微硬度为HV1300~1800)因此也提高了耐磨性,这就是高铬白口铸铁。
但是,高铬铸铁成本高,加上我国铬铁货源不足,使其应用受到限制。
二是锻造白口铁。
使其网状的共品碳化物破碎,以捉高其韧性,这种方法主要受锻造设备的限制,目前在工业上还没有应用。
三是用稀土元索对白口铸铁进行变质处理,使共晶碳化物由连续网状变为断开的、孤立的板条状,从而提高其韧性。
四是对白口铸铁进行热处理,使网状共晶碳化物在高温下局局部断开,并变为较孤立的条状。
从而提高其韧性[5]。
如果在对低铬白口铸铁进行变质处理的基础上,再进行热处理,这样既可以进一步改善共晶碳化物的形态和分布,提高韧性,而且通过热处理获得马氏体基体,提高其硬度和耐磨性。
发展这种经变质处理一热处理的低铬白口铸铁抗磨材料,需要的铬铁较少,成本较低。
比较符合我国国情。
所以本次实验中,我们组选择的导卫板材料为低铬白口铁,其具体成份如表2。
经过对市场调查得到近期铸造原材料价格如表3。
表2低铬白口铁成份
成份
C
Si
Mn
Cr
Re
S
含量(%)
3.0
0.7
1.5
1.0
0.5
<0.01
表3原料市场价格
原料名称
废钢
生铁
硅铁
锰铁
铬铁
铝
价格(元/吨)
2800
3000
8500
10000
20000
15000
4.3铸造工艺方案确定
4.3.1零件结构的铸造工艺性分析
零件结构的铸造工艺性指的是零件的结构应符合铸造生产的要求,易于保证铸件的品质,简化铸造工艺过程和降低成本[8]。
4.3.1.1零件结构分析及零件结构的铸造工艺性分析原则
(1)铸件应有合适的壁厚。
(2)铸件结构不应造成严重的收缩阻碍,注意壁厚过渡和圆角。
(3)铸件内壁应薄于外壁。
(4)壁厚力求均匀,减少肥厚部分,防止形成热节。
(5)利于补缩和实现顺序凝固。
(6)防止铸件翘曲变形。
(7)避免浇注位置上有水平的大平面结构。
(8)改进妨碍起模的凸台、凹缘和肋板的结构。
(9)取消铸件外表面侧凹。
(10)改进铸件内腔结构以减少砂芯
(11)减少和简化分型面。
(12)要有利于砂芯的固定和排气。
(13)要减少清砂的工作量。
(14)要简化模具的制造。
(15)大型复杂件要分体铸造和简单小件要联合铸造。
4.3.1.2本次实验零件的铸造工艺性分析
本次实验是用已成形的木模直接造型,所以无法再从零件的结构上去改进。
结合学校的实验条件(熔炼炉的大小)把原来的木模切下了一段。
修改后的模型的铸造工艺性还是满足以上的要求。
其图为图1。
4.3.2分型面及浇注位置的确定
4.3.2.1分型面的选择
分型面是指两半铸型相互接触的表面。
分型面的优劣,很大程度上影响铸件的尺寸精度、成本和生产率。
选择的原则如下:
(1)应使铸件全部或大部置于同一半型内。
(2)应尽量减少分型面的数目。
(3)分型面应尽量选用平面。
(4)便于下芯、合箱和检查型腔的尺寸。
(5)受力件的分型面的选择不应消弱铸件结构的强度。
结合以上原则,零件的分型面选择如图2。
图2导卫板铸造工艺图
4.3.2.2浇注位置的确定
铸件的浇注位置是指浇注时铸件在型腔所处的状态和位置。
生产中常以浇注时分型面是处于水平、垂直或倾斜位置,分别成为水平浇注、垂直浇注和倾斜浇注,但这并不代表铸件的浇注位置的函意[8]。
确定浇注位置时所遵守的原则如下:
(1)铸件的重要部分应尽量置于下部。
(2)重要加工面应朝下或呈直立状态。
(3)使铸件的大平面朝下,避免夹砂结疤类缺陷。
(4)应保证铸件能充满。
(5)应有利于铸件的补缩。
(6)避免用吊砂、吊芯或悬臂式砂芯,便于下芯、合箱及检验。
(7)应使合箱位置、浇注位置和铸件冷却位置相一致。
本次实验选择的浇注位置如图3(水平浇注)
4.4冒口设计
(1)冒口补缩原理及位置的选择
冒口是铸型内用以储存金属液的空腔,在铸件形成时补给金属,有防止缩孔、缩松、排气和集渣的作用。
冒口的补缩原理就是在铸件凝固过程中让冒口中的金属液去填补因铸件凝固形成的缩孔,从而是铸件的组织致密,防止铸件的缩孔类缺陷,提高铸件的质量。
冒口的有效补缩距离为冒口作用区与末端区长度之和,它是确定冒口数目的依据,与铸件结构、合金成分及凝固特性、冷却条件、对铸件质量要求的高低等多种因素有关,简称冒口补缩距离。
(2)冒口位置的选择
①冒口应就近设在铸件热节的上方或侧旁。
②冒口不应设在铸件重要的、受力的部位,以防组织粗大降低强度。
③冒口位置不要选在铸造应力集中处,应注意减轻对铸件的收缩妨碍,以免一起裂纹。
④尽量用一个冒口同时补缩几个热节或铸件。
⑤冒口布置在加工面上,可以节约铸件精整工时,零件外观好。
⑥不同高度上的冒口,应用冷铁使各个冒口的补缩范围隔开[8]。
(3)冒口计算
由于,低铬白口铸铁无石墨析出,自补缩的能力差,冒口和浇注系统的计算可近似高碳钢来计算。
根据,冒口定义及对零件的机构分析,本铸件需要补缩的位置如图4。
模数法计算如下[8][10]:
利用Pro/E仿真计算出需要补缩段的体积(VC)及有效散热面积(Ac)分别为:
Vc=1119.5cm3Ac=968.7cm2
则:
Mc=Vc/Ac=1119.5÷968.7=1.2
根据简化模数计算法计算冒口
MR=fMc
式中MR—冒口模数(cm);
MC—被补缩部分铸件模数(cm3);
f—扩大系数,f=1.1~1.2,明冒口f=1.2,顶暗冒口f=1.1。
则:
MR=1.2×1.2=1.44
根据计算并查阅《铸造手册》选择标准圆柱形明冒口(h=d)类型Ⅱ,其图为图5及相关参数如表4
表4标准圆形明冒口
冒口
收缩率为5%
类型
MR/cm
D=h/mm
VR/dm3
GR/Kg
VC/dm3
GC/kg
Ⅰ
Ⅱ
1.77
1.66
100
0.95
0.785
6.5
5.4
1.71
1.41
13.4
11
图5冒口图
4.5浇注系统计算
阻流截面设计法,认为浇注系统各单元中截面积最小单元为浇注系统阻流截面,根据小孔出流托里拆利定律,计算阻流截面积,按照预定截面比,进一步计算其余各单元截面积。
根据分析浇注系统中内浇口的截面积最小,所以以内浇口为阻流截面,则S内=S阻[8]。
式中m—流经阻流的金属总质量,Kg;
—充填型腔的总时间,s;
—充填全部型腔时,浇注系统阻流截面的流量系数;
HP—充填型腔时的平均计算压力头。
利用Pro/E仿真计算出铸件的质量为16.5Kg,则流经阻流截面的金属液总质量为21.9Kg;充填型腔的时间为8s;流量系数为0.50;平均压力头为25cm。
则:
预定截面积比为:
由:
则:
经查《铸造手册》内浇口及横浇道的截面形状及尺寸如图6[10]
直浇道的面积为4.14cm2,则其直径d=2.3cm
根据砂箱形状确定的横道长度为36cm,直浇道长度为25cm;则浇注系统的质量为1.7Kg。
绘制合箱图如图7。
4.6混砂及造型制芯
4.6.1混砂
型砂是由原砂、粘土、粘结剂、附加物及水按一定配比组成的。
其中原砂是骨架、粘土为粘结剂。
经过混制后,粘土、附加物和水混合成浆,包覆在砂粒表面形成一层粘结膜。
(1)原材料
铸造生产中使用的原砂以石英为主要矿物成份的天然硅砂为主,为了改善劳动条件或提高铸件质量,生产中也用一些非石英质原砂(镁砂、橄榄石砂、锆砂、铬铁矿砂、石灰石砂、孰料砂、碳素砂、刚玉砂、太铁矿砂等)。
铸造中根据不同的粘结剂可将型砂分为粘土砂、无机化学粘结剂砂、有机化学粘结剂砂。
粘土根据矿物种类不同可分为铸造用粘土和铸造用膨润土两类。
常用的无机粘结剂砂有水玻璃砂、水泥系砂、磷酸盐砂等。
有机物砂有油砂、合脂砂。
型砂中除了含有原砂、粘结剂和水等材料以外,通常还要特意加入一些材料如煤粉、渣油、淀粉等,目的是使型砂具有特定的性能,并且改善铸件的表面质量,这些材料即为附加物。
本次实验的型砂配比如表5
表5型砂配比
原材料
砂
粘土
水玻璃
水
含量(%)
90
10
适量
适量
(2)型砂混制
生产中常用的混砂设备有辗轮式、摆轮式、叶片式混砂机等。
由于实验设备的限制本次实验采用人工混砂。
混砂时先把砂和粘土混均匀,然后加入适量的水待混均匀后再加入水玻璃继续混制,型砂一定要充分的混制均匀。
混制的型砂应有合适的含水量、良好的流动性及透气性。
用手捏的方式来判断型砂的质量,手捏时应只有潮的感觉,但不觉得沾手,且手感柔和,印在砂团上的手指痕迹清晰,砂能捏成团,不易破碎[10]。
4.6.2造型
造型步骤:
(1)检测砂箱是否完好,检测造型器材齐备,测量模具的尺寸是否符合工艺设计的要求,并在木模上均匀的用干砂涂抹,这样做是为了不让木模和砂型粘接。
(2)选择一块平整的场地,将下箱和木模放好,根据浇注位置准确定位木模在下箱的位置。
(3)填砂要均匀,一边填砂一边用手紧实不易紧实的转角处。
(4)用型砂填满下箱并高出一部分再用锤头的平头紧实。
(5)下箱造好后反转过来,将上箱放上,根据浇注系统和冒口的位置,准确的放好模具,填砂紧实和造下箱一样,造好上箱后,取下上箱。
(6)起模时要先用锤头轻轻敲击木模周边使木模和型砂分离,起模时要平稳,尽量不让型腔的尺寸发生太大的变化。
(7)根据计算所得的浇注系统的形状和尺寸,在下箱挖出内浇口和横浇道,用钢丝在上箱均匀的扎出透气孔,孔的大小不能太大以免合金液漏出形成多肉缺陷,也不能太小达不到及时排除型内气体的作用。
(8)修整型腔缺陷部位。
(9)用软毛刷在型腔内刷上涂料,涂料需刷均匀,涂料不得过稀以使涂料层达到要求的厚度,注意在刷涂料过程中不要破坏型腔。
烘烤:
待砂型干到有一定的强度后,将砂箱放入烤箱,在转移砂箱时一定要平稳,不要在转移过程中破坏砂箱。
设定好烘烤温度(150℃)和时间(6h),同时把合金块也一并放入烤箱。
砂箱烘烤后取出待用[10]。
4.7合金熔炼
4.7.1配料
本次试验合金成分如表2所示。
根据以上成分含量,设铸件的总质量为1,加料时加入生铁的量为x,废钢的量为y,锰铁的量为z,硅铁的量为m,铬铁的量为n,列出下列方程式[7][9]:
1、加入原料的总量等于总出钢量:
x+y+z+m+n=1;
2、生铁和废钢中的碳总量等于出钢液中的碳:
20x+y=15;
3、废钢、生铁和硅铁中的硅含量等于出钢液中的硅含量:
x+2y+750m=7;
4、废钢和锰钢中的锰含量等于出钢液中的猛含量:
2y+600z=15;
5、铬铁中的铬的总量等于钢液中的铬的总量:
n=0.03
综合上述五个方程式解得:
x=42.5%;
y=50.1%;
z=1.95%;
m=2.33%;
n=3.01%;
根据以上比例,算得加入料的量为:
生铁加入量=钢液总量X比例=21.9X42.5%=9.3kg;
废钢加入量=钢液总量X比例=21.9X50.1%=10.97kg;
锰铁加入量=钢液总量X比例=21.9X1.95%=0.43kg;
硅铁加入量=钢液总量X比例=21.9X2.33%=0.51kg;
铬铁加入量=钢液总量X比例=21.9X3.01%=0.66kg.
4.7.2熔炼
(1)熔炼前检查感应炉是否完好。
(2)熔炼前需先通冷却水,使水压在0.1~0.2Mpa之间,检查各路冷却水是否通畅无阻,各水管接头应无渗漏现象。
(3)接通电源,顺时针慢慢旋动“功率调节”旋钮,直到平率表、中频电压表及直流电压表均出现计数,并听到机器中发出的中频啸叫声,说明逆变启动成功。
(4)在启动操作过程中,出现直流电流表指示急剧增大,而中频频率表、中频电压表没有指示且听不到中频啸叫声时,则表面启动失败。
此时应将“功率调节”旋至最小,重新按“e”项方法启动。
(5)启动或运行过程中,设备如果出现过流、过压现象时,应先将“功率调节”旋至最小位置,再按“故障解除”,然后按“e”项方法重新启动。
(6)加入的炉料应干净,氧化部分少。
(7)成功启动感应炉后,先下体积较小的生铁,待熔炼有一定的铁液后加入剩余的生铁,在熔炼时把待加入的废钢放在炉口烘烤去除水分。
(8)生铁熔炼完毕后,加入废钢,熔炼是注意拔出金属液表面的浮渣。
(9)用烘烤方法烘烤浇包、硅铁和锰铁,并用一块铁皮把称量好的稀土放在炉口烘烤,去除水分。
(10)出炉前十分钟加入硅铁和锰铁,然后加入铝豆进行脱氧。
(11)把烘好的稀土放入浇包出钢[3]。
(12)出钢时应降低感应炉功率,注意人生安全,穿戴好保护装备[9]。
4.8表面合金化
在轧钢的过程中,轧钢机的钢材进出口处的导卫板工作环境十分的恶劣,900℃以上的红热钢材连续从上通过,同时又要喷水冷却,温差变化大而剧烈。
所以导卫板磨损快,寿命低,需频繁的更换,耗量很大,且易产生龟裂和断裂,影响生产效率;再则易产生粘钢现象,影响轧制钢材的质量,所以为了提高轧钢作业效率和钢材质量,降低消耗,减轻工人劳动强度,导卫板主要由于尖部磨损而失效,我们对最容易受损的尖部部位进行合金化处理,表面合金化处理就是直接利用金属液流渗能力、金属液余热,与粉末发生冶金反应,就可以到达延长铸件使用寿命的目的。
本次实验使用的合金化粉末化学成分见表6。
表6合金化粉末主要化学成分%
C
Cr
Mo
Ni
W
B
7.0
42
3.0
5.0
7.0
3.0
进行合金化处理时直接把合金块贴在导卫板尖部的型腔内,并用铁钉固定,不让合金块被金属液冲离本来的位置。
进行浇注完成后落砂得到的铸件如下图形8所示
从上图可以看到合金化处理后的铸件表面有许多的气孔,主要是因为合金块还没有完全的烘干,还有水份,在浇注的时候变为气体因而形成的气孔,只要在合金化处理时把合金块彻底的烘干就不会出现上述情况[4]。
4.9浇注及清砂
浇注步骤:
(1)在砂堆上推出一块平整的地方,把烘烤后的下箱放上,在型腔内需要进行表面合金化的地方用钉子固定烘烤好的合金块,注意固定时一定要小心不要破坏砂型。
(2)抬起上箱,从垂直于下箱的方向竖直合箱,如果位置不正确,应抬起从新合箱不可用推移的方式,以防破坏砂型或者把杂物推进型腔内。
(3)在直浇口和冒口处分别放上选取的浇口杯和冒口,在浇口杯和冒口与上箱连接处堆放混制后的型砂并轻轻紧实,注意堆放型砂时不要让型砂堵塞了出气孔;在上箱适当位置放上压铁,选择的压铁应尽可能的平整宽大以使砂型受力均匀。
(4)抬起浇包,把浇包内的合金液从浇口杯浇如型腔,浇注时应先慢后快,在选择的浇注时间内完成浇注;浇注时注意用点火装置在冒口和出气孔处点火,燃烧掉型腔内因高温产生的气体,这样作不但可以保证浇注过程的安全防止爆箱,还可以减少铸件的气孔内缺陷。
(5)浇注完毕,让铸件在砂箱内自然凝固(2h以上),这样得到的铸件组织才是接近平衡太的组织。
实际的合箱如图9。
清砂步骤:
小件落砂清理的流程如图10
图10清砂流程图
本次实验的清砂步骤为:
(1)铸件完全凝固后,用锤头敲落型砂,取出铸件,用锤头敲下浇注系统和冒口。
(2)用锤头敲击用震动的方式去除铸件表面的粘砂。
清理后的铸件如图形11
4.10热处理
根据导卫板的使用条件,本次实验确定用淬火加回火的热处理工艺。
分别利用硬度剂测量式样的硬度和用光学显微镜观察式样的显微组织。
清砂后用锤头从导卫板上敲下三块大小适中的式样。
对每一块式样进行编号,分好每一块式样将作那些实验。
将式样加热至950℃(300℃/h),保温2h,风吹强制冷却(空淬),250℃保温1h回火(随炉冷。
具体的加热曲线如图8所示[6][11]。