基于PLC压力控制系统毕业设计.doc
《基于PLC压力控制系统毕业设计.doc》由会员分享,可在线阅读,更多相关《基于PLC压力控制系统毕业设计.doc(51页珍藏版)》请在冰点文库上搜索。
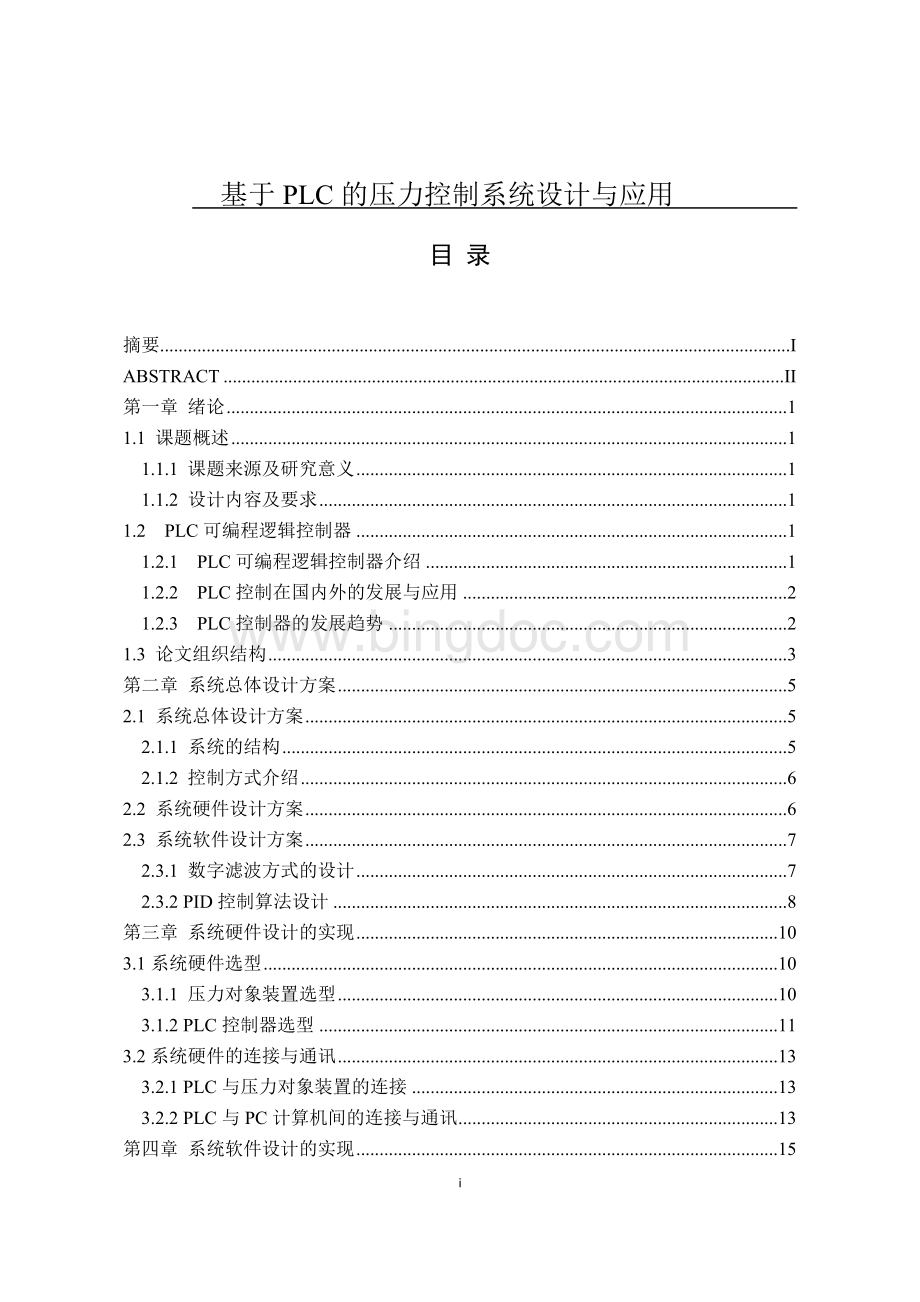
基于PLC的压力控制系统设计与应用
目录
摘要 I
ABSTRACT II
第一章绪论 1
1.1课题概述 1
1.1.1课题来源及研究意义 1
1.1.2设计内容及要求 1
1.2PLC可编程逻辑控制器 1
1.2.1PLC可编程逻辑控制器介绍 1
1.2.2PLC控制在国内外的发展与应用 2
1.2.3PLC控制器的发展趋势 2
1.3论文组织结构 3
第二章系统总体设计方案 5
2.1系统总体设计方案 5
2.1.1系统的结构 5
2.1.2控制方式介绍 6
2.2系统硬件设计方案 6
2.3系统软件设计方案 7
2.3.1数字滤波方式的设计 7
2.3.2PID控制算法设计 8
第三章系统硬件设计的实现 10
3.1系统硬件选型 10
3.1.1压力对象装置选型 10
3.1.2PLC控制器选型 11
3.2系统硬件的连接与通讯 13
3.2.1PLC与压力对象装置的连接 13
3.2.2PLC与PC计算机间的连接与通讯 13
第四章系统软件设计的实现 15
4.1PLC控制程序 15
4.1.1STEP7软件介绍 15
4.1.2PLC硬件组态 15
4.1.3PLC控制程序的实现 16
4.2上位机实时监控程序 22
4.2.1WinCC组态软件介绍 22
4.2.2实时监控程序的实现 23
第五章系统投运与调试 29
5.1系统运行方法 29
5.2系统的调试 29
5.2.1硬件间的通讯状态的诊断 29
5.2.2PID参数的整定 31
5.2.3调试过程中的问题及其解决办法 41
第六章总结与展望 43
6.1课题研究总结 43
6.2后续工作展望 44
结束语 45
参考文献 46
ii
摘要
鉴于压力控制在工业中的广泛应用,研究PLC在压力控制系统中的应用是教学乃至实践技能培养的一个很重要的环节。
本课题针对实验室现有的压力控制对象,提出了一种基于PLC的压力控制系统的设计方案,该系统采用两级计算机控制,底层选用PLC作为控制器,上层选用PC计算机为上位机。
本次设计系统以西门子S7-300PLC为控制器,采用STEP7软件构造系统硬件组态和编写控制程序,完成现场压力信号的数据采集、数字滤波和PID自动控制。
上位PC机选用工业组态软件WinCC编写监控界面,完成对现场的实时监控和数据的存储,并能对现场工艺过程进行模拟动态以及显示实时趋势曲线。
在实验室调试过程中,系统软件运行良好,系统实现了数字PID调节,监控界面基于WINDOWS,操作简便,具有较强的可靠性和实用性,满足现场控制的要求,达到了设计目标。
关键词PLC控制器,WinCC组态,压力过程控制,PID控制算法
47
ABSTRACT
Sincepressurecontrolsystemwaswidelyusedintherealmsofindustrialcontrol,theresearchoftheapplicationofPLCinpressurecontrolsystemisaveryimportantlinkforteachingandpracticalskillstraining.Accordingtopressurecontrolobjectinthelaboratorycurrently,thisessayproposedadesignproposalofpressurecontrolsystembasedonPLC.Thesystemisconsistoftwolayersofcomputercontrol.PLCcontrollerperformsastheslavecomputerinabaselayer,whileaPCfunctionsasthehostcomputerintheupperlayer.
ThesystemuseSiemensS7-300PLCforcontroller,andsoftwareSTEP7forboththeconfigurationofthePLChardwareandthedesigningofcontrolprogram,toaccomplishthedataacquisition,digitalfilteroffieldpressuresignalandPIDautocontrol.OnthePC,WinCC(adustrialconfigurationsoftware)isameansofcompilingthemonitoringandcontrollinginterface,toaccomplishthereal-timemonitoringanddatastorage,andbeabletosimulatetheprocessofdynamicprocessanddisplaythereal-timetrendcurve.
Duringthecommissioningprocessinthelaboratory,softwareofthesystemrunswell.ThesystemrealizedthedigitalPIDregulating,duetotheWINDOWS-basedmonitoringinterface,thesystemwaswithadvantagesineasyoperation,strongreliabilityandpracticability.Thesystemsatisfiedcontrolrequirements,andreachedthetargetofthedesign.
KEYWORDS PLCController,WinCCConfiguration,PressureProcessControl,PIDControl
基于PLC的压力控制系统设计与应用第一章绪论
第一章绪论
1.1课题概述
1.1.1课题来源及研究意义
该课题来源于中南大学信息科学与工程学院过程控制实验室的教师科研题,题目类型属于实验研究。
在一些生产现场,如各种冶炼生产中,容器罐内气体压力必须保持在一定的范围内,反应才可以正常进行。
适宜的压力下,反应速率可以达到最高,而且原料和催化剂的利用更为彻底。
可见,压力过程控制是一项富有意义的研究。
随着技术的发展,PLC的性能不断提高,其价格也能让更多的中小型企业接受。
近年来,越来越多的中小设备开始采用PLC进行控制,PLC在我国的应用增长十分迅速。
本课题研究的基于PLC的压力控制系统接线简单、可移植性强、灵活方便、具有强大的人机交互功能,并且可以实现在线调试,将在工业生产中得到广泛应用。
1.1.2设计内容及要求
本课题的设计内容是基于PLC的压力控制系统设计与应用,即设计一个以S7-300PLC为控制器的压力控制系统,根据过程压力系统的控制要求选用合适的检测装置和执行机构,实现压力过程量的自动控制。
系统要求采用两级计算机控制,底层选用PLC作为控制器,上层选用PC计算机为监控机,用WinCC组态软件编制上位机的监控软件,完成人机界面的控制功能,实现一套完整的集测量、控制、组态、监视为一体的压力自动控制系统。
1.2PLC可编程逻辑控制器
1.2.1PLC可编程逻辑控制器介绍
可编程逻辑控制器(ProgrammableLogicController),简称PLC,在二十世纪六十年代美国推出,主要用来取代传统继电器实现逻辑控制[1]。
20世纪70年代,人们将微机技术应用到PLC中,使得其更多的发挥计算机的功能,远远超过了逻辑控制的范围,从而真正成为一种电子计算机工业控制设备。
随着计算机技术、信号处理技术、控制技术网络技术的不断发展和用户需求的不断提高,PLC在开关量处理的基础上增加了模拟量处理和运动控制等功能。
今天的PLC不再局限于逻辑控制,在运动控制、过程控制等领域也发挥着十分重要的作用。
PLC可以直接应用于工业环境,具有很强的抗干扰能力,广泛的适应能力和应用范围。
1.2.2PLC控制在国内外的发展与应用
在工业控制自动化领域,PLC是一种重要的控制设备,它代表着当前程序控制的先进水平。
无论是从国外引进的自动化生产线,还是国内自行生产设计的自动控制系统,都可以看到PLC的身影。
可以说,PLC装置已成为自动化系统[2]的基本装置。
20世纪末期,可编程控制器的发展特点是更加适应于现代工业的需要。
从控制规模上来说,这个时期发展了大型机和超小型机;从控制能力上来说,诞生了各种各样的特殊功能单元,用于压力、温度、转速、位移等各式各样的控制场合[3];从产品的配套能力来说,生产了各种人机界面单元、通信单元,使应用可编程控制器的工业控制设备的配套更加容易。
目前,可编程控制器在机械制造、石油化工、冶金钢铁、汽车、轻工业等领域的应用都得到了长足的发展。
目前,全世界PLC生产厂家约200家,生产300多种产品。
国内PLC市场仍以国外产品为主,如Siemens、Modicon、A-B、OMRON、三菱、GE的产品。
我国可编程控制器的引进、应用、研制、生产是伴随着改革开放开始的。
最初是在引进设备中大量使用了可编程控制器。
随后在各种企业的生产设备及产品中不断扩大了PLC的应用[4]。
目前,我国自己已可以生产中小型可编程控制器。
可以预期,随着我国现代化进程的深入,PLC在我国将有更广阔的应用天地。
我国的PLC生产目前也有一定的发展,小型PLC已批量生产;中型PLC已有产品;大型PLC已开始研制。
国内PLC形成产品化的生产企业约30多家,国内产品市场占有率不超过10%,主要生产单位有:
苏州电子计算机厂、苏州机床电器厂、上海兰星电气有限公司、天津市自动化仪表厂、杭州通灵控制电脑公司、北京机械工业自动化所和江苏嘉华实业有限公司等。
国内产品在价格上占有明显的优势。
随着微处理器、网络通信、HMI界面技术的迅速发展,工业自动化技术日新月异,各种产品竞争激烈,新产品不断涌现。
PLC也由最初的只能处理开关量而发展到可以处理模拟量和数据,加之与DCS、PID调节器、工业PC等技术相结合,使之不再是一种简单的控制设备,而且必将随着自动控制技术的不断发展而发展生存下去。
1.2.3PLC控制器的发展趋势
PLC作为工控机的一员,在主要工业国家中成为自动化系统的基本电控装置。
它具有控制方便、可靠性高、容易掌握、体积小、价格适宜等特点。
据统计,当今世界PLC生产厂家约150家,生产300多个品种。
2000年销售额约为86亿美元,占工控机市场份额的50%,PLC将在工控机市场中占有主要地位,并保持继续上升的势头。
新一代的PLC具有PID调节功能,它的应用已从开关量控制扩大到模拟量控制领域,广泛地应用于航天、冶金、轻工、建材等行业。
但PLC也面临着其它行业工控产品的挑战,各厂家正采取措施不断改进产品,主要表现为以下几个方面:
①微型、小型PLC功能明显增强
很多有名的PLC厂家相继推出高速、高性能、小型、特别是微型的PLC。
三菱的FXOS14点(8个24VDC输入,6个继电器输出),其尺寸仅为58mm×89mm,仅大于信用卡几个毫米,而功能却有所增强,使PLC的应用领域扩大到远离工业控制的其它行业,如快餐厅、医院手术室、旋转门和车辆等,甚至引入家庭住宅、娱乐场所和商业部门。
②集成化发展趋势增强
由于控制内容的复杂化和高难度化,使PLC向集成化方向发展,PLC与PC集成、PLC与DCS集成、PLC与PID集成等,并强化了通讯能力和网络化,尤其是以PC为基的控制产品增长率最快。
PLC与PC集成,即将计算机、PLC及操作人员的人—机接口结合在一起,使PLC能利用计算机丰富的软件资源,而计算机能和PLC的模块交互存取数据。
以PC机为基的控制容易编程和维护用户的利益,开放的体系结构提供灵活性,最终降低成本和提高生产率。
③向开放性转变
PLC曾存在严重的缺点,主要是PLC的软、硬件体系结构是封闭而不是开放的,绝大多数的PLC是专用总线、专用通信网络及协议,编程虽多为梯形图,但各公司的组态、寻址、语文结构不一致,使各种PLC互不兼容。
现在,以PC为基础、在WINDOWS平台下、符合IEC1131-3国际标准的新一代开放体系结构的PLC的开发正在规划中。
1.3论文组织结构
本文主要研究基于PLC的压力过程控制系统的设计与应用,本文的篇章结构安排如下:
第一章绪论,介绍了此次研究的课题,以及PLC控制器和该领域的研究现状,最后阐述了本文的篇章结构。
第二章系统总体设计方案,介绍了系统的结构和控制方式,以及系统软硬件设计方案。
第三章系统硬件设计的实现,介绍了系统的硬件选型,以及各部分之间的连接与通讯。
第四章系统软件设计的实现,介绍了STEP7软件平台上PLC控制程序的编程,以及WinCC组态软件平台上实时监控程序的编程。
第五章系统的运行和调试,介绍了系统投运的方法和步骤,以及PID参数的整定,并且讲述了系统调试过程中遇到的问题及其解决方法。
最后一章为总结与展望,对课题的研究进行总结,并提出今后研究的问题与方向。
基于PLC的压力控制系统设计与应用第二章系统总体设计方案
第二章系统总体设计方案
2.1系统总体设计方案
系统的总体设计包含硬件设计和软件设计两个方面。
根据课题的要求和中南大学过程控制实验室提供的设备,系统控制对象选用三个压力容器作为被控对象,底层采用PLC作为控制器,上层采用普通的PC机作为上位机。
系统软件设计主要包括PLC控制程序和上位机监控程序的设计,采用STEP7和WinCC工具软件进行软件开发,这两款软件是西门子公司针对PLC控制器推出的。
2.1.1系统的结构
基于PLC的压力过程控制系统[5]的被控对象是由三个压力容器对象组成,可以根据需要构成不同阶(1阶、2阶[6]或3阶)的被控对象,如图2.1所示。
压缩空气经过两路进入压力容器中,经过两个流量调节阀,在单回路控制过程中,一路作为主回路,另一路作为干扰回路。
图2.1压力控制对象
如图2.1所示,1#、2#、3#压力罐为被控对象,三个气罐的压力信号分别由压力变送器[7]检测变成4~20mA的标准信号送入PLC(可编程控制器),PLC通过PID程序运算后,输出4~20mA的标准信号送给电动执行机构,由其控制阀门开度,调节气压,使气罐内的压力保持在给定的压力值上。
即当气罐内的压力大于或小于给定值时,PLC控制阀门开度,以达到减压或者加压的目的,实现气罐内的压力值保持在给定范围内。
系统采用两级计算机控制,底层选用PLC为控制器,上层选用PC机为监控机,用STEP7软件编写PLC控制程序,用WinCC组态软件编写上位机监控程序,完成对系统的实时监控。
系统结构框图如图2.2所示。
图2.2压力过程控制系统结构框图
2.1.2控制方式介绍
系统采用单回路控制方式,三个气罐的压力信号分别由检测装置进行实时检测,然后将被测信号转换为4~20mA的标准信号[8]送入PLC控制器,经过PID算法处理,PLC输出4~20mA的模拟信号给执行机构,对气罐的进气阀门进行控制,实现气罐中的气体压力自动控制。
系统单回路控制原理框图如图2.3所示。
图2.3系统单回路控制原理框图
2.2系统硬件设计方案
系统硬件主要由压力对象装置、PLC控制器以及PC计算机组成。
目前,全世界PLC控制器的厂家约200家,生产300多种产品,根据中南大学信息科学与工程学院过程控制实验室的提供的设备和调研结果,系统选用西门子公司的S7-300系列PLC为控制器,系统的总体硬件示意图如图2.4所示。
图2.4系统硬件示意图
底层PLC与压力对象的连接是通过模拟量输入输出模块,压力对象装置中的压力变送器将气罐内的压力信号转换为4~20mA的电流信号送入PLC的模拟量输入通道,在PLC中经过多种PID控制运算处理,由模拟量输出通道输出4~20mA的电流信号给压力装置中的电动执行机构,来控制气压的变化。
PLC与上位机PC计算机之间的通讯[9]有多种方式,由于被控对象只有一个,而且系统对PC计算机没有特殊的要求,因此这里采用的是TCP/IP通讯方式,简单方便。
PLC的通讯模块通过双绞线连接到交换机,PC计算机的网卡也用一根双绞线连接到交换机,从而PLC控制器和PC计算机可以通过IP协议进行通讯。
2.3系统软件设计方案
系统的软件设计主要包括两个方面:
PLC控制程序设计和上位机实时监控程序的设计。
其中,PLC控制程序采用西门子[10]的STEP7软件编程,先对系统的硬件进行组态,然后使用梯形图(LAD)编写采样滤波,输入输出线性转换,PID控制算法等程序。
上位机实时监控程序采用WinCC组态软件[11]编程,编制实时监控界面,完成对现场的实时监控和数据的存储,并能对现场工艺过程进行模拟动态以及显示实时趋势曲线。
2.3.1数字滤波方式的设计
PLC控制器可以对工业现场的各种被控对象(如温度、压力、流量、液位等)进行处理,在工业现场一般都会有瞬时干扰对信号的产生影响,系统采取数字滤波算法[12],来降低或消除采样过程中的噪声影响。
本设计中,PLC采用的数字滤波算法是平均值计算法,即对采样和模拟量/数字量转换得到多个数据,用算术平均值法求平均值,以此平均值作为模拟量/数字量转换的最终结果进行处理。
算术平均值法的算法公式为:
公式(2.1)
其中:
N—采样次数;Xi—第i次采样值;—平均值。
2.3.2PID控制算法设计
在控制工程中,PID控制[13]是应用最广泛的一种控制规律,它的参数整定方式简便,结构改变灵活。
PID控制表示比例(proportional)—积分(integral)—微分(differential)控制,连续系统的PID调节即为对误差的比例、积分、微分。
本设计中采用的几种控制算法就是基于PID的,包括位置式PID算法,增量式PID算法,以及在位置式上改进的积分分离PID算法、带死区的PID算法[13]。
1.位置式PID算法
位置式PID算法如公式2.2所示。
公式(2.2)
式中:
为积分时间常数,为微分时间常数,为控制周期,称为比例系数,为当前时刻的给定量和检测量的偏差。
2.增量式PID算法
增量式PID算法如公式(2.3)所示。
公式(2.3)
式中:
Du(kT)是控制器输出量的变化量,为当前时刻的给定量和检测量的偏差,为上一时刻的给定量和检测量的偏差,为两个时刻前的给定量和检测量的偏差,、、、同上。
增量式PID算法计算的是控制器输出量的变化量Du(k),不需要对偏差进行累加。
控制器输出量为,而。
3.积分分离PID算法
积分分离PID算法是在位置式PID算法上进行改进的,需要设置积分分离阈E0。
当时,也即偏差值比较小时,采用PID控制,可保证系统的控制精度。
当时,也即偏差值比较大时,采用PD控制,可使超调量大幅度降低。
积分分离算法可表示为公式2.4。
公式(2.4)
式中,Kl为逻辑系数,
4.带死区PID算法
带死区PID算法是在位置式PID算法上进行改进的。
对于带死区的PID算法,需要设定死区值,当时,调节器的输出前一个时刻的输出量,即。
当时,调节器才有PID输出。
带死区PID算法可表示为公式2.5。
公式(2.5)
以上几种基于PID的控制算法在控制效果上有所差异,在第五章中,对几种算法分别进行整定,并对各种算法进行了比较和分析。
基于PLC的压力控制系统设计与应用第三章系统硬件设计的实现
第三章系统硬件设计的实现
3.1系统硬件选型
系统硬件主要由压力对象、PLC控制器以及PC计算机三个部分组成。
目前世界上不乏生产PLC的厂家,主要的有:
德国的西门子(Siemens)公司,美国Rockwell公司所属的AB公司,GE-Fanuc公司,法国的施耐德(Schneider)公司,日本的三菱和欧姆龙(OMRON)公司。
根据课题的要求和中南大学过程控制实验室的条件,这里选用西门子公司的S7-300系列PLC,压力对象也选用实验室现有的压力对象实验装置。
3.1.1压力对象装置选型
该装置由三个互相串联的不同大小的压力容器、针型阀、压力及流量的检测[14]、变送、执行仪表等组成。
从控制角度来说,如第二章中图2.1所示,整个装置有三个压力检测变量(即1#、2#、3#罐的压力),从中选择一到两个作为被控变量。
装置还有两个可控变量,即两路经调节阀调节的压缩空气流量。
支路1的流量通常作为主控变量,而支路2则作为扰动输入。
1.压力变送器
压力变送器用于测量液体、气体或蒸汽的液位、密度和压力,然后将压力信号转变成4~20mADC信号输出。
压力变送器主要有电容式压力变送器和扩散硅压力变送器,陶瓷压力变送器,应变式压力变送器等。
一般意义上的压力变送器主要由测压元件传感器(也称作压力传感器)、测量电路和过程连接件三部分组成。
它能将测压元件传感器感受到的气体、液体等物理压力参数转变成标准的电信号(如4~20mADC等),以供给指示报警仪、记录仪、调节器等二次仪表进行测量、指示和过程调节。
本系统设计中,压力变送器采用湖南立升信息设备有限公司的型号为LSYB变送器,如图3.1所示,其量程均为0~80KPa,输出信号为4~20mA的标准电流信号。
2.电动执行器
电动执行机构一种能提供直线或旋转运动的驱动装置,它利用某种驱动能源并在某种控制信号作用下工作。
执行机构使用液体、气体、电力或其它能源并通过电机、气缸或其它装置将其转化成驱动作用。
目前的执行机构包含了位置感应装置,力矩感应装置,电极保护装置,逻辑控制装置,数字通讯模块及PID控制模块等,而这些装置全部安装在一个紧凑的外壳内。
本设计中选用湖南立升信息设备有限公司的型号为LSDZ的电子式电动执行机构,如图3.2所示,其动作范围为0~90°,定位精度和位置反馈精度均为0.6%,输入输出信号均为4~20mA标准电流信号。
图3.1LSYB压力变送器图3.2LSDZ电子式电动执行机构
3.1.2PLC控制器选型
本系统设计中采用西门子S7-300PLC为控制器,因为西门子S7-300系列PLC功能强大,采用模块化设计,有中央处理单元(CPU)、各种信号模块(SM)、通信模块(CP)、功能模块(FM)、电源模块(PS)、接口模块(IM)等,有多种规格的CPU可供选择。
本系统采用西门子S7-300系列,CPU为315-2DP的