制作与拼装施工方案Word文档格式.docx
《制作与拼装施工方案Word文档格式.docx》由会员分享,可在线阅读,更多相关《制作与拼装施工方案Word文档格式.docx(47页珍藏版)》请在冰点文库上搜索。
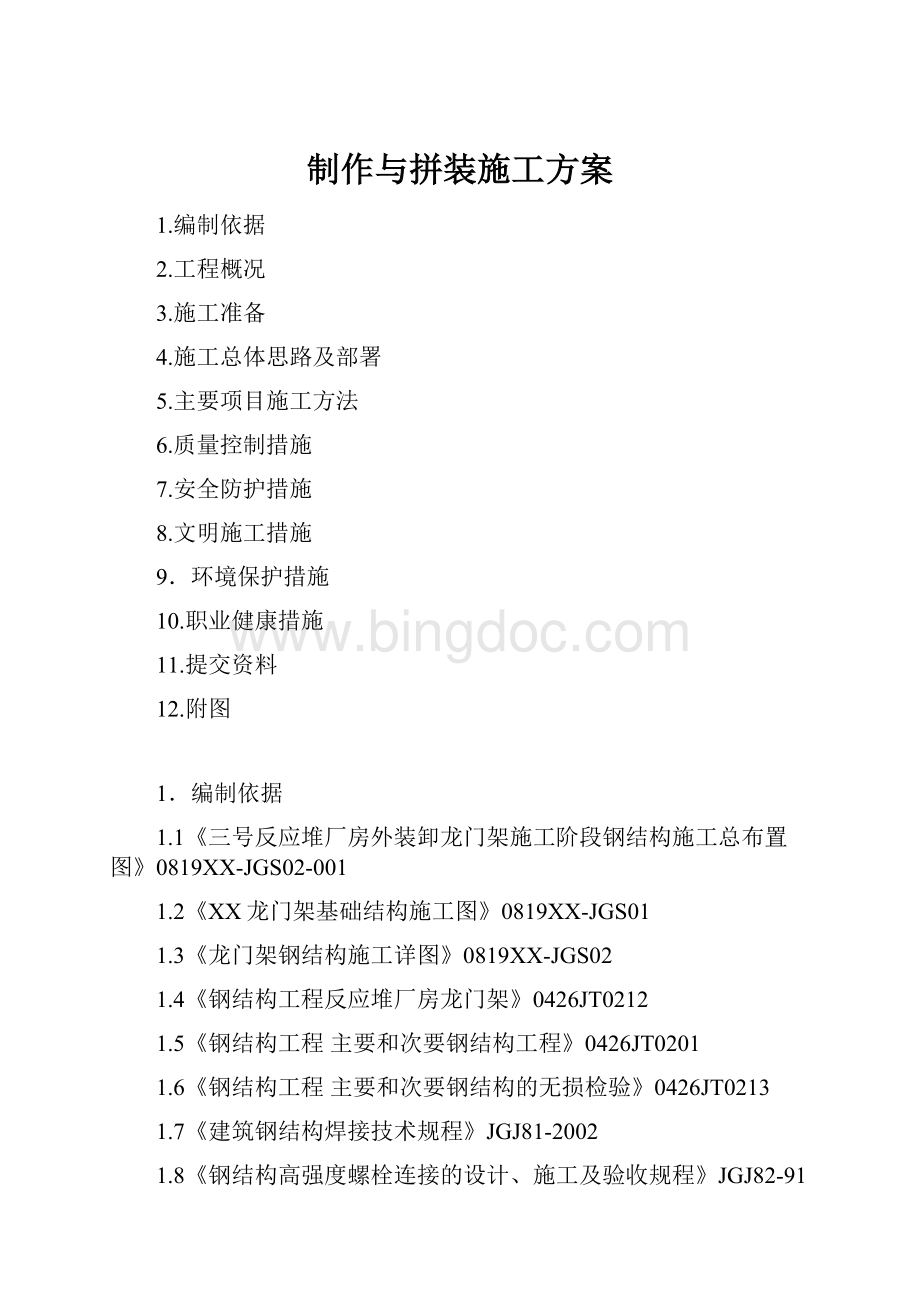
由四根大型箱型立柱、上下部桁架支撑、柱间横梁、柱间支撑、柱外侧支撑、700KN吊车梁、3800KN吊车梁、20.000m标高B、B’轴间操作平台、螺栓张拉机平台及维护结构等组成的大型焊接与栓接组合的钢结构工程。
龙门架油漆涂层系统为PEC200Ⅱ,面漆颜色为蓝色。
2.1钢柱概况
钢柱有A轴柱和B轴柱各两根箱形立柱,各柱由柱脚、柱身、柱帽三部分组成,其中柱脚板材质为Q390C,有长为4.4米的高强螺栓与之固定连接,每根螺杆下部焊接有与螺杆相同材质的锚固块。
钢柱总长度为30.650m,其中A柱每根重约30.8t,B柱每根重约38.6t。
A柱柱身截面1300×
920mm,柱脚由一块1350×
970×
120mm柱脚底板和一块转轴支座及一块板厚为125mm下部板组成。
在柱脚附近的柱身一侧腹板上设有一830×
830mm的人孔;
从柱脚沿柱身4787.5mm的柱身四壁设有T形加劲肋,接着T形加劲肋沿柱身高度四壁设有角钢加劲肋;
柱身横向设置若干横隔加强板,且每隔一个横隔板,以横隔板为中心在柱身腹板一侧预留600*1200mm的人孔;
28.065m标高A柱横梁的节点连接板直接与柱身横向连接;
柱帽由一块60mm厚的柱顶支撑,一块60mm厚加劲肋等组成。
B柱柱身截面1300×
1040mm,柱脚由一块1800×
1530×
120mm的柱脚板,六块120mm厚抗剪板,3块40mm厚的柱脚加劲板,六块螺栓垫板组成。
从柱脚沿柱身2880mm的柱身四壁设有T形加劲肋,接着T形加劲肋柱身高度四壁设有角钢加劲肋;
柱身横向设置若干加强隔板,且每隔一个横隔板,以横隔板为中心在柱身腹板一侧预留600*1200mm的人孔;
柱帽由一块上部支撑板,一块加劲肋等组成。
柱身的主要材料见附表1。
2.2桁架及支撑概况
龙门架桁架及柱间支撑共有六榀,其中上部桁架两榀,其弦杆由两块18mm厚钢板为翼缘与一块带有纵向加劲勒的腹板组成,腹杆形式采取人字形,斜杆由两块12mm厚钢板为翼缘与一块8mm厚钢板为腹板组成H型截面,竖杆一种采用H型截面钢组成,另一种由两块18mm厚钢板为翼缘与一块8mm厚钢板为腹板组成H型截面,外形尺寸为:
25.0m3.382m,每榀重量约为18.8t;
下部桁架两榀,其弦杆形式同上部桁架,腹杆形式采取X型,竖杆一种由两块18mm厚钢板为翼缘与一块8mm厚钢板为腹板组成H型截面,另一种由两块16mm厚钢板为翼缘与一块12mm厚钢板为腹板组成H型截面,斜杆采用两块翼缘板和一块腹板组成H型截面,尺寸为:
25.0m9.75m,每榀重量约为25.5t;
A、B轴柱间支撑各一榀,柱间支撑的弦杆由两块12mm厚钢板为翼缘与一块8mm厚钢板为腹板组成,腹杆体系为X型,由两翼缘与一腹板组成的H型截面,尺寸为:
7.5m3.6m,其中A轴支撑重量约为4.8t,B轴支撑重量约为5.6t。
主要材料表情况见附表2
2.3700KN吊车轨道梁与支撑平台梁概况
龙门架700KN吊车轨道梁标高为28.925m,作用是施工阶段协助3800KN吊车起吊重型设备时完成设备定向和定位之用和用于装卸轻型部件。
两根轨道梁分三个梁段,分别为中间梁段、位于B轴段梁与位于A轴段梁三部分,总跨度为27m,每根重约3.5t。
吊车轨道梁主要是由两大小不等翼缘及中间一腹板组成工字型梁,上部翼缘两侧分别设一加强腹板,翼缘与腹板之间设有若干纵向加强肋,另外在A轴、A’轴、B’轴、B轴,下翼缘处分别设支撑支座。
支承平台的B轴横梁,B’轴横梁,A轴横梁。
A轴横梁为工字梁,腹板上设有纵向、横向加强肋,梁尺寸为7500×
600×
1965mm,重约4t;
B轴横梁为箱形梁,梁上翼板设有重载轨道梁和运输轨梁的支墩,其一侧腹板和下翼板设有纵向加劲肋,在梁的两端各设三块隔板,梁尺寸7500×
1000×
1240mm,重约7.9t;
B’轴横梁为工字梁,梁尺寸7500×
300×
1280mm,重约4t;
腹板上设有纵向加劲肋和横向加强肋。
2.420.000m标高操作平台和螺栓张拉机平台工程概况
XX操作平台标高20.000m,并设有4根以设备闸门中心线为中线的轨道,通过活动连接平台与反应堆厂房内部结构相连,并将重型部件运入反应堆厂房。
它为核岛设备从外面转运进设备闸门的中转平台。
总长9770mm,宽9250mm,总重约为25.240t。
操作平台体系由平台下钢管支撑、平台骨架、花纹钢板面板三部份组成。
钢管支撑为A字形结构,主杆件为两根Φ273×
8的20#钢管,其余杆件采用Φ219.1×
6.3的20#钢管制成。
支撑长约8450mm,底宽约7520mm,重约1.423t。
平台骨架体系主要由H型钢和工字钢组成;
平台面板采用花纹钢板,约118m2。
操作平台骨架的连接形式为螺栓连接。
平台由两侧和中间三片组成。
两端支承在龙门架钢梁上,并用高强螺栓限位连接。
螺栓张拉机平台由平台支撑、平台骨架、花纹钢板面板及钢格栅板组成。
平台支撑、平台骨架体系主要由角钢、H型钢和工字钢组成;
面板A~A’轴线中部采用花纹钢板。
螺栓张拉机平台骨架的连接形式为螺栓连接。
2.53800KN吊车梁
3800KN吊车是在施工安装阶段用于起吊重型设备和运入反应堆厂房。
3800KN吊车对于3号反应堆龙门架,吊车在33.500m标高的上部轨道上运行。
轨道梁由上部翼缘为80mm厚钢板、下部翼缘为40mm厚钢板以及带有纵向加劲肋的22mm厚钢板为腹板组成工字梁。
轨道梁总长29m、跨度为25m,每根重约33.021t(不含支撑桁架)。
在轨道梁下部翼缘有两个支墩与A柱、B柱柱帽连接,轨道梁一侧还设有由型钢组成的框架支撑桁架,支撑桁架的连接、支撑桁架与吊车轨道梁的连接为栓焊组合连接。
2.6XX楼梯及爬梯概况
为了能够通至龙门架各个标高在0m标高到20m标高设有楼梯,在20m标高到33.715m设有爬梯。
楼梯位于B’与B柱之间,楼梯立柱之间的跨度为4075mm,在9.305m及19.055m处分别设有K型支撑。
楼梯两立柱采用HW250*250*9*14的型钢组成,楼梯走道平台及踏步板边缘采用[20b槽钢及L50×
50×
5作为支撑梁。
楼梯走道平台及踏步采用钢格栅板,在楼梯平台及走道边缘设有竖向栏杆以作防护之用,护栏杆与梯梁、平台梁之间用螺栓连接固定,竖向栏杆的安装详见标准图CSTN.29C002。
爬梯的制作详见建筑铁结构标准图CSTN.29C002。
2.7龙门架主体结构质保要求
钢柱、桁架及柱间支撑、轴间横向支撑、20.000m标高操作平台、吊车梁属于主要钢结构,质保等级为QA1级。
楼梯(爬梯)、工作走道等属于次要钢结构,其质保等级为QA3级。
2.8主要技术条件
2.8.1钢柱、桁架及柱间支撑、操作平台、吊车轨道梁,属于主要钢结构,其质保等级为QA1级。
楼梯(爬梯)属于次要钢结构,其质保等级为QA3级。
2.8.2龙门架钢结构各构件零件选用的钢材材质分别为:
低合金钢Q345B、Q345C、Q390B、Q390B-Z35、Q390C、Q390D;
碳素结构钢Q235A、Q235B、Q235C、Q235C-Z35;
法国标准钢材S355K2;
锻件材质20MnMoNb。
2.8.3龙门架钢结构的焊接方式采用手工电弧焊和埋弧焊,其中埋弧焊主要用于柱身、桁架、700KN吊车梁、3800KN吊车梁、平台梁将柱间横梁等的焊接。
对于碳素结构钢如Q235B、Q235C等的焊接,手工电弧焊接焊条选用E43XX型电焊条,埋弧焊焊丝及焊剂选用H08MnA+SJ14HR、H08MnHR+SJ14HR、H08MnA+F4A2等;
对低合金钢如Q345B、Q345C、Q390B等的焊接,手工电弧焊接焊条选用E50XX型电焊条,埋弧焊焊丝及焊剂选用H08MnA+SJ14HR、E5016、H10Mn2+F5A2;
对于20MnMoNb钢的焊接手工电弧焊焊条选用E50XX型。
焊接材料必须经质保评审合格后的生产厂家生产的焊接材料且进场后复验合格方可使用。
2.8.4龙门架的焊接按照《建筑钢结构焊接技术规程》JGJ81-2002执行;
焊缝等级依据技术规格书0426JT0212《钢结构工程反应堆厂房龙门架》和图纸要求分级;
焊缝分类以及相应的检验方式和检验范围依据技术规格书0426JT0201《钢结构工程主要和次要钢结构工程》;
无损检验依据技术规格书0426JT0213《钢结构工程主要和次要钢结构的无损检验》。
2.8.5龙门架的组装连接,龙门架构件在车间制作完成后,现场组装连接都是通过构件节点板螺栓连接。
普通螺栓和高强螺栓等的应用应符合现行国家标准要求。
2.8.6钢柱、桁架及支撑、钢平台、700KN吊车轨道梁等的制作、焊接、喷砂油漆和安装,应按设计规定的相应技术条件、规范和标准执行。
2.8.7各构件制作公差
2.8.7.1钢柱焊接连接制作组装的允许偏差:
——箱形截面高度h允许偏差±
2.0mm
——箱形截面宽度允许偏差±
——垂直度允许偏差b/200,且不应大于3.0mm
2.8.7.2钢柱外形尺寸允许偏差:
——构件长度公差±
——柱截面尺寸连接处允许偏差±
3.0mm,非连接处允许偏差±
4.0mm。
——翼缘板对腹板的垂直度允许偏差连接处1.5mm其它处b/100且5.0mm
——柱身弯曲矢高允许偏差H/1200且不应大于12.0mm
——柱身扭曲牛腿处3.0mm,其它处8.0mm
——柱脚底板平面度5.0mm
——柱脚螺栓孔中心对柱轴线的距离3.0mm
——箱型截面连接处对角线差:
3.0mm
——箱型柱身板垂直度:
h(b)/150且不应大于5.0mm
2.8.7.3700KN吊车轨道梁和3800KN吊车、20.000m平台轨道梁制造公差:
——上翼缘倾斜度公差(翼缘对水平面的倾斜),“L”指翼缘宽度L/100
——上翼缘凸起公差(上翼缘与翼缘低边之间的高差)L/100
——上翼缘跨间的垂直偏差1/1000
——上翼缘平整度3mm/m
——承压板高度公差(承压面已磨光)0~+2mm
——长度公差0~+5mm
——长度弯曲度公差(水平偏差)1/1000
2.8.7.4杆件制作的允许偏差:
项目
允许偏差(mm)
截面高度(h)
h500
±
2.0
500h1000
3.0
h1000
4.0
截面宽度(b)
腹板中心偏移
翼缘板垂直度
b/100且不应大于3.0
弯曲矢高
l/1000且不应大于10.0
扭曲
h/250且不应大于5.0
腹板局部平面度(f)
t14
t14
2.8.7.5制孔的允许偏差:
螺栓孔的允许偏差(mm)
项目
允许偏差
直径
0.0~+1.0
圆度
垂直度
0.03t,且不应大于2.0(t为部件厚度)
螺栓孔孔距的允许偏差(mm)
螺栓孔孔径范围
≤500
501~1200
1201~3000
>3000
同一组内任意两孔间距离
1.0
1.5
——
相邻两组的端孔孔间的距离
2.5
2.8.8焊缝检验说明如下表:
焊缝类型
检验方法
检验范围
A类
外观检验
100%
X射线或超声检验
B类
10%
C1类
液体渗透检验
C2类
D1类
D2类
D3类
注:
当焊缝为A类或B类时,1级焊缝必须经过100%超声波探伤。
焊缝类型表示方法,例如:
1A表示焊缝等级为1级,焊缝类型为A类,以此类推。
3.1人员配备
序号
人员配置
数量
备注
1
总工程师
1人
2
焊接工程师
3
热处理工程师
4
焊接及结构技术员
2人
5
工长
6
质检员
7
安全员
8
材料管理员
9
无损检测人员
4人
10
焊工
20人
11
自动埋弧焊工
3人
12
铆工
10人
13
起重工
14
气焊工
15
热处理操作工
16
测量工
17
电工
18
普工
若干
参与工程施工的工人和管理人员都要求经过质保培训,安全生产教育;
特种作业人员应具备相应的上岗资格,如焊工及焊接操作工必须按HAF603取得相应的资格证书,无损检测人员需取得《钢结构工程主要和次要钢结构的无损检验》0426JT0213相应的无损检测资格证书。
3.2主要设备机具和工具
3.2.1设备如下表:
设备名称
型号
行车10t
LD-10t
1台
行车5t
LD-5t
2台
龙门吊10t
M10t-22
铣边机
XBJ-15
剪板刀纵放联合冲剪机
Q34-16
车床
CA6140/1000
摇臂钻床
Z30505422
落地砂轮机
M3040
林肯埋弧焊机
DC1000
全纤维节能电阻炉
RBXD-150-7
温度程序控制箱
WCR360-1212
履带式加热器(带工装)
WCK-360.1212
箱式电阻炉
RX3-45-9
数控直条切割机
GS/2-4000
型钢门型自动埋弧焊
MZG-4000H
型钢翼缘液压矫正机
YJ-608H
松下焊机
YD-400AT
20台
远红外带贮藏室焊条烘箱
YXH2-100
19
磁力钻机
J3C-CX-28
4台
20
扭距扳手
AC(250-1000)N.m
2把
21
汽车吊
25t
22
50t
3.2.2工具:
螺旋千斤顶、螺旋式卡具、角磨机20个、钢尺2把、卷尺10把、直角尺5把、钢丝绳若干、卡兰若干、焊缝检验尺2把、温湿度计2个、测温仪1块、水平尺5把、测风仪1台等计量器具。
3.2.3设备要求运转正常可靠,检验仪器和计量器具经过检验合格并在标定有效期内,计量器具应具有有效标定。
3.3龙门架材料
龙门架钢结构在制作各分部分项工程前所用板材、型材、焊材、油漆等均应复验合格。
3.4施工方法
3.4.1主要项目施工方法
钢柱、桁架、吊车梁、轨道梁等制作工艺方法见“5.主要项目施工方法”。
3.4.2焊接方法
龙门架钢结构的焊接方式采用手工电弧焊和埋弧焊,其中埋弧焊主要用于柱身、桁架、700KN吊车梁、3800KN吊车梁、平台梁将柱间横梁等的焊接。
详见“2.8.3”。
3.4.3防腐
龙门架防腐施工按照《3、4号机组龙门架钢结构防腐施工方案》执行。
龙门架防腐工作在车间制作、现场拼装及现场安装各阶段都会涉及到,车间制作过程中注意高强螺栓摩擦面的处理及保护,现场拼装过程中防腐一定不能留死角,现场安装过程中防腐要根据安装顺序及施工操作空间确定防腐时机,但是,一定要在脚手架拆除前完成所有需要在现场进行的防腐工作。
3.5技术准备:
3.5.1完成施工转换图的编制,确保转换图与原设计要求相一致,并满足施工要求;
3.5.2组织施工人员熟悉图纸和相关技术及质量要求;
3.5.3编制质量计划,对龙门架中所涉及到的焊缝形式进行焊接工艺评定,根据焊接工艺评定报告编制生产时的焊接工艺卡;
3.5.4施工前进行技术交底,安全交底和相关程序的交底。
3.6施工场地的准备
3.6.1龙门架制作的场地准备
钢柱、桁架及支撑、700KN吊车轨道梁、钢平台等的制作在钢结构车间外龙门吊下面的场地上进行,场地布置见附图9。
制作平台应平整、牢固以满足焊接条件的要求。
场地上应有足够的空间,作为制作区和成品堆放区,成品堆放区与制作区要明显分开。
场地应与喷砂油漆车间联系方便,并且应配备起重运输设备,加工设备、焊接设备、热处理设备等。
3.6.2现场拼装的场地准备
在现场规划出用于钢柱、桁架、柱间支撑、3800KN吊车梁等的拼装场地,场地筑混凝土支墩或铺设钢平台,在上铺设钢板,在钢板上制作拼装胎具,采用测量方式控制拼装胎具整体平整度,场规划场地布置见附图10。
现场应配备起重设备、焊接设备及支架等。
钢柱Z-A1(除柱脚及节点后重13.388t)和Z-A2(除柱帽及节点后重13.543t)分二节制作,Z-B1(除柱脚及节点后重12.764t)和Z-B2(除柱帽及节点后重12.625t)分二节制作。
在现场将钢柱各节依次在拼装胎上进行拼装,拼装胎简图见附图4。
4.1施工总体思路
根据龙门架的结构特点及安装工序,先进行钢柱和桁架及柱间支撑、横梁的制作,再进行20.000m标高操作平台及吊车梁的制作,再进行楼梯及钢爬梯的制作,最后进行螺栓张拉机平台和维护的制作。
其中钢柱在车间分节制作,现场拼接;
柱身上桁架、柱间支撑安装节点待钢柱拼装好后再与钢柱焊接;
A轴柱身单根重量约30.8吨,根据蓝图将柱身划分成二节制作:
第一节,从柱底板至14.300米标高处,第二节到14.300至30.650米标高处;
B轴钢柱单根重量约38.6吨,根据蓝图将柱身划分成二节制作,第一节从柱底板至14.900米标高处,第二节从14.900至30.650米标高处,柱脚到现场再与第一节拼接。
A、B柱柱帽及A柱柱脚与柱身拼接可根据车间实际情况,尽可能在车间拼接好再出厂。
下部桁架的制作采取在车间制作杆件及连接节点,再现场组装;
其弦杆应分成三节制作,以A’节点和B’节点为分割点,节点单独制作。
上部桁架的上弦杆分三节制作,以A’节点和B’节点为分割点,下弦杆分成两节在车间制作,在现场拼装。
柱间支撑在车间制作,现场安装。
20.000m标高操作平台在车间制作,在现场安装。
3800KN吊车梁按图纸分两段制作,再到现场拼装,并安装完不影响吊装部分的工作走道及栏杆。
4.2施工部署
4.2.1钢构厂负责XX龙门架的制作、拼装及安装。
4.2.2工程运营部负责协调车间与各施工队的工程进度和关系。
4.2.3喷砂车间负责喷砂、油漆的施工。
4.2.4质量管理部负责XX龙门架制作与安装的质量和质保监查及与外部的接口工作。
4.2.5测量组负责测量工作。
4.2.6无损检测室负责XX龙门架的无损检测工作。
5.主要项目施工方法
5.1钢柱制作的施工方法及技术措施
5.1.1钢柱制作的主要工艺流程如下:
胎具制作→钢材矫正→放样→下料→边缘加工→零件装配焊接→(热处理)→变形矫正→柱节组装焊接→质量检查(包括无损检测)→除锈、喷漆→验收出厂→钢柱现场拼接→桁架及柱间支撑安装节点与柱身组装焊接→质量检查(包括无损检测)→尺寸验收
5.1.2钢柱下料:
根据下料图将构件尺寸参数输入到数控直条切割机下料,下料前核查图纸各零、部件的尺寸及输入零、部件尺寸参数,确定无误后再下料。
下料时,应留足工艺余量和焊接收缩量,其中工艺余量按板宽度方向上3~5mm,焊接收缩余量按每米2mm计算。
下料前,应首先对钢材进行调平校直,边缘要平齐,钢板整个厚度的切口要光洁,无撕裂或裂口等应满足GB50205-2001相应规定。
下料结束,应及时清理切割边缘和坡口加工,腹板和翼缘板坡口可进行铣边处理,休整隔板四条边的垂直度,以便保证腹翼板与隔板组对精度;
同时在第一节或第二节的一段长度方向上预留拼装余量。
特别是对柱脚基座板及垫块的加工,应保证表面的平整度,从而确保在组装时基座板和垫块之间的紧密接触。
5.1.3柱身的组对和焊接顺序:
柱身的制作在专门的制作胎具上进行,胎具图见附图1所示。
首先根据放样下料图进行腹翼板的拼接、检验,在下好的翼缘及腹板上划出角钢纵向加劲肋或T型加劲肋和隔板的位置轴线,再进行角钢纵向加劲肋或T型加劲肋与翼缘和腹板焊接,并校正好。
A柱5.200m和B柱3.000m标高处的柱身四壁的T型加劲肋的翼缘板弯曲采用热弯方法进行。
钢柱柱身组对顺序是:
a.在胎具上组对两个翼缘和一个腹板,校正检查尺寸后,在焊翼缘和腹板内侧点焊固定;
b.加强隔板组对到翼缘和腹板上并点焊固定,接着完成角钢加劲肋和隔板的焊接、检验;
c.组对最后一块腹板与隔板点焊固定并焊接腹翼板焊缝,再翻身,焊接隔板及角钢加劲肋及腹翼板的焊接(参照附图2进行)。
由于钢柱分两节制作使翼板构件尺寸较长,焊接及吊装时注意构件变形,在有必要的情况下进行加固。
柱帽、柱脚组对和焊接顺序:
B柱柱脚先在底座板正反面上划出抗剪锚固板等位置线,检查无误后,将抗剪锚固板焊好,然后翻身焊接其它加劲肋等构件。
B柱脚的组对和焊接顺序见附图3进行。
A柱脚的组对和焊接顺序参考B柱脚的组对和焊接顺序进行。
焊接时先焊靠近中心的焊缝,而后焊接其它焊缝。
5.1.4钢柱的现场拼装和焊接顺序:
根据柱节长度布置混凝土支墩(拼装胎),并在支墩上安装预埋铁件,以柱脚和柱帽的两支墩为基准,调整其余支墩的位置并用水准仪或张紧的细钢丝抄平支墩的支撑面,然后在预埋件上焊接固定支架,并用张紧的细钢丝来保证固定支架的轴线。
在每节柱身两端腹板和翼缘板的中心线上打上样冲,以便在施工时进行校核。
并在接头附近的腹板和翼缘上焊接两个用于调节柱间距的耳板,耳板见附图5。
先拼装第一节