模具设计异形垫片冲压模具毕业设计Word格式.docx
《模具设计异形垫片冲压模具毕业设计Word格式.docx》由会员分享,可在线阅读,更多相关《模具设计异形垫片冲压模具毕业设计Word格式.docx(41页珍藏版)》请在冰点文库上搜索。
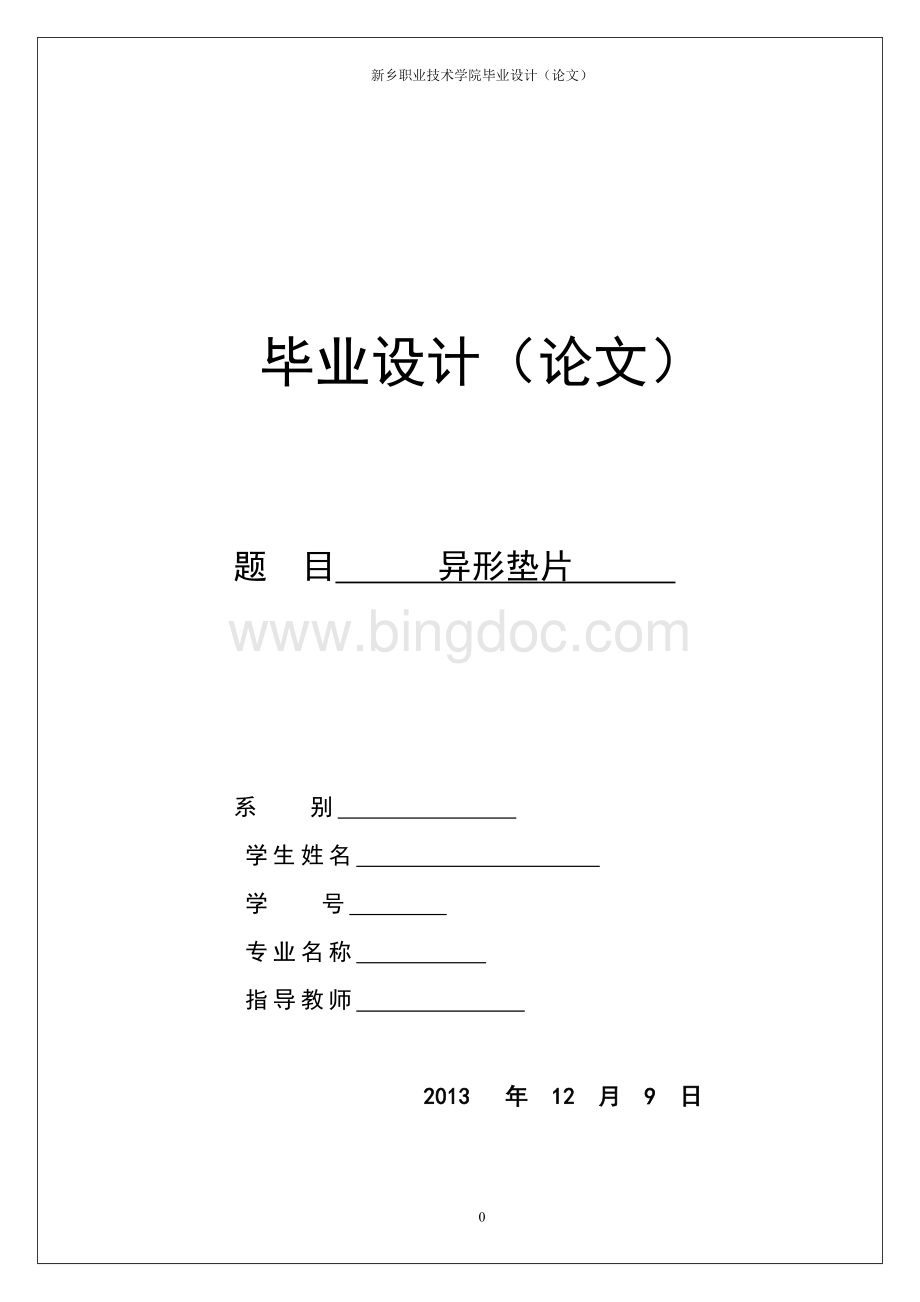
摘要…………………………………………………………………………………2
目录……………………………………………………………………………………4
一、冲裁件的工艺分析….……………………………………………………7
1.冲裁工艺方案的确定………………………………………………………………7
二、工艺与设计计算……………………………………………………………8
2.1.排样设计算………………………………………………………………………8
2.2.搭边值得确定……………………………………………………………………9
2.3.送料进距…………………………………………………………………………10
2.4.条料宽度确定……………………………………………………………………11
2.5.材料利用率计算…………………………………………………………………12
2.6.压力机的选用………………………………………………………………….13
2.7.计算凸凹模刃口尺寸及公差………………………………………………….16
2.8.刃口计算……………………………………………………………………….19
三、模具的总体设计………………………………………………………21
3.1.模具类型的选择………………………………………………………………21
3.2.操作与定位方式的选择………………………………………………………21
3.3.卸料方式的选择………………………………………………………………22
3.4.出件与送料方式的选择………………………………………………………22
3.5.导向方式的选择………………………………………………………………22
四、模具零件的设计…………………………………………………………23
4.1.定位零件的设计………………………………………………………………23
4.2.卸料部件的设计………………………………………………………………26
4.3.工作零件的设计………………………………………………………………26
4.4.模架的设计……………………………………………………………………29
4.5.其他零部件的设计……………………………………………………………31
五、制定模具零件加工工艺过程………………………………………32
5.1.冲孔凸模加工工艺过程………………………………………………………32
5.2.落料凸模加工工艺过程………………………………………………………32
六、模具图纸绘制……………………………………………………………32
6.1.模具装配图的设计绘制………………………………………………………33
6.2.模具零件图的设计绘制………………………………………………………35
七、模具的装配………………………………………………………………37
设计总结…………………………………………………………………38
参考文献……………………………………………………………………39
致谢………………………………………………………………………40
设计任务书
设计课题:
异形垫片的冲压模具设计
冲压件名称
材料
板厚
工件精度
异形垫片
H68
0.15mm
IT13
工件图
设计要求:
1.绘制该工件的零件图和三维实体图。
2.确定该零件的冲压工艺方案,编写工艺卡。
3.绘制该工件制作所需模具的总装配图。
4.绘制该模具的凹模凸模零件图。
5.编写完善的设计说明书。
一、冲裁件的工艺分析
该零件是许多机械上使用的手柄,要对该零件进行中批量生产,外精度不高,只需平整,圆孔是该零件需要保证的重点。
1.1.冲裁工艺方案的确定
该制件的冲裁工序包括落料和冲孔,其冲裁加工有以下三种方案:
方案一:
先冲孔,后落料。
单工序模生产。
方案二:
冲孔—落料复合冲压。
复合模生产。
方案三:
冲孔—落料级进冲压。
级进模生产。
表各类模具结构及特点比较
模具种类
比较项目
单工序模
复合模
级进模
无导向
有导向
零件公差等级
低
一般
可达IT10~IT8级
可达IT13~IT10级
零件特点
尺寸不受限制厚度不受限制
中小型尺寸厚度较厚
形状与尺寸受模具结构与强度限制,尺寸可以较大,厚度可达3mm
小零件厚度0.1~6mm可加工复杂零件,如宽度极小的异形件
零件平面度
由于压料冲件的同时得到了较平的制件,制件平直度好且具有良好的剪切断面
中小型件不平直,高质量制件需较平
生产效率
较低
冲件被顶到模具工作表面上,必须手动或机械排除,生产效率较低
工序间自动送料,可以自动排除制件,生产效率高
安全性
不安全,需采取安全措施
比较安全
模具制造工作量和成本
比无导向的稍高
冲裁较复杂零件时,比级进模低
冲裁简单的零件时,比复合模低
适用场合
料厚精度要求低的小批量冲件的生产
平直度要求高的中小型制件的大批量生产
大批量小型冲压件的生产
方案一模具结构简单,投资少,且每次冲裁所需的冲裁力较小,可以解决冲压设备吨位不够的问题。
其缺点在于零件的精度难于保证,并且零件比较小,在第二次冲孔时,准确定位不宜,容易使人受伤,生产率低。
单冲模结构简单,制造成本低,易于加工和模具的维修,适用于小批量或试制件。
方案二也只需一副模具,制件精度和生产效率都较高,且工件最小壁厚大于凸凹模许用最小壁厚,模具强度也能满足要求。
模具零部件加工制造比较困难,成本较高,并且凸凹模容易受到最小壁厚的限制,而使得一些内孔间距、内孔与边缘间距较小的下件不宜采用。
方案三只需一副模具,生产效率高,模具寿命长,操作方便,精度也能满足要求,生产成本较低,
通过对上述三种方案的分析比较,采用级进模较合理,精度较高。
二、工艺与设计计算
2.1.排样设计与计算
冲裁件在板料、带料或条料上的布置方法称为排样。
排样的意义在于减小材料消耗、提高生产率和延长模具寿命,排样是否合理将影响到材料的合理利用、冲件质量、生产率、模具结构与寿命。
根据材料经济利用程度,排样方法可以分为有废料、少废料和无废料排样三种,根据制件在条料上的布置形式,排样有可以分为直排、斜排、对排、混合排、多排等多重形式。
因此有下列三种方案:
有废料排样沿冲件外形冲裁,在冲件周边都留有搭边。
冲件尺寸完全由冲模来保证,因此冲件精度高,模具寿命高,但材料利用率低。
少废料排样因受剪切条料和定位误差的影响,冲件质量差,模具寿命较方案一低,但材料利用率稍高,冲模结构简单。
无废料排样冲件的质量和模具寿命更低一些,但材料利用率最高。
通过上述三种方案的分析比较,综合考虑模具寿命和冲件质量,该冲件的排样方式选择方案一为佳。
考虑模具结构和制造成本有废料排样的具体形式选择直排最佳。
2.2.搭边值得确定
排样时零件之间以及零件与条料侧边之间留下的工艺余料,称为搭边。
搭边的作用是补偿定位误差,保持条料有一定的刚度,以保证零件质量和送料方便。
搭边过大,浪费材料。
搭边过小,冲裁时容易翘曲或被拉断,不仅会增大冲件毛刺,有时还会拉入凸、凹模间隙中损坏模具刃口,降低模具寿命。
或影响送料工作。
根据制件厚度与制件的排样方法查表2-1得:
两制件之间搭边值=1.8mm.
侧搭边值a=2.0mm.
表2-1搭边值和侧边值
材料厚度t
圆件及r>2t圆角
矩形边长l≤50
矩形边长l>50或圆角r≤2
工件间
侧边a
工件间a
侧边
工件间
侧边a
0.25以下
1.8
2.0
2.2
2.5
2.8
3.0
0.25~0.5
1.2
1.5
0.5~0.8
1.0
0.8~1.2
0.8
1.2~1.5
1.9
1.6~2.0
2.0~2.5
2.5~3.0
3.0~3.5
3.2
3.5~4.0
3.5
4.0~5.0
4.0
4.5
5.0~12
0.6t
0.7t
0.8t
0.9t
2.3.送料进距
条料在模具上每次送进的距离称为送料进距,每个进距可冲出一个或多个零件。
A=D+
式中D——平行于送料方向的冲裁件宽度
——冲裁件之间搭边值
根据公式:
A=D+=55+1.8=56.8mm
模具相对于模架是采用从前往后的纵向送料方式,还是采用从右往左的横向送料方式,这主要取决于凹模的周界尺寸。
如:
L<B时,采用纵向送料方式;
L>B时,则采用横向送料方式;
L=B时,纵向或横向均可。
就本模具而言,采用横向送料方式。
(注:
L为送料方向的凹模长度;
B为垂直于送料方向的凹模宽度)。
图排样形式
2.4.条料宽度确定
(1).计算板料宽度
因为采用了有废料排样,沿制件部分外形冲裁,所以条料宽度为49mm.
(2).确定板料规格
选用H68板料,采用板料的长度为500mm,宽度为49mm,采用横裁的方法
排样方式和搭边值确定以后,条料的宽度也就可以设计出。
计算条料宽度有三种情况需要考虑:
(1)有侧压装置时条料的宽度。
(2)无侧压装置时条料的宽度。
(3)有定距侧刃时条料的宽度。
本设计采用的是无侧压装置的模具。
无测压装置的模具,其条料宽度应考虑在送料过程中因条料的摆动而使侧面
搭边减小。
为了补偿侧面搭边的减小部分,条料宽度应增加一个可能摆动量。
即:
B=[D+2(a+δ)+c]
式中B——条料宽度基本尺寸;
D——条料宽度方向零件轮廓的最大尺寸;
a——侧搭边值;
δ——条料下料剪切公差
c——条料与导板之间的间隙
表剪切公差及条料与导料板之间间隙
条料宽度B
条料厚度t
≤1
>1-2
>2-3
>3-5
δ
c
≤50
>50-100
>100-150
>150-220
>220-300
0.4
0.5
0.6
0.7
0.1
0.2
0.3
0.9
1.1
1.3
跟据零件图查上表确定剪料公差及条料与导板之间的间隙δ=0.5,c=0.1。
B=[D+2(a+δ)+c]
=[45+2(2.2+0.4)+0.1]
=59.7mm
2.5.材料利用率计算
材料利用率
单个零件的材料利用率η=S/S0×
100%=S/AB×
100%
冲裁面积S
S=45×
55=2475 ㎜
n=1B=49L=55+1.8=56.8㎜
S—冲裁件面积
S0—所用材料面积,包括工件面积与废料面积
B—调料宽度
A—送料步距
n—一个步距内冲件数
=S/AB=×
100%≈89%
由此可知,η值越大,材料的利用率就越高,废料越少。
工艺废料的多少决定于搭边和余量的大小,也决定于排样的形式和冲压方式。
因此,要提高材料利用率,就要合理排样,减少工艺废料。
2.6.压力机的选用
冲裁时,压力机的公称压力必须大于或等于冲裁各工艺力的总和。
平刃口模具冲裁力,Fp=KPLtτ
查常用黄铜的力学性能表得
σ=530—660Mpa取σ=600Mpa
查表得K=0.06K=0.07
F=Ltσb=172×
0.15×
600≈15480N
F冲孔=Ltσb=106.76×
600=9608.4N
FQ=KFP=0.06×
15480=874.8N
FQ1=nk1FP=6×
0.07×
15480=6501.6N
FQ2=K2FP=0.08×
15480=1238.4N
F总=Fp+FQ+FQ1=22856.4N
冲压设备属锻压机械。
常见的冷冲压设备有机械压力机(以表示其型号)和液压机(以表示其型号)。
常用冷冲压设备的工作原理和特点如表:
表常用冷冲压设备的工作原理和特点
类型
设备名称
工作原理
特点
机械式
压力机
摩擦压力机
利用摩擦盘与飞轮之间相互接触传递动力,皆助螺杆与螺母相对运动原理而工作。
结构简单,当超负荷时,只会引起飞轮与摩擦盘之间的滑动,而不致损坏机件。
但飞轮轮缘摩擦损坏大,生产率低。
适用于中小件的冲压加工,
曲柄式压力机
利用曲柄连杆机构进行工作,电机通过皮带轮及齿轮带动曲轴传动,经连杆使滑块作直线往复运动。
生产率高,适用于各类冲压加工。
高速压力机
工作原理与曲柄压力机相同,但其刚度、精度、行程次数都比较高,一般带有自动送料装置、安全检测装置等辅助装置。
生产率很高,适用于大批量生产,模具一般采用多工为级进模。
液压机
油压机
水压机
利用帕斯卡原理,以水或油为工作介质,采用静压力传递进行工作,使滑块上、下往复运动。
压力大,而且是静压力,但生产率低。
适用于拉深、挤压等成形工序。
表2-4J23系列开式双柱可倾压力机主要技术参数
技术参数
代号
单位
型号
J23-3.15
J23-6.3
J23-10
J23-16
J23-25
J23-35
J23-40
滑块公称压力
Pe
KN
31.5
63
100
160
250
350
400
滑块行程
S
mm
25
35
45
55
65
封闭高度
120
150
180
220
270
290
330
连杆调节量
30
60
滑块中心线至机身距离
90
110
130
200
滑块地面尺寸
左右
a
140
170
300
前后
b
260
模柄孔尺寸
直径
d
40
50
深度
l
70
垫块厚度
最大倾斜角
°
工作台尺寸
310
370
450
560
610
700
240
380
460
根据冲压力的计算,选择开式双柱可倾压力机的型号为J23-40
(1)压力机的校核
(1)工称压力:
型号J23-40压力为400KN得以校核
(2)滑块行程:
材料厚度t=0.15mm,导料板厚度10mm,凸模进入凹模的最大深度15mm,S1=0.15mm+10mm+15mm=28mm<S=55mm得以校核
(3)行程次数:
次数为80/min,因为大批量生产,有是手工送料,得以校核
(4)闭合高度:
闭合高度H:
在本模具中模具闭合高度为上模座、下模座、垫板、凸模、凸凹模厚度的总和。
即
H=45+30+30+24+10+45+41=225mm
经计算该模具闭合高度H=225mm,开式双柱可倾式压力机J23—40(330mm)满足要求,得以校核。
(2)压力设备的选用
通过校核,选择开式双柱可倾式压力机J23—40能满足使用要求。
其主要技术参数如下:
公称压力:
400kN
滑块行程:
80mm
最大闭合高度:
330mm
工作台尺寸(前后×
左右):
460mm×
700mm
垫板尺寸(厚度):
10mm
2.7.计算凸凹模刃口尺寸及公差
(1)冲裁间隙的确定
图2-4冲裁间隙
①间隙对冲裁件尺寸精度的影响
冲裁件的尺寸精度是指冲裁件的实际尺寸与基本尺寸的差值,差值越小,则精度越高,这个差值包括两方面的偏差,一是冲裁件相对于凸模或凹模的偏差,二是模具本身的制造偏差。
②间隙对模具寿命的影响
模具寿命受各种因素的综合影响,间隙是也许模具寿命诸因数中最主要的因数之一,冲裁过程中,凸模与被冲的孔之间,凹模与落料件之间均有摩擦,而且间隙越小,模具作用的压应力越大,摩擦也越严重,所以过小的间隙对模具寿命极为不利。
③间隙对冲裁工艺力的影响
随着间隙的增大,材料所受的拉应力增大,材料容易断裂分离,因此冲裁力减小。
通常冲裁力的降低并不显著,当单边间隙在材料厚度的5~20%左右时,冲裁力的降低不超过5~10%。
间隙对卸料力推料力的影响比较显著。
间隙增大后,从凸模里卸料和从凹模里推料都省力,当单边间隙达到材料厚度的15~25%左右时的卸料力几乎为零。
但间隙继续增大,因为毛刺增大,又将引起卸料力、顶件力