材料工程基础 复习材料.docx
《材料工程基础 复习材料.docx》由会员分享,可在线阅读,更多相关《材料工程基础 复习材料.docx(13页珍藏版)》请在冰点文库上搜索。
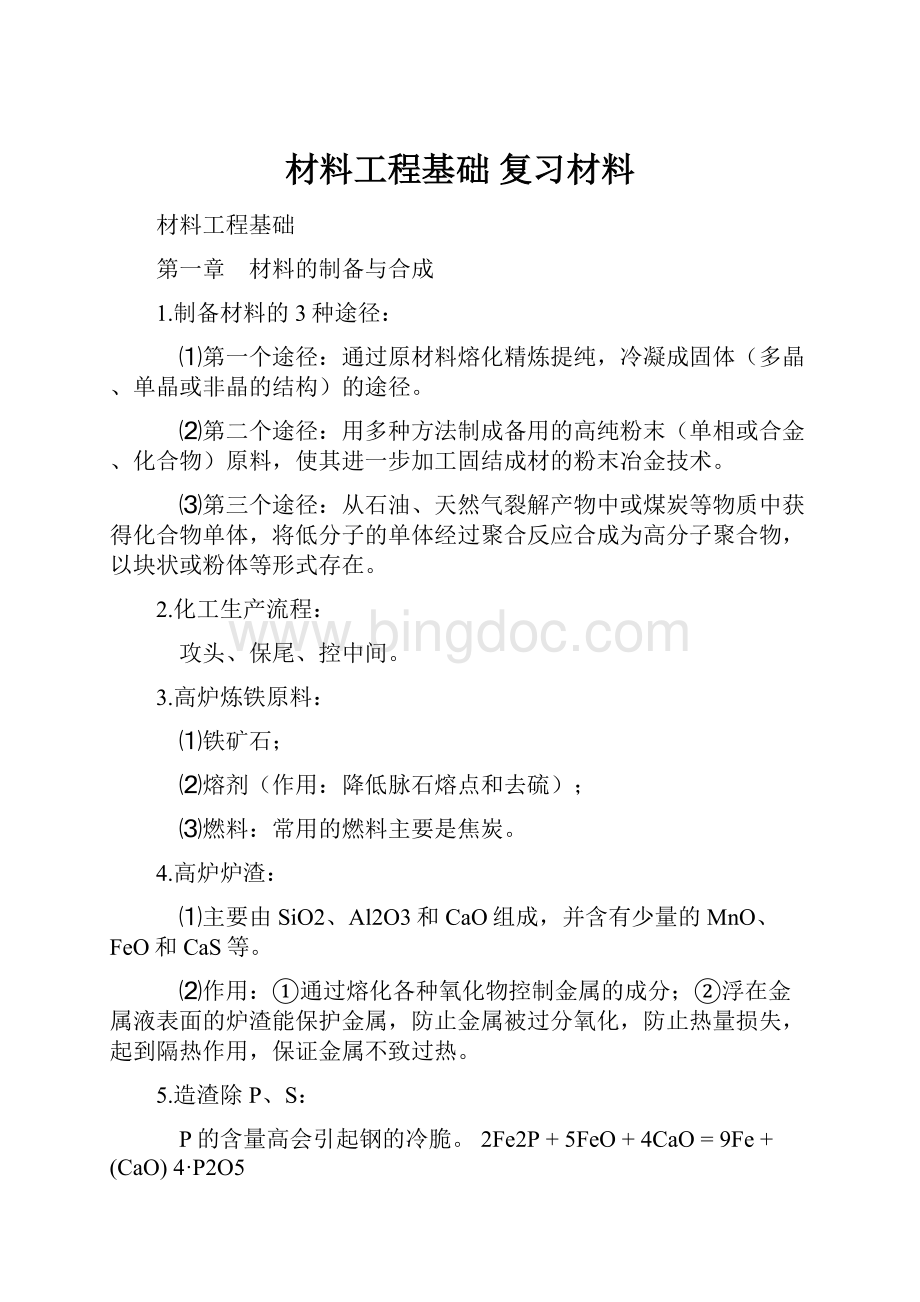
材料工程基础复习材料
材料工程基础
第一章 材料的制备与合成
1.制备材料的3种途径:
⑴第一个途径:
通过原材料熔化精炼提纯,冷凝成固体(多晶、单晶或非晶的结构)的途径。
⑵第二个途径:
用多种方法制成备用的高纯粉末(单相或合金、化合物)原料,使其进一步加工固结成材的粉末冶金技术。
⑶第三个途径:
从石油、天然气裂解产物中或煤炭等物质中获得化合物单体,将低分子的单体经过聚合反应合成为高分子聚合物,以块状或粉体等形式存在。
2.化工生产流程:
攻头、保尾、控中间。
3.高炉炼铁原料:
⑴铁矿石;
⑵熔剂(作用:
降低脉石熔点和去硫);
⑶燃料:
常用的燃料主要是焦炭。
4.高炉炉渣:
⑴主要由SiO2、Al2O3和CaO组成,并含有少量的MnO、FeO和CaS等。
⑵作用:
①通过熔化各种氧化物控制金属的成分;②浮在金属液表面的炉渣能保护金属,防止金属被过分氧化,防止热量损失,起到隔热作用,保证金属不致过热。
5.造渣除P、S:
P的含量高会引起钢的冷脆。
2Fe2P+5FeO+4CaO=9Fe+(CaO)4·P2O5
钢中硫含量高,造成钢的热脆性。
FeS+CaO→CaS+FeO
6.铝的生产流程
电解法制备金属铝必须包括两个环节:
一是从含铝的矿石中制取纯净的氧化铝;二是采用熔盐电解氧化铝得到纯铝。
7.炼铝过程中为什么要加入冰晶石(Na3AlF6)?
①氧化铝的熔点(2050℃)太高,对电解设备的耐高温性能要求过高。
②当用冰晶石(熔点1010℃)作熔剂时,氧化铝溶解于其中(溶解度约10%),将与氧化铝形成低熔点共晶(T共=938℃),这时可在1000℃以下进行电解。
通常的电解温度是950-970℃。
8.单晶制备方法
⑴熔体法:
①提拉法;②坩埚下降法;③泡生法;④水平区熔法;⑤浮区法。
⑵常温溶液法:
①降温法;②流动法;③蒸发法;④电解溶剂法;⑤凝胶法。
⑶高温溶液法
①缓冷法;②助熔剂挥发法;③籽晶降温法;④溶液提拉法;⑤移动溶剂熔区法。
⑷其他相关方法:
①水热法;②高温高压法;③焰熔法。
9.玻璃的熔制过程
⑴硅酸盐的形成
⑵玻璃的形成
⑶玻璃的澄清
⑷玻璃的均化
⑸玻璃液的冷却
第二章 粉末材料制备
1.机械制粉方法:
⑴机械研磨法;
⑵气流研磨法;
2.物理制粉方法:
⑴雾化法;
⑵物理蒸发冷凝法;
3.化学制粉方法:
⑴化学气相沉积法;
⑵还原-化合法;
⑶电化学法;
4.粒度测定
⑴筛分析法:
目数的定义:
筛网上1英寸(25.4mm)长度内的网孔数。
200目:
74μm 325目:
47μm
⑵激光衍射法:
当光入射到颗粒时,会产生衍射,小颗粒衍射角大,而大颗粒衍射角小,某一衍射角的光强度与相应粒度的颗粒多少有关。
原理:
激光粒度分析法是目前最为主要的纳米材料体系粒度分析方法。
当一束波长为λ的激光照射在一定粒度的球形小颗粒上时,会发生衍射和散射两种现象。
通常当颗粒粒径大于10λ时,以衍射现象为主;当粒径小于10λ时,则以散射现象为主。
⑶沉降法
原理:
在具有一定粘度的粉末悬浊液内,大小不等的颗粒自由沉降时,其速度是不同的,颗粒越大沉降速度越快。
如果大小不同的颗粒从同一起点高度同时沉降,经过一定距离(时间)后,就能将粉末按粒度差别分开。
5.粒径分布
D50:
表示粒径分布中占50%所对应的粒径,又称中位径。
D90:
表示粒径分布中占90%所对应的粒径。
Dav:
表示粒径分布的平均粒径。
6.对先进陶瓷用超细粉的基本要求
⑴超细;⑵高纯;⑶粉料的形貌形态;⑷无严重的团聚;⑸粉料的结晶状态。
第三章 高分子材料的聚合
1.聚合反应分类
⑴按元素组成和结构变化关系分类
①加聚反应;②缩聚反应。
⑵按反应机理分类
①连锁聚合反应;②逐步聚合反应。
2.聚合反应基本原理
⑴自由基聚合:
⑵离子聚合
⑶配位聚合。
3.四种自由基聚合方法的比较
第四章 材料的成形与加工
1.五个方面的加工成形技术
①金属铸造与半固态加工;
②金属的塑性加工;
③粉末材料成形与固结;
④高分子材料的成形与加工;
⑤焊接与粘接。
2.液态金属的充型能力
充型能力不足时,会产生浇不足、冷隔、夹渣、气孔等缺陷。
3..合金的收缩
合金的收缩经历三个阶段:
液态收缩、凝固收缩、固态收缩。
⑴体收缩是铸件产生缩孔或缩松的根本原因。
缩孔:
大而集中(逐层凝固)
缩松:
细小而分散(糊状凝固)
防止缩孔与缩松的措施:
①结晶温度范围窄的合金采取顺序凝固方式,冒口最后凝固;②结晶温度范围宽的合金采取同时凝固方式;③铸件在压力下凝固或用热等静压法也能消除缩松或缩孔。
⑵线收缩是铸件产生应力、变形、裂纹的根本原因。
4.液态成形方法:
⑴砂型铸造;
⑵特种铸造:
①熔模铸造;②金属型铸造;③压力铸造;④实型铸造;⑤离心铸造;⑥低压铸造;⑦连续铸造。
5.半固态成形:
半固态合金成形,它是介于液态成形和固态成形之间的一种成形方法。
半固态合金的制备方法:
⑴机械搅拌法;⑵电磁搅拌法;⑶应变激活工艺。
半固态成形方法:
⑴流变成形;⑵触变成形;⑶铸锻成形;⑷复合铸造。
第五章 金属塑性加工
1.金属塑性加工的分类
轧制、挤压、拉拔、锻造、冲压成形。
2.解释以下基本概念:
⑴加工硬化:
金属在室温下进行塑性变形时,随着变形程度的增加,强度和硬度不断提高,塑性和冲击韧性不断降低,这种现象称为加工硬化。
⑵回复:
T回=(0.25~0.3)T熔(K)
金属材料产生塑性变形后,加热时材料的力学性能和物理性能等得到恢复,此现象称为回复。
⑶再结晶:
T再=0.4T熔(K)
金属材料产生塑性变形后加热时,在原来的组织中重新产生无畸变的新晶粒的现象,称为再结晶。
⑷热变形:
T再<T热
热变形是指在金属再结晶温度以上的塑性变形。
⑸冷变形:
T冷<T再
冷变形是指在再结晶温度以下的塑性变形。
⑹温变形:
T回<T温<T再
温变形一般是指在室温以上,再结晶温度以下的塑性变形。
3.已知铅的熔点为327℃,钨的熔点为3380℃。
问:
铅在20℃、钨在1000℃时变形各属哪种变形?
为什么?
解:
T铅再=0.4T熔=0.4(327+273)=240K=-33℃<20℃
故铅在20℃属于热变形。
T钨再=0.4T熔=0.4(3380+273)=1461K=1188℃>1000℃
T钨回=(0.25~0.3)T熔=(913~1096)K=(640~823)℃<1000℃
故钨在1000℃属于温变形。
4.简要说明五种主要的金属压力加工成形过程。
⑴轧制:
是指金属坯料通过转动轧辊间的缝隙,承受压缩变形,而在长度方向产生延伸的过程。
⑵挤压:
是对放在容器内的金属坯料施加外力,使之从特定的模孔中流出,获得所需断面形状和尺寸的一种塑性加工方法。
⑶拉拔:
在外加拉力的作用下,迫使金属通过模孔产生塑性变形,以获得与模孔形状、尺寸相同的制品的加工方法,称之为拉拔。
⑷锻造:
借助锻锤、压力机等设备对坯料施加压力,使其产生塑性变形,获得所需形状、尺寸和一定组织性能的锻件。
⑸冲压成形:
是通过模具和冲压设备,使板材产生塑性变形,获得具有一定形状、尺寸和性能的冲压件的加工方法。
5.多辊轧制有什么优点?
多辊冷轧机的最大特点之一就是采用小直径的工作辊,这样用多辊冷轧机可以生产出更薄的带材。
与一般冷轧机相比,多辊冷轧机具有以下优点:
(1)工作辊径小,总轧制压力小。
(2)由于工作辊径小,轧辊的弹性压扁减小,因而每个轧程的总压下量可增大;此外,工作辊更换十分方便,减少了辅助时间,从而提高了生产率。
(3)多辊冷轧机具有塔形的支撑辊系,尤其是森吉米二十辊轧机,具有整体机架,刚性很好,轧辊挠度很小,因而可获得高精度的成品。
(4)轧机体积小,质量轻。
第六章粉末材料的成形与固结
1.按粉料成形时的状态,成形可分为:
⑴压力成形:
模压成形、三轴压制、等静压成形、高能成形。
⑵增塑成形:
挤压成形、轧膜成形、注射成形、车坯成形。
⑶浆料成形:
注浆成形、热压铸成形、流延法成形、压力渗滤工艺和离心成形、凝胶铸模成形、直接凝固成形。
2.模压成形包括以下几个步骤:
⑴原料准备:
①粉末退火:
可使氧化物还原,降低碳和其它杂质的含量,提高粉末的纯度;同时,还能消除粉末的加工硬化、稳定粉末的晶体结构。
②混合:
是指将两种或两种以上不同成分的粉末混合均匀的过程。
混合可采用机械法和化学法。
③筛分:
目的在于把颗粒大小不同的原始粉末进行分级。
④制粒:
将小颗粒的粉末制成大颗粒或团粒的工序,目的是为了改善粉末的流动性;
⑤添加润滑剂和成形剂:
在成形前,粉末混合料中常常要添加一些能改善成形过程的物质,即成形剂(包括润滑剂、粘合剂和造孔剂)。
⑵装模;
⑶加压:
加压方式有单向加压和双向加压两种;
⑷保压;
⑸脱模。
3.三轴压制
三轴压制就是单轴压制(模压)和等静压的结合。
4.挤压成形
利用压力把具有塑性的粉料通过模具挤出来成形的,模具的形状就是成形坯体的形状。
5.轧膜成形
将加入粘结剂的粉料放入反向滚动的轧辊之间,使物料不断受到挤压,从而得到薄膜状坯体的一种成形方法。
6.注射成形
把粉料与热塑性树脂等有机物混炼后得到的混合物,在注射机上于一定温度和压力下高速注入模具,迅速冷凝后脱模取出坯体。
7.车坯成形
利用粘土的可塑性,采用真空练泥机挤出的泥段或注浆成形挤出的粗泥坯,在车床上加工成形的。
8.堆积密度
以占粉末固体密度的百分比表示。
9.松散粉末的模压或等静压过程可分为3个阶段:
第一阶段:
粉末颗粒发生重排;
第二阶段:
颗粒发生弹塑性变形;
第三阶段:
颗粒断裂。
10.粉末体烧结的驱动力
体系的表面能和缺陷能。
第七章 高分子材料成形与加工
1.塑料成形方法
⑴塑料挤出成形;
⑵塑料注射成形;
⑶塑料压制成形;
⑷塑料压延成形;
⑸塑料中空吹塑成形;
⑹塑料热成形。
2.橡胶的加工
⑴塑炼:
可使生胶降低弹性,增加塑性。
⑵混炼:
目的是通过机械的作用,使各种配合剂均匀地分散在胶料中。
⑶成形:
是将混炼胶制成所需形状、尺寸和性能的橡胶制品的过程。
⑷硫化:
成形品在一定温度、压力下形成网络结构的过程,其结果是使制件失去塑性,同时获得高弹性。
第八章 材料的连接
1.现代连接方法主要包括:
铆接、栓接(螺栓连接)、焊接和粘接。
2.焊接方法的分类
根据被焊材料(母材)是否熔化,焊接方法大致可以分为三类:
①熔焊②压焊;③钎焊。
3.焊条
焊条由焊芯和药皮两部分组成。
⑴焊芯是具有一定长度和直径的焊接专用金属丝。
它的作用如下:
①作用电极,起传导焊接电弧的作用;②起填充金属的作用;③维持电弧稳定燃烧。
⑵药皮由造气剂、造渣剂、合金粉及粘结剂等构成。
其作用如下:
①机械保护作用。
②冶金处理作用。
③改善焊接工艺性能。
第九章
1.四把火
⑴将钢加热到适当温度,保温一定时间,然后缓慢冷却(一般为随炉冷却)的热处理工艺叫做退火。
⑵将钢加热到Ac3(对于亚共析钢)、Ac1(对于共析钢)、Accm(对于过共析钢)以上30℃~50℃,保温适当时间后,在自由流动的空气中均匀冷却的热处理叫做正火。
⑶将钢加热到相变温度以上(亚共析钢Ac3;共析钢和过共析钢Ac1以上30℃~50℃),保温一定时间后,通过浸入水或油中实现快速冷却,获得马氏体的热处理工艺称为淬火。
⑷钢件淬火后,为了消除内应力并获得所要求的组织和性能,将其加热到Ac1以下某一温度,保温一定时间,然后冷却到室温的热处理工艺叫做回火。
2.过冷奥氏体的转变产物
钢在冷却时,过冷 奥氏体的转变产物分为:
⑴高温转变产物:
珠光体(P)、索氏体(S)、屈氏体(T)
⑵中温转变产物:
上贝氏体(上B)、下贝氏体(下B)
⑶低温转变产物:
马氏体(低碳M、高碳M)
第十章 材料的表面改性
1.渗碳
为了增加钢件表层的含碳量和一定的浓度梯度,将钢件在渗碳介质中加热和保温,使碳原子渗入表面的工艺。
2.渗碳的目的
提高表面的硬度、耐磨性及疲劳强度。
3.渗碳的方法
①气体渗碳法;②固体渗碳法;③真空渗碳及离子渗碳。
3.渗氮
在一定温度下使活性氮原子渗入工件表面,形成富氮硬化层的化学热处理工艺。
4.渗氮的目的
更大地提高钢件表面的硬度和耐磨性,提高疲劳强度和抗蚀性。
5.渗氮的方法
①气体氮化;②离子氮化。