炼钢中的造氧化渣工艺.docx
《炼钢中的造氧化渣工艺.docx》由会员分享,可在线阅读,更多相关《炼钢中的造氧化渣工艺.docx(7页珍藏版)》请在冰点文库上搜索。
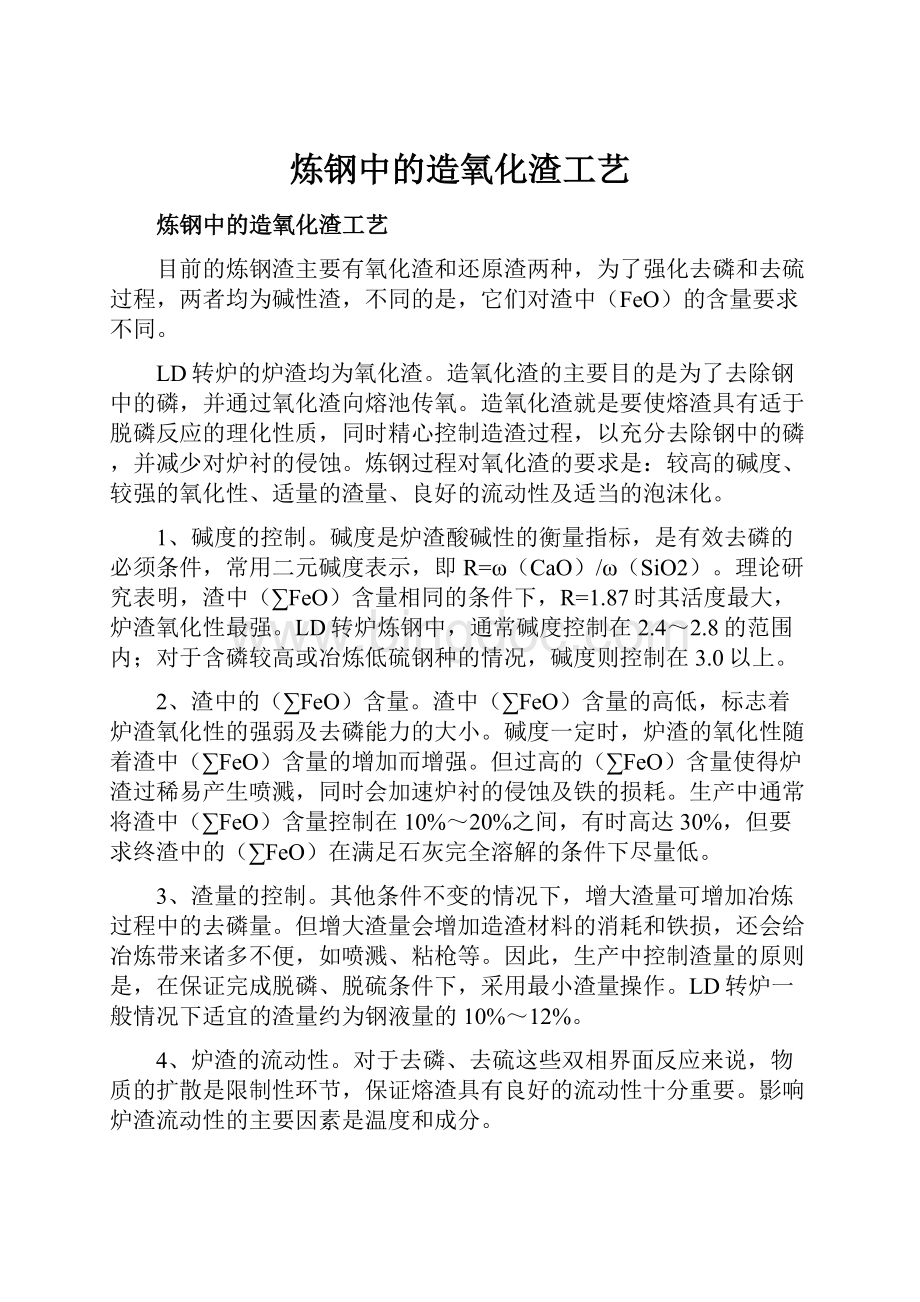
炼钢中的造氧化渣工艺
炼钢中的造氧化渣工艺
目前的炼钢渣主要有氧化渣和还原渣两种,为了强化去磷和去硫过程,两者均为碱性渣,不同的是,它们对渣中(FeO)的含量要求不同。
LD转炉的炉渣均为氧化渣。
造氧化渣的主要目的是为了去除钢中的磷,并通过氧化渣向熔池传氧。
造氧化渣就是要使熔渣具有适于脱磷反应的理化性质,同时精心控制造渣过程,以充分去除钢中的磷,并减少对炉衬的侵蚀。
炼钢过程对氧化渣的要求是:
较高的碱度、较强的氧化性、适量的渣量、良好的流动性及适当的泡沫化。
1、碱度的控制。
碱度是炉渣酸碱性的衡量指标,是有效去磷的必须条件,常用二元碱度表示,即R=ω(CaO)/ω(SiO2)。
理论研究表明,渣中(∑FeO)含量相同的条件下,R=1.87时其活度最大,炉渣氧化性最强。
LD转炉炼钢中,通常碱度控制在2.4~2.8的范围内;对于含磷较高或冶炼低硫钢种的情况,碱度则控制在3.0以上。
2、渣中的(∑FeO)含量。
渣中(∑FeO)含量的高低,标志着炉渣氧化性的强弱及去磷能力的大小。
碱度一定时,炉渣的氧化性随着渣中(∑FeO)含量的增加而增强。
但过高的(∑FeO)含量使得炉渣过稀易产生喷溅,同时会加速炉衬的侵蚀及铁的损耗。
生产中通常将渣中(∑FeO)含量控制在10%~20%之间,有时高达30%,但要求终渣中的(∑FeO)在满足石灰完全溶解的条件下尽量低。
3、渣量的控制。
其他条件不变的情况下,增大渣量可增加冶炼过程中的去磷量。
但增大渣量会增加造渣材料的消耗和铁损,还会给冶炼带来诸多不便,如喷溅、粘枪等。
因此,生产中控制渣量的原则是,在保证完成脱磷、脱硫条件下,采用最小渣量操作。
LD转炉一般情况下适宜的渣量约为钢液量的10%~12%。
4、炉渣的流动性。
对于去磷、去硫这些双相界面反应来说,物质的扩散是限制性环节,保证熔渣具有良好的流动性十分重要。
影响炉渣流动性的主要因素是温度和成分。
但去磷反应是放热反应,不希望温度太高,因此生产中应适当增加渣中(FeO)和(CaF2)等稀渣成分的含量,使碱性氧化渣在温度不高的情况下也具有良好的流动性。
5、炉渣的泡沫化。
泡沫化的炉渣,使钢-渣两相界面积大为增加,改善了去磷、去硫等两相反应的动力学的条件。
但应避免炉渣严重的泡沫化,以防喷溅。
造渣材料及其用量
·1造渣材料
炼钢用造渣材料,主要有石灰、萤石及其代用品、合成渣料和白云石等。
1、石灰
石灰主要成分为CaO,是由主要成分为CaCO3的石灰石煅烧而成。
对炼钢石灰的基本要求是:
CaO含量尽量高、SiO2及S等杂质尽量少、活性要好、新鲜干燥、块度合适。
(1)石灰的有效熔剂性。
所谓石灰的有效熔剂性,是指根据炉渣碱度要求,除去自身酸性氧化物(SiO2)造渣消耗的CaO,剩余CaO的含量,即:
ω(CaO)有效=ω(CaO)石灰-R×ω(SiO2)石灰
(2)石灰的活性。
所谓“活性”,是指石灰与熔渣的反应能力,它是衡量石灰在渣中溶解速度的指标。
石灰的“活性”与生产石灰时的煅烧温度有关。
石灰石的分解温度为880~910℃,如果煅烧温度控制在1050~1150℃,烧成的石灰晶粒细小(1μm左右)、气孔率高(可达40%以上),呈海绵状,活性很好,称为软烧石灰或轻烧石灰。
这种石灰加入熔池成渣快,利于前期脱磷,而且冶炼过程顺利。
如果煅烧温度远高于石灰石的分解温度,烧成的石灰晶粒粗大(10μm左右)、气孔率低(仅20%左右),甚至表面还包有一层熔融物,称为硬烧石灰或过烧石灰。
这种石灰加入熔池后,化渣慢,不利于冶炼和前期脱磷。
如果煅烧温度低于900℃,由于烧成温度低,石灰烧不透,称为生烧石灰。
这种石灰入炉后,内部残留的石灰石要继续分解而吸热,不仅成渣慢,对熔池升温也不利。
(3)石灰的块度。
转炉炼钢一般要求石灰的块度为5~40㎜。
块度过大,熔化慢,成渣晚;块度过小,尤其是含有粉末的,说明吸收了大量水分,应禁止使用。
2、萤石及其代用品
萤石在炼钢中是作为熔剂加入的,目的是化渣和稀渣。
其主要成分是CaF2,熔点仅1400℃左右,并能与CaO及2CaO·SiO2结合成低熔点化合物,因而可以加速石灰熔化和消除炉渣“返干”,且作用迅速。
此外,萤石能与硫反应生成挥发性的化合物,因而还具有一定的脱硫作用。
对炼钢萤石要求CaF2不低于85%,SiO2不超过4%,CaO不超过5%,S小于0.2%,块度10~80㎜,且保持清洁、干燥、不混杂。
3、合成渣料
合成渣料是转炉炼钢中新型造渣材料。
它是将石灰和熔剂按一定比例混合制成的低熔点、高碱度的复合造渣材料,即把炉内的造渣过程部分地,甚至全部移到炉外进行。
显然,这是一个提高成渣速度、改善冶炼效果的有效措施。
目前国内使用较多的合成渣料是冷固结球团。
它是用主要成分为FeO(67%左右)和Fe2O3(16%左右)的转炉炉尘配加一定的石灰粉、生白云石粉和氧化铁皮,在造球盘上造球,尔后在200~250℃下烘干固结而成。
该合成渣成分均匀、碱度高(5~13)、熔点低(1180~1360℃),且遇高温自动暴裂,因而加入后极易熔化,能很快形成高碱度、强氧化性和良好流动性的熔渣。
国外有种黑皮石灰(煅烧石灰时配加氧化铁皮),成渣快,去磷效果好。
4、白云石
白云石是CaCO3和MgCO3的复合矿物,高温下分解后的主要成分是氧化钙CaO和MgO氧化镁,还有一些SiO2、Al2O3和Fe2O3。
采用白云石造渣工艺主要是延长炉衬寿命,其基本原理是根据氧化镁在渣中有一定溶解度的特点,向炉内加入一定量的白云石,使渣中(MgO)将近饱和,从而减弱熔渣对镁质炉衬的侵蚀;另一方面,冶炼中随着炉渣碱度的提高,渣中(MgO)达到过饱和而有少量固态MgO析出,使后期炉渣黏度升高,出钢后利用溅渣护炉技术将炉渣挂在炉衬表面,形成保护层,可减轻冶炼前期低碱度渣对炉衬的侵蚀。
对转炉炼钢用白云石,一般要求其MgO含量在20%以上,CaO含量不低于30%,硫、磷杂质元素含量要低,块度以5~40㎜为宜。
白云石入炉会分解吸热,因此采用轻烧白云石较好。
·2各种渣料的用量——石灰
计算石灰加入量的基本方法是,先根据金属炉料的含硅量计算出渣中(SiO2)的质量,再根据炉渣的碱度求得石灰的质量。
电炉及转炉吹炼含磷量小于0.3%的低磷铁水时,炉渣碱度R用(CaO/SiO2)二元碱度表示,石灰加入量公式如下:
石灰加入量(㎏/t)=(1000×ω〔Si〕×X×60/28×R)/ω(CaO)有效
式中ω〔Si〕-炉料(铁水)中硅的质量分数;
X-炉料中硅被氧化的百分数,转炉吹炼取100%,电炉炼钢取90%;
60/28-1千克硅氧化可生成60/28的二氧化硅。
例1电炉冶炼45钢,炉料含硅量为0.5%,炉渣碱度按2.0控制,所用石灰主要成分为CaO-90%,SiO2-2.0%。
计算1000㎏炉料应加多少千克的石灰?
解:
石灰加入量=(1000×0.5%×90%×60/28×2.0)÷(90%-2.0×2.0%)=22.4㎏
例2转炉吹炼20钢,铁水含硅0.7%,含磷0.25%,终渣碱度要求3.0,石灰的有效熔剂性为80%。
试求1000㎏铁水需加石灰多少千克?
解:
石灰加入量=(1000×0.7%×100%×60/28×3.0)÷80%=56.25㎏
转炉炼钢中使用部分矿石作冷却剂时,由于铁矿石中含有一定数量的二氧化硅,为保证炉渣的碱度不变应补加适量的石灰。
每千克矿石的石灰补加量可按下式计算:
补加石灰量=ω(SiO2)矿石×R/ω(CaO)石灰
例3铁矿石中SiO含量为8%,碱度按3.0控制,石灰的有效熔剂性为80%。
试计算每加入1㎏的矿石应补加石灰多少千克?
解:
补加石灰量=8%×3.0÷80%=0.3(㎏)
·3炉渣组成对石灰溶解的影响
影响石灰在熔渣中的溶解速度的因素主要是石灰的质量、熔池温度及熔渣的组成。
1、(CaO)和(SiO2)
渣中(CaO)的含量小于30%~35%时,石灰的溶解速度随其增大而增大,这是因为石灰溶解过程的限制性因素是物质的扩散,当(CaO)含量小于30%时,渣中存在大量的复合阴离子,增加(CaO)的含量会使这些复合阴离子解体,引起炉渣黏度下降,从而改善石灰溶解的动力学条件,加速石灰的溶解。
当渣中(CaO)含量大于35%时,随着(CaO)的进一步增加,会使炉渣的平均熔点不断升高,黏度不断上升,从而影响石灰的溶解速度。
渣中(SiO2)低时,随着其含量的增加,石灰的溶解速度增加,这是因为该条件下增加(SiO2)会使炉渣熔点降低,黏度下降。
同时它可与(FeO)一起促进石灰的溶解,反应产物是熔点只有1205℃的CaO·FeO·SiO2。
随着(SiO2)大于25%时,进一步增加其含量,不仅在石灰表面形成2CaO·SiO2硬壳,而且会增加渣中复合阴离子的数量,导致炉渣黏度上升。
2、(FeO)和(MnO)
随着(FeO)含量增加,石灰溶解速度直线增大。
其原因有三,一是(FeO)可与渣中其他组元生成低熔点的化合物,有效降低炉渣黏度;二是因(FeO)是炉渣的表面活性物质,可以增强炉渣对石灰的润湿和渗透;三是(FeO)可与CaO及2CaO·SiO2作用生成低熔点化合物而使它们熔化。
(MnO)对石灰熔化速度与(FeO)类似,但不如其作用大。
3、(MgO)
少量的(MgO)含量,可以降低炉渣的黏度;当含量超过6%时,渣中的(MgO)处于过饱和状态,会析出固态的氧化镁颗粒,使炉渣黏度增大。
·4转炉的造渣制度
一、转炉的造渣方法及选用
目前,转炉炼钢的造渣方法有四种:
单渣法、双渣法、双渣留渣法及喷吹石灰粉法,选择的依据是原材料的成分和所炼钢中。
1、单渣法。
在冶炼中只造一次渣,中途不倒渣、不扒渣,直到终点出钢的造渣方法称为单渣法。
单渣法操作的工艺简单,冶炼时间短,生产率高。
但其去硫、磷效率低,一般情况下去硫率为30%-40%,去磷率为90%左右。
2、双渣法。
是指在吹炼中途倒出部分炉渣,然后补加渣料再次造渣的操作方法。
双渣操作的特点是,炉内始终保持较小的渣量,吹炼中可以避免因渣量大造成的喷溅,且渣少易化,同时又能获得较高的脱硫、脱磷效率。
双渣法去硫率可达50%-60%,去磷率达92%-95%。
该法的倒渣时机不易掌握。
3、双渣留渣法。
是指上一炉的高碱度、高温度和较高(FeO)含量的终渣部分地留在炉内,以便加速下一炉钢初渣的形成并在吹炼中途倒出部分炉渣再造新渣的操作方法。
由于留渣,初渣早成,去硫率达60%-70%,总去磷率高达95%左右。
采用双渣留渣法时,对铁水前应先加一批石灰稠化所留炉渣,而且对铁水时要缓慢进行,以防发
生爆发式碳氧反应而引起严重喷溅,若上一炉终点碳过低,一般不宜留渣。
4、喷吹石灰粉法。
是指在冶炼的中后期以氧气为载体,用氧枪将粒度为1㎜以下的石灰粉喷入熔池且在中途倒渣一次的操作方法。
该法成渣速度快,前期去硫磷率高,但该法需要破碎设备,且粉尘量大,石灰粉又容易吸收空气中的水分,制备运输较困难。
单渣法生产稳定,操作简单,便于实现计算机控制。
因此,对于含硅、硫及磷较高的铁水,入炉前应进行预处理使之达到单渣法操作的要求,合理又经济。
单渣法操作时,渣料应分两批加入,否则会造成熔池温度下降过多,导致渣料结团且石灰块表面形成一层金属凝壳而推迟成渣,加速炉衬侵蚀并影响去硫和去磷。
正常情况下,第一批料应在开吹的同时加入,其组成是:
石灰为全部的1/2~2/3,萤石为全部的1/3~½。
其余为第二批渣料,一般在硅锰氧化基本结束,头批渣料已经化好。
反之如果加入过晚,正值碳的激烈氧化期,渣中(FeO)较低,二批料难化,容易产生金属飞溅;同时,由于渣料的加入使炉温降低,碳氧反应将被抑制,导致渣中的氧化铁积聚,一旦温度上升,必会发生爆发式碳氧反应而引起严重喷溅。
二次渣料可视炉内情况一次加入或小批多次加入,但是,最后一小批料必须在终点前3-4分钟加入,否则所加渣料尚未熔化就出钢了。
渣况判断
炉内渣况良好有两个基本条件,一是不出现“返干”现象,二是不发生喷溅,尤其是严重喷溅。
一旦出现均会严重影响炉内化学反应,甚至酿成事故。
预测判断的方法有两种:
1、经验预测。
通常情况,渣料化好、渣况正常的标志是:
炉口的火焰比较柔软,炉内传出的声音也比较柔和、均匀。
如果炉口的火焰由柔软逐渐向硬直方向发展,炉内传出的声音也由柔和逐渐变得刺耳,说明炉渣将要出现“返干”。
如果炉内传出的声音渐渐变闷,炉口处的火焰也逐渐转暗且飘忽无力,同时,还不时地从炉口溅出片状泡沫渣,说明炉渣正在被严重泡沫化。
一般二批料加入过晚易出现这种现象。
2、声纳控渣仪预测。
其基本原理是:
在炉口附近安装定向取声装置和声纳仪采集炉口噪音,为其进行信号转换、选频、滤波、放大、整形后输入计算机,由计算机在显示器上的音强化渣图中绘制冶炼过程中的噪声强度曲线,间接地反映渣层厚度或渣面的高低,同时对吹炼过程中可能发生的喷溅或“返干”进行预报,并由报警装置发出声、光信号。
(两线一区)