12500KVA工业硅矿热炉的设计讲解.docx
《12500KVA工业硅矿热炉的设计讲解.docx》由会员分享,可在线阅读,更多相关《12500KVA工业硅矿热炉的设计讲解.docx(29页珍藏版)》请在冰点文库上搜索。
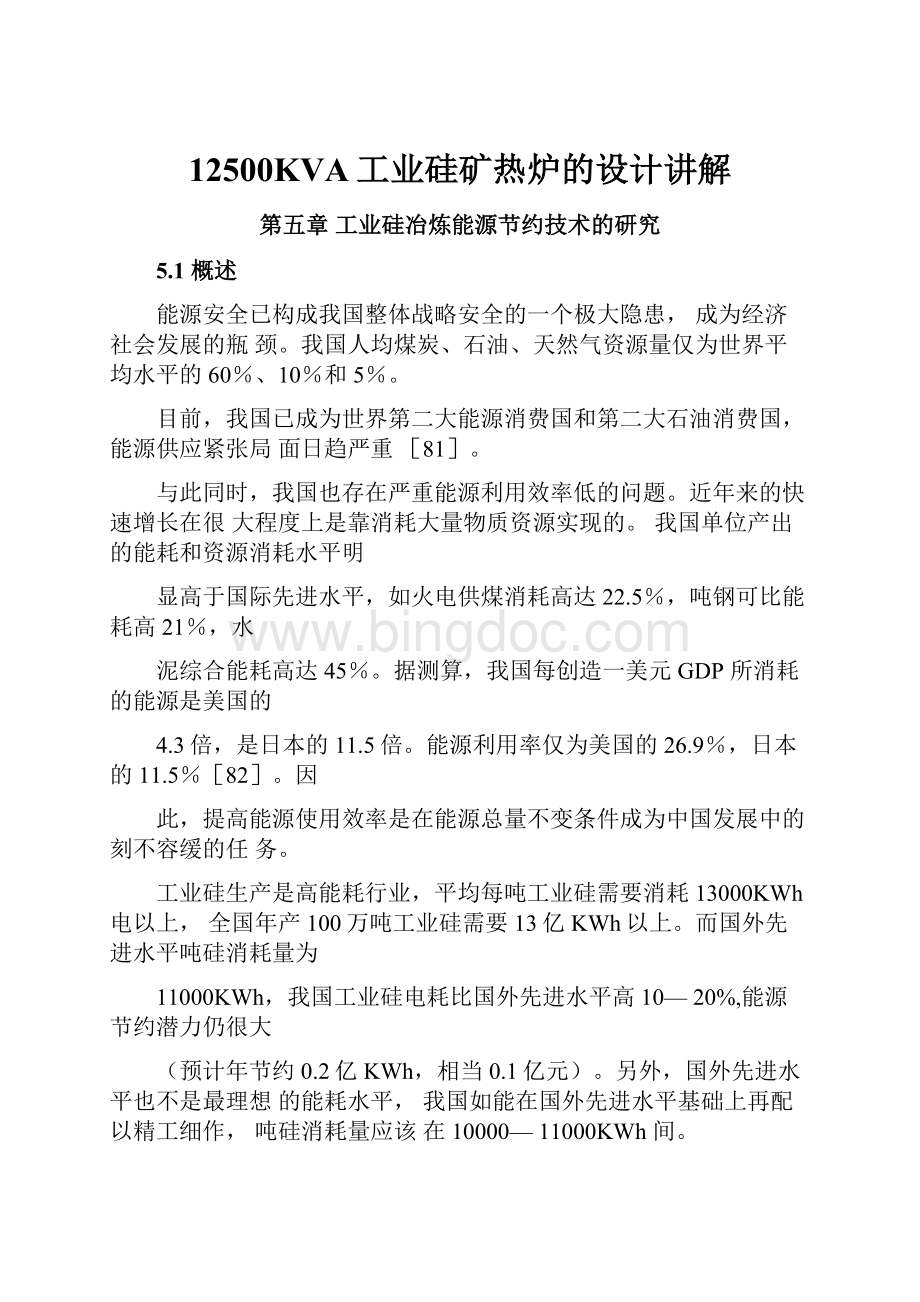
12500KVA工业硅矿热炉的设计讲解
第五章工业硅冶炼能源节约技术的研究
5.1概述
能源安全已构成我国整体战略安全的一个极大隐患,成为经济社会发展的瓶颈。
我国人均煤炭、石油、天然气资源量仅为世界平均水平的60%、10%和5%。
目前,我国已成为世界第二大能源消费国和第二大石油消费国,能源供应紧张局面日趋严重[81]。
与此同时,我国也存在严重能源利用效率低的问题。
近年来的快速增长在很大程度上是靠消耗大量物质资源实现的。
我国单位产出的能耗和资源消耗水平明
显高于国际先进水平,如火电供煤消耗高达22.5%,吨钢可比能耗高21%,水
泥综合能耗高达45%。
据测算,我国每创造一美元GDP所消耗的能源是美国的
4.3倍,是日本的11.5倍。
能源利用率仅为美国的26.9%,日本的11.5%[82]。
因
此,提高能源使用效率是在能源总量不变条件成为中国发展中的刻不容缓的任务。
工业硅生产是高能耗行业,平均每吨工业硅需要消耗13000KWh电以上,全国年产100万吨工业硅需要13亿KWh以上。
而国外先进水平吨硅消耗量为
11000KWh,我国工业硅电耗比国外先进水平高10—20%,能源节约潜力仍很大
(预计年节约0.2亿KWh,相当0.1亿元)。
另外,国外先进水平也不是最理想的能耗水平,我国如能在国外先进水平基础上再配以精工细作,吨硅消耗量应该在10000—11000KWh间。
我国工业硅生产能源消耗高主要是因为设计上不合理、控制水平与管理水平不高。
设计上不合理体现在我国普遍使用的是6300KVA左右的小炉型(散热大、产量低)、炉型设计上为隔热措施不严密、电路设计不合理、极心圆尺寸大小不合理等许多细节方面。
控制水平不高体现在人工操作范围大、炉况稳定性差、造成因调整炉况波动费时较长而使得非生产性能耗损失大。
管理水平不高体现在管理上不严、制度不健全、操作细节缺乏,造成物资或能源上的消耗浪费。
目前工业硅生产中能源节约途径主要有:
1)炉型的大型化方向;2)炉型的密
闭化方向;3)余热利用化方向;4)提高炉子电效率措施如改进短网结构设计、
改善变压器性能、改善电参数、采用低频电源等;5)提高炉子热效率;6)改变炉内反应机制;7)改变原料性能方向;8)采用自动控制方向;9)管理制度建设方向。
由于上述诸多途径尚处于讨论阶段,形成固定技术并推广者仅有短网改进、管理制度建设上,许多技术细节缺乏,因此真正意义上可以直接使用的工业硅生产中能源节约技术还需要研究与试验。
经过多年的摸索探讨,目前我国工业硅电弧炉的电效率平均在92%以上,各种提高电效率的技术或措施也比较成熟如改进短网结构设计、使用优质导电材
质、采用低压补偿技术、改善电参数等方面。
但是,我国工业硅电弧炉的热效率普遍比较低,这是导致我国工业硅生产能耗高、能源利用效率低的主要原因,表
5-1是我国某厂6300KVA电弧炉的热平衡分析表[21]。
表5-1我国某厂6300KVA电弧炉的热平衡分析
热收入项
热量(千卡/h)
百分比
热支出项
热量(千
卡/h)
百分比
1、电热能
4324940
95.98
1、氧化物还原耗热
1834462
40.71
2、电极氧化热
100680
2.234
2、金属硅带走热
269456
5.98
3、还原剂反应放热
80520
1.78
3、逸出气体带走热
826633
18.35
4、炉面散热
269333
5.97
5、炉体散热
166448
3.69
6、短网热损失
336738
7.47
7、冷却水带走热
750000
16.46
8、其他
53370
1.19
合计
4506140
100
4506140
100
从表5-1可以看出6300KVA电弧炉在工业硅生产过程中,电效率为92.21%,热效率为65%,能源大部分由于热效率低而被损失掉,损失途径主要是逸出气体带走热、炉面散热、炉体散热、短网热损失、冷却水带走热。
因此,提高工业硅电弧炉冶炼过程中的热效率应当是今后研究的重点。
在本文研究中,我主要从提高工业硅矿热炉冶炼过程中的热效率角度来研究工业硅冶炼能源节约技术。
提高工业硅冶炼能源的热效率是一项综合性能源节约技术,它应当包括所有能够能够提高热效率、减少热损失的技术或措施。
但是在本文中只研究炉型的大型化方向、炉型的密闭化方向、余热利用化方向、隔热设计技术四个方面来提高
工业硅冶炼过程中的热效率。
因为从表5-1可以看出,工业硅矿热炉热效率低就
是因为逸出气体带走热、炉面散热、炉体散热、短网热损失、冷却水带走热这五个方面热损失大。
炉型大型化则单位热容率增大,能量供应集中,通过外围表面单位面积散热小、炉子热稳定增强,有利于降低热损失。
同时炉型大型化也是今后工业硅行业发展的方向,大型炉具有热容量大、产量高、有利于二次精炼提高产品质量、单位产品成本低、便于烟气余热利用等诸多好处。
因此,研究炉型大型化不仅是降低热损失的需要,也是满足今后工业硅行业长期发展的需要,具有双重意义。
炉型密闭化或近密闭化不仅可以减少炉面热辐射损失,而且也可以减少烟气从6个炉门逸出带走的热,也是降低热损失、增加烟气回收能力、改善炉前操作环境的有力措施。
18.35%,这部分热量
国内包头钢铁研究设
在某厂应用取得较好
从表5-1可以看出,烟气带走热占据了供应总热量的又被散发到大气中,造成了能源损耗,致使能源利用率低,
计院曾经依据钢铁行业余热利用方式设计过余热回收装置,的使用效果,但是由于该余热回收装置初期投资过大,国内工业硅企业又大多数是私营企业,他们不愿意做这么大的投资,所以研究一种新型低造价、多用途、适用于大多数企业的余热利用装置(热材联产装置)很有必要,开辟一条已经被浪费掉的巨大热能集热道路具有非常重要的现实意义。
科技每时每刻都在变化,上世纪60年代所作的设计不应当在这个世纪仍然被当作模范来应用。
当前,由于国内没有实力研究机构来重新对上世纪60年代所作的工业矿热炉设计作改进,致使大多数企业仍用老的设计来建炉子,并且施工队伍都非正规研究机构或有能力去开发建设新型炉子,所以我国目前的工业硅矿热炉普遍都能耗高、设计未能跟上时代发展的需要。
问题的重要一方面反映在炉体隔热设计多年来没有多大改变,普遍使用的是碳砖层、耐火砖层、纤维板、钢板四层结构,随着科技的发展这种结构应当革新,因为国际国内新材料领域发生的一系列创新已经给我们带来了重新设计炉体结构的机遇。
上述四个以提高工业硅冶炼能源的热效率为目的的研究是目前工业硅冶炼能源节约方面尚未涉及完善但又非常重要的领域,需要既具备丰富的科学理论知
识、又掌握国际国内工业硅冶炼情况的人员才能完成,它涉及到的冶金、工艺、传热、设备、设计等多方面的知识与创新要求,使得这方面的工作既具体又复杂、既艺术又有意义。
5.2大容量半密闭式12500KVA工业硅矿热炉的设计
5.2.1设计依据
本项工作采用如下设计规范:
中国节能技术政策大纲》(2005);冶金企业安全卫生设计暂行规定》(1988);
建筑设计防火规范》(GBJ16-87);工业炉窑大气污染排放标准》(GB9078-1996);
工业炉砌筑工程施工及验收规范》(GB50211-2004)。
5.2.2设计内容5.2.2.1变压器选型
大容量矿热炉具有单炉产量大、能量供应均衡性好、便于实现机械化、便于余热综合利用、热稳定性好、便于操作等一系列优点,是业界一致认可的矿热炉发展的方向。
为了促进国内工业硅行业冶炼水平的提高和设备装备的现代化,因此此次设计采用12500KVA容量的矿热炉变压器。
12500KVA矿热炉变压器具体技术参数如下:
型号:
HKSSPZ20-12500/35壳式强油水冷矿热炉变压器;
额定容量:
12500KVA可超载30%
冷却方式:
OFW;F
一次电压(KV):
35;
二次额定电压(V):
151;
二次电压(V):
175,172,169,166,163,160,157,154,151,148,145,142,139,136,133共15档;
阻抗电压(短路电压):
ex%=4-6%。
5.2.2.2矿热炉电气参数的确定
在工业硅冶炼过程中矿热炉的状态与电气参数的变化密切相关,控制最佳的供电制度对保证取得好的经济技术指标十分重要。
一般而言,提高矿热炉的二次电压在功率一定情况下电流就可以降下来,这有利于提高线路功率因数和减少电损失,但是过分提高矿热炉电压,电极就不能
深插,炉膛料面就会过热,热损失增加,硅回收率降低,因此每台电炉都有其适宜的二次电压值。
在设计电炉时往往利用米古林斯基公式[68、83]来确定矿热炉正
常工作时的二次电压:
V2=KP1/3
KVA。
式中:
K为电压系数,取6.0-7.5;P是变压器额定功率,
因此这次设计时取二次电压V2=6.5X125001/3=150.85~151V,
5.2.2.3矿热炉结构设计
正确设计矿热炉的结构是保障矿热炉工作性能的先决条件,是设计工作者面临的最大困难。
好的矿热炉结构设计不仅有利于炉子保障高产、优质、低能耗、少故障的生产,而且有利于节约筑炉成本、方便其它设备布置、保证操作顺畅。
1、电极直径的选取
在确定矿热炉其它结构尺寸之前,必须先确定电极直径,它决定着矿热炉其
它结构尺寸的大小。
电极直径有许多计算方法,一般根据电极电流和电极电流密度确定:
d=2片=102.4cm=1024mm,
式中12为电极电流,A,△I为电极电流密度5.5-6.1A/cm2,取5.8计算。
2、极心圆直径计算
集中(图5-2)就是热量分散(图5-3),这都会造成炉况调节频繁或根本无法调
节的严重错误。
设计中极心圆直径可按下式计算:
Dg=ad=2.3X1050=2415mm
式中a为极心圆倍数,a=2.2-2.3,这里取2.3计算。
结合矿热炉容量、可调极心圆范围、实际电气参数调节空间这里取极心圆直
径为2500mm。
/■
3、炉膛内径计算
过电极一炉料一电极或炉底时所受的阻力。
否则,炉膛内径选择尺寸过大,矿热炉表面散热面积大,还原剂烧损严重,出硅口温度低,出硅困难,炉况会恶化。
炉膛内径选择过小,电极一炉料一炉壁回路上通过的电流增加,反应区偏向炉壁,将使炉内热量分散,炉心反应区温度低,炉壁腐蚀严重,炉况也会恶化。
炉膛内径可按下面经验公式计算:
Dn=rd=5.8X1050=6090mm
式中r为炉膛内径倍数,r=5.8-6.0,这里取5.8。
炉膛内径这次设计中取为6200mm。
4、炉膛深度计算
在选择炉膛深度时,要保证电极端部与炉底之间有一定的距离、电极有效插
入的深度和料层有一定的厚度。
炉膛深度若过深,电极与炉底距离远,电极不能深插,高温区上移,炉底温度低,炉底SiC会沉积,炉底上抬,堵塞出硅口,炉
况变差。
炉膛深度若太浅,料层厚度将很薄,炉口温度升高,硅挥发损失增加,容易露弧操作,能耗增大。
合适的炉膛深度可按下面经验公式计算:
h=Pd=2.5X1050=2625mm
式中P为炉膛深度倍数,P=2.5-2.8,这里取2.5。
炉膛深度这次设计中取为2700mm。
5、炉衬与炉底的结构、尺寸及材料选择
一般而言,炉衬、炉底结构包含了工作层、保温层、隔热层、绝热层、钢板层5个主要层次,但是每个层次的具体尺寸却是很有技术含量的,因为这涉及到筑炉成本、炉子性能、炉子寿命等许多经济因素。
炉衬厚度过厚,引起筑炉成本上升,占地面积扩大,炉衬表面积增加,散热面积也增大;炉衬厚度过薄,抑或炉衬强度不够,抑或无法保温。
炉底厚度亦是如此。
国内外对炉衬、炉底散热强度计算表明,保持炉衬与炉底热损失为2-4%是
合理的范围内网,或者保持炉衬表面温度在70-120C是允许的。
因此按照这个
条件以及结合所选择材料的使用温度,根据传热学知识可确定炉衬与炉底工作层、保温层、隔热层、绝热层的厚度,钢板层的厚度根据强度需要而定。
我们在这次设计中,工作层都使用自焙碳砖、保温层选用新型隔热耐火粘土砖(热导率vO.44W/m?
k)、隔热层使用纳米隔热材料、绝热层使用复合硅酸铝纤维毯、钢板层选用14mm厚的普通钢(炉底钢板厚18mm),如图5-4。
1电极孔2烟罩上盖板3烟囱孔4冷却水道5观测孔6捣料炉门7红砖8隔热耐火砖
9纳米绝热材料10复合硅酸铝纤维毯11钢板12出硅口13高铝砖14自焙炭砖
图5-412500KVA工业硅矿热炉结构图
6出硅口位置、结构、尺寸与材料选择
出硅口是矿热炉上非常重要的一个部位,它的位置、结构形状、尺寸、材料选择都是需要仔细斟酌的。
位置布置不当,出硅口部位温度低,出硅不畅或者是操作不方便;结构形状尺寸不当,也会导致出硅不畅或者封堵困难或者出硅时间延长;材料选择不当,容易氧化腐蚀,维修频繁。
在这次设计中,出硅口设计二个,每个出硅口水平位置与炉底齐平并比炉底
水平线下倾斜3C,角度位置它处于炉心与电极中心两点的延长线与炉壁的焦点上。
出硅口应当设计成圆形,便于烧穿与封堵,尺寸根据出硅时间要求计算并结合实际操作需要来决定大小为直径100-120mm材料选择上容易氧化的外侧使用
石英材料与碳糊。
7、炉门结构、尺寸与材料选择
大容量炉最大的问题是炉缘距离炉心远,上料困难,特别是国内强调以人工
精细加料来取得好质量与低能耗产品的观点下,普遍认为在大容量炉子在国内不如6300KVA炉子的性能,因此一次又一次的阻碍了投资方建造大容量炉子的热情。
我们在这次设计中仅设计了3个捣料炉门,上料操作通过采用前述第三章开发设计的自动上料系统来完成,克服了大容量炉存在的最大恼人的问题。
自动上料装置将料布放在料面各处,捣炉功能通过窥视孔根据需要打开捣料炉门进行捣炉操作。
捣炉炉门门槛下部与炉沿等高,门槛长1200mm,高1500mm,使用单
独水冷结构。
不需要捣炉时,炉门关上,密闭冶炼。
8、烟罩结构、尺寸与材料选择
大容量矿热炉炉膛尺寸跨度大,烟罩设计较困难,同时从烟罩通过的电流大,处理不好涡流损失大。
为了解决烟罩结构强度与防止涡流损失,我们采取用水冷钢管(防磁)做骨架并起吊,上下盖采用石板与水泥构筑,用细钢筋做支撑,既减轻了烟罩整体重量又防止了筑砌或制作上的不便。
烟罩高度离炉沿2300mm,
直径与炉壳直径等同,厚度160mm,上下盖间通水冷却。
5.2.3技术指标
设计完成以后有关该炉的技术参数与性能如下:
电极直径:
1050mm;
极心圆直径:
2500mm;
炉膛直径:
6200mm;
理论电单耗量:
13000KVAh/吨。
5.3余热利用化研究
也就
5.3.1余热利用思路
余能是在一定经济技术条件下,在能源利用设备中没有被利用的能源,是多余、废弃的能源。
它包括高温废气余热、冷却介质余热、废汽废水余热、高温产品和炉渣余热、化学反应余热、可燃废气废液和废料余热以及高压流体余压等七种。
其中最主要的是余热。
根据调查,各行业的余热总资源约占其燃料消耗总量的17%~67%,可回收利用的余热资源约为余热总资源的60%[85]。
余热的回
收利用途径很多。
一般说来,综合利用余热最好;其次是直接利用;第三是间接
利用(产生蒸汽、热水和热空气)。
余热蒸汽的合理利用顺序是:
1)动力供热联
合使用;2)发电供热联合使用;3)生产工艺使用;4)生活使用;5)冷凝发电用。
余热热水的合理利用顺序是:
1)供生产工艺常年使用;2)返回锅炉使用;3)生活
用。
余热空气的合理利用顺序是:
1)生产用;2)暖通空调用;3)动力用;4)发电
用。
但是这不是绝对的,需要每个工厂根据自己实际生产条件和需要而定。
5.3.2工业硅冶炼中不同种类余热的利用
在工业硅冶炼中所有能源供入项为电能和化学反应能,能源支出项为氧化物
92%以
还原、金属硅潜热、逸出气体、炉面、炉体、短网、冷却水带走热。
由于国内外在电能节约方面研究得比较多和透切,目前工业硅冶炼电效率基本都在上。
但是,电能最终要转变为热能才是反应所需的,而从表5-1可知,矿热炉冶炼系统的热效率一般仅有60-70%,因此,整个冶炼系统能源利用效率都低于70%,这样大量的热被逸出气体、炉面、炉体、短网、冷却水、金属硅所带走和
散失。
从表5-1可知,金属硅带走的热占热量总供入量的5.98%,即269456千卡/h。
这部分热是以金属硅潜热形式存在,硅液1600-1800C,硅锭为常温20-30C,
其热具有间断性(出硅前后)、释放缓慢性,存在能量密度低、不便于接触、不便于引出等特点。
在目前经济技术条件下,金属硅的潜热只能以热辐射与对流的方式将这部分热引导出来,其可能的利用方式为烘干物料、预热物料、加热洗澡用水(该余热每小时能使2.7吨水从0C升到100C)、加热生活用水。
炉面损失的热占总热量的5.97%,即26933千卡/h,与金属硅带走的热相当。
这部分热总量大、
由于在炉口损失,
法是炉型密闭化、
能流持续平稳、密度小,主要以热辐射与对流形式损失,但是受制于场地无法加以再利用,只能想办法减少其损失。
节约办
控制料面温度、料面燃烧状况、厚料操作与防止刺火大量、多次发生。
炉体损失的热占总热量的3.69%,即166448千卡/h。
这部分热与料面损失
的热性质相同,它以热传导形式损失,利用也很困难,也只能想办法减少其损失。
减少办法是加强炉体隔热性能。
短网损失的热占总热量的7.47%,即336738千卡/h。
这部分热主要损失在电缆、铜瓦、电极对外热辐射上,数量很大,但是受制于场地、能流密度小等限制,也是无法利用的热损,只能想办法减少。
减少办法就是缩短短网,使用适当电流冶炼,选用制造后导电性能好的短网。
注意不能使用保温材料包裹的办法,这样会适得其反。
冷却水带走的热占总热量的16.46%,即750000千卡/h。
这部分热产生于变
压器、电缆母线、铜瓦,是种功能用水,一般要求入口20-30C,出口30-40r,
水在循环池中来回循环使用,所以冷却水带走的热量虽然很大,但是不能够被利
2)
用。
这部分热可以想办法减少,具体措施为:
1)变压器方面要求硅钢片性能好,
材料、制造都要选技术好的厂家来做。
减少短网闪变,避免过大电流操作。
电缆母线方面要求选用材料热阻小并要求制造水平高的厂家来生产,尽量减少电缆布置长度,避免过大电流操作。
3)铜瓦基本要求也如此,要求使用锻造工艺制造。
逸出气体(烟气)带走的热量占总热量的18.35%,即826633千卡/h。
烟气
从炉内部产生,透过料面以后,温度在400-600C,6300KVA的矿热炉烟气流量为4-8万NM/h,烟气成分为2、Q、CQHO及少量其他气体。
以往国内企业大
多数直接排放,不仅污染了环境,而且造成能源损失。
近年来在环保部门要求下,各企业相继安装了布袋除尘器。
烟气在进入布袋除尘器之前温度必须降到120r
以下,降温措施为混风冷却、空冷、水冷,部分企业的水冷方式产生的热水被用于生产(洗原料、解冻)或生活(洗澡、洗碗),但是混风方式占多数,空冷也有少量,它们吸收或交换的热都被再次损失掉。
从当前烟气处理来看,烟气余热都没有得到利用或很好的利用(利用价值不高)
5.3.3工业硅冶炼中烟气余热的利用
烟气余热利用是余热种类当中最便于利用的一种形式,一般烟气具有较高的温度,流量较大,携带的热量较多,回收利用方便(用对流换热即可回收),不受场地限制,转换容易(转换为蒸汽)。
因此,对烟气的余热回收应好好的珍惜与做文章。
烟气余热回收得到的能量利用方向为生产用与生活用或者是二者联合使用。
生产用一是为本工艺流程服务如预热物料、解冻,二是为其他工艺服务如余热发电、烘干其他物料、加热其他产品或是二者的复合。
生活用一是洗澡洗碗,二是供暖制冷或是二者的复合。
在这里,我提出二种工业硅冶炼系统烟气余热利用方案:
一是余热发电综合利用方案,二是余热加热配套产品综合利用方案。
5.3.3.1烟气余热发电综合利用方案
从一台6300KVA工业硅矿热炉中逸出的烟气流量为4-8万NM3/h,烟气温
度为400-600C,400r烟气比热为1.12kJ/kgC,密度1.295kg/Nm3,烟气相对
于300r时含热量=CpXPXAT=1.12X4X1.295X100=580.16万KJ/h=1381333
千卡/h,此热量能使13.8吨水从0C升至U100C,能使得5.5吨水从40C升到290r
此为蒸汽发电要求过热温度)。
根据青岛4308厂提供的BN型汽轮机技术参数:
进汽压力0.35-0.7Mpa进汽温度250-290r,排汽压力0.15Mpa,抽汽压力0.5Mpa,则发电量可达1000KW。
由此计算,设电价0.5元/度,则一年(7000小时)发电可创造经济效益350万元。
为实现烟气余热发电,需要投资余热锅炉2台30万、汽轮机1台20万、
发电机组1台20万、变压器2台40万、控制柜若干100万左右,总投资210
万左右,承上述计算7个月即可收回投资。
对于上规模企业,如有2台以上6300KVA工业硅矿热炉或者多台12500KVA
工业硅矿热炉,则上马烟气余热发电项目更有价值与必要。
因此,国内投资者应尽快打消烟气余热利用是微不足道且费事的念头,重视余热利用与投身国家能源节约行动当中。
按照上述烟气余热发电规划,已经被利用过的烟气从余热锅炉出来后,温
度仍然有300C,由于温度较低,其热能品位降低,禾I」用难度加大。
为充分利用好能源,提高能源利用效率,根据烟气余热梯级利用原理,其热量可以被用来产
生余热锅炉补汽。
但是从补汽锅炉出来的烟气温度仍然有200C左右,这部分烟
5-5。
气仍包含热量,对此,这部分热量可以用来产生热水用于预热物料、解冻(北方地区)、洗澡、洗碗用,然后被冷却到120C以下的烟气可以符合标准的进入布
袋除尘器进行处理。
整个烟气余热发电综合利用方案系统示意图如图
I、400C烟气2、余热锅炉3、300C烟气4、补汽锅炉5、200C烟气6、换热器7、100C烟气8、布袋除尘器9、可排放烟气10、循环水
II、80C热水12、预热解冻13、洗澡洗碗14、20C补水15、150C补汽16、290C蒸汽17、汽轮机18、变压器119、变压器220、用户
图5-5烟气余热发电综合利用方案系统示意图
该方案从能源利用与工艺角度来讲,它能源利用比较充分,能源利用率高,
出口烟气温度能立即达到布袋尘除尘器的要求,不需要另外投资降温装置,工艺
配合性好。
但是从经济性角度来考虑,也许还有更好的方案。
5.3.3.1烟气余热加热配套产品综合利用方案
工业硅矿热炉烟气寓含的大量热量可以实现多种用途,除了发电之外,实际上,电还只是一