自卸车生产工艺过程作业指导Word文档格式.doc
《自卸车生产工艺过程作业指导Word文档格式.doc》由会员分享,可在线阅读,更多相关《自卸车生产工艺过程作业指导Word文档格式.doc(6页珍藏版)》请在冰点文库上搜索。
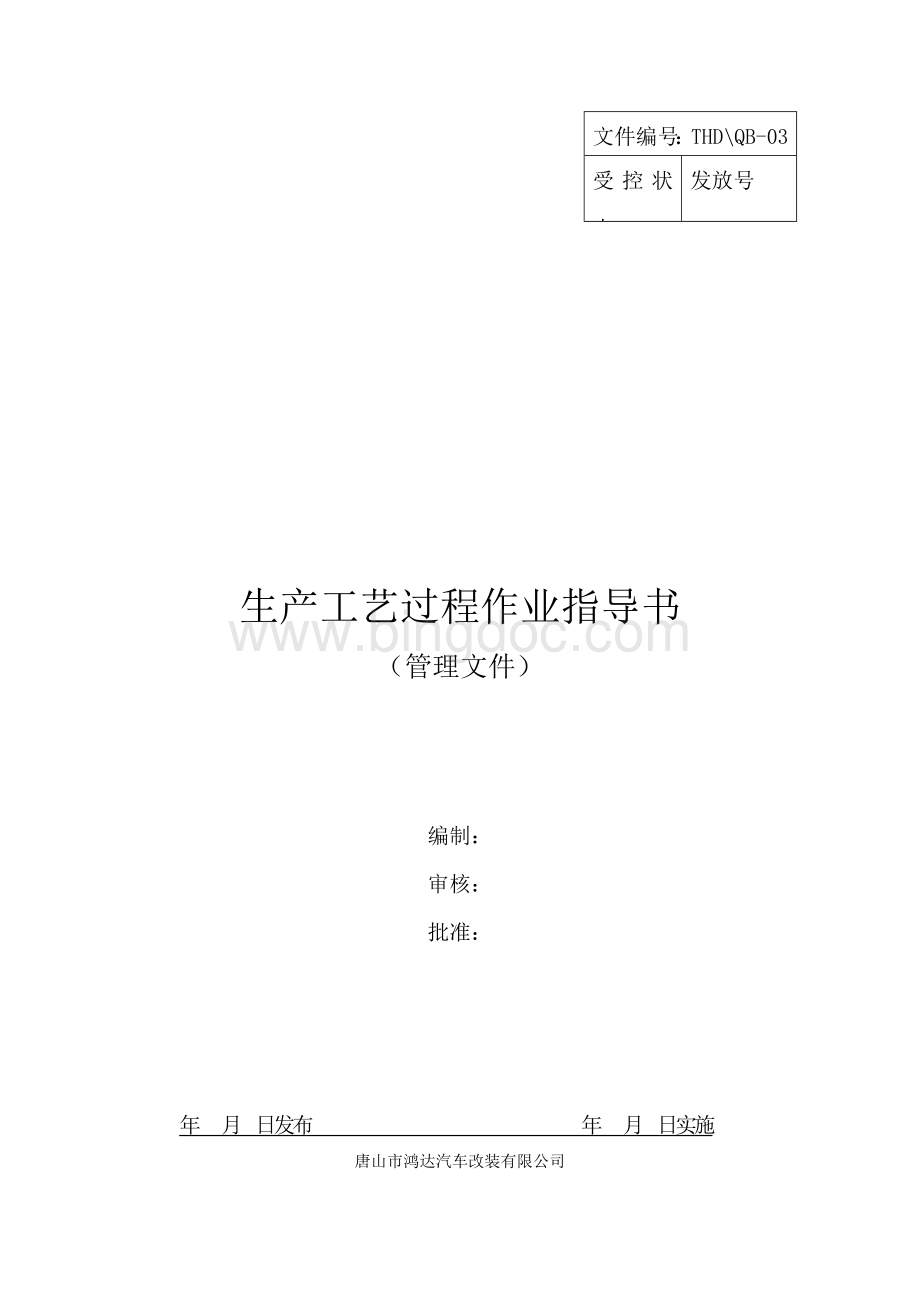
THD\QB-03页码:
1/5
一、拼梁
①首先认真读懂生产任务书。
②根据生产任务书确立主梁的上下及立筋的几何尺寸和穿梁孔形状与尺寸。
③根据主梁的各部位尺寸备料。
④备料时应清除所用材料上的各种杂质(飞溅、氧化物等)。
⑤备完料,根据主梁的几何尺寸在材料上画线,经复尺后下料。
⑥下完料,拼组主梁时,所有焊接口都应根据材料厚度按35度角取双面坡口,焊接材料材质应与主材材质相同。
⑦主梁组拼为间断式点焊成型,其间断为500mm。
焊缝处应高于主材1-2mm。
焊缝丰满平整无缺陷。
焊完后清除药皮,飞溅物、氧化物。
并将超出标定尺寸的余料割除。
⑧在此过程中,应保证主梁立筋与上下板垂直,误差小于等于2mm;
梁高偏差不得超过3mm,检查合格后,标明车号。
二、焊接
①先看待焊主梁上有无药皮飞溅、氧化物等杂质,如有除掉,再用卡具卡紧带焊。
焊主梁卡至焊床上。
②查调试焊机是否正常,焊条、焊丝是否有杂物、潮湿等现象,如有处理掉。
焊接时,根据待焊主梁的厚度适当调节焊机的电流和电压,控制好焊接速度。
③焊接过程中,随时清理焊接药渣与检查焊接质量,出现缺陷进行修补。
④12×
16mm梁焊接不得小于Δ7×
8mm;
14×
22mm梁焊接不得小于Δ8×
10mm;
整车主梁焊缝不允许出现气孔,在300mm长的焊缝上加渣不得超过3处;
不得有明显啃边,啃边长度不得超过30mm,深度不得超过2mm。
⑤注意梁脖部分用手工补焊时一定要清理干净与埋弧焊口衔接处的各种残渣,保
2/5
证焊口接口处不出现缺陷。
⑥焊完梁,清理掉药皮、飞溅、氧化物等杂质。
三、调梁
①主梁调直用火焰调直,在调直前应先挑选两根长度相同,梁高偏差不超过3mm的成品梁并在一起。
检查待调直梁是否有焊接缺陷,如没有缺陷即可调直。
②调梁时应注意火焰温度严禁超过900℃,钢材呈现红黄色,不允许出现芥皮现象。
③调直的目的是将大梁调直,其左右旁弯≤5mm;
调到上弧旋高度≥25mm,两根梁并齐后的弧旋要均匀对称分布。
④再调直过程中,应先调上弧旋,后调旁弯。
⑤调上弧旋时应在力板上用三角火焰加热,加热方向由里指向边缘。
调旁弯时,应用线状或三角形加热翼板向外突起的一侧。
⑥调梁完毕,根据生产任务截取梁长,其偏差≤3mm。
截取后,清理干净氧化物等杂质,并矫正修复即可。
四、车架组装
①组装前认真阅读生产任务单,对生产任务提出的中心销型号,摆放位置悬挂定位,大梁中心距,车的长宽尺寸等技术要求认真阅读,做好各种组装准备工作。
②车驾中心距要求在拼装架上摆放车驾大梁,测量大梁对角线后,用丝杆卡具定位。
大梁中心偏差≤3mm。
两根大梁在车驾中心偏差≤3mm。
③定位完大梁,穿穿梁柱,找好尺寸点焊定位;
然后安装边梁,定位车架,车架对角线不得超过±
5mm边梁垂直度不得超过3mm,根据车架长度确定边梁的弧旋高度,最大弧旋不得超过25mm,并且均匀分布。
④中心销定位,其根据是生产任务单,中心销定位采用挂线三角定位法,要求其
3/5
左右以及与前边梁尺寸偏差不得超过3mm。
⑤悬挂定位,其左右前后偏差不得超过3mm;
悬挂中心距的确定必须以中心销为
基准来确定,偏差不得超过3mm
⑥再组装完毕后,清除各焊点处药皮、飞溅和氧化物。
五车驾焊接
1、车驾焊接是在反转平台架上进行,采用CO2保护焊,焊接施焊前应做如下工作:
a)检查翻转平台架上卡具是否卡紧,牢固可行,如发现问题应即时处理后方可施焊。
b)检查是否有遗漏变形,发现问题及时报告处理。
2、焊接时应从后向前或从前向后施焊,以免发生漏焊,焊肉应饱满,不允许有加渣、气孔、咬边。
3、摩擦板,应先外后里的顺序施焊,以保证摩擦板焊接后,弯曲变形不超过或<5mm,摩擦板衔接后,焊缝不允许超过中心销装配件的接口。
4、焊接完毕,应认真清理焊渣和飞溅,特别是摩擦板上的飞溅物必须清理干净、整洁。
5、检查各部位是否有焊缝和焊接缺陷,发现后及时修补,焊接过程中不允许在工作表面出现电弧划伤的痕迹。
六、车用立柱、工具箱、车厢板及小件制作焊接。
1、立柱
a)根据图纸生产任务单所注明的技术数据,确立立柱的高度、宽度、制作焊接。
b)前桥架的长宽高几何尺寸,制作中必须严格按图纸要求的技术参数进行。
2、工具箱
工具箱制作,应根据图纸、生产任务单提出的技术要求下料、组对、焊接、箱体
4/5
配合不得超过1mm,折弯角度成90°
为成型标准,工具箱的门与框的四边间隙不
得超过3mm,开启自由灵活,平整光滑。
3、各种小件焊接完毕后,应清除药皮,飞溅物认真检查有无焊接缺陷,复尺检查是否符合图纸规定的几何尺寸,不允许在工件上出现电弧划痕,清理各种工艺焊点,必要时用角磨机修复,检查无误后标明车号,将各种工件摆放指定地方待用。
4、车厢制作焊接
a)根据图纸,确定车用厢板的长宽高几何尺寸。
b)厢板外侧单面焊缝焊接时,不得高于用才2mm。
c)划子板,合叶安装焊接时,要水平垂直,如方管网格在300×
400mm以上时,面板与方管应外加焊点,每边各两点,外加焊点长度不少于30mm,要分布对称均匀。
d)厢板内侧面板安装焊接时要逐步将面板展开压实,焊点长度不小于30mm,且分布对称均匀。
半挂车装配整车:
b)厢板的安装,根据车驾标明的号码,到存放场地取,厢板与立柱等小件组装时应确保立柱与厢板之间间隙,上下均匀,左右对称,其偏差≤2mm。
七:
打磨喷漆
①打磨用角磨机,在打磨前先检查角磨机,确定机器正常后开机进行打磨。
②通过打磨使车外观无浮锈及渣尘死角,焊缝无残留药渣和飞溅氧化物,各装配件无剪切覆羽边。
③修理焊接缺陷和电弧划伤点。
整车内外清扫后,再进行喷漆。
5/5
④用手喷枪进行喷漆,应注意手喷枪的移动速度平稳从而达到:
漆喷的均匀。
且
无喷漏现象,整车内外无坠漆和泪痕。
⑤在换颜色时,在两种颜色临界处要注意不能相混,可用报纸挡住可能受影响区域进行喷漆。
八、安装车桥:
①安装车桥须采用三角定位,应在工装平台上进行,尺寸应符合图纸要求。
②前车轴安装用天车或龙门吊将车体吊起,垫好架凳,采取必要的防护措施,防止吊车钩脱落,将前轴(带轮胎)滚入板簧前端达到前悬挂下方,逐渐下落天车或龙门吊,后板簧后端落入平衡悬挂前端,将拉臂放入前悬挂拉臂加强套中,穿好前悬挂拉臂销轴及挂簧套。
③后轴安装滚动后轴使板簧前端落入平衡吊耳后端,落入平衡悬挂前端,将拉臂放入前悬挂拉臂加强套中穿好前悬挂,拉臂销轴及挂簧套。
九、电气路安装:
1、电路安装
a)全车电器安装功能齐全
b)全车电器牢固无缺
c)牵引车挂接后灯光齐全,无错接、短路、断路等现象,灯光亮度正常,电路接线准确。
2、气路安装
a)气路密封良好
b)将制动管路系统通入压力达到553kpa压缩空气切断气源后,挂车处于非制动状态下,3分钟降压值不小于10kpa,气路制动时,压力达到535kpa在15分钟内压降<10kpa。