现代表面技术Word文档格式.docx
《现代表面技术Word文档格式.docx》由会员分享,可在线阅读,更多相关《现代表面技术Word文档格式.docx(13页珍藏版)》请在冰点文库上搜索。
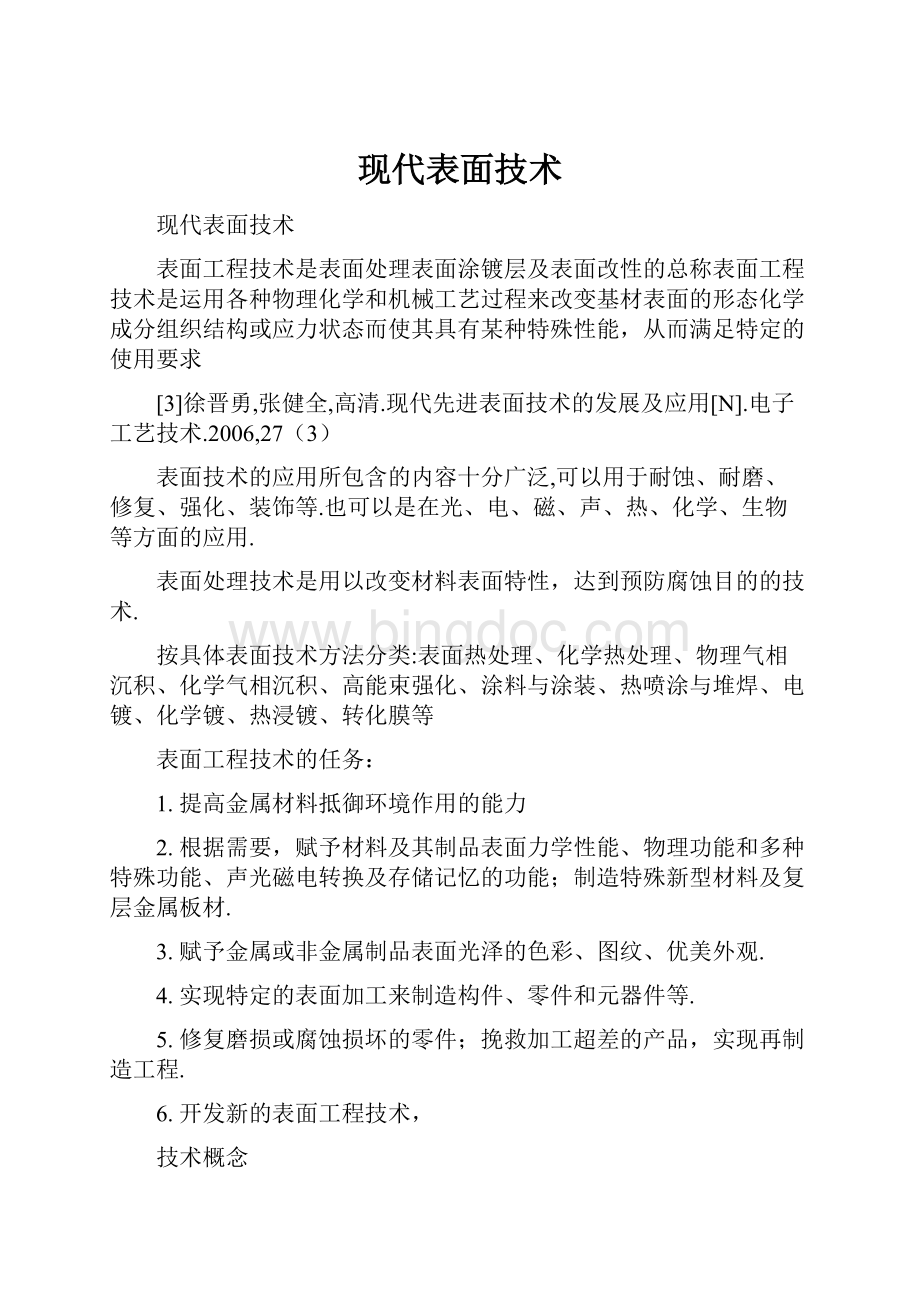
是在无外电流通过的情况下,利用还原剂将电解质溶液中的金属离子化学还原在呈活性催化的工件表面,沉积出与基体牢固结合的镀覆层.工件可以是金属也可以是非金属.镀覆层主要是金属和合金.
涂装:
用一定的方法将涂料涂覆于工件表面而形成涂膜的全过程.涂料为有机混合物,可涂装在各种金属、陶瓷、塑料、木材、水泥、玻璃制品上.
气相沉积:
在金属或非金属材料基体表面牢固沉积同类或异类金属或非金属及其化合物,以改善原材料基体的物理和化学性能或获得新材料的方法.按反应类型分为物理气相沉积和化学气相沉积.
化学转化膜
[5]庞建超,李世杰,曹晓明.现代表面工程技术的发展及应用[N].天津冶金46-49,2005
(1).
热浸镀
简称热镀是一种早就普遍的用来制作金属制品的表面处理方法,一般是将处理好的待镀件浸入熔融的金属液体之中,基体材料与镀层金属发生反应进行冶金结合,从而具有特定的性能,主要是防腐蚀性能和装饰性能.
[3]徐晋勇,张健全,高清.现代先进表面技术的发展及应用[N].电子工艺技术.2006,27(3).
热喷涂是利用一种热源将喷涂材料加热至熔融状态,并通过气流吹动使其雾化高速喷射到零件表面,以形成喷涂层的表面加工技术
气相沉积技术:
物理气相沉积:
在真空条件下,采用物理方法,将材料源——固体或液体表面气化成气态原子、分子或部分电离成离子,并通过低压气体(或等离子体)过程,在基体表面沉积具有某种特殊功能的薄膜的技术.
沉积过程的3个阶段:
从原材料中发射出粒子;
粒子运动到基材;
粒子在基材上积聚、形核、长大、成膜.
物理气相沉积的分类有,真空蒸发沉积、溅射沉积、离子沉积、外延沉积、电阻蒸发沉积、外延沉积离子镀等.
特点:
1.沉积层需要使用固态的或者熔融态的物质作为沉积过程的源物质,采用各种加热源或溅射源使固态物质变为原子态;
2.源物质经过物理过程而进入气相,在气相中及在基材表面不发生化学反应;
3.需要相对较低的气体压力环境下沉积,沉积层质量较高;
4.沉积层较薄,厚度范围通常为纳米或微米数量级;
5.沉积层组织致密,与基材具有很好的结合力,不易脱离;
6.沉积层薄,易生长出单晶、多晶、非晶、多层、纳米层结构的功能薄膜
7.无有害废气排出,属于无空气污染技术
8.基材选用范围很广,可以使金属、陶瓷、玻璃或塑料等
应用:
高档手表金属外观件的表面处理方面达到越来越为广泛的应用
化学气相沉积(CVD):
在一定的真空度和温度下,将几种含有构成沉积膜层的材料元素的单质或化合物反应源气体,通过化学反应而生成固态物质并沉积在基材上的成膜方法.
制膜过程:
1.反应气体的热解
2.反应气体向基材表面扩散
3.反应气体依附于基材的表面
4.在基材表面上发生化学反应
5.在基材表面产生的气相副产物脱离表面而扩散掉或被真空泵抽掉,在基材表面沉积出固体反应产物薄膜.
影响因素:
薄膜的组成、结构与性能还会受到CVD内的输送性质(包括热、质量及动量输送)、气流的性质(包括运动速度、压力分布、气体加热等)、基板种类、表面状态、温度分布状态等因素的影响.
所形成的膜层致密且均匀,膜层与基体的结合牢固,薄膜成分易控,沉积速度快,膜层质量也很稳定,某些特殊膜层还具有优异的光学、热学和电学性能,因而易于实现批量生产.CVD的沉积温度通常很高,在900℃~2000℃之间,容易引起零件变形和组织上的变化,从而降低机体材料的机械性能并削弱机体材料和镀层间的结合力,使基片的选择、沉积层或所得工件的质量都受到限制.
CVD装置示意
加热方式:
电加热、高频诱导加热、红外辐射加热和激光加热.
反应物质源:
1.气态物质源
2.液态物质源
3.固态物质源
化学气相沉积技术:
1.金属有机化合物化学气相沉积技术(MOCVD)
2.等离子化学气相沉积(PCVD)
3.激光化学气相沉积(LCVD)
4.低压化学气相沉积(LPCVD)
5.超真空化学气相沉积(UHVCVD)
6.超声波化学气相沉积(UWCVD)
1涂层保护:
用CVD法制备的TiN、TiC、T(iC,N)等薄膜具有很高的硬度和耐磨性,在刀具切削面上仅覆1~3μm的TiN膜就可以使其使用寿命提高3倍以上.
2.微电子技术:
在超大规模集成电路制作中,化学气相沉积可以用来沉积多晶硅膜、钨膜、铝膜、金属硅化物、氧化硅膜以及氮化硅膜等,这些薄膜材料可以用作栅电极、多层布线的层间绝缘膜、金属布线、电阻以及散热材料等.
3.超导技术:
CVD制备超导材料是美国无线电公司(RCA)在20世纪60年代发明的,用化学气相沉积生产的Nb3Sn低温超导带材涂层致密,厚度较易控制,力学性能好,是目前烧制高场强小型磁体的最优良材料.
4.太阳能利用:
目前制备多晶硅薄膜电池多采用CVD技术,包括LPCVD和PCVD工艺.现已试制成功的硅、砷化镓同质结电池以及利用Ⅱ~Ⅴ族、Ⅰ~Ⅵ族等半导体制成的多种异质结太阳能电池,如SiO2/Si、GaAs/GaAlAs、CdTe/CdS等,几乎全制成薄膜形式,气相沉积是它们最主要的制备技术.
刀具涂层:
国际CVD发展现状:
CVD技术发生突变的是九十年代中期新型MT-CVD(中温化学气相沉积)技术的出现.新型MT-CVD是以含C/N的有机物乙腈(CH3CN)为主要反应气体和TiCL4、H2、N2在700~900℃下产生分解、化学反应,生成TiCN的一种新方法,可获得致密纤维状结晶形态的涂层,涂层厚度可达8~10μm.这种涂层结构具有极高的耐磨损性、抗热震性及韧性,并可通过HT-CVD(高温化学气相沉积)工艺技术在表层沉积上Al2O3、TiN等抗高温氧化性能好、与被加工材料亲和力小、自润滑性能好的材料.MT-CVD涂层刀片适合于高速、高温、大负荷、干式切削条件下使用,其寿命可比普通涂层刀片提高1倍左右.
从目前的发展来看,CVD工艺(包括MT-CVD)主要用于硬质合金车削类刀具的表面涂层,其涂层刀具适合于中型、重型切削的高速粗加工及半精加工,尤其是α-Al2O3涂层是目前PVD技术所难以实现的,因此在干式切削加工中,CVD涂层技术仍占有极其重要的地位.
刀具涂层PVD技术:
目前PVD技术不仅提高了薄膜与刀具基体材料的结合强度,涂层成分也由第一代的TiN发展到了TiC、TiCN、ZrN、CrN、MoS2、TiAlN、TiAlCN、TiN-AlN、CNx等多种多元复合涂层,且由于纳米级涂层的出现(见图2、3ZX涂层,即TiN-AlN涂层),使得PVD涂层刀具质量又有了新的突破,这种薄膜涂层不仅结合强度高、硬度接近CBN、抗氧化性能好,并可有效地控制精密刀具刃口形状及精度,在进行高精度加工时,其加工精度毫不逊色于未涂层刀具.
我国用于刀具涂层的PVD技术:
国内成功开发出了硬质合金TiN-TiCN-TiN多元复合涂层工艺技术,并达到了实用水平.仍以单层TiN涂层为主.
我国刀具PVD涂层技术存在的主要问题:
国外涂层设备的集中引进给PVD技术的后续发展造成了某些负面影响;
与国外相比国内对新工艺的开发重视不够;
在设备的开发上缺乏统一性、合理性及协作性;
涂层质量的不稳定制约了涂层技术的推广应用;
售后服务的欠缺制约了国产涂层设备的推广应用;
国内机械加工的低水平也制约了涂层技术的迅速发展
发展方向:
下一步应该朝着减少有害生成物,提高工业化生产规模的方向发展.同时,CVD反应沉积温度的更低温化,用CVD更精确地控制材料的组成、结构、形态与性能技术的开发,厚膜涂层技术、利用残余应力提高材料强度的技术、大型连续CVD薄膜及涂层制备技术、新材料的合成技术,具有新的结构的反应器的研制,新的涂层材料及具有新的更能的材料体系的探索等
CVD方法和PVD方法的主要区别
项目
PVD方法
CVD方法
物质源
生成物的蒸气
含有生成物组分的化合物蒸气
激发方式
蒸发热的消耗
激发能的供给
形成温度
250-2200℃(蒸发源)
25℃-适当温度(基材)
150-2000℃(基材)
生长速率(μm/h)
25-240
25-1500
可能制备的薄膜材料
所有固体,卤化物,热稳定的化合物
除了碱金属以及碱土金属以外的所有金属,氮化物、碳化物、氧化物、金属间化合物等
用途
表面保护膜、光学薄膜、电子器件用膜等
装饰膜、表面保护膜、光学膜、功能薄膜等
二者结合:
等离子体增强化学气相沉积(PECVD)技术
电镀目的:
1.提高金属制品的耐腐蚀能力,赋予制品表面装饰性外观
2.赋予制品表面某种特殊功能.如提高硬度、耐磨性、导电性、磁性、抗高温氧化性等
3.提供新型材料.如制备具有高强度的各种金属基复合材料,合金、非晶态材料,纳米材料等.
电镀基本原理:
电镀的基本过程是将零件浸在金属盐的溶液中作为阴极,金属板作为阳极,接通电源后,在零件表面就会沉积出金属镀层.
电镀基本过程示意
电源:
大多数电镀设备使用电压为6-12V的不同功率的电源,铝及其合金在阳极氧化时需要电压为60-120的直流电源
阳极:
一般采用与镀层金属相同的块体金属做可溶性阳极
阴极:
预处理(机械处理,化学处理,电化学处理,超声波处理)
电镀挂具:
主要作用是固定镀件和传导电流.要求:
良好的导电性和化学稳定性;
有足够的机械强度,保证装夹牢固;
装卸方便;
非工作部分绝缘处理.
电镀槽:
主要工艺槽
电镀溶液:
主盐,导电盐,络合剂,缓冲剂,稳定剂,阳极活化剂,添加剂,
影响镀层质量的主要因素:
1.镀前处理质量
2.电镀溶液的本性
3.基体金属的本性
4.电镀过程电流密度、温度和搅拌等因素的影响
5.析氢反应
6.镀后处理
单金属电镀:
镀锌、镀镍、镀铬、镀铜、镀银
合金电镀:
电镀铜锡合金、电镀铜锌合金
复合电镀:
是将一种或多种不溶性颗粒经过搅拌使之均匀地悬浮于镀液中,在电场作用下使颗粒与基体金属共沉积而形成复合镀层的一种沉积技术.
[4]郁祖湛.电子电镀与表面处理技术的研发动态[N].电镀与精饰.2010,33(9);
2印制电子技术与宏电子产业
印制电子技术不断提高,将推动宏电子产业的快速发展.我国在近半年内,进行了两次关于印制电子技术的研讨会.2009年11月30日在珠海度假村酒店举行印制电子技术论坛暨印制电子省部级产学研联盟成立大会.2010年3月18日上海国际展览中心举行印制电子新技术研讨会(第二次).2010年9月在复旦大学正式成立了复旦大学-安捷利全印制电子研发中心,从事全印制技术的开发和产业化研究.
英国ConductiveInkjetTechnology公司在珠海会议上展示了他们的产品,并且已经有催化剂、墨水及加工设备销售.在PET薄膜上用柔性印刷技术制作电子标签.要步骤是,利用丝网印刷,在PET薄膜上印制含钯催化层的图形,而后进行化学镀铜,整个过程是在卷到卷自动机上完成.图1为该公司展示的卷到卷生产流程中的一个环节.
图1卷到卷生产流程的一个环节照片
3印制板喷墨打印新工艺
德国纽伦堡应用科技大学W.Jillek教授最近传给复旦大学杨振国教授1幅照片(见图2),是在塑料基材上用碳纳米管做浆料制作的印制板(PCB),线宽50μm,喷制6~8层.
图2以碳纳米管为浆料喷墨打印的PCB板照片
我国的电子工业在制作PCB板时,原来是用银浆料,现正努力开发铜纳米浆料,难度很大.而德国纽伦堡应用科技大学用碳纳米管制作成本大幅下降,更具有实用价值.
4三维模塑互连器件或电子组件(3D-MID是Three-dimensionalmouldedinterconnectdeviceorelectronicassemblies的缩写)
3D-MID的加工工艺主要有三种方法,双组分注射成型法、热冲模压法和激光直接成型法(LDS).,LDS是一种加工的3D-MID新兴工艺.LDS技术用于3D-MID制造是近年来德国LPKF公司发明并在全球迅速发展的一门新兴技术.其产品在电气性能、结构和抗氧化性能有突出的优点.
5印制线路板化学镀锡
厚度合适的化学镀锡层,应用于PCB板行业,彻底排除Pb的污染.实验镀层δ为1.5μm,能经受155℃老化4h或3次重熔的考核试验,在40℃相对湿度93%条件下受潮试验4d,可焊性良好.该化学镀锡液工艺简单,镀液稳定,加工周期短,操作方便,在PCB板行业中有广阔的应用前景.
6真空镀与电镀、有机涂层相结合技术
1)屏蔽布,在涤纶布上真空溅射镀镍+电镀铜.2)锌镁合金镀层钢板,在钢板上电镀Zn+真空镀镁+高温退火,可提高耐蚀性2~3倍.3)溅射电镀型二层挠性覆铜板2-FCL.4)铝轮毂有机膜层+真空镀铝+有机保护层.
8电沉积纳米超疏水镍薄膜材料
由上海交通大学材料学院李明教授课题组开发的电沉积方法制备微纳米分级结构超疏水镍薄膜,取得很大进展,在不同电流密度和时间下电沉积镍薄膜的扫描电镜照片见图3.
图3电沉积镍薄膜的扫描电镜照片
四种不同表面的润湿性示意图.从图4可以看出电沉积方法制备微纳米分级结构超疏水镍薄膜表面与液滴的接能面积最小.
图4不同表面的润湿性示意图
10电镀技术研发中的新热点
1)离子液体中电沉积.
上海交通大学郭兴伍教授课题组发表的《氯化胆碱-尿素离子液体中Zn的电沉积行为及其在AZ91D镁合金上的电镀研究》指出此体系不吸水,很有发展前景,哈尔滨工业大学安茂忠课题组也有多篇有关论文发表
2)硅烷复合稀土转化膜技术.
其保护特性很好,只是有机硅膜的稳定性有待进一步提高
发展前景思考:
电镀技术的劣势是对环境有一定污染,但有可能控制.
制约电镀行业的发展是污染问题,电镀属高污染行业,环保问题关系到行业发展和生存的最重要的问题.因此,也是电镀行业必需要认真面对和解决的问题
如何攻克环保关,需做好以下四方面工作:
1)研发、推广更多技术先进、环境友好型工艺,实施清洁生产,从源头上减少污染.
2)研发、推广真正在技术、经济上可行的三废治理技术.
3)要对电镀行业污染进行科学分析,包括重金属排放标准科学确定,有氰工艺的科学评价,COD测定方法的重新审定等.
4)在技术层面上提供了有效途径后,加强执法,使违法成本不致太低.
热喷涂有4种基本方法:
火焰喷涂、电弧喷涂、等离子喷涂和特殊喷涂.
火焰喷涂就是以气体火焰为热源的热喷涂.电弧喷涂是以电弧为热源的热喷涂.等离子喷涂是以等离子弧为热源的热喷涂.
热喷涂是最先在航空领域发展起来的,然后逐渐辐射到其它的工业领域.目前主要在航空航天、高温超导、电磁电子、生物医学和复合材料五个方面应用
[1]刘光明.表面处理技术概论[M].化学工业出版社.2011;
[2]杨西,杨玉华.化学气相沉积技术的研究与应用进展[J].甘肃水利水电技术.2008,44(3);
[3]刘晓红,陈志勇,邓山江.气相沉积技术的现状与发展[N].华北航天工业学院学报.2006,16(3);
[1]田 威,李小宁,郭 钰.冲击式小型气动马达机械特性研究[N].南京理工大学学报.2006,30
(2);
[2]刘暾,刘育华,陈世杰.静压气体润滑[M].哈尔滨工业大学出版社.1990;
[4]JanPeirs,DominiekReynaerts,FilipVerplaetsen,MichaelPoesen.AMicroturbineMadebyMicro-Electro-DischargeMachining[M].The16thEuropeanConferenceonSolid-StateTransducers.September15-18,2002;
[5]SitakantPatra.designandmodelingofaxialmicrogasturbine[D].NationalInstituteOfTechnology,2010.