锡焊检测方法与无铅化进程.docx
《锡焊检测方法与无铅化进程.docx》由会员分享,可在线阅读,更多相关《锡焊检测方法与无铅化进程.docx(14页珍藏版)》请在冰点文库上搜索。
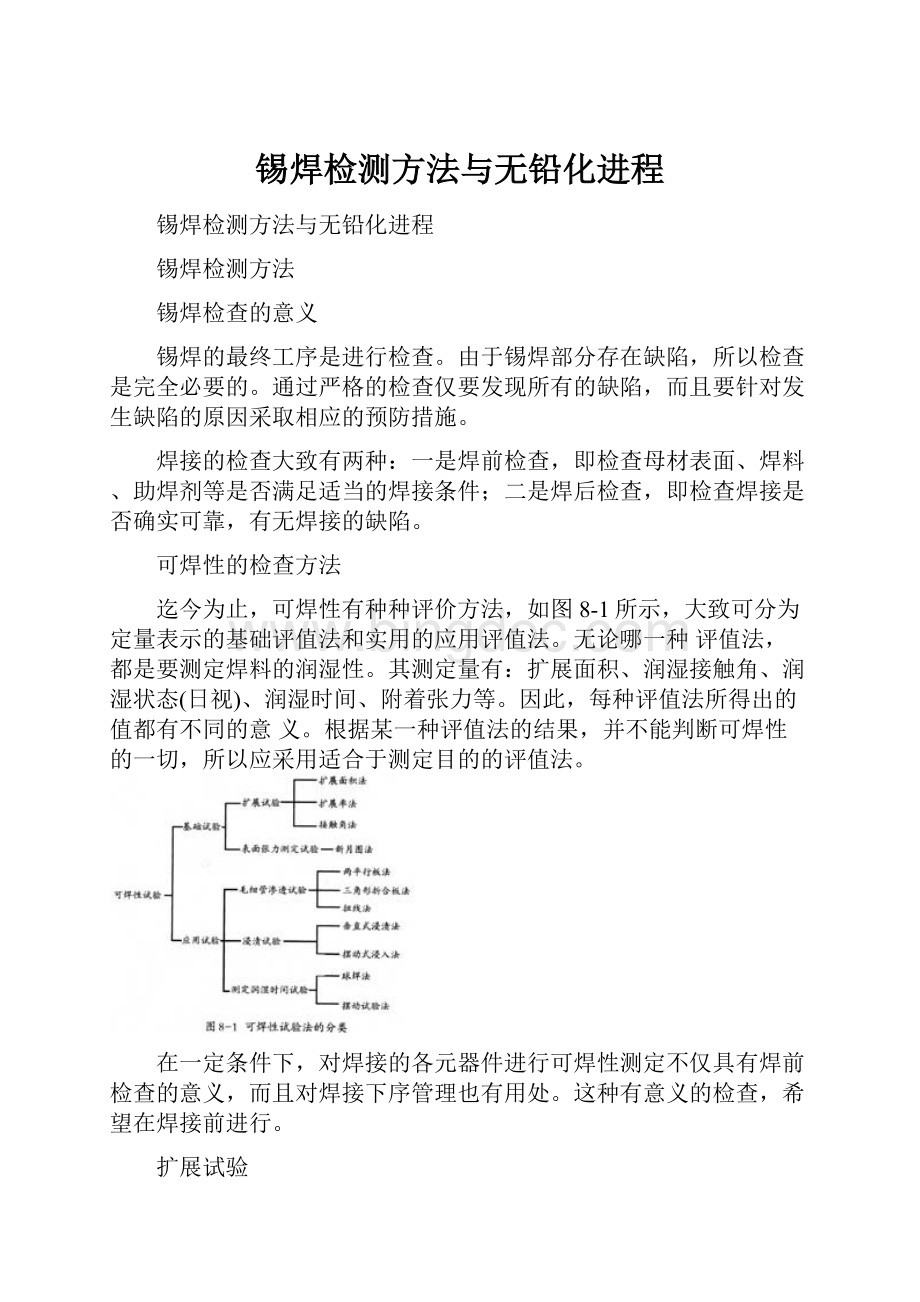
锡焊检测方法与无铅化进程
锡焊检测方法与无铅化进程
锡焊检测方法
锡焊检查的意义
锡焊的最终工序是进行检查。
由于锡焊部分存在缺陷,所以检查是完全必要的。
通过严格的检查仅要发现所有的缺陷,而且要针对发生缺陷的原因采取相应的预防措施。
焊接的检查大致有两种:
一是焊前检查,即检查母材表面、焊料、助焊剂等是否满足适当的焊接条件;二是焊后检查,即检查焊接是否确实可靠,有无焊接的缺陷。
可焊性的检查方法
迄今为止,可焊性有种种评价方法,如图8-1所示,大致可分为定量表示的基础评值法和实用的应用评值法。
无论哪一种评值法,都是要测定焊料的润湿性。
其测定量有:
扩展面积、润湿接触角、润湿状态(日视)、润湿时间、附着张力等。
因此,每种评值法所得出的值都有不同的意义。
根据某一种评值法的结果,并不能判断可焊性的一切,所以应采用适合于测定目的的评值法。
在一定条件下,对焊接的各元器件进行可焊性测定不仅具有焊前检查的意义,而且对焊接下序管理也有用处。
这种有意义的检查,希望在焊接前进行。
扩展试验
它是测定焊料在母材平板上的扩展性,是测定熔融焊料润湿性最普通的方法。
用扩展试验对可焊性的评值法有扩展面积、扩展率(焊球高度和扩展高度之比)、接触角等。
1.扩展面积法,扩展面积法是把一定量的焊料在规定的母材板上扩展以测定扩展面积。
扩展面积越大表示可焊性越好。
评值法有两种:
一定体积(或重量)的焊料的扩展面积的对比。
本法的优点是不用特殊试验装置就能简便地定量评定可焊性的数值,也可应用于助焊剂的性能试验。
2.扩展率法(ASTM-B-545)。
扩展率法是用一定量的焊料在母材板上扩展,如图8-2所示。
扩展率是特扩散焊料作为一个球的直径和焊料扩展中心高度之比,可用下式求得:
扩展率(%)=(D-H)/D×100
式中,H为扩展后焊料中心高度(mm);D为试验用“焊球”的直径(mm)。
用扩展面积法评值,可焊性可以和一定量的焊料对比表示出来。
用扩展率评值,有能定量表示的优点。
但是也有缺点,焊料扩展不均匀时,测定H就很困难。
ASTM规定的测定温度为250±5℃。
3.接触角法。
焊料润湿接触角测定法可采取扩展试验后的试片,沿扩展面积中心作垂直切断后研磨,然后用放大投影仪或显微镜来进行直接测定,如图8-3所示,将焊料扩展看作不完整的球形而间接求得其接触角θ。
接触角(θ)=2tan-lh/X
式中,h为扩展焊料的高度;x为扩展焊料的半径。
θ越小,则焊料的扩展性越大,即可焊性越好。
美国RCA公司提出用目视接触角测定法来评定元器件引线可焊性的方法,如图8-4所示。
把共晶焊锡丝(Φ
0.25mm)在引线上绕一圈,除去多余的线,然后将焊锡线圈浸入聚乙烯二醇恒温液中熔化,用目视法测定熔化在引线上的焊料接触角。
表面张力测定试验
表面张力法是利用母材与焊料之间所作用的表面张力来测定可焊性的方法。
润湿称量法是能定量地直接记录焊料润湿过程的唯一方法,不仅可作可焊性试验,并且可以应用于分析润湿现象。
1.原理。
金属试验片垂直浸入熔化焊料,焊料润湿试验片则附着张力沿直线方向产生作用。
由于附着力是接触角的函数,表示润湿的尺度,因此如能定量测定这个附着张力,便能定量求得焊料的润湿性,用新月图法定量测定附着张力,可间接求得接触角的时间变化。
焊接过程则可用定量来表示。
其测量方法如图8-5所示。
将试验片(板、线材)的一端浸入熔化的焊料中,根据焊料的润湿情况来正确测定试验片(板、线材)上作用的附着张力随时间的变化,以评定可焊性,如图8-6所示。
试验片(棒状)上所作用的润湿力,由于附着张力向下拉,浮力向上推,故润湿力为上述二力之差,于是得出以下列关系式:
F=rifcosθ·2πr-πr2ρgh
式中,F为试验片上的作用(润湿力);rif为焊料的表面张力(焊料—助焊剂的表面张力);θ为接触角;r为试验片的半径;ρ为焊料的密度;g是重力加速度;h为浸入深度。
当h→0,则F=rifcosθ·2πr:
K·cosθ(K:
常数)
由于F只是θ的函数,因此只要测定F即可间接求得表示润湿度的接触角9的变化。
试验片从浸入熔融焊料后到取出的一段时间内,随时间变化的F值和接触角的关系如图8-7所示。
2.装置新月图法的装置由3部分组成:
一种是把焊料槽固定,让试验片和应力检测器成为一体而上下移动;另一种是固定试验片,让焊料槽作上下移动。
润湿力检测装置是新月图法最重要的装置。
能否精密测出微小应力的变化,取决于该装置的精密度。
润湿检测法如图8-8所示,用弹簧(板、线圈)或用电子天平来检测润湿力。
前者是利用弹簧的杨氏模量和用微小变位计读得变位而求得应力。
后者在天平秤的一端悬挂试验片,由于加力于试验片产生微小的变位,将它检波放大送至天平秤另一端的一个机构中,作为传动线圈的动力而起负反馈作用。
因对试验片作用的润湿力和电流成正比例,故记录线圈电流的时间变化,便得知润湿的过程。
图8-9为电子天平秤试验装置方框图。
3.求值法润湿称量的可焊性求值法,是将表示润湿力和时间两者关系的新月图曲线进行分析得到可焊性数值。
根据分析方法的不同,各自的意义也不同。
因此,对可焊性的数值也带来了不同意义,润湿称重典型的润湿曲线如图8-10所示,它的过程可以分为3个阶段。
第1阶段(t0-t3),从浸入到开始润湿的一段时间(浮力对试验片产生作用》第2阶段(t3-t2),进行润湿时间触角逐渐减小,润湿力增大);第3阶段(>t2)润湿力达到最大值。
这些阶段各有其意义,解释方法不同,焊性数值也不同。
润湿称量法的分析方法大致有两种情况:
一是测定曲线特定点的代表值;二是对曲线的全过程月求值。
求图形曲线的代表值,即在图形曲线上规定采用有一定的润湿力数值和润湿力为0的时间作为标准值,然后对试验片的可焊性进行研究。
如图8-10所示,它在假定t1和PW值的情况下测定时间t2以及W值,采用MIL规格。
按MIL-STD-883D规格将PW规定为300dyne/cm,t1为0.59秒,t2在1秒钟以下。
这种求值在实际生产技术中已经使用,并广泛应用于元器件可焊性的前期检查。
求图形曲线的梯度数值,其方法是从焊料润湿开始一直到润湿力最大值为止的全过程,即重视从t3到t2的润湿力的变化。
因此,在润湿时间内,润湿力度增加的比例越大,则润湿性越好。
从图8-11可见,从浮力最大点到润湿力最大值F(o的变化是以指数函数形式增长的,故可写成:
Ft=Fw(1-e-t/τ)
式中Ft为以最大浮力为起点,时间t的润湿力变化;Fw为润湿力最大变化值;τ是时间常数.
当t=τ时,Ft=τ≈0.632Fw
由上式可求得润湿变化的时间常数τ。
简言之,求得润湿力达到最大变化值Fw2/3的时间τ。
这个时间越短,可焊性越好。
4.应用举例:
润湿称量法作为一种定量评定可焊性的方法,可作为元器件的可焊性检查、助焊剂性能检查等。
①元器件引线的可焊性检查。
对焊点进行适当的质量管理必须在元器件焊接质量均匀的条件下才可进行,特别对于自动焊接,必须使各个元器件的可焊性满足一定的标准作为先决条件。
因此,必须定量测定元器件的可焊性作为焊接前的检查,并采用新月图法求其数值。
由于元器件引线的可焊性受到表
面状态和保管环境的极大影响,所以对批量元器件还要进行定期检查。
图8-12表示不同表面状态的同一批元器件在同样的焊接条件下进行试验所得的新月图曲线,可以看出可焊性有明显差异。
对某种新月图润湿曲线必须设立一定的计算标准,对不能满足该标准的批量元器件必须采取表面处理,以去除氧化膜或采用活性强的助焊剂等措施。
②助焊剂性能检查.用扩展试验法和浸渍法虽可对助焊剂的性能进行检查,但定量评定比较困难。
用新月图法能对助焊剂作出定量评价。
图8-13表示3种不同活性助焊剂的新月图法的曲线图。
助焊剂的性能,照样能表示在图表上。
考虑到焊接件的特性和使用环境而选定的助焊剂,采用这个图表就可以制定适当的标准。
8.2.3.毛细管浸透试验
本试验是根据熔融锡料在母材间隙中的毛细管现象来测定浸透距离(垂直上升高度)或测定流入水平放置的两平板间隙中达到指定距离所需的时间。
如图8-14所示,垂直上升高度的试验法有:
①平行板法;②三角形折合板法;③扭线法。
可焊性可根据各自在一定试验条件下焊料上升的高度来估计。
可焊性计值时如用①、②法,必须采用试验片剥离检查或x射线透射检查。
如用③法,则可用目视法直接估计。
扭线法最为简便,经常也可用作助焊剂的性能试验。
除以上介绍的可焊性试验法以外,还有:
测定熔融焊料流经一定距离浸透时间的拉丁法;测定线路板表面可焊性的新月法;对元器件引线可焊性进行润湿时间测定的球焊法等等。
焊点检查方法
焊点的一般检查方法有非破坏性和破坏性检查,锡焊检查法分类如图8-15所示。
电子工业主要进行目视检查和电气检查。
有关电子工业产品的焊接检查至今已提出过多种方法,最终被承认为最实际的方法就是目视检查。
这样,焊接检查几乎都依赖于熟练的检查员目视方法来进行。
但是,为了客观地掌握焊点部分的机械性质和电气特性,以进行完善的质量管理,必须进行抽样的破坏试验或X光射线检查。
目视检查
目视检查可以对单个焊点缺陷乃至线路异常及元器件劣化等同时进行检查,是采用最广泛的一种非破坏性检查方法。
但对空隙等焊接内部缺陷无法发现,因此很难进行定量评价。
目视检测法可用万能投影仪或10倍的放大镜进行检查。
目视检查的速度和精度同检查人员对焊接有关知识和识别能力有关。
这种判断可以按以下基准进行;
1.焊料润湿状态:
焊料的接触角9不仅小,而且流动性好,焊料表面光泽则是理想的;
2.焊料的量引线焊接时,焊料轮廓薄,引线轮廓明显可见;
3.外观无针孔、砂粒、裂纹、桥接、拉尖等微小缺陷。
电气检查
电气检查是焊接产品在加荷条件下通电,以检查是否满足所要求的规范。
它能有效地查出目视检查所不能发现的微小裂纹、桥接等。
检查时使用各种电气测量仪。
电气检查所发现的焊接不良,有导通不良及在焊接过程中引起的安装元器件的热损伤。
前者有微小裂纹、极细线的锡蚀、松香沾附等;后者由于过热使元器件特性恶化、助焊剂分解气体而引起元器件蚀和变质等。
这些缺陷都能通过电气检查验明。
如果能正确地进行目视检查和电气检查,那么几乎所有的缺陷都能发现,这样,焊接检查善了。
X射线透射检查
即在焊接处进行X射线照射,根据X光检查内部缺陷,已成为代表性的非破坏性检查方法。
图8-16表示X射线透射检查法的原理。
X射线透射检查对焊接面积比较大的部件检查比较有效。
机械性破坏检查
机械性破坏检查是将焊接处进行机械性破坏,从它的强度和断裂面来检查缺陷,是一种典型的破坏性检查。
从抗拉强度、剪切强度、疲劳强度、振动强度等来检查,如测定结果比标准小,说明焊点部分有缺陷。
此外,还可以观察断裂面来发现空隙和润湿不良。
因为对所有的成品进行械破坏检查显然是不可能的,所以可进行适量的抽查以作为质量管理手段。
显微镜组织检查
显微镜组织检查是将焊接处切断研磨,用显微镜来观察其界面的检查方法焊料熔蚀、合金层形成及微小裂纹的有效方法。
但是,和机械破坏性检查一样,不能对所有成品进行,只能定期检查建立焊料成份和焊接条件的间接管理。
实负荷检查
实负荷检查就是把每一个焊接部件在实用条件下进行加荷以检查其动作状况,有振动检查、冲击检查、急熟急冷检查、加速度检查、耐压检查等。
根据实用条件把它们组合起来进行实用检查。
要求对每一个成品进行必要的检查,以提供实用合格的成品。
这种检查方法最为严格,可靠性高,航天产品等焊接可靠性要求特别严格的情形才予以采用。
检查设备
焊点的检查用目视法检查最为确实,可靠性最高,这仅是对还没有万能检查设备而说的。
近年来,印制板越来越趋向于微细化和细密化,用目视检查非常困难,很多缺陷被漏检,有时完全不可能作目视检查。
所以,对于微细化高密度化的印制板,必须使用设备作自动检查。
对焊后印制板进行电气线路的电气检查并兼带发现焊接缺陷。
把这种检查设备进一步扩大到对印制板图案进行布线检查的设备,同时也应用了激光与红外技术。
前者接触式电气检查设备,后者是非接触式外观检查设备。
锡焊技术无铅化进程
要实行锡焊技术无铅化是一个长期的过程,必须对锡焊技术基本原理有较深的理解和反复实践才有可能完成企业无铅化的进程。
无铅焊料与有铅焊料
早在上世纪80年代,我国电子工业部在元器件引线可焊性的探讨中,就曾对使用锡基、铅基焊刺进行过非常激烈的争论,我国知名焊接专家也曾提出铅基焊料实用的可能性,当时主要是基于成本约考虑。
我国冶金行业也提出制造低锡焊料以替代锡铅共晶焊料的方案,并在有些企业中有所应用,但是总体来说其性能指标仍达不到锡铅共晶焊料,因此63/37锡铅焊料在上世纪80年代逐步成为我国电子装联锡焊技术的主流焊料,尤其在彩色电视机的应用上(实际上共晶焊料的锡的重量比为61.9%),一直沿用到上世纪90年代和现在。
上世纪90年代后期由于众所周知的原因,铅对人类生存的影响,人们对锡基焊料进行了更多的研究和实践,提出了许多无铅焊料如锡—锌、锡—铋、锡—银—铜等经过许多大型电子工厂的实际使用,并在锡银共晶焊料(锡—3.5%银)在工业界长期使用的基础上逐步形成了以锡—银—铜系列为主的无铅焊料(如锡96.5%、银3%、铜0.5%)。
这一过程的完成将给电子制造业无铅化进程建立一个坚实的新基础。
笔者认为,在这一过程中,实践将是检验和实施无铅化锡焊技术的唯一标准。
无铅锡焊技术对焊接设备的要求
无铅焊料由于其熔点高于锡铅共晶焊料40℃左右,因此必然对焊接设备提出许多新的要求,以下几点是必须解决的。
波峰焊设备锡锅熔蚀问题
这个问题,在使用锡铅共晶焊料时就已存在。
国内在上世纪70年代自制波峰焊设备时就遇到这个问题,当时锡锅采用球墨铸铁和普通钢材,球墨铸铁较不易被熔锡熔蚀。
后又采用不锈钢(不锈铁较易熔蚀)和钛合金(成本较高)。
但使用无铅焊料后熔蚀问题将变得更严重。
因此笔者认为,对不锈钢的表面处理例如可采用不锈钢的离子氮化(并加钛)这应该是一个可行的较好途径。
这个研究领域属于化学热处理的范畴,希望设备厂能加以研究。
无铅焊接设备对助焊剂的选择
由于无铅焊料的可焊性较差,如何选择无铅助焊剂也是设备厂商必须重视的一个问题。
未来无铅助焊剂的发展将采用非有机溶剂助焊剂(这就必须提高预热温度)。
但从目前来看,只有增加助焊剂中的活性含量,这样就会带来离子污染等问题。
无铅锡焊面临的能源问题
由于熔融无铅焊料本身更易于氧化因此对波峰的形状电磁泵和无铅焊料的抗氧化进行研究以节约能源。
无铅锡焊技术对焊接工艺的要求
由于电子锡焊技术无铅化的过程是一个长期的过程,在相当一段时期将有无铅与有铅焊料或镀层共存,这将给搞工艺的技术人员带来麻烦。
因此必须对焊料焊膏焊剂与母材(印制板与元器件的表面镀层)有深刻的认识以制定相应的工艺,特别对于温度敏感区(对元器件印制板镀层的熔融温度)要加以小心处理。
因此工:
艺人员必须熟悉无铅和有铅焊料焊膏焊剂与母材镀层的基本性能,并进行大量实践,对无铅焊接温度曲线(包括波峰焊温度曲线和再流焊温度曲线)进行研究并建立通用标准,以便不断总结提高才能解决无铅化进程中的千艺问题。
浅议焊膏
从电子制造业的发展来看,再流焊工艺将成为主流(特别对于手机等产品),因此焊膏的无铅化将是无铅化进程中的最大难点。
由于无铅焊料可焊性较差,因此必须在焊膏中增加助焊剂含量。
这样将带来焊膏的比重、粘度、触变系数、可焊性、残留物的种种变化。
因此要制作一个好的无铅焊膏,必须对其理化特性和应用特性进行研究,目前特别要制作能适用于细间距、微小器件以及高速印刷的焊膏,这将是国内外许多焊膏厂正在进行的工作。