合成氨工艺操作规程.docx
《合成氨工艺操作规程.docx》由会员分享,可在线阅读,更多相关《合成氨工艺操作规程.docx(72页珍藏版)》请在冰点文库上搜索。
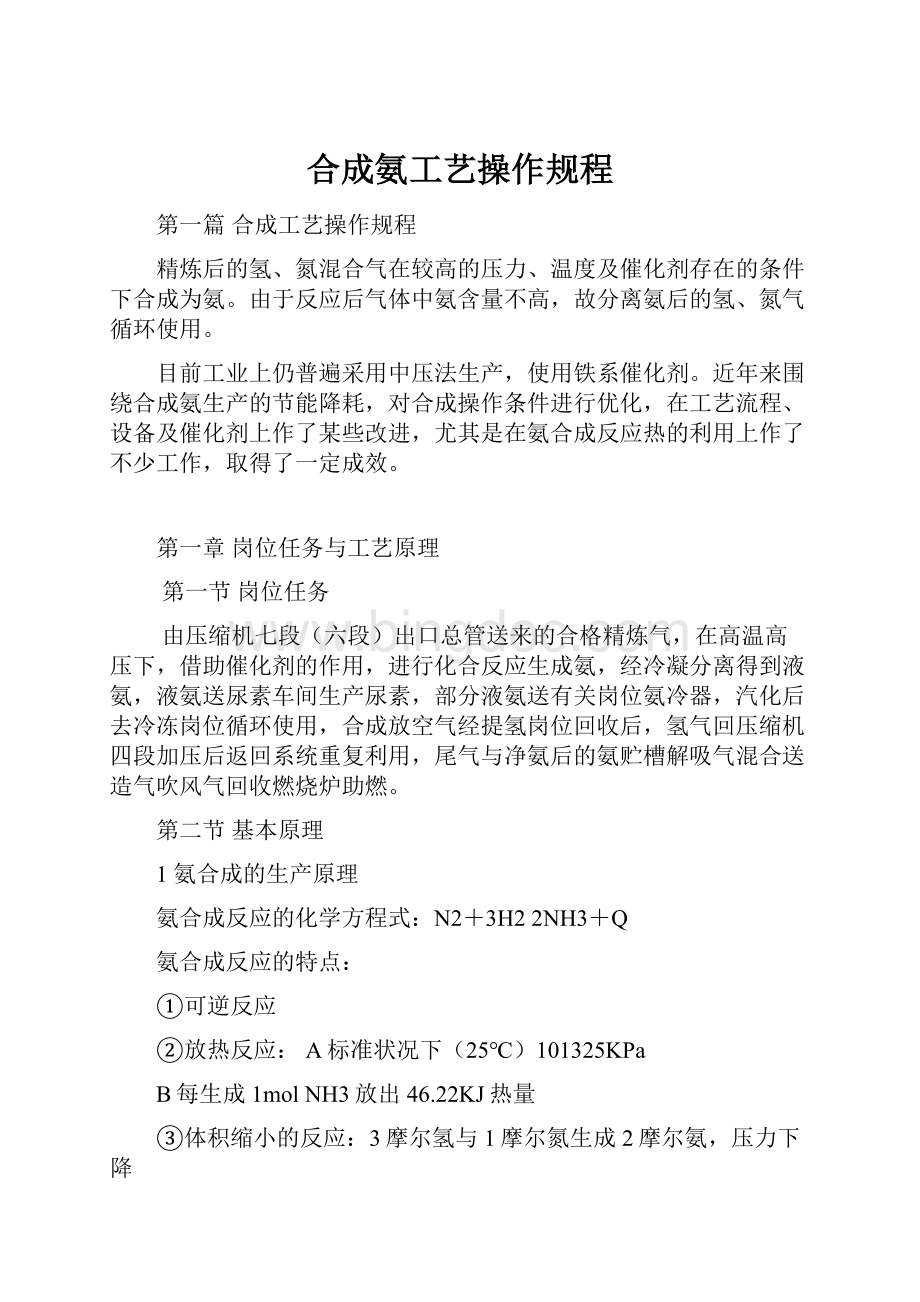
合成氨工艺操作规程
第一篇合成工艺操作规程
精炼后的氢、氮混合气在较高的压力、温度及催化剂存在的条件下合成为氨。
由于反应后气体中氨含量不高,故分离氨后的氢、氮气循环使用。
目前工业上仍普遍采用中压法生产,使用铁系催化剂。
近年来围绕合成氨生产的节能降耗,对合成操作条件进行优化,在工艺流程、设备及催化剂上作了某些改进,尤其是在氨合成反应热的利用上作了不少工作,取得了一定成效。
第一章岗位任务与工艺原理
第一节岗位任务
由压缩机七段(六段)出口总管送来的合格精炼气,在高温高压下,借助催化剂的作用,进行化合反应生成氨,经冷凝分离得到液氨,液氨送尿素车间生产尿素,部分液氨送有关岗位氨冷器,汽化后去冷冻岗位循环使用,合成放空气经提氢岗位回收后,氢气回压缩机四段加压后返回系统重复利用,尾气与净氨后的氨贮槽解吸气混合送造气吹风气回收燃烧炉助燃。
第二节基本原理
1氨合成的生产原理
氨合成反应的化学方程式:
N2+3H22NH3+Q
氨合成反应的特点:
①可逆反应
②放热反应:
A标准状况下(25℃)101325KPa
B每生成1molNH3放出46.22KJ热量
③体积缩小的反应:
3摩尔氢与1摩尔氮生成2摩尔氨,压力下降
④必需有催化剂存在才能加快反应
2氨合成反应的平衡
氨合成反应是一个可逆反应,正反应与逆反应同时进行,反应物质浓度的减少量与生成物质浓度的增加量达到相等,氨含量不再改变,反应就达到一种动态平衡。
从平衡观点来看:
提高反应温度,可使平衡向吸热反应方向移动,降低温度向放热方向移动。
3氨合成反应速度及影响合成反应的因素
反应速度是以单位时间内反应物浓度的减少或生成物浓度的增加量来表示的。
影响氨反应速度的因素:
3.1压力:
提高压力可以加快氨合成的速度,提高压力就是提高了气体浓度,缩短了气体分子间的距离,碰撞机会增多,反应速度加快。
3.2温度:
温度提高使分子运动加快,分子间碰撞的次数增加,又使分子克服化合反应时阻力的能力增大,从而增加了分子有效结合的机会,对于合成反应当温度升高,加速了对氮的活性吸附,又增加了吸附氮与氢的接触机会,使氨合成反应速度加快。
3.3反应物浓度:
反应物浓度的增加,增加了分子间碰撞的机会,有利于加快反应速度。
归纳起来如下:
反应过程必须在高压下进行,压力越高,越有利于氨合成反应的平衡和速度。
反应温度对氨合成反应平衡和速度的影响互相制约。
混合气中氮和氢的含量越高越有利于反应,惰性气体越少越好。
3.4催化剂的影响:
①催化剂又称触媒,它在化学反应中能改变物质反应速度,而本身的组成和质量在反应前后保持不变。
②催化剂的主要作用是降低反应的活化能,加快反应速度,缩短达到反应平衡的时间。
③既然温度对合成氨反应平衡和速度的影响互相矛盾,就存在一个最佳的温度,反应速度对温度的要求是借助于催化剂实现的。
4合成催化剂的组成和结构
铁系催化剂活性组分为金属铁,未还原前为FeO和Fe2O3,Fe2+/Fe3+在0.47-0.57之间,可视为Fe3O4具有尖晶石结构。
作为促进剂的成份有K2O、CaO、MgO、Al2O3、SiO2等。
Al2O3的作用是当催化剂用氢还原时,氧化铁被还原成a-Fe,未被还原Fe3O4保持着尖晶石结构起到骨架作用,防止铁细晶长大,因而增大了催化剂表面,提高了活性。
MgO的作用与Al2O3相似,也是结构型促进剂,通过改善还原态铁的结构而呈现出促进作用。
CaO为电子型促进剂,同时能降低熔体的熔点和粘度,有利于Al2O3与Fe3O4固熔体形成,还可以提高催化剂的热稳定性。
K2O为电子型促进剂,它可以使金属电子逸出功降低,有助于氮的活性吸附,从而提高其活性。
SiO2具有中和K2O、CaO碱性组分的作用。
SiO2还具有提高催化剂抗水毒害和耐烧结性能,通常制成的催化剂为黑色不规则颗粒,有金属光泽。
还原态催化剂的内表面积为4-16㎡/g,催化剂的活性温度一般为350-550℃之间。
5催化剂的还原
Fe2O3和FeO并不能加快氨合成的反应速度,真正起催化作用是具有活性的a-Fe晶粒。
5.1还原方法分类:
将Fe2O3和FeO变成金属a-Fe是催化剂还原过程。
催化剂活性不仅与其组成和制造方法有关,而且还与还原过程的条件和控制方法有关。
催化剂还原反应式为:
Fe3O4+4H2=3Fe+4H2O△H298=149.9kj/mol
触媒整个还原过程为吸热反应,还原温度借助于电加热维持,随着还原的进行,催化剂开始具有活性,并伴有氨生成和放热。
催化剂还原也可在塔外进行,即预还原,预还原有以下优点:
(1)不受热能、塔结构和氨生成的影响,避免了合成塔内不适宜的还原条件对催化剂活性的损害,使催化剂得以在最佳条件下进行还原,有利于提高催化剂的活性。
(2)缩短合成塔的升温还原时间,有利于强化生产。
预还原后的催化剂,需用少量含O2气体加以钝化保护才能转移至合成塔。
5.2还原条件的确定
确定还原条件的原则:
一方面是使Fe3O4和FeO充分还原为a-Fe,另一方面是还原生成铁结晶不因重结晶而长大,以保证有最大的比表面积和更多的活性中心,宜选取合适的还原温度,压力,空速和还原气组成。
还原温度的控制对催化剂活性影响很大,提高还原温度能加快还原反应速度,缩短还原时间。
还原温度过高会导致a-Fe晶体长大,催化剂表面积减小,活性降低。
因此,在实际还原温度不超过它的正常使用温度。
还原气中氢含量尽可能高(>75%)水汽浓度尽可能低(<2g/m3)水汽浓度的高低对催化剂的活性影响很大,尽可能采用高空速以保证还原气中的低水汽含量。
在保证空速的前提下,还原压力低些为好。
5.3催化剂的还原操作
根据塔型号、催化剂还原分为分层还原和整体还原两种:
根据温度变化、出水情况将整个还原分为升温阶段,还原期(初期、主期、未期)降温期、轻负荷等几个阶段。
升温期按40-50℃/小时,迅速将催化剂升温至300℃左右,此时基本无水放出。
还原期根据出水情况提温,出水与提温交替进行。
初期为吸附水,主期为化学水,初还原的催化剂活性高,床层升温快,容易过热进行一段时间,轻负荷生产可以避免催化剂衰老延长使用寿命。
还原操作要点如下:
还原期间温度、压力、循环量、气体成分等工艺条件要稳定。
在正常情况下,不得同时变更多项工艺条件。
严格控制水汽浓度或出水速度,合成塔出水汽浓度不大于3g/m3。
还原过程中要尽量做到高氢比、高空速、低压力,调节温度一般用循环量和电加热器,还原时一般不用副阀调节。
视出水情况提温提压。
严格控制升温曲线,避免温度出现反复波动。
要定时分析合成塔出口气的水汽浓度。
当前工序出现问题时,要及时切断新鲜气。
还原放出水中氨含量大于80%达3小时可放入贮槽。
当出塔水汽浓度连续三次分析<0.1g/m3时,还原即可结束。
(10)还原期间,因循环机跳闸应先停电加热器,保证足够的安全,以免烧断电炉丝。
6催化剂的使用
6.1催化剂的中毒和老化:
原料气中引起催化剂中毒的成分有:
暂时性中毒:
O2、CO、CO2、H2O等
永久性中毒:
H2S、SO2、铜液等
催化剂的衰老受温度影响,催化剂在使用的过程中,由于过热或由于可逆中毒而被反复氧化还原,从而使细晶粒长大,改变了催化剂的结构,导致活性下降。
6.2催化剂的保护
①催化剂升温还原之前应控制速度为30-50℃/h。
防止产生平面温差。
还原出水期间要缓慢升温,防止温度升得太快,防止晶粒长大降低活性。
②新还原的催化剂要保持一段时间的低负荷使未还原的部分继续还原。
③触媒用于生产期间,应稳定操作,使热温度波动在10度以下。
④合成系统停车检修时,升降温速度30-50℃/h。
⑤停车后,合成塔要保持正压,关死进出口阀及副阀,开车时,要将管道内空气用氮气置换合格。
6.3气固相催化反应机理
①气体反应物扩散到催化剂外表面
②反应物扩散到催化剂的内表面
③气体被催化剂表面活性吸附
④在催化剂表面上反应,生成氨
⑤产物自催化剂表面解吸
⑥产物自内表面向外扩散
⑦产物自催化剂外表面扩散到气相
气相中气相中气相中
N2(气相)→N2(吸附)—→2NH(吸附)—→2NH2(吸附)—→2NH(吸附)—→NH3(气相)H2H2H2
6.4工艺条件的选择
(1)根据触媒的型号及不同的使用时期控制较适宜的反应温度。
(2)根据设备的材质及动力消耗选择适宜的操作压力,30MPa左右对氨合成比较有利。
(3)根据触媒层的温度及管道尺寸选择适宜的空间速度。
(4)氨含量接近平衡时,最佳氢氮比趋近3:
1。
同时氮在氨中的溶解度比氢大,溶解于液氨中损失多于氢,因此在生产控制入塔氢氮比低于3:
1,一般为2.8-2.9:
1
第二章工艺流程与工艺指标
第一节工艺流程
1工艺流程简述:
1.11#合成工艺流程
由压缩机七段(六段)出口总管送来的铜洗精炼气经导入阀送入氨冷器出口管,与循环气混合后,进入冷凝塔底部分离套筒内,分离气体中的液氨与油水后进入上部换热器管间,与管内来自水冷排的热气体换热后去循环机加压,气体自循环机出来后进入油分,分离掉油水后气体分四路进入合成塔(一路主线、一路冷副、二路冷激),主线气体由合成塔顶部一次入口进入合成塔内外筒间的环隙,换热后从一次出口出塔,进入气气换热器管间,和管内气体换热后从合成塔二次入口进入塔内下部换热器,与催化剂层来的反应气体换热提温后经中心管进入催化剂层反应,反应后的气体自塔二次出口进入废热锅炉管内。
与废锅内的软水换热,使软水汽化,副产的饱和蒸汽,供变换使用,从废锅出来的混合气体进入软水加热器进行换热,换热后的热软水供铜洗再生使用,出水加热器的气体再进入气气换热器管内,和合成塔一出气体换热。
换热后自换热器底部出,进入水冷却器冷却降温,出冷却器的气体再进入冷凝塔上部换热器管内进一步冷却后进入氨分,分离掉部分液氨,其后气体再进入氨冷器进一步冷却降温,出氨冷器后的循环气和补入的新鲜气混合后一同进入冷凝塔分离液氨,并洗除油水后送循环机加压进行下一个循环,不断产生液氨。
本流程中塔后放空设在氨分离器后,放空气体送提氢岗位回收氢。
氨分和冷交换器分离出来的液氨,放入液氨贮槽。
液氨贮槽的液氨分别再输送到尿素车间生产氨及有关岗位,或送氨冷器做冷冻剂使用,各个氨冷器蒸发后的气氨送至冷冻岗位重新液化成液氨后循环使用。
1.2 2#合成工艺流程
由压缩六段.七段送来合格的精练气经导入阀与氨冷器出口的循环气混合后进入超虑的上部,液氨被分离下来,分离后气体从顶部出来进入冷凝塔底部氨分离套筒内,分离气体中的液氨,油水后进入上部换热气器的管间,与管内冷排来的热气体换热后从上部出来进入循环机,气体经循环机加压后进入油分离器,分离掉油水后的气体分两路进入合成塔(一路线.一路冷副)主线从上部进入沿内外筒环隙顺流而下进入螺旋板换热器板间,从下部螺旋板换热器板间出来进入上部列管换热器的管间,换热后的气体与冷副管来的气体混合进入分器盒,气体被分配到三套管的内管,从外冷管进入集器盒,提温后的气体经中心进入触媒反应,反应后的气体经上部列管内出来进入废锅的管内,气体从废锅出来从二进进入下部螺旋板换热器的板内,经降温后的气体从二出出来进入水冷排下部,气体在冷排被水降温后由上部出来进入冷交上部,气体经换热后从塔顶部出来进入氨分的上部,气体中的氨进一部分离后从顶部出来进入氨冷器的上部,气体在氨冷器降温,气体从底部出来与导入来的气体混合进行下一步的循环.放空气去提氢岗位.
2工艺流程图
第二节工艺指标
催化剂热点温度:
445-500℃(根据催化剂活性情况调整,A±5℃)
成品氨的纯度:
≥99.6%
循环气中入口甲烷:
10-14%
循环气中入口氨含量:
≤3.5%
1#合成塔压差:
≤1.0MPa
2#合成塔压差:
≤2.0MPa
废锅炉水碱度:
≤10mgN/L
废锅炉水氯根:
≤30mgN/L
循环机出口压力:
≤32.0MPa
系统压力:
≤31.0MPa
系统压差:
≤2.5MPa
循环机油压:
0.3-0.6MPa
循环机填料加氨:
0.3-0.4MPa
1#合成废锅压力:
≤1.4MPa
2#合成废锅压力:
≤1.3MPa
中间槽压力:
≤2.1MPa
系统升压速率≤0.5MP/分
氨冷器气氨压力:
≤0.3MPa
合成塔塔壁上部温度:
≤100℃
合成塔塔壁中下部温度:
≤150℃
水冷温度:
≤50℃
氨冷温度:
-5-5℃
废热锅炉液位:
1/2~2/3
中间槽液位:
10-30吨
冷交液位:
0-50
循环机曲轴箱液位:
1/2-2/3
电炉绝缘电阻值:
≥0.2兆欧
催化剂同平面温差:
≤30℃
运行中电机绝缘:
>0.5兆欧
注油量:
20-30滴/分
保护气温度:
5-20℃
保护气流量:
500-800m3/h
轴承温度:
<75℃
定子温度:
<120℃
透平机电流:
<1150A
透平机功率:
<680KWh
循环气入口温度:
<40℃
循环氢:
>60%
轴承运行时间:
2880小时
功率记录仪指示无突跳.轴承定子运行温度记录平稳
透平机进出口压差:
≤3.0Mpa
第三章主要设备构造及设备一览表
第一节主要设备构造
11#氨合成塔
(1)构造合成塔由高压外筒和内件两部分组成:
主要有触媒筐、菱形分布器、层间换热器、下部换热器、电加热器组成。
(2)塔内流程
主线气体由一进合成塔后,沿内外筒环隙下行,从塔下部一出出来,经气气换热器换热,由塔下部二次入口入塔,经过下部换热器管间换热后,在集气盒内与从塔底部来的冷副气体混合,然后由中心管上行至上层触媒顶部后进入触媒层,一冷激气通过冷激管到达埋在上层触媒内的菱形分布器与上层触媒来的主线气体混合通过触媒层。
另一冷激气通过冷激管,从层间换热器底部进入换热器管间,换热后沿中心管外套筒上行至上层触媒顶部,与主线气体混合通过触媒层,然后进入层间换热器管内,气体出换热器后大部分径向流动通过下层触媒,少部分作轴向通过。
气体出下部触媒后进入下部换热器管内,换热后从二次出口出塔。
22#氨合成塔
(1)构造:
合成塔由高压外筒和内件两部分组成:
主要有触媒筐、下部换热器、电加热器组成.
(2)塔内流程
气体从一次入口进入,沿内外筒之间的环隙向下流动,进入下部换热器管间。
然后再进入上部换热器管间。
从上部换热器管间出来的气体进入分气盒,冷副来的气体不经换热直接进入分气盒,气体被分配到各个内冷管,再从外冷管出来进入集气盒,从集气盒出来的气体进入中心管,中心管出来的气体进入触媒层进行反应,反应后的气体从触媒层下部出来,进入上部换热器管内,然后从一次出口出来进入废锅,从废锅出来的气体由合成塔二次入口进入,进入下部换热器管内,然后从二次出口出来。
3冷交
(1)构造:
外壳、换热器、中心管、集气盒、NH3分离套筒、旋流板。
(2)冷交内流程
氨冷器来的气体,由底部进入塔内,沿升气管上升后从上部出口出来,经过旋流板分离掉部分液氨后继续向上进入氨分离套筒,从套筒内部通过套筒上的矩形孔依次向外流动,进行液氨分离,出套筒后向上进入换热器管间,与管内气体进行换热,最后从上部出口出冷交。
冷排来的热气体由上部入冷交,进入换热器管内,与管间冷气体换热后进入下部集气盒,然后由中心管从顶部出冷交。
(3)内件从上到下依次是列管式换热器、集气盒、带矩形孔的分离套筒、旋流板、三层套筒(其内有升气管)。
(4)作用:
A.用氨冷器出口的冷气体冷却将要进氨冷的热气体,以回收部分冷量,从而减轻氨冷的负荷,同时,又使进合成塔的气体温度升高。
B.分离出氨冷器气体中夹带的液氨。
4氨冷
氨冷器主要有外壳和列管组成,管内为高压气体,管外为液氨。
5透平机
透平机由外筒和内件组成,内筒包括两步分:
电动机和透平压缩机。
透平压缩机的主要部件是转子,由主轴、叶轮、气封套筒、平衡盘和连轴节等组成。
1-高压容器
2-电动机
3-中间接筒
4-联轴节
5-密封盘
6-出口隔板
7-“O”型环8-排气管9-主轴10-平衡盘
11-叶轮12-保护气管13-小车14-电极杆
6循环机
(1)循环机主要有电机、飞轮、主轴、曲轴、连杆、十字头、活塞、活塞杆、滑道、油泵、气缸等组成。
(2)工作原理:
由电机带动飞轮,通过主轴带动曲轴,曲轴带动连杆,连杆带动十字头、活塞杆,使活塞在气缸内不断运动,气体即被源源不断得输出。
第二节设备一览表
序号
设备名称
规格型号
1#
2#
1
合成塔外筒
¢1000×17585
¢1000×17711
2
合成塔内件
NC-1000,二轴一径内件触媒筐,容积,6.157m³,电炉功率700kw
三套管并流,内件¢1000,触媒筐容积
5m³,电炉功率700KW
3
废热锅炉
¢1800/¢1400F=100m2L=7559
¢1800/¢1400F=70m2L=5855
4
水冷却器
套管式F=400m²
淋洒式F=282m²
5
氨冷却器
¢1800×8940F=337m²
¢1500×8949F=226m²
6
气气换热器
¢800×11283,F=576m²
--
7
冷凝塔
¢800×11019,F=365m²
¢800×10314,F=254m²
8
氨分离器
¢800×4964
¢800×5137
9
油分离器
¢800×4964
¢800×5137
10
软水加热器
¢1200×7155F=120m²
--
11
气氨分离器
¢800×2880
¢800×2880
12
透平机
TC620—32—12
流量:
620m²/h
功率:
680KW二台
--
13
循环机
--
DZW—3.5/285—320
二台
2DZ—55—1.6/285—320
二台
第四章开停车操作
第一节正常开车操作要点
1开车前的准备
检查各设备、管道、阀门、分析取样点及电器、仪表等(应特别注意检查电炉、循环机、透平机的绝缘电阻值)必须正常完好;
检查系统所有阀门的开关位置,应符合开车要求;
与供水、供电部门及压缩、铜洗、冷冻岗位联系做好开车准备。
2开车
2.1系统未经检修处于保温保压状态下的开车:
微开导入阀,让系统缓慢补压至10.0Mpa,升压速率0.5Mpa/分,待系统压力略高于合成塔压力时,开启合成塔进出口主伐;
按正常开车步骤,开启循环机,调节循环机近路阀及系统近路阀,保持一定循环量,气体打循环;
开启电炉,加电升温,根据催化剂层温度上升情况,逐渐加大功率,并相应加大循环量;
升温期间要保持一定的升温速率,350℃前为30-40℃/h,350℃后为5-10℃/h;
当催化剂层温度大于200℃时开启水冷,300℃时开启氨冷,400℃开始放氨;
当触媒层温度升至反应温度时,应减慢升温速率,加大循环量,以缩小催化剂层轴向温差;
根据温度情况逐渐减小电炉功率,加大补充气量,直至切电,可转入正常生产;
升温时如遇循环机跳闸,应立即切断电炉电源以免将电炉丝烧坏。
2.2系统热洗和检修后的开车
系统吹净、气密试验和置换合格后,按正常开车步骤进行。
第二节正常停车操作要点
1短期停车
1.1系统保压,保温状况下的停车
关闭导入阀、各放空阀、取样阀,稍开导入放空阀;
关闭冷付阀开启系统近路阀,停下循环机;
关闭冷交、氨分放氨阀及氨冷加氨阀,废锅加水阀;
4)停车后将系统调整好,做好开车前的准备工作。
1.2系统需检修时的停车,按长期停车步骤进行。
2紧急停车
当发生重大设备事故等紧急情况时,需紧急停车,步骤如下:
立即与压缩工序联系,停止送气,迅速关闭导入阀,开启导入放空阀,按紧急停车步骤处理循环机,(如电加热器在用时须先停用);
迅速关闭合成塔进出口阀和冷副阀,如本岗位事故,应迅速关闭事故发生地点的前后阀门;
关闭冷交、氨分放氨阀及氨冷器加氨阀;
按短停方案处理。
3长期停车
停车前两小时逐渐关小氨冷器加氨阀,直至关闭,氨冷器内的液氨在停车前应蒸发完;
压缩机停止送气后,关闭导入阀,开启导入放空阀;
以40-50℃/h的速度降低催化剂层温度,当降至300℃时,按正常停车步骤停下循环机,打开系统近路阀,让其自然降温;
放净冷交和氨分内的液氨,关闭放氨阀;
关闭合成塔进出口阀、冷付阀及系统近路阀,关闭冷排冷却水阀(冬天注意防冻);
缓慢开启塔前后放空阀系统卸压,在塔进出口处加装盲板,(如合成塔不用检修,将冷排出口阀关闭,塔内保持一定压力),再用氮气系统置换;
关闭液氨贮槽进出口阀弛放气放空阀,并注意压力变化;
拆开法兰,用蒸汽将系统热洗(合成塔除外)置换,直至合格;
氨冷器及气氨管线,热洗和用空气置换,直至合格。
第三节原始开车操作要点
1开车前的准备
把安装结束后留下的一些阀门、管道以及与开车无关的杂物清出现场。
对照图纸检查和验收系统内所有设备、管道、阀门、分析取样点及电器仪表等,必须正常完好。
2单体试车
循环机单体试车的主要内容:
电机空转、无负荷试车和有负荷试车。
以检查电器和机械部分是否正确,油润滑系统是否正常以及设备的振动情况等;
合成塔内件空气试气密合格(0.8Mpa保持2小时压力不降为合格试验合格后卸压);
电加热器在塔外通电试验合格;
冷热交换器内件空气气密试验合格(方法同合成塔内件)。
3系统吹净
(1)吹净作业以空气进行,用压缩机送来的3.0Mpa左右的压力进行间断吹除;
(2)吹净按单体设备进行,即这一设备及其所连管道吹净后,再按流程连接上往后一设备进行吹净;
(3)利用导入阀控制压力(导入阀前管道已吹净),按照流程的特点和走向可采用顺吹、逆吹的方法进行,各计量仪表管道、取样管道、压力表管、液位计、放氨、加氨管道和岗位的外出管、外来管及死角等应同时进行吹净,低压系统均应在高压系统吹净完毕后,在空气试气密的同时进行。
A:
高压系统吹净
按流程依次拆开各设备和主要阀门的有关法兰并插入挡板;
拆除或关死排污阀、导淋阀、取样阀、压力表阀及液位计气液相阀;
人工清理合成塔外筒内壁,进出口装好盲板,一切准备就绪后,通知压缩机送空气并控制在3.0Mpa左右,冷交及热交管内外压差不大于0.8Mpa进行吹净;
顺流程吹除:
压缩六段或七段来空气→导入阀→冷交管间→循环机→油分→合成塔前→合成塔进气主伐、冷付阀、近路阀前法兰拆开处吹净;
逆流程吹除:
压缩六段或七段来空气→导入阀→氨冷器→氨分→冷交管内→冷排→热交管内→水加热器→废锅→合成塔二次出口法兰拆开处吹出。
B.低压系统吹净:
高压系统吹净后向系统补空气,补够一定压力后利用冷交放氨阀向低压系统串气,控制压力在0.3Mpa左右,把所有低压管道及附属设备进行吹净,直至合格;
C.吹除要求和注意事项:
吹除时吹除口必须留在阀前法兰处和设备前法兰处;
必须通过气体的阀门应全开,吹净时用木锤轻敲外壁,并调解流量,时大时小反复多次,直至气体吹净为合格。
吹净过程中每吹完一部分随即抽掉挡板,并装好有关阀门和法兰,严禁用手在法兰拆开处挡试吹出物;
各计量仪表根部应关死,放空、近路、排污、分析取样、仪表管线应同时吹净;
高压系统吹净时严禁高压气窜入低压系统。
催化剂的填装
制定催化剂装填方案(根据催化剂型号与粒度制定)
把所有装填时用的工具准备好;
把合成塔的的内外筒环隙,内外测温管和中心管用布堵死,以防催化剂掉进去;
装填时应选择晴朗天气进行,且