抽油机系统设计文档格式.docx
《抽油机系统设计文档格式.docx》由会员分享,可在线阅读,更多相关《抽油机系统设计文档格式.docx(19页珍藏版)》请在冰点文库上搜索。
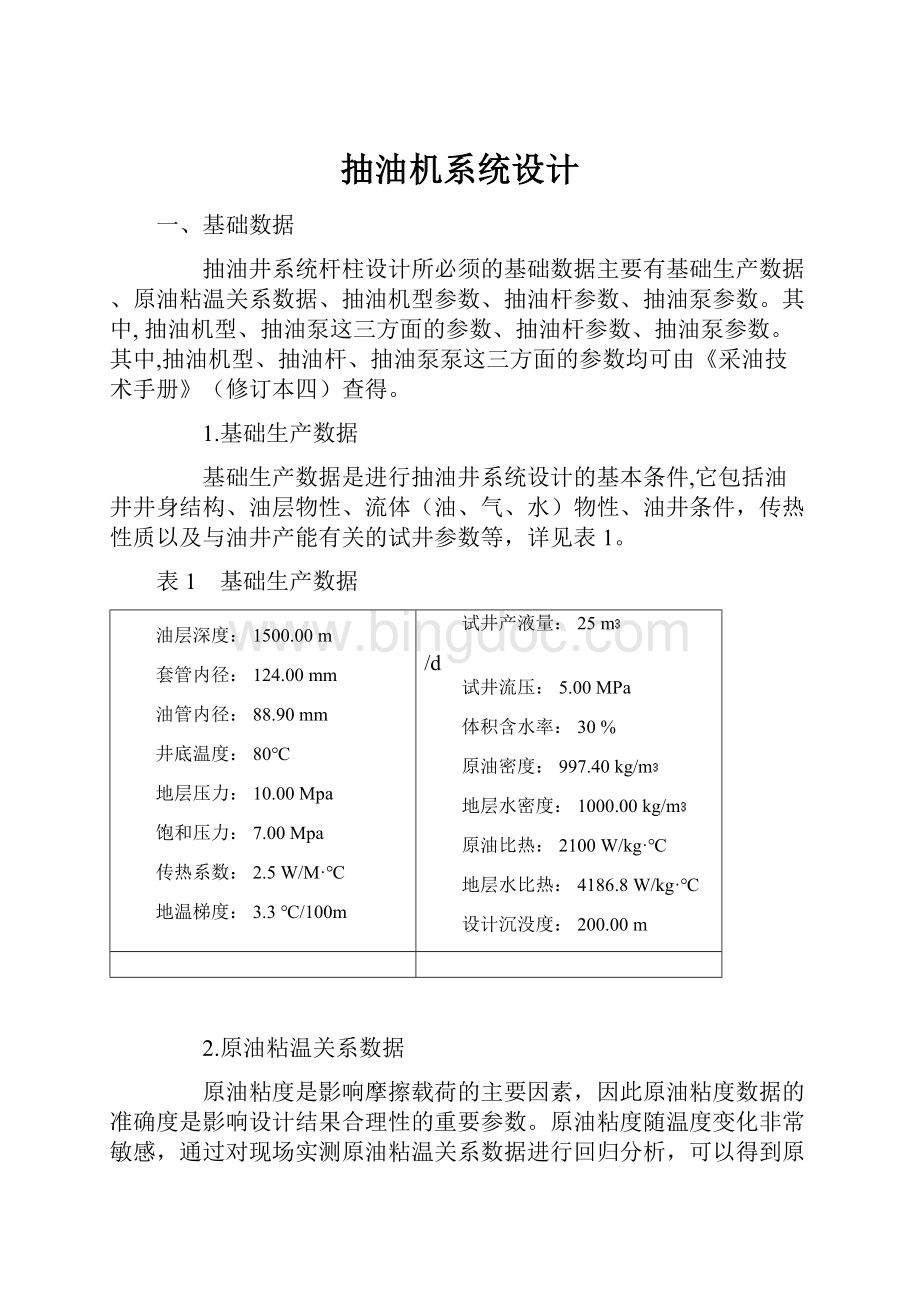
200.00m
2.原油粘温关系数据
原油粘度是影响摩擦载荷的主要因素,因此原油粘度数据的准确度是影响设计结果合理性的重要参数。
原油粘度随温度变化非常敏感,通过对现场实测原油粘温关系数据进行回归分析,可以得到原油粘度随温度变化的关系式。
这样,不仅可以提高抽油井系统设计结果的准确度,而且还易于实现设计的程序化。
现场可以提供的原油粘温关系数据,如表2所示。
表2 某区块原油粘温关系数据
温度,℃
40
45
50
55
60
65
70
75
粘度,mPa·
s
2680
1820
1240
900
600
420
310
230
3.抽油机参数
抽油机参数是指常规型游梁式抽油机的型号、结构参数、可以提供的冲程冲次大小。
目前已有93种不同型号的常规型抽油机,其型号意义如下:
不同型号抽油机的参数可见《采油技术手册》(修订本四)。
这里,以宝鸡产CYJ10-3-48型抽油机为例,其有关参数见表3。
表3抽油机参数
游梁前臂
(mm)
游梁后臂
连杆长度
曲柄半径/冲程
(mm/m)
冲次
(1/min)
3000
2000
3330
6.0,9.0,12.0
另外,由抽油机型号CYJ10-3-48,根据型号意义可直接得出:
许用载荷[Pmax]=100kN;
许用扭矩[Mmax]=48kN
4.抽油杆参数
抽油杆的材质为普通碳钢,其许用应力一般为90N/mm
,可提供的直径有:
16mm、19mm、22mm、25mm和29mm。
二、设计要求
根据以上的基础数据,在产液量为28.29m
/d时,对该井进行系统选择设计以下内容:
(1)确定出该井的井温分布;
(2)确定出原油粘温关系表达式;
(3)确定合理的下泵深度;
(4)选择合适的冲程和冲次;
(5)选择合适的抽油泵;
(6)确定出抽油杆直径及组合;
(7)计算出悬点的最大和最小载荷;
(8)计算并校核减速箱扭矩;
(9)计算电机功率并选电机;
(10)选择出合适的抽油机。
三、设计步骤
针对该井的已知条件,系统设计的步骤如下:
(1)根据油井条件,建立热传导能量方程,计算出井温沿井深的温度分布;
(2)通过对原油粘温关系数据进行回归分析,拟合出原油粘温关系表达式;
(3)根据试井参数,确定出该井的流入动态方程,并进一步确定出在设计排量条件下的井底流压;
(4)根据设计沉没度确定泵吸入口压力;
(5)根据井底流压和泵吸入口压力,确定下泵高度,并进一步确定下泵深度;
(6)初选抽油机,并根据油井条件,选择合适的冲程和冲次;
(7)根据冲程、冲次和设计排量,确定抽油泵的直径;
(8)自下而上,计算并确定抽油杆直径及组合;
(9)计算悬点最大和最小载荷,并对所选择的抽油机进行载荷校核;
(10)计算减速箱的最大扭矩,并进行扭矩校核;
(11)计算需要的电机功率,并进行电机功率校核;
(12)选择抽油机。
四、设计原理及计算
1.油井温度分布
原油越稠,原油粘度随井温变化就越敏感。
因此,井温分布对抽油井系统选择设计是十分重要的。
根据热传导,可建立井筒的能量方程为:
(1)
式中∶
——油管中L位置处原油的温度,℃;
K1——总传热系数,W/(m·
℃);
——内热源,W/m;
W——水当量,W/℃
——井底原油温度,℃;
m——地层温度梯度,℃/m。
对于常规采油来说,由于没有内热源,故可取
=0。
水当量W可如下计算:
W=MfCf+MgCg
式中∶Mf——井液质量流量,kg/s;
Cf——井液比热,W/(g·
Mg——气体质量流量,kg/s;
Cg——气体的比热,W/(g·
g——重力加速度,m/s
。
将已知数据代入方程
(1),可计算出任意深度所对应的油井温度,由此温度便可以计算出处于该深度处原油的粘度,从而可以进一步计算摩擦载荷、选择抽油设备。
另外,还可以根据计算结果做出井温沿井深的分布曲线,如图1所示。
2.原油粘温关系
将现场实测原油粘温数据通过回归分析,发现原油粘度随温度的变化服从指数规律,可用下式表达:
(2)
——原油的动力粘度,mPa·
s;
t——原油的温度,℃;
a——系数常数;
b——温度指数。
其中,a=9.7861,b=3.9483。
对于不同区块原油,a、b的取值不同。
3.井底流压
井底流压是确定下泵深度的重要参数,因此,进行抽油井系统设计时必须首先确定。
井底流压主要是利用油井产能并根据设计排量来确定。
油井流入动态具有多种类型,这里采用沃格尔方程:
(3)
式中∶q1——对应于井底流压pwf下的油井产量;
q1max——油井的极限产量;
pwf——井底流压;
pr——平地层压力。
将已知数据代入上式,在设计排量为q1=28.29m
/d的条件下,求得该井流压为:
pwf=4.50MPa。
4.泵吸入口压力
泵吸入口压力是确定下泵深度的重要参数,主要根据设计沉没度来估算。
沉没段油、水混合液的平均密度为:
(4)
代入已知数据,得
=998.18m
/d。
再根据沉没度hs=200m,可求得泵吸入口压力ps=1.958MPa。
5.下泵深度
下泵深度是抽油井系统设计的重要数据,它决定了抽油杆的总长度,并且影响着悬点载荷、冲程损失以及泵效。
下泵深度主要是根据井底流压与泵吸入口压力的差值,应用相应的方法来确定。
确定方法主要有三类:
1.将油、气、水看成是三相,应用相应的相关式来计算;
2.将油、水处理成液相,这样便应用气、液两相垂直管流理论来计算;
3.是对于象稠油井气体较少,从而可不考虑气体,只考虑单相液体进行估算。
这里采用单相估算法。
自油层中部到泵吸入口之间的压差为2.542Mpa,根据静液柱估算,该压差对应的高度Hp为208.63m。
因此,下泵深度则为:
6.确定冲程和冲次
冲程和冲次是确定抽油泵直径、计算悬点载荷的前提,选择原则为:
1.一般情况下应采用大冲程较小泵径的工作方式。
这样,即可以减小气体对泵效的影响,也可以降低液柱载荷,从而减小冲程损失。
2.如原油比较稠,一般选用大泵径、大冲程和低冲次的工作方式。
3.对于连抽带喷的井,则选用高冲次快速抽汲,以增强诱喷作用。
4.深井抽汲时,要充分注意振动载荷影响的S和n配合不利区。
5.所选择的冲程和冲次应属于抽油机提供的选择范围之内。
对于该井,由于油比较稠,因此将冲程确定为最大值S=3m,冲次确定为最小值n=61/min。
所选择的的冲程和冲次,应与下面的泵径相互配合,满足设计排量的要求。
7.确定泵径
根据设计排量,以及上一步确定的冲程、冲次,按照泵的实际排量公式来确定。
(5)
式中∶Q——泵的实际排量,m
/d;
Dp——泵径,m;
S——光杆冲程,m;
n——冲次,1/min;
——泵效,小数,取0.7。
抽油泵已是规格化的系列产品,计算得出抽油泵直径,应从规格参数表(见表4)中选出最为接近的值作为设计值。
表4抽油泵基本参数表(SY5059-91)
基本
泵型
泵的直径
m
联接油管外径
mm
(YB239-63)
柱塞冲程
长度范围
理论排量
联接抽油杆
螺纹直径
(Sy5029-83)
公称直径
基本直径
杆式泵
32
31.8
48.3,60.3
1.2~6
14~69
23.813
38
38.1
60.3,73.0
20~112
26.988
44
44.5
73.0
27~138
51
50.8
35~173
57
57.2
88.9
44~220
63
63.5
54~259
30.163
管
式
泵
整
体
筒
31.8
0.6~6
7~69
38.1
10~112
44.5
14~138
45.2
57.2
22~220
69.9
33~328
83
101.6
93~467
95
114.3
122~613
34.945
组
合
10~128
13~128
56
21~220
将已知数据代入式(4),并由表4查得最为接近的泵径为56mm。
8.悬点载荷计算及抽油杆强度校核方法
(1)悬点载荷计算
在下泵深度及沉没度不是很大,井口回压及冲次不是很高的油井内,在计算最大和最小载荷时,通常可以忽略振动、沉没压力、井口回压、液柱惯性产生的悬点载荷,此时,悬点最大和最小载荷可表示为:
(6)
(7)
式中∶Pmax、Pmin——悬点承受的最大和最小载荷;
——上冲程中抽油杆柱所受的重力与浮力之差产生的载荷;
——下冲程中液柱的重力与对抽油杆的浮力产生的载荷;
Iru、Ird——上、下冲程中抽油杆产生的最大惯性载荷;
Fu、Fd——上、下冲程中的最大摩擦载荷。
其中
式中∶L——抽油杆长度,m;
——抽油杆材料的密度,kg/m
;
——抽汲液的密度,kg/m
fr——抽油杆截面积,m
fp——抽油泵活塞截面积,m
fo——游动凡尔孔截面积,m
r——抽油机曲柄回旋半径,m;
l——抽油机连杆长度,m;
Frl——抽油杆与液柱之间的摩擦力,N;
——凡尔流量流数。
(8)
式中∶Frl——抽油杆柱与液柱之间的摩擦力,N;
——井内液体的动力粘度,Pas
m——油管内径与抽油杆直径之比,m=dt/dr;
dt——油管内径,m;
dr——抽油杆直径,m;
Vmax——抽油杆柱最大下行速度,m/s;
Vmax可按悬点最大运动速度来计算,当采用简谐运动模型时,其值为:
(2)抽油杆强度校核
抽油杆柱在工作时承受着交变负荷,因此,抽油杆受到非对称循环应力的作用。
其强度条件为:
(9)
——抽油杆的折算应力;
[
]——非对称循环疲劳极限应力,与抽油杆的材质有关。
其中
(10)
(11)
——循环应力的应力幅值。
9.确定抽油杆直径及组合
当下泵深度确定后,抽油杆的总长度便确定下来。
下面将进一步确定抽油杆的直径及组合。
抽油杆的直径及组合是抽油井系统选择设计的核心内容,确定的具体步骤如下:
(1)以抽油泵处为起点。
其高度为
(2)假定一个液柱载荷W10(初值);
(3)给定最下一级抽油杆直径(最小直径);
(4)设计算段长度H,则该计算段的起点高度和末点高度分别为:
如果H2>
Hp,则令H2=Hp,该段的长度应为:
(5)该计算段的平均高度为
=(H1+H0)/2,计算该点的温度和混合物的粘度。
(6)分别计算该计算段的最大载荷
与最小载荷
(7)分别计算累积最大和最小载荷:
(8)计算抽油杆的折算应力c,进行该段抽油杆强度校核;
(9)如不满足强度要求,则换次一级抽油杆直径,返回到步骤(3)重新计算;
(10)如满足强度要求,则以H1作为下一计算段的起点H0,进行下一段计算;
(11)当H0=Hp时则结束,否则返回到(3)继续计算,直到H0=Hp为止;
(12)校核液柱载荷。
如果计算值与假设值的误差达到精度要求,则计算结束;
如果未达到精度要求,则以计算值作为新的假设值,重新计算。
应用计算机程序对核例进行计算,所得到的抽油杆直径及组合如下:
项目
一级杆
二级杆
三级杆
四级杆
直径,mm
19.00
22.00
25.00
29.00
长度,m
395.00
483.50
246.60
66.37
10.计算与校核载荷
在进行抽油杆直径及组合确定计算结束时,便可得到悬点的最大载荷和最小载荷,它们分别为:
由于该抽油机的许用载荷为[Pmax]=100kN,因此满足载荷要求。
11.计算与校核扭矩
曲柄轴处的最大扭矩可采用如下任一公式计算:
式中∶Mmax——曲柄轴最大扭矩,kNm;
Pmax——悬点最大载荷,N;
Pmin——悬点最小载荷,N。
三个公式计算最大扭矩Mmax分别为:
42.93、41.43、40.09kNm。
由于该抽油机的许用扭矩为[Mmax]=48kNm,因此满足扭矩要求。
12.计算需要的电机功率
电机实际输出的最大功率可如下计算:
式中∶Nmax——电机实际输出的最大功率,kW;
Mmax——曲柄轴最大扭矩,kNm;
——传动效率,取0.9。
将Mmax=40.09kNm,n=61/min代入上式,可得需要的最大电机功率为Nmax=27.99kW。
五、设计结果
按照设计要求,最终设计结果如下:
1.井温分布
该井的井温度分布如图2所示。
原油粘温关系附合:
经确定,a=9.7858,b=3.9481。
原油粘温关系曲线如图3所示。
3.下泵深度
经确定,Lp=1291.37m。
4.冲程和冲次
经确定,S=3m,n=61/min。
5.选择抽油泵
选择泵径为56mm的抽油泵。
6.抽油杆直径及组合
确定的抽油杆直径及组合如下表
项 目
一级杆
二级杆
三级杆
四级杆
22.00
25.00
29.00
长度,m
483.50
346.60
66.37
7.悬点最大和最小载荷;
计算的悬点最大载荷和最小载荷分别为:
8.计算并校核减速箱扭矩
经计算:
Mmax=40.09kNm
9.计算电机功率并选择电机
电机最大功率为Nmax=40.09kW
10.选择出合适的抽油机
选择宝鸡CYJ10-3-48型抽油机较为合适。