密炼机液压系统设计说明.docx
《密炼机液压系统设计说明.docx》由会员分享,可在线阅读,更多相关《密炼机液压系统设计说明.docx(59页珍藏版)》请在冰点文库上搜索。
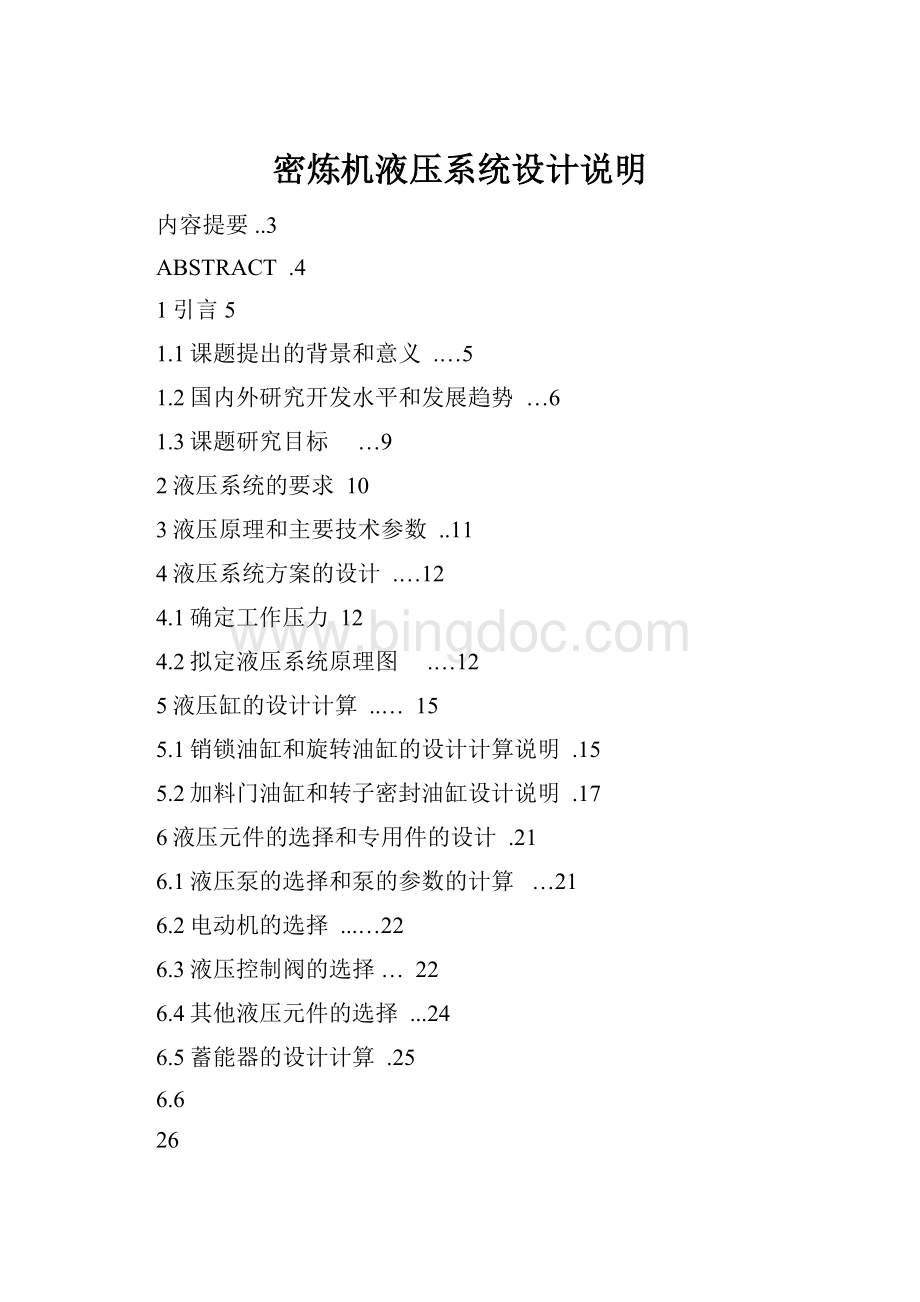
密炼机液压系统设计说明
内容提要..3
ABSTRACT.4
1引言5
1.1课题提出的背景和意义.…5
1.2国内外研究开发水平和发展趋势…6
1.3课题研究目标…9
2液压系统的要求10
3液压原理和主要技术参数..11
4液压系统方案的设计.…12
4.1确定工作压力12
4.2拟定液压系统原理图.…12
5液压缸的设计计算..…15
5.1销锁油缸和旋转油缸的设计计算说明.15
5.2加料门油缸和转子密封油缸设计说明.17
6液压元件的选择和专用件的设计.21
6.1液压泵的选择和泵的参数的计算…21
6.2电动机的选择...…22
6.3液压控制阀的选择…22
6.4其他液压元件的选择...24
6.5蓄能器的设计计算.25
6.6
26
确定油箱的有效容积
6.7管道尺寸的确定.….26
7液压系统性能验算.28
7.1验算回路中的压力损失……….28
7.2液压系统的发热温升的计算……..29
8设计液压装置.34
8.1液压装置总体布局34
8.2液压阀的配置形式..34
8.3集成块的设计...34
8.4绘制正式工作图...35
9密炼机液压系统使用、维护说明书.36
9.1液压系统组成和控制方式..36
9.2液压系统安装及调试39
9.3液压系统的维护及注意事项40
9.4日常维护要求41
9.5常见液压故障处理办法42
9.6主要元件44
9.7易损件46
结论47
致谢48
参考文献49
附录:
1英文原著
2英文翻译3设计图纸
内容提要
本文主要讲述了密炼机液压系统的设计,其中包括系统参数的设计、油缸的计算、
系统的性能验算以及系统的使用说明。
该系统主要用于密炼机的液力装置,控制各工作点油缸动作,由于该系统配置有电接点温度计(WSS)压力继电器(HED10A2)电磁阀、溢流阀、安全阀等,因此可对系统的油液温度、系统压力等实现远程监控,其结构设计紧凑、操作方便、性能可靠、节约能源是密炼机液力装置的理想配套液压设备。
其主要特点是:
当主机超载时,本系统可自动进入浮动状态;该系统采用多种措施来实现加料门开、关动作的缓冲,以减少对液压系统和机械设备的冲击。
ABSTRACT
ThisdocumenttalksaboutthehydraulicsystemdesignoftheCloseRubberExtrusionMachine,itincludethesystemparameterdesign、thecalculationofthecylinder、thecheckofthesystempropertyandtheusingapplicationofthesystem.Thissystemismainlyusedforcontrolthecylindermotionatanyworkingpointinthehydraulicequipmentofthecloserubberextrusionmachine,foritequippedwiththeelectricconnectthermometer(WSSX)、pressurerelay(HED10A20)、solenoidvalve、reliefvalve、safetyvalveandsoon,itcanfarawaycontroltheoiltemperaturesystempressure,anditalsohasthepriorityofgoodstructureconvenientoperationreliableproperty、lessenergyconsumingandsoon.Themaincharacteristicsis:
itcanautomaticgointothefloatingstatewhenitoverloading;thesystememploysmanymeasuresinordertobufferfeeddoor'impact.
1引言
1.1课题提出的背景和意义
我国液压工业发展历程,大致可分为三个阶段,即:
20世纪50年代初到60年代初为
起步阶段;60~70年代为专业化生产体系成长阶段;80~90年代为快速发展阶段。
其中,液压工业于50年代初从机床行业生产仿苏的磨床、拉床、仿形车床等液压传动起步,液压元件由机床厂的液压车间生产,自产自用。
进入60年代后,液压技术的应用
从机床逐渐推广到农业机械和工程机械等领域,原来附属于主机厂的液压车间有的独立出来,成为液压件专业生产厂。
到了60年代末、70年代初,随着生产机械化的发展,特别是在为第二汽车制造厂等提供高效、自动化设备的带动下,液压元件制造业出现了迅速发展的局面,一批中小企业也成为液压件专业制造厂。
1968年中国液压元件年产
量已接近20万件;1973年在机床、农机、工程机械等行业,生产液压件的专业厂已发展到100余家,年产量超过100万件,一个独立的液压件制造业已初步形成。
这时,液压件产品已从仿苏产品发展为引进技术与自行设计相结合的产品,压力向中、高压发展,并开发了电液伺服阀及系统,液压应用领域进一步扩大。
进入80年代,在国家改革开放的方针指引下,随着机械工业的发展,基础件滞后
于主机的矛盾日益突出,并引起各有关部门的重视。
为此,原一机部于1982年组建了
通用基础件工业局,将原有分散在机床、农业机械、工程机械等行业归口的液压专业厂,统一划归通用基础件局管理,从而使该行业在规划、投资、引进技术和科研开发等方面得到基础件局的指导和支持。
从此进入了快速发展期,先后引进了60余项国外先进技
术,其中液压40余项,经消化吸收和技术改造,现均已批量生产,并成为行业的主导产品。
近年来,行业加大了技术改造力度,1991~1998年国家、地方和企业自筹资金总投入共约20多亿元,其中液压16亿多元。
经过技术改造和技术攻关,一批主要企业技术水平进一步提高,工艺装备得到很大改善,为形成高起点、专业化、批量生产打下了良好基础。
近几年,在国家多种所有制共同发展的方针指引下,不同所有制的中小企业迅猛崛起,呈现出勃勃生机。
随着国家进一步开放,三资企业迅速发展,对提高行业水平和扩大出口起着重要作用。
目前我国已和美国、日本、德国等国著名厂商合资或
由外国厂商独资建立了柱塞泵/马达、行星减速机、转向器、液压控制阀、液压系统、静液压传动装置、液压件铸造、机械密圭寸、橡塑密圭寸等类产品生产企业50多家,引进外
资2亿多美元。
1.2国内外研究开发水平和发展趋势
1.2.1国内外开发水平
(1)基本概况
经过40多年的努力,我国液压行业已形成了一个门类比较齐全,有一定生产能力
和技术水平的工业体系。
据1995年全国第三次工业普查统计,我国液压工业乡及乡以
上年销售收入在100万元以上的国营、村办、私营、合作经营、个体、三资”等企业约有700余家,其中液压700家。
按1996年国际同行业统计,我国液压行业总产值23.48亿元,占世界第6位
(2)当前供需概况
通过技术引进,自主开发和技术改造,高压柱塞泵、齿轮泵、叶片泵、通用液压阀门、油缸和各类密封件第一大批产品的技术水平有了明显的提高,并可稳定的批量生产,为各类主机提高产品水平提供了保证。
另外,在液压元件和系统的CAD、污染控制、比
例伺服技术等方面也取得一定成果,并已用于生产。
目前,液压产品总计约有1200个
品种、10000多个规格。
已基本能适应各类主机产品的一般需要,为重大成套装备的品种配套率也可达60%以上,并开始有少量出口。
1998年国产液压件产量480万件,销售额约28亿元;密封件产量约8亿件,销售额约10亿元。
据中国液压气动密封件工业协会1998年年报统计,液压产品产销率为97.5%,密封为98.7%。
这充分反映了产销基本衔接。
我国液压业虽取得了很大的进步,但与主机发展需求,以及和世界先进水平相比,还存在不少差距,主要反映在产品品种、性能和可靠性等方面。
以液压产品为例,产品品种只有国外的1/3,寿命为国外的1/2。
为了满足重点主机、进口主机以及重大技术装备的需要,每年都有大量的液压、气动和密封产品进口。
据海关统计及有关资料分析,1998年液压、气动和密封件产品的进口额约2亿美元,其中液压约1.4亿美元,气动近0.3亿美元,密封约0.3亿美元,比1997年稍有下降。
按金额计,目前进口产品的国内市场占有率约为30%。
1998年国内市场液压件需求总量约600万件,销售总额近40亿元;气动件需求总量约500万件,销售总额7亿多元;密封件需求总量约11亿件,销售总额约13亿元。
由于液压传动具有体积小、操作灵活、输出功率大等优点;也可用简单的管路连接代替复杂的机械传动,因而在收割机和插秧机中得到了广泛关注和大量应用。
随着农业机械化的推广与普及,农机研究部门、主机生产厂家和农户对液压系统的认识程度也在不断的提高,他们不仅要求产品有低廉的价格,更要求有较高的品质、可靠的使用性能;作为农业机械推广重点之一的联合收割机、插秧机,其液压系统的配置通过液压件生产厂家近几年的探索与努力,在功能、可靠性、合理性等方面已取得了较大的突破。
集成、复合、大通径、多功能。
已成为新一代农机液压件的开发热点。
结构上的集成化便于安装布置;性能上的复合为用户提供了很大方便;通道的大而畅更有利于减少发热与能耗;产品的多功能与农业机械的发展与开创紧密相连。
作为液压件,曾经困扰着农业机械的应用与发展,劣质液压元件、配置不合理的液压系统曾一度充斥着农机市场。
由此这也成为了液压件生产厂家的一个攻关课题。
通过多年的探索与研究,农机液压件的整体配套水平已取得了一个飞跃,并逐步接近了发达国家水平。
比如说,带有复合功能的手控、电控的操纵系统替代了功能单一的分配阀,而且性能、功效在不断升级;此外,行走系统采用了静液压无级变速器(HST),大大提高了操纵性能与工作效率。
因此,我们必须按照客观规律去办事,不能守旧,一定要有创新,要有突破,相信,液压技术在农机上的应用将更普及一定会达到发达国家水平。
液压系统结构紧凑、重量轻、体积小、压力高、自吸性能好。
在液压系统的设计中,不但要实现其拖动与调节功能,还要尽可能地利用能量,达到
高效、可靠运行的目的。
液压系统的功率损失会使系统的总效率下降、油温升高、油液变质,导致液压设备发生故障。
因此,设计液压系统时必须多途径地考虑降低系统的功率损失。
目前普遍使用着的定量泵节流调速系统,其效率较低(<0.385),这是因为定量泵与油缸的效率分别为85%与95%左右,方向阀及管路等损失约为5%左右。
所以,即使不进行流量控制,也有25%的功率损失。
加上节流调速,至少有一半以上的浪费。
此外,还有泄漏及其它的压力损失和容积损失,这些损失均会转化为热能导致液压油
温升。
所以,定量泵加节流调速系统只能用于小流量系统。
为了提高效率减少温升,应采用高效节能回路,上表为几种回路功率损失比较。
另外,液压系统的效率还取决于负载。
同一种回路,当负载流量QL与泵的最大流量Qm比值大时回路的效率高。
例如可采用手动伺服变量、压力控制变量、压力补偿变量、流量补偿变量、速度传感功率
限制变量、力矩限制器功率限制变量等多种形式,力求达到负载流量QL与泵的流量
的匹配。
1.2.2今后发展走势
(1)影响发展的主要因素
1企业产品开发能力不强,技术开发的水平和速度不能完全满足先进主机产品、重大技术装备和进口设备的配套和维修需要。
2不少企业的制造工艺、装备水平和管理水平都较落后,加上质量意识不强,导致产品性能水平低、质量不稳定、可靠性差,服务不及时,缺乏使用户满意和信赖的名牌产品。
3行业内生产专业化程度低,力量分散,低水平重复严重,地区和企业之间产品趋同,盲目竞争,相互压价,使企业效益下降,资金缺乏、周转困难,产品开发和技术改造投入不足,严重地制约了行业整体水平的提高以及竞争实力的增强。
4国内市场国际化程度日益提高,国外公司纷纷进入中国市场参与竞争,加上国内私营、合作经营、个体、三资等企业的崛起,给国有企业造成愈来愈大的冲击。
(2)发展走势
随着社会主义市场经济的不断深化,液压产品的市场供求关系发生较大变化,长期来以短缺”为特征的卖方市场已基本成为以结构性过剩”为特征的买方市场所取代。
从总体能力看,已处于供大于求的态势,特别是一般低档次液压件,普遍供过于求;而主机急需的技术含量高的高参数、高附加值的高档产品,又不能满足市场需要,只能依赖于进口。
在我国加入WTO后,其冲击有可能更大。
因此,十五”期间行业产值的增长,决不能依赖于量的增长,而应针对行业自身的结构性矛盾,加大力度,调整产业结构和产品结构,也就是应依靠质的提高,促进产品技术升级,以适应和拉动市场需求,求得更大的发展。
在工业生产的各个部门都应用液压传动技术。
例如,工程机械、矿山机械、压力机械和航空工业中采用液压传动,机床上的传动系统也采用液压传动。
液压传动所采用的工作介质为液压油或其它合成液体,气压传动所采用的工作介质为压缩空气。
1.3课题研究目标
液压元件将向高性能、高质量、高可靠性、系统成套方向发展;向低能耗、低噪声、低振动、无泄漏以及污染控制、应用水基介质等适应环保要求方向发展;开发高集成化高功率密度、智能化、机电一体化以及轻小型微型液压元件;积极采用新工艺、新材料和电子、传感等高新技术。
液压技术正向咼压、咼速、大功率、咼效、低噪声、咼性能、咼度集成化、模块化、智能化的方向发展。
同时,新型液压元件和液压系统的计算机辅助设计、计算机辅助测试、计算机直接控制、计算机实时控制技术、机电一体化技术、计算机仿真和优化设计技术、可靠性技术,以及污染控制技术等方面也是当前液压传动及控制技术发展和研究的方向;气压传动技术在科技飞速发展的当今世界发展将更加迅速。
随着工业的发展,气动技术的应用领域已从汽车、采矿、钢铁、机械工业等行业迅速扩展到化工、轻工、食品、军事工业等各行各业。
气动技术已发展成包含传动、控制与检测在内的自动化技术。
由于工业自动化技术的发展,气动控制技术以提高系统可靠性,降低总成本为目标。
研究和开发系统控制技术和机、电、液、气综合技术。
显然,气动元件当前发展的特点和研究方向主要是节能化、小型化、轻量化、位置控制的高精度化,以及与电子学相结合的综合控制技术。
液压与气压传动是研究利用有压流体(压力油或压缩空气)作为传动介质来实现各种机械的传动和自动控制的学科。
液压传动与气压传动实现传动和控制的方法基本相同,它们都是利用各种元件组成需要的控制回路,再由若干回路组成能够完成一定控制功能的传动系统来完成能量的传递、转换与控制。
2液压系统的要求
本液压系统应用于橡胶厂炼提炼橡胶,具体要求如下:
(1)加料门油缸运动要平稳,不能很大有的冲击载荷
(2)当主机超载时,本系统可自动进入浮动状态;
(3)本液压系统采用多种措施来实现加料门开、关动作的缓冲,以减少对液压系统和机械设备的冲击。
(4)本液压系统控制各工作点油缸的动作。
(5)对系统的油液温度、系统压力等实现远程监控,系统结构设计紧凑、操作方便、
性能可靠。
(6)为保证安全生产,系统设有安全联锁装置,停电安全联锁装置。
3液压原理和主要技术参数
本液压系统配置有电接点温度计(WSSX)、压力继电器(HED10A20)、电磁阀、溢流阀、安全阀等,可对系统的油液温度、系统压力等实现远程监控,系统结构设计紧凑、操作方便、性能可靠、节约能源是密炼机液力装置的理想配套液压设备。
(1)双联叶片油泵:
型号一PV2R13-10/52-FRAAB,排量一10/52ml/rev额定压力一
31.5Mpa,系统设定压力小流泵一10Mpa,大流量油泵为一8Mpa。
(2)电机:
型号一Y180M-4-B35(50HZ、AC380V),供应商一南阳电机,
功率一18.5KW,转速一1470r/Min,防护等级一IP54。
(3)电磁铁电压:
DC24Vo
(4)工作介质:
抗磨液压油L-HM46,(建议用美孚油ISOVG46)
工作介质污染度等级:
NAS8级
(5)油箱容积:
500L
(6)液压系统压力范围:
5-10M
4液压系统的方案的设计
4.1确定工作压力
压力的选择要根据载荷大小和设备和类型而定。
还要考虑执行元件的装配空间和经济条件及元件供应情况等的限制。
在载荷一定的情况,工作压力低,势必要加大执行元件的结构尺寸,对某些设备来说,尺寸要受到限制,从材料消耗角度看也不经济;反之压力选得太高,对泵、缸、阀等元件的材质、密封、制造精度也要求很高,必然要提高设备成本。
一般来说,对于固定的尺寸不太受限的设备,压力可以选低一些,行走机械重载设备压
力要选得高一些。
具体选择参考表4.1
表4.1按载荷选择工作压力
载荷/KN
v5
5〜10
10〜20
20〜30
30〜
750
>50
工作压力
/MPa
v0.8〜1
1.5〜2
2.5〜3
3〜4
4
5
>5
所以本系统的工作压力5~10MPa,
4.2拟定液压系统原理图
该液压系统包括旋转油缸、转子密封油缸、加料门油缸、销锁油缸、液压系统压力
保护、油箱部分电气控制等几个部分。
其完整液压系统图4.2
图4.2液压原理图动力部分:
图4.3液压系统图的执行部分
其动作循环状况见下表4.4
表4.4加料机构电磁铁动作
工磁一铁
YV3
YV2
备注
启始位置
-
-
加料门打开
+
-
加料门关闭
-
+
不失电
表4.5锁紧、卸料机构电磁铁动作
电磁铁
工步
YV8
YV9
YV6
YV7
YV4
YV5
备注
启始位置
-
-
-
-
-
+
-
卸料门快速关闭
+
-
+
-
-
-
-
卸料门慢速关闭
+
-
-
-
-
-
-
锁紧机构锁紧
+
-
-
-
+
-
-
机构锁紧后,炼胶
-
-
-
-
-
-
-
锁紧机构松开
-
+
-
+
-
+
-
卸料门快速打开
-
+
-
+
-
-
-
卸料门慢速打开
-
+
-
-
--
-
-
停电锁紧机构松开
-
-
-
-
-
<>
-
停电卸料门打开
-
-
-
<>
-
-
-
5液压缸的计算
5.1销锁油缸和旋转油缸的设计计算说明
5.1.1液压油缸的缸径、杆径和工作压力确定
根据技术条件:
确定液压缸径和杆径及行程为:
缸径D=①160mm,杆径d=①63mm
由此计算出液压系统工作压力为:
P=1(D2d2)
4
(5.1)
=(4X169X103)/(nX(1602-632))
=10MPa
式中F为锁紧力,F=169KN
5.1.2缸筒壁厚计算
根据机械设计手册,在此液压系统中,3.2公式,此时:
(5.2)
s=(2rJpyD3pyr+C
9:
强度系数,对无缝钢管,®=1
C:
用来圆整壁厚数
Py:
液压缸内最高工作压力。
Py=10MPa
D:
缸筒内径
[(T]=[(Ts]/2.5=150/2.5=60MPa
S=10X160/(2.3x60-3x10)+C=17mm
故油缸缸筒外圆取D1=194mm.
5.1.3缸筒强度校核
根据SL41-93,缸体合成应力按下式计算:
800mm故油缸的活
(取截面直径较少值)
(5.6)
(5.7)
(5.8)
P:
工作压力,P=i0MPa
D:
油缸缸径,D=①i60mm
d:
油缸杆径,d二①63mm
8:
缸筒壁厚,S=17mm
终计算,0zhi二z12n12z1h1=53.2MPa<60MPa
即:
0zhi<[0],符合要求•
5.1.4活塞杆长度和缸筒长度计算
根据设计要求的行程,来设计活塞杆的长度;本油缸的行程为塞杆的长度为920mm缸筒的长度为1027mm
5.1.5活塞杆强度计算
活塞杆受拉力最危险截面是两端连接螺纹的退刀槽横截面,
其应力计算如下:
0n=232<[0]
式中0为拉应力:
0=坐号
.di
t为剪应力:
t二“"Ff0
0.2d1
上面两公式中,K:
螺纹拧紧系数,此处取K=1.25
K1:
螺纹内摩擦系数,一般取K仁0.12
di:
活塞杆危险截面处直径,d1=60mm
d0:
螺纹外径,d0=61mm
[(T]:
60MPa
则:
(T==35.3MPa
t==15.3MPa
得:
(Tn=50.3MPa
所以:
(T*[(T],符合工况要求。
5.1.6下盖联接螺钉强度校核计算
螺钉联接采用高强度螺钉M20X80(GB/T70.1-2000)联接,两端数量均为24件,螺钉精度等级为10.9级,其强度校核,按照公式(5.7)、(5.8)。
4kF
拉应力:
(T二上斗■=184.8MPa
.z.d1
剪应力:
t==83.92MPa
0.2.z©
K:
螺纹拧紧系数,此处取K=1.25
K1:
螺纹摩擦系数,一般取K1=0.12
d1:
螺纹内径,d1=16.752mmd0:
螺纹外径,d0=20mm
Z:
24
(Ts螺钉材料屈服强度,(Ts>900Mpa(10.9级)
[(T]=[(Ts]/2=450Mpa
得:
(Tn=“232〜235.12MPa<[]符合工况要求
5.1.7活塞杆柔度校核计算
活塞杆细比计算如下:
入=生<[入](5.9)
d
此处:
L为折算长度,导向套中心至吊头尺寸,约920mm
活塞杆直径d=63mm,
[入]活塞杆许用细长比,按规定拉力杆此处[入]<100。
计算得入=4X920/63=59v[入],
故满足要求
5.2加料门油缸和转子密封油缸设计说明
5.2.1液压油缸的缸径、杆径和工作压力确定
根据设计要求确定液压缸径和杆径及行程为:
缸径D=①63mm,杆径d二①35mm
由此计算出液压系统工作压力为:
P=F=(4X21.5X103)/(nX(632-352))=10MPa
4(D2d2)
4
式中F为加料力,F=21.5KN
5.2.2缸筒壁厚计算
根据机械设计手册,在此液压系统中,D/16,故液压缸缸筒壁厚应按薄壁筒计算公式,此时:
2[]
PyD
(5.10)
Py—试验压力
工作压力小于16MPa时,Py=1.5P
D—液压缸内径
[]--液压缸缸体材料许用应力
(5.11)
[]=b/n
b--液压缸缸