基于S7200PLC的液氨汽化器.docx
《基于S7200PLC的液氨汽化器.docx》由会员分享,可在线阅读,更多相关《基于S7200PLC的液氨汽化器.docx(34页珍藏版)》请在冰点文库上搜索。
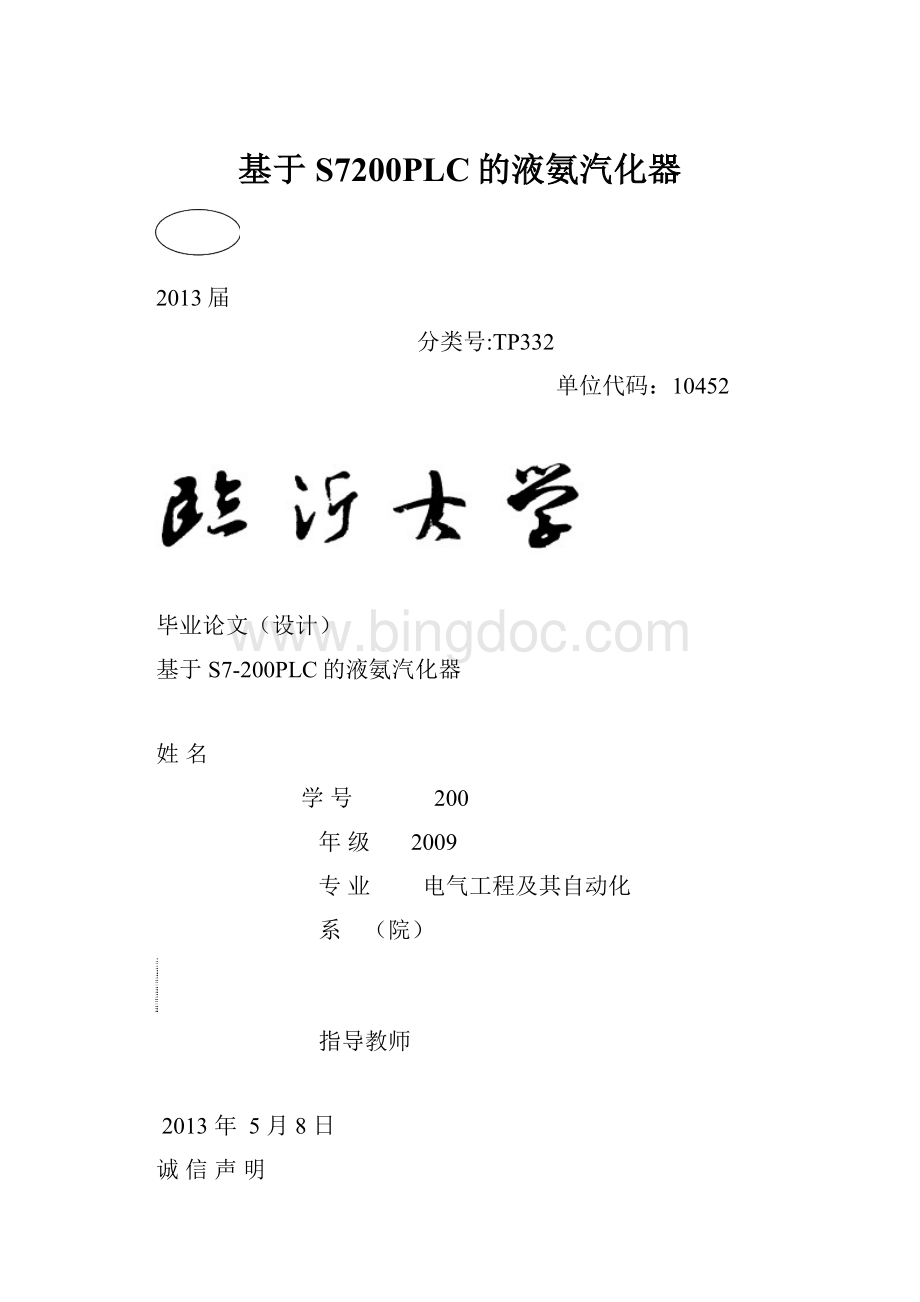
基于S7200PLC的液氨汽化器
2013届
分类号:
TP332
单位代码:
10452
毕业论文(设计)
基于S7-200PLC的液氨汽化器
姓名
学号 200
年级 2009
专业 电气工程及其自动化
系 (院)
指导教师
2013年5月8日
诚信声明
本人呈交给临沂大学的这篇毕业论文,除了所注参考文献和世所公认的文献外,全部是本人在指导老师指导下的设计成果。
学生签名:
日期:
经检查该毕业设计(论文)为独立完成,不存在抄袭现象。
指导老师签名:
日期:
摘要
从上世纪80年代至90年代中期,PLC得到了快速的发展,在这时期,PLC在处理模拟量能力、数字运算能力、人机接口能力和网络能力得到大幅度提高,PLC逐渐进入过程控制领,在某些应用上取代了在过程控制领域处于统治地位的DCS系统。
PLC具有通用性强、使用方便、适应面广、可靠性高、抗干扰能力强、编程简单等特点。
PLC在工业自动化控制特别是顺序控制中的地位,在可预见的将来,是无法取代的。
本文介绍了以调节阀为被控对象,采用压力变送器、PT100,实现对压力、温度检测、传送,以S7-200PLC为控制器,构成汽化器控制系统;采用PID算法,运用PLC梯形图编程语言进行编程,实现汽化器的自动控制。
本文根据汽化器的控制系统工作原理,就变送器的选型、PLC配置、电气原理图等几方面进行阐述。
通过改造的控制系统具有响应快、稳定性好、可靠性高等特点,对工业控制有现实意义。
关键词:
温度;压力;PLC;PID
Abstract
Fromthe80'softhelastcenturytothemid90's,PLCobtainedthefastdevelopment,inthisperiod,PLCcapabilityindealingwithanalog,digitaloperationability,abilityofman-machineinterfaceandnetworkcapacityhasbeengreatlyimproved,PLCgraduallyintotheprocesscontrolfield,theDCSsystemisinadominantpositionintheprocesscontrolfieldreplacedinsomeapplication.PLChasstrongcommonality,convenientuse,wideadaptability,highreliability,stronganti-interferenceability,simpleprogrammingandsoon.PLCinindustrialautomationandcontrol,especiallythesequencecontroltheposition,intheforeseeablefuture,isnosubstitutefor.
Thispaperintroducesthecontrolvalveforthecontrolledobject,thepressuretransmitter,PT100,torealizethepressure,temperaturedetection,transmission,usingS7-200PLCasthecontroller,constitutesacarburetorcontrolsystem;usingPIDalgorithm,usingPLCprogramminglanguageprogramming,toachieveautomaticcontrolcarburetor.
Accordingtotheworkingprincipleofcontrolsystemofthecarburetor,discussedseveralaspectsoftheselectionoftransmitter,PLCconfiguration,electricalprinciplediagram.Throughthetransformationofthecontrolsystemhasfastresponse,goodstability,highreliability,practicalsignificanceforindustrialcontrol.
Keywords:
Temperature;pressure;PLC;PID
第1章绪论2
1.1课题背景2
1.2现在汽化器现状2
1.3设计主要内容2
第2章硬件的设计4
2.1硬件配置4
2.1.1西门子S7-200CUP2264
2.1.2模拟量输入/输出模块(EM231/EM232)4
2.1.3传感器的选择5
2.1.4调节阀的选择5
2.2电气原理图6
2.2.1氨气出口温度控制6
2.2.2氨液压力控制6
2.3I/O分配表7
2.4硬件接线图8
第3章软件的设计9
3.1编程软件STEP7--Micro/WIN概述9
3.2西门子S7-200内的PID控制9
3.3S7-200程序设计11
3.3.1流程图11
3.3.2内存地址分配13
3.3.3PID指令回路表13
3.3.4S7-200程序设计梯形图14
3.4系统程序调试20
总结24
参考文献25
致谢26
附录27
第1章绪论
1.1课题背景
在半个世纪内我国将以煤炭作为能源结构的主体。
最有效的利用煤炭的热能的方式是将煤炭用于燃煤电厂,但煤炭在燃烧过程中会产生大量的烟尘、硫氧化合物(SOX)、氮氧化合物(NOX)等。
最初人们只意识到烟尘和硫氧化合物(SOX)对大气污染的严重性,近年来随着环保意识的提高,氮氧化合物(NOX)对环境造成污染的严重性越来越引起人们的重视。
目前我国已经在《火电厂大气污染物排放标准》(GB13223-2003)中对NOX排放做了明确规定,并要求国内新建及已建燃煤电厂将脱硝系统列入规划。
目前,脱硝技术日趋成熟,在多种脱硝技术中,选择性催化还原(SCR)脱硝技术是世界公认的最有成效、最成熟的脱硝技术,也是应用最广的脱硝技术,我国也主要采用此种技术。
SCR技术主要是利用还原剂与NOX反应生成N2和H2O。
目前最常采用的还原剂是NH3,因此液氨气化器成为SCR技术中主要设备之一。
1.2现在汽化器现状
液氨气化器按照加热源分有:
电加热式、蒸汽加热式、温水加热式;按照结构分有两种:
常压容器式和压力容器式。
通常情况下相同结构不同加热源的气化器控制方式相近,而相同加热源不同结构的气化器控制方式有所不同。
目前国内燃煤电厂蒸汽供应最为常见,以蒸汽作为加热源的常压容器式气化器通常有两种形式,分别为蒸汽水浴式和蒸汽加热器式。
蒸汽水浴式气化器是指蒸汽直接喷入气化器筒体内的水浴中,加热后的水与盘管内的液氨换热,这种气化器称为的蒸汽水浴式;蒸汽加热器式气化器是指蒸汽直接加热管中的液氨,这种气化器称为蒸汽加热器式。
1.3设计主要内容
设计包括硬件设计和软件设计,其中硬件是基础,软件是核心,软件的数据通过硬件进行处理和控制,最终实现用户的功能。
一、设计任务
要求能保证一定的气化能力,并安全、稳定的提供脱硝系统所需的氨气
随着氨气的使用量的变化,氨气温度、压力也会随之发生变化。
要求在PLC控制系统下,通过调节阀的调节,能够平滑的调节氨气温度及压力,保持系统平衡。
③汽化撬设有安全连锁,保护装置及声光报警装置。
阐述基本原理,画出流程图、电气原理图。
二、方案介绍
在气化器入口设置液氨调节阀,通常该调节阀采用等百分比形式的气动调节阀。
在阀门仪表风管道上没置紧急切断电磁阀,在蒸汽入口设置蒸汽调节阀。
在控制系统中共有2个控制点:
蒸汽调节阀开度控制、液氨调节阀开度控制;3个检测点:
蒸汽温度检测、氨气出口压力检测、氨气出口液位检测。
采用PID控制技术,用蒸汽温度控制蒸汽调节阀开度,用出口压力控制液氨入口调节阀开度。
具体调节方式如下:
由于液氨进入量的变化,导致蒸汽温度变送器检测到的蒸汽温度测量值与水温给定值有所偏差,PID控制系统将测量值与给定值进行比较,并根据测量值与给定值偏差进行比例、积分、微分运算,从而输出一个控制信号给蒸汽入口调节阀,控制其开度,从而控制蒸汽流量,促使水温的测量值恢复到给定值。
因此,在逐步增大液氨入口调节阀开度的同时,蒸汽调节阀也自动跟随蒸汽温度增大开度。
直至氨气流量达到用户需求量,此时系统达到动态平衡。
同理,用氨气出口压力PID控制调节液氨入口调节阀的开度。
当氨气用量减小时,氨气出口压力升高,系统将通过PID运算,减小液氨入口调节阀的开度,减小液氨进入气化器的流量;反之,当氨气用量增加时,增大液氨入口调节阀的开度,增大液氨进入气化器流量。
直至系统达到动态平衡。
为保证系统工作安全,在控制系统设置安全连锁控制。
当蒸汽温度低限、出口气液分离罐内液位高限、气态氨气出口温度低限这3项中的其中1项超限报警,控制系统将连锁紧急关闭液氨入口调节阀,不让液氨进入气化器盘管,防止盘管内低温导致盘管冻裂或者损坏后续设备。
第2章硬件的设计
2.1硬件配置
2.1.1西门子S7-200CUP226
S7-200系列小型可编程逻辑控制器(Micro PLC)可应用于各种小型自动化控制系统。
高集成度的设计、低廉的成本以及丰富的指令集使得S7-200 PLC成为各种小型控制任务理想的解决方案,其产品的多样化以及基于Windows的编程工具,能够更加灵活地完成自动化任务。
S7-200系列PLC可提供4种不同的基本单元和6种型号的扩展单元。
其系统构成包括基本单元、扩展单元、编程器、存储卡、写入器等。
S7-200系列的基本单元如表1所示。
表1S7-200系列PLC中CPU22X的基本单元
型号
输入点
输出点
可带扩展模块数
S7-200CPU221
6
4
0
S7-200CPU222
8
6
2个扩展模块
S7-200CPU224
24
10
7个扩展模块
S7-200CPU224XP
24
16
7个扩展模块
S7-200CPU226
24
16
7个扩展模块
本论文采用的是CUP226。
它具有24输入/16输出共40个数字量I/O点。
可连接7个扩展模块,最大扩展至248路数字量I/O点或35路模拟量I/O点。
26K字节程序和数据存储空间。
6个独立的30kHz高速计数器,2路独立的20kHz高速脉冲输出,具有PID控制器。
2个RS485通讯/编程口,具有PPI通讯协议、MPI通讯协议和自由方式通讯能力。
I/O端子排可很容易地整体拆卸。
用于较高要求的控制系统,具有更多的输入/输出点,更强的模块扩展能力,更快的运行速度和功能更强的内部集成特殊功能。
可完全适应于一些复杂的中小型控制系统。
2.1.2模拟量输入/输出模块(EM231/EM232)
S7-200系列PLC用于热电阻测量输入(A/D转换)的特殊功能模块为EM231,模块可以将外部输入的2信道温度传感器(热电阻)测量值,转换为PLC内部处理所需的15位数字量。
EM231热电阻测量模块通过扩展电缆与PLC基本单元或扩展单元相连接,通过PLC内部总线传送数字量
表2所示为如何用DIP开关设置EM231模块。
在该表中,ON是闭合,OFF是断开。
只在电源接通时读取开关设置。
表2
EM232模块是组合强功率精密线性电流互感器、意法半导体(ST)单片集成变送器ASIC芯片于一体的新一代交流电流隔离变送器模块,它可以直接将被测主回路交流电流转换成按线性比例输出的DC4~20mA(通过250Ω电阻转换DC1~5V或通过500Ω电阻转换DC2~10V)恒流环标准信号,连续输送到接收装置(计算机或显示仪表)。
2.1.3传感器的选择
温度传感器——热电阻
热电阻是中低温区最常用的一种温度检测器。
它的主要特点是测量精度高,性能稳定。
其中铂热是阻的测量精确度是最高的,它不仅广泛应用于工业测温,而且被制成标准的基准仪;而热电偶一般用于中高温的测量,并且测量介质为氨气,氨气属于易燃气体,考虑到安全,选择隔爆型热电阻。
同时需要把信号远传至PLC,也就要求热电阻还需要远传功能。
输出信号分为4-20mA。
压力传感器——压力变送器
一般普通压力传感器的输出为模拟信号,只有经过A/D变换后才能得到数字信号。
本设计温度最大范围为40-80℃,所以选用工业级,其范围为-25-80℃。
设计压力范围为0-3.5MPa。
一般而言需要选择一个具有比最大值还要大1.5倍左右的压力量程的变送器。
所以选择测压范围为0-6MPa。
同样输出信号为4-20mA。
2.1.4调节阀的选择
调节阀有电动、气动两种类型。
而气动调节阀外部安装两个独立的行程调节机构,方便进行±5°全开或全关位置的调整。
更重要的是控制简单,且本质安全。
不需另外再采取防爆措施。
所以选用气动调节阀。
当使用工作温度为-20-+250℃时,只需采用普通的结构。
液氨是剧毒、易挥发、介质。
选用的密封填料为聚四氟乙烯的调节阀。
当气源中断时,要求调节阀处于关闭的位置。
需用气开方式调节阀。
所以蒸汽管路需用气开普通型调节阀,而液氨管路调节阀的密封填料为聚四氟乙烯。
2.2电气原理图
2.2.1氨气出口温度控制
投入运行后,通过调节蒸汽进口阀开度将氨气出口温度控制在60℃左右,为单回路控制。
用气量的变化会导致出口气温的变化,设在出口的PT100测量出口气体温度的变化,同时将温度信号通过模拟量输入模块EN231传送给PLC内,进行标准化转换及PID运算,这是PLC会通过模拟量输出模块EM232输出一个4-20mA的电流信号,蒸汽调节阀根据此信号连续调节蒸汽的进入量,保持NH3出口气体温度在设定的范围内波动,同时也保证了用气量与气化量基本一致,这样气化器出口温度也稳定维持在一个较小的范围内波动。
2.2.2氨液压力控制
通过蒸发器氨液入口调节阀控制氨气出口压力,为单回路控制。
由氨气压力控制液态氨入口气动调节阀开度。
随着氨气用量变化,气化器筒体内的氨气压力将发生变化,此时压力表送器会精确测量压力的变化趋势,同时将压力信号通过模拟量输入模块EN231传送给PLC内,进行标准化转换及PID运算,这是PLC会通过模拟量输出模块EM232输出一个4-20mA的电流信号,调节阀执行机构根据这个信号控制调节阀的开度,使液氨压力维持在预先设定的范围内,并且保持相对的稳定。
图1电气原理图
2.3I/O分配表
表3I/O分配表
输入
I0.0
启动按钮
I0.1
停止按钮
输出
Q0.1
启动指示灯
Q0.2
停止指示灯
Q0.3
正常运行指示灯
Q0.4
温度越低限报警指示灯
Q0.5
压力高限指示灯
Q0.6
液位高限指示灯
2.4硬件接线图
图2硬件连接图
第3章软件的设计
3.1编程软件STEP7--Micro/WIN概述
STEP7-Micro/WIN编程软件是基于Windows的应用软件,由西门子公司专为S7-200系列可编程控制器设计开发,它功能强大,主要为用户开发控制程序使用,同时也可以实时监控用户程序的执行状态。
以STEP7-Micro/WIN创建程序,为接通STEP7-Micro/WIN,可双击STEP7-Micro/WIN的图示,如图4所示,STEP7-Micro/WIN项目窗口将提供用于创建程序的工作空间。
浏览条给出了多组按钮,用于访问STEP7--Micro/WIN的不同编程特性。
指令树将显示用于创建控制程序的所有项目对象指令。
程序编辑器包括程序逻辑和局部变量表,可在其中分配临时局部变量的符号名。
子程序和中断程序在程序编辑器窗口的的底部按卷标显示。
图4STEP7--Micro/WIN项目窗口
本项目中我们利用STEP7--Micro/WINV4.0SP5编程软件,其接口如图4所示。
项目包括的基本组件:
程序块、数据块、系统块、符号表、状态表、交叉引用表。
3.2西门子S7-200内的PID控制
模拟量闭环控制较好的方法之一是PID控制,PID在工业领域的应用已经有60多年,现在依然广泛地被应用。
人们在应用的过程中积累了许多的经验,PID的研究已经到达一个比较高的程度。
比例控制(P)是一种最简单的控制方式。
其控制器的输出与输入误差信号成比例关系。
其特点是具有快速反应,控制及时,但不能消除余差。
在积分控制(I)中,控制器的输出与输入误差信号的积分成正比关系。
积分控制可以消除余差,但具有滞后特点,不能快速对误差进行有效的控制。
在微分控制(D)中,控制器的输出与输入误差信号的微分(即误差的变化率)成正比关系。
微分控制具有超前作用,它能猜测误差变化的趋势。
避免较大的误差出现,微分控制不能消除余差。
PID控制,P、I、D各有自己的长处和缺点,它们一起使用的时候又和互相制约,但只有合理地选取PID值,就可以获得较高的控制质量。
1、PID在PLC中的回路指令
西门子S7-200系列PLC中使用的PID回路指令,见表4
表4PID回路指令
名称
PID运算
指令格式
PID
指令表格式
PIDTBL,LOOP
梯形图
使用方法:
当EN埠执行条件存在时候,就可进行PID运算。
指令的两个操作数TBL和LOOP,TBL是回路表的起始地址,本文采用的是VB100,因为一个PID回路占用了32个字节,所以VD100到VD132都被占用了。
LOOP是回路号,可以是0~7,不可以重复使用。
PID回路在PLC中的地址分配情况如表5所示。
表5PID指令回路表
偏移地址
名称
数据类型
说明
0
过程变量(PVn)
实数
必须在0.0-1.0之间
4
给定值(SPn)
实数
必须在0.0-1.0之间
8
输出值(Mn)
实数
必须在0.0-1.0之间
12
增益(Kc
实数
比例常数,可正可负
16
采样时间(Ts)
实数
单位为s,必须是正数
20
采样时间(Ti)
实数
单位为min,必须是正数
24
微分时间(Td)
实数
单位为min,必须是正数
28
积分项前值(MX)
实数
必须在0.0-1.0之间
32
过程变量前值(PVn-1)
实数
必须在0.0-1.0之间
2、回路输入输出变量的数值转换方法
设定的给定值SP,但它不完全是过程变量PV,过程变量PV和PID回路输出有关。
在本文中,经过测量的温度、压力信号被转化为标准信号值才是过程变量,所以,这两个数不在同一个数量值,需要他们作比较,那就必须先作一下数据转换。
传感器输入的电压信号经过EM231换后,是一个整数值,但PID指令执行的数据必须是实数型,所以需要把整数转化成实数。
使用指令DTR就可以了。
如本设计中,是从AIW0读入温度被传感器转换后的数字量。
其转换程序如下:
MOVWAIW0AC0
DTRAC0AC0
MOVRAC0VD100
3、实数归一化处理
因为PID中除了采样时间和PID的三个参数外,其它几个参数都要求输入或输出值0.0-1.0之间,所以,在执行PID指令之前,必须把PV和SP的值作归一化处理。
使它们的值都在0.0-1.0之间。
单极性的归一化的公式:
Rnoum=(Rraw/32000)(3-1)
3.3S7-200程序设计
3.3.1流程图
主程序子程序0
图5主程序图6子程序0
子程序1
图7子程序1
中断1中断0
图8中断1图9中断0
3.3.2内存地址分配
表6内存地址分配
地址
说明
VD0
实际温度存放
VD4
设定温度存放
VD10
实际压力存放
VD14
设定压力存放
3.3.3PID指令回路表
表7内存地址分配
地址
名称
说明
VD100
过程变量(PVn)
必须在0.0-1.0之间
VD104
给定值(SPn)
必须在0.0-1.0之间
VD108
输出值(Mn)
必须在0.0-1.0之间
VD112
增益(Kc)
比例常数,可正可负
VD116
采样时间(Ts)
单位为s,必须是正数
VD120
采样时间(Ti)
单位为min,必须是正数
VD124
微分时间(Td)
单位为min,必须是正数
VD128
积分项前值(MX)
必须在0.0-1.0之间
VD132
过程变量前值(PVn-1)
必须在0.0-1.0之间
3.3.4S7-200程序设计梯形图
主程序
调用子程序(SBR_0为温度PID参数设定SBR_1为压力PID参数设定)
整数至双整数至实数实数相除(归一处理)把数字信号存入VD100。
子程序
3.4系统程序调试
PID参数整定方法就是确定调节器的比例系数P、积分时间Ti和和微分时间Td,改善系统的静态和动态特性,使系统的过渡过程达到最为满意的质量指针要求。
由于西门子S7-200的V4.0版的编程软件STEP7-Micro/WIN提供了PID参数自整定功能和PID整定控制面板。
这两项功能相结合,使用户能轻松地实现PID的参数自整定,同时可以对最多8个回路进行自整定。
自整定能提供一组近似最优的整定参数。
西门子S7-200的PID参数自整定可由PID整定控制面板来实现,如图10:
图10PID调节面板界面
第一步:
在PIDWizard(向导)中完成PID功能配置
第二步:
打开PID调节控制面板,设置PID回路调节参数
在Micro/WINV4.0在线的情况下,进入PID调节控制面板中,如果面板没有被启动(所有地方都是灰色),可点击配置按钮运行CPU。
在PID调节面板的当前PID区选择要调节的PID回路号,在调节参数区选择手动,调节PID参数并点击更新,使新参数值起作用,监视其趋势图,根据调节状况改变PID参数直至调节稳定。
第三步:
在调节参数区点击高级按钮,设定PID自整定选项。
如果不是很特殊的系统,也可以不加理会。
图11高级PID自动调节参数界面
第四步:
在手动将PID调节到稳定状态后,即过程值与设定值接近,且输出没有不规律的变化,并最好处于控制范围中心附近。
此时可点击调整参数区内的开始自动调节按钮启动PID自整定功能,这时按钮变为停止自动调节。
这时只需耐心等待,系统完成自整定后会自动将计算出的PID参数显示在d.区。
当按钮再次