火力发电厂主要控制工艺逻辑.docx
《火力发电厂主要控制工艺逻辑.docx》由会员分享,可在线阅读,更多相关《火力发电厂主要控制工艺逻辑.docx(18页珍藏版)》请在冰点文库上搜索。
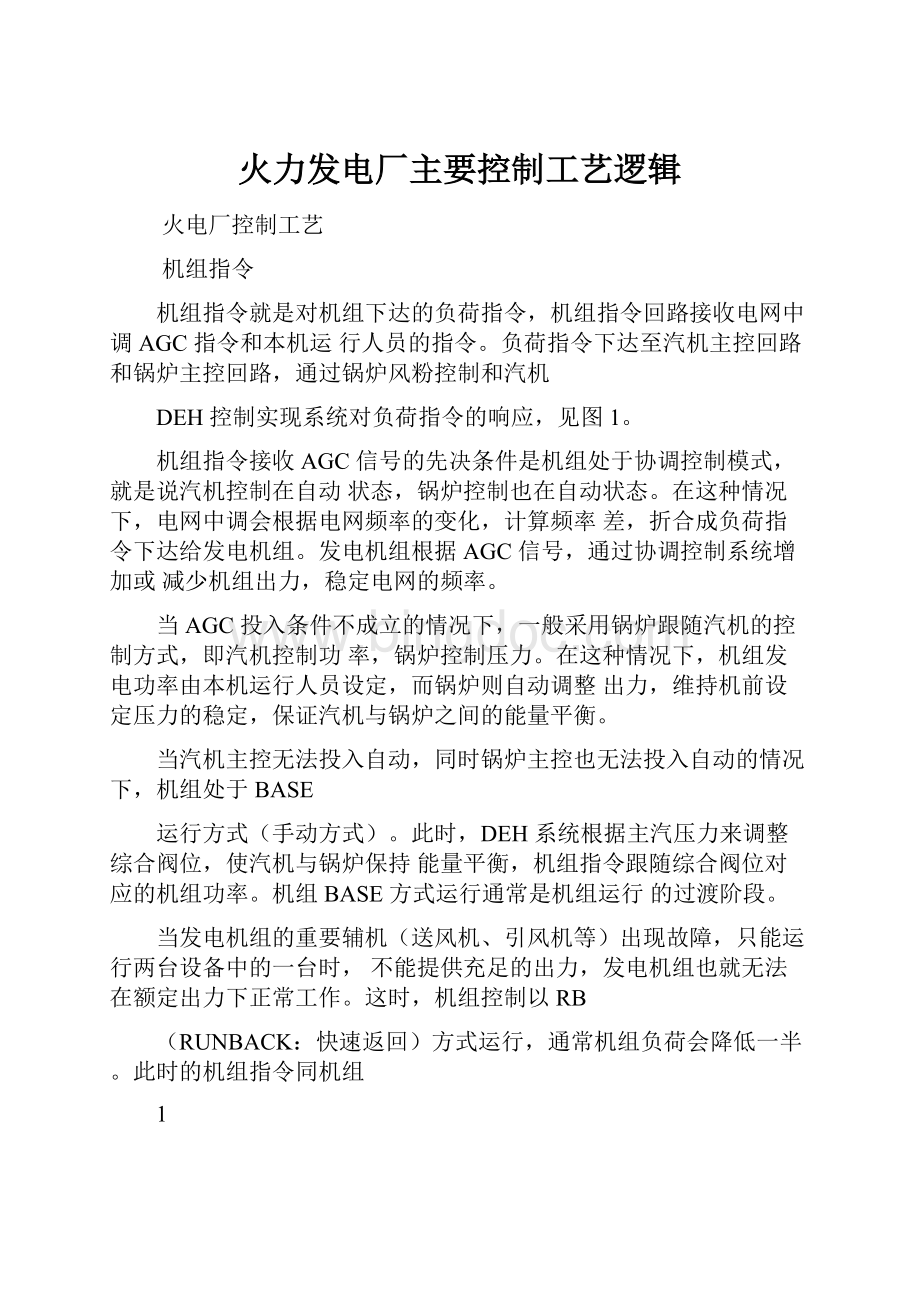
火力发电厂主要控制工艺逻辑
火电厂控制工艺
机组指令
机组指令就是对机组下达的负荷指令,机组指令回路接收电网中调AGC指令和本机运行人员的指令。
负荷指令下达至汽机主控回路和锅炉主控回路,通过锅炉风粉控制和汽机
DEH控制实现系统对负荷指令的响应,见图1。
机组指令接收AGC信号的先决条件是机组处于协调控制模式,就是说汽机控制在自动状态,锅炉控制也在自动状态。
在这种情况下,电网中调会根据电网频率的变化,计算频率差,折合成负荷指令下达给发电机组。
发电机组根据AGC信号,通过协调控制系统增加或减少机组出力,稳定电网的频率。
当AGC投入条件不成立的情况下,一般采用锅炉跟随汽机的控制方式,即汽机控制功率,锅炉控制压力。
在这种情况下,机组发电功率由本机运行人员设定,而锅炉则自动调整出力,维持机前设定压力的稳定,保证汽机与锅炉之间的能量平衡。
当汽机主控无法投入自动,同时锅炉主控也无法投入自动的情况下,机组处于BASE
运行方式(手动方式)。
此时,DEH系统根据主汽压力来调整综合阀位,使汽机与锅炉保持能量平衡,机组指令跟随综合阀位对应的机组功率。
机组BASE方式运行通常是机组运行的过渡阶段。
当发电机组的重要辅机(送风机、引风机等)出现故障,只能运行两台设备中的一台时,不能提供充足的出力,发电机组也就无法在额定出力下正常工作。
这时,机组控制以RB
(RUNBACK:
快速返回)方式运行,通常机组负荷会降低一半。
此时的机组指令同机组
1
BASE方式运行时相似,处于跟随模式。
即主汽压力不断下降,汽机进汽调节阀逐渐关小,
机组负荷指令则根据综合阀位的大小跟随相应值。
机组指令控制是机组控制系统的顶层控制,也是协调控制的顶层控制,伴随着机组运行
工况的变化,指令控制会选择相应控制策略,保持机组出力与电网需求的平衡和汽机与锅炉
的能量平衡。
图1指令控制SAMA图
协调控制系统
协调控制系统就是汽机与锅炉协调控制系统,通常存在三种协调控制方式:
机炉协调控
制方式、锅炉跟随方式、汽机跟随方式,见图2。
图2协调控制系统SAMA图
在汽机主控在自动态,且锅炉主控在自动态时,机组控制处于机炉协调控制模式。
在机炉协调控制方式下,汽机与锅炉并行操作,锅炉控制机前压力,汽轮机控制功率,两者互相影响。
负荷变化过程先于锅炉指令信号,同时压力变化修正调节阀位置。
当汽机主控在手动态,且锅炉主控在自动态时,机组控制处于锅炉跟随模式。
在锅炉跟随控制方式下,锅炉控制机前主汽压力,汽机调门采用手动调节的方式来获得期望的功率。
3
控制过程为,主汽压力设定值与机前压力相比较,其偏差经过发电机信号前馈和修正后产生锅炉指令信号去风和燃料回路。
同时,运转员通过设定调节阀位置来建立负荷指令。
当锅炉主控在手动,且汽机主控在自动时,机组控制处于汽机跟随模式。
在汽机跟随控制模式下,汽轮机控制机前蒸汽压力,通过调节锅炉的燃烧率来获得期望的负荷。
运转员手动设置燃料和风量值,燃料和风量的变化会带来锅炉能量水平的变化,从而改变机前压力的
变化。
定压滑压选择
机前压力是单元制机组负荷控制一个十分重要的参数,定压和滑压选择指在机组正常运
行时,机前压力是保持一个定值还是维持某一个函数关系。
机前压力设定值应该等于某个目
标值还是按照某个函数关系跟踪负荷指令,则是由定压滑压选择控制策略来实现,见图3。
偏置设定值
I
A
I
滑压设定值
AI
AI
IA
PS
I
压力速率限制
定压设定值
压力实际设定值
图3定压滑压选择
单元机组按照定压方式运行时,机前压力保持不变,机组功率与调节阀的开度保持一一
对应关系。
单元机组滑压运行时,汽机调节阀的开度维持不变——一般为全开位置,机组功
率与机前压力保持一一对应关系。
定压可以在机组任意控制模式下选择,而滑压需要在锅炉跟随控制模式并且机组负荷较
大的情况下进行。
在机炉协调模式下,如果出现RB,则控制方式变为锅炉跟随,机前压力
维持动作前压力一段时间,然后按照一定的速率滑压下降。
4
汽机控制工艺
汽机控制
汽机控制就是汽轮机调节阀控制,汽机控制的执行部分就是数字电液调节系统DEH。
汽机控制在不同的控制方式下,将汽机指令送达DEH系统,DEH系统根据汽机指令作出相应的动作,驱动调节阀动作,完成对负荷或压力的控制,见图4。
汽机指令
TD
TF
CCS遥控
DEH反馈信号
100%
T
T
T
0%
II
H/L
A
至DEH
图4汽机控制SAMA图
相对于锅炉控制,汽机控制要简单一些,主要DEH控制。
DEH系统控制根据指令调节调节阀的开度,完成对转速和负荷的控制。
给水控制在设备属于汽机侧,但是在自动状态下接收的锅炉指令。
给水控制主要对两台汽动给水泵和一台电动给水泵的控制。
在机组启动阶
段和低负荷阶段,由30%负荷的电动给水泵供水,采用单冲量水位控制方式。
在负荷较高阶段和额定负荷运行时,有两台50%负荷的启动给水泵供水,采用三冲量的水位控制模式。
给水控制(汽泵)
汽动给水泵是机组正常运行时的全部给水来源,采用三冲量的水位控制策略,见图5。
汽包水位被控对象的扰动有四个来源,给水量的扰动为内部扰动,其余如蒸汽负荷的扰
动、燃料量的扰动以及汽包压力的扰动等为外部扰动。
其中给水扰动、汽机负荷扰动和锅炉
热负荷扰动影响比较大。
由于蒸汽流量和燃料量的变化是经常产生的外部扰动,并且是产生"虚假水位"的根源,
所以在给水控制系统里常常引入蒸汽流量、燃料量信号作为前馈信号,以改善外部扰动时的
控制品质。
如上图所示,三冲量的调节回路中主要包含有主调节器TPI及付调节器TPI,付
调节器一般用比例规律的。
主调节器接受水位信号作为主控信号去控制副调节器。
副调节器
除接受主调节器信号外,还接受给水量反馈信号和蒸汽流量信号,组成一个三冲量的串级控制系统,其中副调节器的作用主要是通过内回路进行蒸汽流量和给水流量的比值调节,并快速消除来自给水侧的扰动。
而主调节器主要是通过副调节器对水位进行校正,使水位保持在
给定值。
当负荷变化而出现“虚假水位”时,由于采用了蒸汽流量信号,就有一个使给水量与负
荷同方向变化的信号,从而减少了由于“虚假水位”现象而使给水量向与负荷相反方向变化
的趋势,从而改变蒸汽负荷扰动下的水位控制质量。
汽动给水泵控制分成遥控和本地自动两种控制方式。
遥控时接收锅炉指令,自动维持水
位稳定;本地自动时,根据操作员的指令设定水位维持水位在设定值。
图5给水控制——汽泵
给水调节阀控制
给水调节阀是低负荷阶段电动给水泵供水时维持水位稳定的控制手段,见图6。
在机组启动初期,主给水门关闭,电动给水泵定速运行,通过控制给水调节阀的开度,
调节给水流量,达到控制水位的目的。
此时,水位控制器对设定值和水位值的偏差进行运算,生成自动控制指令去控制给水调节阀的开度,改变给水流量,使水位跟踪设定值,进行单冲
量的水位调节。
当机组运行在高负荷状态,锅炉供水由两台启动给水泵供应,水位控制是三冲量控制方式。
如果此时有一台启动给水泵跳闸,则会联锁启动电动给水泵,保持水位的三冲量控制方式不变,此时串级控制器1计算水位实际值与水位设定值之间的偏差,然后与主蒸汽流量相加输出至串级控制器2。
串级控制器2计算控制器1与凝结水流量的偏差,计算相应阀位指令。
给水调节阀接收阀位指令,作出相应的开关动作,调节给水流量,从而达到控制水位的
目的。
图6给水调节阀控制SAMA图
7
给水控制(电泵)
电动给水泵是机组启动和低负荷阶段锅炉供水设备,控制策略,见图7。
在机组启动初期,电动给水泵定速运行,通过控制给水调节阀的开度,调节给水流量,达到控制水位的目的。
随着负荷的开高,要求的给水量增加,该启动控制阀逐渐开大,到了一定开度以后,调节性能变差,当发现控制阀已无法再对给水进行调节时,手动升高电泵转速,提高给水母管压力,增加给水,此时,启动控制阀仍然可以自动地将水位维持在设定值
上。
随着负荷继续升高,给水压力已升得较高,给水调节阀承受的节流压差也越来越大,当给水调节阀门开到90%以后,将电动给水泵转速控制投自动。
给水控制由给水调节阀节流
调节方式变成了给水泵转速调节方式。
当启动给水泵跳闸时,电动给水泵联锁启动,三冲量方式调节水位。
图7给水控制——电泵
8
除氧器水位控制
除氧器是凝结水通路上净化凝结水,保证水、汽纯净的重要设备,主要作用是除去溶解
在凝结水中的非凝结空气。
除氧器水位控制是平衡锅炉给水和凝结水的重要控制策略,与汽包水位或者汽水分离器
水位控制策略相似。
在给水流量较小的情况下,采用单冲量控制方式。
在给水流量较大时,
采用三冲量控制方式,将给水流量和凝结水流量扰动纳入控制策略中。
见图8。
在给水流量较小,单冲量控制方式下,除氧器水位控制通过除氧器给水调节阀开度的调
控实现控制目的,使除氧器水位跟踪除氧器水位设定值。
在给水流量较大,三冲量控制方式下,除氧器水位控制同时要将凝结水流量和给水流量
作为调节过程中的扰动量加以处理。
首先,除氧器水位设定值与实测值比较,差值经过一级
PID处理,得出值与给水流量换算值累加,累加后的值在第二级PID处理前与凝结水流量比
较,得出的差值经过计算得出除氧器给水调节阀开度需要的增加值或者减小值。
开度变化值
送到除氧器给水调节阀,阀门作出相应动作,除氧器供水量随之变化,达到维持除氧器水位
跟踪设定值的目的。
图8除氧器水位控制SAMA图
9
凝汽器热井水位控制
凝汽器是是机组安全、高效、经济、稳定运行的重要环节,是机组汽水循环中水的起点。
凝结水位控制的有效运行可以保障凝汽器运行的安全性,也使机组运行的经济性和稳定性得
到保证。
与凝结水水位相关的有两台设备,凝结水位调节阀和凝结水至凝补水箱溢流阀。
当凝结水水位低于设定值时,凝结水位调节阀增大开度,增加凝结水箱补水,使水位上升,跟踪设定值。
当凝结水位高于凝结水位设定值时,凝结水至凝补水箱溢流阀增大开度,凝结水热井
中的凝结水通过溢流阀泄至凝补水箱,凝结水位下降,跟踪设定值。
见图9。
图9凝结水位控制SAMA图
首先,凝汽器水位实测值与凝汽器水位设定值比较,差值经过左侧PID计算,得出凝
结水位调节阀需要增大或者减小的开度,开度指令驱动凝结水位调节阀开大或者关小,达到
调节水位的目的;同时,差值经过右侧PID处理得出溢流阀需要减少或者增加的开度,开
度指令驱动溢流阀动作,同样实现调节凝结水位的目的。
高压加热器水位控制
高压加热器(或者低压加热器)是提高凝给水温度和机组热循环效率的装置。
高压加热器是一种表面式热交换器,一般放在除氧器之后,抽取汽轮机高压缸中的蒸汽
加热给水。
高压加热器安装疏水调节阀和危急疏水调节阀,用来不断地排出加热给水的蒸汽
10
凝结后的疏水,疏水的水位(即高压加热器的水位)需要维持一个稳定值。
如果高加水位过高,影响热交换效果,还有可能使疏水从抽汽管直接通过疏水阀排出,影响加热效果,还可能使疏水从抽汽管倒流入汽轮机,形成水冲击;如果水位过低,加热蒸汽可能直接通过疏水
阀排出,影响加热效果和经济性,同时还影响环境。
低压加热器是加热凝结水的装置,作用与高压加热器相同。
二者的不同之处在于温度不
同、抽汽位置不同。
本文通过解析高压加热器的控制策略来说明高压加热器和低压加热器共
通的控制原理,见图10。
高压加热器水位控制由高加疏水调节阀和高加危急疏水调节阀两个装置完成。
高加疏水
调节阀在调节稳定高加水位的过程中起到主要作用。
高加危急疏水调节阀在高加水位异常高
的情况下加入调节高加水位的控制中,高加危急疏水调节阀动作比高加疏水调节阀更快,二
者的设定值不同。
首先,高加水位实测值与设定值比较,差值经过左侧PID计算得出调节阀需要增大或
减小的开度,开度指令送到调节阀,调节阀根据指令值开大或者关小阀门,完成水位调控的
一次循环。
如果水位异常高,危急调节阀加入水位调节。
高加水位实测值与危急调节阀设定
值比较,差值经过右侧PID处理得出危急调节阀的开度指令,高加危急疏水调节阀根据开
度指令迅速动作,完成高加水位的调节。
图10高压加热器水位控制SAMA图
2.2.7高压旁路减压调节阀控制
高压旁路被控对象为减压阀、喷水隔离阀、喷水调节阀,高压旁路控制系统有启动、溢
流和安全三个主要功能(即三用阀功能)。
启动功能:
改善机组的启动特性;提高锅炉在启动过程中的燃烧率;使蒸汽温度与汽轮
机缸温得到最佳匹配;缩短机组启动的时间,减少寿命损耗。
溢流功能:
吸收机、炉之间的不平衡负荷;排泄机组在负荷瞬变过度过程中的剩余蒸汽;
调整稳定争气压力;维持锅炉在不投油情况下的最低稳燃负荷。
安全功能:
取代锅炉安全阀的功能。
机组旁路系统投入备用后,当机组的机前实际压力
与机组高压旁路压力设定值差值大于旁路超压偏置设定值时,旁路系统将自动参与压力调节,维持主蒸汽压力等于设定值。
在旁路控制中,关键控制是对高旁减压调节阀的控制,本闻就高旁减压调节阀的控制策略加以说明,见图11。
图11高旁减压调节阀SAMA图
首先,主汽压力实测值与一级PID输出比较,差值经过第二级PID处理得出阀位开度
12
指令。
减压调节阀根据指令动作,调整主汽压力。
同时,阀位指令回到一级PID入口,指
令与坡度处理后指令比较,差值经过一级PID处理得出下一次处理循环与主汽压力实测值
的比较值。
高旁减压阀的调节压力过程是动态调整的,这就保证了调整过程的平滑和有效。
锅炉控制工艺
燃烧控制
锅炉燃烧控制是机组控制的难点,合适的控制策略能够减少锅炉对负荷指令响应的延迟
时间,提高机组的响应速度和运行的经济性。
图12是能量输入信号图,能量输入必须与能量需求匹配。
能量输入的计量如果采用给
粉机转速或者容量风的风门开度来计算,易受制粉系统延迟或者煤质变化等因素的影响。
本
文采用P1+dPd/dt(一级压力与汽包压力变化率之和)作为锅炉能量输入的信号反馈。
一级
压力和汽包压力都容易计量,这就提供了一个在稳态和动态工况下都比较稳定的能量输入测
量方法。
图12能量信号SAMA图
13
燃烧控制的滞后与延迟一直是火电机组控制不易解决的问题,新兴的控制策略如预测控
制、矩阵控制等较好的改善了锅炉燃料输入延迟和滞后,基本策略都是在能量需求信号上加
上比较大的前馈,以缩短响应时间,提高响应速度,见图13。
由一级压力P1和汽包压力变化值相加得出锅炉能量输入信号,能量输入信号需要经过实际燃料输入值的热值修正,修正的锅炉能量输入热值与锅炉指令(能量需求)相比较。
差值经过一级PID运算得出第一个燃料需求值,第一个燃料需求值再经过实际燃料输入的校正,经过第二级PID计算得出燃料需求值,送给给煤机或容量风门,增加或者减少燃料输
入。
这种控制策略的优点在于:
在增加和减少燃料的过程中,动态修正燃料指令,避免过于追求前馈控制而造成波动,使锅炉响应的可控制增强。
图13燃烧控制SAMA图
在当代,火力发电在电力供应中占有主要地位,提供着大部分社会生活生产用电。
而锅炉是火力发电生产中的重要设备,其效能直接影响火力发电的效率和经济性。
锅炉燃烧中用到的煤等又是重要的不可再生资源,因此锅炉的燃烧控制相当重要,控制水平的低下将造成资源浪费、效率不高和环境污染。
近期,锅炉燃烧控制又出现了利用模糊综合评判,运用具体的实例,评价了锅炉燃烧控制系统,调整燃烧控制量等新的燃烧控制策略。
模糊综合评判方法,对锅炉燃烧系统的控制量进行综合评判,通过改变燃料量、送风量、引风量,进而改变控制量,达到较好的燃烧效果。
相信这些新策略和新技术的逐步成熟会带来燃烧控制水平的逐步提升。
当前,社会经济快速发展,能源的供需矛盾日益突出。
目前,煤炭在我国的能源消费结
构中占主导地位。
全国煤炭消耗总量中有60%以上直接用在电站锅炉中燃烧,要充分利用锅炉和锅炉燃烧中的煤炭资源,适当的改善燃烧的控制量因素使煤炭燃烧充分,以提供高效
的热量,同时减少空气的污染。
引风控制
锅炉炉膛压力是锅炉运行需要监控的重要参数,引风控制就是维持锅炉炉膛的压力稳定,并使锅炉处于微负压运行状态的控制策略,见图14。
引风控制的设备是两台引风机,控制目标是炉膛压力。
自动控制状态下,引风控制的目标是维持锅炉压力始终跟踪设定值。
当送风量发生变化时,送风指令作为前馈送到引风控制
第一级PID,第一级PID得出第一个引风指令,第一个引风指令经过实际引风值的校正,在
第二级PID计算出最终引风指令,即引风挡板开度指令或引风机转速指令。
引风控制的最
终目的就是维持炉膛压力稳定,避免锅炉运行正压或负压波动。
图14引风控制SAMA图
15
送风控制
送风机是锅炉风量与氧气供应的主要设备,锅炉风量由一次风(制粉风)和二次风(助燃风)构成,风量的调控由送风机完成。
锅炉通常运行在富氧状态,即锅炉内氧气的供应量要略大于燃料对氧气的需求量,这样可以保证燃料的充分燃烧,避免资源的浪费。
而锅炉内氧气是否充足的依据是尾部烟道(一般在省煤器入口取样)烟气中的含氧量,烟气中含氧就表明锅炉供氧是充足的。
但是,锅炉中的供氧量不宜过高,否则容易出现尾部烟道的二次燃烧。
送风控制就是根据锅炉对氧气的需求为基础,以烟气氧量为控制目标,生成相应的风量
指令,见图15。
图15送风控制SAMA图
送风控制策略比较复杂,烟气含氧量的控制目标要由风量调整来实现。
首先,由一级压
力换算得出锅炉燃料燃烧需要的氧气供应量与操作员输入的富氧水平相加,然后与烟气实际
16
含氧量比较得出差值,经过PI运算得出需要增加或减少的氧量指令。
氧量指令还要经过能量需求BD、锅炉实际输入能量HR和一级压力P1综合计算值的
修正,修正后得出锅炉对送风量的需求。
送风量需求值与实际风量比较,得出差值,差值一
级PID运算后得出需要增加或减少的送风量,一级PID得出的送风量再经过实际送风量指
令的修正得出最后的风量指令。
最后的送风量指令送到送风机或送风机挡板,通过送风机转速或挡板开度达到调整送风
量的目的,而送风量的调整同时会完成锅炉烟气含氧量的调整。
一级减温控制
锅炉过热蒸汽减温器是控制过热汽温度的重要装置,过热蒸汽一级减温器在控制过热汽
温度过高的同时,也保护过热器管道不被烧毁。
一级减温控制采用串级控制方式,以二级减温器前汽温为调节目标,通过控制一级减温
器后温度实现,见图16。
首先,二级减温器前实测汽温与二级减温器前汽温设定值比较,差值运算后得出一级减温器后汽温目标值。
一级减温器后气温目标值与实测值比较,差值经过PID运算得出一级减温水调节阀应该增加或减小的开度。
开度变化指令送到减温水调节阀,通过减温水调节阀
开度的变化,增加或减少减温水投入量,达到调控温度的目的。
图16一级减温控制SAMA图
17
二级减温控制
二级减温控制是锅炉二级减温水调节阀控制策略,二级减温控制以主汽温度作为调控目
标,通过调节二级减温器后汽温实现调控目标,见图17。
二级减温控制的主要作用在于维持主汽温度的稳定。
饱和蒸汽要经过多段过热器继续加
热,生成高温高压且温度稳定过热汽去推动汽轮机工作。
而且每一种锅炉与汽轮机组都有一个规定的运行温度。
锅炉出口过热蒸汽温度是整个锅炉蒸汽通道中温度最高的地方,过热器材料虽然是耐高温、高压的合成材料,但在锅炉正常运行时过热器温度已接近材料容许的极限温度,为了设备的安全,必须严格控制过热器的温度。
若过热蒸汽温度过高,会使过热器、汽轮机高压缸等设备过热变形而造成损坏,温度过低则会降低机组热效率,因此要求控制出口温度稳定可靠。
减温控制的控制滞后与传输滞后都很大,要达到高精度高灵敏度的温度控制是很困难的。
为此采用分段调节,其中最常见的是两段调节。
这样,每段中的对象容积滞后与传输滞后时间均可减少一半。
图17二级减温控制SAMA图
一级减温控制前面已经有所阐述,二级减温同样采用串级控制的方式实现温度调控。
首
先,过热器出口温度实测值与操作员设定值比较,差值经过一级PID处理得出二级减温器
后目标值。
二级减温器后汽温目标值再与实测温度比较,差值经过二级PID处理得出二级
18
减温水调节阀需要增加或减小的开度。
开度指令送到减温水调节阀,调节阀动作,增加或减
少减温水投入量,汽温随之发生相应的变化,控制目的达成。
煤层二次风控制
在锅炉燃烧过程中,二次风挡板的调节起重要作用。
二次风挡板包括周界风挡板、二次
风挡板、顶部燃尽风挡板和油枪层风门挡板。
运行时二次风挡板的调整可使燃烧器保持适当
的一、二次风配比,同时保持合适的一、二次风出口速度和风量,使风粉混合均匀,保证燃
料正常着火与燃烧。
煤质发生变化的二次风挡板在高负荷时应采用均等配风;低负荷时采用倒宝塔配风。
可
以通过细微调整部分二次风挡板来调节汽温、排烟温度。
各二次风门可通过改变各自的偏置
值来进行调整。
下面就煤层二次风控制来说明二次风控制策略,见图18。
图18煤二次风门控制SAMA图
煤层二次风控制的作用是保持风、煤配比适度,使进入锅炉的煤粉充分燃烧。
一般的锅
炉在实际运行中对二次风的控制并不精细,通常选择小开度或者全开。
二次风挡板随给粉量
作相应调整在实际运行中并不经常使用,这就造成了二次风控制的粗糙性。
本文的控制策略很好解决了二次风挡板粗糙控制的问题。
首先,在只有煤粉燃料的情况
下,二次风挡板选择煤粉对应挡板开度指令,指令送达二次风门电机,风门动作,二次风量调整完成;在只有燃油供应锅炉热量的情况下,二次风挡板开度指令切换到燃油供应热量状态,同样开度指令送达二次风门电机,完成风量调整;在煤粉投运,同时附近燃油也在供应的情况下,改由负荷指令换算二次风门开度指令,指令送达风门电机,完成调整。
一次风压力控制
在大型机组的风系统中,一次风是提供给制粉系统的制粉动力。
一次风分为冷一次风和热一次风,冷一次风从一次风机出口直接送到磨煤机,而热一次风经过空气预热器后送到磨
煤机。
热一次风用于保证煤粉进入锅炉时即有一定的温度,提高能量利用率和制粉效率,冷
一次风用于调节热一次风温,以保证磨煤机出口温度保持合适的水平。
图19热一次风压控制SAMA图
一次风在制粉过程中的作用主要是干燥原煤、粗粉与细粉分离、输送煤粉进入炉膛。
首
先,冷一次风和热一次风在磨煤机一次风入口汇合,混合成温度适中的一次温风。
然后,一
次风温风分成两路,一路称为旁路风,一路称为容量风。
旁路风进入磨煤机燃料混合箱,干
燥原煤斗来煤,然后进入磨煤机。
容量风直接从磨煤机底部进入磨煤机,吹起磨煤机研磨而
成的煤粉。
旁路风和容量风在磨煤机内汇合,携带煤粉沿着送粉管道离开磨煤机,中间经过
粗