模具设计中为避免锻件折叠应考虑的因素.docx
《模具设计中为避免锻件折叠应考虑的因素.docx》由会员分享,可在线阅读,更多相关《模具设计中为避免锻件折叠应考虑的因素.docx(12页珍藏版)》请在冰点文库上搜索。
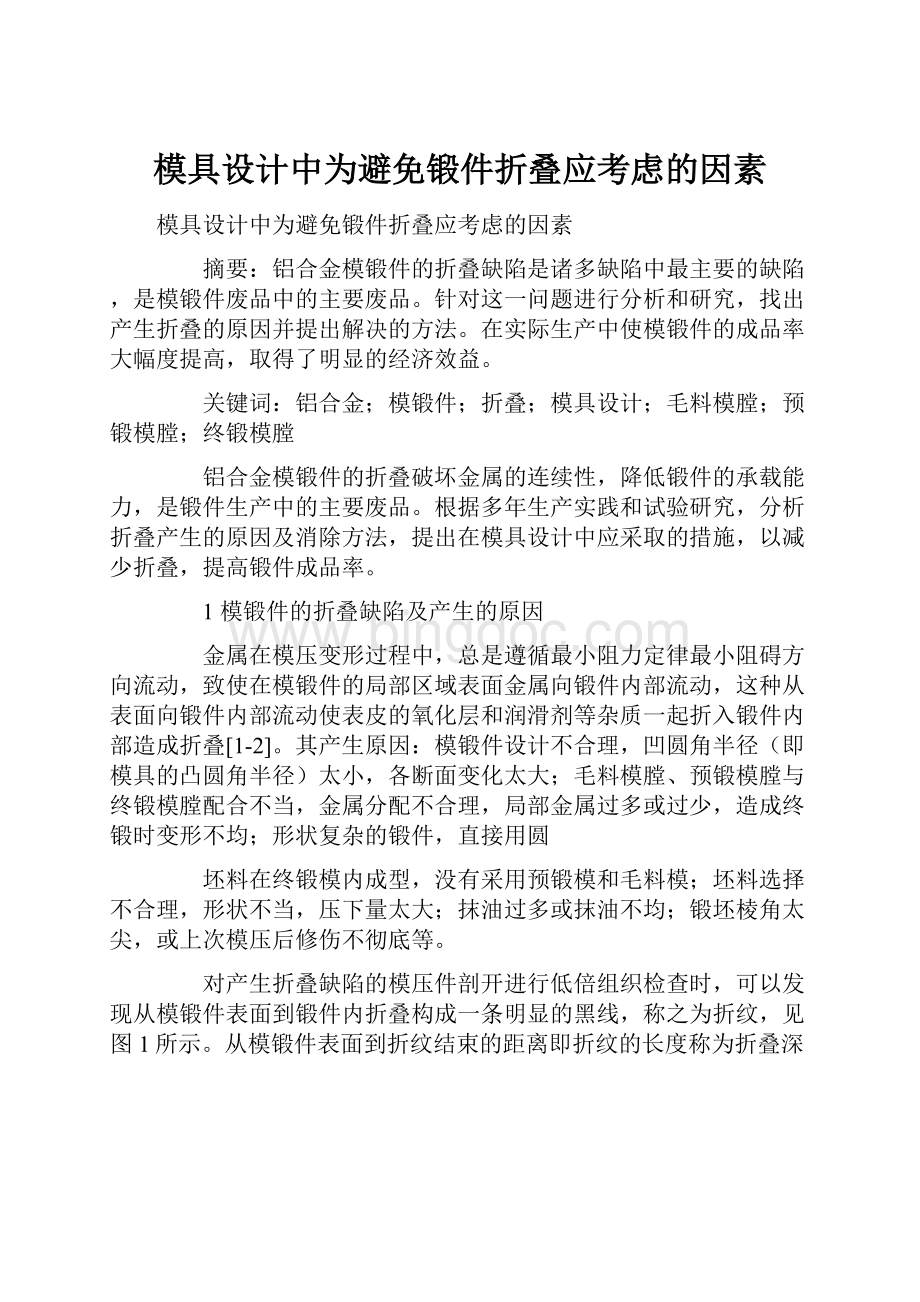
模具设计中为避免锻件折叠应考虑的因素
模具设计中为避免锻件折叠应考虑的因素
摘要:
铝合金模锻件的折叠缺陷是诸多缺陷中最主要的缺陷,是模锻件废品中的主要废品。
针对这一问题进行分析和研究,找出产生折叠的原因并提出解决的方法。
在实际生产中使模锻件的成品率大幅度提高,取得了明显的经济效益。
关键词:
铝合金;模锻件;折叠;模具设计;毛料模膛;预锻模膛;终锻模膛
铝合金模锻件的折叠破坏金属的连续性,降低锻件的承载能力,是锻件生产中的主要废品。
根据多年生产实践和试验研究,分析折叠产生的原因及消除方法,提出在模具设计中应采取的措施,以减少折叠,提高锻件成品率。
1模锻件的折叠缺陷及产生的原因
金属在模压变形过程中,总是遵循最小阻力定律最小阻碍方向流动,致使在模锻件的局部区域表面金属向锻件内部流动,这种从表面向锻件内部流动使表皮的氧化层和润滑剂等杂质一起折入锻件内部造成折叠[1-2]。
其产生原因:
模锻件设计不合理,凹圆角半径(即模具的凸圆角半径)太小,各断面变化太大;毛料模膛、预锻模膛与终锻模膛配合不当,金属分配不合理,局部金属过多或过少,造成终锻时变形不均;形状复杂的锻件,直接用圆
坯料在终锻模内成型,没有采用预锻模和毛料模;坯料选择不合理,形状不当,压下量太大;抹油过多或抹油不均;锻坯棱角太尖,或上次模压后修伤不彻底等。
对产生折叠缺陷的模压件剖开进行低倍组织检查时,可以发现从模锻件表面到锻件内折叠构成一条明显的黑线,称之为折纹,见图1所示。
从模锻件表面到折纹结束的距离即折纹的长度称为折叠深度。
图1模锻件的典型折叠(低倍组织)
折叠对模锻件的质量有严重的影响。
首先折叠破坏了模锻件表面的完整性,使制件承受载荷面积大为减小。
折叠本身又是制件上的一个缺口,在使用中造成应力集中,成为疲劳源,可能导致部件在此产生疲劳断裂。
其次折缝夹杂有润滑剂或其他杂质,在随后的蚀洗工序中折缝又残存有酸、碱的残液,会造成制件在折叠处过腐蚀。
从模锻件的内部组织看,表面存在折叠处金属的流纹将产生涡流或穿流,折叠越是严重,金属流线就越不顺。
折叠缺陷的产生是由表面折波、生成折叠、折叠发展三个过程组成。
在折叠的初生阶段,折纹的尾端成小圆角状(见图2)。
如果经大量变形之后折纹的尾端又可成尖裂状或叉形开裂状(见图3)。
极为严重的折叠会把模锻件的整个筋型穿断(见图4)。
一般某一处的折叠主要是由一个主要折纹组成。
由单个折纹构成的折叠较深,而由多股折纹构成的折叠深度较浅。
图2初生折叠、折纹尾端成小圆角状
图3折叠尾端的尖裂
图4严重折叠穿断筋型
现场生产的轻合金模锻件大量的是属于普通开式模锻,其锻件与其零件之间存在有一定的加上余量,还有模锻斜度和较大的圆角。
因此尽管有些模锻件局部存在折叠缺陷,但只要折叠的深度不超过机械加工余量,即最终折叠部残存在零件主体上还是允许的,是符合产品技术要求的。
所以现场生产中,通过剖伤的方法来确定锻件是否报废。
多年的实践证明,这种剖伤的方法是鉴别折叠缺陷是否构成锻件报废的行之有效的、方便的检查方法。
折叠按其位置而言可分为筋根折叠、筋顶折叠、弯角折叠、边缘折叠四种。
按其产生的机制而言可分为穿筋折叠、包覆折叠、回流折叠、汇流折叠和压堆折叠五种。
造成折叠的原因及影响因素是多方面的,主要可归纳为三个方面:
从零件图到模锻件图设计过程中考虑的因素;生产工艺编制上的因素;生产具体操作中的因素。
下面将就模具设计过程中为消除锻件折叠应考虑的因素进行讨论。
2模锻件设计中必要的形状简化
模锻件的形状应该尽量与零件形状一致,但是为便于模锻的顺利完成和消除象折叠等模锻缺陷就得进行必要的形状简化。
生产实践证明,产生折叠的主要原因往往是在金属已经充满模腔之后,由于还有过多的金属存在,则使锻件的欠压合量(简称欠压量)过大,为了减少欠压量,即使过多的金属以毛边的形式排出就得继续施压变形。
这样在过多的金属外流的时候就是最易产生折叠的阶段,而且这些折叠集中地产生在模件筋形根部与腹板连接的圆角处。
具有框形封闭筋的模锻件,在其内侧筋根处易产生折叠。
从图5a可以看到箭头所示的8个位置都是易产生折叠的。
为了减少折叠,在模锻件设计中把形状进行必要的简化,虽增加一点加工余量,但可以大大减少折叠。
如图5b所示易折叠的位置只有两个,如果形状再进一步简化如图5c所示那样,就可完全避免图5a中的各处折叠。
图5不同设计方案对产生折叠的影响
在图6a中两筋间距a小于筋高b,在箭头所示各处最易产生严重折叠。
如能把它简化为图6b那样就会消除这些折叠。
图6模具设计中必要的形状简化对产生折叠的影响
从上述实例中可以看出,在模具设计过程中,针对不同锻件或不同的部位采取必要的形状简化措施,对保证模锻件锻压成型过程中避免产生折叠缺陷有其重要意义。
3分模面的选择对产生折叠的影响
在普通开式模锻中,分模面选择的正确与否不仅会直接影响到模压的顺利完成,模具寿命的长短、生产效率的高低,而且对锻件的质量有重要影响。
下面仅从对产生折叠的影响来说明选择分模面时应考虑的因素。
图7列举同一个模锻件如选用三种不同分模面将产生不同折叠的结果:
图7a分模面选在腹板的中间,筋根与腹板面距分模面仅为h2,这样圆角处的金元非常容易参与外流,结果最易造成折叠。
图7b的分模面是设在腹板的端面上,这样使筋根与腹板面距分模面的距离为H,腹板的金属与图7a的相比,使圆角R较远离分模面,筋根圆角处的金属虽不像图7a的那样易于参入外流造成折叠,但还是难以避免出现折叠。
而像图7c那样把分模面改在筋顶,使成型条件从图7a和7b的压入成型改为反挤成型,当多余的金属排除是依次按顺序流动,所以完全可以避免图7a和7b中可能造成的折叠。
图7不同分模面对产生折叠的不同影响(P均相同,↓表示分模面)
图8列举工字形断面的制件选择不同分模面对产生折叠的影响。
图8a分模面是选在中间,它将在筋和腹板连接的四个圆角处易于产生折叠,而且断面上的金属流线也将发生穿流。
而图8b把分模面选在筋的顶部,使筋与腹板连接的圆角将不产生折叠。
图8工字形断面选择不同分模面对产生折叠的影晌
综上述举例可以看出,为了消除折叠,在模具设计时在兼顾其他因素的同时,应对分模面对产生折叠的影响给予充分的考虑。
4模锻件圆角半径的选择
模锻件的所有棱角为便于金属充填和尽量降低模具磨损都是设计成具有一定R的圆角来圆滑过渡。
所有模锻件的各个表面都分别是由内圆角、外圆角、水平内圆角和水平外圆角过渡连接的。
图9示出某一锻件的各种圆角。
其中内圆角处一般不易出现折叠,只有个别锻件可能出现筋顶包覆折叠。
外圆角处不易产生筋根折叠(穿筋折叠)。
在水平内圆角上一般也不出现折叠,只有在图示的下部a′—a′两处的水平内圆角与筋根和腹板的连接处,由于它位于锻件几何形状改变的转弯处,在此处两侧筋条的端头,两侧筋对腹板金属横向流动的阻碍突然消失,金属发生大量的横向流动,导致锻件不成型,随着变形的继续、不成型部位就由邻
近的腹板和筋上金属来充填,最后构成折叠。
水平外圆角d、e、f都是等于90°的弯角一般不易折叠,但是就d而言,由于它处于整个锻件的拐角处,纵向筋条和横向筋条上金属分别有纵和横流动(见图10所示)。
这两个不同方向的流动分力在此拐角处合成一个45°方向向外的合力,这个合力将是导致产生折叠的主要因素。
如果从设计加大此水平外圆角的半径,就可以削弱产生折叠的危害。
图9一般模锻件圆角的分类及各圆角对产生折叠的影响
图10弯角筋型折叠程序与角度的关系
在水平外圆角g、h、i中,它们都是小于90°的角,金属流动合力用下两式表示(参看图10):
当α=90°,合力P12=a2+b2
当α<90°,合力P22=a2+b2+2a•b•cosa
当α<90°,其余弦值都是大于0,∴P2>P1
这说明夹角小于90°时,此处金属更易外流,更加剧折叠的产生,而且随着夹角越小折叠越趋严重。
尤其像图9中g和h两处都位于锻件端角,对产生折叠更敏感。
对于这些地方在模具设计中都必须尽量采用较大的水平外圆角半径改善金属流动,以避免折叠。
下面着重讨论筋与腹板连接圆角,即简称外圆角的大小对产生折叠的影响,其影响分为两部分:
(1)在首次模压的开始阶段(图11)
金属充填型腔时,如R过小,变形金属就不是紧贴着圆角流入型腔,而且沿金属流动惯性方向先与圆角相对的型腔外壁接触,接着冲向筋顶,然后从筋顶返回向圆角外倒流,结果在圆角处形成折叠。
如果R选用得合适就可避免这种折叠。
(2)是在金属充满模腔以后排出多余金属时,R大小对折叠的影响
在普通开式模锻中,坯料量一般都要比模锻件所需的金属量多20%~15%,在锻至金属充满模型之后,还要有一部分多余的金属将以毛边的形式从锻件上流向毛边仓,这种金属的流动过程决不是像图12a所示的理想地流动。
实际上这些多余金属总是遵循最小阻力定律选其捷径流动,图12b就是金属真实流动过程。
这些多余金属量都是以欠压大的形式存在于锻件的腹板及与分模面相垂直的方向上,它们外流时穿过筋型直接奔向分模面,如果润滑不当或是变形速度快,将使锻件出现流纹不顺和穿筋折叠,这种穿筋折叠是整个折叠缺陷中的主要类型,图1就是这种折叠的典型照片。
为了避免这种折叠,模具设计时尽量选用大的外圆角半径。
在图13中同一个筋与腹板的连接处假定给它设置不同的外圆角半径,其中R1<R2。
当外圆角半径是R1时,阻碍腹板多余金属外流的摩擦面长度为a;当外圆角半径是R2时,其阻碍金属外流的摩擦面的长度为b。
b远大于α,因为阻力大小与摩擦面的大小成正比,R2所产生的阻力就远大于R1的。
这样它就迫使腹板上多余金属在远离锻件表面的金属内部向外流动,即使表面金属不参与外流,所以可大大减少穿筋折叠。
在同一模锻件上,不同位置的外圆角对产生折叠的影响也不同,在设计中选择的R值也应不同。
图14中R1、R2、R3分别是不同位置的外圆角半径。
就其位置而言R1处是最易折叠的。
R1的选择与筋宽B、筋高H或腹板厚h有关:
从筋宽上看,R1和R3是对应位置,因为R3处的筋厚度B3远大于B2。
厚的筋对腹板金属穿筋外流构成很大的障碍,所以R3处的金属就很难产生穿筋折叠,R3可比R1选择得小些。
从筋高上看,R1和R1-1是上下相邻的位置,但各处在不同的筋高位置上。
R1处的筋高是H,R1-1处的筋高是H1,H1因此R1-1就可以比R1小些。
从居于中间筋根的R2来看,在此处多余之金属将分别向两侧流动,根本构不成折叠,所以R2也可以小些。
在实践中,类似R1的外圆角半径一般是在H/2~H/3之间选取。
5模锻斜度的大小对折叠的影响
在普通开式模锻中所有离开分模面的几何形状在与分模面的连接面或棱线上,都做成具有一定斜度的斜角,称之为模锻斜度。
它不仅影响锻件的成型、模具的磨损和锻件的脱模,而且对产生折叠有一定的影响。
但其影响不象圆角半径那样敏感。
就图15所示筋型与分模面和腹板的连接采用的不同斜度而言。
当采用3°时,筋与腹板接触点的长度为α;如采用7°时,筋与腹板的连接长度为b。
b>α,就阻碍弯角处金属参与外流而言,7°的阻碍作用比3°的更强,故不易产生折叠:
所以从避免和减少折叠出发,应把模锻斜度尽量选择大些。
通常在生产中大量采用的是7°,还有个别的采用5°或l0°。
6适当形状模锻件的组合设计以消除折叠
有一些易产生折叠的锻件,根据其特定形状在设备能力允许的情况下,可通过双型或多型组合设计放在同一套模具上,以达到消除折叠的目的,图16a所示的模锻件,在单型模具设计时,横向压力中心线必须置于锻件中部,压力中心线左侧之金属将穿越模筋向外流动,这样就在筋根中的“R”处很难避免沿横筋全长上的穿筋折叠。
如果把它像图16b所示那样,在同一套模具上把两个锻件对应组合起来,构成一个新几何形状,这样外流金属都离开横筋向两外侧流动,完全可以避免图16a单型布置所产生的穿筋折叠。
组合锻件可在成品工序之前沿中心线切开。
图16模锻件型槽对称组合设计可避免折叠
7毛压和预压模的采用对消除折叠的作用
一些形状极为复杂和断面变化悬殊的制件,不仅很难选择毛料,也不易模压成型,而且变形极不均匀,也容易产生折叠缺陷。
这些制件用一套终压模锻压是不能完成的,必须采用预压模或者设计毛料模。
毛料模只具有模锻件的初步轮廓,按其模锻件的要求起分配金属的作用,其总的金属量比最终要求的一般多10%~8%。
预压模则具备模锻件的形状,只是筋型的高度比最终要求的矮些,腹板厚些,圆角大些,总的金属量比最终锻件要多8%~5%。
从图17中可以看出,从毛压—预压—终压,锻件是从粗到精逐渐充满模膛,使变形金属的流动过程变得比较平稳,变形也更加均匀,可以减少由于激烈变形产生折叠的机会。
图17设置毛料模、预压模、终压模避免折叠
8结束语
在合理的模具设计、工艺编制、生产操作的前提下,充分发挥操作者的技术水平,使各工序都控制得合理,就能减少模锻件的折叠或完全避免折叠,从而降低废品率,提高经济效益。