电阻炉温度控制系统设计毕业设计论文Word格式.docx
《电阻炉温度控制系统设计毕业设计论文Word格式.docx》由会员分享,可在线阅读,更多相关《电阻炉温度控制系统设计毕业设计论文Word格式.docx(61页珍藏版)》请在冰点文库上搜索。
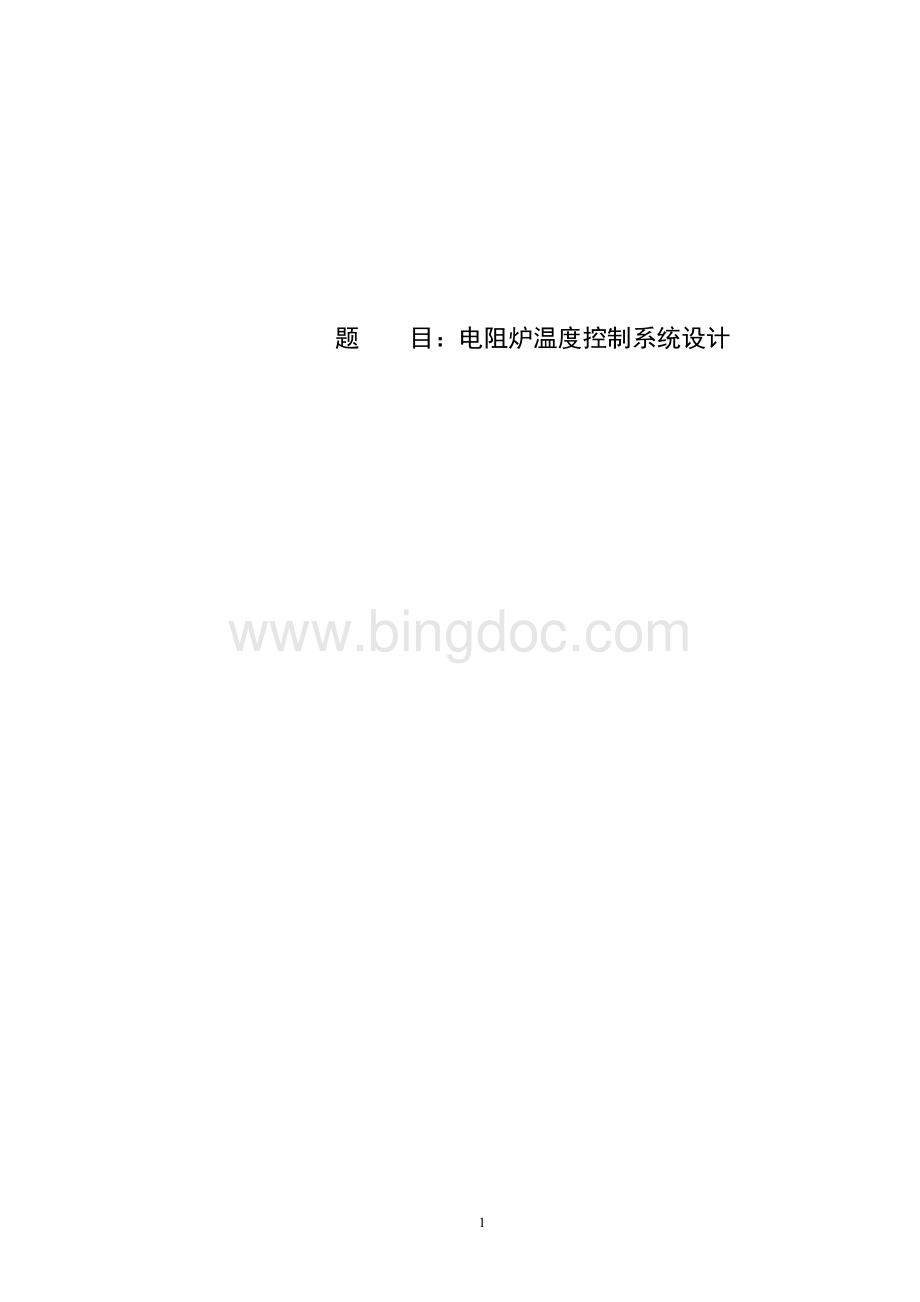
resistancefurnace;
characteristicsofthetestobject;
controlsystem;
regulator
内蒙古科技大学毕业设计说明书(毕业论文)
目录
IV
摘 要 I
Abstract II
目录 III
第一章引言 1
1.1电阻炉的概述 1
1.2电阻炉温度控制系统的应用与发展 2
第二章电阻炉的温度控制系统设计概述 4
2.1总体方案设计 4
2.2设计要求 4
2.3设计原理 4
第三章电阻炉温度特性的测试、记录及分析 6
3.1电阻炉温度特性测试 6
3.1.1对象特性测试中所用仪表 6
3.1.2对象特性测试原理 6
3.1.3进行温度特性曲线测试的仪器仪表的接线图 6
3.2温度特性曲线的记录与分析 8
3.2.1温度特性曲线的记录 8
3.2.2温度特性曲线试验结果的数据处理的方法 9
3.2.3温度特性曲线数据处理 14
第四章电阻炉温度控制系统的设计 17
4.1电阻炉温度控制系统的实现过程 17
4.1.1电阻炉温度控制系统的系统方框图及调节过程 17
4.1.2仪器仪表介绍 17
第五章电阻炉温度控制系统的参数整定及系统调试 31
5.1温度控制系统的实现线路 31
5.1.1系统的连线框图 31
5.1.2系统的连接线路及自动控制过程 31
5.2PID调节器及其参数的整定 31
5.2.1P、I、D各运算规律的作用 31
5.2.2PID参数的整定方法 35
5.2.3系统的PID整定结果及分析 38
总结 40
参考文献 42
附录A系统接线端子图 44
附录BPWM电路原理图 45
附录CPWM程序 46
致谢 52
第一章引言
1.1电阻炉的概述
工业炉是在工业生产中利用燃料燃烧或电能转化的热量将物料或工件加热的热工设备。
机械工业应用的工业炉有多种类型,在铸造车间,有熔炼金属的冲天炉、感应炉、电阻炉、电弧炉、真空炉、平炉、坩埚炉等;
在锻压车间,有对钢锭或钢坯进行锻前加热的各种加热炉,和锻后消除应力的热处理炉;
在金属热处理车间,有改善工件机械性能的各种退火、正火、淬火和回火的热处理炉;
在焊接车间,有焊件的焊前预热炉和焊后回火炉;
在粉末冶金车间有烧结金属的加热炉等。
自1973年能源危机以来,开发新能源和节约燃料引起世界各国的普遍关注。
工业炉是我国能源的一大用户,它所耗用的能源占全国总能耗的25%,热轧生产用各种加热炉的能耗约占全厂总能耗的60%以上。
因此,降低它们的能耗是很有意义的,实施自动控制是一种有效的途径[3]。
电阻炉是工业炉的一种,它是利用电流使炉内电热元件或加热介质发热,从而对工件或物料加热的工业炉。
电阻炉在机械工业中用于金属锻压前加热、金属热处理加热、钎焊、粉末冶金烧结、玻璃陶瓷焙烧和退火、低熔点金属熔化、砂型和油漆膜层的干燥等。
自从发现电流的热效应(即楞茨-焦耳定律)以后,电热法首先用于家用电器,后来又用于实验室小电炉。
随着镍铬合金的发明,到20世纪
20年代,电阻炉已在工业上得到广泛应用。
工业上用的电阻炉一般由电热元件、砌体、金属壳体、炉门、炉用机械和电气控制系统等组成。
加热功率从不足一千瓦到数千千瓦。
工作温度在650℃以下的为低温炉;
650~1000℃为中温
炉;
1000℃以上为高温炉。
在高温和中温炉内
主要以辐射方式加热。
在低温炉内则以对流传热方式加热,电热元件装在风道内,通过风机强迫炉内气体循环流动,以加强对流传热。
电阻炉有室式、井式、台车式、推杆式、步进式、马弗式和隧道式等类型。
可控气氛炉、真空炉、流动粒子炉等也都是电阻炉。
与其它的工业炉相比,电阻炉具有发热部分简单,对炉料的种类限制少,炉
56
温控制精度高,容易实现在真空或控制气氛中加热等特点。
因此电阻炉广泛应用于冶金、机械、材料等行业,是发展最早,品种规格最多,需要量最大的一类工业炉。
电阻炉按其加热方式不同,可以分为间接电热和直接电热两大类。
前者依靠电流通过炉内的电热体或导电液体产生热量,再经过一定的传热过程将热量传给被加热的物体。
目前大多数的电阻炉都属于这一类。
后者是电流直接通过被加热的物料,依靠物料本身的电阻发热。
间接电热电阻炉的电热原理:
电流通过炉内的专门电阻发热即电热体所产生的热量,借热辐射、对流和传导将热量传递给被处理的物料,这种电炉称为间接电热电阻炉。
其特点是:
采用不同材料的电热体可在炉内达到不同的最高工作温度;
采用不同的电热体安装和布置方式,可在炉内得到各种所需的温度分布以及做成各种形式和大小的炉子。
所以间接电热电阻炉是工业生产和科研中应用最广泛的一种炉子。
1.2电阻炉温度控制系统的应用与发展
现在所说的电阻炉温度控制系统,多指采用电脑或微处理器进行智能控制的系统,在系统的发展史上,称为第三代控制系统,以PLC和DCS为代表,从70年代开始应用以来,在冶金、电力、石油、化工、轻工等工业过程控制中获得迅猛的发展。
70年代中期,由于设备大型化、工艺流程连续性要求高、要控制的工艺参数增多,而且条件苛刻,要求显示操作集中等,使已经普及的电动单元组合仪表不能完全满足要求。
在此情况下,在原来采用中小规模集成电路而形成的直接数字控制器(DDC)的自控和计算机技术的基础上,开发出了以集中显示操作、分散控制为特征的集散控制系统
(DCS)。
因而将集散控制系统(DCS)应用到电阻炉温度的控制上,可以提高控制精度,可靠性和安全性。
从90年代开始,陆续出现了现场总线电阻炉温度控制系统、基于
PC的电阻炉温度控制系统等。
目前,由于控制的目的、工艺要求、精度要求的不同,可以采用不同的控制方式。
控制方式的使用范围也不同:
PLC适用于离散过程控制,如开关、顺序动作执行等场所,随着PLC的功能越来越强大,PLC也开始进入过程自动化领域。
DCS系统则以
模拟量反馈控制为主,辅以开关量的顺序控制和模拟量开关量混合型的批量控制,它们可以覆盖炼油、石化、化工、冶金、电力、轻工及市政工程等大部分行业。
而现场总线的突出特点在于它把集中与分散相结合的DCS集散控制结构,变成新型的全分布式结构,把控制功能彻底下放到现场,依靠现场智能设备本身实现基本控制功能。
在本设计中以电阻炉为研究对象,利用实验室现有的管式电阻炉和一系列的数字化仪表来完成电阻炉的温度控制系统。
通过改变调节器的比例带、积分时间和微分时间来实现对电阻炉的温度控制。
当系统处于平衡状态时,炉温将稳定在给定值上,从而实现了电阻炉的恒温控制。
该方法简单,易操作,控制精度高,可靠性强。
同时这种控制方案可以根据不同的研究对象完成不同的控制要求。
第二章电阻炉的温度控制系统设计概述
2.1总体方案设计
自动控制系统设计首先要研究被控对象,即对被控对象进行测试。
测试的方法有:
时域测试法(这里指飞升曲线法)、频域测试法、统计法等。
这里采用飞升曲线法。
本设计的研究对象是实验室现有的管式电阻炉,因此对它进行性能实验测试。
设计中取的是对象的飞升曲线,所以实验中让对象(电阻炉)在某一稳态下稳定一段时间后,快速的改变它的输入量,使对象达到另一稳定状态,从而求得对象在阶跃函数时的飞升曲线。
测得对象特性后,根据要求选择一个合适的控制系统。
因为在一般连续生产过程中,单回路调节系统可以满足大多数的控制要求,所以这里采用单回路调节系统。
单回路调节系统一般是指在一个调节对象上用一个调节器来保持一个参数恒定,而调节器只接受一个测量信号,其输出也只控制一个执行机构。
想要实现电阻炉的温度控制,控制方法有很多,例如利用常温仪表,数字仪表,
PLC等,它们都可以实现自动控制,但由于数字仪表即比常温仪表操作简单,控制精度高,又比PLC经济实用,故本设计采用数字仪表足已满足我们的控制要求。
在确定了控制方法后还要先根据经验值定一组最初的调节器参数,然后再结合实验数据求得的调节器参数,调节整定系统,使控制效果达到最佳,从而确定最后的调节器参数,最终实现电阻炉的温度控制。
2.2设计要求
针对电阻炉组成一个简单实用的恒温控制系统,可以通过设置参数使其温度在
0-1000摄氏度内得到有效的控制,并且控制精度达到预想效果,控制时间也可以随意改变。
2.3设计原理
以电阻炉温度为研究对象,采用数字PID控制器对电阻炉温度进行控制,通过调节比例带、积分时间、微分时间来调节控制效果,同时针对不同温度段所表现出来的不同
热性能,采用全功率或比例控制加快升温过程,再进行PID算法结合积分分离或积分削弱算法控制稳定过程的方案。
使电阻炉温度控制达到超调量小、稳定精度高的优良控制效果。
第三章电阻炉温度特性的测试、记录及分析
3.1电阻炉温度特性测试
一般研究调节对象特性的方法有两种。
对于简单的对象或系统各环节的特性,可以通过分析过程的机理、物料或能量平衡关系求得数学模型,即对象动态特性的微分方程式,这种方法称为分析法。
但是,复杂对象的微分方程式很难建立,也不容易求解。
所以,另一种方法是通过实验测定,对取得数据进行加工整理而求得对象的微分方程式或传递函数,这种方法称为实验测定法。
目前用来测定对象动态特性的实验方法主要有三种:
测定动态特性的时域方法、测定动态特性的频域方法、测定动态特性的统计方法。
这里仅对本次设计用到的是时域方法加以介绍。
时域方法主要是求对象的飞升曲线或方波响应曲线,如输入量做阶跃变化,测绘对象输出量随时间变化曲线就得到飞升特性。
如果将输入量作一个脉冲方波变化,测出对象输出量随时间的变化曲线就得到脉冲方波响应曲线。
这些方法都不需要特殊的信号发生器,在很多情况下可以利用调节系统中原有的仪器设备完成,方法简单,测试工作量小,故应用甚广。
此法缺点是测试精度不高且对生产有一定影响。
3.1.1对象特性测试中所用仪表
电阻丝高温炉,自耦变压器,无纸记录仪,S型热电偶
3.1.2对象特性测试原理
在实验中,用调压变压器将220V的交流电转换成不同伏值的电压,通过这些电压为管式电阻炉提供电源,将热电偶所测的电阻炉在不同伏值供电电压下的毫伏信号接入无纸记录仪进而实时地绘制电阻炉的温度特性曲线。
3.1.3进行温度特性曲线测试的仪器仪表的接线图
下面我们将进行温度特性测试原理图和接线图的绘制。
调压器
电阻炉
T
220
交流
S型热电偶
无纸记录仪
图3.1电阻炉的温度性能测试原理图
电阻丝
12热电偶输出端
220V
自耦变压器
图3.2电阻炉的温度性能测试接线图
由图3.2可以看出,我们是将自耦变压器原边接民用电源,其副边的输出接至管式电阻炉的电源输入端,从而使电阻炉开始加热,我们利用S型的铂铑-铂热电偶作为传感器来测试炉温,其热电偶的输出端1,2应接至无纸记录仪的输入端,由无纸记录仪的USB接口读取曲线图,再利用无纸记录仪U盘数据存储分析软件分析曲线图。
我们按照图3.2将各仪器仪表的引脚相互连接,这就组成了测试温度特性的电路。
我们通过调节自耦变压器的给定电压,使电阻炉的温度变化并绘出温度升高或降低的曲线图。
3.2温度特性曲线的记录与分析
在电阻炉温度特性曲线的测试中,我们通过选择不同的给定电压送入电阻炉,从而使电阻炉的温度由一个稳态阶跃到另一个稳定状态,也相当于给电阻炉一个阶跃信号,来得到温度的阶跃响应曲线。
3.2.1温度特性曲线的记录
在开始实验时,我们选定的初始给定值是30V,待温度上升到某一稳定值时,我们将给定值改变为70V,相当于给该系统一个阶跃信号,从而使温度的变化曲线出现阶跃响应。
为了使我们的设计达到一定的要求,应多给几个阶跃信号,使温度比较高时,也能很好的进行自动控制。
因而,我们又将给定值设为70V,温度升高到稳定状态时,再给一个阶跃信号,即将变压器的电压调至110V。
图3.3阶跃响应曲线
图3.3为电阻炉温度特性曲线截取图。
在响应曲线测定后,为了分析和设计控制系统,需要将响应曲线转化为传递函数。
在转化过程中,首要问题是选定模型的结构。
对于采用PID控制的闭环控制系统,并不要求非常准确的被控对象模型。
因此在满足精度要求的情况下,常采用低阶传递函数来拟和被控对象。
3.2.2温度特性曲线试验结果的数据处理的方法
在描绘生产过程的动态特性时,常用微分方程式或传递函数的形式表达。
如何将实验所获得的各种不同对象的飞升曲线进行处理,以便用一些简单的典型微分方程或传递函数来近似表达,既适合工程应用,又有足够的精度,即这里所指的数据处理。
(1)由飞升曲线确定有纯滞后的一阶环节的参数
图3.4电阻炉的飞升曲线
有纯滞后的S形飞升曲线,如图3.4所示。
在变化速度最快处作一切线,
它的斜率m就是最快的速度
dydtm
,并从时间轴的交点得出滞后时间 。
同时
记下输入阶跃变化量x和y的最终变量y 。
然后用下列式子求K及T:
y
K ;
(3-1)
x
T y
dy
dtm
(3-2)
这种处理方法极为简单但准确性不高,再介绍一种比较准确的方法:
求稳态放大系数K的式子不变,在计算时间常数T及纯滞后 时,将yt
曲线修改成无因次的飞升曲线y t为
y t yt ytKx y
(3-3)
对于有滞后的一阶非周期环节来说,在阶跃作用下的解为
y t 0
t ;
y t
t
1eT
t (3-4)
t2为了确定T及 的值,在无因次飞升曲线上选取 y t的两个坐标值,现
选择t1及t2如下:
y t1 1
t1 t2
eT;
y t2 1eT
(3-5)
其中,t2>
t1>
τ,对上式联立求解可得
t2ln1
y t1
t1ln1
y t2
;
ln1 y t1
T t1
ln1 y t2
t2
o (3-6)
ln1
可以看出,由t1,t2及对应飞升曲线上的两个值y t 及y t 求得T及 。
1 2
若选择y t
0.39,y t
2
0.63则可得
2t1
t2;
T
2t t
(3-7)
对于计算结果,可在
t3≤τ
t4 0.8T
t5 2T
y t3 0
y t4 0.55
y t5 0.87
这几个时间上,对飞升曲线进行校验。
(2)由飞升曲线确定二阶环节的参数
响应曲线测定后,为了分析和设计控制系统,需要将响应曲线转化为传递函数。
本设计采用二阶系统的S形飞升曲线的分析方法对实验结果进行处理。
下面介绍一下二阶系统的S形飞升曲线的分析方法,并用该方法对实验测得的电阻炉温度特性曲线进行分析。
对于S形的实验飞升曲线,规定其传递函数按下式:
Gs
TTs2
K
T Ts
(3-8)
或
12 1 2
Gs K
es (3-9)
T2s2 2Ts1
来近似,前者相当于过阻尼的二阶环节(传递函数的分母有两个实根
1及1,后者
T1 T2
为阻尼系数为1的有纯滞后的二阶环节。
在生产实际中,多数对象的飞升曲线都是过阻尼的,因此该方法适用于大批的工业对象。
对于式(3-8),在零初始条件下,当输入xt作阶跃变化,阶跃变量为x时,它
的解为
yt Kx1
T1
eT1
T2
eT2
(3-10)
用无因式表示:
yt T t T t
y t 1
Kx T1
1 eT1
2
T1T2
eT2
(3-11)
由式(3-11)可知,为了求y t的值,应先确定两个时间常数T1和T2,而这就要建立两个方程。
在式(3-11)中引入时间无因次量
t t;
T1;
T T2
(3-12)
2T 1 2T 2 2T
其中2T=T1+T2,则可化为:
t t
T1
eT1
T2
(3-13)
注意:
1 T1
T2;
T2,可见式(3-13)表达了y t ,t,和
1 2 2 2 2 2
三者之间的关系。
令y t
0.7,则在式(3-13)中只剩t,和T1
T2两个参量。
因
T T T1 T2,故T T 1。
当T T
在0~1之间取值时,可算出与之