塑料模复习资料8Word文件下载.docx
《塑料模复习资料8Word文件下载.docx》由会员分享,可在线阅读,更多相关《塑料模复习资料8Word文件下载.docx(16页珍藏版)》请在冰点文库上搜索。
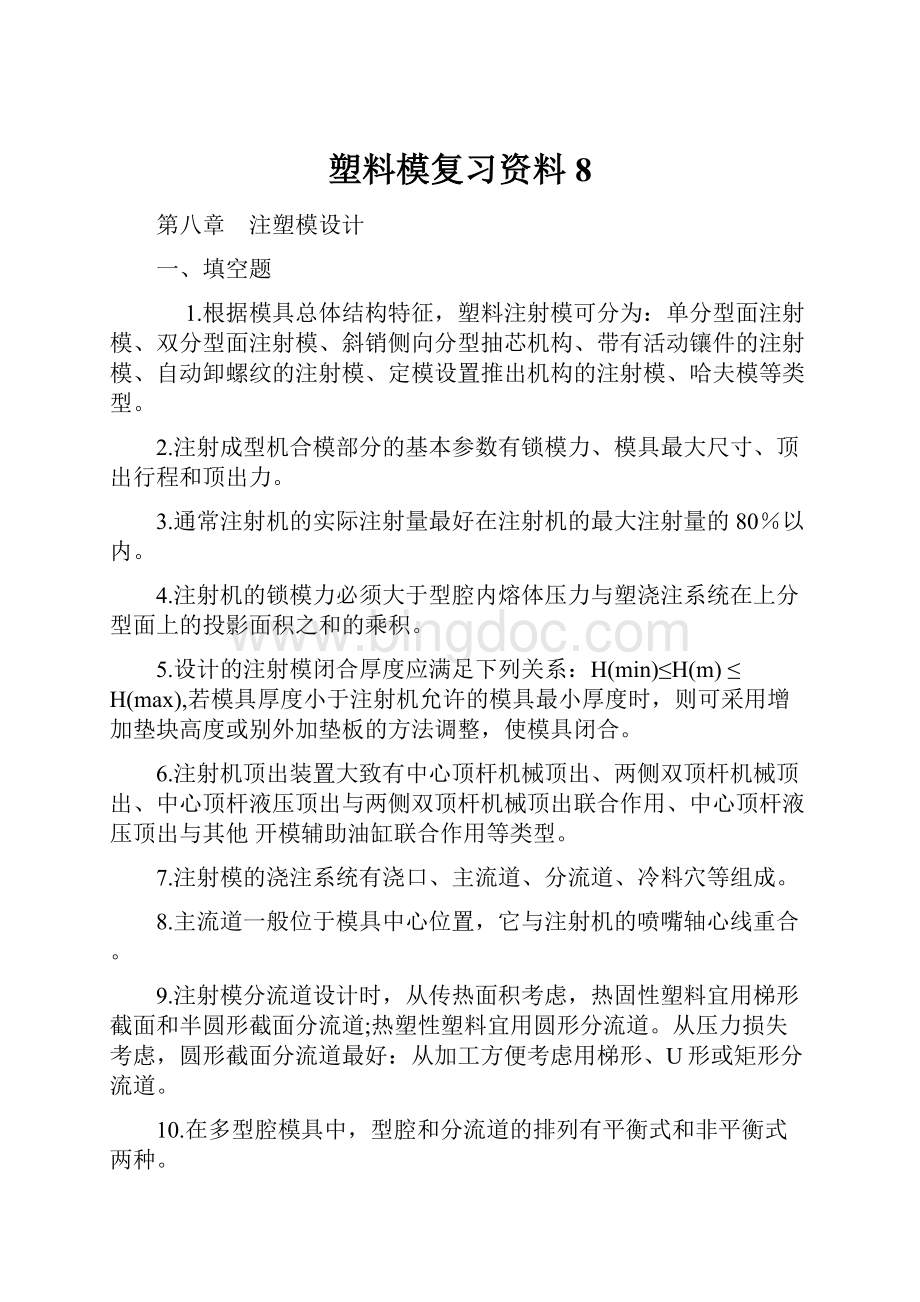
20.在实际生产中斜导柱斜角a一般取15°
~20°
,最大不超过25°
。
21.为了保证斜导柱伸出端准确可靠地进入滑块斜孔,则滑块在完成抽芯后必须停留在一定位置上,为此滑块需有定位装置。
22.在塑件注射成型过程中,侧型芯在抽芯方向受到型腔内塑料熔体较大的推力作用,为了保护斜导柱和保证塑件精度而使用楔紧块,楔紧块的斜角a′一般为a+(2~3)°
23.在斜导柱分型及抽芯机构中,可能会产生干涉现象,为了避免这一现象发生,应尽量避免推杆的位置与侧型芯在闭模状态下在水平方向上的投影重合或推杆或推管推出距离大于侧型芯底面。
24.斜导柱分型及抽芯机构按斜导柱大型芯设置在动、定模的位置不同有
(1)斜导柱在定模,滑块在动模
(2)斜导柱在动模,滑块在定模(3)斜导柱、滑块在定模(4)斜导柱、滑块在动模四种结构形式。
25.斜导柱在定模,滑块在动模,设计这种结构时,必须避免干涉现象。
26.斜导柱与滑块都设置在定模上,为完成抽芯和脱模工作,需采用定距分型拉紧机构。
27.斜导柱与滑块都设置在动模上,这种结构可通过推出机构或
定距分型机构来实现斜导柱与滑块的相对运动,由于滑块可以不脱离斜导柱,所以可以不设置滑块定位装置。
28.设计注射模的推出机构时,推杆要尽量短,一般应将塑件推至高于型芯10ms左右。
注射成型时,推杆端端面一般高出所在
型芯或型腔表面0.05~0.1mm.
29.对于局部是圆筒形或中心带孔的圆筒形的塑件,可用推管推出机构进行脱模。
30.对薄壁容器、壳体零件、罩子以及不允许有推杆痕迹的塑件,可采用推出机构、这种机构不另设复位机构。
31.推杆、推管推出机构有时和侧型芯发生干涉,当加大斜导柱斜角还不能避免干涉时,就要增设机构,它有楔形—三角滑块先行复位机构、连杆先行复位机构、弹簧先行复位机构等几种形式。
32.设计注射模时,要求塑件留在动模上,但由于塑件结构形状的关系,塑件留在定模或动、定模上均有可能时,就须设双推出机构。
33.注射过程中热固性塑料的流动性很好,所以分型面时可采用减少分型面的接触面积,改善型腔周围的贴合状况。
34.在热固性塑料系统中,主流道设计得较小,分流道布置形式一般选择平衡式,分流道开设在动模分型面上,排气槽位置开设在浇口对面的分型面上。
二判断题(正确的画√,错误的画×
)
1.注射机的最大注射量是以模塑聚苯乙烯为标准而规定的,由于各种塑料的密度和压缩比不同,因而实际最大注射量是随塑料的不同而不同的。
(√)
2.注射机的最大注射压力应梢大于塑件成型所需的压力。
所以要对注射机的注射压力进行校核。
(√)
3.多型腔注射模各腔的成型条件是一样的,熔体到充满各腔的时间是相同的,所以适合成型各种精度的塑件,以满足生产率的要求。
(×
)
4.注射机的最大开模行程等于注射机允许的模具最大厚度。
5.各种型号的注射机最大开模行程均与模具厚度无关。
6.同一台液压合模机构的注射机对于单分型模具和双分型模具。
其开模行程是相同的。
(√)
7.分流道设计时,究竟采用哪一种横截面的分流道,即应考虑各种塑料注射成型的需要,又要考虑到制造的难易程度。
8.在对注塑模的型腔与分流道布置时,最好使塑件和分流道在分型面上总投影面积的几何中心和琐模力的中心相重合。
9.为了减少分流道对熔体流动的阻力,分流道表面必须修的光滑。
10.浇口的主要作用之一是防止熔体倒流,便于凝聊和塑件分离。
11.中心浇口适用圆筒形,圆环形,或中心带孔的塑件成型。
属于这类浇口有盘形,环形,爪形和轮辐式等浇口。
12.侧浇口包括扇形浇口和薄片式浇口,扇形浇口常用来成型宽度较大薄片状塑件;
薄片式浇口常用来成型大面积薄板塑件
13.点浇口对于注塑流动性差和热敏性塑料及平薄易变形和形状复杂的塑件是很有利的。
(×
14潜伏式浇口是点浇口变化而来的,浇口因常设在塑件侧面的较隐蔽的部位而不影响塑件外观。
15.浇口饿截面尺寸越小越好。
16.浇口的位置应开设在塑件截面最厚处,以利于熔体填充及补料。
17.浇口位置应使熔体的流程最短,流向变化最小。
18.浇口数量越多越好,因为这样可能使熔体很快充满型腔。
19.注射模具设计时,应适当选择浇口位置,尽量减少注射时熔体沿流动方向产生的定向作用,以免导致塑件出现应力开裂和收缩具有的方向性。
20.大多数情况下利用分型面或模具零件配合间隙自然排气。
当需开设排气槽时。
通常开设在分型面的凹槽一侧开设排气槽。
21.无流道塑料注射模适用于各种塑料的注射成型。
22.绝热流道和热流道注射模均属于无流道注射模。
23.对于不带孔的壳体塑件,脱模时的抽拔力仅指塑件在冷凝收缩时对型心的包紧力而引起的抽拔阻力和机械动摩擦力。
24.若注射压力小,保压时间短,则抽拔力较大。
25.在斜导柱抽芯机构中,采用复位杆复位可能产生干扰。
尽量避免推杆与侧型芯的水平投影重合或者使推杆推出的距离小于侧型芯的底面均可防止干扰。
26塑件留在动模上可以使模具的推出机构简单,故应尽量使塑件留在动模上。
27.脱模斜度小、脱模阻力大的管形和箱形塑件,应尽量选用推杆推出。
28.为了确保塑件质量与顺利脱模,推杆数量应尽量地多。
29.推板推出时,由于推板与塑件接触的部位,需要有一定的硬度和表面粗糙度要求,为防止整体淬火引起的变形,常用镶嵌的组合结构。
30.推出机构中的双推出机构,即是推杆与推块同时推出塑件的推出机构。
31.顺序推出机构即为顺序推出机构。
32.二级推出机构即为顺序推出机构。
33.通常推出元件为推杆、推管、推块时,需增设先复位机构。
34.XS-ZY-125注射机,可用来注射成型热固性塑料。
35.设计热固性塑料注射模的浇注系统时,主流道直径应尽量小;
分流道取平衡式分布且开在动模分型面上;
浇注位置及形状与热塑性注射模相同,仅浇口厚度厚些。
36.由于热固性塑料在固化过程中会产生低分子挥发性气体,所以,在热固性塑料注射成型时,排气是十分重要的,其排气口常设在浇口附近。
三、选择题
1.注射成型时,型腔内熔体压力大小及其分布与很多因素有关。
在工程实际中用来C
校核。
A、注射机柱塞或螺杆加于塑料上的压力
B、锁模力
C、模内平均压力
2.采用多型腔注射模时,需根据选定的注射机参数来确定型腔数。
主要按注射的
A
来确定。
A、最大的注射量
B、锁模力
C、公称塑化量
3.分流道设计时,热塑性塑料用圆形截面分流道,直径一般取d=2~12㎜,流动性很好的
,可取较小截面,分流道很短时,可取2㎜;
对流动性差的
C
取较大截面。
A尼龙
B聚砜
C聚丙烯
D聚碳酸酯
4.采用直接浇口的单型腔模具,适用于成型 B 塑件,不宜用来成型
的塑件。
A、平薄易变形 B、壳形 C、箱形
5.直接浇口适用于各种塑料的注射成型,尤其对 A 有利。
A、结晶型或易产生内应力的塑料 B、热敏性塑料 C、流动性差的塑料
6.通过浇口进入型腔的熔料应呈 B 关进入腔内。
A、紊流 B、层流
C、涡流
7.熔体通过点浇口时,有很高的剪切速率,同时由于摩擦作用,提高了熔体的温度。
因此,对A
的塑料来说,是理想的浇口。
A、表观粘度对速度变化敏感
B、粘度较低C、粘度大
8.护耳浇口专门用于透明度高和要求无内应力的塑件,它主要用于ABD
等流动性差和对应力较敏感的塑料塑件。
A、ABS
B、有机玻璃
C、尼龙
D、聚碳酸酯和硬聚氯乙烯
9.斜导柱分型面与抽芯机构中C
的结构,需有定距分型机构。
A、斜导柱在动模,滑块在定模
B、斜导柱在定模,滑块在动模
C、斜导柱与滑块同在定模
D、斜导柱与滑块同在动模
10.带推杆的倒锥形冷料穴和圆形冷料穴适用于
B
塑料的成型。
A、硬聚氯乙烯
B、弹性较好的
C、结晶型
11.简单推出机构中的推杆推出机构,不宜用于BCD
塑件的模具。
A、柱形
B、管形C、箱形 D、形状复杂而脱模阻力大
12.推管推出机构对软质塑料如聚乙烯、软聚氯乙烯等不宜用单一的推管脱模,特别对薄壁深筒形塑件,需用 C 推出机构。
A、推板 B、顺序 C、联合 D、二级
13.大型深腔容器,特别是软质塑料成型时,用推件推出,应设
B 装置。
A、先手复位 B、引气 C、排气
14.绝热流道利用 C 保持流道中心部位的塑料处于熔融状态。
A、空气 B、金属 C、塑料
D、电热圈
15.热流道板用于A
结构的热流道注射模。
A、多型腔
B、单型腔
C、单分型面
D、双分型面
16.采用阀式浇口热流道是为了防止熔料的D
现象。
A、高温
B、低温
C、低压
D、流涎
17.内加热式热流道的特点是A
。
A、热量损失小
B、热量损失大
C、加热温度高
D、加热温度低
18.将注射模具分为单分型面注射模、双分型面注射模等是按
C
分类的。
A、按所使用的注射机的形式
B、按成型材料
C、按注射模的总体结构特征
D、按模具的型腔数目
19.卧式注射机注射系统与合模锁模系统的轴线A
布置。
A、都水平
B、都垂直
C、注射机注射系统水平,合模锁模系统垂直
D、注射机系统垂直,合模锁模系统水平
20.注射机XS-ZY-125中的″125″代表
D
A、最大注射压力
B锁模力
C、喷嘴温度
D、最大注射量
21.注射主流道始端的凹球半径比注射机喷嘴头部球面半径 B 。
A、相等
B、大
C、小
D.随意
四、名词解释
分流道、冷料穴、流动比、无流道凝料浇注系统、热流道注射模、侧向分型抽芯机构、抽芯距、起始抽芯力、定距分型拉紧机构、联合推出机构、二级推出机构、双推出机构
分流道--指介于主流道和浇口之间的一段通道,它是熔融塑料由主流道注入型腔的过度通道,能使塑料的流向得到平稳的转换。
冷料穴――指流道中的一些盲孔或盲槽,其作用是储藏注射间隔期间产生的冷料头,以防止冷料进入型腔且影响塑件质量,甚至堵塞浇口而影响注射成型。
流动比――是指熔体流程长度与流道厚度的比值。
无流道浇注系统――特点是模具的主流道和分流道都很粗大,因此在整个注射过程中,靠近流道壁部的塑料容易散热而冷凝,形成冷硬层,它起着绝热作用,而流道中心部位的塑料仍保持熔融状态,从而使熔融塑料能通过它顺利地进入型腔,达到连续注射而无需取出流道凝料的要求。
热流道注射模――热流道注射模不受塑件盛开周期的限制,停机后也不需要打开流道板取出流道凝料,在开机后只需要接通电源重新加热流道达到所需温度即可。
侧向分型抽芯机构――当塑件上具有内外侧孔或内、外侧凹时,塑件不能直接从模具中脱出。
此时需将成型塑件侧孔或侧凹等的模具零件做成活动的,这种零件称为侧抽芯,当塑件脱模前先将侧型芯从塑件上抽出,然后再从模具中推出塑件。
完成侧型芯抽出和复位的机构就叫做侧向分型与抽芯机构。
抽芯距――是指侧型芯从成型位置推至不妨碍塑件推出时的位置所需的距离。
起始抽芯力――是将侧型芯从塑件中抽出时所需的最初瞬间的最大抽出力。
定距分型拉紧机构――模具中用来保证模具各个分型面按一定的顺序打开的机构叫做定距分型拉紧机构。
联合推出机构――实际生产中,有些塑件结构十分复杂,采用单一的推出机构容易损坏推坏塑件或者根本 推不出来,这时就往往要采用两种以上的推出方式进行推出,这就是联合推出机构。
二级推出机构――是一种在模具中实现先后再次推出动作,且这再次动作在时间上有特定顺序的推出机构。
双推出机构――在动、定模上都设置推出机构的叫做双推出机构。
五、问答题
1.模具设计时,对所设计模具与所选用的注射机必须进行哪些方面的校核(从工艺参数、合模部分参数方面来考虑)?
答 应对注射机的最大注射量、注射压力、锁模力进行校核以及对装模部分相关尺寸、开模行程、顶出装置等进行校核。
2.浇注系统的作用是什么?
注射模浇注系统由哪些部分组成?
答 浇注系统的作用是塑料熔体平稳且有顺序的填充到型腔中,并在填充和凝固过程中把注射压力充分传递到各个部位,以获得组织紧密、外形清晰的塑件。
注射模浇注系统由主流道、分流道、浇口、冷料穴。
3.分流道设计时应注意哪些问题?
答 分流道的设计应能使塑料的流向得到平稳的转换并尽快地充满型腔,流动中温度降低尽可能低,同时应能将塑料熔体均衡的分配到各个型腔。
设计时应注意a分流道的截面尺寸视塑件的大小和壁厚、塑料和品种、注射速率和分流道长度等因素而定b分流道的表面不必很光滑,其表面粗糙度为1.6um即可,这样流道内料流的外层流速较低,容易冷却而形成固定表皮层,有利于流道的保温。
4.注射模浇口的作用是什么?
有哪些类型?
各自用在哪些场合?
答 浇口的作用:
熔料经狭小的浇口增速、增温,利于填充型腔。
注射保压补缩后浇口处首先凝固封闭型腔,减小塑件的变形和破裂,狭小浇口便于浇道凝料下塑件分离,修整方便。
浇口类型:
直接浇口 直接浇口广泛应用于单型腔模具
侧浇口 一般开设在分型面上,适合于一模多腔,浇口去除方便,但压力损失大、壳形件排气不便、易产生熔接痕。
圆盘浇口 此类型浇口适用同心。
且尺寸的要求严格。
及不容许有熔接痕生成的塑料制品。
轮辐式浇口 轮辐浇口双称为四点浇口或是十字浇口。
此种浇口适用于管状塑料制品,且浇口容易去除和节省材料。
薄膜浇口 薄膜浇口适用于既平坦又大面积、且翘曲要保持最小的设计。
护耳浇口 通常应用于平板状且薄的成型品,以降低型腔内的剪应力
点浇口 适合于多型腔模。
塑件外观要求较高时采用
环形浇口 用于型芯装在两侧的管状塑件
扇形浇口 应用于多型腔模,进料边宽度较大的薄片状塑件
针点浇口 应用于成型中小型塑件的一模多腔模具中,也可用于单型腔模
5.浇口位置选择的原则是什么?
答 浇口的位置的选择应注意:
(1)避免引起熔体破裂
(2)浇口的位置应尽可能避免熔接痕的产生。
(3)有利于熔体流动和补缩
(4)有利于型腔内气体排出
(5)防止料流将型芯或嵌件挤压变形
(6)保证流动比在允许范围内
6.为什么要设排气系统?
常见的排气方式有哪些?
答 在注射成型过程中,模具内除了型腔和浇注系统中有原有的空气外,还有塑料受热或凝固产生的低分子挥发气体,这些气体若不能被熔融塑料顺利的排除型腔,则可能因填充时气体被压缩而产生高温,引起塑件局部碳化烧焦,或是塑件产生气泡,或是塑料熔接不良而引起塑件强度的降低,甚至阻碍塑料填充等。
为了使这些气体从型腔中及时排出,在设计模具时必须要考虑排气的问题。
常见的排气方式有开设排气槽排气和利用模具分型面或模具零件的配合间隙自然排气等。
7.无流道模有哪些特点?
它对所成型的塑料有些什么要求?
答 无流道注射模特点:
压力损失小,可低压注射,同时有利于压力传递、提高塑件质量
有利于实现自动化生产,提高生产率、降低成本
基本上实现了无废料加工,节约塑料原料
模具结构复杂、制造成本高,适用于质量要求高、生产批量大的塑件成型。
无流道注射模对塑料的要求
对温度不敏感,低温下易流动成型
对压力敏感,但在低压下易流动
热变形温度较高,可迅速从模具内顶出
热传导性能好
比热容小,塑料既易熔融又易凝固
8.绝热流道注射模有何特点?
答模具的主流道和分流道都粗大,模具流道部分不加热,主要靠料流的冷硬层绝热保持流道内塑料的熔融状态。
9.如何确定塑件的抽芯距?
答一般抽芯距等于塑件侧孔深度或凸台高度另加2-3mm安全距离,即:
S(抽)=h+(2-3)mm
当塑件结构比较特殊时,如圆形线圈骨架的抽芯距
S(抽)=S1+(2-3)mm
=
六、综合题
(1)
1.
模具是哪种类型?
答案:
传递模。
2.
模具采用哪种浇口?
侧浇口。
3.
件9的作用是什么?
定位作用。
4.
写出该模具工作原理?
成型后先从模具上取下移动式料腔,然后从压机中取出模具,用撬棒分开Ⅰ—Ⅰ面,拿走上模板1,拔出定位杆9,再用撬棒分开Ⅱ—Ⅱ面,制品连同浇道脱离模具,剪除浇口后得到制品。
依照推件板、嵌件、定位杆和上模板的顺序重新装模,放上料腔,倒入塑料,即可进行下一模的成型。
(2)
模具有几个分型面?
两个分型面。
模具采用什么推出机构?
斜滑块。
为使浇注系统自动脱落,应补设什么机构?
拉料杆。
件17的作用是什么?
复位作用。
5.
叙述模具工作原理。
开模时,在弹簧11作用下模具由Ⅰ—Ⅰ分型面分型,浇口凝料由该分型面内取出。
当定距拉杆10拉住凹模固定板2后,Ⅱ—Ⅱ分型面分型,制品随动模后退,点浇口拉断。
推出时,斜滑块23沿主型芯T形导轨向内移动与制品脱离。
闭模时,由复位杆18带动斜滑块复位。
主型芯6采用了防转定位措施,以确保与斜滑块的正确装配。