minitab部分因子设计响应面设计参数设计Word格式文档下载.docx
《minitab部分因子设计响应面设计参数设计Word格式文档下载.docx》由会员分享,可在线阅读,更多相关《minitab部分因子设计响应面设计参数设计Word格式文档下载.docx(19页珍藏版)》请在冰点文库上搜索。
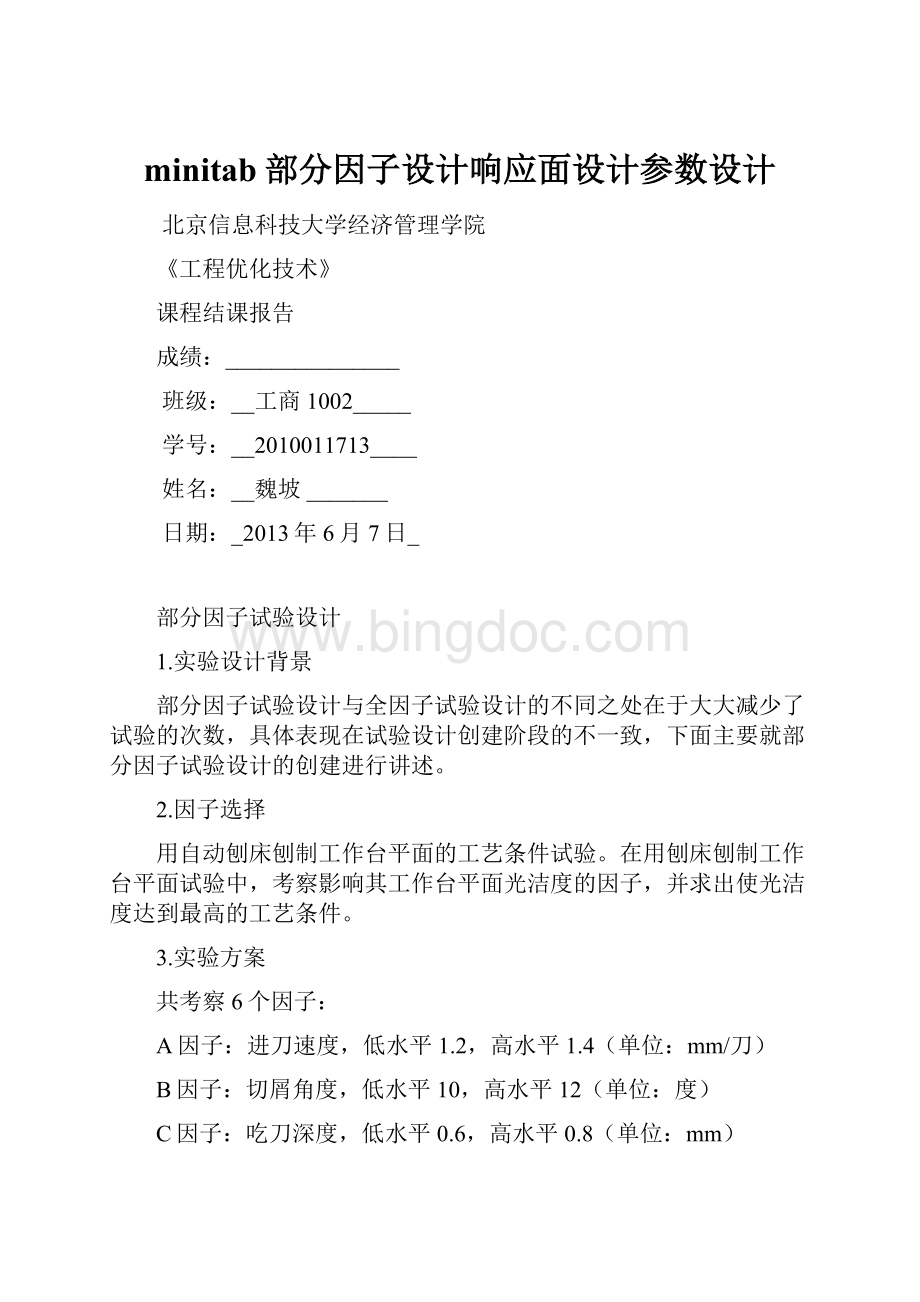
B因子:
切屑角度,低水平10,高水平12(单位:
度)
C因子:
吃刀深度,低水平0.6,高水平0.8(单位:
mm)
D因子:
刀后背角,低水平70,高水平76(单位:
E因子:
刀前槽深度,低水平1.4,高水平1.6(单位:
F因子:
润滑油进给量,低水平6,高水平8(单位:
毫升/分钟)
要求:
连中心点在内,不超过20次试验,考察各因子主效应和2阶交互效应AB、AC、CF、DE是否显著。
由于试验次数的限制,我们在因子点上只能做试验16次,另4次取中心点,这就是
的试验,通过查部分因子试验分辨度表可知,可达分辨度为Ⅳ的设计。
具体操作为:
选择[统计]=>
[DOE]=>
[因子]=>
[创建因子设计],单击打开创建因子设计对话框。
在“设计类型”中选择默认2水平因子(默认生成元),在“因子数”中选定6。
单击“显示可用设计”就可以看到下图的界面,可以确认:
用16次试验能够达到分辨度为Ⅳ的设计。
单击“设计”选项,选定1/4部分实施,在每个区组的中心点数中设定为4,其他的不进行设定,单击确定。
单击“因子”选项,设定各个因子的名称,并设定高、低水平值。
点击确定。
再点击确定后,就可以得到试验计划表,如下:
与全因子设计不同的是,我们不能肯定这个试验计划表一定能满足要求,因为部分因子试验中一定会出现混杂,这些混杂如果破坏了试验要求,则必须重新进行设计,从运行窗中可以看到下列结果:
设计生成元:
E=ABC,F=BCD
别名结构
I+ABCE+ADEF+BCDF
A+BCE+DEF+ABCDF
B+ACE+CDF+ABDEF
C+ABE+BDF+ACDEF
D+AEF+BCF+ABCDE
E+ABC+ADF+BCDEF
F+ADE+BCD+ABCEF
AB+CE+ACDF+BDEF
AC+BE+ABDF+CDEF
AD+EF+ABCF+BCDE
AE+BC+DF+ABCDEF
AF+DE+ABCD+BCEF
BD+CF+ABEF+ACDE
BF+CD+ABDE+ACEF
ABD+ACF+BEF+CDE
ABF+ACD+BDE+CEF
从此表得知,计算机自己选择的生成元是:
E=ABC,F=BCD。
后面的别名结构中列出了交互作用项的混杂情况,即每列中互为别名的因子有哪些;
从上表可以看出,主效应与三阶及四阶交互作用混杂,二阶交互作用与四阶交互作用混杂,三阶交互作用与四阶交互作用混杂;
关键是要检查一下题目所要求的2阶交互作用情况,将3阶以上的交互作用忽略不计,混杂的情况有:
AB=CE,AC=BE,AD=EF,AF=DE,AE=BC=DF,BD=CF,BF=CD。
本例中所要求的4个2阶交互作用是AB,AC,CF,DE,显然可以看到,这四个2阶交互作用均没有混杂。
因此可以看到此试验计划是可行的。
响应面设计的分析
提高烧碱纯度问题。
在烧碱生产过程中,经过因子的筛选,最后得知反应炉内压力及温度是两个关键因子。
在改进阶段进行全因子试验,因子A压力的低水平和高水平分别取为50帕和60帕,因子B反应温度的低水平和高水平分别取为260及320摄氏度,在中心点处也作了3次试验,试验结果在数据文件:
DOE_烧碱纯度。
2.实验因子的选择
对于这批数据按全因子试验进行分析,具体操作为:
选择[统计]=>
[分析因子设计],打开分析因子设计对话框。
首先将全部备选项列入模型,删除在模型中包括中心点,在“图形”中的残差与变量下将压力和温度选入进去。
得到的结果如下:
纯度的效应和系数的估计(已编码单位)
项效应系数系数标准误TP
常量96.9610.4150233.630.000
压力-2.665-1.3320.5490-2.430.094
温度-0.765-0.3820.5490-0.700.536
压力*温度0.0350.0180.54900.030.977
S=1.09803PRESS=134.203
R-Sq=68.01%R-Sq(预测)=0.00%R-Sq(调整)=36.01%
对于纯度方差分析(已编码单位)
来源自由度SeqSSAdjSSAdjMSFP
主效应27.68747.687453.843723.190.181
2因子交互作用10.00120.001230.001230.000.977
残差误差33.61703.617011.20567
弯曲13.51783.517813.5178170.920.014
纯误差20.09920.099200.04960
合计611.3057
从上述表中可以看到,主效应和2因子交互作用对应的概率P值均大于0.1,说明模型的总效应不显著,而且弯曲对应的概率P值为0.014,拒绝原假设,认为存在明显的弯曲趋势;
R-Sq和R-Sq(预测)的值都比较小,说明了模型的总效果不显著。
从残差与各变量的图也验证了存在严重的弯曲现象。
这些都表明,对响应变量单纯地拟合一阶线性方程已经不够了,需要再补充些“星号点”,构成一个完整的响应曲面设计,拟合一个含二阶项的方程就可能问题了。
补充的4个星号点的实验结果见数据表:
DOE_烧碱纯度(响应2)。
下面对全部11个点构成的中心复合序贯设计进行分析,拟合一个完整的响应曲面模型。
分析如下:
第一步:
拟合选定模型。
选择[统计]>
[DOE]>
[响应曲面]>
[分析响应曲面设计],打开分析响应曲面设计对话框。
点击窗口“项”以后,可以看到模型中将全部备选项都列入了模型,包括A(压力)、B(温度)以及它们的平方项AA、BB和交互作用项AB;
打开“图形”窗口,选定“正规”、“四合一”以及残差与变量,并将压力和温度都选入残差与变量中;
打开“储存”窗口,选定“拟合值”、“残差”以及“设计矩阵”。
单击确定。
纯度的估计回归系数
项系数系数标准误TP
常量97.78040.10502931.0660.000
压力-1.89110.09114-20.7500.000
温度-0.60530.09092-6.6570.001
压力*压力-2.58220.15339-16.8350.000
温度*温度-0.46150.15314-3.0140.030
压力*温度0.03510.182530.1920.855
S=0.181900PRESS=0.693667
R-Sq=99.35%R-Sq(预测)=97.27%R-Sq(调整)=98.70%
对于纯度的方差分析
回归525.231025.23105.04620152.510.000
线性215.712715.71277.85635237.440.000
平方29.51719.51714.75853143.820.000
交互作用10.00120.00120.001230.040.855
残差误差50.16540.16540.03309
失拟30.06620.06620.022080.450.747
纯误差20.09920.09920.04960
合计1025.3964
结果解释:
(1)看方差分析表中的总效果。
在本例中,回归项的P值为0.000,表明应该拒绝原假设,认为本模型总的来说是有效的。
看方差分析表中的失拟现象,本例中,失拟项对应的P值为0.747,明显大于显著性水平0.05,接受原假设,认为本模型中不存在失拟现象。
(2)看拟合的总效果。
本例中,R-Sq与R-Sq(调整)比较接近,认为模型的拟合效果比较好;
R-Sq(预测)比较接近于R-Sq值且这个值比较大,说明将来用这个模型进行预测的效果比较可信。
(3)各效应的显著性。
从表中可以看到,压力、温度以及它们的平方项对应的概率值都小于显著性水平,说明这些效应都是显著的;
而压力和温度的交互效应项对应的概率值为0.855,显然大于显著性水平,认为该效应项是不显著的。
第二步:
进行残差诊断
利用自动输出的残差图来进行残差诊断。
从上述残差图中可以看出,残差的状况是正常的。
第三步:
判断模型是否需要改进。
根据第一步的分析,我们得知压力和温度的交互作用项是不显著的,应该予以剔除,因此需要重新拟合新的模型,使得新的模型中不包含交互作用项。
得到的结果为:
常量97.78040.096221016.1770.000
压力-1.89110.08350-22.6470.000
温度-0.60530.08331-7.2650.000
压力*压力-2.58220.14054-18.3730.000
温度*温度-0.46150.14031-3.2890.017
S=0.166665PRESS=0.546550
R-Sq=99.34%R-Sq(预测)=97.85%R-Sq(调整)=98.91%
回归425.229825.22986.30744227.070.000
线性215.712715.71277.85635282.830.000
平方29.51719.51714.75853171.310.000
残差误差60.16670.16670.02778
失拟40.06750.06750.016870.340.836
纯度的估计回归系数,使用未编码单位的数据
项系数
常量-59.9731
压力5.36834
温度0.134611
压力*压力-0.0512244
温度*温度-2.56700E-04
(1)先看方差分析表中的总效果。
回归项对应的P值为0.000,拒绝原假设,说明回归模型总的来说是有效的;
看方差分析表中的失拟现象,可以看到失拟对应的P值为0.836,大于0.05,接受原假设,即可以判定,本模型删去了一项,但没有造成失拟现象。
(2)看删减后的模型是否比原来的有所改进。
全模型
变化
删减模型
R-Sq
99.35%
减小
99.34%
R-Sq(调整)
98.70%
增大
98.91%
S
0.181900
0.166665
R-Sq(预测)
97.27%
97.85%
PRESS
0.693677
0.546550
由于模型项缺少了一项,R-Sq通常会有所降低,但关键要看调整的R-Sq(调整)是否有所提高,s值是否有所降低,预测残差平方和PRESS是否有所降低,R-Sq(预测)是否有所提高。
从表中来看,均符合上述要求,表明删除了不显著的交互作用后,回归的效果更好了。
此外,我们还可以得到最后确定的回归方程:
从标准化残差以及删后残差的结果分析表中,可以看到这些值都小于2,因此认为新的模型的残差没有发现任何不正常的情况。
第四步:
对选定的模型进行分析解释。
通过前面得到的回归方程,运用数学方法我们可以得到使得纯度最大的A和B分别取什么值,但是不能保证该最大值就一定落在试验范围之内。
在求解前,先看一下等值线图和曲面图,具体实现:
[统计]>
[等值线图/曲面图]。
从图中可以看到,在原试验范围内确实有个最大值。
运用人工解方程的方法,可以得到当压力=52.4、温度=262.2时所获得的纯度最高。
从上图中也可以看到,在压力=52.3465、温度=262.1616时,纯度达到最大值为98.3249,与我们手算的结果是一样的。
为了获得置信区间,从“统计]>
[分析响应曲面设计]”入口,选定“响应”为纯度,在“预测”中,在自变量设置处,填写“52.4,262.2”则可以得到如下结果:
使用纯度模型的新设计点数的预测响应
点拟合值拟合值标准误95%置信区间95%预测区间
198.32500.0859139(98.1148,98.5353)(97.8662,98.7839)
从结果中可以看到,预测结果的值与我们最优化的值是一样的,说明预测结果是可信的。
前一个置信区间表明的是回归方程上的点的置信区间,此值可以作为改进的结果的预报写在总结报告中;
后一个置信区间表明的是以上述回归方程上的预测值的置信区间为基础,加上观测值固有的波动所给出的置信区间,这就是将来做一次验证试验时将要落入的范围,可供做验证试验时使用
水射流钻头喷嘴电火花线切割加工工艺
正交优化试验
针对水射流钻头喷嘴制造过程中存在的问题,试验采用正交优化试验方法,通过极差分析和方差分析,研究了电火花线切割脉冲电流、脉冲宽度和脉冲间隔等工艺参数对射流钻头喷嘴孔口表面粗糙度的影响,确定了因素的最佳水平组合和因素的主次顺序及线切割的最佳工艺参数。
试验结果表明,当采用脉冲电流1.6A、脉冲宽度8μs和脉冲间隔40μs的参数组合时,喷嘴孔口表面质量较高,其表面粗糙度小于2.4μm。
研究结果可为选择水射流喷嘴电火花线切割加工工艺制定提供试验依据。
表1因素水平表
水平
因素
A:
脉冲电流IN/A
B:
脉冲宽度T1/μs
C:
脉冲间隔T2/μs
1
0.6
8
16
2
1.6
32
3
2.8
24
40
3.实验步骤
3.1选择统计>
DOE>
因子>
创建田口设计:
3.2在田口设计中选择3水平设计,因子数为4:
3.3在田口设计中选择设计,如下所示,在对话框中单击确定:
3.4在田口设计中选择因子,如下所示,点击确定:
3.5在田口设计中点击确定后,如下图所示:
4.数据分析
5.分析过程
因素水平对表面粗糙度的影响趋势图:
如图所示为各因素指标对水射流钻头喷嘴线切割加工表面粗糙度影响的变化趋势图。
从图可以看出,喷嘴的表面粗糙度随脉冲电流、脉冲宽度的增加而显著增加,而随着随脉冲间隔的增大,喷嘴的表面粗糙度变化很小。
因此,在实际生产中,制定喷嘴的线切割工艺规范时,要着重考虑脉冲电流和脉冲宽度的选取范围,以求效果达到最优。