整理年混装事故原因分析Word文件下载.docx
《整理年混装事故原因分析Word文件下载.docx》由会员分享,可在线阅读,更多相关《整理年混装事故原因分析Word文件下载.docx(10页珍藏版)》请在冰点文库上搜索。
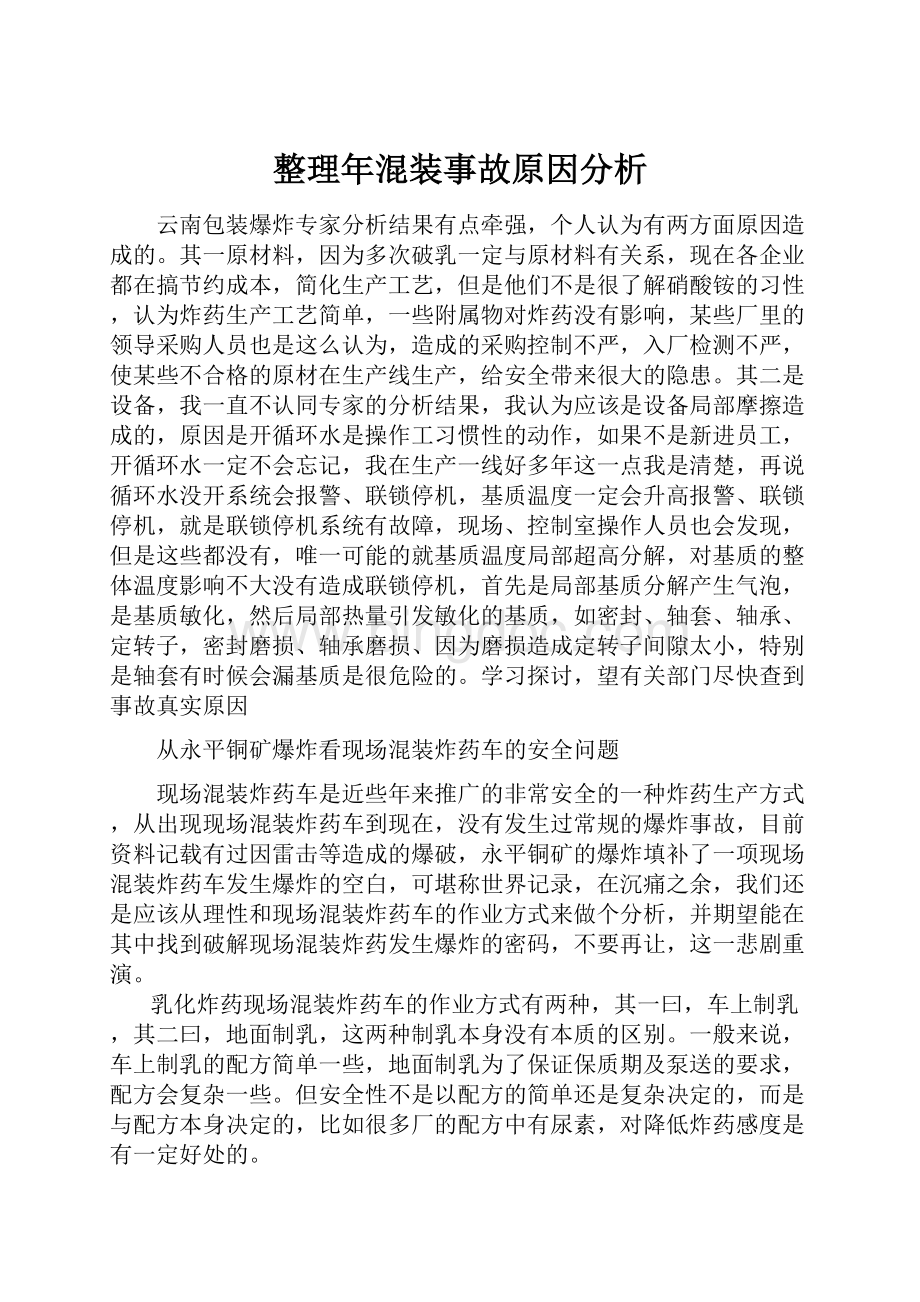
不合格的乳化基质是可以爆炸的,这在很多资料上都可以查询到,因此,对比车上制乳和地面制乳,一整车的乳化基质可以爆炸,一车硝酸铵水溶液总不会爆炸吧,而且剩下的硝酸铵溶液是可以返回贮藏罐的。
车上制乳和地面制乳的安全性问题,此事可以做一个案例吧。
在全中国都在盲从的说着地面制乳更安全的同志们可能会有一点点儿的尴尬吧。
现场混装炸药车的爆炸是沉痛的事故,对行业是一个沉痛的打击,但不管怎么样,以科学的态度来对待,是应该的。
不管怎么说,现场混装炸药目前为止还是世界上最安全的一种炸药生产方式。
按中国的经济周期,每隔5-8年就是一次事故周期,前一个事故周期是李毅中先生那一段时间,云南某炸药厂、永平铜矿炸药厂陆续发生爆炸,可能意味着一个新的事故周期的到来(以后再专文论述),各位同仁还应高度警惕,确保安全,才是行业之福,人民之福。
在2006年9月15日的亚利桑那州的一个露天铜矿上,散装炸药混装车发生了火灾爆炸事故[MSHA]。
在火灾发生时,矿上的爆破小组工人正在用乳化炸药填装炮孔,在装药过程中,位于司机座位一侧的车身上出现小火星,进而开始延伸,并快速蔓延到驾驶室。
报道称在短短几秒钟时间内,火焰窜到原材料区,火势便越来越大,以至于使用手提式灭火器无法去扑灭大火。
大火继续蔓延到了混装车的原材料区包括硝酸铵溶液、油相和密度调节剂,为了确保现场人员生命安全,整个矿井区域的作业人员迅速被全部疏散到安全区域。
混装车继续燃烧至70分钟后,大爆炸发生了。
爆炸碎片迸射的直径大约137.2米。
爆炸力使地面形成一个长为3.35米,宽为2.13米,深度为0.76米的爆坑。
该混装车在大火和爆炸中被损坏。
车上制乳有几个问题难以回避:
一、增加乳化器危险源,乳化器是精密仪器,不主张在长期颠簸和恶劣环境中工作;
二、硝酸铵保温不好容易析晶,生产安全难以确保;
三、开机启动及停机时的料头料尾没办法回收利用,对环境污染较大,且容易造成爆炸物品的流失。
楼主有些分析还是很到位,但有些技术上的东西就有些牵强了。
比如,地面制乳作业方式中“螺杆泵内的炸药是已经敏化过的,存在于螺杆泵内”的说法站不住脚。
在摩擦升温造成的热分解中敏化与否不是关键的,硝酸铵分解温度基本上一致,但是冲击波感度差别很大。
另外,关于联合国的八组试验,其可靠性目前尚存疑,结果重复性比较差。
。
但是,此次事故还是提醒大家的对混装车的安全要高度重视,提高认识,总结教训,虽然代价很惨重。
关于云南爆炸事故成因分析
根据事故分析座谈会上公布的录像、生产线运行数据记录以及专家、同行的发言,我对此次事故有如下认识,希望与各位同行一起讨论,目的是找到事故真正原因,提出应对预防措施,提高生产线的安全运行水平。
1、录像显示,事故发生前操作员工作平稳有序,无异常惊慌举动,说明乳化器运行无异常振动、噪音,这一点从乳化器平稳的工作电流可以印证,从而说明乳化器没有发生转子与定子的碰撞、摩擦。
2、录像显示,生产开始初基质表面光滑有光泽,一段时间后光泽消失,然后有大约2秒钟时间排除黄白色基质,由此可以判断,基质是在乳化器内被均匀的卷入气泡或硝铵颗粒,使基质浑浊失去光泽。
上述现象可以说明,硝铵热分解一定是在乳化器夹缝中进行的,因为只有这样才可能使分解产生的气体经乳化器转子搅拌作用而均匀分散到基质中。
排出黄白色基质,说明硝铵分解温度已经很高,分解产生了氧化氮气体,氧化氮气体也被均匀的分散到基质中。
3、水相流量曲线显示,在开机后,水相流量是一直增加的趋势,在爆炸前又迅速下降。
水相泵电流曲线显示,在开机后,水相泵电流缓慢升高,在爆炸前迅速升高。
水相流量曲线及水相泵电流曲线说明,开机生产后,水相流量一直没有达到工艺要求的流量,控制系统会自动增加水相泵频率来提高水相流量,这个过程会使水相泵电流升高。
水相流量在很长一段时间内都没有达到工艺要求流量,这说明水相管路不畅通,有析晶的硝铵晶体堵塞管路,随着生产的进行,热的水相溶液不断将硝铵晶体带走,使管路逐渐畅通,水相流量逐渐升高。
在爆炸前水相流量迅速下降说明乳化器内硝铵分解已产生了大量气体或已开始爆燃,形成了很高的压力,同时使水相泵电流升高。
4、录像显示,爆炸事故发生前,乳化器有7、8次起停机过程,而且启动时间间隔很短,由此可以断定,乳化器停机后没有进行水冲洗操作,这就使大量硝铵留在了乳化器内。
操作员为保证顺利成乳,必定不断的对乳化器进行保温,这就是乳化器腔体具有了较高的温度。
乳化器再次启动后,乳化器转子便和残留在乳化器内的硝铵晶体不断摩擦产生热量,随后又不断有硝铵颗粒被水相带进乳化器,硝铵颗粒会堵塞部分通道,使后进来的硝铵颗粒滞留,与乳化器转子不断摩擦升温,最后达到硝铵分解自加速温度。
由于在乳化器夹缝中形成了热积累,可以断定乳化器冷却水没有开启,甚至可能还通有保温蒸汽,促进了硝铵热分解。
5、由于乳化器夹缝的薄层空间约束,基质受热后只能形成爆燃,在爆燃进入乳化器顶腔后,由于失去空间约束便转为爆轰。
爆轰波引爆堆积钢带上被敏化的基质,使事故进一步扩大。
6、根据以往事故经验,由于设备局部摩擦生热引起的爆炸事故都会有断料现象,而此次事故中,基质一直连续出料,这与以往的事故有所不同,这说明造成此次事故的热源非常多,只凭基质本身已不能将生成的热全部带走,由此可以排除乳化器本身局部机械摩擦生热引发事故的可能性。
根据以上分析,我们今后生产中需要注意:
1、加强乳化器冷却水监控保护。
2、加强停机清洗操作的监控。
3、流量保护增加欠流量保护停机。
4、严禁频繁启停机。
5、完善压力监控联锁保护。
6、提高温度监控保护准确性及时性。
7、加强现场管理,严格控制操作人员数量。
8、加强人员培训,提高危险的辨识能力。
爆炸前30多秒中,乳化机出口物料呈浅黄色且颜色均一,说明氮氧化物在物料被均匀混合前已经产生,在乳化机转子与定子的侧间隙内与基质混合均匀,敏化
环境影响经济损益分析一般按以下四个步骤进行:
据我所知未成乳再启动乳化在不少企业确实存在,但重复启动7-8次不冲洗,太不可思议了,必须提高从业人员素质,加强培训。
4.将环境影响价值纳入项目的经济分析
“水相流量在很长一段时间内都没有达到工艺要求流量,这说明水相管路不畅通,有析晶的硝铵晶体堵塞管路,---”,难道管路没有安装测压装置并安全联锁?
?
(一)环境影响评价的概念“---这说明造成此次事故的热源非常多,只凭基质本身已不能将生成的热全部带走,由此可以排除乳化器本身局部机械摩擦生热引发事故的可能性。
”但我觉得不能排除乳化器本身局部机械摩擦生热引发事故的可能性。
一、环境影响评价的发展与管理体系、相关法律法规体系和技术导则的应用我想,还是应该了解其工艺条件,包括水相配方特别是水含量,有无其他添加剂等,其次还应了解乳化器的结构和运行条件,只有弄清这些才有助于分析事故真正原因。
(五)规划环境影响评价的跟踪评价一次安全事故不是偶然哪一个因素出现而出现,是其他众多因素聚集在一起的结果!
要分析一起事故不能单从哪一方面来定妥,只有全面的分析与细致深究才能汲取到别人的教训,达到安全的目的!
!
工艺配方、原材料、设备、现场操作、技术文件制定与执行、危险有害性分析与防范、管理人员责任心、员工意识与教育、、、、、、、
以森林为例,木材、药品、休闲娱乐、植物基因、教育、人类住区等都是森林的直接使用价值。
分析很全面,但是分解的根本原因在哪?
乳化器腔体内的温度达到了硝酸铵分解的温度(210度左右)了吗?
那么此时基质的温度应该超过工艺设定的温度(我们的经验为不超过110度),控制系统应该报警啊!
为何控制系统没有报警?
还有:
水相管道加热不够,硝酸铵晶体带到乳化器腔体,那么水相管路的压力应该异常,或者超过工艺设定值,也应该报警的!
但是很遗憾,这些都没有!
看来该厂的控制系统很成问题!
厂方为何没有做好有关报警测试就生产呢?
那怕是维修检查后都必须做报警实验的呀!
厂方的技术水平值得怀疑!
该厂的管理上有很大的漏洞!
血的教训应该引起重视啊!
安全预评价方法可分为定性评价方法和定量评价方法。
1)地方环境标准是对国家环境标准的补充和完善。
在执行上,地方环境标准优先于国家环境标准。
“现场调查显示,乳化机电流无任何异常,说明没有机械摩擦,在正常转速的情况下,如果有摩擦,电流肯定有波动。
”在出料不中断状态下,未成乳水相溶液在乳化器腔体内应是浆糊状,转子的湿摩擦和机械摩擦的干摩擦比较,可能后者温升更大。
另外乳化机电流记录时间间隔是几分钟?
“乳化机电流无任何异常,说明没有机械摩擦,在正常转速的情况下,如果有摩擦,电流肯定有波动。
”乳化器电机功率多大?
电流检测灵敏度?
多大的摩擦才足以检测出电流波动?
有待验证。
1.直接市场评估法
这个和电机功率没关系啊,乳化机的电流是由变频器提供的,约每200毫秒提供给PLC一次。
虽然反馈到组态里会有滞后现象,但系统肯定会记录下来的。
如果有机械摩擦,也就是转子和定子有摩擦,定子肯定不会动,也就意味着转子失去动平衡了,在高转速的情况下,电流肯定有异常的。
所以可以排除机械摩擦的原因。
电流数据记录一般是间断的,通常几秒或几十秒记录一次,如果瞬间电流高,不一定能记下来。
硝铵结晶,摩擦,热分解,气体,敏化,变色、发泡、爆炸!
(一)安全预评价依据
论成功科技在梅州中低温乳化炸药生产线安全隐患及对策
该生产线采用的CYJ精乳器就是云南包装厂爆炸的那种乳化器。
根据事故专家组调查结论,其具有如下几个缺陷(唐总他们也请了河北大学的机械专家对此进行了论证,说要对这些缺陷进行改进)可能导致极端情况下出现安全隐患。
一.按石家庄成功机电有限公司提供的CYJ精乳器使用说明书第二页“轴封采用骨架油封,为防止主轴被油封磨损,更换成本高,在轴与油封间安装有隔套(外表面经镀硬络处理),硬度高,耐腐蚀,耐磨损”和拆开其在云南包装厂二分厂的同类乳化器发现如下:
a).骨架油封和隔套接触的地方有约1毫米的磨痕;
b).骨架油封沿乳化器进口方向向下有个O型圈密封,它和隔套接触的地方有磨擦发亮的痕迹。
C).这些密封的地方未见有任何冷却装置。
由于O型圈和骨架密封处总是有物料(乳胶基质或未成乳的油水相物料)填满其间隙形成死角而该死角在密封失效前始终在和1470rpm高速旋转的主轴摩擦,如该处摩擦产生的热量不能被及时带走,就会造成热积累并在极端的情况下发热至乳胶基质或含油硝铵的热分解点导致硝铵分解反应最终和油相形成氧化还原化学反应。
建议该设备的这些密封处要加装冷却水装置以避免上述可能发生的热积累而导致的分解化学反应。
b).该设备在密封处采用的镀硬络隔套没有与主轴固定,而是通过轴的台阶定位和在隔套涂覆密封胶形成和主轴的连接关系。
这种设计不能保证隔套与主轴间产生相对转动,在极端的不可预知的情况下,该隔套会与主轴发生相对运动。
而此时如果隔套和轴之间的密封胶被物料(乳胶基质等)取代,该处的金属和金属之间的摩擦会在瞬间产生大量的热量至隔套与主轴之间的物料(乳胶基质等)发生热分解最终形成氧化还原化学反应。
建议该设备和密封配套使用的隔套要和主轴固定,彻底消除隔套和主轴可能发生相对转动而产生瞬间温度急剧上升导致的分解化学反应。
c).该设备采用立式悬臂结构,其轴承仅采用一个圆柱孔调心球轴承,主轴和电机联轴器采用套筒和平键方式连接无法保证其悬臂在极端情况下的径向摆动。
鉴于其转子和定子的间隙仅为5毫米,为保证在极端(轴承损坏等)的情况下,定转子不会发生碰撞摩擦而产生瞬间温度急剧上升导致的分解化学反应。
建议该设备主轴采用至少二个角接触球轴承,它们之间的距离建议设置为不小于轴悬臂长度的两倍。
二.该生产线采用水冷皮带,长度仅为18米,为把乳胶基质温度降到45度左右,在产能8吨每小时,水冷皮带速度5米每分钟的条件下,其物料在水冷皮带上的厚度约为14毫米。
云南包装厂事故表明,钢带厚度在7毫米时,当乳胶基质出现异常36秒后发生爆炸后将钢带上的药殉爆了。
按唐总的“乳化炸药在水里爆炸时殉爆距离大幅提升”的理论,其水冷皮带的药量在发生事故时是能扩大事故的。
建议重新评估水冷皮带的防殉爆功能,在水冷皮带进入敏化机之前采用有效的隔爆措施。
三.该生产线采用仿制的Tippertie转盘机装药。
由于其炸药粘度大,很容易在泵入口处物料架桥导致泵实际吃进的料减少或者干磨,尤其是在其产能提高时这些事故概率将大大增加。
扬祖一等专家在工信部2012年10月组织的研讨会上,明确指出:
对用于包装型特别是小直径中低温敏化工艺的塑膜装药系统输送泵的结构和防止断料干磨措施,应该重新进行安全性评估。
由于叶片装药泵上有个装200公斤已敏化炸药的料斗,建议将叶片装药泵和转盘机用隔墙隔开,同时研究如何解决叶片泵和装药机的管路传爆问题。
综上所述,唐总在梅州的生产线存在诸多安全隐患,且没有相关事故发生的隔爆措施,个人认为唐总在忧虑高温线的安全问题时,首先把其转让的类似乳化炸药生产线的安全隐患及时解决,消除这些隐患可能带来的再次爆炸事故!
一、生产实践情况
CYJ乳化器国内外销售77台,生产炸药500万吨。
3.11爆炸事故使用的乳化器已运行2.5年,生产炸药近5万吨,事故发生前乳化器无噪音、电流正常,但乳化基质却异常为敏化。
我国乳化炸药工业化以来,采用电机轴承定位的乳化器一直占据主流,生产乳化炸药超过2000万吨。
目前生产线大部分仍使用该类型乳化器。
部分发达国家也采用该类定位乳化器。
另外,在发生爆炸的乳化器中,有50%为该类定位,另50%为电机外多轴承定位。
二、乳化器的相关试验结果
(一)密封的温升情况
某国内同类搅拌设备,采用8个骨架油封。
CYJ乳化器设计仅采用1个骨架油封,死角体积和摩擦发热量将小5~7倍。
而且其安装位置位于乳化端盖轴孔上部,设计上利用安装位置直接与空气接触,通过空气或机油散热。
表1为密封处温度测定结果。
表1
CYJ乳化器密封温度生产测试结果
厂家
广东天诺
梅州分公司
福建海峡科化
永安分公司
广东明华
韶关分公司
罗定分公司
乳化器转速,rpm
970
970
冷却介质
空气
机油
机油
测定日期
3月23日
3月25日
3月27日
3月28日
生产时长,小时
4
0.5
3
0.3
室温,℃
26
21
16
15
基质温度,℃
96
97
92
88
油封温度,℃
86
80
升温,℃
0
-11
-8
结论
1密封上部通过空气冷却,不升温;
2密封上部通过机油冷却,冷却效果优于空气。
上表说明,CYJ乳化器的密封设计发热量较小,热量能被有效传导出乳化器外由空气消散,密封处没有产生温升。
(二)轴套扭矩试验
试验情况:
若轴套与轴之间产生相对滑动,需要扭矩4.72kgm,
而轴套作用于密封的扭矩仅为0.061kgm。
结论:
轴套作用于密封的扭矩仅为轴套与轴滑动所需扭矩的1.3%,密封与轴套摩擦产生的扭矩远不能带动轴套与轴的相对滑动。
(三)转子摆动
转子转动位移(轴向与径向)试验,见表2。
表2
CYJ型乳化器实际间隙情况测试结果
行业要求
最小间隙
乳化器
设计间隙
乳化器实测最小间隙
结论
1470rpm
970rpm
轴向mm
6
5.84
5.81
达到行业要求
径向mm
2.5
5
4.49
4.67
乳化器运行时,定转子间隙分别大于行业规定轴向、径向最小间隙95%、80%,符合行业要求,而且间隙余量大。
再说几点,我只是就事论事而已,我的观点也是和很多生产厂家交流后大家共同的关注点。
1.任何事故的发生,都是一系列因素导致的。
乳化器发生爆炸事故,目前国内有两种观点,一是热分解,一是热积累。
无论是热分解还是热积累,设备自身有死角或者断料干磨肯定是主要原因。
就技术转让方来说,不仅要考虑设备正常时的安全可靠性,还要调研极端情况下设备的危险潜在点,通过极端试验来验证设备的安全性,然后再通过一系列的后续手段和自控手段来保障设备的本质安全。
2.轴套和转轴万一发生相对运动,是会给AN很大的能量造成爆炸?
很难想象枪击没有感度的基质在外力较小时会爆炸。
在这里应该做一个极端试验,轴和套发生相对运动并填满炸药,试验转速,时间,轴套与轴间隙等关联因素会不会导致爆炸的产生。
3.空气冷却或者水冷却的检测装置是否可靠,在有AN水溶液冲洗的环境下,多久会失效?
4.能不能做一个连锁保护,使乳化器在短时间内不得连续启动?
比如设置10分钟内乳化器不得连续启动2次,1小时内不得启动3次?
这个连锁应该很好做,大家可能没有考虑到,我在这里抛砖引玉下。
5.乳化器转子和定子的间隙,还能不能再加大一些?
或者换一种乳化方式?
6.还是要多推广现场混装的生产方式。
毕竟包装型乳化炸药面临着较强的竞争,为了性能上有优势,追求高转速高工艺温度的方式终究是不可取。