压块机的液压系统以及控制系统的设计.docx
《压块机的液压系统以及控制系统的设计.docx》由会员分享,可在线阅读,更多相关《压块机的液压系统以及控制系统的设计.docx(24页珍藏版)》请在冰点文库上搜索。
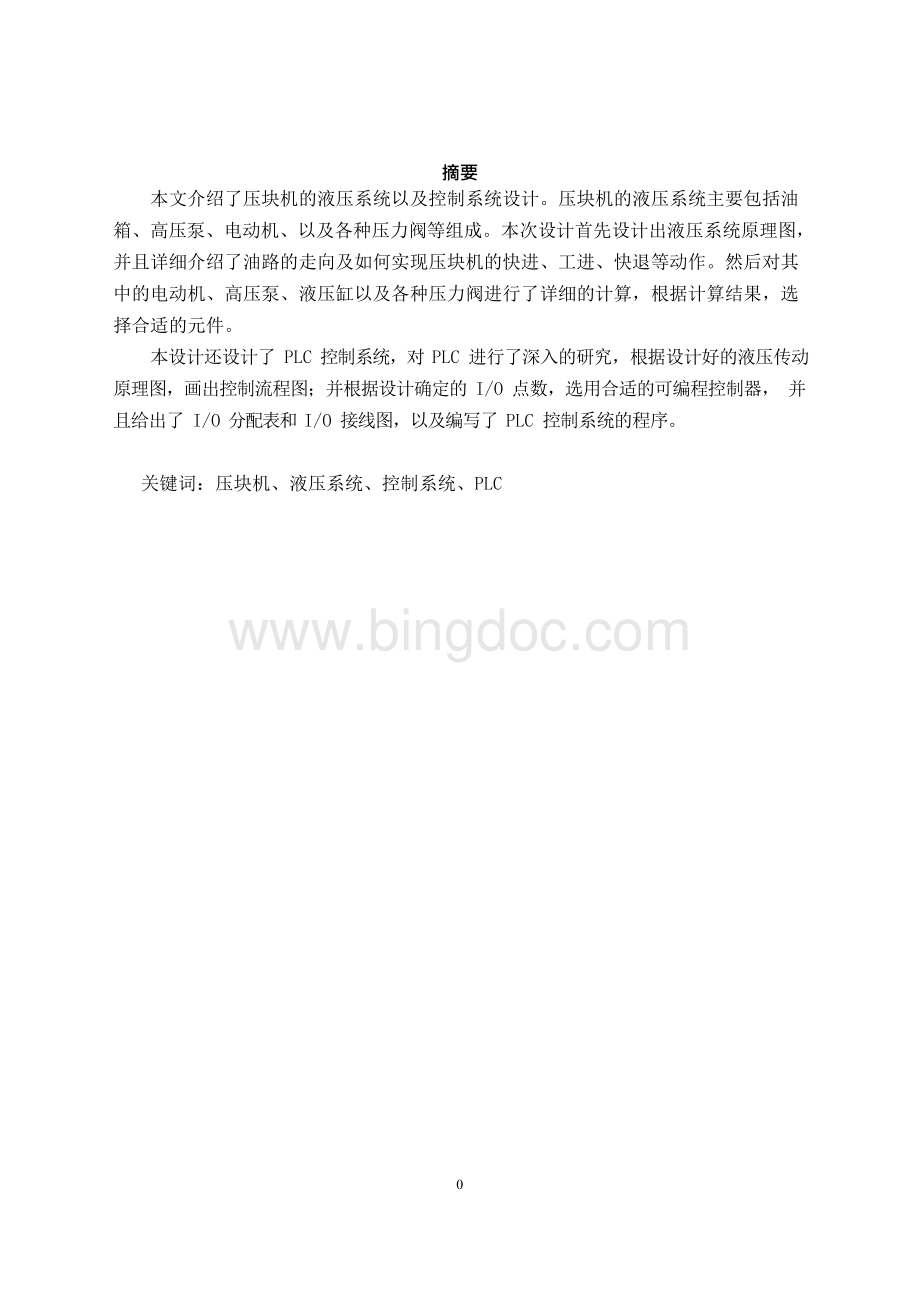
摘要
本文介绍了压块机的液压系统以及控制系统设计。
压块机的液压系统主要包括油箱、高压泵、电动机、以及各种压力阀等组成。
本次设计首先设计出液压系统原理图,并且详细介绍了油路的走向及如何实现压块机的快进、工进、快退等动作。
然后对其中的电动机、高压泵、液压缸以及各种压力阀进行了详细的计算,根据计算结果,选择合适的元件。
本设计还设计了PLC控制系统,对PLC进行了深入的研究,根据设计好的液压传动原理图,画出控制流程图;并根据设计确定的I/O点数,选用合适的可编程控制器,并且给出了I/O分配表和I/O接线图,以及编写了PLC控制系统的程序。
关键词:
压块机、液压系统、控制系统、PLC
0
目录
摘要 1
1.绪论 3
1.1课题研究的背景 3
1.2研究课题所做的工作 4
2.液压系统设计 4
2.1液压技术的简介 5
2.2压块机工况分析 6
2.3液压系统图及其工作原理 7
2.3.1液压系统图:
7
2.4液压元件的选择与计算 9
2.4.1.分析负载 9
2.4.2.液压缸设计计算 10
2.4.3液压泵设计计算 11
2.4.4阀类元件与辅助元件的选择 12
2.4.4.1溢流阀 12
2.4.4.2电磁换向阀 13
2.4.4.3顺序阀 13
2.4.5双联叶片泵 13
2.4.6油箱 14
3.PLC的选用和设计 14
3.1.采用PLC控制的优点 14
3.2.输入输出I/O点数的估算 14
3.2.1 控制功能的选择 14
3.3PLC的控制设计 15
3.3.1PLC控制工作原理 16
3.3.2I/O口的分配 16
3.3.3外部电路接线图 16
3.3.4PLC梯形图的概述 18
3.3.5PLC控制梯形图 18
3.3.6根据梯形图写出以下程序 21
参考文献 23
23
1.绪论
1.1课题研究的背景
随着现在社会的发展,机械、液压、电气等科学技术的进步,挤压机的应用越来越广泛,渐渐成为机械行业不可或缺的加工机械。
目前挤压技术已经应用于硬质合金、食品工业及机械加工业等诸多领域。
利用硬质合金挤压成型技术可生产截面积较小且长度较长的产品,如棒材、管材、带材等。
由于采用挤压技术可以获得沿长度方向密度均匀的产品,且生产效率高,因此在硬质合金生产中挤压机技术已经得到普及应用。
同时随着挤压机的发展,种类逐渐细化,其产品应用领域不断扩展,使挤压机在国民经济中地位在不断加强。
而伴随着资源、能源的缺乏和对环境保护要求的提高,越来越多的节能、减排产品投放到了市场,而金属锯屑挤压机便是其中的一种,它可以将金属锯屑压成块再回炉,不仅减少了对环境的污染,而且给运输带来了方便。
在中国,金属锯屑挤压机市场有很大的发展空间,有很高的投资价值,为保护环境,节约能源起到了举足轻重的作用。
因此,可以看出金属锯屑挤压机具有很大的发展潜力与极好的市场。
金属锯屑挤压机的具体发展方向为:
1)智能化送料装置
送料量的多少及是否均匀,直接关系到屑块的形状、尺寸及松紧度。
现在金属屑压块机大多无独立送料装置或装置达不到要求,导致屑块形状、尺寸及松紧度差异较大,为了达到均匀稳定送料,可采用振动机重量检测进行控制。
2)工艺性好
与主机配合完美的金属锯屑挤压机控制系统将会有所发展,它具有友好的人机界面,不占太多的工作空间,便于操作,便于维护,可大大减少操作工人的工作强度。
3)良好的工作性能
具有较低的噪声、较小的能耗,在高速换向时,利用程序控制、软件来实现对换向冲击的缓冲。
4)能够实现从进料到出块全自动的金属锯屑压块生产流水线。
5)发展智能化金属锯屑挤压机控制系统。
6)应配置屑块智能称重仪,使屑块具有重量即时显示、超重报警、累计重量、累计数量、班次产量等功能。
7)发展机电液一体化金属锯屑挤压机。
屑块质量好、生产效率高是金属锯屑压块机的发展方向,现有使用金属锯屑压块机均成为单一的机械设备。
可以综合使用机械、液压、电气控制等技术,发展结构紧凑,元件高度集成,使得液压站的体积大大减小,减少连接管路、液压元辅件,从而使可靠性相应的提高。
8)增加出料装置
配备出料装置可以避免二次操作,从而节省了时间与劳动强度。
9)高效率、低故障率,便于维修
这就要求系统结构尽可能的简单,从而降低故障率,并且便于维修。
同时要求液压系统反应速度快,行程短。
设计须考虑到多尘和高温等环境因素,以减少故障发生。
10)全方位的监控运行控制系统。
本次研究的金属屑挤压机的应用更为广泛。
只要有锯切设备,锯屑的产生就不可避免。
如何处理、回收锯屑,尤其是铜、铝材等贵金属切屑,就成为一个必须考虑的问题。
如果每天产生大量的锯屑,依靠人工将锯屑装入翻斗车,需要较多人力,既影响环境,又不便于运输、回收。
因此,金属压块机的功用就显得尤为重要,它不仅节约了资源,而且提高了工作效率。
1.2研究课题所做的工作
1)问题的提出
金属锯屑挤压机是各个机械加工行业不可或缺的辅助设备。
随着机械加工行业不断地发展,金属的需求量逐年的增加,随之产生了大量的金属锯屑,而对锯屑的回收就显得更加必要。
这就需要有一种专门的工具进行回收,而金属锯屑压块机的出现,使之得到了解决,它不仅能节省成本,而且也能节约资源。
本次课程设计所要解决的问题就是设计出这种锯屑挤压机的液压控制系统。
2)解决问题所做的工作
A.详细分析金属锯屑液压压块机的工作过程;并根据工作过程,设计能满足
工作要求的液压控制系统。
B.以设计的液压系统为基础,画出控制流程图;并根据设计确定I/O点数,选用合适的可编程控制器,写出I/O分配表,画出I/O接线图;编写PLC控制系统的程序。
2.液压系统设计
2.1液压技术的简介
一个完整的液压系统由五个部分组成,即动力元件、执行元件、控制元件、辅助元件和液压油。
动力元件的作用是将原动机的机械能转换成液体的压力能,指液压系统中的油泵,它向整个液压系统提供动力。
液压泵的结构形式一般有齿轮泵、叶片泵和柱塞泵。
执行元件(如液压缸和液压马达)的作用是将液体的压力能转换为机械能,驱动负载作直线往复运动或回转运动。
控制元件(即各种液压阀)在液压系统中控制和调节液体的压力、流量和方向。
根据控制功能的不同,液压阀可分为压力控制阀、流量控制阀和方向控制阀。
压力控制阀又分为溢流阀(安全阀)、减压阀、顺序阀等;流量控制阀包括节流阀、调整阀、分流集流阀等;方向控制阀包括单向阀、液控单向阀、梭阀、换向阀等。
根据控制方式不同,液压阀可分为开关式控制阀、定值控制阀和比例控制阀。
辅助元件包括油箱、滤油器、油管及管接头、密封圈、压力表、油位油温计等。
液压油是液压系统中传递能量的工作介质,有各种矿物油、乳化液和合成型液压油等几大类。
液压由于其传动力量大,易于传递及配置,在工业、民用行业应用广泛。
当前,液压技术在实现高压、高速、大功率、高效率、低噪声、经久耐用、高度集成化、微型化、智能化等各项要求方面都取得了重大的进展,在完善比例控制、伺服控制、数字控制的技术上也有许多新成就。
此外,在液压元件和液压系统的计算机辅助设计,计算机仿真和优化以及计算机控制等开发性研究方面成就更大。
液压设备以其“柔性”的动力和单一的直线驱动力,使系统具有较长的生命和较高的工作效率,加上液压设备与PLC结合很容易实现压力、行程、速度及自动、半自动循环工作控制,已成为成型机械首选驱动方式。
本次设计的金属锯屑压块机充分综合这些特点,利用PLC控制液压机械,将散碎的锯屑挤压成块料。
辅刚压下
主缸快进
主缸轻压
重压
主缸退回到位
保压
主缸退回少许
辅缸上升
主缸推出
辅缸压下,准备下一循环
主缸退回到位
2.2压块机工况分析
图 压块机的工序流程图
2.3液压系统图及其工作原理
2.3.1液压系统图:
(1)过滤器;
(2)大流量泵;(3)小流量泵;(4)电机;(5)顺序阀;(6)单向阀;(7)溢流阀;(8)(9)三位四通电磁换向阀;(10)(11)压力继电器;(12)蓄能器;(13)平
衡阀;(14)主液压缸;(15)辅液压缸(16)二位二通电磁换向阀(17)节流调速阀(18)溢流阀
2.3.2工作原理
快速回路由流量泵1和流量泵2组合提供,流量泵1为大流量泵,流量泵2为小流量泵,在快速运动时,泵1输出的油液经过单向阀6与泵2输出的油液共同向系统供油;工作行程时,系统压力升高,打开顺序阀5使泵1卸荷,由泵2单独向系统供油,整个系统的工作压力由溢流阀7调定。
系统的执行器为主液压缸14和辅液压缸15,两缸的运动方向分别由三位四通电磁换向阀8和9控制;压力继电器10用于轻压到达要求之后开始保压信号,压力继电器11用于重压达到要求后,主缸
开始后退少许的信号。
立置的辅缸15由平衡阀13控制,以防该缸因自重自行下落。
系统工作期间,当负载小时,电磁铁1YA通电时三位四通换向阀8切换向右位,大流量泵1和小流量泵2同时经换向阀8向主缸14的无杆腔供油,主缸快速进给;锯
屑压紧到一定程度后,系统压力上升,使外顺序阀5打开,泵1卸荷,泵2单独向主缸无杆腔供油,主缸由快速推进变成慢速推进,从而实现对锯屑的慢速挤压;当电磁阀2YA通电使电磁阀8切换向左位时,双泵同时经电磁阀8向主缸的有杆腔供油,主缸快速退回。
2.3.3压块机液压系统的工序流程详解
1辅缸压下:
按下启动键,3YA得电,辅缸压下到SQ4
2主缸快进:
压下SQ4,3YA失电,1YA和5YA得电,主缸快进。
3主缸轻压:
压下SQ5,5YA失电,1YA和压力继电器1得点电,主缸开始轻压
4主缸保压:
当主缸压力到达压力继电器1的调定值后,1YA和压力继电器1
失电,计时器1得电开始计时,主缸由蓄能器保压
5主缸回退到位:
当计时器1计时完,即保压时间到,计时器1失电,2YA得电主缸退回到SQ1
6主缸重压:
压下SQ1,2YA失电,1YA和压力继电器2得点电,主缸开始重压
7主缸回退少许:
当主缸压力到达压力继电器2的调定值后,1YA和压力继电器2失电,2YA得电,计时器2得电开始计时,主缸开始回退
8辅缸上升:
当计时器2计时完,即回退时间到,计时器2失电,2YA失电,
4YA得电,辅缸开始上升到SQ3
9主缸推出:
辅缸压下SQ3,4YA失电,1YA得电,主缸推出到SQ2
10主缸退回到位:
压下SQ2,1YA失电,2YA得电,主缸退回到SQ1
11辅缸压下,进入下一循环:
压下SQ1,2YA失电,3YA得电,辅缸压下。
2.3.4压块机液压系统的工序流程图汇总
输出
工序
1YA
2YA
3YA
4YA
5YA
计时器
1
计时器
2
辅缸压
下
-
-
+
-
-
-
-
主缸快
进
-
-
-
-
+
-
-
主缸轻
压
+
-
-
-
-
-
主缸保
压
-
-
-
-
-
+
-
主缸退
回到位
-
+
-
-
-
-
-
主缸重
压
+
-
-
-
-
-
-
主缸退
回少许
-
+
-
-
-
-
+
辅缸上
升
-
-
-
+
-
-
-
主缸推
出
+
-
-
-
-
-
-
主缸回
退到位
-
+
-
-
-
-
-
辅缸压
下
-
-
+
-
-
-
-
2.4液压元件的选择与计算2.4.1.分析负载
(1)外负载
表2-1按负载选择液压执行元件工作压力表
载荷/KN
<5
5-10
10-20
20-30
30-50
>50
工作压力
/Mpa
<0.8-1
1.5-2
2.5-3
3-4
4-5
>5-7
表2-2按主机类型选择液压执行元件工作压力表
设备类
型
磨床
组合机
床
车床,铣
床
衍磨机
床
拉床
农业机
械
工程机
械
工作压
力/Mpa
<1.2
<6.3
2-4
2-5
<10
10-16
16-32
取最大外负载Fg=1000KN.
(2)惯性负载
机床工作部件总质量m=1000kg,取△t=0.2sFm=m*△v/△t=1000*0.05/0.2=250N
(3)阻力负载
机床工作部件对滑台的法向力为:
Fn=m*g=1000*9.81=9810N
静摩擦阻力:
Fs=fs*Fn=0.2*9810N=1962N动摩擦阻力:
Fd=fd*Fn=0.1*9810N=981N
表2-3液压缸各工作阶段负载F.
工况
负载组成
负载值F/N
启动
F=fs*Fn
1962
加速
F=fd*Fn+m*△v/△t
1231
快进
F=fd*Fn
981
工进
F=fd*Fn+Fg
1000981
快退
F=fd*Fn
981
2.4.2.液压缸设计计算
1.主要尺寸的确定
(1)缸筒内径D
根据负载大小和选定的工作压力,从GB/T2348-2001标准中选取尺寸。
(2)活塞杆直径d
对单杆活塞缸,d值可由D和λv来决定,查GB/T2348-2001进行圆整。
2.液压缸主要技术参数对单活塞杆缸:
A2=F/ηm(P1*φ-P2)
A1=φ*A2
其中F-缸最大外负载1000KNP1-缸最大工作压力16Mpa
P2-缸背压,查表2-4,取3Mpa
Pmin-缸空载启动压力,查表2-5,取0.3Mpa
ηm-液压缸机械效率=0.96取φ=A1/A2=2
表2-4 背压压力
系统类型
背压压力/Mpa
系统类型
背压压力/Mpa
中低压系统或轻
载节流调速系统
0.2-0.5
采用辅助泵补油
的闭式油路系统
1-1.5
回油路带调速阀
或背压阀的系统
0.5-1.5
采用多路阀的中
高压系统
1.2-3
表2—5液压缸空载启动压力及效率
活塞密封圈形式
Pmin/Mpa
ηm
O,L,U,X,Y
0.3
0.96
V
0.5
0.94
活塞环密封
0.1
0.985
A2=F/ηm(P1*φ-P2)=1000000/0.96×(16*2-3)×1000000=0.036㎡
A1=φ*A2=2*0.036=0.072㎡
D=√4*A1/π=0.30m
d=0.707*D=0.21m
3.液压缸在不同工作阶段的压力,流量。
快进时:
P1=(F/ηm+A2*△p)/(A1-A2)=1.58Mpa
Q=(A1-A2)*V1=0.0018m³
P=P1*Q=2844W
工进时:
P1=(F/ηm+A2*P2)/A1=15.96Mpa
Q=A1*V2=0.00072m³
P=P1*Q=11462W
快退时:
P1=(F/ηm+A1*P2)/A2=6.03Mpa
Q=A2*V1=0.0018m³
P=P1*Q=11340W
表2-6液压缸在不同工作阶段的压力流量表
工况
负载
回油腔压力
P2/Mpa
进油腔压力
P1/Mpa
输入流量Q
输入功率
P/W
快进
981N
1.55Mpa
1.58mpa
0.0018
2844
工进
1000981N
3Mpa
15.96mpa
0.00072
11462
快退
981N
3Mpa
6.03mpa
0.0018
11340
2.4.3液压泵设计计算
液压缸整个工作循环最大工作压力为15.96Mpa,取油路压力损失0.01Mpa,使压力继电器可靠工作,调整高出工作压力0.03Mpa,即小流量泵最大工作压力为:
Pp1=15.96+0.01+0.03=16Mpa
大流量泵在快进,快退时才向液压缸输油,取进油路上的压力损失0.02Mpa,则大流量泵的最大工作压力为:
Pp2=6.03+0.02=6.05Mpa
液压泵向缸输入的最大流量为Q=(A1-A2)*V1=0.036*0.05*60*1000=108L/min,
取泄漏系数Kl=1.07,则实际流量为116L/min.
当工进时只有小流量泵向液压缸输油
Q小=A1*V2=0.072*0.01*60*1000=43.2L/min
大流量泵只有快进和快退时向液压缸输油
Q大=108-43.2=64.8L/min
溢流阀最小稳定溢流量为3L/min,工进时流量为30L/min,所以小流量泵流量规格最少为33L/min
根据以上压力和流量的数值查阅产品样本,最后确定选取PV2R23-47/66,即小流量液压泵和大流量液压泵的排量分别为:
47 ml/r和66ml/r,当液压泵的转速
Np=1000r/min时,若取液压泵的容积效率为ηv=0.9,则液压泵的实际输出流量为:
Qp=(47+66)*1000*0.9/1000=101.7L/min
2.4.4阀类元件与辅助元件的选择
表2-7元件的型号及规格
元件名称
额定流量
额定压力
额定压降
型号,规格
双联叶片泵
47+66
PV2R23-47/66
三位四通电磁
换向阀
80
外控卸荷阀
单向阀
63
16
0.2
AXQF-E10B
二位二通电磁
换向阀
先导式溢流阀
63
16
YF3-E10B
单向阀
63
16
<0.2
AF3-Ea10B
平衡阀
63
-
<0.02
XU-63*80-J
滤油器
压力继电器
10
HED1kA/10
2.4.4.1溢流阀
稳压作用:
溢流阀串联在回油路上,溢流阀产生背压运动部件平稳性增加。
1.系统卸荷作用:
在溢流阀的遥控口串接溢小流量的电磁阀,当电磁铁通电时,溢流阀的遥控口通油箱,此时液压泵卸荷。
溢流阀此时作为卸荷阀使用。
2.安全保护作用:
系统正常工作时,阀门关闭。
只有负载超过规定的极限(系统压力超过调定压力)时开启溢流,进行过载保护,使系统压力不再增加(通常使溢流阀的调定压力比系统最高工作压力高10%~20%)。
3.实际应用中一般有:
作卸荷阀用,作远程调压阀,作高低压多级控制阀,作顺序阀,用于产生背压(串在回油路上)。
2.4.4.2电磁换向阀
变换阀心在阀体内的相对工作位置,使阀体各油口连通或断开,从而控制执行元件的换向或启停。
1.换向性能:
在规定的工作条件下,电磁阀通电后能否可靠地换向,断电后能否可靠地复位。
2.压力损失:
电磁换向阀的压力损失由液流流过电磁换向阀的阀口时产生的流动损失和节流损失组成。
3.内泄露量:
电磁换向阀的内泄露量是指在规定的工作条件下,处于各个不同工作位置时,从高压腔到低压腔的泄露量。
4.换向和复位时间:
从电磁铁通电到阀芯换向终止所需要的时间,复位时间是指从电磁断电到阀芯回复到初始位置所需要的时间。
5.换向频率:
在单位时间内所允许的最大换向次数。
6.使用寿命:
电磁阀使用到主要零部件损坏,不能进行正常的换向和复位动作,或者使用到其主要性能指标明显恶化超过了规定指标所经历的换向次数。
2.4.4.3顺序阀
顺序阀主要是用来控制液压系统中各执行机构动作的先后顺序。
通过改变控
制方式、卸油方式和二次油路的接法,顺序阀还可以用作其他用途,如作背压阀、卸荷阀、平衡阀用。
1.顺序阀是利用油路的压力来控制液压缸或液压马达顺序动作,以实现油路系统的自动控制。
当进口油路的压力没有达到顺序阀所预调的压力以前,此阀关闭;达到后,阀门开启,油流进入二次压力油路,使下一级元件动作。
它与溢流阀的区别,在于它通过阀门的阻力损失接近于零。
2.顺序阀内部装有单向元件时,称为单向顺序阀,它可使油流自由地反向通过,不受顺序阀的限制,在需要反向的油路上使用单向顺序阀较多。
3.控制液压缸或液压马达顺序动作。
直控顺序阀或直控单向顺序阀可用来控制液压缸或液压马达顺序动作。
4.作普通溢流阀用。
将直控顺序阀的二次压力油路接回油箱,即称为普通起安全作用的溢流阀。
5.作卸荷阀用。
作蓄能器系统泵的自动卸荷用。
6.作平衡阀用。
用来防止液压缸及工作机构由于本身重量而自行下滑。
2.4.5双联叶片泵
双联叶片泵是由两个单级叶片泵装在一个泵体内在油路上并联组成。
两个叶片泵的转子由同一传动轴带动旋转,有各自独立的出油口,两个泵可以是相等流量的,也可以是不等流量的。
双联叶片泵常用于有快速进给和工作进给要求的机械加工的专用机床中,这时双联泵由一小流量和一大流量泵组成。
当快速进给时,两个泵同时供油(此时压力较低),当工作进给时,由小流量泵供油(此时压力较高),同时在油路系统上使大流量泵卸荷,这与采用一个高压大流量的泵相比,可以节省能源,减少油液发热。
这种
双联叶片泵也常用于机床液压系统中需要两个互不影响的独立油路中。
2.4.6油箱
油箱容积按下式估算,取经验数据ζ=7,故其容积为V=ζ*Qp=7*101.7=711.9L
按JB/T7938-1999规定,取最靠近的标准值800L.
3.PLC的选用和设计
3.1.采用PLC控制的优点
1)控制方式上看:
电气控制硬件接线,逻辑一旦确定,要改变逻辑或增加功能是很困难的;而PLC软件接线,只需要改变控制程序就可以轻易改变逻辑或增加功能。
2)工作方式上看:
电气控制并行工作,而PLC串行工作,不受约束。
3)控制速度上看:
电气控制速度慢,触电易抖动;而PLC通过半导体控制,速度很快,无触点,故而无抖动之说。
4)定时、计数上看:
电气控制精度不高,容易受环境温度变化影响,且无计数功能;PLC时钟脉冲由晶振产生,精度高,定时范围宽,有计数功能。
5)可靠、维护上看:
电器控制触点多,会产生机械磨损和电弧烧伤。
接线也多,可靠、维护性能差;PLC无触点,寿命长,且有自我诊断能力,对程序执行的监控功能,现场调试和维护方便。
3.2.输入输出I/O点数的估算
I/O点数是PLC的一项重要指标。
合理选择I/O点数可使系统满足控制要求,又可使系统总投资最低。
PLC的输入输出点数和类型应根据被控对象所需控制的模拟量、开关量等输入输出设备情况(包括模拟量、开关量等输入信号和需控制的输出设备数目类型)来确定,一般一个输入/输出元件要占用一个输入/输出点。
因此,I/O点数估算是应该考虑适当的余量,通常根据统计的输入输出点,在增加10%-20%的可扩展。
余量后,作为输入输出点数估算数据。
本次设计有9个输入和5个输出。
3.2.1控制功能的选择
该选择包括运算功能、控制功能、通讯功能、编程功能、诊断功能和处理速度等特性的选