检验控制程序范本模板Word文档格式.docx
《检验控制程序范本模板Word文档格式.docx》由会员分享,可在线阅读,更多相关《检验控制程序范本模板Word文档格式.docx(15页珍藏版)》请在冰点文库上搜索。
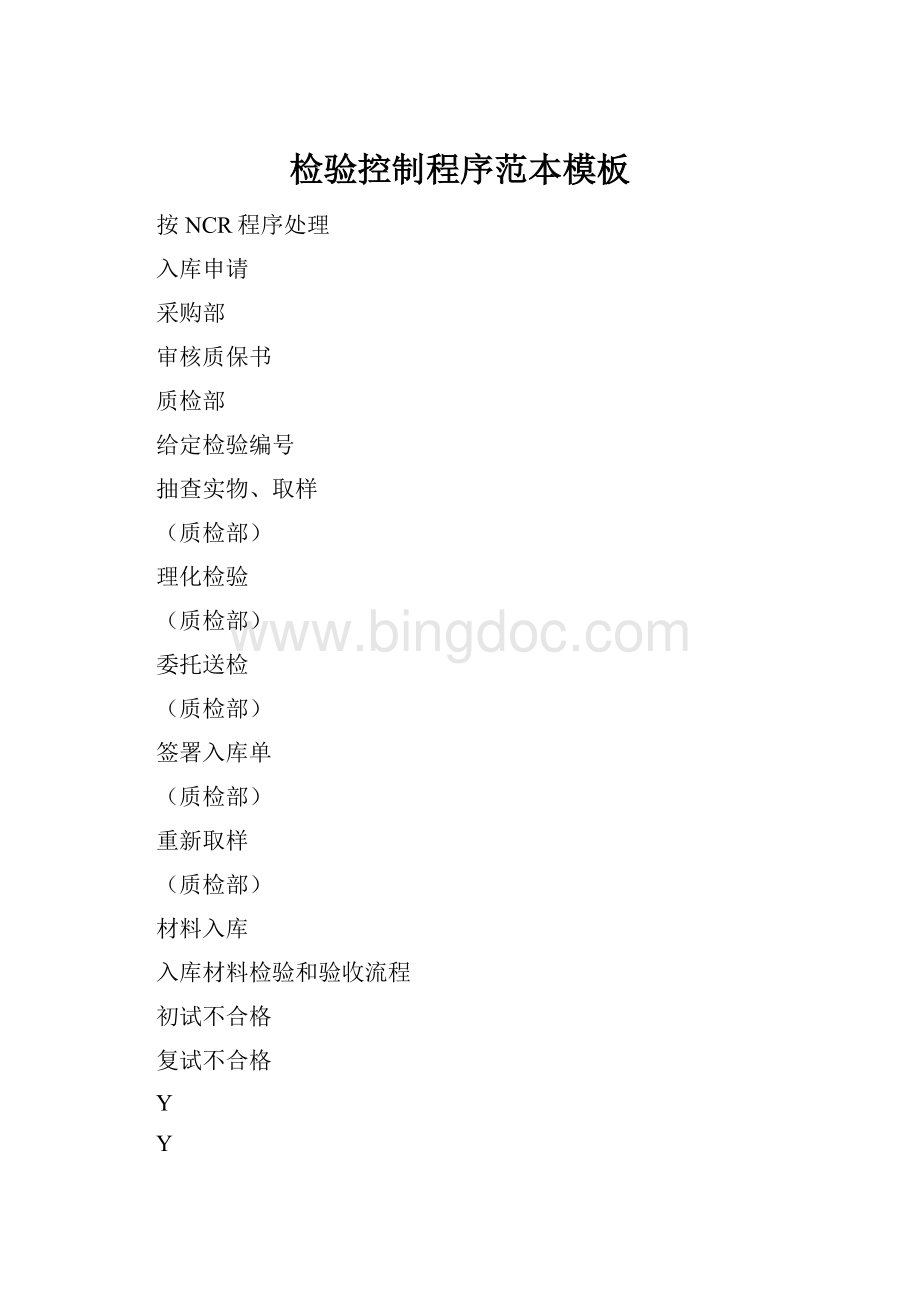
零件检查
不合格
合格
焊接质量检验
热处理质量检验
产品最终检查
检验合格报告
返修
(分厂)
NDE判定
压力、气密性试验
1.0目的
规范原材料入厂检验,产品制造过程检验的控制程序,确保产品质量满足技术规范和合同要求。
2.0适用范围
本程序适用于受公司质量体系覆盖的锅炉压力容器产品的质量检验控制.
3.0职责
3.1质量检验部
3。
1。
1计量管理员:
负责对公司检测量具、仪器仪表和检验用样板等进行计量管理,确保其在计量有效期内使用。
3.1.2分厂检查员
1)负责按“三按”要求对产品制造过程实施检验,并按规定做好检验记录;
2)负责在检验过程中行使鉴别、把关、报告职能;
3)负责对返工、返修过程的纠正措施进行验证;
4)负责对产品光谱、试样及无损检测委托等工作;
5)负责对完工产品进行100%完工检查。
3.1.3探伤人员
1)负责从事持证探伤方法的无损检测工作,探伤人员根据工艺流转卡或产品检验与试验计划开展无损检测,并及时做好检验记录;
2)Ⅱ级及以上资质探伤人员负责编制NDE工艺及签署探伤报告;
负责对已检验的产品或工序实施鉴别、把关、报告职能;
3)技术组探伤复评人员负责对分厂探伤结果进行复评;
4)Ⅱ级及以上资质的探伤人员负责对探伤设备进行校验;
5)负责对所有探伤设备按要求实施维护与保养,保证其满足检测产品的要求.
3.1.4材料检查员
1)负责原材料的入厂验收及库房原材料发放监督工作;
2)负责及时反馈检验过程(含原材料入库检验和理化检验)中发现的各种问题.
3.1.5理化试验人员
1)负责持证项目的理化检验工作(理化试验人员须持证上岗);
2)负责新材料开发的理化试验工作;
3)负责对各种缺陷或问题材料进行理化分析,为制定解决方案提供依据;
2)负责材料、试样的理化试验工作;
3)负责配合设计部门编制、修订材料采购技术条件或规范.
3.1.6质量技术人员
1)质量技术人员包括:
质量技术员、探伤技术员、材料技术员。
2)负责配合设计部门编制、修订材料采购技术条件或规范。
3)负责根据合同、有关技术标准、技术文件规定编制产品检验与试验计划(需要时),编制关键工序检验规程,并予以实施;
4)负责对检查员及分厂探伤工作的业务指导和过程监督;
5)负责编制并审核产品质量证明书。
3.2人力资源部
3.2.1负责检验人员的配置;
3.2.2负责相关检验人员的培训管理.
3.3物资管理部
3.1.1负责原材料的接收、保管、发放工作;
3.1.2负责协助原材料取样工作.
3.1.3负责原材料色标及标识工作.
3.4各分厂
3.4.1负责配合制造过程各项检验工作;
3.4.2负责产品试样的制备、协助检查人员取样工作;
3.4.3负责制造过程中材料标记移植工作;
3.4.4负责分厂余料管理工作。
4.0检验与试验控制准备
4。
1工艺及检验规程
1)质量技术员负责在工艺流转卡中设置质量控制点(见证点、审核点、停止点)并签字确认。
2)质检部检验技术人员依据标准、相关法规、程序及工艺文件编制各类检验规程,检验责任人审核后发放.
4.2探伤工艺
质量检验部持有相应方法Ⅱ级及以上资格证书的无损检测人员依据标准、相关法规、程序及工艺文件编制各类探伤工艺,无损检测责任人审核后发放.
4.3检验与试验计划(ITP)或质量计划
4.3.1对用户或技术协议有要求的产品,质检部检验技术人员依据工艺部的产品工艺流转卡、图样、规范/标准、合同和技术协议编制检验与试验计划(ITP)或质量计划,经检验责任人审核批准后发放并实施.
2检验与试验计划(ITP)或质量计划的主要内容有:
产品过程检验和试验的引用规范/标准和规程、使用的记录表格或报告、设置的质量控制点(审查点、停止点、见证点)、不合格品报告记录,监检、监造或第三方检验要求控制点等相关内容。
4.3.3分厂检查员在过程检验中严格按检验与试验计划(ITP)或质量计划进行检验控制,并做好规定的相关记录。
监造、业主或第三方检验所的控制点由车间通知检查员,经检查员检查确认后通知其见证,必要时由质检部联系项目部门或科质部通知。
5.0材料检验控制
5.1入库材料由材料检查员按同材料牌号、同规格、同炉(批)号给定一个检验编号,该检验编号具有唯一性;
5.2材料到公司后,材料检查员按照《材料管理程序》进行材料入厂验收;
5.3材料检查员应检查材料合格证是否与“采购命令单”和/或“材料采购说明书”相符,并核查材料标记是否可追踪到材料合格证,并与技术条件和规范相符;
5.4材料验收后,检查员应填写“材料验收记录"
。
并根据XXX标准要求,对材料取样进行“原材料入厂复验”,复验数据应符合规范要求.并将“材料验收记录"
与材料质量证明书一起交至材料责任人供其审核并归档。
5.5对不合格的材料和部件,应在不合格品上贴上“不一致品扣留标签”,材料检查员按《不合格品控制程序》执行.
5.6质检部材料检查员建立《入厂材料登记卡》,材料检验编号按《检验编号编码规程》执行,以确保其编号的唯一性;
5.7材料检查员按照《材料管理程序》的规定监督检查材料的保管与发放并履行材料发放日志及限额领料单的签字手续;
5.8材料到分厂后,分厂检查员核对材料发放日志或限额领料单与实物标识的一致性,并对下料情况进行监督在下料记录上签字确认,同时对材料在使用过程中的标记移植状况也应进行监督检查。
6.0产品制造过程检验
6。
1总则
6.1.1检查员严格按“三按”(标准/法规、设计图样、制造工艺)进行过程检验控制,并做好各项检验记录。
产品制造过程中,上道工序未完成所要求的检验、试验或者必须的检验、试验报告(合格通知单)未签发前,不得转入下道工序;
6.1.2检验与试验使用的检测器具及样板应按规定的检定周期进行计量;
3对检验过程中发现的不合格品,按《不合格品控制程序》执行。
6.2机械加工质量检验
2.1机械加工产品同一工号、图号在5件以下应逐件检查,5件以上按批量检查,实施首检,完工后抽查的方式进行检验控制;
6.2。
2首件检查合格后,检查员负责做好首件标识,操作者方能成批加工.同一工号、图号在5件以上,50件以下时至少随机检查6件;
同一工号、图号在50件以上时至少随机检查10件。
抽查发现不合格,应扩大一倍抽查比例进行抽查,如仍有不合格,则进行100%逐件检查,检查员应作好检查记录。
6.3冷作加工件质量检验
1检查员按标准、图样、流转卡或拼接图/落料单的要求检验下料尺寸,对筒体、封头等主要零件,应逐一检查;
对成批下料的零件,实行首件检查,中间抽查和完工抽样检查;
6.3.1经检验合格后工件/零件才能转入下道工序;
6.3.2在工件的整个加工期间,检查员应进入加工现场巡检,抽查工件的加工质量.对违反技术规范或工艺纪律的情况,检查员应立即通知操作者停止该工序的加工,直至违反的事项得到纠正或处理后,经检查员同意,操作者方能继续加工;
6.4焊接质量检验
6.4.1检查员按《焊接控制程序》、《预热消氢控制程序》的规定对焊接过程实行检查.
2检查员应核查焊工资质是否符合施焊产品的规定;
3检查焊接坡口几何尺寸符合标准、图样和工艺文件规定,坡口区域清理后应无锈蚀、油污、重皮、夹渣等影响焊接质量的杂物及宏观裂纹;
4.4检查预热温度(当工艺有此要求时)应符合工艺文件的规定,并做好记录;
4.5检查员监督检查焊工焊材领用、施焊过程中焊材保管、标识、使用的焊接规范、焊接过程是否符合焊接工艺规范的要求;
6.4.6检查员检查焊后消氢及热处理应符合工艺规范要求,并做好记录;
6.4。
7检查员按标准、图纸、工艺文件要求检查焊缝的几何尺寸及表面质量;
6.4.8检查员对产品试样的制备和焊接过程按工艺流转卡的要求进行控制。
6.4.9检查员核实焊工钢印,收集并核实焊接记录;
6.5无损探伤检测(NDE)
6.5.1检查员根据设计图样或工艺文件的要求,按规程、相关标准、检验与试验计划和图样的要求对需要进行无损探伤的产品进行焊缝尺寸和外观质量检查,表检合格后出具无损检测委托单交探伤室。
6.5.2无损检测工作结束后,探伤人员应立即做好探伤记录。
6.5.3无损探伤不合格,探伤室出具“焊缝返修通知单”交检查站、分厂技术组和工艺部,根据返修工艺返修完成后重新进行复探;
5.4无损探伤检测合格且复评合格后,复评人员在探伤记录上签章确认,探伤人员在流转卡上签字,产品放行转入下道工序.
5。
5焊缝返修根据《返修控制程序》进行返修控制并重新检验。
6.6热处理质量检验
6.6.1分厂在热处理前应通知检查员,检查员按《热处理控制程序》及热处理工艺规程的规定对产品装炉、试样随炉、热电偶布置等情况进行核实.
6.6。
2操作者应在热处理自动记录曲线表上注明热处理产品的工号、图号、纵横坐标的示值、数量等,填写热处理操作记录并签名,检查员核实后签名。
6.3检查员负责将热处理随炉试样与试验委托单一起送理化试验室,并负责取回试验报告。
4检查员审查热处理操作记录及曲线,合格后结合检查情况出具热处理检验报告,热处理检验报告应经质量技术员审核签字;
热处理曲线应经热处理责任人审核签字。
6.7压力试验
6.7.1压力试验分为耐压试验和泄漏试验,产品耐压试验和泄漏试验的选择根据设计图样及相应标准/规范执行;
6.7.2耐压试验应在无损探伤和热处理完成,且应有的报告均已收齐且合格后进行,泄漏试验须在耐压试验合格后方可进行;
6.7.3耐压试验和泄漏试验按《压力试验控制程序》进行检查控制;
6.7.4操作者应按工艺规程和作业指导书的要求进行压力试验操作,检查员现场监督检查压力试验全过程,需要时须在监检人员、监造、业主、第三方检验见证下进行压力试验。
试验时操作者做好操作记录,检查员做好检验记录,检查员依据检验记录核实操作者的操作记录并签字确认;
7。
5检查员根据检验记录出据《产品压力试验报告》。
6.8成品最终检查
成品最终检验是指产品全部制造工序完成后,完工报交、入库发运前所进行的检验,一般分为100%完工检查和放行检查两个步骤;
6.8.1100%完工检查:
产品制造完工后,分厂检查员按图纸、工艺、标准对产品实物逐件全面检查(详见附件1。
《受压件100%完工检查细则》);
6.8.2放行检验:
放行检验由分厂在产品100%完工检验合格后向质检部申请,由质检部实施放行检验。
6.8.3放行检验合格后,质检部开出产品《放行合格通知单》,分厂收到《放行合格通知单》后才能办理完工报交手续.
6.8.4产品放行后,方可进行产品包装;
产品油漆包装应经质检部检查确认后,开出《产品油漆包装放行合格通知单》,分厂将《产品油漆包装放行合格通知单》交项目部组织发运.
7.0协作件质量检验
1公司内协作件检验由加工分厂检查员进行过程控制检验。
协作件转出分厂时应将产品转送单交所在分厂检查员签字认可,以示该批转送件已检验合格。
转出分厂检查站将协作件质量资料,包括“材料限额料领料单"
、“材料代用单”、“试验或检验记录"
(包括试样报告、光谱报告、弯管记录等)收集整理齐全,并建立转入、出资料登记台帐;
协作件资料由转出分厂检查站随同产品一起转送接受分厂检查站,资料交接须有签字手续;
2外包协作件(含工序性外包加工件)原则上落地检查,必要时由质检部技术组负责进行实物检验及资料审核。
产品转回分厂时,采购部将相关质量资料转送质检部,质检部对实物及质量资料检查合格后在转送单上签字确认。
3接收分厂发现转回的协作件出现不符合项时,经检查站核实后对协作件进行扣留.
7.3.1公司内协作件出现不符合项时,接收分厂检查站通知协作件转出分厂检查站以质量信息反馈方式通知相关部门进行处理;
7.3。
2外包协作件出现不符合项时,接收分厂检查站通知质检部技术组以质量信息反馈方式通知相关部门进行处理;
8.0外包产品检验控制
8。
1外包产品的供方必须是经公司评审后合格的供方;
2主要受压件外包,公司将派驻监造代表进行过程质量监督;
8.3外包产品制造完工后由采购部门向质检部申请放行检验,放行检验合格后质检部出具《放行检验合格通知单》交采购部;
8.4采购部收到《放行检验合格通知单》后才能报交并通知外包方发运。
9.0检验、试验状态的控制
9.1产品检验与试验状态分为:
合格、不合格、待检三种状态;
9.2产品制造过程中通过产品实物标识、标牌、工艺流转卡签字、检验记录、试验报告、工件放置地点等适当方法,表明产品检验与试验状态;
9.3原材料由物资管理部按“待检区"
“合格区”“不合格区”等分区堆放,表明材料检验状态;
9.4工序流转检验状态控制
9.4.1分厂内的工序质量检验状况控制
1)质量检查实行自、互检与专检相结合进行质量控制的原则,操作者应严格“三按”生产,完工后在工艺流转卡签字流转;
对专检工序专检人员严格按“三按”检查,检查合格后检查人员在工艺流流转卡上签字确认后方可转序,上道工序不合格不得转入下道工序。
水压、完检等工序检查合格后,须在实物上进行该工序检验合格的状态标识,如“水压合格"
等。
2)对于应作记录的检验项目,按指定表格所规定的内容作好记录,作为检验项目合格与否的见证件.
3)批量机械加工件首检合格后须用油漆做出“首检合格”标识,并作好检验数据记录。
9.4.2试样检验状态控制:
由分厂在试样上标记钢印,分厂检查站负责对焊缝质量、标识进行检查,并在实物上做检查合格与否标识,探伤人员做探伤合格与否标识,检查人员核实合格后在试样上标记检查员代号钢印;
产品试样送检后,检查站建立“试样登记台帐”,对送样情况进行记录,未收到试样检验合格报告,产品不得转序;
试样加工完成后,由机加车间在试样上移植或打上正确的钢印标识。
9.4.3无损检测检验状态控制:
无损探伤检验由检查站按相关要求开出《无损探伤委托单》交探伤室,无损探伤检测合格后,探伤人员在流转卡上签字,产品放行转入下道工序。
9.4.4光谱检验检验状态控制:
检查站开出《光谱检验申请单》交光谱检验员,光谱检验合格后,光谱检验员在流转卡上签字,产品放行转入下道工序.
9.4.5协作件产品检验状态控制:
采用转送单签字控制和检验软件资料跟踪的方法进行检验状态控制,确保接口质量.
9.5产品完工检验状态控制
9.5。
1产品完工检查后在产品实物上进行完检合格与否的状态标识;
9。
5.2完工产品在报交签字前由分厂对产品实物进行标识,并经检查员认可;
5.3凡需订铭牌的产品,生产分厂将铭牌交检查站检查,确认铭牌标识内容符合规定要求后,在检查人员的监控下由生产分厂打上产品制造日期,并确认铭牌已装在图样规定的位置.
10.0质量检验资料的收集、整理、审核及归档
10.1产品质量检验资料是指产品在制造、检验和试验过程中所形成的有关产品质量方面的记录、报告、图表和卡片等文件资料,至少包括下列内容:
10.1.1受压元件及直接与受压元件相焊零件的材料和焊接材料的限额领料单、材料代用单、焊材领用单及焊接记录等;
10.1.2焊接试样的试验报告;
10.1.3质量计划或检验与试验计划、产品工艺流转卡、设计和工艺的临时更改单;
10.1.4不合格品报告单;
10.1.5产品的热处理检验报告、热处理操作记录和自动记录曲线图;
10.1.6各类探伤报告及其委托、光谱检验报告;
10.1.7产品的主要检查记录或图表(如质量检查记录卡、结构尺寸检查报告或完工检查记录等);
10.1.8产品压力试报告,产品铭牌拓印件或复印件等。
10.2质量档案资料的汇总、审核和归档
10.2.1产品放行检查后,分厂检查站将资料汇总整理后交质检部技术组。
10.2.2质检部质量技术员根《固定式压力容器安全技术监察规程》编制产品质量证明书。
10.2.3质量证明书经检验工程师审核无误,由质检部部长审定,加盖质量检验合格专用章、质保工程师印章。
由质检部负责办理监检证明。
10.2.4质量记录和资料的归档、保存按公司档案管理相关制度执行.
11.0相关文件
●《不合格品控制程序》
●《热处理控制程序》
●《材料管理程序》
●《焊接控制程序》
●《压力试验控制程序》
●《计量管理程序》
●《检验编号编码规程》
●《预热消氢控制程序》
●《返修控制程序》
12.0
相关表格
●《机加工零件质量检验记录》
●《光谱检验申请单》
●《光谱检验分析报告》
●《产品授权放行申请单》
●《放行合格通知单》
●《产品油漆包装放行合格通知单》