冲击试验操作规程DOCWord格式.docx
《冲击试验操作规程DOCWord格式.docx》由会员分享,可在线阅读,更多相关《冲击试验操作规程DOCWord格式.docx(18页珍藏版)》请在冰点文库上搜索。
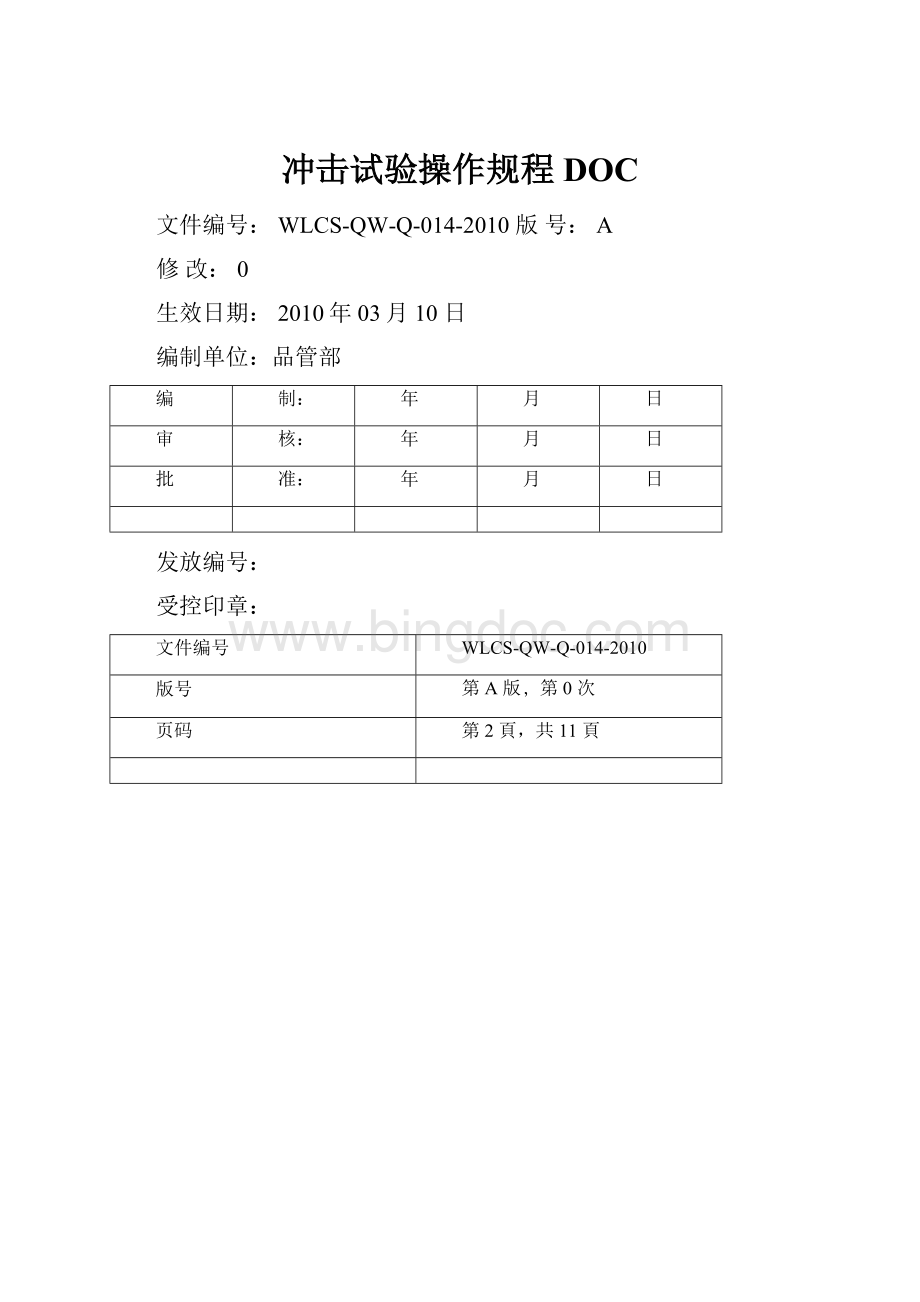
3.5冲击试验机操作规程
3.6试验机的常规检查⋯
3.7设备校验⋯⋯⋯⋯⋯
4.相关文件⋯⋯⋯⋯⋯⋯⋯
5.质量记录⋯⋯⋯⋯⋯⋯⋯
6.修订记录⋯⋯⋯⋯⋯⋯⋯
7.附件⋯⋯⋯⋯⋯⋯⋯⋯⋯
第3頁,共11頁
1.岗位职责和权限
1.1职责1.1.1按力学测试技术标准保质保量完成力学测试任务,认真执行力学测试操作规程。
1.1.2提前5分钟到岗,检查物理室仪器设备是否正常。
1.1.3坚守工作岗位,不得随便离开,有事应向组长请假。
1.1.4认真做好原始记录,对测试结果负责。
1.1.5负责提出设备易损件的请购计划,做好仪器的清洁卫生工作,管好、用好各类计量器具,并协助计量室做好仪器设备的定期检定工作。
1.1.6有责任接收上级主管的考核与检查。
1.1.7努力钻研技术,对工作精益求精,保证试验的准确性。
1.2权限
1.2.1对试验结果按产品标准的规定,有权作出试验结论。
1.2.2对既无产品性能说明,又无技术标准的产品有权拒绝试验。
1.2.3有权向主管部门如实反映产品质量情况。
1.2.4有权拒绝其它部门人员进入试验室,随便乱开设备,以防设备损坏而影响正常的试验情况。
2.主要设备参数及工装主要设备为JB-300B型号的冲击试验机。
3.作业流程及操作规程
3.1一般要求
3.1.1冲击试验试按国标《GB/T229金属材料夏比摆锤冲击试验方法》或相应的产品标准要求进行试验。
3.1.2钢管产品冲击性能测试在冲击试验机(JB-300B)上进行。
3.1.3试样的制取和验收按相应的产品标准规定,试样尺寸偏差不得超过标准允许范围。
3.1.6根据《检测委托单》验收试样的钢种、炉号、检测内容,填写台帐并做好原始记录。
3.2试样
采用V型缺口试样。
3.2.1试样的尺寸
3.2.1.1ASTM及GB,EN标准试样尺寸:
冲击试样长度为55mm,横截面为10×
10方形截面,试样长度中间有V型缺口,缺口应有45°
夹角,其深度为2mm,底部曲率半径为0.25mm,缺口对称面垂直于试样纵向轴线,如图1,缺口根部应无影响吸收能的痕迹。
EN还注明缺口开在试样窄的面上,若相关产品标准允许,可不加工试样宽度,使产品厚度为试样宽度。
第4頁,共11頁
图1
3.2.1.2小尺寸标准试样:
A为加工面,最小28mm;
B为原始外表面,最大13.5mm;
T为试样厚度,尺寸见图1;
t为端部厚度,最小1/2T
图2
ASTM——可采用宽度为7.5mm,6.7mm,5mm,3.3mm,2.5mm的小尺寸标准试样。
对于吸收功超过实际初始势能的80%的材料,采用小尺寸标准试样;
材料不足时,采用材料允许的最大的小尺寸标准试样,试样不包括距钢管表面0.5mm以内的材料。
在管子横向方向试验的试样,若不能获得标准试样,可采用图2所示的标准试样。
GB——可采用宽度为7.5mm,5mm,2.5mm的小尺寸标准试样。
EN——可采用宽度为7.5mm,5mm的小尺寸标准试样。
3.2.1.3试样的尺寸偏差见表1。
表1
名称
GB
ASTM
EN
公称尺寸
机加工偏差
长度
55
±
0.60mm
+0,-2.5mm
高度
10
0.075mm
宽度——标准试样——小试样——小试样——小试样——小试样——小试样
10mm
7.5mm
5mm
2.5mm
0.11mm
0.06mm
0.04mm
6.7mm5mm
3.3mm
1%
5mm
缺口角度缺口底部高度
45°
8mm
2°
1°
缺口根部半径
0.25mm
0.025mm
缺口对称面-端部距离
27.5mm
0.42mm
—
缺口对称面-试样纵轴角度
90°
试样纵向面间夹角
10min
表面粗糙度
除端部外,试样表面粗糙度优于5μm
缺口表面和背面2μm另外两面4μm
3.3试验程序
3.3.1一般要求试样应紧贴试验机跕座,锤刃沿缺口对称面打击试样缺口的背面,试样缺口对称
第5頁,共11頁
面偏离两跕座间的中点应不大于0.5mm(ASTM例外,为0.25mm)。
试验前检查摆锤空打时的回零差或空载能耗。
回零差不应超过最小分度值的四分之一。
(ASTM中规定总的摩擦力损失和风损不得超过试验机刻度盘能力的0.75%,指
示装置的摩擦力损失不得超过刻度盘能力的0.25%。
)试验前检查跕座跨距,跕座跨距应保证在40+0.2mm以内(ASTM例外,为40±
0.05mm)。
3.3.2试验温度
3.3.2.1对于试验温度有规定的,其温度偏差如下:
GB——应在规定温度±
2℃范围内进行;
EN——应在规定温度±
ASTM——应在规定温度±
1℃范围内进行若果没有规定,在室温下进行冲击试验:
GB——23℃±
5℃;
EN——23℃±
ASTM——20℃±
5℃。
用于夹持试样的钳子应与试样保持相同的温度。
3.3.2.2当使用液体介质冷却或加热试样时,试样应放置于一容器的网栅上。
GB及EN——网栅至少高于容器底部25mm,液体浸过试样的高度至少25mm,试样距容器侧壁至少10mm。
ASTM——缺口部分至容器底部和侧壁至少25mm,试样的任何部分不接触容器。
应连续均匀搅拌介质以使温度均匀。
测定介质温度的仪器推荐置于一组试样中间处。
介质温度应在规定温度±
1℃以内,保持至少5min。
当采用气体介质冷却试样时,试样距低温装置内表面以及试样与试样之间应保持足够的距离,试样应在规定温度下保持一端时间:
GB——至少20min;
ASTM及EN——至少30min。
3.3.2.3对于试验温度不超过200℃的高温试验,试样应该在规定温度±
2℃的液池中保持至少10mmin。
对于试验温度超过200℃的试验,试样应该在规定温度±
5℃以内的高温装置内至少保持20min。
(ASTM及EN无此说明)3.3.3试样的转移
当试样不再室温进行时,试样从高温或低温装置中移出至打断的时间应不大于5s。
转移装置的设计和使用应能使试样温度保持在允许的温度范围内。
转移装置与试样接触部分应与试样一起加热或冷却。
应采取措施确保试样对中装置不引起低能量高强度试样断裂后回弹到摆锤上而引起不正确的能量偏高指示。
试样端部与对中装置的间隙或定位部件的间隙应大于13mm,否则,在断裂过程中,试样端部可能回弹到摆锤上。
(EN中无此说明)本实验室规定试样从液体介质中移出至打击的时间应在5秒之内,试样离开气体介质装置至打击的时间应在1秒之内,如果不能满足上述要求则必须在3-5秒内打断试样。
3.3.4试验机能力范围
GB——试样吸收能量K不应超过实际初始势能的80%,如果试样吸收能量超过此值,在试验报告中应报告为近似值并注明超过试验机能力的80%。
建议试样吸
收能量K的下限不低于试验机最小分辨力的25倍。
ASTM——试验机能力一般为300到400J,冲击线速度在4.9~5.8m/s范围内。
第6頁,共11頁
EN——试验机能力一般为300±
10J冲击瞬间速度为5~5.5m/s,1983年以前生产的试验机,冲击速度4.5~7m/s。
本实验室规定冲击试验机一般在摆锤最大能量的10%-90%范围内使用。
3.4试验结果
3.4.1试样冲击吸收功
ASTM冲击吸收功精确到1J。
GB冲击吸收功应至少估读到0.5J或0.5个标度单位(取两者之间较小值)。
试验结果至少保留两位有效数字,修约方法按GB/T8170执行
EN冲击吸收功精确到1J。
3.4.2断面形貌
3.4.2.1测定剪切断面率
1)测量断裂面的脆性区(解理断裂部分),如图3所示。
剪切断面率=1-A*B*100%,测量A和B的尺寸精确到0.5mm。
2)将试样的断口形貌与GB229-07附录C,图C.2所示的标准断口形貌进行比较。
3.4.3侧面膨胀
3.4.3.1检查两半截试样的突出部分,是否由于与试验机跕座接触或测量安装时被损坏。
若被损坏,则此试样不做测量,作废。
3.4.3.2检查试样侧边是否出现毛刺,如过有毛刺要用砂布或毛刷去除。
磨毛刺时,注意不应磨掉试样侧面的突出部分。
3.4.3.3侧面膨胀量为试样宽度方向的增量。
如图4所示,将试样沿原始侧面对齐,分别以原始侧面为基础测量两半断样(X和Y)两侧的突出量,取两侧最大值。
例如,A1>
A2,A3=A4时,LE=A1+(A3或A4);
A1>
A2,A3>
A4时,LE=A1+A3。
3.4.3.4ASTM规定膨胀量的测量精确到0.025mm。
3.4.3.5测量侧面膨胀值的量具如图5所示。
3.4.4试样未完全断裂
GB——对于试样试验后没有完全断裂,可以报出冲击吸收能量,或与完全断裂试样结果平均后报出。
由于试验机打击能力不足,试样未完全断开,吸收能量不确定,试验报告应注明用**J的试验机试验,试样未断开。
ASTM——对于冲击吸收功小于试验机能力的80%,没有完全断裂的试样,若不用单独报出每个试样的冲击吸收功,未完全断裂试样结果应与完全断裂试样结果
第7頁,共11頁
平均后报出并注明未断裂试样百分比,若冲击吸收功超过试验机能力的80%,并
且试样从跕座中间完全穿过,则报出吸收功近似值,若未从跕座中间完全穿过,则报告试验结果超过试验机能力,同一试样不能冲击两次。
EN——试样试验后没有完全断裂,在试验报告中注明用**J的试验机试验,试样未断开。
本实验室规定,由于试验机打击能量不足使试样未完全折断时,应在试验数据之前加大于符“>
”,其它情况则应注明“未折断”。
图5
3.5.1开机使用时经空转运行,以检查机子是否正常,如果保险销不复位,需按动“退销”按钮,使保险销复位。
3.5.2根据能量要求可选用300焦耳摆锤或150焦耳摆锤。
换摆时先拧出压紧螺母,用拆卸器插入摆杆插头两侧的槽内,拧动丝杠,顶住摆轴端面即可退出,换上需要的摆锤。
3.5.3摆锤挂钩与摆锤机构接触长应为3-4mm左右为宜,若需调整则要移动挂钩的位置。
3.5.5当摆锤在扬摆过程中尚未挂于挂摆机构上,工作人员不得在摆锤摆动范围内活动或工作,以免偶然断电而发生危险。
3.5.6摆轴两端轴承出厂时已加油,一般不必加油。
经修理清洗后可加1-2滴缝纫机油
或钟表油,其余动力轴承加凡士林或黄油。
3.5.7试验完毕后,按住放摆按钮,将摆锤落放至铅垂位置时,松开放摆按钮,切断电源。
3.6试验机的常规检查
3.6.1在每天,每次改动后,或试验前对间歇使用仪器进行一次常规检查。
3.6.2目视检查摆锤和跕座上有无明显损坏和磨损。
3.6.3回零检查:
将摆锤举到保险销位置,指针指到使用范围的最大能力,松开摆锤,读取指示值,指针应指向能量读数的零位置。
3.6.4按以下步骤检验摩擦力损失和风损:
将摆锤提升到保险销位置,将指针指到负零位置,释放摆锤,让其摆动5个周期(一前一回的摆动作为一周期),第六次向前摆动之前,将指针调到刻度盘能量刻度的5~10%,第六次向前摆动之后(11次半摆动),记录指针指示数值,将其除以11之后,再除以最大刻度值,最后乘以100得到摩擦力损失的百分数。
试验结果中,摩擦力损失和风损不得超过所测量
第8頁,共11頁
的能量刻度范围的0.4%,并且与之前试验机的摩擦测量值之差不超过10%,若摩擦力损失和风损超过0.4%或与之前的测量值有明显差别,应检查指示装置,保险销高度和轴承的磨损与破坏情况。
若机器有一段时间没有用过,则在校正试验机之前,让摆锤摆动50~100个周期,检验摩擦力损失。
3.7设备校验校验由两部分组成,直接校验和间接校验。
检验应每年进行一次。
更换部件,机器修理、调节或移动之后,或对试验结果有怀疑时应进行校验。
3.7.1需要年检的部件的直接校验
3.7.1.1检查试样支座,跕座及摆锤,发现磨损即进行更换,用直角尺或半径量规来测量这些部件未使用前和使用之后的尺寸来判定磨损情况,支座、跕座及摆锤的尺寸见图6
3.7.1.2将螺栓按机器说明书固定紧。
3.7.1.3采用U型摆锤时,检查防止试样回弹的铁罩是否安装好。
3.7.1.4摆锤释放装置应在两个方向都进行检查。
摆锤释放装置应运转灵活,释放摆锤时应没有延迟现象,对摆锤无推动力且使摆锤无侧面摆动。
若释放摆锤用的杆壁也用来衔接刹车,则应避免杆壁意外的衔接刹车。
3.7.1.5在两个方向对机器水平度进行检查,机器应配备有确定摆锤摆动轴线的水平面的测量装置。
机器的水平度应在3:
1000以内,并且用螺栓牢固的固定在厚度不小于150mm的混凝土地面或固定在质量不小于40倍摆锤质量的地基上。
3.7.1.6跕座应按机器说明书牢固地固定在地面上
3.7.1.7按3.5.3检查指针回零和摩擦力损失。
3.7.2每年至少一次直接校验的部件
3.7.2.1跕座和支座应符合图3的要求(图中ANVIL指跕座,SpecimenSuppor指t支座,STRIKE指摆锤)
3.7.2.2摆锤应符合图3的要求,摆锤刀刃表面应干净无缺陷,摆锤的中心线与跕座的中点的偏差应不超过0.40mm。
摆锤垂直于试样的纵向轴线,偏差不超过
第9頁,共11頁
0.5%。
摆锤平行于背靠跕座的完全正方的试样表面,偏差不超过0.1%。
3.7.2.3摆锤的定位应符合以下要求:
自由悬挂时,锤头与试样之间的距离在2.5mm之内。
摆锤自由摆动,将指针指向零位置,摆动停止后将摆锤紧靠试样,读数应该在刻度盘范围的0.2%以内。
摆锤的摆动方向应垂直于试样的横向轴。
锤头在4%摆锤质量的横向力作用下,横向摆动不超过0.75mm,摆锤轴承的径向间隙不超过0.075mm。
若摆锤的侧面摆动或轴承的径向摆动超出限定值,则调整或更换轴承
3.7.2.4打击中心的确定——采用半宽试样(10×
5×
55mm),将锤头与试样接触,沿试样顶部边缘在锤头上画一条直线,即标出打击中心。
3.7.2.5势能的测定——摆锤打击中心与从摆锤轴承,这里叫转动轴,到重心的连线应一致。
若打击中心偏离此直线多于1.0mm,则应采取合适的措施(见3.7.2.8,3.7.2.9)来调整打击中心。
势能为摆锤掉落高度乘以支撑力。
1)为了测量支撑力,用两个支架来支撑水平摆放的摆锤,一个支架放在摆锤轴承(或转动轴中心)处,另一个支架放在台称或天平上,并支撑在锤头打击中心处,可使用垫片来让摆锤处于水平状态。
将两支撑物处的摩擦力降至最小,台称或天平读数准确到0.4%。
支撑力为天平读数减去支架以及垫片的质量。
2)处于保险销位置的打击中心高度应在能力范围除以支撑力所得值的0.4%范
围内。
可通过提高摆锤掉落高度来补偿摩擦损失和风损,摆锤掉落高度的增量不超过1%。
摆锤掉落高度可通过量取半宽试样的顶部边缘到打击中心之间的距离来获得,精确到0.1%。
3.7.2.6冲击速度ν的测定(不记摩擦损失)
式中,ν=速度,m/s;
g=重力加速度,9081m/s2;
h=摆锤初始高度,m3.7.2.7打击中心应为大小在转动轴至试样上摆锤打击中心距离的1%以内的一点,
打击中心位置的测定:
1)使摆锤在总角度不大于15°
的范围内摆动,用测量单位小于0.2s的时间测量装置,记录摆锤摆动100个周期(一次前摆和一次后摆组成一周期)所耗费时间,摆锤的周期为此耗费时间除以100所得的数值。
2)通过下式来测定打击中心:
式中,L=转动轴到打击中心的距离,m
2g=重力加速度,m/s2π=3.1416
P=一个摆动周期,s
3.7.2.8摩擦损失的测定通常用提高摆锤起始高度的方法来补偿摩擦损失。
测定摩擦能量损失的方法如下:
1)在试验机上不摆放试样,将指针指到能量刻度的最大值,从起始高度释放摆锤,记录指针指示能量。
若摩擦损失已经被生产商校验好,则此读数应该为0。
慢慢将摆锤升高,直至指针指到自由摆动时的数值。
将摆锤保持在
第10頁,共11頁
这一高度,在试样支座上放置半宽试样,测量从打击中心到半宽试样顶部的垂直距离,误差不超过0.1%。
按3.7.2.5中1)的方法计算支撑力,然后乘以此垂直距离,得到的数值与初始势能之差即为摆锤和指针总的能量损失。
不重设指针位置,重复的将摆锤从初始位置释放,直至指针不再移动。
最终指针位置即为摆锤能量损失。
指针的摩擦力损失可由总能量损失减去摆锤能量损失获得。
3.7.2.9检查整个量程内指示装置的精确度,刻度盘任何一点的的误差不超过量程的0.2%或读数的0.4%,两者取较大值。
在每个量程的近似对应于0,10,20,30,50以及70%处的刻度标记处做检查。
采用做有标记的锤头来标识打击中心,将摆锤升到使指针读数,如13J,的位置并固定好,测定从锤头打击中心到半宽度试样顶部的距离,精确到0.1%。
将此距离乘以支撑力(3.5.2.5中1)项)得到残余能量。
摆锤在保险销位置时的势能减去残余能量和比例能量损失(摆锤自由摆动时总的能量损失乘以摆锤从保险销位置到指针读数位置的夹角与摆锤从保险销位置到指针读数为零时位置的夹角的比值)得到一数值,指针的读数应与此数值一致。
在刻度盘上其它读数位置做相同的计算。
指示装置不能超过或滞后于摆锤。
从不同的高度释放摆锤,目视检查不同量程范围内指针的转动灵活性。
3.7.3间接校验
3.7.3.1采用有确定的冲击吸收功的试样来检查试验机的准确性。
校验试样分低(13~20J),高(88~136J)和超高(176~244J)三个能量等级。
每一能量等级的一组试样测得的冲击吸收功平均值与名义值的差不超过1.4J或5.0%,两者
取较大值。
3.7.3.2用可在试验机上进行试验的试样的最低和最高冲击吸收功来表示试验机的校验范围,采用两个或更多能量等级的试样来确定此范围,除非试验机能力有限,只能采用一个能量等级的试样。
3.7.3.3在用校验试样进行试验之前,先测定冲击试验机的可用量程。
读数表盘的分辨力决定试验机可用量程的下限,试验机量程下限为15J的刻度盘分辨力的25倍。
试验机可用量程的上限为试验机能力的80%。
3.7.3.4试验时采用的校验试样的冲击吸收功应在冲击试验机的可用量程范围内。
为了能在整个可用量程内对试验机进行校验,对在量程范围内可采用的最低能量等级和最高能量等级的试样进行试验。
若试样的最高和最低冲击吸收功名义数值之比大于4,则应再取一组冲击吸收功处于两者之间的试样进行试验。
用校验试样每个能量等级的上限(20,136和245J)来测定可采用的试样最高能量等级。
用校验试样能量等级的下限来测定试验可采用的校验试样最低能量等级。
若没有采用低能量等级的校验试样(仅采用高和超高水平能量等级),校验量程的下限为试验采用的校验试样的最低冲击吸收功的一半。
例,试验时高等级试样的名义冲击吸收功为100J,则下限为50J。
若试验机可采用的最高冲击吸收功试样没有进行试验,则量程上限为试验采用的最高名义冲击吸收功的1.5倍。
例,冲击试验机的最大能力为325J,但是只用低等级和高等级的校验试样进行了试验,高等级试样的名义冲击吸收功为100J,则校验量程的上限为150J。
因此,为了在这台试验机的全量程内进行校验,应对低,高,和超高等级的校验试样进行试验。
超高等级的校验试样可以在能力为325J的试验机上进行试验,因为80%×
325J=260>
J244J。
第11頁,共11頁
4.相关文件
4.1
4.2
4.3
4.4
4.5
4.6
实验试验管理办法》数值修约规则》金属夏比缺口冲击试验方法》钢制品机械性能试验方法及定义》金属缺口试样冲击试验方法》金属夏比缺口冲击试验》
WLCS-QA-Q-002-2010
GB8170
GB/T229-2007
ASTMA370-03a
ASTME23-02a
EN10045-1-1990
5.质量记录
5.1质量要求
5.1.1产品质量必须符合相应要求标准后方可出厂。
5.1.2达不到产品标准要求的要加倍取样进行复验。
5.1.3对复验仍达不到要求的产品由质检科进行改判
5.1.4试验结束后,试验结果输入QMS